Durable Steel Conveyor Belt Shaft Driving Components
The conveyor belt shaft is a critical component in industrial conveyor systems, responsible for the smooth operation and movement of the conveyor belt. Motorized roller conveyors with advanced conveyor belt shaft technology offer superior performance for industrial applications, ensuring efficient power transmission. Its primary role is to provide rotational power, ensuring that the belt moves consistently and efficiently, which is essential for maintaining productivity in various industries. The conveyor belt shaft must be durable and precisely engineered to handle the stresses and loads it encounters during operation. Proper maintenance of the conveyor belt shaft is crucial to prevent downtime and extend the lifespan of the conveyor system. Understanding the importance of the conveyor belt shaft can help industries optimize their material handling processes and improve overall efficiency.
Common Conveyor Belt Shaft Sizes
The conveyor belt shaft is a crucial component of conveyor systems, playing a significant role in their efficiency and performance. Choosing the right conveyor belt shaft size is essential for ensuring the proper functioning of the conveyor system. Conveyor belt shafts come in various sizes, each designed to accommodate different load capacities, speeds, and applications.
Standard Sizes
The sizes of conveyor belt shafts are typically standardized to meet the requirements of different industrial applications. The most common sizes include diameters ranging from 20mm to 100mm, although shafts with larger diameters are also available for heavy-duty applications. These sizes are designed to fit within the standard dimensions of mine conveyor belt systems, ensuring compatibility and ease of replacement.
- Small Diameter Shafts (20mm to 40mm) These shafts are used in light-duty conveyor systems where the load capacity is relatively low. They are ideal for applications such as small packaging lines, food processing, and light manufacturing. The smaller diameter shafts are also beneficial for systems that require high speed but carry lighter loads. Their lightweight nature reduces the overall weight of the system, contributing to energy efficiency.
- Medium Diameter Shafts (40mm to 70mm) Medium diameter shafts are commonly used in medium-duty conveyor systems. They strike a balance between load capacity and speed, making them suitable for a wide range of applications, including automotive assembly lines, warehouse logistics, and medium-scale manufacturing processes. These shafts offer enhanced durability while maintaining a reasonable weight, making them versatile and widely adopted in various industries.
- Large Diameter Shafts (70mm to 100mm) Large diameter shafts are designed for heavy-duty conveyor systems that require high load capacities. These shafts are robust and can withstand significant stress and wear. They are typically used in applications such as mining, heavy manufacturing, and large-scale material handling. The increased diameter provides additional strength and rigidity, ensuring the conveyor system can handle substantial loads without compromising performance.
Custom Sizes
In addition to the standard sizes, custom conveyor belt shafts can be manufactured to meet specific requirements. Custom sizes are essential for unique applications where standard shafts may not provide the necessary performance or fit within the existing system. Customization can include variations in diameter, length, and material composition, tailored to the specific needs of the conveyor system.
Factors Influencing Shaft Size Selection
Selecting the appropriate conveyor belt shaft size involves considering several factors, including load capacity, speed, and the nature of the material being conveyed. Understanding these factors is crucial for optimizing the performance and longevity of the conveyor system.
- Load Capacity The load capacity is one of the primary considerations when selecting a conveyor belt shaft size. The shaft must be able to support the weight of the conveyed materials without bending or breaking. Engineers calculate the required diameter based on the maximum load the system will handle, ensuring the shaft can withstand the operational stress.
- Speed The speed of the conveyor system also impacts the choice of shaft size. Higher speeds generate more centrifugal force, which can affect the shaft’s stability. Therefore, shafts used in high-speed applications may require larger diameters to maintain their structural integrity and prevent excessive vibrations.
- Material Characteristics The type of material being conveyed influences the shaft size selection. Abrasive or heavy materials may require larger and more robust shafts to resist wear and tear. Additionally, materials with specific handling requirements, such as fragile or temperature-sensitive items, may necessitate custom shaft designs to ensure safe and efficient transportation.
The selection of the appropriate conveyor belt shaft size is a critical aspect of designing and maintaining efficient conveyor systems. Standard sizes provide versatility and compatibility, while custom sizes offer tailored solutions for unique applications. By considering factors such as load capacity, speed, and material characteristics, engineers can ensure the optimal performance and longevity of the conveyor belt shaft.
Materials Used in Conveyor Belt Shaft Manufacturing
The choice of materials used in the manufacturing of conveyor belt shafts significantly impacts their performance, durability, and suitability for various applications. Different materials offer unique properties that cater to specific industrial needs. This section explores the common materials used in conveyor belt shaft manufacturing and their respective benefits.
Steel
Steel is one of the most commonly used materials for conveyor belt shafts due to its excellent strength and durability. It is available in various grades, each with specific properties that make it suitable for different applications.
- Carbon Steel Carbon steel is widely used for its high strength and toughness. It is suitable for medium to heavy-duty conveyor systems where the shafts are subjected to significant stress and load. Carbon steel shafts are also cost-effective, making them a popular choice in many industries. However, they may require protective coatings to prevent rust and corrosion, especially in humid or wet environments.
- Stainless Steel Stainless steel is known for its corrosion resistance, making it ideal for applications where the conveyor system is exposed to moisture, chemicals, or other corrosive substances. It is commonly used in the food processing, pharmaceutical, and chemical industries. Stainless steel shafts also offer good strength and durability, ensuring long-term performance with minimal maintenance.
- Alloy Steel Alloy steel shafts are made by combining carbon steel with other elements such as chromium, molybdenum, and nickel to enhance specific properties like strength, hardness, and resistance to wear and corrosion. These shafts are used in heavy-duty applications where high performance is critical. Alloy steel shafts offer superior mechanical properties, making them suitable for demanding environments.
Aluminum
Aluminum is another material used in conveyor belt shaft manufacturing, particularly for applications where weight reduction is essential. Aluminum shafts are lightweight yet strong, making them ideal for high-speed conveyor systems that carry lighter loads. They also offer good corrosion resistance, making them suitable for outdoor or humid environments. However, aluminum shafts may not be suitable for heavy-duty applications due to their lower strength compared to steel.
Composite Materials
Composite materials are becoming increasingly popular in conveyor belt shaft manufacturing due to their unique properties. These materials are made by combining two or more different substances to create a material with enhanced characteristics.
- Fiber-Reinforced Plastics (FRP) FRP shafts are made by reinforcing plastic with fibers such as glass, carbon, or aramid. These shafts offer excellent strength-to-weight ratios, making them suitable for high-speed and lightweight applications. They also provide good corrosion resistance and can be designed to withstand specific environmental conditions. FRP shafts are commonly used in the aerospace, automotive, and marine industries.
- Carbon Fiber Carbon fiber shafts are known for their exceptional strength and stiffness while being lightweight. They are used in high-performance applications where weight reduction is critical, such as in the aerospace and automotive industries. Carbon fiber shafts also offer excellent fatigue resistance, ensuring long-term durability under cyclic loading conditions.
Ceramic Coatings
In some cases, conveyor belt shafts are coated with ceramic materials to enhance their wear resistance and extend their service life. Ceramic coatings provide a hard and durable surface that can withstand abrasive environments and high temperatures. These coatings are commonly used in mining, material handling, and manufacturing processes where the shafts are exposed to harsh conditions.
Plastic
Plastic shafts are used in applications where weight reduction, corrosion resistance, and low friction are essential. They are typically made from high-performance polymers such as nylon, polyethylene, and polycarbonate. Plastic shafts are suitable for light-duty applications and are often used in the food processing, packaging, and pharmaceutical industries.
Factors Influencing Material Selection

The choice of material for conveyor belt shafts depends on several factors, including the application’s specific requirements, environmental conditions, and cost considerations.
- Load Capacity and Strength The material must provide adequate strength to support the load without deforming or failing. For heavy-duty applications, materials with high tensile strength, such as steel or alloy steel, are preferred.
- Corrosion Resistance In environments where the shafts are exposed to moisture, chemicals, or other corrosive substances, materials with good corrosion resistance, such as stainless steel or composites, are essential to prevent degradation and ensure longevity.
- Weight The weight of the material is a critical consideration for high-speed applications. Lightweight materials like aluminum or composites reduce the overall weight of the conveyor system, enhancing efficiency and reducing energy consumption.
- Wear Resistance In abrasive environments, materials with high wear resistance, such as alloy steel or ceramic coatings, are necessary to withstand the harsh conditions and extend the shaft’s service life.
- Cost Cost is always a significant factor in material selection. While high-performance materials like carbon fiber and alloy steel offer excellent properties, they can be expensive. Balancing performance and cost is crucial for selecting the most suitable material for the application.
The materials used in conveyor belt shaft manufacturing play a vital role in determining the performance, durability, and suitability of the conveyor system for various applications. By carefully considering factors such as load capacity, corrosion resistance, weight, wear resistance, and cost, engineers can select the most appropriate material to meet the specific needs of the conveyor system.
Signs Indicating the Need for Conveyor Belt Shaft Replacement
Regular maintenance and inspection of conveyor belt shafts are essential to ensure the smooth operation of conveyor systems. Over time, shafts may experience wear and tear, leading to potential failures if not addressed promptly. Recognizing the signs that indicate the need for conveyor belt shaft replacement is crucial for preventing downtime and costly repairs.
Excessive Wear and Tear
One of the most apparent signs that a conveyor belt shaft needs replacement is excessive wear and tear. This can manifest in several ways, including:
- Surface Degradation The surface of the conveyor belt shaft may show visible signs of wear, such as grooves, scratches, or pitting. These defects can reduce the shaft’s effectiveness in transmitting power and may lead to further damage to the conveyor system components.
- Reduced Diameter Over time, continuous operation can lead to a reduction in the shaft’s diameter due to abrasion and friction. A noticeable decrease in diameter can compromise the shaft’s structural integrity and load-bearing capacity, necessitating replacement.
- Cracks and Fractures Cracks or fractures in the conveyor belt shaft are serious indicators of impending failure. These can occur due to excessive stress, impact, or fatigue. Regular inspections should include checking for any signs of cracking, particularly around key stress points.
Unusual Noises
Unusual noises coming from the conveyor system can be an early warning sign of shaft issues. These noises may include grinding, squealing, or clunking sounds, which can indicate misalignment, bearing failure, or excessive wear on the shaft. Investigating and addressing these noises promptly can prevent further damage and system downtime.
Vibration and Misalignment
Increased vibration and misalignment are common signs that a conveyor belt shaft may need replacement. Vibration can be caused by several factors, including:
- Imbalance An imbalanced shaft can cause significant vibration during operation. This can result from uneven wear, material buildup, or damage to the shaft. Imbalance not only affects the performance of the conveyor system but can also lead to accelerated wear on other components.
- Misalignment Misalignment of the conveyor belt shaft can occur due to improper installation, wear, or deformation. Misaligned shafts can cause increased friction, leading to excessive wear and potential failure. Regular alignment checks are essential to ensure the shaft operates smoothly and efficiently.
Overheating
Overheating is another sign that a conveyor belt shaft may need replacement. Overheating can occur due to excessive friction, inadequate lubrication, or bearing failure. If the shaft becomes too hot during operation, it can lead to thermal expansion, weakening the material and potentially causing deformation or failure. Monitoring the temperature of the shaft and addressing any overheating issues promptly can prevent damage and extend the shaft’s lifespan.
Reduced Performance
A noticeable decline in the performance of the conveyor system can indicate issues with the conveyor belt shaft. Reduced performance may manifest as:
- Decreased Speed If the conveyor system is operating at a slower speed than usual, it may be due to increased resistance or wear on the shaft. This can affect the overall efficiency and productivity of the system.
- Increased Power Consumption A worn or damaged shaft can cause the conveyor system to require more power to operate, leading to higher energy costs. Monitoring power consumption and identifying any significant increases can help detect issues with the shaft.
Lubrication Issues
Proper lubrication is essential for the smooth operation of conveyor belt shafts. Lubrication issues can indicate the need for shaft replacement, including:
- Inadequate Lubrication If the shaft is not receiving adequate lubrication, it can lead to increased friction and wear. This can be caused by a malfunctioning lubrication system or blockages that prevent lubricant from reaching the shaft.
- Contaminated Lubrication Contaminants such as dirt, debris, or moisture in the lubrication system can cause damage to the shaft and bearings. Regularly checking and maintaining the lubrication system can prevent these issues and prolong the shaft’s lifespan.
Bearing Failure
Bearing failure is a significant indicator that a conveyor belt shaft may need replacement. Bearings support the shaft and allow it to rotate smoothly. Signs of bearing failure include:
- Noise As mentioned earlier, unusual noises can indicate bearing issues. Grinding or squealing sounds often suggest that the bearings are worn or damaged.
- Excessive Play Excessive play or movement in the shaft can indicate that the bearings are no longer providing adequate support. This can lead to misalignment and increased wear on the shaft.
- Heat Overheating bearings can cause the shaft to overheat as well. Monitoring the temperature of both the shaft and bearings can help detect issues early.
Visual Inspection and Regular Maintenance
Conducting regular visual inspections and maintenance is crucial for identifying signs of wear and tear on conveyor belt shafts. During inspections, look for:
- Surface Damage Check for any visible signs of damage, such as cracks, grooves, or wear on the shaft’s surface.
- Alignment Ensure that the shaft is properly aligned and that there are no signs of misalignment.
- Lubrication Verify that the shaft is receiving adequate lubrication and that the lubrication system is functioning correctly.
- Bearings Inspect the bearings for any signs of wear, noise, or excessive play.
By performing regular inspections and maintenance, operators can detect issues early and take corrective action before the shaft fails, preventing costly downtime and repairs.
Recognizing the signs indicating the need for conveyor belt shaft replacement is essential for maintaining the efficiency and reliability of conveyor systems. Excessive wear and tear, unusual noises, vibration and misalignment, overheating, reduced performance, lubrication issues, and bearing failure are all critical indicators that the shaft may need replacement. Regular visual inspections and maintenance can help detect these issues early, allowing operators to take corrective action and ensure the continued smooth operation of the conveyor system.
Steps to Perform Conveyor Belt Shaft Replacement
Replacing a conveyor belt shaft is a critical maintenance task that ensures the smooth operation of your conveyor system. The process can be intricate, requiring meticulous attention to detail to ensure safety and efficiency. Here, we provide a comprehensive step-by-step guide on how to replace a conveyor belt shaft effectively and safely.
Step 1: Prepare the Necessary Tools and Equipment
Before starting the replacement process, gather all the necessary tools and equipment. These typically include:
- Safety gear (gloves, goggles, helmets)
- Wrenches and sockets
- Bearing pullers
- Hydraulic jacks
- Alignment tools
- Replacement shaft
- Lubricants and cleaning agents
Having all tools on hand will minimize downtime and ensure a smoother replacement process.
Step 2: Ensure Safety Measures
Safety is paramount when performing maintenance on heavy machinery. Follow these safety measures:
- Shut down the conveyor system and disconnect it from any power source.
- Lockout and tagout the system to prevent accidental reactivation.
- Ensure the work area is clean and free from obstructions.
- Wear appropriate personal protective equipment (PPE).
Step 3: Remove the Conveyor Belt
To access the conveyor belt shaft, the conveyor belt must be removed. This involves:
- Loosening the tension on the conveyor belt by adjusting the tensioning system.
- Carefully lifting the belt off the pulleys and rollers.
- Using appropriate lifting tools to support the belt during removal to prevent damage.
Step 4: Disconnect the Shaft Components
Once the conveyor belt is removed, the next step is to disconnect the components attached to the conveyor belt shaft. These components typically include:
- Bearings
- Sprockets or pulleys
- Gearboxes or motors
Use bearing pullers and wrenches to carefully remove these components, taking care not to damage them, as they may be reused.
Step 5: Remove the Old Shaft
With all components disconnected, you can now remove the old shaft. Depending on the size and weight of the shaft, you may need hydraulic jacks or other lifting equipment. Carefully slide the shaft out of its housing, ensuring you do not damage the surrounding structure.
Step 6: Clean and Inspect the Shaft Housing
Before installing the new shaft, thoroughly clean the shaft housing and inspect it for any signs of wear or damage. Use appropriate cleaning agents to remove any debris, and check for cracks or deformations that could affect the new shaft’s performance.
Step 7: Install the New Shaft
Align the new conveyor belt shaft with the housing and carefully slide it into place. Ensure the shaft is properly seated and aligned to prevent any operational issues. Use alignment tools to check the shaft’s position and make necessary adjustments.
Step 8: Reattach the Shaft Components
Reattach the bearings, sprockets, pulleys, and any other components removed earlier. Ensure each component is securely fastened and properly aligned. Apply lubricants as needed to ensure smooth operation.
Step 9: Reinstall the Conveyor Belt
Once the shaft and its components are securely in place, reinstall the conveyor belt. Ensure the belt is properly aligned and tensioned according to the manufacturer’s specifications. Carefully adjust the tensioning system to achieve the correct belt tension.
Step 10: Test the Conveyor System
Before resuming normal operations, perform a thorough test of the conveyor system. Check for any unusual noises, vibrations, or misalignments. Run the conveyor at different speeds to ensure it operates smoothly and efficiently. Make any necessary adjustments to achieve optimal performance.
Step 11: Document the Replacement Process
Finally, document the entire replacement process, including any issues encountered and the solutions implemented. This documentation will be valuable for future maintenance and troubleshooting.
Maintenance Tips for Conveyor Belt Shaft Longevity
Maintaining the longevity of your conveyor belt shaft is crucial for ensuring the overall efficiency and reliability of your conveyor system. Regular maintenance can prevent costly breakdowns and extend the lifespan of your equipment. Here are some practical tips and best practices for maintaining conveyor belt shafts:
Regular Inspection

Conduct regular inspections of the conveyor belt shaft and its components. Look for signs of wear, misalignment, and lubrication issues. Early detection of potential problems can prevent more significant issues down the line.
Proper Lubrication
Lubrication is vital for reducing friction and wear on the conveyor belt shaft and its bearings. Use the manufacturer’s recommended lubricants and follow the specified lubrication schedule. Over-lubrication or under-lubrication can both cause problems, so ensure the correct amount is applied.
Alignment Checks
Misalignment of the conveyor belt shaft can lead to increased wear and tear. Regularly check the alignment of the shaft and adjust it as needed. Use precision alignment tools to ensure accuracy.
Monitor Vibration Levels
Excessive vibration can indicate problems with the conveyor belt shaft or its components. Use vibration monitoring tools to track vibration levels and identify any abnormalities. Address any issues promptly to prevent further damage.
Temperature Monitoring
Monitor the operating temperature of the conveyor belt shaft and its bearings. Overheating can indicate lubrication issues or excessive load. Install temperature sensors to track temperature levels and take corrective action if necessary.
Load Management
Ensure the conveyor system is not overloaded. Excessive load can strain the conveyor belt shaft and lead to premature failure. Regularly check the load capacity and distribute the load evenly across the conveyor.
Cleaning and Debris Removal
Keep the conveyor system clean and free from debris. Accumulated dirt and debris can cause damage to the conveyor belt shaft and its components. Regularly clean the system and remove any obstructions.
Regular Maintenance Schedule
Establish a regular maintenance schedule and adhere to it. Routine maintenance tasks, such as lubrication, alignment checks, and component inspections, should be performed according to the manufacturer’s recommendations.
Staff Training
Ensure that all personnel involved in the maintenance and operation of the conveyor system are properly trained. Training should cover safety procedures, maintenance tasks, and the correct use of tools and equipment.
Use Quality Replacement Parts
When replacing components of the conveyor belt shaft, use high-quality replacement parts from reputable suppliers. Inferior parts can lead to premature failure and reduced performance.
Documentation and Record-Keeping
Maintain detailed records of all maintenance activities, including inspections, repairs, and replacements. Documentation helps track the condition of the conveyor belt shaft and aids in troubleshooting future issues.
Preventive Maintenance Programs
Implement preventive maintenance programs to address potential issues before they lead to failures. Regularly review and update the maintenance schedule based on the condition and performance of the conveyor system.
Choosing the Right Conveyor Belt Shaft for Your System
Selecting the appropriate conveyor belt shaft is crucial for ensuring the efficient operation of your conveyor system. Various factors need to be considered to match the shaft to the specific requirements of your application. Here are the key factors to consider when choosing the right conveyor belt shaft:
Load Capacity
The load capacity of the conveyor belt shaft must match the demands of your application. Consider the maximum load the shaft will need to handle and select a shaft with adequate strength and durability. Overloading the shaft can lead to premature failure and operational inefficiencies.
Material and Construction

The material and construction of the conveyor belt shaft are critical for its performance and longevity. Common materials include steel, stainless steel roller, and aluminum. The choice of material depends on factors such as:
- Corrosion resistance
- Wear resistance
- Weight considerations
- Operating environment
For applications in harsh or corrosive environments, stainless steel shafts may be preferred for their durability and resistance to corrosion.
Shaft Diameter and Length
The diameter and length of the conveyor belt shaft must be compatible with the conveyor system’s design. The shaft should fit precisely within the bearings and other components. Incorrect shaft dimensions can lead to alignment issues and operational problems.
Bearing Compatibility
Ensure the conveyor belt shaft is compatible with the bearings used in the conveyor system. The shaft and bearings must work together seamlessly to provide smooth and efficient operation. Consider the bearing type, size, and load capacity when selecting the shaft.
Environmental Conditions
The operating environment plays a significant role in shaft selection. Consider factors such as:
- Temperature extremes
- Exposure to moisture or chemicals
- Dust and debris levels
Choose a conveyor belt shaft that can withstand the specific environmental conditions of your application.
Alignment and Tolerances
Precision alignment and tight tolerances are essential for the smooth operation of the conveyor belt shaft. Ensure the shaft meets the required alignment specifications and tolerances to prevent excessive wear and operational issues.
Speed and Torque Requirements
Consider the speed and torque requirements of the conveyor belt system. The conveyor belt shaft must be capable of handling the desired speed and torque without compromising performance. Select a shaft that can accommodate the system’s operating parameters.
Maintenance and Replacement
Ease of maintenance and replacement is another important consideration. Choose a conveyor belt shaft that is easy to install, maintain, and replace. This can help minimize downtime and reduce maintenance costs.
Cost and Budget
While quality is paramount, cost is also a factor. Balance the need for a high-quality conveyor belt shaft with your budget constraints. Investing in a durable and reliable shaft can save money in the long run by reducing maintenance and replacement costs.
Manufacturer Support and Warranty
Choose a conveyor belt shaft from a reputable manufacturer that offers strong support and a comprehensive warranty. Manufacturer support can be invaluable for troubleshooting issues and ensuring the long-term performance of the shaft.
Industry Standards and Compliance
Ensure the conveyor belt shaft complies with industry standards and regulations. Compliance with standards ensures the shaft meets the required safety and performance criteria.
Application-Specific Requirements
Consider any specific requirements of your application that may impact the choice of conveyor belt shaft. For example, food processing applications may require shafts that meet hygiene standards, while heavy industrial applications may require shafts with high load-bearing capabilities.
By carefully considering these factors, you can select the right conveyor belt shaft for your system, ensuring optimal performance, longevity, and reliability.
FAQs about Conveyor Belt Shaft
A shaft on a conveyor belt is a cylindrical component that supports and drives the conveyor belt. It connects to the conveyor’s drive system, which includes motors and gears, to transfer rotational power. The shaft ensures the smooth movement of the belt and can be located at different points along the conveyor system, typically at the drive and tail ends. It is a crucial part of the conveyor’s operation, providing stability and direction to the belt as it transports materials from one point to another.
A conveyor belt system consists of several key parts:
Belt: The flexible, continuous loop that carries materials.
Pulleys: Wheels on either end of the belt that help it move.
Rollers: Cylindrical components that support the belt and its load.
Motor: Provides the power to move the belt.
Shaft: Cylindrical component that transfers rotational power from the motor to the belt.
Frame: The structure that supports the entire system.
Idlers: Support the belt and reduce friction.
Drive Unit: Comprises the motor, gear reduction, and belt drive.
Take-up: Adjusts the belt tension to maintain proper alignment and tension. Each of these parts works together to ensure efficient and effective material handling.
Conveyor shafts are typically made from durable materials such as steel, stainless steel, or aluminum. The choice of material depends on the application and the environment in which the conveyor operates. For example, stainless steel shafts are used in food processing or pharmaceutical industries due to their corrosion resistance and hygienic properties. Steel is commonly used for heavy-duty applications because of its strength and durability. Aluminum shafts are lighter and used in applications where weight reduction is important.
The end of a conveyor belt can be referred to as the “discharge end” or “tail end.” The discharge end is where the materials are unloaded from the belt, typically into another conveyor system or directly into a designated area for further processing or packaging. The tail end, on the other hand, is where the belt returns and usually houses the tail pulley, which helps in redirecting the belt back into the loop. This end is crucial for maintaining belt tension and alignment, ensuring the smooth operation of the conveyor system.
To join a broken conveyor belt, follow these detailed steps:
1. Identify the Type of Belt and Damage
Material: Determine if the belt is made of rubber, PVC, or other materials.
Damage: Assess the extent and type of damage (e.g., clean cut, tear, or hole).
2. Gather Necessary Tools and Materials
Tools: Belt cutter, belt skiver, belt clamps, measuring tape, straight edge, and a heat gun (if using a thermoplastic belt).
Materials: New belt section (if needed), belt fasteners (e.g., mechanical fasteners, vulcanizing tools), adhesive (if applicable), and a repair kit.
3. Prepare the Belt Ends
Clean the Belt: Ensure the belt ends are clean and free of debris.
Cut Straight Ends: Use a belt cutter or sharp knife to make clean, straight cuts on both ends of the belt. This is crucial for a seamless joint.
4. Choose the Joining Method
Mechanical Fasteners: Suitable for quick repairs and belts under lower tension.
Vulcanizing: Offers a strong, permanent bond for higher tension belts and requires special equipment.
Cold Bonding: Uses adhesives for belts that cannot be vulcanized.
5. Mechanical Fastening
Align the Belt Ends: Clamp the belt ends together ensuring they are properly aligned.
Install Fasteners: Insert fasteners across the belt ends. Follow the manufacturer’s instructions for spacing and securing the fasteners.
6. Vulcanizing
Skive the Belt Ends: Use a skiver to bevel the belt ends to ensure a smooth overlap.
Apply Vulcanizing Solution: Coat the skived ends with a vulcanizing solution and let it dry as per the manufacturer’s instructions.
Heat and Pressure: Use a vulcanizing press to apply heat and pressure, ensuring a strong bond. Follow specific temperature and pressure settings for the belt material.
7. Cold Bonding
Prepare the Adhesive: Mix the adhesive as per the manufacturer’s guidelines.
Apply Adhesive: Coat both ends of the belt with the adhesive and allow it to become tacky.
Join the Ends: Press the ends together, ensuring proper alignment, and apply even pressure until the adhesive sets.
8. Inspect and Test the Repair
Visual Inspection: Check the joint for alignment and secure fastening.
Run the Conveyor: Test the conveyor belt at a slow speed to ensure the joint holds under load.
Adjust if Necessary: Make any required adjustments to ensure smooth operation.
9. Maintenance and Monitoring
Regular Checks: Frequently inspect the repaired joint for any signs of wear or damage.
Routine Maintenance: Maintain the conveyor system to prevent future belt issues.
By following these steps, you can effectively join a broken conveyor belt, ensuring minimal downtime and maintaining the efficiency of your conveyor system.
Last Updated on August 9, 2024 by Jordan Smith
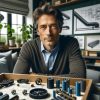
Jordan Smith, a seasoned professional with over 20 years of experience in the conveyor system industry. Jordan’s expertise lies in providing comprehensive solutions for conveyor rollers, belts, and accessories, catering to a wide range of industrial needs. From initial design and configuration to installation and meticulous troubleshooting, Jordan is adept at handling all aspects of conveyor system management. Whether you’re looking to upgrade your production line with efficient conveyor belts, require custom conveyor rollers for specific operations, or need expert advice on selecting the right conveyor accessories for your facility, Jordan is your reliable consultant. For any inquiries or assistance with conveyor system optimization, Jordan is available to share his wealth of knowledge and experience. Feel free to reach out at any time for professional guidance on all matters related to conveyor rollers, belts, and accessories.