Conveyor Belt Testing and Inspection
Conveyor belt systems are integral to numerous industries, streamlining operations and enhancing productivity. However, the efficiency and safety of these systems hinge significantly on the integrity of the conveyor belts themselves. This is where conveyor belt testing plays a crucial role. By rigorously assessing various aspects of conveyor belts, such as their tensile strength, abrasion resistance, and overall durability, testing ensures that these belts can handle the demanding conditions of industrial use. Regular testing not only helps in maintaining operational efficiency but also plays a vital part in ensuring the safety of the workers and the life of the conveyor belts. Through systematic testing, potential issues can be identified and rectified before they escalate into major problems, thereby safeguarding both the conveyor system’s functionality and the investment made in it.
Overview of Conveyor Belt Testing
The term conveyor belt testing encompasses a series of tests and evaluations designed to determine the durability, functionality, and safety of conveyor belts used in various industries. The primary purpose of conveyor belt testing procedure is to ensure that the belts meet specific standards of quality and safety before they are employed in material handling and processing applications. This testing is crucial as it directly impacts the efficiency, reliability, and longevity of the conveyor systems.
Conveyor belt testing involves several key aspects, each focusing on a different property of the belt:
- Abrasion Resistance: This test measures the ability of the conveyor belt to withstand wear and tear over time. It involves subjecting the belt material to abrasive forces and evaluating the amount of wear that occurs. This is critical in determining how long the belt can operate effectively in harsh working environments.
- Elongation: Elongation testing assesses the extent to which a conveyor belt can stretch without losing its strength and integrity. This property is vital for ensuring that the belt can handle the stress and strain of carrying heavy loads without breaking or deforming.
- Hardness: The hardness test evaluates the rigidity and flexibility of the conveyor belt material. A balance between hardness and flexibility is essential for the belt to function correctly under varying operational conditions.
- Conveyor Belt Tensile Strength: This aspect of conveyor belt testing measures the maximum load that a belt can support before it breaks. Tensile strength testing ensures that the belt can withstand the operational loads it will encounter, which is crucial for preventing belt failures that could lead to operational downtime and safety hazards.
Conveyor belt testing is a comprehensive process that evaluates various characteristics of conveyor belts to ensure their suitability for specific applications. By rigorously testing for abrasion resistance, elongation, hardness, and tensile strength, manufacturers and users of conveyor belts can be confident in their performance and reliability.
Conveyor Belt Testing:Abrasion and Elongation
Conveyor belts play a crucial role in industries, transporting materials efficiently over varying distances. To ensure durability and performance, conveyor belts undergo rigorous testing, with abrasion and elongation tests being particularly critical. These tests provide insight into the belt’s wear resistance, stretching behavior under load, and overall lifespan, helping manufacturers produce reliable products.
Abrasion Testing
Abrasion testing measures the conveyor belt’s resistance to wear caused by friction and contact with materials. This test is especially important for belts used in industries where they face abrasive materials, such as mining, construction, and bulk handling. The goal is to assess the belt’s durability and ability to withstand harsh operating conditions without significant material loss.
Procedure:
- Preparation of Test Samples: Samples are cut from the belt material, usually in standard sizes, for uniformity.
- Test Setup: The sample is mounted onto an abrasion tester, which typically involves a rotating drum or wheel coated with abrasive material.
- Abrasion Process: The sample is subjected to a specified amount of pressure and speed as it moves against the abrasive surface. The friction generated simulates real-world conditions where the belt faces rough materials.
- Measurement: After testing, the amount of material loss is measured by weighing the sample before and after the test. Alternatively, thickness reduction is recorded. The result is often expressed in mm³, indicating the volume of material lost.
Standards:
Abrasion testing for conveyor belts is commonly conducted following standards like ISO 4649 and DIN 53516, which specify parameters such as pressure, abrasion distance, and type of abrasive material. Lower abrasion values indicate higher wear resistance.
Elongation Testing
Elongation testing assesses the conveyor belt’s capacity to stretch under tension without permanent deformation. This is essential for belts that carry heavy loads over long distances, as excessive stretching can lead to belt misalignment, slipping, and premature wear.
Procedure:
- Sample Preparation: A sample strip of the belt material is cut to a standardized length.
- Initial Measurements: The original length and width of the sample are measured and recorded.
- Applying Tension: The sample is placed in a tensile testing machine, where a controlled tensile force is applied. The force simulates the stress the belt undergoes when moving heavy loads.
- Measuring Elongation: As force increases, the stretch or elongation of the belt is measured in two ways:
- Permanent Elongation: The amount the belt stretches without returning to its original length after the force is removed.
- Elastic Elongation: The temporary elongation, or stretch, that the belt returns to its original size once the force is released.
Standards:
Standards like ISO 9856 dictate procedures and acceptable elongation limits for conveyor belts, focusing on the percentage increase in length under specific loads. Lower elongation percentages indicate that the belt can handle higher loads with minimal stretching.
Importance of Abrasion and Elongation Testing
- Durability: Both tests help identify belts that will last longer in demanding applications, reducing the frequency of replacement and maintenance.
- Efficiency: By selecting belts with optimal abrasion and elongation characteristics, industries can achieve smoother operations and minimized downtime.
- Cost-Effectiveness: Testing helps manufacturers provide suitable products for different industries, leading to cost savings by avoiding underperforming belts and improving operational reliability.
Through abrasion and elongation testing, manufacturers can design and produce conveyor belts that meet the demands of specific industries, ensuring a balance of conveyor belt strength, flexibility, and resistance to wear.
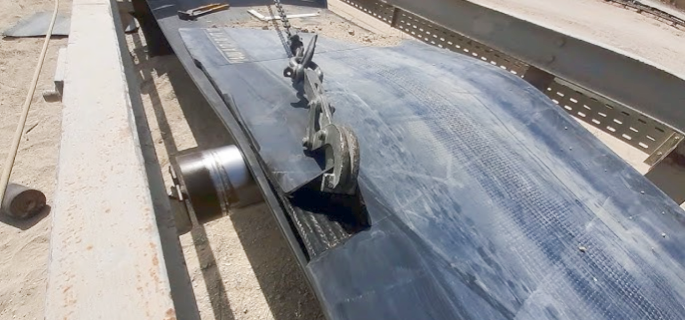
Conveyor Belt Testing:Adhesion
Adhesion testing is a key assessment in conveyor belt manufacturing, evaluating the strength of the bond between the various layers of the belt—primarily between the cover layers and the inner fabric or steel reinforcement layers. This test is critical because a conveyor belt’s durability and performance largely depend on how well these layers are bonded. Strong adhesion ensures the belt can withstand the rigors of heavy-duty applications without delamination, which can lead to failure and costly downtime.
Adhesion testing in conveyor belts assesses the bond strength, providing data on the quality of the belt’s construction and its ability to withstand stress, strain, and environmental factors (e.g., heat, moisture, chemicals). This is particularly important for belts used in industries such as mining, manufacturing, and logistics, where belts are subject to high tension and heavy loads.
Procedure for Adhesion Testing
- Sample Preparation:
- Samples are cut from a conveyor belt in a standardized shape and size, typically with separate strips for cover-to-fabric, fabric-to-fabric (if multilayered), and cover-to-steel reinforcement adhesion testing.
- Test Setup:
- The sample is placed in an adhesion testing machine, which pulls apart the layers at a controlled rate. The machine is equipped to measure the force required to separate these layers, with specific rates for different types of belts and thicknesses.
- Testing Process:
- The machine gradually applies force to peel the cover layer away from the fabric reinforcement layer, or to separate other bonded interfaces within the belt.
- The force required to separate each layer is measured, typically recorded in newtons per millimeter (N/mm). Higher values indicate stronger adhesion between the layers.
- Failure Observation:
- During testing, observations are made about the type of failure (cohesive vs. adhesive). In cohesive failure, the bond is so strong that the material itself fails before the bond, which indicates superior adhesion quality. Adhesive failure, on the other hand, occurs when the layers come apart at the bond interface, which could signal weaker adhesion.
Standards for Adhesion Testing
Standards such as ISO 252 specify the methodology and acceptable adhesion values for conveyor belts. These standards provide guidelines on the testing procedure, including sample dimensions, testing rate, and minimum acceptable bond strength values based on the belt’s intended application. Belts used in high-tension environments require higher adhesion strength, while lighter-duty belts may have lower requirements.
Importance of Adhesion Testing
- Longevity:
- Strong adhesion ensures that the belt layers remain intact under stress, extending the belt’s lifespan and preventing issues like delamination.
- Safety:
- In industrial applications, a belt with weak adhesion could delaminate under heavy loads, potentially leading to accidents or equipment damage.
- Performance:
- Adhesion strength affects the belt’s ability to withstand environmental conditions, such as temperature fluctuations, which can impact the adhesive material.
- Cost Efficiency:
- High-quality adhesion reduces the need for frequent repairs or replacements, leading to reduced operational costs and increased efficiency.
Key Takeaways
Adhesion testing provides a clear measure of the quality and durability of a conveyor belt, making it an essential step in the manufacturing process. By ensuring that conveyor belts have strong, durable bonds between layers, manufacturers can meet industry demands for reliability, safety, and efficiency, which are critical in high-stress industrial applications.
4
Ultrasonic Equipment for Conveyor Belt Testing
Ultrasonic testing (UT) is a non-destructive testing (NDT) technique that uses high-frequency sound waves to evaluate the internal integrity and structural health of conveyor belts. This technology is essential for detecting hidden flaws, delaminations, and voids within the belt, allowing operators to assess the belt’s condition without causing any damage. Ultrasonic equipment is widely used in industries such as mining, manufacturing, and logistics, where conveyor belts are subjected to heavy loads, abrasion, and environmental stressors.
Working Principle of Ultrasonic Testing
In ultrasonic testing, a transducer emits sound waves (usually in the frequency range of 1-10 MHz) that travel through the belt material. When these waves encounter a boundary or flaw within the belt (such as a delamination or a foreign object), part of the wave is reflected back to the transducer. By analyzing these reflections, the equipment provides data on the location, size, and nature of any defects.
Key Components of Ultrasonic Equipment for Conveyor Belts
- Ultrasonic Transducer:
- This is the core component that generates and receives ultrasonic sound waves. Transducers can be configured to inspect specific types of flaws or to penetrate deeper into thicker belts.
- Pulser/Receiver Unit:
- The pulser generates electrical pulses to excite the transducer, while the receiver captures the returning signals. The equipment then interprets these signals to identify structural variations.
- Signal Processor:
- Modern ultrasonic testing equipment includes a signal processing unit that converts sound wave reflections into readable data or visual representations (like graphs or images).
- Display Unit:
- The display screen provides a real-time visual of the inspection area, showing reflections and indicating potential flaws or anomalies within the belt.
- Data Storage and Analysis Software:
- Advanced equipment often includes software for data analysis, allowing for the storage of test data, which can be used for historical tracking of the belt’s condition over time. This helps predict when maintenance or replacement might be needed.
Types of Ultrasonic Testing for Conveyor Belts
- Pulse-Echo Testing:
- This method sends a single pulse of sound into the belt material. When this pulse encounters a flaw, it reflects back to the transducer. The time taken for the echo to return helps determine the flaw’s location and size.
- Through-Transmission Testing:
- This technique uses two transducers—one on each side of the belt. One transducer sends a pulse, and the other receives it. If the pulse is interrupted or weakened, it indicates a flaw or material irregularity.
- Phased Array Ultrasonic Testing (PAUT):
- PAUT involves multiple transducers that can be programmed to focus at different depths and angles within the belt. This method provides a detailed, cross-sectional image, making it easier to detect and size complex defects like delaminations or voids.
Applications of Ultrasonic Testing for Conveyor Belts
- Detecting Internal Defects:
- Ultrasonic equipment is highly effective at identifying internal flaws such as voids, inclusions, and delaminations within the belt structure. This is especially important for belts with multi-layer construction or steel reinforcements.
- Monitoring Adhesion Quality:
- UT can be used to inspect the bonding quality between different belt layers. Weak adhesion between layers can lead to belt failure, so periodic ultrasonic testing helps ensure the bonding remains intact.
- Evaluating Belt Thickness:
- Ultrasonic equipment can measure belt thickness at various points, allowing operators to monitor wear over time. This is especially valuable for belts exposed to abrasive materials.
- Steel Cord Inspection:
- In steel-reinforced conveyor belts, ultrasonic testing can detect breaks, corrosion, and other forms of damage within the steel cords, providing insights into the belt’s overall strength and longevity.
Advantages of Ultrasonic Equipment for Conveyor Belt Testing
- Non-Destructive:
- UT is a non-invasive technique, which means it does not harm the belt or require downtime for testing. This allows for frequent inspections without disrupting operations.
- Accurate and Reliable:
- Ultrasonic testing provides high-resolution data, enabling the detection of even small flaws. This accuracy helps prevent unexpected belt failures.
- Early Defect Detection:
- By identifying defects early, UT helps in planning maintenance, reducing the risk of costly, unplanned downtime, and extending the belt’s service life.
- Data-Driven Maintenance:
- UT provides quantitative data on the belt’s condition, allowing for data-driven maintenance and replacement decisions.
Ultrasonic testing equipment is an invaluable tool for conveyor belt maintenance and quality assurance, helping industries maintain operational efficiency by enabling early flaw detection. With the ability to assess internal conditions without damaging the belt, ultrasonic testing supports predictive maintenance practices, ultimately enhancing conveyor belt safety, reliability, and longevity.
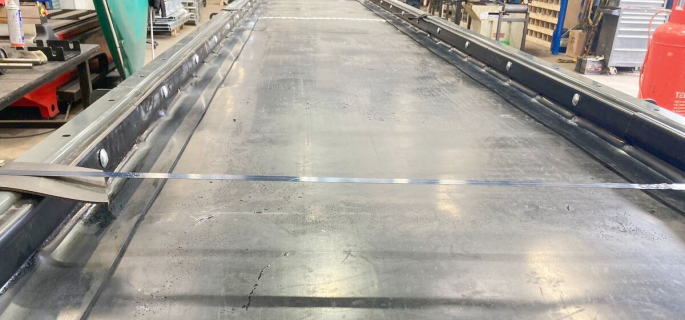
Conveyor Belt Testing Procedures
The procedures involved in conveyor belt testing are meticulously designed to evaluate the performance and durability of conveyor belts under various conditions. These standardized procedures are crucial for obtaining accurate and reliable results, which are essential for ensuring the safety and efficiency of conveyor belt operations.
- Abrasion Tests: One of the primary procedures in conveyor belt testing procedure is the abrasion test. This test assesses the wear resistance of the belt material when subjected to continuous friction. The process involves running an abrasive surface against the belt and measuring the material loss. This test helps in determining the lifespan of the belt under normal working conditions.
- Elongation Tests: Elongation tests are conducted to measure the extent to which a conveyor belt can stretch without permanent deformation. During this test, a specific length of the belt is subjected to a tension force until it reaches its breaking point. The elongation at break is recorded to assess the belt’s elasticity and flexibility. This test is crucial for understanding how the belt will behave under strain and load.
- Tensile Strength Tests: Tensile strength testing is a critical part of conveyor belt testing. It involves applying a progressively increasing force to a belt sample until it breaks. The maximum force the belt can withstand before failure provides a measure of its tensile strength. This test is vital for determining the load-carrying capacity of the belt and ensuring it is suitable for the intended application.
Following these standardized testing procedures is essential for ensuring the conveyor belts meet the required safety and quality standards. Accurate testing results are crucial for predicting the performance of the belts in real-world conditions and for making informed decisions about their suitability for specific applications. Therefore, adherence to these conveyor belt testing procedures is not just a matter of compliance, but a commitment to safety and reliability in conveyor belt operations.
Conveyor Belt Testing Standards
In the realm of conveyor belt testing, adherence to established standards is paramount for ensuring uniformity and reliability in testing results. These standards, set by recognized organizations such as the International Organization for Standardization (ISO) and the American Society for Testing and Materials (ASTM), provide a framework for evaluating various aspects of conveyor belt quality and performance.
ISO Standards: The ISO standards for conveyor belt testing procedure are comprehensive and cover various aspects of a conveyor belt’s performance. For instance, ISO 5048 specifies methods for calculating the operating power requirements and the strength of the belt components. ISO 3684 provides guidelines on the determination of minimum pulley diameters. These standards ensure that conveyor belts are tested under consistent conditions, providing reliable data for evaluating their suitability for different industrial applications.
ASTM Standards: ASTM standards are widely recognized in the United States and internationally. ASTM D378 covers the testing of rubber belts used in conveyors, focusing on aspects like the tensile strength of the belt and its resistance to abrasion. ASTM D2240, while not specific to conveyor belts, is often used to measure the hardness of rubber materials, including those used in conveyor belts. These standards help in assessing the quality and durability of the belts, ensuring they meet the required safety and performance criteria.
By adhering to these conveyor belt testing standards, manufacturers and users can be assured of the quality and reliability of the conveyor belts. These standards not only facilitate uniform testing procedures across different manufacturers and industries but also instill confidence in the end-users about the product’s safety and efficiency. Consequently, these standards play a crucial role in the global market, enabling compatibility and comparability of conveyor belts from different sources.
Conveyor Belt Hardness and Hardness Chart in Conveyor Belt Testing
Understanding the hardness of conveyor belts is a critical aspect of conveyor belt testing. Hardness, in the context of conveyor belts, refers to the resistance of the material to permanent indentation. It is a key factor that influences the belt’s wear resistance, flexibility, and overall durability. The hardness of a conveyor belt affects how it interacts with the materials it transports and the various components of the conveyor system, such as rollers and pulleys.
In conveyor belt testing, the hardness is typically measured using a durometer, a device that gauges the depth of an indentation in the material made by a standardized presser foot. This measurement is expressed in Shore Hardness units, commonly on the Shore A scale for rubber materials. The hardness values can range from very soft and flexible materials to very hard and rigid ones.
The conveyor belt hardness chart is an essential tool used in this context. It provides a visual representation of hardness levels, helping users understand where a particular belt falls on the hardness scale. For instance, a lower Shore A value indicates a softer, more flexible material, which might be suitable for applications requiring good grip and adaptability. On the other hand, a higher Shore A value signifies a harder material, which might be more appropriate for heavy-duty or abrasive applications where wear resistance is crucial.
Interpreting the conveyor belt hardness chart is vital for selecting the right belt for specific applications. It helps in determining the suitability of a belt in terms of load-bearing capacity, resistance to abrasion, and compatibility with the conveyed material and the operating environment. By understanding and utilizing the hardness chart effectively in conveyor belt testing, manufacturers and end-users can make informed decisions, ensuring optimal performance and longevity of the conveyor belts.
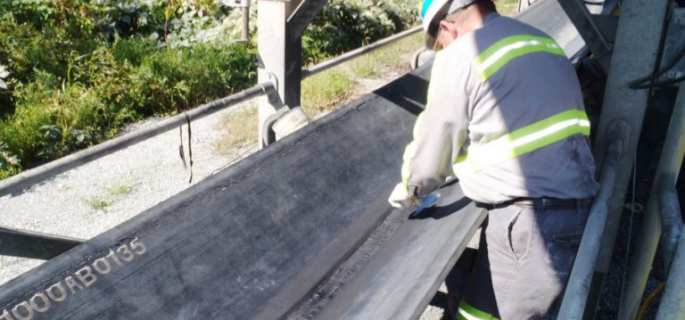
Conveyor Belt Splicing and Testing
In the realm of conveyor belt testing, the process of splicing plays a pivotal role. Splicing refers to the method of joining the ends of conveyor belts to form a continuous loop. This process is crucial as it directly impacts the belt’s strength, operational efficiency, and overall lifespan. In conveyor belt testing, evaluating the effectiveness and durability of splicing methods is essential to ensure the reliability of the conveyor system.
Role of Splicing in Conveyor Belt Testing
Role of Splicing in Conveyor Belt Testing
During conveyor belt testing procedure, splicing is scrutinized to assess its strength and compatibility with the belt’s material. The testing process involves subjecting the spliced section to various stresses and strains that mimic real-world operational conditions. This includes tensile strength tests, where the spliced area is subjected to increasing tension to determine its maximum load-bearing capacity. Additionally, fatigue tests may be conducted to evaluate how the splice withstands repetitive stress over time.
Impact of Splicing on Performance and Durability
The method and quality of splicing have a significant impact on the conveyor belt’s performance. A poorly executed splice can become the weakest link in the conveyor belt, leading to potential failures and operational disruptions. For instance, an improper splice can result in belt misalignment, increased conveyor belt tear and wear, and reduced tensile strength. On the other hand, a well-executed splice maintains the belt’s integrity and allows for smooth operation. It ensures that the belt can handle the intended load without risk of separation or damage at the splice.
In conveyor belt testing, various splicing techniques, such as mechanical fastening, vulcanization, or cold bonding, are evaluated to determine their suitability for different types of conveyor belts and operational demands. The choice of splicing method depends on factors like the belt material, the operating environment, and the nature of the materials being conveyed. By thoroughly testing and assessing the splicing methods, conveyor belt manufacturers and users can ensure that the belts are not only fit for purpose but also offer longevity and reliability in their applications.
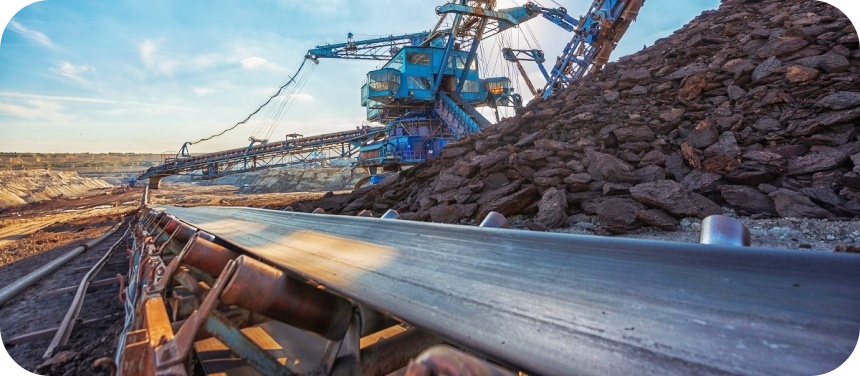
Practical Considerations in Conveyor Belt Testing
When it comes to conveyor belt testing, there are several practical considerations that businesses and operators must take into account to ensure the effectiveness and reliability of their conveyor systems. Two key aspects in this regard are locating nearby testing facilities and accessing comprehensive resources for a deeper understanding of conveyor belt testing.
Conveyor Belt Testing Near Me: Finding local testing facilities is a crucial step for businesses that rely on conveyor belts. Proximity to testing facilities can significantly reduce downtime and logistical complexities. To locate nearby testing services, businesses can search online directories, consult industry associations, or reach out to conveyor belt manufacturers who often have partnerships with testing facilities. Local testing centers offer a range of services, including routine testing, emergency analysis, and certification of conveyor belts. By choosing a nearby facility, companies can ensure quick turnaround times for testing and maintenance, thereby minimizing operational disruptions.
Conveyor Belt Testing PDF: For those seeking an in-depth understanding of conveyor belt testing procedure, numerous resources are available in the form of PDF documents. These resources often include detailed guides on testing procedures, standards, and best practices. They can be found on the websites of conveyor belt manufacturers, industry associations, and standardization bodies. These PDFs serve as valuable references for understanding the technical aspects of conveyor belt testing, including the methodologies used for assessing various belt properties like tensile strength, abrasion resistance, and splice integrity. They are also useful for training maintenance staff and ensuring that in-house procedures align with industry standards.
Practical considerations in “conveyor belt testing procedure” involve not only finding and utilizing local testing facilities but also accessing and understanding comprehensive resources. These steps are essential for maintaining the high performance and safety standards of conveyor belt systems in various industrial applications.
Conveyor Belt Examples and Calculations in Conveyor Belt Testing
The application of conveyor belt testing extends beyond theoretical analysis and into real-world scenarios where conveyor belts play a crucial role. Understanding how these belts are used in various industries, along with the basic calculations for performance assessment, is essential for ensuring their optimal functionality.
Real-World Examples of Conveyor Belt Applications
Conveyor belts are integral in numerous industries, each with unique requirements and challenges. In mining, for instance, conveyor belts are designed to handle heavy loads and abrasive materials over long distances. In the food industry, belts must comply with hygiene standards and often require specific material properties to prevent contamination. In manufacturing, conveyor belts are used for assembly lines where speed and precision are key. Each of these applications demands specific conveyor belt properties, which are determined and validated through rigorous conveyor belt testing.
Basic Conveyor Belt Calculations for Performance Assessment
To assess the performance of a conveyor belt, several calculations are essential. The most basic include belt speed, load capacity, and belt tension. Belt speed is calculated based on the desired throughput and the size of the material. Load capacity depends on the belt width, the spacing of the rollers, and the density of the material being transported. Belt tension calculations are crucial for determining the strength required to move the load and keep the belt in motion without slipping. These calculations are fundamental in designing a conveyor belt system that meets specific operational requirements.
Incorporating real-world examples and basic performance calculations into conveyor belt testing provides a comprehensive understanding of how conveyor belts function in different scenarios. This approach ensures that conveyor belts are not only tested for quality and durability but are also tailored to meet the specific demands of various industrial applications.
Advanced Testing and Future Trends in Conveyor Belt Testing
The field of conveyor belt testing is continually evolving, with emerging technologies and methods shaping the future of conveyor belt design and testing. These advancements are not only enhancing the accuracy and efficiency of testing procedures but are also paving the way for innovative conveyor belt designs that can meet the growing demands of various industries.
Emerging Technologies and Methods in Conveyor Belt Testing: Recent advancements in technology have introduced new methods for testing conveyor belts. One such development is the use of digital imaging and 3D scanning to assess wear patterns and damage on the belt surface. This technology allows for more precise and comprehensive analysis than traditional visual inspections. Another emerging method is the use of sensors and IoT (Internet of Things) technology to continuously monitor the condition of the conveyor belt in real-time. These sensors can detect issues such as misalignment, abnormal vibrations, and temperature changes, enabling proactive maintenance and reducing downtime.
Future Trends and Developments in Conveyor Belt Design and Testing: Looking ahead, the future of conveyor belt testing procedure is likely to focus on sustainability and eco-friendliness. This includes the development of conveyor belts made from recycled materials or materials that are more environmentally friendly. Additionally, there is a growing trend towards designing belts that are easier to recycle at the end of their life cycle. In terms of testing, future trends may include the integration of advanced analytics and AI (Artificial Intelligence) to predict potential failures and optimize maintenance schedules. This predictive approach to maintenance, based on data-driven insights, could significantly enhance the longevity and efficiency of conveyor belts.
Advanced testing and future trends in conveyor belt testing are set to revolutionize the way conveyor belts are designed, tested, and maintained. These advancements promise not only to improve the performance and reliability of conveyor belts but also to make them more sustainable and cost-effective in the long run.
Get a customized quote for your conveyor belt needs here.
FAQs about Conveyor Belt Testing
Inspecting a conveyor belt is a critical task that should be conducted thoroughly to ensure the belt’s optimal functioning. Start by visually examining the entire length of the belt for signs of wear, tear, or damage such as cuts, cracks, or frayed edges. Pay special attention to the belt’s seams and edges. Next, inspect the belt’s tension and alignment; an improperly tensioned or misaligned belt can lead to operational issues. Check the condition of the rollers and pulleys for wear and proper rotation. Look for any material buildup that could affect the belt’s movement. Additionally, inspect the conveyor frame to ensure it is straight and level, as any misalignment can impact the belt’s performance. Electrical components, such as motors and sensors, should also be checked for proper operation. Remember, safety first: ensure the conveyor is turned off and locked out before performing any inspection.
The frequency of conveyor inspections largely depends on the usage intensity and the operational environment. For conveyors in heavy-duty operations or harsh environments, a daily inspection is recommended. This includes a quick visual check for obvious issues like belt misalignment, unusual noises, or visible wear and tear. A more comprehensive inspection should be conducted weekly and monthly, focusing on different components each time. Annually, a thorough inspection by a professional technician is advisable to assess parts that require specialized knowledge, such as gearboxes and drive trains. Keeping a regular maintenance schedule not only prolongs the life of the conveyor but also helps prevent unexpected breakdowns and costly downtime.
Troubleshooting a conveyor belt requires a systematic approach to identify and resolve issues. Start by observing the conveyor in operation, noting any unusual noises or movements. If the belt is not moving, check the electrical components, including the motor, switches, and wiring, for any faults. If the belt is moving but experiencing issues like slipping or misalignment, inspect the tension and tracking. Adjust the tension if the belt is too loose or tight. For misalignment, check the rollers and pulleys to ensure they are correctly positioned and functioning. Look for signs of wear or damage on the belt itself, such as tears or worn spots, which might require repair or replacement. Material buildup on the belt or rollers can also cause issues and should be cleaned off. If the problem persists after these checks, consult the manufacturer’s manual or a professional technician for further guidance.
Checking conveyor belt alignment is crucial for the smooth operation of the conveyor system. Begin by visually inspecting the belt while it’s running, looking for any sideways movement along the conveyor. The belt should consistently be centered on the pulleys and rollers. If you notice the belt drifting to one side, first check for debris or material buildup on the rollers, as this can cause misalignment. Next, inspect the condition and alignment of the rollers and pulleys. They should be parallel to each other and perpendicular to the conveyor frame. If adjustment is needed, use the tracking mechanisms provided on the conveyor, typically located on the end pulleys. Adjust these tracking mechanisms incrementally and observe the effect on the belt’s position. It’s important to make small adjustments and allow the belt to run for a period before making further changes. If alignment issues persist, it may indicate a more complex problem, such as uneven wear on the belt or structural issues with the conveyor frame.
The aging test for a conveyor belt involves subjecting the belt material to accelerated aging conditions, such as elevated temperatures, UV exposure, or chemical treatments, to assess its durability and performance over time. This test helps determine how well the belt resists degradation, ensuring that it will maintain its strength, flexibility, and resistance to wear in its intended operational environment.
The tensile test for a conveyor belt measures the belt’s strength and elasticity by applying a controlled, gradual pulling force until it breaks. This test helps evaluate the maximum load the belt can bear and its elongation properties. High tensile strength and proper elongation characteristics are essential for conveyor belts to withstand the forces applied during operation.
Key items to check on a conveyor belt include:
Surface condition: Look for cracks, cuts, or signs of wear.
Alignment: Ensure the belt is tracking correctly without deviation.
Tension: Check for proper belt tension to prevent slippage and excess wear.
Three essential inspection points on conveyor belts are:
Belt surface and edges: Look for tears, holes, or frayed edges that could lead to further damage.
Belt tracking: Ensure the belt is properly aligned on the pulleys and rollers.
Tension and splice integrity: Check for correct tension and examine splices for any loosening or wear.
To check the quality of a conveyor belt, examine the material composition, uniform thickness, surface smoothness, and resistance to abrasion. Perform strength tests, check the belt’s flexibility, and assess its ability to handle the required load. A high-quality belt should show durability, flexibility, and resistance to wear under operational conditions.
To check the RPM (revolutions per minute) of a conveyor belt, use a tachometer or a contact-based speed sensor on the belt’s pulley. Alternatively, if you know the belt’s speed and the pulley diameter, you can calculate the RPM by using the formula:
RPM=Belt Speed (m/s)×60 /Pulley Circumference (m)
This will give you the RPM of the conveyor belt system.
Last Updated on October 31, 2024 by Jordan Smith
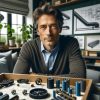
Jordan Smith, a seasoned professional with over 20 years of experience in the conveyor system industry. Jordan’s expertise lies in providing comprehensive solutions for conveyor rollers, belts, and accessories, catering to a wide range of industrial needs. From initial design and configuration to installation and meticulous troubleshooting, Jordan is adept at handling all aspects of conveyor system management. Whether you’re looking to upgrade your production line with efficient conveyor belts, require custom conveyor rollers for specific operations, or need expert advice on selecting the right conveyor accessories for your facility, Jordan is your reliable consultant. For any inquiries or assistance with conveyor system optimization, Jordan is available to share his wealth of knowledge and experience. Feel free to reach out at any time for professional guidance on all matters related to conveyor rollers, belts, and accessories.