Key Components of Conveyor Belt Support
The efficiency and reliability of conveyor operations heavily depend on robust conveyor belt support systems. These systems are essential for maintaining optimal performance, preventing belt sagging, and reducing maintenance needs. Key components of conveyor belt support include impact idlers, which absorb shocks and protect the belt, and item conveyors, which facilitate smooth material handling. Understanding and implementing effective conveyor belt support is crucial for minimizing downtime and maximizing operational productivity across various industries.
The Crucial Role of Conveyor Belt Support Systems
Functionality and Purpose
Conveyor belt support systems play a pivotal role in maintaining the operational efficiency and reliability of conveyor systems across various industries. These systems ensure the belt remains properly aligned, preventing sagging and reducing the need for frequent maintenance. Proper conveyor belt support is essential for minimizing downtime and maximizing productivity.
One of the primary functions of conveyor belt support systems is to maintain belt alignment. When a conveyor belt is misaligned, it can lead to uneven wear and tear, increased energy consumption, and even system failure. For example, in the mining industry, companies like Vale and Rio Tinto rely on precise belt alignment to handle heavy loads efficiently. Misalignment in such settings can lead to significant operational disruptions and financial losses.
Conveyor belt support systems also play a critical role in preventing belt sagging. Sagging can cause material spillage, leading to wastage and environmental hazards. Additionally, sagging increases the risk of belt damage, resulting in costly repairs and replacements. By providing consistent support, these systems ensure the belt remains flat and stable, particularly in areas where heavy materials are loaded onto the belt. For instance, in the bulk material handling sector, companies like Cargill and BHP Billiton utilize robust conveyor belt support systems to prevent sagging and ensure smooth operations.
Another vital purpose of conveyor belt support systems is to reduce maintenance requirements. Frequent maintenance can be both time-consuming and expensive. Conveyor belt support systems minimize wear and tear on the belt by distributing the load evenly and reducing friction. This leads to longer belt life and fewer maintenance interventions. For example, in the manufacturing industry, Toyota and Honda implement advanced conveyor belt support systems to maintain continuous production lines with minimal downtime, thus ensuring high efficiency and cost-effectiveness.
Key Components
The effectiveness of conveyor belt support systems depends on several key components, each playing a specific role in ensuring the system’s overall functionality and reliability.
Idlers: Idlers are one of the most critical components in a conveyor belt support system. They consist of a series of rollers positioned along the conveyor frame, providing support and stability to the belt. There are various types of idlers, including carrying idlers, return idlers, and impact idlers. Impact idlers, in particular, are designed to absorb the shock of heavy loads, protecting the belt from damage. Companies like Flexco and Martin Engineering manufacture high-quality idlers that are widely used in industries such as mining and logistics.
Rollers: Rollers are another essential component of conveyor belt support systems. They facilitate the smooth movement of the belt and help in maintaining its alignment. High-performance rollers are typically made from durable materials like steel or high-density polyethylene (HDPE) to withstand harsh operating conditions. In the food processing industry, for example, companies like Nestlé and Tyson Foods utilize conveyor systems with stainless steel rollers to ensure hygiene and durability.
Support Structures: The support structure of a conveyor belt system is the framework that holds the idlers and rollers in place. This structure must be sturdy and well-designed to handle the weight of the materials being transported. Support structures can be made from various materials, including steel, aluminum, and reinforced plastics, depending on the application. For instance, in the automotive industry, companies like Ford and General Motors use conveyor belt support systems with robust steel frameworks to support the weight of car parts during assembly processes.
Together, these key components—idlers, rollers, and support structures—form an integrated conveyor belt support system that ensures efficient, reliable, and safe material handling. By maintaining belt alignment, preventing sagging, and reducing maintenance needs, these systems play a crucial role in optimizing the performance of conveyor operations in various industries.
For example, Flexco’s adjustable idlers and Martin Engineering’s high-impact rollers are specifically designed to enhance conveyor belt support in mining operations, where the handling of bulk materials requires robust and durable support systems. These innovations not only improve operational efficiency but also contribute to the overall safety and longevity of the conveyor system.
Ensuring that conveyor belt support systems are properly designed and maintained is essential for companies aiming to maximize productivity and minimize operational costs. By investing in high-quality components and regularly inspecting and maintaining their conveyor systems, companies can achieve significant improvements in efficiency and reliability.
The Essential Role of Impact Idlers in Conveyor Belt Support
Definition and Purpose
Impact idlers are a critical component of conveyor belt support systems, designed to protect the belt and enhance its operational efficiency. Specifically, impact idlers are rollers with extra cushioning—typically made of rubber or other shock-absorbing materials—positioned at loading and transfer points along the conveyor belt. Their primary purpose is to absorb the impact of heavy or abrasive materials falling onto the conveyor belt, thereby preventing damage to the belt and minimizing maintenance requirements.
For example, companies like Caterpillar and Joy Global in the mining industry use impact idlers extensively. In such environments, heavy rocks and minerals are frequently loaded onto conveyor belts from significant heights. Without impact idlers, the force of these materials could quickly lead to belt tears, punctures, or misalignment, causing frequent downtime and costly repairs. Impact idlers mitigate these risks by providing a resilient surface that absorbs and dissipates the kinetic energy of falling materials.
For a detailed quote on conveyor belts, please fill out the form.
Impact on Performance
The incorporation of impact idlers in conveyor belt support systems has a substantial impact on the overall performance and longevity of the conveyor belt. By absorbing shocks and reducing the force exerted on the belt, impact idlers help to minimize wear and tear, leading to extended belt life and reduced maintenance costs.
In a case study by Martin Engineering, a coal mining operation in West Virginia implemented impact idlers in their conveyor system. The result was a 40% reduction in belt damage incidents and a significant decrease in maintenance downtime. This improvement translated into cost savings of over $100,000 annually, as the need for frequent belt replacements and repairs was substantially diminished.
Impact idlers also contribute to smoother operation by maintaining a more consistent belt surface, which helps to prevent spillage and misalignment. For instance, in the food processing industry, companies like Nestlé rely on impact idlers to handle the transfer of heavy sacks of raw materials. The shock absorption provided by these idlers ensures that the belts remain stable and aligned, reducing the risk of spillage and contamination.
Installation and Maintenance
Proper installation and maintenance of impact idlers are crucial to ensure they function effectively and provide the intended benefits within the conveyor belt support system. Correct installation involves positioning the impact idlers precisely at high-impact zones, such as loading points and transfer areas, where the belt is most vulnerable to damage from falling materials.
Manufacturers like Flexco and ASGCO provide detailed guidelines and support for the installation of impact idlers. Flexco, for example, recommends that impact idlers be installed with a slight troughing angle to match the profile of the conveyor belt, ensuring maximum surface contact and shock absorption. Additionally, they advise regular inspections to check for signs of wear and tear on the idlers themselves, such as rubber degradation or bearing issues.
Routine maintenance is essential to keep impact idlers in optimal condition. This includes periodic cleaning to remove any accumulated debris, which can cause additional wear or interfere with the idlers’ performance. In environments with high levels of dust or moisture, such as cement manufacturing plants operated by companies like LafargeHolcim, more frequent maintenance checks are necessary to prevent contamination and ensure smooth operation.
Replacing worn or damaged impact idlers promptly is critical to maintaining the effectiveness of the conveyor belt support system. For example, a survey conducted by the Conveyor Equipment Manufacturers Association (CEMA) found that proactive maintenance, including timely replacement of impact idlers, could extend the life of a conveyor belt system by up to 50%, significantly reducing long-term operational costs.
The role of impact idlers in conveyor belt support systems is indispensable. They provide vital protection to the belt, enhance performance, and reduce maintenance costs through effective shock absorption. Companies across various industries, from mining to food processing, can benefit from the strategic implementation of impact idlers, ensuring their conveyor operations remain efficient and cost-effective.
Types of Conveyor Belt Support Systems
Flat vs. Troughed Designs
Conveyor belt support systems come in two primary designs: flat and troughed. Each design has its unique applications and benefits, catering to different industrial needs.
Flat belt support systems are often preferred in industries where handling light and evenly distributed materials is crucial. For example, Amazon uses flat belt support systems in their distribution centers to ensure that packages move smoothly along the sorting lines. These systems are straightforward to install and maintain, making them cost-effective for operations that prioritize speed and simplicity.
Troughed belt support systems, on the other hand, are designed to handle bulk materials over longer distances. The angled sides of the troughed design help contain loose materials, preventing spillage and ensuring efficient transport. Companies like BHP Billiton use troughed belt systems extensively in their mining operations to move large quantities of ore and other bulk materials. The increased capacity and control provided by the troughed design make it indispensable for heavy-duty applications.
High-Performance Materials
The materials used in conveyor belt support systems are critical to their performance and durability. High-performance materials like Ultra-High-Molecular-Weight (UHMW) polyethylene and stainless steel are commonly used due to their specific advantages in different industrial environments.
UHMW is favored for its exceptional durability and low friction properties. This material is particularly useful in environments where abrasion resistance is essential. For instance, in the food processing industry, companies like Tyson Foods use conveyor belt support systems with UHMW components to ensure smooth and hygienic handling of products. The low friction of UHMW helps minimize wear and tear on the belts, extending their lifespan and reducing maintenance costs.
Stainless steel, known for its strength and corrosion resistance, is another popular choice. In industries such as pharmaceuticals and chemicals, where cleanliness and resistance to corrosive substances are crucial, stainless steel conveyor belt support systems are indispensable. Pfizer, for example, employs stainless steel supports in their manufacturing plants to maintain high standards of cleanliness and durability under rigorous operating conditions.
Custom Solutions
While standard conveyor belt support systems suffice for many applications, some industries require custom solutions to address unique operational challenges. Custom conveyor belt support systems are tailored to meet specific needs, ensuring optimal performance and efficiency.
Custom solutions often involve modifications to the design, materials, or configuration of the support system. For example, in the automotive industry, companies like Toyota and General Motors require conveyor systems that can handle a variety of parts and assemblies with precision. Custom conveyor belt support systems in these settings might include specialized idlers, rollers, and support structures designed to accommodate different shapes, sizes, and weights of automotive components.
Another example is in the aerospace industry, where manufacturers like Boeing need conveyor systems that can handle delicate and high-value components. Custom support systems here might include advanced cushioning and alignment features to protect these components during transport.
To develop these custom solutions, manufacturers often work closely with their clients, conducting detailed assessments of their operational requirements. This collaborative approach ensures that the resulting conveyor belt support systems are perfectly aligned with the specific needs of the operation, leading to improved efficiency, reduced downtime, and lower overall costs.
Companies specializing in custom conveyor solutions, such as Flexco and Dorner, offer extensive expertise and a wide range of customization options. They provide tailored systems that address the unique challenges of each application, ensuring that their clients achieve the best possible performance from their conveyor belt support systems.
Custom conveyor belt support systems are essential for industries with specialized needs, ensuring that their operations run smoothly and efficiently. By investing in these tailored solutions, companies can achieve significant improvements in productivity and operational reliability.
Key Benefits of Effective Conveyor Belt Support
Improved Efficiency
Effective conveyor belt support systems are essential for enhancing the overall efficiency of conveyor operations. These systems ensure that the conveyor belt remains properly aligned and adequately supported, reducing friction and wear. By maintaining optimal belt alignment, conveyor belt support systems minimize energy consumption, leading to smoother and more efficient operations.
For instance, in the mining industry, Rio Tinto has implemented advanced conveyor belt support systems to manage the transportation of heavy loads over long distances. These systems help reduce energy consumption by ensuring that the conveyor belt operates smoothly without unnecessary resistance. The result is a significant improvement in operational efficiency, allowing Rio Tinto to transport materials more quickly and with less energy expenditure.
In the manufacturing sector, companies like Toyota utilize conveyor belt support systems to maintain high levels of productivity on their assembly lines. By keeping the conveyor belts aligned and preventing sagging, these support systems reduce the need for frequent adjustments and maintenance. This leads to fewer interruptions in the production process, allowing for continuous and efficient operation. Toyota’s implementation of robust conveyor belt support has contributed to their reputation for efficient and reliable manufacturing processes.
Enhanced Safety
Proper conveyor belt support is crucial for ensuring the safety of conveyor operations. Well-designed support systems reduce spillage, which can create hazardous working conditions. By keeping the belt properly aligned and supported, conveyor belt support systems help to minimize the risk of materials spilling onto the floor, which can cause slips, falls, and other accidents.
For example, in the food processing industry, companies like Nestlé rely on conveyor belt support systems to handle the transportation of raw materials and finished products. Effective support systems prevent spillage and contamination, ensuring that the production environment remains safe and hygienic. This not only protects workers from potential accidents but also ensures that the products meet stringent safety and quality standards.
In the logistics industry, firms like FedEx employ conveyor belt support systems to handle the high-volume movement of packages and parcels. These systems help maintain belt stability, preventing misalignment and the subsequent risk of packages falling off the conveyor. By reducing the likelihood of such incidents, FedEx can ensure the safety of their employees and the integrity of the packages they handle.
Cost Savings
One of the most significant benefits of effective conveyor belt support systems is the cost savings they can provide. By extending the life of the conveyor belt and reducing downtime, these systems help companies save on maintenance and replacement costs.
In the mining sector, companies like BHP Billiton have reported substantial cost savings through the use of advanced conveyor belt support systems. By reducing the wear and tear on their conveyor belts, BHP Billiton has been able to extend the lifespan of their equipment, reducing the frequency of expensive belt replacements. Additionally, the reduced need for maintenance has led to less downtime, allowing for more consistent and productive operations.
In the automotive industry, General Motors has also benefited from the cost savings associated with effective conveyor belt support. By implementing high-quality support systems, GM has minimized the need for frequent belt repairs and replacements. This has not only lowered their maintenance costs but also improved their overall production efficiency. The savings realized from reduced downtime and maintenance have had a positive impact on GM’s bottom line.
Effective conveyor belt support systems are a vital component of efficient, safe, and cost-effective conveyor operations. By ensuring proper belt alignment, reducing spillage, and minimizing wear and tear, these systems play a crucial role in enhancing the performance and reliability of conveyor systems across various industries. The benefits of improved efficiency, enhanced safety, and significant cost savings underscore the importance of investing in high-quality conveyor belt support systems for any operation that relies on conveyor technology.
Integrating Item Conveyor Systems with Conveyor Belt Support
Definition of Item Conveyor Systems
Item conveyor systems are specialized conveyor systems designed to transport individual items or small packages within a larger conveyor framework. These systems are essential for various industries that require precise and efficient handling of smaller units, such as manufacturing, logistics, and distribution. Unlike bulk conveyor systems that move large quantities of materials simultaneously, item conveyor systems are tailored to handle discrete items, ensuring accurate sorting, tracking, and delivery.
For example, in the e-commerce sector, companies like Amazon utilize item conveyor systems to manage the high volume of parcels in their distribution centers. These systems are designed to handle individual packages, sorting them based on destination and ensuring timely delivery. The precision and reliability of item conveyor systems are crucial for maintaining the efficiency and accuracy of such high-speed operations.
Integration with Belt Support
The seamless integration of item conveyor systems with conveyor belt support is vital for maintaining smooth and efficient operations. Conveyor belt support systems ensure that the belts remain properly aligned and stable, providing a reliable surface for item conveyors to operate. This integration minimizes disruptions, reduces wear and tear on the belts, and ensures the accurate movement of items.
One critical aspect of this integration is the use of advanced tracking and alignment technologies. For instance, companies like Siemens offer automated tracking systems that continuously monitor the alignment of the conveyor belts and make real-time adjustments. These technologies help prevent misalignment and reduce the risk of belt damage, ensuring that item conveyor systems can operate without interruptions.
Another essential component of this integration is the use of high-quality support structures. These structures are designed to handle the specific demands of item conveyor systems, providing the necessary stability and support. For example, in the automotive industry, companies like Ford use customized support structures that accommodate the varying sizes and weights of car parts. This customization ensures that the conveyor belts remain stable and that the item conveyor systems can handle the parts efficiently.
Applications and Industries
Item conveyor systems, combined with robust conveyor belt support, are essential in various industries. Their ability to handle individual items with precision and efficiency makes them indispensable in settings where accuracy and speed are critical.
In the pharmaceutical industry, companies like Pfizer use item conveyor systems to manage the movement of medicine bottles and packages within their production facilities. These systems ensure that each item is accurately tracked and handled, maintaining the integrity and safety of the products. The integration with conveyor belt support systems ensures that the belts remain stable and aligned, reducing the risk of product damage and contamination.
In the food processing industry, companies like Nestlé rely on item conveyor systems to handle individual food packages. These systems are designed to meet strict hygiene and safety standards, ensuring that the products are transported without contamination. The robust conveyor belt support systems used in these settings provide the necessary stability and alignment, ensuring smooth and efficient operations.
The logistics and distribution sector also benefits significantly from the integration of item conveyor systems with conveyor belt support. Companies like FedEx and UPS use these systems to manage the high volume of parcels in their sorting centers. The precise handling and sorting capabilities of item conveyor systems, combined with the stability provided by conveyor belt support systems, ensure that packages are processed quickly and accurately, meeting the high demands of fast-paced distribution networks.
Integrating item conveyor systems with conveyor belt support is essential for maintaining efficient, accurate, and reliable operations in various industries. By ensuring proper alignment and stability, these integrated systems enhance the performance of item conveyors, reducing downtime and maintenance costs while improving overall productivity.
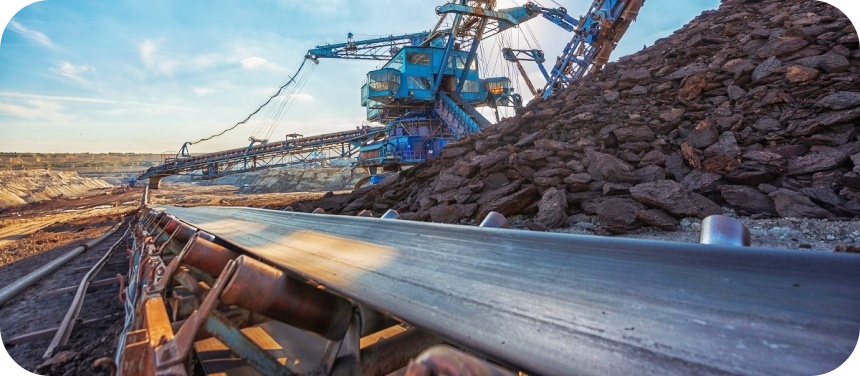
FAQs about Conveyor Belt Support
Conveyor belt support refers to the structures and mechanisms that provide stability and smooth operation to the conveyor belt system. This support is crucial for maintaining the alignment and efficiency of the belt as it transports materials across various stages of production or handling. The primary components of conveyor belt support include idlers, rollers, and frames. These elements work together to reduce friction, wear, and tear, ensuring the belt moves smoothly and efficiently.
Idlers, placed at regular intervals along the conveyor, help bear the weight of the materials on the belt and prevent sagging. Rollers, typically positioned beneath the belt, provide additional support and facilitate smooth movement. The frame or structure of the conveyor holds these components in place and ensures they are aligned correctly.
Proper conveyor belt support is essential to avoid operational disruptions, reduce maintenance costs, and extend the lifespan of the conveyor system. Regular inspection and maintenance of support components are necessary to ensure optimal performance and safety in conveyor belt operations.
Belt roller support is a crucial component of conveyor belt systems, providing the necessary backing to ensure the smooth and efficient movement of the belt. Belt rollers, also known as idler rollers or simply idlers, are cylindrical components that are strategically placed under or alongside the conveyor belt to support its weight and the load it carries. These rollers help reduce the friction between the belt and its supporting structure, minimizing wear and tear and enhancing the belt’s longevity.
There are various types of belt rollers, including carrying idlers, return idlers, and impact idlers. Carrying idlers support the loaded belt, ensuring that it remains flat and stable during operation. Return idlers support the empty belt on its return trip, preventing sagging and maintaining tension. Impact idlers are placed at loading points to absorb the impact of falling materials, protecting the belt from damage.
Effective belt roller support is essential for maintaining the alignment and tracking of the conveyor belt. It helps in distributing the load evenly, reducing the risk of belt misalignment and potential operational disruptions. Regular maintenance and inspection of belt rollers are vital to ensure their proper functioning and to avoid downtime in conveyor belt operations.
A conveyor belt pulley is a key component in conveyor belt systems, responsible for driving and directing the belt’s movement. Pulleys are typically cylindrical devices positioned at either end of the conveyor or at strategic locations along the belt’s path to control its motion and maintain tension. The primary types of pulleys include drive pulleys, which are connected to the motor and provide the force needed to move the belt, and idler pulleys, which guide and maintain tension on the belt.
Drive pulleys, also known as head pulleys, are equipped with a motor that rotates the pulley, causing the belt to move. These pulleys often have a rough or textured surface to provide better grip on the belt, preventing slippage and ensuring efficient power transmission. On the other hand, tail pulleys are usually located at the opposite end of the conveyor, helping to guide the belt back to the drive pulley.
Pulleys play a critical role in maintaining the proper tension and alignment of the conveyor belt. Properly functioning pulleys ensure smooth and continuous operation, reducing the risk of belt misalignment, slippage, and potential breakdowns. Regular inspection and maintenance of pulleys are essential to ensure the longevity and reliability of conveyor belt systems.
Keeping a conveyor belt centered is crucial for efficient and safe operation. Belt misalignment can lead to increased wear and tear, potential damage to the conveyor system, and operational disruptions. Several methods and mechanisms can be employed to ensure the belt remains centered during operation.
Firstly, proper installation and alignment of the conveyor belt are essential. Ensuring that the belt is correctly positioned on the pulleys and that the supporting structures are straight and level can prevent initial misalignment. Regular inspections and adjustments can help maintain this alignment over time.
Secondly, the use of belt tracking devices and systems can significantly aid in keeping the belt centered. Tracking rollers, also known as training idlers, are designed to automatically adjust the belt’s position by pivoting and guiding it back to the center. These rollers are strategically placed along the conveyor to detect and correct any deviations.
Additionally, adjusting the tension of the belt can help maintain its alignment. Ensuring that the tension is evenly distributed across the belt prevents one side from becoming tighter or looser than the other, which can cause the belt to veer off-center.
Regular maintenance and monitoring are crucial for identifying and correcting alignment issues early. By implementing these practices and using appropriate tracking devices, conveyor belt systems can operate smoothly and efficiently, minimizing the risk of misalignment and its associated problems.
Last Updated on August 5, 2024 by Jordan Smith
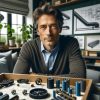
Jordan Smith, a seasoned professional with over 20 years of experience in the conveyor system industry. Jordan’s expertise lies in providing comprehensive solutions for conveyor rollers, belts, and accessories, catering to a wide range of industrial needs. From initial design and configuration to installation and meticulous troubleshooting, Jordan is adept at handling all aspects of conveyor system management. Whether you’re looking to upgrade your production line with efficient conveyor belts, require custom conveyor rollers for specific operations, or need expert advice on selecting the right conveyor accessories for your facility, Jordan is your reliable consultant. For any inquiries or assistance with conveyor system optimization, Jordan is available to share his wealth of knowledge and experience. Feel free to reach out at any time for professional guidance on all matters related to conveyor rollers, belts, and accessories.