In-Depth Conveyor Belt Splicer Job Description Overview
Conveyor belt systems are vital components across a wide range of industries, including mining, manufacturing, and logistics. They play a crucial role in the efficient and safe transport of materials, contributing to streamlined operations and reduced downtime. Within this context, the conveyor belt splicer job description becomes essential. Conveyor belt splicers are responsible for installing, repairing, and maintaining these critical systems, ensuring they function smoothly. Their expertise not only minimizes operational disruptions but also enhances workplace safety. Understanding the conveyor belt splicer job description provides valuable insights into the skills and responsibilities required to excel in this indispensable role, highlighting its significance in industrial settings.
Conveyor Belt Splicer Job Description Overview
Definition of a Conveyor Belt Splicer
A conveyor belt splicer is a skilled technician responsible for the installation, repair, and maintenance of conveyor belt systems used in various industries. The primary role involves splicing, which is the process of joining two pieces of conveyor belt together. This task requires a high level of precision and expertise, as the integrity of the splice directly impacts the efficiency and safety of the conveyor system. The conveyor belt splicer job description includes tasks such as inspecting conveyor belts for damage, conducting regular maintenance, and performing emergency repairs to minimize downtime.
Key Responsibilities of a Conveyor Belt Splicer
The conveyor belt splicer job description outlines several key responsibilities that are essential to the role:
- Installation of Conveyor Belts: This involves setting up new conveyor belt systems, ensuring they are correctly aligned and tensioned for optimal performance. Splicers must be adept at using various tools and equipment to handle different types of belts and splicing methods.
- Repair and Maintenance: Regular inspection and maintenance are crucial to prevent breakdowns. Splicers must identify signs of wear and tear, such as frayed edges, tears, or misalignment, and take corrective actions promptly.
- Splicing Techniques: Splicers employ various splicing methods, including mechanical splicing, vulcanized splicing, and cold splicing. Each technique requires specific skills and tools. For example, vulcanized splicing involves using heat and pressure to create a seamless bond, which is ideal for high-stress environments.
- Safety Protocols: Adherence to safety standards is paramount. Splicers must follow OSHA and MSHA guidelines to ensure a safe working environment. This includes using personal protective equipment (PPE) and ensuring that all splicing work is conducted safely to prevent accidents.
Types of Environments for Conveyor Belt Splicers
Conveyor belt splicers work in a variety of environments, each with its unique challenges and requirements. The conveyor belt splicer jobs must reflect the adaptability needed to operate in different settings.
Mining Industry
In the mining industry, conveyor belt splicers play a critical role in maintaining the equipment that transports raw materials from the extraction site to processing facilities. These environments are often harsh, with exposure to dust, heavy loads, and abrasive materials. Splicers must be prepared to work in underground mines or open-pit mines, where the conditions can be demanding and require strict adherence to safety protocols.
Manufacturing Industry
In manufacturing settings, conveyor belts are used to move products through various stages of production. Here, splicers ensure that the belts are functioning correctly to avoid any disruptions in the production line. This environment often requires precision and speed, as any downtime can result in significant production losses. The conveyor belt splicer job description for this setting emphasizes the need for quick and efficient problem-solving skills.
Industrial Settings
Other industrial settings, such as warehouses and distribution centers, rely heavily on conveyor belt systems for material handling and logistics. Splicers in these environments must ensure that the belts are capable of handling a variety of goods, from lightweight packages to heavy pallets. The work often involves routine inspections and preventative maintenance to keep the systems running smoothly.
Examples of Specific Environments
To further illustrate the diverse environments where conveyor belt splicers work,
- Underground Mines: Conveyor belt splicers in underground mines must deal with confined spaces, low lighting, and the constant movement of heavy machinery. They must be adept at handling emergency repairs and ensuring that the belts can withstand the harsh conditions.
- Automotive Manufacturing Plants: In these facilities, conveyor belts are crucial for moving car parts and assemblies through various production stages. Splicers must ensure that the belts are precisely aligned and tensioned to prevent any production delays.
- Food Processing Plants: Conveyor belts in food processing plants must meet stringent hygiene standards. Splicers in this environment need to use materials and techniques that prevent contamination and ensure easy cleaning and maintenance.
The conveyor belt splicer job description encompasses a wide range of responsibilities and skills, making it a critical role in many industries. From ensuring the smooth operation of conveyor belts in mining and manufacturing to maintaining high standards in food processing, splicers must be versatile and skilled technicians. Understanding the detailed job description helps highlight the importance of their work and the diverse environments they operate in, showcasing the essential role they play in maintaining operational efficiency and safety across various industrial settings.
Detailed Job Responsibilities in Conveyor Belt Splicer Job Description
Installation, Repair, and Maintenance of Conveyor Belts and Systems
The conveyor belt splicer job description entails a variety of detailed responsibilities that ensure the smooth operation of conveyor systems across different industries. At the core of the role is the installation, repair, and maintenance of conveyor belts. This involves setting up new conveyor systems, aligning and tensioning belts for optimal performance, and ensuring that all components are securely in place.
Installation: During the installation phase, splicers must read and interpret blueprints and technical drawings to understand the layout and specifications of the conveyor system. They use tools such as belt cutters, presses, and vulcanizers to splice belts and create strong, durable joints. Precision in measurements and alignment is crucial to prevent misalignment and ensure efficient operation.
Repair: When conveyor belts break down or suffer damage, splicers must quickly diagnose the issue and perform repairs to minimize downtime. This includes identifying wear and tear, such as frayed edges, cuts, or abrasions, and using the appropriate splicing technique to fix the problem. Repairs may also involve replacing damaged sections of the belt or components like rollers and pulleys.
Maintenance: Regular maintenance is vital to extend the lifespan of conveyor belts and prevent unexpected breakdowns. Splicers conduct routine inspections to check for signs of wear and perform preventative maintenance tasks, such as cleaning and lubricating moving parts, adjusting tension, and replacing worn components. Maintenance schedules are often dictated by the operating conditions and usage frequency of the conveyor system.
Techniques in Conveyor Belt Splicing: Lap Splice, Finger Splice, and Cable Belt Splice
The conveyor belt splicer job description includes mastering various splicing techniques to join belt ends effectively. Each technique is suited to specific types of belts and operational demands:
Lap Splice: This is one of the simplest and most common splicing methods, where the ends of the belt are overlapped and joined using adhesives, vulcanizing agents, or mechanical fasteners. It is suitable for belts that do not operate under high stress or heavy loads.
Finger Splice: This technique involves cutting the belt ends into a series of fingers, which are then interlaced and bonded together. The finger splice provides a strong, flexible joint that is ideal for high-tension applications. It distributes stress more evenly across the splice, reducing the risk of failure.
Cable Belt Splice: Used for belts that contain steel cables or cords, the cable belt splice involves stripping the cover and exposing the cables, which are then connected using specialized splicing materials. This method is highly durable and suitable for heavy-duty applications, such as in mining or large-scale manufacturing operations.
Roles in Refurbishment: Pulley Lagging, Basic Rigging, and Lifting
Another significant aspect of the conveyor belt splicer job description is the role in refurbishing conveyor systems. This includes tasks like pulley lagging, which involves covering the pulley surfaces with materials like rubber or ceramic to increase friction and extend the life of the pulleys. Proper lagging ensures better grip and reduces belt slippage, enhancing overall system efficiency.
Basic Rigging and Lifting: Splicers often work with heavy equipment and must perform basic rigging and lifting tasks to move conveyor components into place. This requires knowledge of safe lifting techniques and the use of rigging equipment like cranes, hoists, and slings. Ensuring that all components are correctly positioned and secured is crucial to the stability and safety of the conveyor system.
Importance of Safety Protocols and Adherence to OSHA and MSHA Standards
Safety is paramount in the conveyor belt splicer job description. Splicers must adhere to strict safety protocols to protect themselves and their colleagues from accidents and injuries. This includes following Occupational Safety and Health Administration (OSHA) and Mine Safety and Health Administration (MSHA) standards, which set guidelines for safe work practices in industrial and mining environments.
- Personal Protective Equipment (PPE): Splicers must wear appropriate PPE, such as hard hats, safety glasses, gloves, and steel-toed boots, to protect against injuries from moving parts, falling objects, and hazardous materials.
- Lockout/Tagout (LOTO) Procedures: Before performing maintenance or repairs, splicers must follow LOTO procedures to ensure that the conveyor system is de-energized and cannot be accidentally restarted. This prevents accidental injuries from unexpected movement.
- Hazard Communication: Proper labeling and communication of hazardous materials and conditions are essential. Splicers must be aware of the potential dangers associated with the chemicals and equipment they use and ensure that safety data sheets (SDS) are accessible.
- Fall Protection: In environments where work is performed at heights, splicers must use fall protection equipment, such as harnesses and lanyards, and follow protocols to prevent falls and related injuries.
- Emergency Response Training: Splicers should be trained in emergency response procedures, including first aid and the use of fire extinguishers, to effectively handle accidents or incidents that may occur on the job.
By incorporating these safety measures into their daily routines, conveyor belt splicers can significantly reduce the risk of workplace injuries and ensure a safer working environment for everyone involved. The comprehensive understanding and adherence to these responsibilities and safety protocols underscore the importance of the conveyor belt splicer job description in maintaining operational efficiency and safety in various industrial settings.
Skills and Requirements for Conveyor Belt Splicer Job Description
Required Technical Skills
The conveyor belt splicer job description emphasizes several technical skills crucial for performing the role effectively. A splicer must possess a strong mechanical aptitude and proficiency with various splicing tools and equipment.
- Mechanical Aptitude: Understanding the mechanics of conveyor systems and how different components interact is essential. Splicers must be able to troubleshoot and resolve mechanical issues quickly.
- Proficiency with Splicing Tools: Splicers need to be skilled in using tools such as belt cutters, presses, vulcanizers, and splicing kits. These tools are vital for creating strong, reliable splices.
- Understanding of Splicing Techniques: Knowledge of different splicing methods, including lap splices, finger splices, and cable belt splices, is crucial. Each technique requires specific skills and precision to ensure the durability of the splice.
- Knowledge of Materials: Splicers must understand the properties of various conveyor belt materials, such as rubber, PVC, and steel cords, to choose the appropriate splicing method and materials.
- Equipment Maintenance: Regular maintenance of splicing tools and equipment is necessary to ensure they function correctly and safely. Splicers need to be adept at performing routine checks and repairs on their tools.
Necessary Certifications and Training
Certifications and training are crucial components of the conveyor belt splicer job description. These credentials ensure that splicers have the necessary knowledge and skills to perform their duties safely and effectively. Some key certifications and training programs include:
- Conveyor Belt Splicing Certification: Many industries require splicers to have a formal certification in conveyor belt splicing. This certification often involves coursework and hands-on training in various splicing techniques and safety protocols.
- Technical Training Programs: Splicers can benefit from technical training programs offered by manufacturers and industry organizations. These programs cover the latest splicing technologies, equipment, and industry best practices.
- OSHA Training: Splicers must complete Occupational Safety and Health Administration (OSHA) training to understand workplace safety standards and regulations. This training helps them recognize and mitigate potential hazards on the job.
- MSHA Certification: For those working in the mining industry, Mine Safety and Health Administration (MSHA) certification is required. This training focuses on safety practices specific to mining environments.
- First Aid and CPR Certification: Having first aid and CPR certification is beneficial, as it prepares splicers to respond to medical emergencies that may occur on the job.
Experience Needs
The experience requirements for conveyor belt splicers can vary depending on the complexity of the job and the specific industry. The conveyor belt splicer job description outlines different levels of experience needed:
- Entry-Level Positions: Entry-level splicers typically require basic knowledge of mechanical systems and some hands-on experience with tools and equipment. They often work under the supervision of more experienced splicers and gradually take on more complex tasks.
- Intermediate Positions: Splicers with a few years of experience can take on more responsibilities, such as leading splicing projects, performing advanced splicing techniques, and training junior splicers.
- Advanced Positions: Experienced splicers with extensive knowledge of conveyor systems and splicing methods are often sought after for supervisory or managerial roles. They oversee large projects, ensure adherence to safety standards, and provide expert guidance to their teams.
- Industry-Specific Experience: Some industries, like mining or manufacturing, may require splicers to have specific experience relevant to their unique environments. This includes understanding industry-specific safety protocols and equipment.
- Continual Learning: Splicers must stay updated on the latest advancements in splicing technology and industry practices. Continuous education and training are essential to maintaining expertise and improving job performance.
Soft Skills
In addition to technical skills and experience, the conveyor belt splicer job description highlights several soft skills that are crucial for success in this role. These skills enable splicers to work effectively in various environments and collaborate with others.
- Communication: Clear and effective communication is essential for coordinating with team members, supervisors, and clients. Splicers must be able to convey technical information and safety protocols accurately.
- Teamwork: Splicing often involves working in teams, and the ability to collaborate and support colleagues is vital. Teamwork ensures that tasks are completed efficiently and safely.
- Adaptability: Conveyor belt splicers must be adaptable to varying work schedules, environments, and challenges. This includes being flexible with shifts and able to work in different industrial settings.
- Problem-Solving: Splicers need strong problem-solving skills to diagnose issues with conveyor belts and determine the best solutions. This involves critical thinking and the ability to make quick, informed decisions.
- Attention to Detail: Precision and accuracy are crucial in splicing work. Splicers must pay close attention to details to ensure that splices are performed correctly and that all safety standards are met.
By possessing these technical skills, certifications, experience, and soft skills, conveyor belt splicers can excel in their roles and contribute significantly to the efficiency and safety of conveyor systems across various industries. The comprehensive understanding of these skills and requirements as outlined in the conveyor belt splicer job description highlights the importance of this role in maintaining the smooth operation of industrial processes.
Machines and Technology in Conveyor Belt Splicer Job Description
Belt Splicing Machines and the Role of Technology
The conveyor belt splicer job description includes a comprehensive understanding of the machines and technologies used in the splicing process. Conveyor belt splicing machines are specialized equipment designed to join the ends of conveyor belts. These machines play a critical role in ensuring that splices are strong, durable, and capable of withstanding the operational demands of various industries.
Types of Belt Splicing Machines
- Vulcanizing Presses: Vulcanizing presses use heat and pressure to splice conveyor belts. This process involves placing the belt ends between heated platens, which melt the splice materials and create a seamless bond. Vulcanizing presses are known for producing strong, reliable splices that are suitable for heavy-duty applications.
- Mechanical Fasteners: These machines use metal or plastic fasteners to join belt ends. Mechanical fasteners are quick to install and ideal for temporary repairs or applications where belts are frequently replaced. While not as strong as vulcanized splices, they offer flexibility and ease of installation.
- Cold Splicing Kits: Cold splicing involves using adhesives to bond belt ends without heat. These kits include special glues and bonding agents that create a strong splice at room temperature. Cold splicing is advantageous in environments where heat is not practical or could damage the belt material.
- Finger Splicing Machines: Finger splicing machines cut the belt ends into a series of fingers, which are then interlaced and bonded. This method provides a strong, flexible joint that distributes stress evenly. Finger splicing machines are used for high-tension belts that require precision splicing.
- Portable Splicing Machines: These lightweight, compact machines are designed for on-site splicing. Portable splicing machines are ideal for use in remote locations or where mobility is essential. They offer convenience and efficiency, allowing splicers to perform repairs quickly and effectively.
Role of Technology in Conveyor Belt Maintenance and Repair
Technology plays a pivotal role in the conveyor belt splicer job description, enhancing the efficiency and accuracy of maintenance and repair tasks. Advanced technologies enable splicers to perform their duties with greater precision, improving the overall performance and longevity of conveyor systems.
Technological Advancements:
- Automated Splicing Systems: Automated systems streamline the splicing process by reducing manual labor and ensuring consistent, high-quality splices. These systems use sensors and computer controls to monitor and adjust parameters, such as temperature and pressure, during the splicing process.
- Laser Alignment Tools: Proper alignment is crucial for conveyor belt performance. Laser alignment tools provide precise measurements and ensure that belts are correctly aligned and tensioned. These tools help prevent misalignment, reducing wear and tear on the belt and associated components.
- Ultrasonic Testing Equipment: Ultrasonic testing is a non-destructive method used to detect flaws or weaknesses in conveyor belts. This technology uses high-frequency sound waves to identify issues, allowing splicers to perform targeted repairs and prevent potential failures.
- Digital Inspection Systems: Digital inspection systems use cameras and imaging software to monitor the condition of conveyor belts. These systems can detect damage, wear, and other issues in real-time, enabling proactive maintenance and reducing the risk of unexpected breakdowns.
- Remote Monitoring and Diagnostics: Remote monitoring systems use sensors and IoT technology to collect data on conveyor belt performance. This data is transmitted to a central system, where it can be analyzed to identify trends and potential issues. Remote diagnostics allow splicers to address problems before they escalate, minimizing downtime and improving efficiency.
Advancements in Conveyor Belt Splicing Techniques and Equipment
The conveyor belt splicer job description also includes staying updated on the latest advancements in splicing techniques and equipment. Continuous improvements in these areas enhance the reliability and efficiency of conveyor systems.
- Improved Splicing Materials: New materials, such as high-strength adhesives and advanced bonding agents, provide stronger, more durable splices. These materials are designed to withstand extreme conditions, such as high temperatures and heavy loads, improving the longevity of the splice.
- Enhanced Vulcanizing Equipment: Modern vulcanizing presses feature advanced controls and automation, ensuring precise temperature and pressure settings. These enhancements lead to more consistent splices and reduce the risk of human error.
- Modular Splicing Systems: Modular systems offer flexibility and scalability, allowing splicers to adapt their equipment to different belt sizes and types. These systems are easy to transport and set up, making them ideal for on-site repairs.
- Quick-Change Tools: Tools designed for rapid setup and adjustment streamline the splicing process, reducing downtime and improving efficiency. Quick-change tools allow splicers to switch between different splicing methods and materials with ease.
- Eco-Friendly Technologies: Advances in eco-friendly splicing technologies focus on reducing the environmental impact of the splicing process. These technologies include low-emission vulcanizing presses and biodegradable adhesives, contributing to sustainable maintenance practices.
By incorporating these advanced machines and technologies, conveyor belt splicers can perform their duties more efficiently and effectively. Understanding the detailed role of technology in the conveyor belt splicer job description highlights the importance of staying current with industry advancements to maintain optimal conveyor system performance.
Training and Career Development in Conveyor Belt Splicer Job Description
Importance of Formal Training Programs for Conveyor Technicians
Formal training programs are crucial for anyone pursuing a career as a conveyor belt splicer. These programs provide the foundational knowledge and hands-on experience necessary to perform the job effectively and safely.
- Basic Splicing Techniques Course: This program covers the fundamental splicing methods, including mechanical, cold, and hot vulcanizing splicing techniques. Participants learn how to properly prepare and join belt ends, ensuring strong and durable splices.
- Advanced Conveyor Belt Maintenance: This course focuses on in-depth maintenance procedures for conveyor systems. It includes training on troubleshooting common issues, preventive maintenance practices, and advanced repair techniques.
- Safety and Compliance Training: Ensuring safety is a top priority for conveyor belt splicers. Safety and compliance training programs, such as OSHA and MSHA certifications, teach technicians how to adhere to safety regulations and implement best practices to prevent workplace accidents.
- Specialized Equipment Training: Conveyor belt splicers often use specialized tools and equipment. Training programs that focus on the operation and maintenance of these tools, such as vulcanizing presses and laser alignment devices, are essential for efficient and accurate splicing work.
- Technology Integration in Splicing: With the advancement of technology, training programs that cover the integration of digital tools and automated systems in splicing processes are increasingly important. These programs teach technicians how to use technology to enhance their efficiency and precision.
Pathways for Career Advancement Within the Field of Conveyor Belt Maintenance and Repair
The conveyor belt splicer job description not only includes performing splicing tasks but also offers numerous opportunities for career advancement. As splicers gain experience and expertise, they can pursue various pathways to progress in their careers:
- Senior Splicer or Lead Technician: Experienced splicers can advance to senior or lead technician roles, where they oversee splicing projects, mentor junior technicians, and ensure the quality of splicing work. These roles often come with increased responsibilities and higher salaries.
- Specialization in Advanced Techniques: Technicians who specialize in advanced splicing techniques, such as finger splicing or cable belt splicing, can become experts in their field. Specialization can lead to roles that focus on complex projects and challenging environments.
- Maintenance Supervisor or Manager: With extensive experience in conveyor belt maintenance, splicers can move into supervisory or managerial positions. These roles involve overseeing maintenance teams, managing schedules, and ensuring that all maintenance activities adhere to safety and quality standards.
- Technical Trainer or Instructor: Skilled splicers with a passion for teaching can transition into roles as technical trainers or instructors. They can work for training institutions or within their own companies to educate new technicians on splicing techniques and best practices.
- Field Service Engineer: Technicians with a strong understanding of conveyor systems and splicing can become field service engineers, providing on-site support and consultation for clients. This role often involves traveling to different locations to solve complex splicing and maintenance issues.
Resources for Ongoing Education and Skill Enhancement in Conveyor System Technologies
Continuous learning and skill enhancement are vital for conveyor belt splicers to stay updated with the latest technologies and industry practices. Several resources are available to support ongoing education and professional development:
- Online Courses and Webinars: Many educational institutions and industry organizations offer online courses and webinars on various aspects of conveyor belt splicing and maintenance. These resources provide flexibility for technicians to learn at their own pace and stay current with new developments.
- Industry Conferences and Workshops: Attending industry conferences and workshops allows splicers to network with peers, learn about the latest innovations, and participate in hands-on training sessions. These events are valuable for staying informed about industry trends and best practices.
- Manufacturer Training Programs: Conveyor belt and splicing equipment manufacturers often provide specialized training programs for their products. These programs ensure that technicians are proficient in using the latest tools and technologies specific to the manufacturer’s equipment.
- Professional Associations: Joining professional associations, such as the Conveyor Equipment Manufacturers Association (CEMA) or the International Society of Automation (ISA), provides access to a wealth of resources, including industry publications, training materials, and certification programs.
- Mentorship and On-the-Job Training: Learning from experienced colleagues through mentorship and on-the-job training is an invaluable resource for skill enhancement. Mentorship programs allow junior technicians to gain practical insights and knowledge from seasoned professionals.
By taking advantage of these training programs, career advancement pathways, and educational resources, conveyor belt splicers can continuously improve their skills and knowledge. The conveyor belt splicer job description highlights the importance of ongoing education and professional development to ensure that technicians are equipped to handle the evolving demands of the industry. This commitment to continuous improvement not only enhances individual career prospects but also contributes to the overall efficiency and safety of conveyor systems across various industries.
FAQs About Conveyor Belt Splicer Job Description
Splicing in a conveyor belt is the process of joining two pieces of conveyor belt to create a continuous loop. This is essential for ensuring the smooth operation of conveyor systems, which are widely used in industries such as mining, manufacturing, and logistics. There are several methods of splicing, including mechanical splicing, cold splicing, and hot vulcanizing splicing. Each method has its specific applications and benefits. Mechanical splicing uses metal or plastic fasteners to join the belt ends, offering a quick and easy solution. Cold splicing involves the use of adhesives to bond the belt ends without heat, making it suitable for environments where heat is impractical. Hot vulcanizing, on the other hand, uses heat and pressure to create a seamless bond, resulting in a strong and durable splice ideal for heavy-duty applications.
A conveyor technician is responsible for the installation, maintenance, and repair of conveyor systems used in various industries. Their job description includes inspecting conveyor belts for wear and tear, performing regular maintenance to ensure optimal performance, and conducting emergency repairs to minimize downtime. Conveyor technicians must have a strong understanding of mechanical systems and be proficient with tools and equipment used in splicing and maintaining conveyor belts. They also need to adhere to safety standards and protocols, such as those set by OSHA and MSHA, to ensure a safe working environment. Additionally, conveyor technicians often need to work in various industrial settings, from mining sites to manufacturing plants, requiring flexibility and adaptability. Effective communication and teamwork are also essential, as they frequently collaborate with other technicians and supervisors to ensure the smooth operation of conveyor systems.
Belt splicing can be a challenging job due to the technical skills and physical demands it requires. Splicers need to have a strong mechanical aptitude and be proficient with various splicing techniques, such as lap splicing, finger splicing, and cable belt splicing. The job often involves working in harsh industrial environments, such as mines or manufacturing plants, where conditions can be demanding. Additionally, splicing work requires precision and attention to detail to ensure that splices are strong and durable. Physical stamina is also important, as splicers may need to lift heavy equipment and work in confined spaces. Despite these challenges, many splicers find the job rewarding, as it plays a critical role in maintaining the efficiency and safety of conveyor systems. With proper training and experience, splicers can develop the skills needed to perform their duties effectively and advance their careers in the field of conveyor belt maintenance and repair.
The primary function of a conveyor belt is to transport materials from one point to another efficiently and safely. Conveyor belts are used in a wide range of industries, including mining, manufacturing, food processing, and logistics. They consist of a continuous loop of material, typically made of rubber, PVC, or metal, that moves over a series of rollers or pulleys. Conveyor belts can handle various types of materials, from bulk goods like coal and ore to packaged products and components in manufacturing processes. By automating the movement of materials, conveyor belts significantly improve productivity, reduce manual labor, and enhance workplace safety. They can be customized to meet specific operational requirements, such as handling heavy loads, operating at high speeds, or working in harsh environmental conditions. Overall, conveyor belts are a critical component in industrial operations, facilitating the efficient and reliable transport of materials.
Last Updated on June 5, 2024 by Jordan Smith
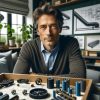
Jordan Smith, a seasoned professional with over 20 years of experience in the conveyor system industry. Jordan’s expertise lies in providing comprehensive solutions for conveyor rollers, belts, and accessories, catering to a wide range of industrial needs. From initial design and configuration to installation and meticulous troubleshooting, Jordan is adept at handling all aspects of conveyor system management. Whether you’re looking to upgrade your production line with efficient conveyor belts, require custom conveyor rollers for specific operations, or need expert advice on selecting the right conveyor accessories for your facility, Jordan is your reliable consultant. For any inquiries or assistance with conveyor system optimization, Jordan is available to share his wealth of knowledge and experience. Feel free to reach out at any time for professional guidance on all matters related to conveyor rollers, belts, and accessories.