Detailed Conveyor Belt System Definition Insights
A conveyor belt system is a critical component in various industries, enabling the efficient transport of materials across different stages of production. This blog post will provide a comprehensive conveyor belt system definition, exploring its historical development and importance in modern industry. Understanding the conveyor belt system definition is crucial as these systems minimize labor costs, enhance productivity, and ensure the smooth operation of industrial processes. By delving into the details of different conveyor types, their applications, and calculation methods, we aim to offer a thorough understanding of how these systems function and their significance in today’s industrial landscape.
Conveyor Belt System Definition: Types and Applications
Overview of Various Types of Conveyor Belts
Conveyor belt systems are essential in modern industry, offering numerous benefits such as increased efficiency and reduced labor costs. The conveyor belt system definition encompasses a variety of belt types designed for different applications and industries. Understanding these types is crucial for selecting the right system for specific needs.
Description and Uses of Different Conveyor Belt Types
Flat Belt
Flat belts are the most common type of conveyor belt, featuring a simple design that is versatile and easy to maintain. They are typically made of rubber or synthetic materials and are used in various industries, including manufacturing, food processing, and packaging.
Uses:
Flat belts are ideal for transporting light to medium-weight items. In the food industry, companies like Nestlé use flat belts to move packaged goods through production lines. In manufacturing, flat belts are used to transport components between assembly stations.
Advantages:
- Simple and cost-effective design
- Easy to install and maintain
- Versatile for different industries
Limitations:
- Not suitable for heavy or abrasive materials
- Limited in handling inclined or curved paths
Modular Belt
Modular belts are composed of interlocking plastic segments, providing flexibility and durability. They are commonly used in industries requiring frequent cleaning and sanitation, such as food processing and pharmaceuticals.
Uses:
Modular belts are used for transporting items that require frequent cleaning or are subject to spills. For instance, companies like Tyson Foods use modular belts in their meat processing plants due to the ease of cleaning and maintenance.
Advantages:
- Easy to clean and sanitize
- Flexible design allows for complex routing
- Durable and resistant to corrosion
Limitations:
- Higher initial cost compared to flat belts
- Requires more complex maintenance procedures
Cleated Belt
Cleated belts feature vertical cleats or ribs along their surface, providing additional grip and stability for transporting loose or bulky materials. They are commonly used in agriculture, mining, and recycling industries.
Uses:
Cleated belts are ideal for moving bulk materials such as grains, ores, and waste. For example, John Deere uses cleated belts in their agricultural machinery to transport harvested crops.
Advantages:
- Enhanced grip for moving bulk materials
- Prevents material slippage and spillage
- Suitable for inclined transport
Limitations:
- More complex design and higher cost
- Increased wear and tear on cleats
Curved Belt
Curved belts are designed to navigate turns and bends within a conveyor system, allowing for flexible layout designs. They are used in industries where space optimization and efficient routing are essential, such as airports and distribution centers.
Uses:
Curved belts are commonly used in airport baggage handling systems, such as those implemented by Siemens at major international airports. They help efficiently route luggage through complex terminal layouts.
Advantages:
- Optimizes space and layout flexibility
- Smooth and efficient handling of turns
- Reduces the need for multiple straight belts
Limitations:
- Higher cost due to specialized design
- More complex installation and maintenance
Advantages and Limitations of Each Type
Understanding the advantages and limitations of each conveyor belt type is vital for choosing the right system based on specific operational needs. The conveyor belt system definition varies across different types, each offering unique benefits and challenges.
Selecting the appropriate conveyor belt system requires a thorough understanding of the conveyor belt system definition and the specific needs of the operation. Companies like Amazon and FedEx rely on a combination of these conveyor belt types to ensure efficient and reliable material handling across their facilities, demonstrating the critical role of these systems in modern industry.
Conveyor Belt System Definition: Detailed Conveyor Belt Definition
Detailed Definition of a Conveyor Belt
A conveyor belt is a fundamental component within a conveyor belt system, designed to move materials from one location to another efficiently and seamlessly. According to the conveyor belt system definition, a conveyor belt typically consists of a continuous loop of material that is driven by pulleys and supported by rollers, enabling the smooth transport of various goods and materials. This definition is essential in understanding how conveyor belts function within larger systems and the pivotal role they play in industrial processes.
Conveyor belts are integral to a wide range of industries, including manufacturing, mining, food processing, and logistics. For instance, in the automotive industry, companies like Ford utilize conveyor belts to move car parts through assembly lines, ensuring consistent and efficient production. This application of the conveyor belt system definition highlights its versatility and critical importance in modern industrial operations.
Materials Used in Conveyor Belts
The materials used in conveyor belts are crucial to their performance, durability, and suitability for different applications. The conveyor belt system definition encompasses various materials, each selected based on specific operational requirements and environmental conditions.
- Rubber: Commonly used for general-purpose conveyor belts, rubber offers excellent flexibility and resistance to wear and tear. It is ideal for transporting bulk materials in industries such as mining and construction. For example, ContiTech, a leading manufacturer, produces high-quality rubber conveyor belts that are used in mining operations worldwide.
- PVC (Polyvinyl Chloride): PVC belts are known for their durability, lightweight properties, and resistance to chemicals and oils. They are widely used in the food processing industry, where hygiene and easy cleaning are paramount. Ammeraal Beltech, a renowned company, provides PVC conveyor belts that meet strict food safety standards.
- PU (Polyurethane): PU belts are highly flexible and resistant to abrasion, making them suitable for applications requiring high precision and cleanliness, such as pharmaceuticals and electronics manufacturing. Habasit, a major player in the industry, offers a range of PU belts for these specialized sectors.
- Metal: Metal belts, typically made of stainless steel, are used in environments requiring high strength, heat resistance, and sanitary conditions. They are prevalent in the baking and metalworking industries. Wire Belt Company manufactures robust metal conveyor belts for these demanding applications.
The choice of material significantly impacts the performance and longevity of the conveyor belt, aligning with the conveyor belt system definition’s emphasis on efficiency and reliability.
Manufacturing Process of Conveyor Belts
The manufacturing process of conveyor belts is a critical aspect of ensuring their quality and performance. The conveyor belt system definition involves several steps, each contributing to the final product’s durability and functionality.
- Design and Engineering: The process begins with designing the conveyor belt to meet specific operational needs. This includes selecting the appropriate materials, determining the belt’s dimensions, and specifying any special features such as cleats or sidewalls.
- Material Preparation: Raw materials, such as rubber, PVC, PU, or metal, are prepared according to the design specifications. This involves processes like cutting, extruding, and laminating to form the belt’s layers.
- Fabrication: The prepared materials are then assembled and bonded together using heat, pressure, or chemical adhesives. For example, rubber belts are typically vulcanized, a process that involves applying heat and pressure to cure the rubber and enhance its strength and flexibility.
- Testing and Quality Control: The fabricated conveyor belts undergo rigorous testing to ensure they meet industry standards and performance criteria. Tests may include tensile strength, abrasion resistance, and flexibility. Leading manufacturers like Flexco implement comprehensive quality control measures to deliver reliable conveyor belts.
- Finishing and Customization: The final step involves adding any necessary features such as cleats, sidewalls, or perforations. The belts are then cut to the required lengths and widths and prepared for shipment to customers.
Key Components of a Conveyor Belt System: Pulleys, Rollers, and Belts
The conveyor belt system definition is incomplete without understanding its key components: pulleys, rollers, and belts. Each component plays a vital role in the system’s overall functionality and efficiency.
- Pulleys: Pulleys are the driving force behind the conveyor belt. They are positioned at either end of the conveyor system and are responsible for moving the belt. Drive pulleys are powered by motors and transmit motion to the belt, while idler pulleys provide support and tension. For example, Flexco’s conveyor belt systems incorporate high-quality pulleys that ensure smooth and efficient operation.
- Rollers: Rollers support the conveyor belt and facilitate its movement. They are strategically placed along the conveyor’s length to minimize friction and wear on the belt. Rollers are available in various materials and configurations to suit different applications. Rexnord, a prominent manufacturer, supplies durable rollers that enhance the longevity and performance of conveyor systems.
- Belts: The belt itself is the central component that transports materials. It must be strong, flexible, and suitable for the specific materials it will carry. The conveyor belt system definition emphasizes the belt’s critical role in ensuring efficient and reliable transport across various industries.
Understanding these components and their functions is essential for comprehending the full conveyor belt system definition. Companies like Siemens and Honeywell leverage advanced conveyor belt systems in their operations, showcasing the importance of these systems in achieving high productivity and operational efficiency.
Conveyor Belt System Definition: Chain Conveyor
Definition and Working Principle of Chain Conveyors
A chain conveyor is a type of conveyor system that uses chains to move materials along a set path. According to the conveyor belt system definition, chain conveyors consist of a series of interconnected links, driven by sprockets, that transport goods. These systems are particularly effective for handling heavy loads and are widely used in industrial settings where durability and reliability are paramount.
The working principle of a chain conveyor involves a motor that drives a chain or set of chains, which are looped around sprockets at each end of the conveyor. The movement of the chains carries materials placed on attachments or directly on the chains themselves. This mechanism allows for precise control of the speed and movement of the conveyed items. For example, Daifuku, a leading manufacturer, uses chain conveyors in their automated warehouse systems to ensure the efficient and reliable transport of heavy pallets and containers.
Comparison Between Chain Conveyors and Belt Conveyors
While both chain conveyors and belt conveyors fall under the broader conveyor belt system definition, they have distinct differences in terms of design, functionality, and applications. Understanding these differences is crucial for selecting the appropriate system for specific industrial needs.
- Design and Construction: Chain conveyors are built with robust metal chains and sprockets, making them suitable for heavy-duty applications. In contrast, belt conveyors use a continuous loop of material, typically rubber or synthetic, to move items. This fundamental design difference impacts their respective strengths and weaknesses.
- Load Capacity: Chain conveyors can handle much heavier loads compared to belt conveyors. They are ideal for applications that involve transporting bulky or heavy materials, such as automotive parts or heavy machinery components. For instance, the automotive industry often uses chain conveyors to move car frames and engines along the production line.
- Maintenance and Durability: Chain conveyors are generally more durable and require less frequent maintenance than belt conveyors, particularly in harsh environments. However, when maintenance is required, it can be more complex and time-consuming. Belt conveyors, while easier to maintain, may wear out faster under heavy loads or abrasive materials.
- Flexibility and Versatility: Belt conveyors offer greater flexibility in terms of routing and can easily accommodate inclines, declines, and curves. Chain conveyors, on the other hand, are typically used for straight-line transport but can be designed to handle more complex paths with appropriate modifications.
Applications of Chain Conveyors in Various Industries
Chain conveyors are used in a wide range of industries due to their strength and reliability. The conveyor belt system definition emphasizes the importance of these conveyors in scenarios where heavy loads need to be transported efficiently and safely.
- Automotive Industry: Chain conveyors are extensively used in automotive manufacturing plants to transport car bodies, engines, and other heavy components. Companies like Toyota and General Motors rely on these systems for their production lines, ensuring a smooth flow of materials and efficient assembly processes.
- Mining and Quarrying: In the mining industry, chain conveyors are used to transport ores, coal, and other bulk materials from one location to another. Caterpillar, a major player in the mining equipment sector, uses robust chain conveyor systems to handle the extreme conditions of underground and surface mining operations.
- Heavy Manufacturing: Industries that involve heavy manufacturing, such as steel production or shipbuilding, utilize chain conveyors to move large and heavy parts. For example, ArcelorMittal, one of the world’s largest steel producers, employs chain conveyors to transport raw materials and finished steel products within their facilities.
- Warehousing and Distribution: Chain conveyors are also used in warehouses and distribution centers for moving heavy pallets and containers. Companies like Amazon and DHL implement these systems to enhance their logistics operations, ensuring timely and efficient handling of goods.
Advantages and Challenges of Using Chain Conveyors
Chain conveyors offer several advantages, making them a preferred choice for specific applications, but they also come with certain challenges that need to be considered.
Advantages:
- High Load Capacity: Chain conveyors can transport very heavy and bulky materials that belt conveyors cannot handle efficiently. This makes them ideal for industries dealing with large-scale production and heavy goods.
- Durability and Longevity: Built from robust materials like steel, chain conveyors are highly durable and can withstand harsh working conditions, including high temperatures and abrasive materials. This durability translates to longer operational life and reduced downtime.
- Precision and Control: Chain conveyors offer precise control over the movement of materials, which is essential in manufacturing processes that require exact positioning and timing. This precision is critical in assembly lines and production processes.
Challenges:
- Complex Maintenance: While chain conveyors are durable, when maintenance is required, it can be complex and time-consuming. The interconnected nature of the chains and the need for proper lubrication and alignment can pose challenges.
- Higher Initial Costs: The robust construction and specialized components of chain conveyors result in higher initial costs compared to belt conveyors. This higher upfront investment can be a barrier for smaller businesses or those with limited budgets.
- Limited Flexibility: Chain conveyors are less flexible in terms of routing and design modifications. They are typically used for straight-line transport, and adapting them to handle curves or inclines can be challenging and costly.
Understanding the full scope of the conveyor belt system definition, including the specificities of chain conveyors, is essential for selecting the right conveyor system for industrial applications. Companies like Ford and Amazon illustrate the practical benefits of using chain conveyors in their operations, highlighting their critical role in enhancing efficiency and productivity.
Conveyor Belt System Definition: Conveyor Belt Nederlands
Explanation of the Term “Conveyor Belt” in Dutch (Nederlands)
The term “conveyor belt” in Dutch is “transportband.” This term falls within the broader conveyor belt system definition, describing a mechanism used to move goods and materials from one point to another efficiently. The Dutch term “transportband” is used across various industries, reflecting the widespread adoption and importance of conveyor systems in the Netherlands. These systems are crucial for optimizing logistics, reducing labor costs, and enhancing production efficiency.
In the Dutch context, the conveyor belt system definition remains consistent with its global understanding. It includes various types of belts, such as flat belts, modular belts, and chain conveyors, each designed to meet specific industrial needs. Understanding the term “transportband” helps in recognizing the critical role these systems play in Dutch industries, ranging from manufacturing to food processing.
Overview of the Dutch Conveyor Belt Industry
The Netherlands boasts a robust conveyor belt industry, characterized by innovation, quality, and a focus on sustainability. The conveyor belt system definition in the Dutch industry encompasses a wide range of applications, from agriculture to high-tech manufacturing. Dutch companies are renowned for their engineering prowess and commitment to environmental standards, making them leaders in conveyor belt technology.
Industry Characteristics:
- Innovation and Technology: The Dutch conveyor belt industry is known for its innovative approaches. Companies invest heavily in research and development to create advanced conveyor systems that meet the evolving needs of modern industries. For example, Vanderlande, a Dutch company, specializes in designing automated logistics systems, including advanced conveyor belts that are used in airports and warehouses worldwide.
- Sustainability: Dutch manufacturers place a significant emphasis on sustainability. Conveyor belts are designed to be energy-efficient, reducing the overall carbon footprint. Materials used in these belts are often recyclable, and production processes adhere to stringent environmental regulations. This focus on sustainability is a hallmark of the Dutch approach to manufacturing.
- Quality and Reliability: Quality assurance is a critical component of the Dutch conveyor belt industry. Manufacturers implement rigorous testing procedures to ensure that their products meet high standards of performance and durability. This commitment to quality has earned Dutch conveyor belt manufacturers a reputation for reliability and excellence.
Notable Dutch Conveyor Belt Manufacturers and Their Contributions
Several Dutch companies are prominent in the global conveyor belt market, contributing significantly to advancements in conveyor technology and setting industry standards.
Vanderlande:
Vanderlande is a leading global supplier of logistics automation systems, including conveyor belts. The company’s systems are used in various industries, such as airports, warehousing, and parcel handling. Vanderlande’s conveyor belt system definition includes innovative features like automated sorting and high-speed transport, which enhance operational efficiency and accuracy.
- Example: Vanderlande’s automated baggage handling systems are used in major international airports, including Schiphol Airport in Amsterdam. These systems ensure the efficient and reliable transport of luggage, handling millions of bags annually.
Ammeraal Beltech:
Ammeraal Beltech is another key player in the Dutch conveyor belt industry. The company specializes in manufacturing high-performance conveyor belts for diverse applications, including food processing, logistics, and manufacturing. Ammeraal Beltech is known for its extensive range of products, which cater to specific industry requirements.
- Example: In the food processing industry, Ammeraal Beltech provides hygienic conveyor belts that meet strict food safety standards. These belts are used by companies like FrieslandCampina, a major Dutch dairy producer, to ensure safe and efficient handling of food products.
Habasit Nederland:
Habasit Nederland is part of the global Habasit Group, offering a wide range of conveyor and processing belts. The company focuses on providing customized solutions to meet the unique needs of its clients. Habasit Nederland’s products are used in various sectors, including automotive, textile, and paper industries.
- Example: In the automotive industry, Habasit Nederland supplies conveyor belts to manufacturers like VDL Nedcar, ensuring efficient transport of car components along the assembly line.
Contributions and Impact
Dutch conveyor belt manufacturers have made significant contributions to the global market, influencing industry standards and practices. Their focus on innovation, quality, and sustainability sets them apart, making them preferred partners for businesses worldwide.
- Innovation: Dutch companies are at the forefront of integrating cutting-edge technologies into conveyor systems. This includes the use of sensors, automation, and smart technology to enhance the functionality and efficiency of conveyor belts.
- Global Reach: The products and solutions offered by Dutch manufacturers are used globally, reflecting their reliability and high performance. This global presence underscores the importance of the Dutch conveyor belt industry in the international market.
- Sustainability: By prioritizing environmentally friendly practices, Dutch manufacturers contribute to the global effort to reduce industrial carbon footprints. This commitment to sustainability resonates with modern businesses seeking eco-friendly solutions.
Understanding the conveyor belt system definition within the context of the Dutch industry provides valuable insights into how these systems are developed, implemented, and continuously improved to meet the dynamic needs of various sectors. Dutch companies like Vanderlande, Ammeraal Beltech, and Habasit Nederland exemplify the excellence and innovation that define the conveyor belt industry in the Netherlands.
Conveyor Belt System Definition: Bulk Material Handling Systems
Definition and Significance of Bulk Material Handling Systems
Bulk material handling systems are integral to various industries, enabling the efficient movement, storage, and control of large quantities of materials. The conveyor belt system definition in the context of bulk material handling encompasses a range of mechanical devices designed to transport bulk materials such as coal, minerals, grains, and other loose goods. These systems are critical for optimizing productivity, reducing labor costs, and ensuring the safe handling of materials.
The significance of bulk material handling systems lies in their ability to handle large volumes of materials with minimal human intervention, thus enhancing operational efficiency and safety. Industries such as mining, agriculture, and manufacturing rely heavily on these systems to maintain continuous production processes and meet high demand. For instance, in the mining industry, companies like Rio Tinto use bulk material handling systems to transport extracted ores from mines to processing plants efficiently.
Role of Conveyor Belts in Bulk Material Handling
Conveyor belts play a pivotal role in bulk material handling systems. According to the conveyor belt system definition, these belts provide a continuous and reliable means of transporting bulk materials over long distances and through various stages of processing. Conveyor belts are designed to handle different types of materials, ensuring that they are moved efficiently from one point to another.
- Efficient Transport: Conveyor belts enable the smooth and continuous movement of bulk materials, reducing the need for manual handling and minimizing the risk of spillage and loss. This efficiency is particularly important in industries where large volumes of materials must be transported quickly and safely.
- Cost-Effective Operation: By automating the transport process, conveyor belts help reduce labor costs and increase productivity. For example, Cargill, a global food corporation, uses conveyor belts in its grain handling facilities to streamline operations and reduce labor-intensive tasks.
- Safety and Reliability: Conveyor belts enhance workplace safety by reducing the need for manual handling of heavy and potentially hazardous materials. They are designed to operate reliably under various conditions, ensuring minimal downtime and consistent performance.
Types of Materials Handled Using Conveyor Belts
The conveyor belt system definition extends to various types of materials commonly handled in bulk material handling systems. Each type of material requires specific belt characteristics to ensure efficient and safe transport.
- Minerals and Ores: Conveyor belts are extensively used in the mining industry to transport minerals and ores from extraction sites to processing plants. These belts must be robust and resistant to abrasion to handle the rough and heavy nature of mined materials. Companies like BHP Billiton employ heavy-duty conveyor belts in their mining operations to move large quantities of ore efficiently.
- Grains and Agricultural Products: In the agriculture sector, conveyor belts are used to transport grains, seeds, and other agricultural products. These belts are designed to be gentle on the materials to prevent damage. AGI, a leading agricultural equipment manufacturer, provides specialized conveyor belts that ensure the safe and efficient handling of grains during harvest and storage.
- Construction Materials: Conveyor belts are also used to move construction materials such as sand, gravel, and cement. These materials require belts that can withstand heavy loads and abrasive conditions. For example, LafargeHolcim utilizes conveyor belts in its cement production facilities to transport raw materials and finished products seamlessly.
- Chemicals and Fertilizers: The chemical industry relies on conveyor belts to handle bulk chemicals and fertilizers. These belts must be resistant to chemical corrosion and capable of handling fine powders and granules. Yara International, a major fertilizer producer, uses conveyor belts designed for chemical resistance and precision handling.
Industrial Applications and Examples
Conveyor belts are crucial components in various industrial applications, providing reliable and efficient transport solutions for bulk materials. Understanding the conveyor belt system definition helps in recognizing the diverse applications and the impact of these systems on different industries.
- Mining Industry: In mining, conveyor belts are used to transport extracted ores and minerals. Rio Tinto, one of the largest mining companies, employs extensive conveyor systems to move ore from mines to processing plants, ensuring continuous and efficient operations.
- Agriculture and Food Processing: Conveyor belts facilitate the handling of agricultural products from harvest to processing and storage. Companies like Cargill use conveyor belts in their grain handling operations to ensure efficient transport and minimize waste.
- Construction and Cement Industry: Conveyor belts are used to transport raw materials and finished products in construction and cement production. LafargeHolcim employs conveyor systems in its plants to move materials such as limestone, sand, and cement, improving operational efficiency and reducing manual labor.
- Chemical and Fertilizer Industry: Conveyor belts are essential for handling bulk chemicals and fertilizers, ensuring safe and precise transport. Yara International uses specialized conveyor belts that meet the stringent requirements of handling chemical products and fertilizers.
- Ports and Terminals: Conveyor belts are used in ports and terminals to handle bulk cargo such as coal, grain, and minerals. These systems streamline the loading and unloading processes, enhancing the efficiency of port operations. For example, the Port of Rotterdam, one of the largest ports in the world, utilizes advanced conveyor belt systems to manage the high volume of bulk cargo efficiently.
The conveyor belt system definition encompasses a wide range of applications and industries, demonstrating the versatility and critical importance of these systems in modern industrial operations. By understanding the specific needs of different materials and industries, companies can select the appropriate conveyor belt systems to enhance productivity, safety, and efficiency.
Conveyor Belt System Definition: Conveyor Belt Calculation
Importance of Proper Conveyor Belt Calculations
Accurate conveyor belt calculations are crucial for the efficient and safe operation of any conveyor system. The conveyor belt system definition includes ensuring that the belt operates within its design parameters to avoid overloading, excessive wear, and potential failures. Proper calculations help in optimizing the system’s performance, reducing energy consumption, and prolonging the lifespan of the conveyor belt.
For instance, in large-scale distribution centers like those operated by Amazon, precise conveyor belt calculations ensure that the vast network of belts can handle the high volume of packages without interruption. Miscalculations could lead to system downtimes, affecting delivery schedules and increasing operational costs.
Key Factors in Conveyor Belt Calculations
Several key factors must be considered when calculating conveyor belt specifications to align with the conveyor belt system definition. These factors include load, speed, tension, and power requirements.
Load
The load is one of the most critical factors in conveyor belt calculations. It includes both the weight of the material being transported and the belt itself. The total load impacts the belt’s durability and the motor power needed to move it. For example, in a coal mining operation where large quantities of ore are transported, the load calculation must account for the high weight to ensure the belt can handle the strain without excessive wear.
Speed
The speed of the conveyor belt must be calculated to match the requirements of the production process. If the belt moves too quickly, it might lead to material spillage or damage. Conversely, a belt that moves too slowly can bottleneck the entire operation. For instance, in a food processing plant, conveyor belts must move at precise speeds to ensure proper handling and packaging of products, which is crucial for maintaining quality and safety standards.
Tension
Tension calculations are vital to prevent the belt from sagging or slipping off the pulleys. The correct tension ensures that the belt runs smoothly and efficiently. This factor is particularly important in systems with long conveyor belts, such as those used in the transportation of minerals over long distances. Improper tension can lead to belt misalignment and increased wear and tear.
Power Requirements
Power requirements are calculated based on the load, speed, and tension factors. This calculation determines the size and type of motor needed to drive the conveyor belt efficiently. For example, in a steel manufacturing plant, conveyor belts used to transport heavy steel rolls require powerful motors. The power requirements calculation ensures that the motors are sufficient to handle the load without consuming excessive energy.
Tools and Methods for Calculating Conveyor Belt Specifications
Several tools and methods are available to assist in the precise calculation of conveyor belt specifications. These tools help engineers design systems that meet the exact needs of their operations, in line with the conveyor belt system definition.
Conveyor Design Software
Modern conveyor design software, such as FlexSim and Sidewinder Conveyor Design Software, allows engineers to model and simulate conveyor systems. These tools take into account various parameters, including load, speed, tension, and power requirements, to provide accurate calculations and design recommendations.
Analytical Methods
Analytical methods involve using mathematical formulas and engineering principles to calculate conveyor belt specifications. These methods are often used in conjunction with software tools to verify results and ensure accuracy. Formulas for calculating belt tension, power requirements, and load capacity are standard in conveyor design handbooks and industry guidelines.
Field Measurements
In addition to theoretical calculations, field measurements are essential for validating the design assumptions and ensuring that the conveyor system operates as intended. Techniques such as belt tension measurement, load testing, and speed monitoring help in fine-tuning the system after installation.
Examples of Calculation Scenarios for Different Industries
Understanding how conveyor belt calculations apply to different industries can provide practical insights into their importance and implementation.
Mining Industry
In the mining industry, conveyor belts are used to transport ores from extraction sites to processing plants. Calculations must account for the heavy loads, long distances, and harsh environmental conditions. For example, a conveyor belt in a copper mine must be designed to handle the weight of the ore and the rugged terrain, ensuring continuous and efficient operation.
Food Processing Industry
In the food processing industry, conveyor belts are used to move products through various stages of production, from raw material handling to packaging. Calculations for these systems must ensure that belts move at precise speeds to avoid damaging delicate products like fruits and vegetables. Companies like Nestlé use conveyor belts that are carefully calculated to maintain product quality and hygiene standards.
Manufacturing Industry
In manufacturing, conveyor belts are used to transport parts and assemblies along production lines. Accurate calculations ensure that the belts can handle the variable loads and speeds required at different stages of production. For instance, in an automotive assembly plant, conveyor belts must be designed to transport heavy car parts efficiently while maintaining the pace of production.
Distribution Centers
In distribution centers, conveyor belts play a critical role in sorting and moving packages. Calculations must consider the high volume and diverse range of package weights. Companies like FedEx rely on conveyor belts that are precisely calculated to manage the rapid sorting and transport of packages, ensuring timely deliveries and efficient operations.
The conveyor belt system definition underscores the importance of accurate calculations in designing and operating efficient and reliable conveyor systems. By considering load, speed, tension, and power requirements, and using advanced tools and methods, industries can optimize their conveyor belt systems to meet specific operational needs and enhance overall productivity.
FAQs about Conveyor Belt System Definition
A conveyor belt system is a mechanical apparatus used for the efficient transportation of materials from one location to another within a defined space. The system comprises a continuous belt made from materials such as rubber, fabric, or metal, which moves over rollers or a flat surface. These belts can be customized for specific tasks, including transporting heavy loads, fragile items, or even food products. The conveyor belt system is widely used in industries such as manufacturing, mining, and logistics to streamline operations, reduce manual labor, and enhance productivity.
The primary function of a conveyor belt system is to transport materials efficiently across various distances within an industrial setting. This transportation can occur horizontally, vertically, or at an incline, depending on the design and requirements of the operation. Conveyor belt systems are integral to assembly lines, sorting facilities, and bulk material handling. They ensure a continuous flow of products, reduce the need for manual handling, minimize the risk of workplace injuries, and increase overall operational efficiency. By automating the movement of goods, these systems help maintain a steady production rate and improve logistical coordination.
The purpose of a conveyor belt is to facilitate the smooth and efficient movement of materials or products from one point to another. This purpose extends beyond simple transportation; conveyor belts are designed to handle specific operational needs such as sorting, packaging, inspection, and assembly. In manufacturing, conveyor belts contribute to seamless production processes, while in logistics, they aid in the rapid and organized distribution of goods. The overarching goal is to optimize workflow, reduce operational costs, and enhance productivity by automating the material handling process.
A conveyor belt control system refers to the set of devices and software that manage the operation of the conveyor belt. This system ensures the belt runs smoothly, maintains proper speed, and handles materials correctly. It includes sensors, motors, controllers, and other electronic components that monitor and adjust the conveyor belt’s performance. The control system can automate start/stop functions, regulate speed, detect blockages, and ensure the alignment and tracking of the belt. Advanced control systems may also incorporate programmable logic controllers (PLCs) and human-machine interfaces (HMIs) for enhanced precision and user control. The primary aim is to improve the efficiency, safety, and reliability of the conveyor belt system.
Last Updated on May 27, 2024 by Jordan Smith
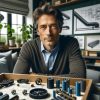
Jordan Smith, a seasoned professional with over 20 years of experience in the conveyor system industry. Jordan’s expertise lies in providing comprehensive solutions for conveyor rollers, belts, and accessories, catering to a wide range of industrial needs. From initial design and configuration to installation and meticulous troubleshooting, Jordan is adept at handling all aspects of conveyor system management. Whether you’re looking to upgrade your production line with efficient conveyor belts, require custom conveyor rollers for specific operations, or need expert advice on selecting the right conveyor accessories for your facility, Jordan is your reliable consultant. For any inquiries or assistance with conveyor system optimization, Jordan is available to share his wealth of knowledge and experience. Feel free to reach out at any time for professional guidance on all matters related to conveyor rollers, belts, and accessories.