Conveyor Belt Storage and Handing
Proper conveyor belt storage is crucial for maintaining the longevity and performance of your conveyor system. In this blog, we will discuss the importance of proper conveyor belt storage and how it can prevent damage, reduce wear and tear, and extend the lifespan of your conveyor belts. We will cover essential tips and best practices for storing conveyor belts, ensuring they remain in optimal condition until they are ready for use. By following these guidelines, you can maximize the efficiency and durability of your conveyor system, ultimately saving time and money on repairs and replacements.
Conveyor Belt Storage Forms
Conveyor Belt Storage Forms refers to the different configurations or types of conveyor belt systems that can be employed for storing and handling items. These forms can vary based on the specific needs of the storage environment, the nature of the items being stored, and the operational goals of the facility. Below is a detailed description of various conveyor belt storage forms:
Flat Conveyor Belt Storage
- Flat Surface: This is the most common form of conveyor belt, where the belt runs flat along its length. It is ideal for transporting items that have a stable base and do not require any special handling.
- Use Cases: Flat conveyor belts are used in various industries, including manufacturing, packaging, and distribution centers. They are suitable for moving boxes, cartons, and other items that can lie flat.
- Direct Placement: Items are placed directly on the flat surface of the conveyor. They can be spaced evenly to avoid collisions and ensure easy access.
- Sorting and Sequencing: This form is often used in sorting operations, where items are automatically sequenced or sorted as they move along the belt.
Inclined Conveyor Belt Storage
- Incline and Decline: These conveyor belts are angled, allowing items to be moved up or down between different levels or floors within a facility. The angle can vary depending on the type of items and the height difference that needs to be overcome.
- Use Cases: Inclined conveyor belts are used in multi-level warehouses, production lines, and facilities where vertical movement of goods is necessary.
- Anti-Slip Surfaces: To prevent items from slipping during the incline, the belt may have a textured or rubberized surface, or cleats (small protrusions) may be added to hold items in place.
- Vertical Space Optimization: This form of storage is ideal for maximizing vertical space, allowing facilities to store items on multiple levels.
Curved Conveyor Belt Storage
- Belt Curvature: Curved conveyor belts are designed to change the direction of the conveyor system. They can curve at various angles, typically ranging from 30 to 180 degrees.
- Use Cases: These belts are used in layouts where space is limited, or where the conveyor system needs to navigate around obstacles. They are common in packaging, airports (baggage handling), and assembly lines.
- Smooth Transition: Items are stored and transported along the curved path, with the conveyor belt designed to ensure smooth transitions without items tipping or falling.
- Guided Edges: The conveyor may have raised edges or side guards to keep items aligned and prevent them from sliding off during the curve.
Modular Belt Storage
- Interlocking Segments: Modular conveyor belts are made of interlocking segments that can be easily replaced or reconfigured. They offer flexibility in terms of length, width, and configuration.
- Use Cases: These belts are ideal for applications requiring frequent changes in layout or where different belt surfaces are needed for different products.
- Custom Configurations: Items can be stored on belts configured to specific needs, such as belts with drainage holes for wet environments or belts with tight surfaces for small items.
- Versatility: The modular design allows for easy adaptation to different storage requirements, making it suitable for industries like food processing, where hygiene and flexibility are critical.
Roller Conveyor Belt Storage
- Roller Mechanism: Unlike traditional flat belts, roller conveyors use a series of rollers to move items. The rollers can be powered or gravity-fed, depending on the application.
- Use Cases: Roller conveyors are used for heavy or bulky items, such as pallets, where a flat belt would be less effective. They are common in distribution centers, manufacturing plants, and airports.
- Load Distribution: Items are placed on the rollers, where they can easily be moved along the conveyor with minimal friction. The rollers distribute the load, making it easier to handle heavy items.
- Accumulation Zones: Roller conveyors can be designed with accumulation zones, where items can be temporarily held without stopping the entire conveyor system.
Overhead Conveyor Belt Storage
- Overhead Design: Overhead conveyors are suspended from the ceiling or a supporting structure, allowing items to be stored and moved above the ground. This frees up floor space for other uses.
- Use Cases: These systems are often used in automotive assembly lines, garment manufacturing, and warehouses where space efficiency is crucial.
- Hanging Storage: Items are typically hung from the conveyor using hooks, hangers, or carriers. This is particularly useful for garments, car parts, or other items that can be suspended.
- Vertical Storage: Overhead conveyors make use of vertical space, allowing for more efficient storage in facilities with high ceilings.
Chain Conveyor Belt Storage
- Chain Mechanism: Chain conveyors use linked chains to drive the belt. They are robust and can handle heavy loads or items that require a durable transport system.
- Use Cases: These systems are common in industries that handle heavy or bulky materials, such as automotive, metalworking, and construction.
- Durable Storage: Items are stored on a belt supported by chains, ensuring they can be transported over long distances or through rugged environments without damage.
- Heat and Chemical Resistance: Chain conveyors are often used in environments where heat, chemicals, or other harsh conditions are present, providing reliable storage and transport.
Accumulation Conveyor Belt Storage
- Buffering Capacity: Accumulation conveyors are designed to allow items to accumulate or buffer on the belt without damaging or stopping the system. This is achieved through the use of sensors and controls that regulate the movement of items.
- Use Cases: These belts are ideal in packaging lines, assembly processes, and distribution centers where temporary storage or buffering is needed before the next process.
- Controlled Flow: Items are stored on the belt in accumulation zones, where they can be held until the system is ready to move them forward. This ensures a smooth flow of materials through the facility.
- Reduced Handling: Accumulation conveyors reduce the need for manual handling by allowing items to queue up automatically, improving efficiency.
Each of these conveyor belt storage forms is designed to meet specific operational needs, from optimizing space and improving safety to handling specialized items or harsh environments. Choosing the right form depends on the nature of the items being stored, the physical layout of the facility, and the overall goals of the operation.

Conveyor Belt Storage Conditions
When discussing “Conveyor Belt Storage Conditions,” the focus shifts to the environmental and operational factors that must be considered when storing items on or around a conveyor belt system. These conditions are crucial for ensuring the longevity of both the conveyor belt itself and the items being transported or stored. Here’s a detailed exploration:
1. Temperature Control:
- Ambient Temperature: Conveyor belts, particularly those made of rubber or other synthetic materials, can be sensitive to extreme temperatures. Excessive heat may cause the belt to soften, stretch, or degrade, while cold temperatures might make it brittle and prone to cracking. Items stored on the belt should also be stable within the operating temperature range.
- Temperature Regulation: In environments with fluctuating temperatures, it’s important to maintain a stable climate using HVAC systems. If transporting perishable goods, refrigerated conveyor systems may be necessary.
2. Humidity and Moisture:
- Moisture Control: Excessive humidity can lead to condensation on the belt, which may cause slippage, rusting (in metal parts), or mold growth (on belts with organic components).
- Waterproofing: In wet environments, belts should be water-resistant or waterproof, and drainage systems should be in place to prevent water accumulation. The storage area should also have proper ventilation to avoid moisture buildup.
3. Cleanliness and Contamination Prevention:
- Dust and Debris: Conveyor belts must be kept clean to prevent the buildup of dust and debris, which can cause mechanical issues or contaminate the items being transported. Regular cleaning schedules are essential.
- Contamination Risks: In environments where food or sensitive materials are stored, the conveyor belt should be made of food-grade materials, and strict hygiene protocols should be enforced to prevent contamination.
4. Load Capacity and Weight Distribution:
- Weight Limits: Every conveyor belt system has a maximum load capacity. Exceeding this can cause damage to the belt, motors, or supporting structures. Items should be evenly distributed to avoid overloading a particular section.
- Item Stability: Stored items must be securely placed on the belt to prevent tipping, sliding, or falling, especially when the belt is in motion.
5. Chemical Resistance:
- Material Compatibility: If the conveyor belt or stored items are exposed to chemicals, such as cleaning agents, lubricants, or industrial chemicals, the belt material must be resistant to these substances. Exposure to incompatible chemicals can cause degradation or failure of the belt material.
- Spill Containment: Systems should be in place to quickly manage and contain any chemical spills to protect both the conveyor system and the surrounding environment.
6. Vibration and Shock Absorption:
- Mechanical Stress: Conveyor belts in industrial settings might be subject to vibrations from machinery or shocks from heavy items being placed or dropped on them. The belt system should be designed to absorb or mitigate these stresses to avoid damage.
- Item Protection: Delicate items stored on the conveyor should be cushioned or stabilized to protect them from vibrations or impacts during transport.
7. Light Exposure:
- UV Degradation: Prolonged exposure to sunlight or artificial UV light can cause degradation of certain conveyor belt materials, especially those made of rubber or plastics. Storage areas should minimize UV exposure, or UV-resistant belts should be used.
- Light Sensitivity of Items: Items sensitive to light, such as certain chemicals or pharmaceuticals, should be stored on covered or enclosed conveyor systems to protect them from light-induced degradation.
8. Fire Safety:
- Flammability: Conveyor belts, particularly those made of organic materials or polymers, can be flammable. Fire-resistant belts and materials should be used in environments with a fire risk.
- Fire Suppression: Storage areas should be equipped with appropriate fire detection and suppression systems, such as sprinklers, to quickly manage any fire that may occur.
9. Operational Environment:
- Noise Levels: Conveyor belts can contribute to noise pollution in the workplace. Noise dampening measures, such as acoustic panels or low-noise belts, should be considered if the storage area is in proximity to workers.
- Safety and Ergonomics: The design of the conveyor belt system should prioritize worker safety and ergonomic access, with proper guarding, emergency stops, and clear operating procedures.
10. Maintenance and Inspection:
- Routine Checks: Regular inspections are necessary to check for wear and tear, misalignment, or any other issues that could lead to belt failure or unsafe storage conditions.
- Lubrication and Adjustments: Conveyor systems often require periodic lubrication of moving parts and adjustments to tension or alignment to maintain optimal operation.
By adhering to these storage conditions, the integrity of the conveyor belt system and the safety and quality of the stored items can be maintained, ensuring efficient and reliable operations.

Conveyor Belt Storage and Handing
When discussing “Conveyor Belt Storage and Handling,” the focus is on how materials or items are stored and managed on a conveyor belt system, as well as the best practices for handling these items to ensure efficiency, safety, and longevity of both the system and the goods being transported. Here’s a detailed breakdown:
Storage on Conveyor Belts
Organization and Placement
- Item Arrangement: Items should be organized on the conveyor belt according to their size, weight, and fragility. Heavier items should be placed first to avoid crushing lighter, more delicate items.
- Spacing: Adequate spacing between items is essential to prevent collisions, ensure smooth operation, and allow for easy access when retrieving items.
- Orientation: Items should be placed in a stable orientation to avoid tipping or shifting during belt movement. This is particularly important for irregularly shaped or stacked items.
Storage Conditions
- Environmental Control: The storage environment should be controlled for temperature, humidity, and cleanliness, as outlined previously, to prevent damage to both the items and the conveyor belt system.
- Material Compatibility: Ensure that items stored on the conveyor are compatible with the belt material. For instance, avoid placing sharp or abrasive items directly on belts that could be easily damaged.
Handling of Items on Conveyor Belts
Loading and Unloading
- Manual Handling: When loading or unloading items manually, ensure workers follow ergonomic practices to avoid strain or injury. Items should be lifted with proper technique, and conveyors should be positioned at a height that minimizes bending or stretching.
- Automated Systems: For automated loading and unloading, use robotic arms or other machinery designed to handle specific item types. These systems should be calibrated to avoid applying excessive force, which could damage the items or the conveyor belt.
Transfer Between Conveyors
- Transition Points: When items are transferred between conveyor belts, transition points must be smooth to avoid jamming or item damage. This often involves synchronized speeds and well-aligned belts.
- Guides and Rails: Use side rails or guides to keep items aligned during transfer, especially for conveyors that operate at different speeds or angles.
Special Considerations
Handling Fragile Items
- Cushioning: Use padded surfaces or cushioning materials on the conveyor belt when handling fragile items to absorb shocks and reduce the risk of breakage.
- Gentle Transfers: For fragile items, employ gentle transfer mechanisms and slower belt speeds to minimize handling stress.
Handling Hazardous Materials
- Containment: When transporting hazardous materials, ensure that they are properly contained to prevent leaks or spills. Use conveyors with spill-resistant features if necessary.
- Safety Protocols: Implement strict safety protocols for handling and storing hazardous materials, including the use of appropriate personal protective equipment (PPE) for workers.
By following these guidelines for storage and handling on conveyor belts, operations can be optimized for safety, efficiency, and longevity, ensuring smooth and reliable material handling processes.
Proper Conveyor Belt Storage Techniques
Proper conveyor belt storage techniques are essential to maintain the belt’s quality, performance, and longevity. Improper storage can lead to issues such as deformation, contamination, and premature wear. Below are detailed guidelines and best practices for storing conveyor belts correctly:
Preparation Before Storage
- Debris Removal: Before storing, ensure the conveyor belt is thoroughly cleaned to remove any debris, dirt, or residues. Contaminants can cause surface damage or lead to deterioration during storage.
- Drying: If the belt has been exposed to moisture or liquids, dry it completely to prevent mold growth, rusting of metal components, or weakening of the belt material.
- Check for Damage: Inspect the belt for any signs of wear, tears, or damage that need to be repaired before storage. This prevents small issues from worsening while the belt is not in use.
- Record Condition: Document the condition of the belt before storage, noting any existing wear or defects. This record will be useful for future reference when the belt is retrieved.
Storage Environment
- Optimal Temperature: Store conveyor belts in a cool, dry place with a stable temperature. Ideal storage temperatures range between 10°C and 25°C (50°F to 77°F).
- Avoid Extremes: Protect the belt from extreme temperatures, which can cause the belt material to harden (in cold) or soften and degrade (in heat).
- Dry Conditions: Ensure the storage area is dry and has low humidity. High humidity can lead to moisture absorption, resulting in mold growth, oxidation, or material degradation.
- Moisture Barriers: If storing belts in environments prone to humidity, use moisture barriers such as plastic wrapping or desiccants to keep the belts dry.
- UV Exposure: Conveyor belts should be stored away from direct sunlight or strong artificial light, which can cause UV degradation. Prolonged exposure to UV light can weaken the belt material, leading to cracking and brittleness.
- Covering: Store belts in opaque coverings or containers that block light exposure.
Physical Storage Techniques
- Proper Rolling: Conveyor belts should be stored in a rolled-up position rather than laid flat or folded. Rolling reduces the risk of creases, bends, or deformation.
- Core Support: Use a cylindrical core or drum of appropriate diameter as a support when rolling the belt. The core should be wide enough to prevent sharp bends but small enough to maintain compactness.
- Avoid Over-tightening: Do not roll the belt too tightly, as this can cause stress and deformation. Maintain a moderate tension that keeps the belt secure without excessive compression.
- Vertical Storage: Ideally, store conveyor belts in a vertical orientation on a rack or stand. This minimizes pressure points and prevents flat spots from forming. Ensure that the belts are stable and not prone to tipping over.
- Horizontal Storage: If vertical storage is not possible, store belts horizontally on a flat, clean surface. Use spacers or supports to keep belts off the ground and prevent them from being compressed by their own weight.
- Avoid Stacking: It’s generally advisable not to stack conveyor belts on top of each other. If stacking is necessary, limit the number of belts in a stack to avoid excessive weight on the lower belts, which can cause deformation.
- Support Structures: Use racks or shelves designed for belt storage, providing individual support for each belt to prevent flattening or distortion.
Long-Term Storage Considerations
- Periodic Checks: Regularly inspect stored conveyor belts to ensure they remain in good condition. Look for signs of moisture, dust accumulation, or any deformation that may have occurred during storage.
- Re-tensioning: If belts were rolled, check that they remain properly tensioned and adjust as necessary to prevent the roll from loosening or tightening excessively over time.
- First In, First Out (FIFO): Apply FIFO principles to belt storage, where older belts are used before newer ones. This helps prevent belts from deteriorating due to prolonged storage.
- Inventory Management: Keep an accurate record of storage dates and conditions for each belt, facilitating better management and retrieval when needed.
Special Considerations
- Heat-Resistant Belts: For belts designed to withstand high temperatures, ensure that storage conditions do not exceed their rated temperature even in storage, as prolonged exposure to high temperatures can still cause degradation.
- Chemical-Resistant Belts: Store belts resistant to chemicals away from any chemical substances to prevent accidental exposure that could affect other belts or materials in storage.
- Cleaning: Clean used belts thoroughly before storage to remove any contaminants, including residues, oils, or chemicals that could cause deterioration.
- Separate Storage: Store used belts separately from new belts to avoid cross-contamination or confusion during retrieval.
By following these proper storage techniques, conveyor belts can be preserved in optimal condition, ensuring they are ready for use when needed without any compromise in performance or longevity.
Long-Term Conveyor Belt Storage
Long-term conveyor belt storage requires careful planning and execution to ensure that the belts remain in optimal condition over extended periods. Here’s a detailed guide on how to store conveyor belts for the long term effectively:
Preparation for Long-Term Storage
- Debris Removal: Clean the conveyor belt thoroughly to remove any dirt, dust, or residue. Even small particles can cause damage over time if left on the belt.
- Chemical and Oil Removal: Use appropriate cleaning agents to remove any chemical residues or oils that might cause the belt material to degrade during storage.
- Damage Assessment: Conduct a detailed inspection of the belt for any signs of wear, such as tears, cuts, or abrasions. Repair any damages before storage to prevent them from worsening.
- Documentation: Document the belt’s condition, noting any repairs made and areas to monitor. This information will be useful when retrieving the belt after long-term storage.
Selecting the Storage Environment
- Stable Temperature: Store the belt in an environment with a stable temperature between 10°C and 25°C (50°F to 77°F). Extreme temperature fluctuations should be avoided as they can cause the belt material to expand, contract, or harden.
- Avoid Heat Sources: Ensure that the storage area is away from heat sources like radiators, machinery, or direct sunlight, which can cause the belt to age prematurely.
- Dry Environment: The storage area should be kept dry, with a relative humidity of around 50% to 60%. Excess moisture can lead to mold growth, corrosion of metal components, and degradation of the belt material.
- Dehumidifiers: In areas prone to high humidity, consider using dehumidifiers to maintain the proper humidity levels.
- UV Protection: Store the belts in a dark environment or use UV-resistant coverings to protect them from light exposure. Prolonged exposure to UV light can cause the belt material to weaken and crack.
- Opaque Wrapping: Use opaque plastic wrapping or tarps to cover the belts, ensuring they are shielded from any light source.
Proper Physical Storage Techniques
- Proper Rolling: Roll the conveyor belt around a cylindrical core or drum with a diameter that prevents sharp bends or creases. The core should be sturdy enough to support the belt’s weight without bending.
- Vertical Storage: Store the rolled belts vertically on a rack or stand. This minimizes surface contact, reducing the risk of flat spots or deformation. Ensure the belts are securely fastened to prevent them from tipping over.
- Flat Surface: If vertical storage is not feasible, store the belts horizontally on a flat, clean surface. Use supports to elevate the belts slightly off the ground, reducing the risk of moisture absorption or deformation from direct contact with the floor.
- Avoid Stacking: Avoid stacking belts on top of each other. If stacking is necessary, place the heaviest belts at the bottom and limit the height to prevent excessive pressure on the lower belts.
- Dust Protection: Cover the belts with dust-proof tarps or sheets to prevent dust accumulation, which can cause abrasion or contamination over time.
- Moisture Barriers: Use moisture-resistant coverings, such as plastic wrap, to protect the belts from any potential water or humidity in the storage area.
Long-Term Storage Maintenance
- Periodic Checks: Schedule regular inspections of the stored belts (every 3 to 6 months). Check for signs of moisture, dust accumulation, or any changes in the belt’s condition.
- Condition Monitoring: Look for any warping, cracking, or changes in flexibility. Address any issues immediately to prevent further damage.
- Re-tensioning: If the belts have been stored for a long period, re-roll them to maintain proper tension and prevent the belt from sagging or becoming misshapen.
- Repositioning: Rotate the stored belts periodically to ensure even pressure distribution and prevent permanent deformation, especially if stored horizontally.
Special Considerations for Long-Term Storage
- Heat-Resistant Belts: For belts designed for high-temperature environments, ensure that storage conditions remain within their operational temperature range to prevent material degradation.
- Chemical-Resistant Belts: Keep chemical-resistant belts away from any chemicals, even in storage, to prevent any adverse reactions that could occur over time.
- Extended Storage: If the belts will be stored for several years, consider additional protective measures, such as vacuum sealing, to further reduce the risk of environmental damage.
- Rotation of Stock: Implement a system to ensure older belts are used first (FIFO) to prevent belts from being stored for excessively long periods.
Preparing Belts for Reuse After Long-Term Storage
- Detailed Examination: Before placing a belt back into service, conduct a thorough inspection to ensure no damage occurred during storage.
- Flexibility Test: Check the belt’s flexibility and surface condition. If the belt has stiffened or developed cracks, it may need conditioning or replacement.
- Proper Handling: When unrolling the belt, do so carefully to avoid kinks or sharp bends. Allow the belt to acclimate to the operating environment before full installation.
- Conditioning: If necessary, run the belt under light load conditions initially to ensure it returns to optimal performance gradually.
By adhering to these long-term storage techniques, conveyor belts can be preserved in a condition that ensures they remain functional and reliable when needed for future use. Proper storage not only extends the life of the belts but also reduces the risk of unexpected failures or costly replacements.

Best Practices for Conveyor Belt Storage Ideas
Storing conveyor belts correctly is essential to prevent conveyor belt damage and ensure their optimal performance. Implementing innovative conveyor belt storage ideas can significantly enhance the efficiency and longevity of your belts. Here are some of the best practices to consider:
Vertical Storage Racks
One of the most effective conveyor belt storage ideas is using vertical storage racks. These racks allow you to store belts in an upright position, which minimizes the risk of damage and makes them easily accessible. Vertical storage racks are particularly beneficial for facilities with limited floor space, as they maximize the use of vertical space.
Temperature-Controlled Storage
Maintaining the right temperature is crucial for preserving the quality of conveyor belts. Extreme temperatures can cause belts to become brittle or soften, leading to damage. Implementing temperature-controlled storage solutions ensures that the belts are kept at optimal conditions, extending their lifespan and maintaining their performance.
Moisture Control
Moisture can have detrimental effects on conveyor belts, leading to mold growth and material degradation. To prevent these issues, it’s essential to store belts in a dry environment. Using dehumidifiers and moisture-absorbing materials can help control humidity levels and protect the belts from moisture-related damage.
Organized Labeling System
An organized labeling system is a key aspect of effective conveyor belt storage. Labeling belts according to their size, type, and usage makes it easier to locate and retrieve them when needed. This practice not only saves time but also ensures that the right belt is used for the right application, reducing the risk of errors.
Regular Inspections
Conducting regular inspections of stored conveyor belts is essential to identify any signs of damage or wear. Inspections should include checking for cracks, fraying, or other forms of deterioration. By identifying issues early, you can take corrective measures to prevent further damage and extend the belts’ lifespan.
Proper Handling Techniques
Proper handling techniques are critical when storing and retrieving conveyor belts. Avoid dragging belts across rough surfaces, as this can cause abrasions and tears. Instead, use appropriate lifting equipment and techniques to handle the belts carefully, ensuring they remain in good condition.
Rotational Storage
Rotational storage involves periodically rotating the stored conveyor belts to ensure even wear and prevent deformation. This practice helps maintain the belts’ shape and integrity, ensuring they perform optimally when in use. Implementing a rotational schedule can be part of your regular maintenance routine.
Customized Storage Solutions
Customized storage solutions tailored to your specific needs can significantly improve the efficiency of conveyor belt storage. Consider factors such as the size and type of belts, available storage space, and environmental conditions when designing your storage system. Custom solutions ensure that your storage setup is optimized for your unique requirements.
Utilizing Conveyor Belt Storage Containers
Conveyor belt storage containers play a crucial role in maintaining the quality and performance of belts during storage. These containers are designed to protect belts from environmental factors and physical damage, ensuring they remain in optimal condition. Here, we discuss the importance of storage containers and the types available:
Role of Conveyor Belt Storage Containers
Conveyor belt storage containers provide a controlled environment that shields belts from adverse conditions such as temperature fluctuations, moisture, dust, and physical impacts. By keeping belts in a protected state, these containers prevent premature wear and damage, extending the belts’ service life. Additionally, storage containers facilitate organized and efficient storage, making it easier to manage inventory and access belts when needed.
Types of Conveyor Belt Storage Containers
Plastic Storage Bins
Plastic storage bins are a popular choice for conveyor belt storage due to their durability, lightweight nature, and resistance to corrosion. These bins are available in various sizes and shapes, allowing you to choose the right container based on the size and type of belts you need to store. Plastic bins are also easy to clean and maintain, making them a practical option for long-term storage.
Metal Storage Containers
Metal storage containers offer robust protection for conveyor belts, especially in industrial environments where heavy machinery and equipment are present. These containers are highly durable and can withstand rough handling and harsh conditions. Metal containers also provide excellent security, protecting belts from theft or unauthorized access.
Fabric Storage Bags
For smaller conveyor belts or those requiring flexible storage options, fabric storage bags are an excellent choice. These bags are made from durable materials that protect belts from dust and moisture. Fabric bags are lightweight and easy to transport, making them ideal for temporary storage or situations where mobility is required.
Wooden Crates
Wooden crates provide a sturdy and protective storage solution for conveyor belts. They are particularly suitable for long-term storage and transportation, as they can withstand significant weight and pressure. Wooden crates can be customized to fit specific belt dimensions, ensuring a snug and secure fit.
Pallet Racking Systems
Pallet racking systems are an efficient way to store multiple conveyor belts in a compact and organized manner. These systems use pallets to store belts off the ground, reducing the risk of damage from moisture and pests. Pallet racking systems can be easily integrated into existing warehouse setups, providing a scalable storage solution.
Modular Storage Units
Modular storage units offer versatility and flexibility for conveyor belt storage. These units can be configured to accommodate different belt sizes and types, allowing for efficient use of space. Modular units can be expanded or reconfigured as storage needs change, providing a long-term solution that adapts to your requirements.
Benefits of Using Conveyor Belt Storage Containers
Protection from Environmental Factors
Storage containers shield conveyor belts from environmental factors such as temperature fluctuations, humidity, dust, and UV exposure. This protection is crucial for preserving the belts’ material properties and ensuring they remain in optimal condition.
Improved Organization
Using storage containers enhances the organization of conveyor belt storage. Containers can be labeled and arranged systematically, making it easier to locate and retrieve specific belts when needed. This organized approach reduces downtime and increases operational efficiency.
Space Optimization
Storage containers help optimize available storage space by allowing for vertical stacking and efficient use of floor space. This optimization is particularly beneficial in facilities with limited storage areas, enabling you to store more belts in a smaller footprint.
Enhanced Safety
Storing conveyor belts in containers improves safety by reducing the risk of belts being damaged or causing accidents. Containers provide a secure environment that minimizes the potential for belts to be dropped, dragged, or otherwise mishandled.
Ease of Transport
Containers facilitate the easy transport of conveyor belts within and between facilities. Whether moving belts to different storage areas or transporting them to job sites, containers provide a convenient and secure means of transportation.
Optimizing Space with Conveyor Belt Storage Ideas
Maximizing storage space is essential for efficient operations, especially in facilities with limited room. Implementing creative conveyor belt storage ideas can help you make the most of your available space while ensuring that belts are stored safely and accessibly. Here are some tips for optimizing space:
Vertical Storage Solutions
Vertical storage solutions, such as shelving units and vertical racks, allow you to store conveyor belts upright. This approach maximizes the use of vertical space, freeing up valuable floor space for other operations. Vertical storage is particularly beneficial in warehouses and facilities with high ceilings.
Modular Shelving Systems
Modular shelving systems provide flexible storage options that can be adapted to your needs. These systems can be easily reconfigured to accommodate different belt sizes and quantities. By using adjustable shelves, you can optimize space based on the specific dimensions of the belts you are storing.
Overhead Storage
Overhead storage solutions, such as ceiling-mounted racks or pulley systems, make use of otherwise unused space above work areas. This approach keeps conveyor belts off the floor and out of the way, reducing clutter and creating a more organized workspace. Overhead storage is ideal for belts that are not frequently accessed but still need to be readily available.
Mobile Storage Units
Mobile storage units, such as rolling racks or carts, provide flexibility and mobility in your storage setup. These units can be easily moved to different locations within the facility, allowing you to adapt your storage configuration as needed. Mobile units are particularly useful for temporary storage or when belts need to be transported to different workstations.
Compact Storage Designs
Compact storage designs, such as stackable bins or nesting containers, help maximize space by minimizing the footprint of stored items. These designs allow you to store more belts in a smaller area, making efficient use of available space. Compact storage solutions are ideal for facilities with limited storage capacity.
Multi-Level Storage
Implementing multi-level storage systems, such as mezzanine floors or tiered shelving, allows you to create additional storage levels within your facility. This approach effectively doubles or triples your storage capacity without requiring additional floor space. Multi-level storage is particularly useful for high-volume storage needs.
Space-Saving Storage Containers
Using space-saving storage containers, such as collapsible bins or foldable crates, helps optimize storage space when containers are not in use. These containers can be collapsed and stored compactly, freeing up space for other operations. Space-saving containers are ideal for seasonal or temporary storage needs.
Efficient Layout Planning
Planning an efficient storage layout is crucial for optimizing space. Consider the dimensions and accessibility of stored belts when designing your storage area. Group similar belts together and arrange containers to minimize the distance and time required to retrieve items. An efficient layout reduces clutter and enhances workflow.
Regular Inventory Management
Regular inventory management helps optimize storage space by ensuring that only necessary items are stored. Conduct periodic audits of your conveyor belt inventory to identify unused or obsolete belts. Removing unnecessary items frees up space for more critical storage needs.
Custom Storage Solutions
Custom storage solutions tailored to your specific requirements can significantly enhance space optimization. Work with storage solution providers to design systems that fit your unique needs, taking into account the size, type, and quantity of belts you need to store. Custom solutions ensure that your storage setup is fully optimized for your operations.
Optimizing space with conveyor belt storage ideas involves implementing vertical storage solutions, modular shelving systems, overhead storage, mobile units, compact designs, multi-level storage, space-saving containers, efficient layout planning, regular inventory management, and custom solutions. These strategies help you make the most of your available space, ensuring that conveyor belts are stored efficiently and accessibly.
Benefits of Conveyor Belt Storage Containers
Conveyor belt storage containers play a crucial role in maintaining the quality and performance of belts during storage. These containers are designed to protect belts from environmental factors and physical damage, ensuring they remain in optimal condition. Here, we discuss the benefits of using storage containers and how they protect and preserve conveyor belts:
Protection from Environmental Factors
One of the primary benefits of conveyor belt storage containers is their ability to protect belts from adverse environmental conditions. Conveyor belts can be susceptible to damage from temperature fluctuations, humidity, dust, and UV exposure. Storage containers create a controlled environment that shields belts from these harmful factors. By keeping belts in a stable and protected state, containers help prevent premature wear and deterioration, extending the belts’ service life and maintaining their performance.
Improved Organization
Using conveyor belt storage containers enhances the organization of storage areas. Containers can be labeled and arranged systematically, making it easier to locate and retrieve specific belts when needed. This organized approach not only saves time but also ensures that the right belt is used for the right application, reducing the risk of errors. Improved organization also means that inventory management becomes more efficient, helping you keep track of your assets and ensuring that belts are readily available when required.
Space Optimization
Storage containers help optimize available storage space by allowing for vertical stacking and efficient use of floor space. This optimization is particularly beneficial in facilities with limited storage areas, enabling you to store more belts in a smaller footprint. By utilizing space-saving storage solutions, you can maximize the efficiency of your storage operations and ensure that belts are stored in a manner that prevents damage and facilitates easy access.
Enhanced Safety
Storing conveyor belts in containers improves safety by reducing the risk of belts being damaged or causing accidents. Containers provide a secure environment that minimizes the potential for belts to be dropped, dragged, or otherwise mishandled. This secure storage helps prevent injuries to personnel and damage to equipment, contributing to a safer working environment.
Ease of Transport
Containers facilitate the easy transport of conveyor belts within and between facilities. Whether moving belts to different storage areas or transporting them to job sites, containers provide a convenient and secure means of transportation. Storage containers protect belts from damage during transit, ensuring that they arrive at their destination in optimal condition.
Preservation of Belt Integrity
Conveyor belt storage containers play a critical role in preserving the integrity of belts during storage. By shielding belts from environmental and physical stressors, containers help maintain the belts’ structural integrity and performance characteristics. This preservation is crucial for ensuring that belts perform reliably when put into service, reducing the risk of operational disruptions and costly downtime.
Versatility
Conveyor belt storage containers are versatile and can be used in a variety of storage environments. Whether in a warehouse, outdoor storage area, or transport vehicle, containers provide a consistent and reliable storage solution. This versatility makes them suitable for a wide range of industries and applications, ensuring that belts are stored safely and efficiently regardless of the setting.
Cost Savings
The benefits of using conveyor belt storage containers translate directly into cost savings. By preventing damage and extending the lifespan of belts, containers reduce the need for frequent replacements and repairs. This reduction in maintenance costs, combined with the increased efficiency of organized storage, results in significant cost savings over time. Additionally, the protection offered by containers reduces the risk of unexpected belt failures, helping to avoid costly operational downtime.
Implementing Effective Conveyor Belt Storage Ideas
Implementing effective conveyor belt storage ideas is essential for maintaining the quality and performance of your belts. A well-thought-out storage strategy can prevent damage, optimize space, and improve overall efficiency. Here is a step-by-step guide on implementing storage ideas, along with real-life examples of successful storage implementations:
Step-by-Step Guide on Implementing Storage Ideas
Step 1: Assess Storage Needs
Begin by assessing your storage needs. Consider the number and size of conveyor belts you need to store, as well as the available storage space. Identify any environmental factors that may affect belt storage, such as temperature fluctuations, humidity, and exposure to dust or chemicals. Understanding your specific storage requirements is crucial for developing an effective storage strategy.
Step 2: Choose Appropriate Storage Solutions
Based on your assessment, choose appropriate storage solutions that meet your needs. This may include vertical storage racks, modular shelving systems, storage containers, or overhead storage solutions. Consider the benefits and limitations of each option and select the ones that best fit your requirements.
Step 3: Design an Efficient Layout
Design an efficient layout for your storage area. Arrange storage solutions in a manner that maximizes space utilization and ensures easy access to stored belts. Group similar belts together and label storage containers to facilitate quick and accurate retrieval. An efficient layout reduces clutter and enhances workflow, making it easier to manage inventory and access belts when needed.
Step 4: Implement Environmental Controls
Implement environmental controls to protect conveyor belts from adverse conditions. This may include temperature control, humidity control, and dust mitigation measures. Use dehumidifiers, climate control systems, and dust covers to create a stable and protective storage environment. Regularly monitor environmental conditions to ensure they remain within acceptable ranges.
Step 5: Train Personnel
Train personnel on proper storage and handling techniques. Ensure that all staff members understand the importance of correct storage practices and know how to handle belts safely and efficiently. Provide training on using storage solutions, labeling systems, and environmental controls to maintain the quality and performance of stored belts.
Step 6: Conduct Regular Inspections
Conduct regular inspections of stored conveyor belts to identify any signs of damage or wear. Inspections should include checking for cracks, fraying, and other forms of deterioration. By identifying issues early, you can take corrective measures to prevent further damage and extend the belts’ lifespan. Regular inspections also help ensure that storage solutions and environmental controls are functioning correctly.
Step 7: Maintain an Organized Inventory
Maintain an organized inventory of stored conveyor belts. Keep accurate records of belt quantities, sizes, and locations to facilitate efficient inventory management. Regularly update inventory records to reflect any changes, such as belts being put into service or new belts being added to storage. An organized inventory helps you keep track of your assets and ensures that belts are readily available when needed.
Real-Life Examples of Successful Storage Implementations
Example 1: Vertical Storage Racks at XYZ Manufacturing
XYZ Manufacturing, a company specializing in the production of industrial equipment, implemented vertical storage racks to store their conveyor belts. These racks allowed XYZ Manufacturing to store belts in an upright position, maximizing the use of vertical space and freeing up valuable floor space. The company also introduced a comprehensive labeling system to organize belts by size and type, making it easier for employees to locate and retrieve specific belts. This storage solution improved organization, optimized space, and protected belts from damage, resulting in increased efficiency and reduced downtime for XYZ Manufacturing.
Example 2: Temperature-Controlled Storage at Fresh Foods Processing Plant
Fresh Foods Processing Plant, a facility focused on processing and packaging fresh produce, implemented temperature-controlled storage solutions to protect their conveyor belts from extreme temperatures. The plant installed advanced climate control systems in their storage area to maintain a stable temperature, preventing belts from becoming brittle or softening. They also deployed dehumidifiers to control humidity levels and prevent mold growth. This storage solution ensured that belts remained in optimal condition, extending their lifespan and maintaining their performance, ultimately supporting the high standards of Fresh Foods Processing Plant.
Example 3: Overhead Storage at Global Logistics Warehouse
Global Logistics, a leading warehousing and distribution company, implemented overhead storage solutions to maximize space utilization. They installed ceiling-mounted racks and pulley systems to store conveyor belts above work areas, keeping belts off the floor and out of the way. This storage solution reduced clutter, created a more organized workspace, and ensured that belts were readily accessible when needed. The overhead storage system also provided protection from physical damage, preserving the quality and performance of the belts, thus enhancing the operational efficiency of Global Logistics.
Example 4: Modular Shelving Systems at Prime Distribution Center
Prime Distribution Center, a major player in the logistics and supply chain industry, implemented modular shelving systems to store their conveyor belts. The adjustable shelves allowed the center to reconfigure their storage setup as needed to accommodate different belt sizes and quantities. Prime Distribution Center also designed an efficient layout that grouped similar belts together and labeled storage containers for easy retrieval. This storage solution optimized space, improved organization, and facilitated efficient inventory management, contributing to the overall productivity and operational efficiency of Prime Distribution Center.
Maintenance Tips for Conveyor Belt Storage Containers
Maintaining conveyor belt storage containers is essential for ensuring the longevity and performance of the stored belts. Proper maintenance practices help prevent damage, preserve the quality of the containers, and ensure that they continue to provide effective protection for the belts. Here are some maintenance tips for conveyor belt storage containers:
Regular Cleaning
Regular cleaning of storage containers is crucial for maintaining their quality and performance. Dust, dirt, and debris can accumulate on containers over time, potentially contaminating stored belts and affecting their performance. Clean containers periodically using appropriate cleaning methods and materials. For plastic containers, use mild detergents and warm water, while metal containers may require specialized cleaning solutions to prevent corrosion.
Inspect for Damage
Conduct regular inspections of storage containers to identify any signs of damage or wear. Check for cracks, dents, rust, and other forms of deterioration that could compromise the integrity of the containers. Address any issues promptly to prevent further damage and ensure that the containers continue to provide effective protection for the stored belts.
Monitor Environmental Conditions
Monitor the environmental conditions of the storage area to ensure that they remain within acceptable ranges. Temperature, humidity, and dust levels can affect the quality and performance of storage containers. Implement environmental controls, such as climate control systems and dehumidifiers, to maintain stable conditions and protect both the containers and the stored belts.
Lubricate Moving Parts
For storage containers with moving parts, such as hinges and locks, regular lubrication is essential to ensure smooth operation
. Use appropriate lubricants to prevent rust and ensure that moving parts function correctly. Lubricate hinges, locks, and other moving components as part of your routine maintenance schedule.
Replace Worn Components
Over time, certain components of storage containers may wear out and require replacement. This may include seals, gaskets, hinges, and locks. Regularly inspect these components and replace them as needed to maintain the integrity and functionality of the containers. Using high-quality replacement parts ensures that the containers continue to provide effective protection for the stored belts.
Ensure Proper Labeling
Proper labeling of storage containers is essential for maintaining an organized storage system. Ensure that labels are clear, accurate, and up-to-date. Replace any faded or damaged labels to ensure that containers can be easily identified and retrieved. Proper labeling helps prevent confusion and ensures that the right belts are used for the right applications.
Implement Pest Control Measures
Pests can pose a significant threat to storage containers and the stored belts. Implement pest control measures to prevent infestations and protect the quality of the containers. This may include using pest repellents, sealing entry points, and maintaining a clean storage area. Regularly inspect containers for signs of pest activity and address any issues promptly.
Store Containers Properly
Proper storage of empty containers is also important for maintaining their quality. Store containers in a dry, clean, and stable environment to prevent damage and contamination. Avoid stacking containers too high, as this can cause them to become unstable and potentially damage the containers at the bottom of the stack.
Conduct Routine Maintenance Checks
Establish a routine maintenance schedule for storage containers. Conduct regular checks to ensure that containers are clean, undamaged, and functioning correctly. Routine maintenance helps identify potential issues early and allows for timely corrective measures, ensuring that storage containers continue to provide effective protection for conveyor belts.
Use Appropriate Storage Solutions
Using appropriate storage solutions for the specific type of conveyor belts you are storing is crucial for maintaining their quality. Consider the size, material, and environmental requirements of the belts when selecting storage containers. Using containers that are well-suited to your specific needs helps ensure that belts remain in optimal condition during storage.
Proper maintenance of conveyor belt storage containers involves regular cleaning, inspections for damage, monitoring environmental conditions, lubricating moving parts, replacing worn components, ensuring proper labeling, implementing pest control measures, storing containers properly, conducting routine maintenance checks, and using appropriate storage solutions. These practices help maintain the quality and performance of storage containers, ensuring that they continue to provide effective protection for stored conveyor belts.
FAQs about Conveyor Belt Storage
Storing conveyor belts correctly is crucial for maintaining their quality and longevity. When storing conveyor belts, they should be kept in a cool, dry place away from direct sunlight and harsh weather conditions. It’s important to store them horizontally on a flat surface or a properly designed rack to prevent any deformation. Avoid stacking belts on top of each other as this can cause creasing and damage. Additionally, conveyor belts should be kept away from chemicals, oils, and other substances that could degrade the belt material. Regularly inspect the stored belts for any signs of damage or wear, and rotate them periodically to ensure even aging.
In a warehouse setting, belts should be stored under similar conditions to those used for conveyor belts. Keep them in a clean, dry area that is protected from temperature extremes and direct sunlight. Use racks or shelves designed to support the belts without causing them to sag or deform. If possible, store the belts in their original packaging to provide extra protection against dust and contaminants. Labeling each belt clearly can help in quick identification and inventory management. Regularly check the stored belts for signs of aging, cracking, or other damage, and make sure to rotate stock to use older belts first, ensuring that no belts are stored for excessively long periods.
Maintaining conveyor belts involves several key practices to ensure their longevity and efficient operation. Regular inspections are essential to identify any signs of wear, damage, or misalignment. Clean the belts regularly to remove any buildup of dirt, debris, or oil that could affect performance. Proper lubrication of the conveyor system’s moving parts, such as bearings and rollers, helps reduce friction and wear. It’s also important to keep the belt tensioned correctly; over-tensioning or under-tensioning can lead to premature wear and operational issues. Perform routine preventive maintenance, such as checking and replacing worn components, repairing any damages promptly, and keeping detailed maintenance logs. Training personnel on proper conveyor belt usage and safety procedures is also crucial for maintaining the system effectively.
V belts should be stored in a similar manner to other types of belts, emphasizing protection from environmental factors that could cause damage. Store V belts in a cool, dry area, away from direct sunlight, heat sources, and ozone-generating equipment, which can cause rubber deterioration. V belts should be hung on racks that allow them to maintain their shape without bending or kinking. If hanging is not possible, store them on shelves with enough support to prevent deformation. Avoid placing heavy objects on top of stored V belts to prevent creasing and damage. Regular inspections of stored V belts for signs of aging, such as cracks or hardening, are essential. Rotate stock periodically to ensure that older belts are used first, and maintain an organized inventory system for easy retrieval and identification.
To store mechanical belts properly, keep them in a cool, dry environment with temperatures between 10°C and 30°C (50°F and 86°F) and relative humidity of 30% to 70%. Avoid exposure to direct sunlight and UV light, as well as chemicals and solvents that can degrade the material. Belts should be stored either flat on a clean surface or coiled loosely to prevent kinks. Hanging them on large-diameter pegs is also an option, provided they aren’t under tension. Keep belts clean and free of dirt before storage, and avoid stacking heavy items on top. Rotate stock using a first-in, first-out (FIFO) method to ensure older belts are used first. Ideally, use belts within five years to maintain their performance. This careful storage approach will extend the life and reliability of the belts.
Last Updated on August 23, 2024 by Jordan Smith
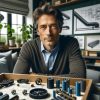
Jordan Smith, a seasoned professional with over 20 years of experience in the conveyor system industry. Jordan’s expertise lies in providing comprehensive solutions for conveyor rollers, belts, and accessories, catering to a wide range of industrial needs. From initial design and configuration to installation and meticulous troubleshooting, Jordan is adept at handling all aspects of conveyor system management. Whether you’re looking to upgrade your production line with efficient conveyor belts, require custom conveyor rollers for specific operations, or need expert advice on selecting the right conveyor accessories for your facility, Jordan is your reliable consultant. For any inquiries or assistance with conveyor system optimization, Jordan is available to share his wealth of knowledge and experience. Feel free to reach out at any time for professional guidance on all matters related to conveyor rollers, belts, and accessories.