Conveyor Belt System Design: Best Practices, Types, and Components
Conveyor belt systems are integral components of numerous industrial processes, providing a reliable and efficient means of transporting goods and materials across various stages of production and distribution. Central to the concept of modern manufacturing, warehousing, and logistics, these systems streamline operations, ensuring that materials move smoothly from one point to another with minimal human intervention. The design of a conveyor belt system is crucial, as it directly impacts the system’s efficiency, safety, and operational cost. A well-thought-out conveyor belt system design accommodates specific industry needs, handling requirements, and spatial constraints, thereby enhancing the overall productivity and safety of the workplace. By automating the movement of materials, these systems reduce the likelihood of errors and accidents, making them indispensable in today’s fast-paced industrial environments.
What is Conveyor Belt System Design
Delving into the realm of belt conveyor system design unveils a complex yet fascinating process that combines engineering principles with practical applications. The basic knowledge of conveyor belt system design encompasses understanding the components, mechanics, and dynamics that make up a conveyor system. This includes the belt material and structure, pulleys, motors, idlers, support framework, and control systems. Each of these elements plays a pivotal role in ensuring the conveyor system operates smoothly, efficiently, and safely.
Basics of Conveyor Belt System Design
The conveyor belt, often made from materials like rubber, PVC, or fabric, is the heart of the system, carrying materials from one point to another. Pulleys guide and drive the belt, with the drive pulley providing the necessary force to move the belt and its load. Motors power the system, while idlers support the belt and help maintain its tension and alignment. The support structure holds all these components in place, providing stability and durability to the entire system.
Significance of Custom Design
A belt conveyor system, designed to transport materials, goods, or people from one point to another, typically consists of a flat belt-driven mechanism and two motorized pulleys with the conveyor material looped over them, ensuring proper belt tension. Custom design in conveyor belt system design is not just beneficial but essential for meeting specific operational requirements. Here are nine significant reasons why:
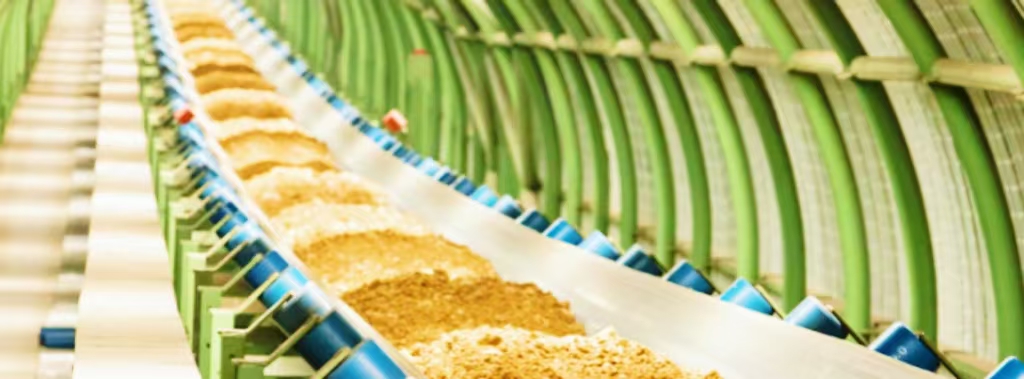
- Material Handling: Custom designs can accommodate the specific types of materials being transported, whether they are heavy, abrasive, delicate, or require special handling to prevent contamination.
- Operational Efficiency: Tailored systems can optimize the speed, capacity, and routing of materials, improving overall operational efficiency and productivity.
- Space Utilization: Every facility has its unique layout and space constraints. Custom conveyor designs can be adapted to fit available spaces, maximizing the use of the area while ensuring smooth material flow.
- Integration: Custom designs allow for seamless integration with existing equipment and processes, ensuring that the conveyor system enhances rather than disrupts the current operation.
- Safety: By considering the specific operational environment, custom conveyor systems can incorporate necessary safety features and protocols to protect workers and materials.
- Flexibility and Scalability: Custom designs can be made flexible and scalable, allowing for future modifications and expansions as operational needs change.
- Cost-Effectiveness: Although custom designs might require a higher initial investment, they can lead to long-term savings by reducing maintenance issues, minimizing downtime, and enhancing productivity.
- Compliance: Custom conveyor systems can be designed to comply with industry standards and regulations, ensuring that the operation meets all legal and safety requirements.
- Innovative Solutions: Custom design opens the door to innovative solutions that address unique challenges, leveraging the latest technologies and materials to create highly efficient and effective conveyor systems.
Understanding conveyor belt system design and the importance of custom solutions is crucial for businesses looking to optimize their material handling processes. By considering the specific needs and challenges of an operation, custom conveyor designs can deliver unmatched efficiency, safety, and reliability.
Importance of Conveyor Belt Systems in Industrial Operations
Conveyor belt systems are vital for a wide range of industries including manufacturing, mining, food processing, and logistics. Their primary function is to move materials from one point to another within a facility, thereby streamlining production processes and enhancing overall productivity. These systems are designed to handle various types of materials, from lightweight goods to heavy and bulky items, ensuring smooth and continuous operation.
- Enhanced Efficiency: Conveyor belt systems are designed to operate continuously, reducing the need for manual handling of materials. This continuous operation significantly enhances production efficiency by minimizing downtime and increasing throughput.
- Reduced Labor Costs: By automating the transportation of materials, conveyor belt systems reduce the reliance on manual labor. This not only lowers labor costs but also minimizes the risk of workplace injuries associated with manual handling tasks.
- Improved Safety: Conveyor belt systems are equipped with various safety features such as emergency stop buttons, guards, and sensors that detect obstructions. These safety measures help to protect workers and prevent accidents, thereby creating a safer working environment.
Benefits of Conveyor Belt System Design
The design of a conveyor belt system is critical to its performance and operational efficiency. Proper Conveyor Belt System Design ensures that the system meets the specific needs of the operation, including the type of materials being transported, the required speed of transportation, and the layout of the facility.
- Customization: One of the key benefits of Conveyor Belt System Design is the ability to customize the system to meet specific operational requirements. This includes selecting the appropriate type of belt, determining the optimal layout, and incorporating any necessary features such as cleats or sidewalls.
- Scalability: Well-designed conveyor belt systems are scalable, allowing for future expansion and modification. This is particularly important for growing businesses that may need to increase their production capacity or reconfigure their facility layout.
- Durability and Reliability: A robust Conveyor Belt System Design takes into account the durability and reliability of the components. This includes selecting materials that can withstand the operating conditions and ensuring that the system can handle the anticipated load without frequent breakdowns.
- Energy Efficiency: Modern Conveyor Belt System Design incorporates energy-efficient components and technologies. This not only reduces the operational costs but also minimizes the environmental impact of the system.
Key Components of Conveyor Belt Systems
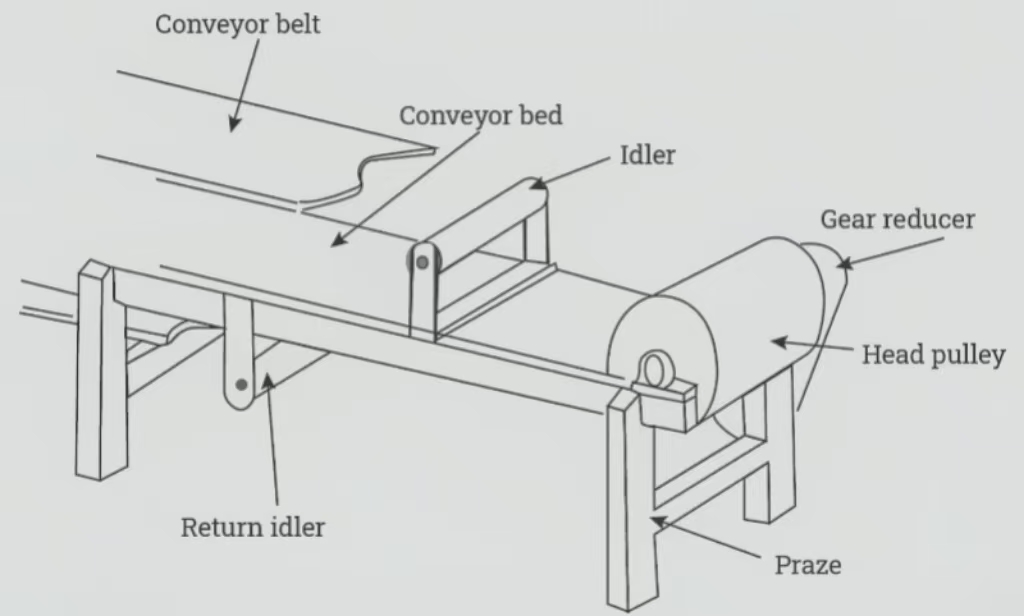
In the realm of conveyor belt system design, understanding the key components and their functions is crucial for ensuring the system’s efficiency and reliability. These components are the building blocks of the conveyor system, and their quality and compatibility with each other play a significant role in the system’s overall performance.
- The Belt: At the heart of every conveyor system is the conveyor belt itself, which serves as the surface on which materials are transported from one point to another. The selection of the belt material is a critical decision in belt conveyor system design, as it must be suited to the type of materials being conveyed and the environment in which the system operates. Options range from rubber and fabric belts for general applications to specialized belts with features like heat resistance, oil resistance, or cleated surfaces for inclined transport.
- Pulleys: Pulleys guide and drive the conveyor belt, with the drive pulley providing the motive force for the belt’s movement. The tail pulley, on the other end, serves as a return for the belt. Pulleys are designed to provide optimal traction for the belt and are often coated or lagged to enhance grip and reduce wear.
- Idlers: Idlers support the conveyor belt along its length, preventing sagging and ensuring smooth belt movement. They come in various types, including flat idlers for straight sections of the conveyor troughing idlers that shape the belt into a ‘U’ for carrying bulk materials. The spacing and configuration of idlers are carefully considered in conveyor belt system design to balance load distribution and belt support.
- Drive Units: The drive unit is the powerhouse of the conveyor system, comprising motors and gearboxes that convert electrical energy into the mechanical energy needed to move the belt. The specification of the drive unit is based on the required belt speed, the load to be transported, and the conveyor’s length and incline.
- Support Structure: The support structure provides the framework that holds all other components in place. It must be robust enough to handle the load and stresses of operation without deformation. The design of the support structure varies widely depending on the application, from simple frames for light-duty conveyors to complex truss structures for heavy loads and long spans.
Each of these components must be carefully selected and engineered to work together seamlessly. The success of conveyor belt system design hinges on a deep understanding of these key components and their interplay, ensuring that the final system is not only efficient and reliable but also tailored to the specific needs of the application.
Conveyor Belt Design Calculations and Considerations
The conveyor belt system design is a sophisticated process that involves meticulous planning and calculations to ensure the system’s functionality, efficiency, and safety. This process includes several critical design calculations, each serving a specific purpose in the overall design of the conveyor system.
Critical Design Calculations
Here are eight essential calculations integral to the conveyor belt system design:
- Belt Speed: Determines how fast the belt should move, balancing the need for efficiency with the potential impact on the materials being transported and the machinery itself.
- Belt Width: Calculated to ensure the conveyor can handle the intended load volume and size, preventing spillage and optimizing the system’s capacity.
- Load Capacity: Involves determining the maximum load the conveyor belt can carry at any given time, which influences the selection of belt material and the design of the belt’s support structure.
- Belt Tension: Essential for maintaining the correct pressure on the belt to prevent slippage on the drive pulley, ensuring smooth operation and prolonging the life of the belt.
- Power Requirements: Calculated to identify the necessary power output for the conveyor’s motors, ensuring they can move the loaded belt without overstressing the system.
- Idler Spacing: Determines the distance between idlers to provide adequate support for the belt and the load, minimizing belt sag and ensuring smooth operation.
- Pulley Diameter: Affects the belt’s speed and tension; selecting the appropriate pulley size is crucial for the system’s efficiency and the longevity of the belt.
- Conveyor Length and Incline: The total length of the conveyor and any inclines or declines it must navigate are factored into the design to ensure the system can transport materials efficiently over the required distances and gradients.
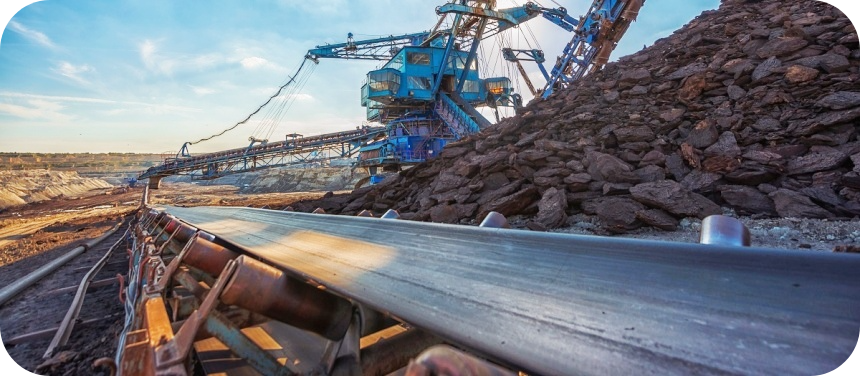
Software and Tools
To aid in these complex calculations, several conveyor belt design software and tools have been developed, offering precision and efficiency in the design process. These tools allow for the modeling of the conveyor system, simulation of its operation under various conditions, and adjustments to the design based on the outcomes of these simulations. Here are six notable conveyor belt design software and tools:
- BeltStat: Renowned for its comprehensive analysis capabilities, BeltStat offers detailed modeling of belt conveyors and their components, facilitating precise design calculations.
- Sidewinder Conveyor Design Software: Provides a wide range of tools for designing conveyor systems, including belt tensions, load distributions, and drive power requirements, among others.
- Helix Delta-T Online: An online platform offering a range of conveyor design, analysis, and simulation tools for complex conveyor systems.
- FlexSim Conveyor Simulator: Allows designers to visualize and test conveyor system designs in a virtual 3D environment, identifying potential issues before implementation.
- AC-Tek Newton: A powerful simulation software that focuses on the analysis of dynamic belt conveyor systems, offering insights into complex behaviors under varying conditions.
- Conveyor Analyst: Designed for the comprehensive analysis of belt conveyors, this software covers everything from belt tensions to impact loading, providing a solid foundation for effective conveyor system design.
By leveraging these critical calculations and advanced design tools, engineers can create conveyor belt systems that are tailored to the specific needs of their operations, ensuring optimal performance, reliability, and safety.
Types of Conveyor Belts and Their Applications
In conveyor belt system design, selecting the appropriate type of conveyor belt is crucial as it directly impacts the system’s efficiency and suitability for specific tasks. Below is a table that outlines various types of conveyor belts and their typical applications, helping designers make informed decisions based on material characteristics and application requirements.
When integrating a conveyor belt into a system design, it’s essential to consider not just the type of belt but also factors like load capacity, environmental conditions (e.g., temperature, chemicals), and the need for special features like resistance to abrasion or chemicals. The choice of conveyor belt has a significant impact on the system’s performance, maintenance requirements, and overall cost-effectiveness.
Conveyor Design Standards and Best Practices
The conveyor belt system design is governed by a set of industry standards and best practices that ensure the safety, efficiency, and reliability of conveyor systems. These guidelines are developed by authoritative bodies such as the American Society of Mechanical Engineers (ASME), Conveyor Equipment Manufacturers Association (CEMA), and International Organization for Standardization (ISO), among others. Adhering to these standards is crucial for maintaining high-quality systems that meet operational demands while ensuring the safety of workers and the integrity of materials being transported.
Industry Standards
- ASME B20.1: Safety standard for conveyors and related equipment.
- ISO 5048: Establishes methods for calculating the operating power requirements on the driving pulley of a belt conveyor.
- CEMA Standards: The CEMA Standard for Belt Conveyor provides comprehensive guidelines for the design, manufacture, and application of conveyor systems.
- DIN 22101: German standard that specifies conditions for stationary belt conveyors.
- BS EN 620: British standard for continuous handling equipment and systems.
- OSHA Standards: Regulations for conveyor safety in the United States play a crucial role in shaping the United States Conveyor Belt Market.
- MSHA Standards: Mining safety guidelines, including those for conveyor systems.
- ISO 5285: Conveyor belts – Guidelines for storage and handling.
Best Practices
- Risk Assessment: Conducting thorough risk assessments to identify potential hazards and implement necessary safety measures.
- Regular Maintenance: Establishing routine maintenance schedules to ensure the conveyor’s optimal performance and longevity.
- Material Consideration: Selecting conveyor components and materials suitable for the specific type of goods being transported.
- Energy Efficiency: Designing systems with energy-efficient motors and controls to reduce operational costs and environmental impact.
- Ergonomic Design: Ensuring the conveyor design considers human factors, reducing the risk of injury and improving usability.
- System Integration: Designing conveyors to integrate seamlessly with other equipment and systems within the facility.
- Training and Documentation: Providing comprehensive training and documentation for operators and maintenance personnel.
- Innovation and Upgrades: Keeping abreast of technological advancements and incorporating innovative features that enhance system performance.
Importance of Adhering to Standards
- Safety: Ensuring the safety of operators and maintenance personnel by minimizing the risk of accidents and injuries.
- Compliance: Meeting legal and regulatory requirements to avoid fines and legal issues.
- Reliability: Enhancing the reliability of conveyor systems, reducing downtime and maintenance costs.
- Efficiency: Optimizing operational efficiency by designing systems that meet specific material handling needs.
- Quality Assurance: Maintaining high-quality standards in the design and manufacture of conveyor components and systems.
- Interoperability: Facilitating the integration of conveyor systems with other equipment and processes.
- Sustainability: Promoting sustainable practices by designing energy-efficient and environmentally friendly conveyor systems.
- Innovation: Encouraging innovation and the adoption of new technologies to improve conveyor system design and functionality.
- Marketability: Enhancing the marketability of conveyor systems by ensuring they meet recognized standards and best practices.
Adhering to established conveyor design standards and best practices is essential for creating conveyor belt systems that are safe, efficient, and reliable. These guidelines provide a foundation for designing systems that meet the specific needs of various industries while ensuring compliance with regulatory requirements and promoting continuous improvement and innovation in belt conveyor system design.
Emerging Trends in Conveyor Belt System Design
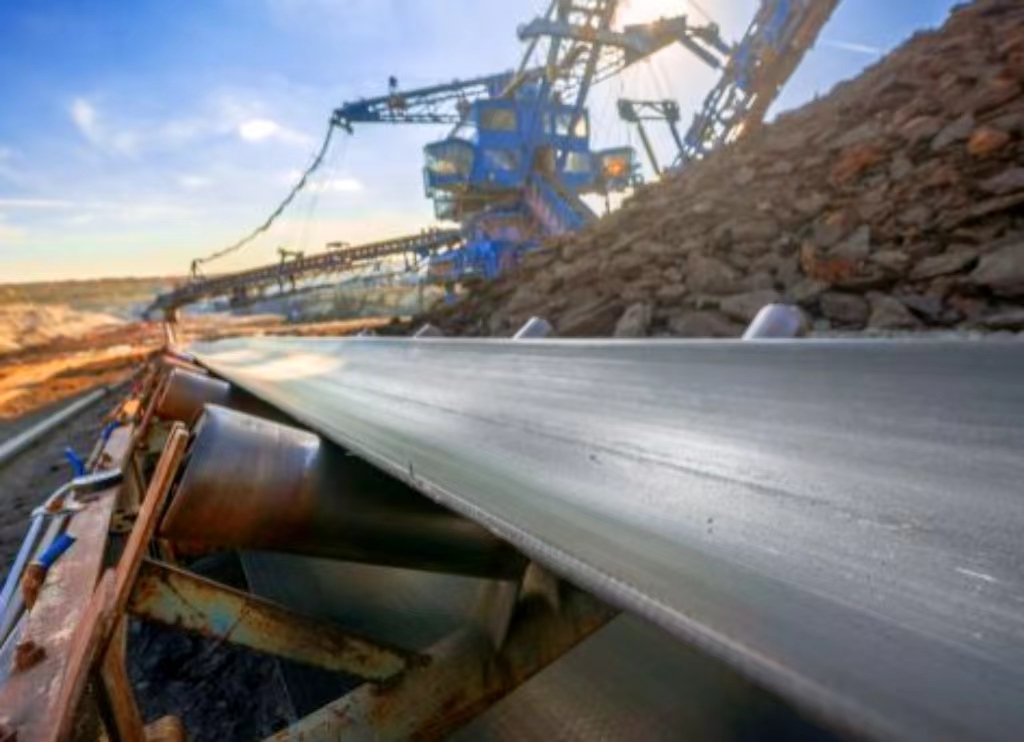
Innovations in Materials and Technology
The field of Conveyor Belt System Design is continually evolving, driven by innovations in materials and technology. These advancements are crucial for improving the efficiency, durability, and functionality of conveyor belt systems, making them more adaptable to diverse industrial needs.
Advanced Materials
- Composite Materials: The use of composite materials in conveyor belts is one of the significant trends in Conveyor Belt System Design. These materials, which combine different substances to achieve superior properties, offer enhanced strength, flexibility, and resistance to wear and tear. For instance, belts made from a combination of polyurethane and aramid fibers are lightweight yet extremely durable, suitable for high-stress applications.
- Eco-friendly Materials: With the increasing focus on sustainability, eco-friendly materials are gaining traction in Conveyor Belt System Design. Biodegradable and recyclable materials are being developed to reduce the environmental impact of conveyor systems. These materials not only meet regulatory requirements but also align with the corporate sustainability goals of many industries.
- Temperature-Resistant Materials: Industries such as mining and metallurgy require conveyor belts that can withstand extreme temperatures. Innovations in temperature-resistant materials, such as high-temperature thermoplastics and specially formulated rubbers, ensure that conveyor belts can operate efficiently under harsh conditions without degrading or losing their structural integrity.
Technological Advancements
- Smart Conveyor Belts: The integration of sensors and IoT (Internet of Things) technology in conveyor belts is revolutionizing Conveyor Belt System Design. Smart conveyor belts can monitor their own performance, detect issues such as misalignment or wear, and communicate this data to a central control system. This real-time monitoring enables predictive maintenance, reducing downtime and extending the lifespan of the conveyor belt system.
- Modular Design: Modular conveyor belts are designed with interchangeable parts, allowing for easy customization and scalability. This innovation in Conveyor Belt System Design enables businesses to adapt their conveyor systems quickly to changing production needs without significant downtime or expense.
- Energy-efficient Motors: Advancements in motor technology, including the development of high-efficiency motors and drives, are making conveyor belt systems more energy-efficient. These motors consume less power while delivering the same level of performance, helping businesses reduce their operational costs and environmental footprint.
Enhanced Automation and Control Systems
Automation and control systems play a pivotal role in modern Conveyor Belt System Design, enhancing operational efficiency and reliability. These systems incorporate advanced technologies to streamline operations, improve accuracy, and reduce human intervention.
Automated Control Systems
- PLC (Programmable Logic Controller) Integration: PLCs are essential components in automated conveyor systems, allowing for precise control and coordination of various system functions. PLC integration in Conveyor Belt System Design facilitates seamless communication between different components, ensuring synchronized operation and reducing the likelihood of errors.
- Automated Sorting and Routing: Automation in sorting and routing processes is a significant trend in Conveyor Belt System Design. Advanced algorithms and machine learning technologies enable conveyor systems to sort and route materials with high accuracy and speed. This capability is particularly beneficial in industries such as logistics and e-commerce, where efficient order fulfillment is critical.
- Adaptive Control Systems: Adaptive control systems use real-time data to adjust conveyor belt speeds, loading rates, and other operational parameters dynamically. This adaptability ensures optimal performance under varying conditions, enhancing the efficiency and flexibility of the conveyor belt system.
Robotics and AI Integration
- Robotic Assistance: The integration of robotics in Conveyor Belt System Design is transforming material handling processes. Robots can perform tasks such as picking, placing, and packaging materials, reducing the need for manual labor and increasing throughput. These robotic systems are often equipped with advanced vision systems and AI algorithms to recognize and handle different types of materials accurately.
- Artificial Intelligence: AI plays a crucial role in optimizing conveyor belt operations. Machine learning algorithms analyze data from sensors and other sources to predict maintenance needs, optimize routing paths, and improve overall system efficiency. AI-driven Conveyor Belt System Design helps in minimizing downtime, reducing energy consumption, and enhancing productivity.
Practical Examples and Case Studies in Conveyor Belt System Design
The realm of belt conveyor system design is rich with real-world applications that demonstrate the ingenuity and adaptability of these systems across various industries. Through an examination of practical examples and case studies, we can gain insights into the challenges faced during the design process and the innovative solutions that were implemented to overcome them.
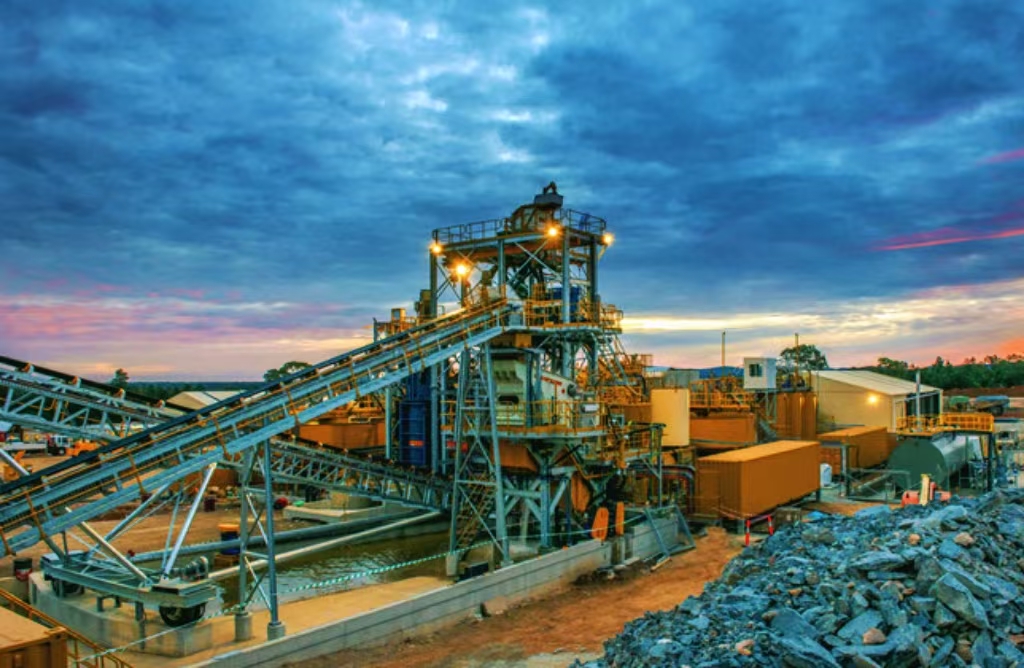
E-Commerce Fulfillment Centers
Amazon: Amazon, a major e-commerce company, faced the challenge of managing a vast volume of orders with high efficiency. The requirement was to design a conveyor system that could rapidly sort and route packages to the correct shipping lanes without errors. The solution implemented was a sophisticated conveyor belt system design that incorporated barcode scanners and automated sorting arms. This setup significantly increased throughput and accuracy, allowing Amazon to handle peak order volumes seamlessly.
Airport Baggage Handling
Heathrow Airport: At Heathrow Airport, a busy international hub, the challenge was to ensure secure and swift handling of passenger luggage. The integration involved a conveyor system capable of accommodating varying sizes of luggage, routing them through security screening, and delivering them to the correct flights with minimal delays. The system utilized advanced tracking technology and redundant pathways, ensuring reliability and efficiency even during peak travel times.
Food Processing Industry
Nestlé: In a Nestlé food processing plant, the belt conveyor system design had to comply with strict hygiene standards while handling delicate products. The challenge was to minimize product damage and prevent contamination. The implemented solution was a modular belt conveyor with easy-to-clean surfaces and gentle handling features, ensuring the integrity and safety of Nestlé’s food products throughout the processing stages.
Automotive Manufacturing
Toyota: Toyota, an automotive manufacturer, needed a system to transport heavy car parts through various stages of assembly with precision. The solution was a heavy-duty conveyor belt system designed with reinforced belts and precise control mechanisms. This allowed for the synchronized movement of parts through the assembly line, enhancing productivity and safety, and maintaining Toyota’s high standards of manufacturing efficiency.
Mining Operations
Rio Tinto: In the mining sector, Rio Tinto faced the challenge of designing a conveyor system capable of transporting heavy loads of raw materials over long distances in harsh environments. The solution involved the use of high-strength belts, durable materials, and advanced monitoring systems. This ensured the continuous and reliable operation of the conveyor system, even under extreme conditions typically encountered in mining operations.
Recycling Facilities
Waste Management Inc.: At Waste Management Inc., a recycling facility needed an efficient conveyor system to sort a wide variety of materials. The challenge was the diverse nature of recyclables and the need for precise sorting. The implemented conveyor belt system design included multiple sorting lines with specialized sensors and sorting mechanisms, significantly improving the facility’s sorting efficiency and capacity.
Pharmaceutical Packaging
Pfizer: In the pharmaceutical industry, Pfizer required a conveyor system to handle fragile vials and packages with utmost care. The challenge was to maintain a sterile environment and prevent any damage to the products. The solution was a conveyor belt system design that incorporated soft-touch belts, precise speed control, and cleanroom compatibility, ensuring the safe and efficient handling of Pfizer’s pharmaceutical products.
These case studies illustrate the versatility and adaptability of conveyor belt systems in addressing specific industry challenges. Through innovative design and customization, conveyor systems continue to play a pivotal role in enhancing operational efficiency, safety, and reliability across diverse sectors.
Our conveyor belts deliver the results you need – act fast!
FAQs about Conveyor Belt System Design
Conveyor systems are designed through a meticulous process that involves understanding the specific needs of the operation where they will be used. The design process begins with an assessment of the materials or products that the conveyor will transport. This includes considering the size, weight, and type of materials, as well as how quickly and in what volumes they need to be moved. Designers also take into account the environmental conditions where the conveyor will operate, such as temperature, humidity, and potential exposure to chemicals.
The layout of the facility is another critical factor, as the conveyor system must fit within the existing space and integrate seamlessly with other equipment and processes. This may involve designing straight, curved, inclined, or declined sections of the conveyor to navigate around obstacles and efficiently use available space.
Once these factors are understood, engineers use specialized software to model the conveyor system, perform simulations, and make necessary adjustments. This software helps in calculating critical parameters such as belt speed, belt width, load capacity, and motor power requirements. The final design includes detailed specifications for all components, including the belt material, pulleys, idlers, drive units, and support structures, ensuring that the conveyor system is tailored to meet the specific requirements of the operation.
The criteria for conveyor system design revolve around ensuring the system meets the operational requirements efficiently, safely, and cost-effectively. Key criteria include:
Material Handling Requirements: The system must be capable of handling the specific types of materials or products, considering their size, weight, and properties. This influences the choice of conveyor type, belt material, and system configuration.
Throughput and Speed: The design must accommodate the required throughput rate and speed, ensuring that the system can move materials at the necessary pace to meet production demands.
Spatial Constraints: The conveyor must fit within the available space, requiring careful planning of its path and dimensions. This may involve designing custom configurations to navigate around obstacles or through tight spaces.
Integration with Other Systems: The conveyor system must integrate seamlessly with other equipment and processes, requiring coordination and compatibility in design.
Safety and Compliance: Safety is paramount, and the design must include features such as guards, emergency stops, and other safety mechanisms. Compliance with industry standards and regulations is also essential.
Reliability and Maintenance: The system should be designed for reliability, with durable components and features that facilitate easy maintenance and minimize downtime.
Cost-Effectiveness: While meeting operational requirements, the design should also consider the total cost of ownership, including initial costs, maintenance, and energy consumption, to ensure the system is cost-effective over its lifespan.
A conveyor belt system is a mechanical device that transports materials or products from one location to another within a facility or across distances. It consists of a continuous belt made from various materials, including rubber, fabric, or metal, which is stretched over a series of pulleys. One or more of these pulleys are powered, moving the belt and the materials on it with efficiency and precision.
Conveyor belt systems are versatile and can be customized to suit a wide range of applications, from simple tasks like moving boxes within a warehouse to complex operations in manufacturing, mining, and food processing. They can be designed to handle various materials, including solids, liquids, and loose bulk products, and can be configured in numerous layouts, including straight, curved, inclined, and declined paths.
The primary advantage of conveyor belt systems is their ability to improve efficiency and safety in material handling, reducing the need for manual labor, minimizing the risk of injury, and increasing throughput. They are an integral part of modern industrial operations, logistics, and supply chains.
The belt conveyor design principle centers on creating an efficient, reliable, and safe system for transporting materials from one point to another. This principle encompasses several key concepts:
Minimal Energy Consumption: The design should ensure that the conveyor operates with the least possible energy consumption, which involves optimizing the belt speed, reducing friction, and selecting energy-efficient motors.
Uniform Material Flow: The system should provide a consistent and controlled flow of materials, preventing bottlenecks, spillage, and uneven loading, which can affect efficiency and safety.
Adaptability and Flexibility: The design should be adaptable to various materials and operational conditions, allowing for adjustments in belt speed, incline, and direction as needed.
Safety: Safety features, such as guards, emergency stops, and warning signals, should be integral to the design, protecting workers and materials.
Durability and Reliability: The system should be built with high-quality materials and components to withstand the operational demands, minimizing maintenance requirements and ensuring long-term reliability.
Ease of Maintenance: The design should facilitate easy access to key components for maintenance and repairs, reducing downtime.
Designing a conveying system involves several key steps to ensure efficiency and reliability. First, identify the specific requirements of your application, including the type of materials to be transported, their weight, size, and the desired speed of conveyance. Next, determine the layout of the system, considering factors such as the length of the conveyor, the height differences between loading and unloading points, and the overall space available. Select appropriate components, such as motorized pulleys, belts, and support structures, based on the operational requirements. It’s also crucial to consider safety features, maintenance access, and potential future expansions. Properly design the control systems to manage the conveyor’s speed and direction. Finally, simulate the system using design software to optimize performance and identify any potential issues before installation.
Several software tools are widely regarded as excellent for belt conveyor design, each offering unique features. Some of the top choices include:
AutoCAD: A versatile tool for detailed conveyor system drawings, allowing for precise layout planning and component placement.
FlexSim: Specializes in simulation, enabling designers to visualize conveyor operations and optimize performance through virtual testing.
Helix Delta-T: Specifically designed for conveyor systems, it provides comprehensive capabilities for calculating and modeling the behavior of conveyor components under various conditions.
Sidewinder Conveyor Design Software: Known for its robust features in designing and analyzing belt conveyor systems, it offers detailed reports on system performance, power requirements, and potential stress points.
SolidWorks: Offers 3D CAD modeling capabilities that are beneficial for designing complex conveyor systems and integrating them with other machinery.
Choosing the right software depends on your specific needs, including the complexity of the system, budget, and the level of detail required.
Last Updated on June 14, 2024 by Jordan Smith
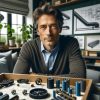
Jordan Smith, a seasoned professional with over 20 years of experience in the conveyor system industry. Jordan’s expertise lies in providing comprehensive solutions for conveyor rollers, belts, and accessories, catering to a wide range of industrial needs. From initial design and configuration to installation and meticulous troubleshooting, Jordan is adept at handling all aspects of conveyor system management. Whether you’re looking to upgrade your production line with efficient conveyor belts, require custom conveyor rollers for specific operations, or need expert advice on selecting the right conveyor accessories for your facility, Jordan is your reliable consultant. For any inquiries or assistance with conveyor system optimization, Jordan is available to share his wealth of knowledge and experience. Feel free to reach out at any time for professional guidance on all matters related to conveyor rollers, belts, and accessories.