Efficient Conveyor Belt Supporting Structure Solutions
The conveyor belt supporting structure is a critical component in ensuring the efficiency and reliability of conveyor systems. A well-designed and properly maintained conveyor belt supporting structure prevents operational issues, minimizes downtime, and extends the lifespan of the conveyor belt. This guide explores various aspects of conveyor belt supporting structures, including design considerations, documentation, and specific applications in underground and overland conveyor systems. By understanding the importance of these structures, businesses can enhance their material handling processes and ensure the long-term success of their conveyor operations.
Conveyor Belt Supporting Structure Design
Importance of Design
The design of the conveyor belt supporting structure is crucial in ensuring smooth and efficient operation. The structure supports the belt and the materials it transports, preventing sagging and misalignment, which can lead to operational inefficiencies and increased wear. A well-designed supporting structure maintains belt tension and alignment, reducing downtime and maintenance costs. For instance, a poorly designed structure can cause belt drift, leading to frequent stoppages and potential damage to the belt and other components.
Components
The conveyor belt supporting structure comprises several key components:
- Frames: The backbone of the supporting structure, frames provide the necessary rigidity and support. They are typically made from steel or aluminum to withstand heavy loads.
- Supports: These are the vertical elements that hold up the frames. They must be sturdy and properly anchored to ensure stability.
- Brackets: Connect the belt to the frame and supports, ensuring the belt remains in place. They must be durable and precisely positioned to maintain belt alignment.
Design Considerations
Several factors must be considered in the design of a conveyor belt supporting structure:
- Load Capacity: The structure must be designed to handle the maximum load it will carry, including the weight of the belt, materials, and any additional equipment.
- Environmental Conditions: The structure must withstand environmental factors such as temperature extremes, humidity, and exposure to chemicals or corrosive materials. For example, in a coastal quarry, materials resistant to corrosion from saltwater are essential.
- Material Characteristics: The properties of the materials being transported, such as weight, abrasiveness, and moisture content, influence the design. For instance, transporting heavy, abrasive materials like crushed rock requires a robust structure with reinforced supports and brackets to prevent wear and tear.
By considering these factors and ensuring each component is designed and constructed to meet specific needs, the conveyor belt supporting structure can provide reliable and efficient performance in various operational environments. Proper design not only enhances efficiency but also extends the lifespan of the conveyor system, leading to significant cost savings over time.
Conveyor Belt Supporting Structure Design PDF
Resources and Documentation
Design PDFs for conveyor belt supporting structures are essential resources for engineers and technicians. These documents provide detailed guidelines and specifications required for designing, constructing, and maintaining robust supporting structures. Access to these PDFs ensures that all components are accurately planned and implemented according to industry standards, enhancing overall system reliability.
Key Elements in Design PDFs
Design PDFs for conveyor belt supporting structures contain critical information, including:
- Specifications: Detailed measurements, material requirements, and load capacities.
- Dimensions: Exact sizing for frames, supports, and brackets to ensure proper fit and alignment.
- Materials: Recommendations for materials based on environmental conditions, such as using galvanized steel in humid environments to prevent corrosion.
For instance, a design PDF might specify using high-strength steel for frames in heavy-duty applications, ensuring the structure can support significant loads without deforming.
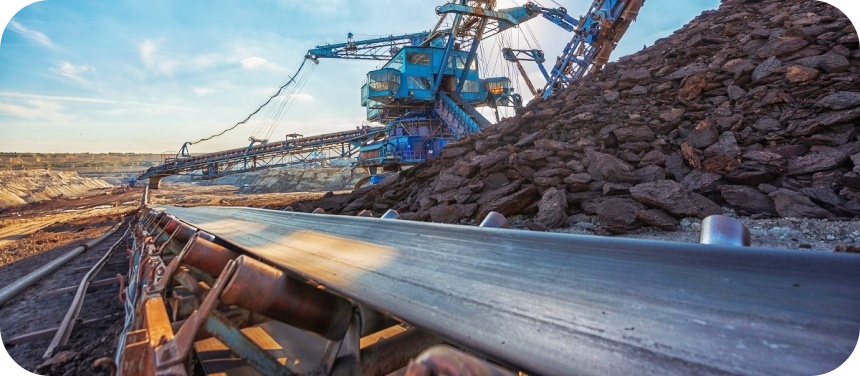
Practical Applications
In practice, these design PDFs are used to guide the installation and maintenance of conveyor belt supporting structures. Engineers and technicians rely on these documents to ensure precise assembly and alignment, preventing operational issues like belt misalignment or sagging.
For example, during the installation of a new conveyor system in a mining operation, the design PDF helps ensure that all components are correctly positioned and secured, minimizing the risk of downtime due to structural failures. Regular reference to these PDFs during maintenance can also help identify potential issues early, allowing for proactive repairs and adjustments.
Conveyor Belt Supporting Structure in Underground Conveyor Belt Systems
Challenges in Underground Systems
Designing a conveyor belt supporting structure for underground systems presents unique challenges. Space constraints often require compact and efficient designs, as tunnels and underground corridors are limited in size. Safety is a primary concern; structures must be robust enough to handle potential rock falls and seismic activity. Additionally, ventilation is crucial in underground environments to ensure air quality and temperature control. For example, in coal mines, the conveyor belt supporting structure must withstand explosive atmospheres and prevent static electricity buildup, necessitating the use of non-sparking materials and grounding systems.
The limited space and harsh conditions necessitate special design considerations. For instance, in an underground gold mine, the supporting structure must be flexible enough to navigate tight corners and uneven surfaces while maintaining the integrity and alignment of the conveyor belt. This requires precise engineering and customization for each specific environment.
Supporting Structure Requirements
The design requirements for a conveyor belt supporting structure in an underground system are stringent. Structures must be compact, allowing them to fit within the narrow confines of underground tunnels. Materials used should be corrosion-resistant to withstand the humid and sometimes chemically aggressive conditions found underground. For example, galvanized steel or stainless steel are often used due to their durability and resistance to rust and corrosion.
Compact frames are essential to maximize space utilization and ensure the structure can support the conveyor belt without obstructing the passage. These frames often incorporate modular designs for easy installation and maintenance. In an underground copper mine, for example, the supporting structure might include retractable or foldable elements to facilitate quick adjustments or repairs without disrupting operations.
The structure must also be designed to handle the weight and vibrations of the conveyor system and the transported materials. Reinforced joints and supports ensure stability and longevity. For instance, in a salt mine, the conveyor belt supporting structure must be reinforced to handle the abrasive nature of the transported material, preventing premature wear and tear.
Case Studies
Successful implementation of conveyor belt supporting structures in underground systems can be seen in various mining operations. One notable example is the use of such structures in the Grasberg mine in Indonesia, one of the world’s largest gold and copper mines. Here, the supporting structure is designed to navigate complex underground tunnels, providing stable and reliable support for the conveyor system transporting ore to the surface.
Another case study involves the Sudbury Basin in Canada, where nickel and copper mining operations utilize advanced conveyor belt supporting structures. These structures are engineered to withstand the harsh underground environment, including high humidity and temperature variations, ensuring continuous and efficient material transport.
In South Africa’s Mponeng gold mine, the deepest mine in the world, the conveyor belt supporting structure is designed to operate at extreme depths, where temperatures can rise significantly. The supporting structure incorporates special cooling systems and heat-resistant materials to ensure safe and efficient operation.
These examples highlight the importance of tailored solutions for underground conveyor belt systems, demonstrating how effective design and implementation of supporting structures can overcome the unique challenges of underground mining environments.
Overland Conveyor Systems and Conveyor Belt Supporting Structure
Scope and Scale
Overland conveyor systems are extensive and complex, relying heavily on robust conveyor belt supporting structures. These systems span long distances, often several kilometers, and are used to transport materials such as coal, minerals, and aggregate. The conveyor belt supporting structure in overland systems must be designed to handle significant loads and stresses over these long distances. For instance, an overland conveyor transporting 5,000 tons of material per hour requires a supporting structure capable of maintaining stability and alignment over varying terrains and environmental conditions. This complexity necessitates precise engineering to ensure efficient and continuous operation.
Overland conveyors often traverse challenging terrains, including mountains, valleys, and rivers, which require customized supporting structures. For example, the Grasberg mine in Indonesia utilizes overland conveyors that navigate steep gradients and difficult terrain, necessitating robust and flexible supporting structures. The design must account for both vertical and horizontal curves, ensuring the belt remains aligned and tensioned throughout its journey. This involves using advanced materials and construction techniques to create supports that can withstand environmental stresses, such as temperature fluctuations and seismic activity.
Design Specifications
Key aspects of designing the conveyor belt supporting structure for overland systems include stability, support for varying terrains, and weather resistance. Stability over long distances is achieved through a combination of strong materials, such as steel or reinforced concrete, and precise engineering. For example, supports may be spaced at intervals determined by load calculations and terrain analysis to ensure the conveyor belt remains taut and aligned.
Support for varying terrains involves designing structures that can adapt to changes in elevation and surface conditions. This may include adjustable supports and flexible joints that allow the conveyor to move smoothly over hills and through valleys. In the case of the Los Pelambres copper mine in Chile, the overland conveyor system spans over 12 kilometers and includes multiple curves and elevation changes. The supporting structure must accommodate these variations while maintaining the integrity and performance of the conveyor belt.
Weather resistance is another crucial factor. Overland conveyor belt supporting structures must withstand harsh weather conditions, including extreme temperatures, heavy rainfall, and strong winds. Materials such as galvanized steel or weather-resistant coatings are used to protect the structure from corrosion and wear. Additionally, designs may incorporate features such as wind guards and drainage systems to manage environmental impacts. For example, in the Pilbara region of Australia, overland conveyors transporting iron ore must endure high temperatures and cyclonic conditions, requiring robust and weather-resistant supporting structures.
Benefits and Applications
The primary benefit of overland conveyor systems with strong conveyor belt supporting structures is their efficiency in transporting materials over large distances. This significantly reduces the need for truck transport, leading to lower operational costs and reduced environmental impact. For instance, an overland conveyor system in a coal mining operation can eliminate the need for hundreds of truck trips daily, reducing fuel consumption and emissions.
Overland conveyors are used in various industries, including mining, aggregate production, and bulk material handling. In the mining industry, these systems transport ore from remote extraction sites to processing facilities, improving overall productivity and efficiency. For example, the Antapaccay copper mine in Peru uses overland conveyors to move ore over 6 kilometers from the pit to the concentrator plant, streamlining operations and reducing transportation costs.
In the aggregate industry, overland conveyors are used to transport sand, gravel, and crushed stone from quarries to processing plants. This enhances the efficiency of material handling and reduces the wear and tear on equipment associated with traditional truck transport. For example, a quarry in Texas uses an overland conveyor system to move aggregate from the extraction site to the processing plant, resulting in significant cost savings and increased operational efficiency.
Overland conveyor systems with well-designed conveyor belt supporting structures offer numerous benefits, including increased efficiency, reduced transportation costs, and lower environmental impact. By addressing the specific challenges and requirements of long-distance material transport, these systems play a critical role in modern industrial operations.
West River Conveyors and Conveyor Belt Supporting Structure
Company Overview
West River Conveyors is a leading provider of conveyor belt supporting structures and comprehensive conveyor systems, specializing in designing and manufacturing solutions for mining and industrial applications. Founded over 35 years ago, the company has built a reputation for engineering excellence and innovation. They offer a wide range of conveyor components, including custom-designed systems tailored to meet specific operational needs. West River Conveyors is dedicated to improving material handling efficiency and ensuring that their conveyor belt supporting structures meet the highest standards of safety and durability.
Product Offerings
West River Conveyors offers an extensive range of products designed to support various conveyor applications. Their conveyor belt supporting structures are engineered to withstand the harshest environments and heaviest loads. Products include:
- Underground Conveyor Systems: Designed for confined spaces, these systems feature compact and robust supporting structures, ideal for mining operations. For example, their underground conveyors are used in coal mines, where space and safety are critical considerations.
- Overland Conveyor Systems: These systems span long distances and require sturdy supporting structures that can handle varying terrains and environmental conditions. West River’s overland conveyors have been implemented in projects transporting materials over several kilometers, demonstrating their reliability and efficiency.
- Tail Sections: Tail sections are crucial for managing the tension and alignment of conveyor belts. West River offers customizable tail sections with adjustable frames, ensuring optimal performance for specific site requirements.
- Custom Solutions: Recognizing that each operation has unique needs, West River provides custom-designed supporting structures tailored to specific applications. They work closely with clients to develop solutions that enhance operational efficiency and reduce downtime.
Their supporting structures incorporate advanced materials and engineering techniques to ensure longevity and reduce maintenance requirements. For instance, the use of galvanized steel in their structures provides corrosion resistance, making them suitable for harsh environmental conditions.
Customer Support and Services
West River Conveyors prides itself on providing exceptional customer support and services. They offer 24/7 customer assistance to address any issues promptly, minimizing operational disruptions. Their support team is knowledgeable and experienced, ready to assist with installation, troubleshooting, and maintenance of conveyor systems.
- Custom Design Services: West River offers custom design services to ensure that their conveyor belt supporting structures meet the specific needs of each client. This involves a thorough analysis of the operational requirements, site conditions, and material characteristics to develop a tailored solution.
- Maintenance and Training: The company provides comprehensive maintenance services and training programs to help clients maintain their conveyor systems in peak condition. This includes scheduled inspections, preventive maintenance, and emergency repairs. For example, their training programs cover the proper installation and alignment of conveyor belt supporting structures, ensuring that staff can manage and maintain the systems effectively.
- Technical Support: In addition to on-site services, West River offers technical support via phone and online resources. Their technical team can provide guidance on troubleshooting common issues, optimizing system performance, and upgrading existing systems to enhance efficiency.
By focusing on customer needs and providing robust support services, West River Conveyors ensures that their conveyor belt supporting structures deliver reliable performance and long-term value. Their commitment to quality and customer satisfaction has made them a trusted partner in the mining and industrial sectors.
Overland Conveyor Belt Supporting Structure
Advantages of Overland Conveyors
Overland conveyors provide several advantages, primarily by reducing operational costs and environmental impact. These conveyor systems transport materials over long distances, often eliminating the need for extensive truck fleets. For instance, using an overland conveyor instead of trucks can significantly lower fuel costs and reduce emissions, contributing to a smaller carbon footprint. Overland conveyors also offer higher efficiency, as they provide a continuous flow of materials, minimizing delays associated with truck loading and unloading.
In terms of maintenance, overland conveyors are more cost-effective. Trucks require frequent servicing and fuel, whereas conveyor systems need periodic inspections and minor adjustments. For example, a mining operation using an overland conveyor can reduce operational costs by up to 40% compared to traditional truck hauling. Additionally, the conveyor belt supporting structure ensures the stability and durability of the system, further enhancing its cost-effectiveness and reliability.
Design and Installation
Designing and installing a conveyor belt supporting structure for overland conveyors involves several key considerations:
- Stability: The supporting structure must be robust enough to handle the weight and movement of the conveyor belt over long distances. This includes using materials like reinforced steel and concrete for the supports and frames.
- Terrain Adaptability: Overland conveyors often traverse varied terrains, including hills, valleys, and rivers. The supporting structure must be adaptable, with adjustable supports and flexible joints to accommodate changes in elevation and ground conditions.
- Weather Resistance: Given that overland conveyors are exposed to the elements, the supporting structure must withstand harsh weather conditions. This includes using weather-resistant materials and coatings to prevent corrosion and damage from sun, rain, and wind.
For instance, in the installation of an overland conveyor system at a limestone quarry, the supporting structure was designed with elevated trusses to cross a river, utilizing corrosion-resistant materials to ensure longevity and performance. The design also included windbreaks to protect the belt from strong winds.
Real-World Examples
Several case studies illustrate the effectiveness of overland conveyor belt supporting structures:
- Grasberg Mine, Indonesia: This mine uses overland conveyors to transport ore over complex terrains. The supporting structures are engineered to navigate steep gradients and difficult terrains, ensuring stable and efficient material transport.
- Antapaccay Copper Mine, Peru: An overland conveyor system here spans over 6 kilometers, transporting ore from the pit to the concentrator plant. The supporting structure is designed to handle the high load and varying terrain, significantly reducing transportation costs and improving operational efficiency.
- Los Pelambres Mine, Chile: This mine utilizes overland conveyors to move copper ore across challenging terrains, including steep hills and valleys. The supporting structure incorporates flexible joints and robust materials, ensuring continuous and efficient operation despite environmental challenges.
These examples demonstrate how well-designed conveyor belt supporting structures enhance the performance and reliability of overland conveyor systems, providing substantial operational and environmental benefits across various industries.
Fill out the inquiry form to explore custom conveyor belt solutions.
FAQs about Conveyor Belt Supporting Structure
The conveyor belt supporting structure is essential for the proper functioning and longevity of the conveyor system. It typically consists of several key components:
Frame: The main support of the conveyor that holds all other components in place. It’s usually made of metal, such as steel or aluminum, providing the necessary strength and rigidity.
Idlers: These are rollers that support the conveyor belt and its load while maintaining its alignment and tension. Idlers are spaced throughout the length of the conveyor and can be adjusted to manage the belt’s path.
Drive Unit: This includes the motor and the gearbox, which are critical for moving the conveyor belt at the desired speed. The drive unit is usually mounted at one end of the conveyor.
Belt Support: For longer conveyor systems, additional support slats or panels are placed beneath the belt to prevent sagging and reduce stress on the belt itself.
Leg Supports: These are necessary to maintain the stability and level of the conveyor. Adjustable legs can accommodate different terrains and heights.
These components work together to ensure that the conveyor belt operates smoothly and efficiently, with minimal downtime and maintenance needs.
A conveyor belt system is composed of various integrated parts that work together to move goods and materials from one point to another. The primary parts include:
Conveyor Belt: The moving platform which carries the load. It’s made from various materials such as rubber, fabric, or metal.
Pulleys: These are used to drive the belt, adjust its direction, and maintain tension. They are located at the ends of the conveyor system.
Motors: These provide the power to the pulleys and are typically electric.
Belt Cleaners: Located at the discharge end of the conveyor, these help keep the belt clean, which prolongs its life and prevents material build-up.
Safety Guards and Sensors: These are crucial for preventing accidents and ensuring the system operates safely.
Understanding the parts of the conveyor system is crucial for troubleshooting and performing maintenance effectively.
Conveyor belts run on a system of rotating rollers and pulleys which are part of the conveyor belt supporting structure. Here’s a detailed look at what supports the conveyor belt:
Rollers: These cylindrical components are spaced along the length of the conveyor to support the belt and guide it as it moves.
Pulleys: Located at either end of the conveyor, these are responsible for the movement of the belt. The drive pulley is powered, moving the belt, while the tail pulley is usually free-spinning.
Slide Bed or Roller Bed: Depending on the type of conveyor, the belt may run on a smooth metal plate (slide bed) or a series of rollers (roller bed), both of which reduce friction and wear on the belt.
Rails: In some conveyor models, especially those used in inclined or declined transportation, side rails are added to ensure that materials stay on the belt.
These elements are meticulously designed to ensure efficient operation and to minimize wear and tear on the belt.
Belt roller support refers to the use of rollers placed beneath the conveyor belt to provide support, reduce sagging, and facilitate smooth and efficient belt movement. The specifics include:
Support Rollers: These are strategically placed to distribute the weight of the load and the belt evenly. This prevents excessive stress and deformation of the belt.
Impact Rollers: Located at points where materials are loaded onto the belt, these rollers are designed to absorb the shock and impact of falling materials, thereby protecting the belt and the structure.
Return Rollers: These are used on the underside of the conveyor belt to guide and support the belt as it returns after depositing its load.
Belt roller support is crucial for maintaining the integrity and performance of the conveyor belt, reducing downtime, and increasing the system’s overall efficiency and lifespan.
Last Updated on August 2, 2024 by Jordan Smith
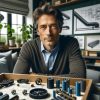
Jordan Smith, a seasoned professional with over 20 years of experience in the conveyor system industry. Jordan’s expertise lies in providing comprehensive solutions for conveyor rollers, belts, and accessories, catering to a wide range of industrial needs. From initial design and configuration to installation and meticulous troubleshooting, Jordan is adept at handling all aspects of conveyor system management. Whether you’re looking to upgrade your production line with efficient conveyor belts, require custom conveyor rollers for specific operations, or need expert advice on selecting the right conveyor accessories for your facility, Jordan is your reliable consultant. For any inquiries or assistance with conveyor system optimization, Jordan is available to share his wealth of knowledge and experience. Feel free to reach out at any time for professional guidance on all matters related to conveyor rollers, belts, and accessories.