Guide to Choosing Conveyor Belt Thickness for Optimal Performance
Conveyor belt thickness is a pivotal aspect in the realm of industrial applications, holding significant sway over both performance and durability. This concept is not merely about the physical dimension; rather, it embodies the capacity of conveyor belts to withstand various operational demands. The thickness of a conveyor belt is tailored to cater to the specific requirements of the material it conveys, the environment it operates in, and the mechanical stresses it endures. It acts as a critical factor in determining the belt’s resistance to wear and tear, impact, and overall longevity. In essence, the right conveyor belt thickness is instrumental in ensuring seamless, efficient, and cost-effective material handling, thereby playing a key role in the optimization of industrial processes. This brief overview underscores its importance and sets the stage for a deeper exploration into how conveyor belt thickness impacts the intricate world of conveyor systems.
The Essentials of Conveyor Belt Thickness
Conveyor belt thickness is a critical measurement in the design and application of conveyor systems. It refers to the depth of the belt material itself, from the top surface to the bottom. This measurement is not just a dimensional attribute; it significantly influences the belt’s capability to handle various types of loads, resist wear and tear, and operate efficiently in different environments. The right conveyor belt thickness is paramount for ensuring that the belt can endure the physical demands of the materials it transports, whether they are heavy, abrasive, or require delicate handling.
The importance of selecting the appropriate thickness cannot be overstated. In heavy-duty industries like mining or construction, a thicker belt is essential to withstand the harsh conditions and heavy loads. Conversely, in sectors like food processing or pharmaceuticals, where flexibility and precision are more critical, a thinner belt may be more suitable. This selection impacts not only the durability of the conveyor belt but also the efficiency and safety of the entire conveying process.
To assist in the selection process, a thickness of conveyor belt chart is an invaluable tool. This chart provides a range of thicknesses suited for various applications, helping users choose the most appropriate belt for their specific needs. Below is an overview of a typical conveyor belt thickness chart:
This chart illustrates that conveyor belt thickness varies considerably depending on the intended use. By consulting such a chart, businesses can make informed decisions about which belt thickness is most suitable for their particular industrial application, ensuring optimal performance and longevity of their conveyor system.
Types of Conveyor Belts and Their Thickness

The selection of the right conveyor belt thickness is heavily dependent on the type of conveyor belt being used. Each type of belt, whether it’s rubber, 2 ply, 3 ply, 4 ply, or 5 ply, has its unique thickness range that caters to specific operational needs. Understanding these variations is crucial for ensuring the belt’s suitability for the intended application, whether it’s for heavy-duty tasks like mining or for lighter duties such as packaging or assembly lines.
To provide a clearer understanding, the following table breaks down common types of conveyor belts and their respective thicknesses:
When comparing heavy-duty versus light-duty conveyor belts, one of the most significant differences lies in their thickness. Heavy-duty belts, such as 4 ply and 5 ply, are thicker to provide greater strength and durability. They are designed to withstand the high stresses of heavy loads and harsh operating conditions, commonly found in industries like mining and construction.
Conversely, light-duty belts like 2 ply and 3 ply are thinner, offering more flexibility and efficiency for less demanding tasks. These belts are typically used in applications such as retail, distribution, and light manufacturing, where the loads are lighter and the operational conditions are less severe.
In terms of standard measurements, conveyor belt thickness is typically measured in millimeters (mm). The choice of thickness must be aligned with the operational requirements of the conveying system, considering factors like the weight of the material being transported, the speed of the conveyor, and the environmental conditions it operates in.
Selecting the appropriate thickness of conveyor belt is a critical decision that impacts the efficiency, safety, and cost-effectiveness of industrial operations. This section emphasizes the importance of understanding the different types of conveyor belts and their respective thickness ranges, enabling a more informed selection process.
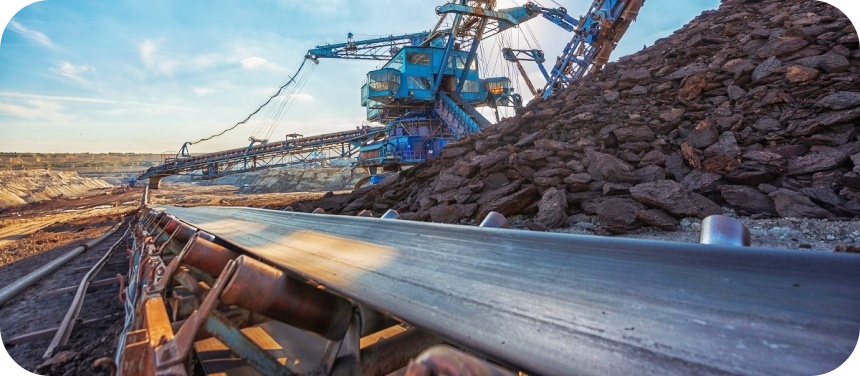
Choosing the Right Thickness for Your Conveyor Belt
Selecting the appropriate conveyor belt thickness is not a decision to be taken lightly. It is a process influenced by a multitude of factors, each playing a critical role in ensuring that the conveyor system operates efficiently, safely, and cost-effectively. Understanding these factors is key to making an informed choice that aligns with the specific needs of your industrial application.
Factors Influencing the Choice of Conveyor Belt Thickness
Load Capacity: The weight and nature of the material being transported are perhaps the most significant factors. Heavier and more abrasive materials require a thicker belt for enhanced durability and resistance to wear and tear.
Conveying Distance: Longer conveyor systems typically demand thicker belts. This is due to the increased exposure to mechanical stresses and potential damage over longer distances.
Environmental Considerations: Factors such as exposure to chemicals, extreme temperatures, and UV radiation can dictate the need for specialized belt materials and thicknesses.
Type of Material: The physical properties of the material being conveyed (e.g., sharpness, temperature) can also influence thickness requirements.
Operational Speed and Frequency: Higher speeds and more frequent use can lead to quicker wear, necessitating a thicker belt for prolonged life.
Case Studies/Examples
For instance, in mining operations where conveyor belts transport heavy and sharp materials over long distances, choosing a belt with inadequate thickness can lead to frequent replacements and downtime. A study in a mining facility showed that increasing the belt thickness by just 2mm resulted in a 20% increase in the belt’s operational life.
In contrast, XYZ Packaging Facility found that using a thinner, lighter belt significantly improved their system’s efficiency and reduced energy costs. This adjustment was ideal for their specific conveying needs, which involved lighter loads and shorter distances.
Using the Conveyor Belt Thickness Chart Effectively
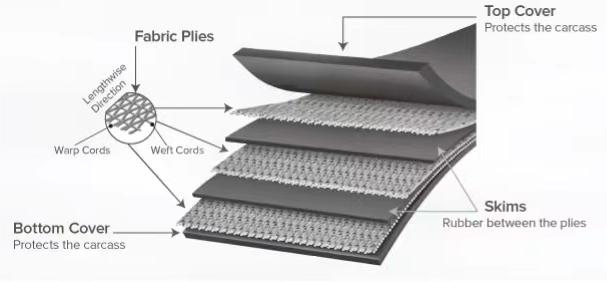
A conveyor belt thickness chart is an invaluable tool in the selection process. It lists various belt types along with their standard thicknesses, tailored for different applications. Here’s how to use it effectively:
Identify Your Requirements: Consider the factors mentioned above – load capacity, material type, etc.
Consult the Chart: Match your requirements with the suggested thickness ranges for different belt types.
Consider Manufacturer Recommendations: Manufacturers often provide specific guidance based on extensive testing and experience.
Seek Expert Advice: If in doubt, consulting with industry experts or engineers can provide additional insights.
The choice of conveyor belt thickness should be a carefully considered decision, based on a thorough understanding of the operational requirements and environmental conditions. Proper selection not only ensures the longevity and efficiency of the conveyor belt but also contributes significantly to the overall success and sustainability of the industrial operation.
Conveyor Belt Grade
Understanding the different grades of conveyor belts and their specific applications is essential for selecting the right belt for your needs. Conveyor belt grades are categorized based on conveyor belt material properties, durability, and suitability for various industrial applications. This section will discuss the most common conveyor belt grades—Grade A, Grade B, and Grade C—and provide guidance on how to choose the appropriate grade based on your application requirements.
Different Grades of Conveyor Belts and Their Applications
Grade A: Abrasion-Resistant Belts
Characteristics:
Grade A conveyor belts are designed to be highly resistant to abrasion. They are made from materials that can withstand constant friction and contact with sharp or rough materials without wearing down quickly.
Applications:
These belts are ideal for applications that involve handling sharp, abrasive materials such as rocks, minerals, gravel, and crushed stone. They are commonly used in the mining, quarrying, and construction industries where the belt is subject to continuous wear and tear from abrasive loads.
Benefits:
The high abrasion resistance of Grade A belts ensures a longer lifespan and reduces the frequency of belt replacements, leading to lower maintenance costs and increased productivity.
Grade B: General-Purpose Belts
Characteristics:
Grade B conveyor belts are designed for general-purpose use. They offer a good balance of durability, flexibility, and resistance to various environmental conditions.
Applications:
These belts are suitable for a wide range of applications, including the transportation of bulk materials, agricultural products, and packaged goods. They are commonly used in industries such as agriculture, food processing, manufacturing, and warehousing.
Benefits:
The versatility of Grade B belts makes them a cost-effective choice for many operations. They provide reliable performance across different applications and can handle moderate levels of abrasion and impact.
Grade C: Impact-Resistant Belts
Characteristics:
Grade C conveyor belts are specifically designed to withstand high impact loads. They are made from materials that provide extra cushioning and shock absorption to prevent damage from heavy, falling objects.
Applications:
These belts are ideal for heavy-duty applications where the belt is exposed to significant impact forces, such as in the handling of large, heavy materials like steel, logs, and heavy machinery parts. They are commonly used in industries such as steel manufacturing, lumber processing, and heavy machinery.
Benefits:
The impact resistance of Grade C belts ensures that they can handle heavy loads without suffering damage, reducing downtime and the need for frequent repairs or replacements.
How to Choose the Appropriate Grade Based on Application Requirements
Selecting the right conveyor belt grade is crucial for ensuring efficient operation, minimizing maintenance costs, and extending the lifespan of the belt. Here are some factors to consider when choosing the appropriate grade for your application:
Material Characteristics:
Assess the type of materials you will be transporting. For abrasive materials, a Grade A belt with high abrasion resistance is essential. For general bulk materials, a Grade B belt will suffice, while for heavy, impact-prone materials, a Grade C belt is necessary.
Operational Conditions:
Consider the environmental conditions the belt will be exposed to, such as temperature, humidity, and exposure to chemicals. Ensure the chosen belt grade can withstand these conditions without degrading.
Load and Impact:
Evaluate the weight and size of the materials being transported. Heavy and bulky loads that create significant impact require a Grade C belt for optimal performance. Lighter, less abrasive materials can be handled with Grade B belts.
Frequency of Use:
Determine the frequency and duration of conveyor belt operation. For continuous, high-intensity use, choose a belt grade that offers enhanced durability and resistance to wear.
Cost Considerations:
While higher-grade belts may have a higher initial cost, they often result in lower long-term maintenance and replacement expenses. Consider the total cost of ownership when selecting the belt grade.
Compliance with Standards:
Ensure the chosen belt grade meets industry standards and regulations for safety and performance. This can help in maintaining operational compliance and avoiding potential legal issues.
Contact us today for top-quality conveyor belts tailored to your needs.
Technical Specifications and Standards for Conveyor Belt Thickness
The technical specifications and standards for conveyor belt thickness are integral in defining the quality, durability, and suitability of conveyor belts for various industrial applications. These standards, often available in PDF format for easy accessibility and reference, provide a comprehensive guideline for manufacturers, engineers, and end-users.
Overview of Conveyor Belt Specification Standards (PDF Format)
Conveyor belt specification standards are documents that outline crucial parameters such as thickness, width, tensile strength, material composition, and other physical and chemical properties. Standards such as those from the International Organization for Standardization (ISO) and the American Society for Testing and Materials (ASTM) are widely recognized. For example, ISO 10247 and ASTM D378 detail specifications for different types of conveyor belts. These documents are essential in ensuring uniformity and compatibility across conveyor belt systems globa
The Relationship Between Conveyor Belt Width and Thickness
The width and thickness of a conveyor belt are interrelated and play a vital role in the belt’s load-bearing capacity and operational efficiency. Wider belts typically require greater thickness to evenly distribute the weight of the materials being transported, ensuring stability and reducing the risk of belt deformation or failure. This relationship is critical in applications involving heavy or bulky materials where the distribution of load is a key concern. Standards provide guidelines on optimal width-to-thickness ratios for different types of conveyor systems.
Rubber Conveyor Belt Specification: Key Features and Standards
Rubber conveyor belts, known for their flexibility, strength, and durability, have specific standards outlining their ideal thickness and other key features. These standards take into account factors such as the type of rubber, the environment in which the belt will be used (e.g., temperature, exposure to chemicals), and the physical demands of the conveying process. Specifications detail the minimum and maximum thickness for different categories of rubber belts, ensuring they are fit for purpose. For example, the thickness for a standard heavy-duty rubber conveyor belt used in mining may differ from that used in a food processing plant.
Adhering to technical specifications and standards for conveyor belt thickness is crucial in ensuring the efficiency, safety, and longevity of conveyor systems. These standards provide a foundation for selecting the right conveyor belt, tailored to the specific needs of each industrial application. They ensure that the belts not only meet the required performance parameters but also contribute to the overall reliability and effectiveness of the conveying system.
Conveyor Belt Thickness Measurement
Measuring the thickness of a conveyor belt is essential for ensuring its optimal performance and longevity. Accurate measurement allows for the detection of wear and tear, helping to prevent potential failures and costly downtime. This section will discuss the tools and techniques for accurately measuring conveyor belt thickness, the importance of regular checks, and provide a step-by-step guide for measurement.
Tools and Techniques for Accurately Measuring Conveyor Belt Thickness
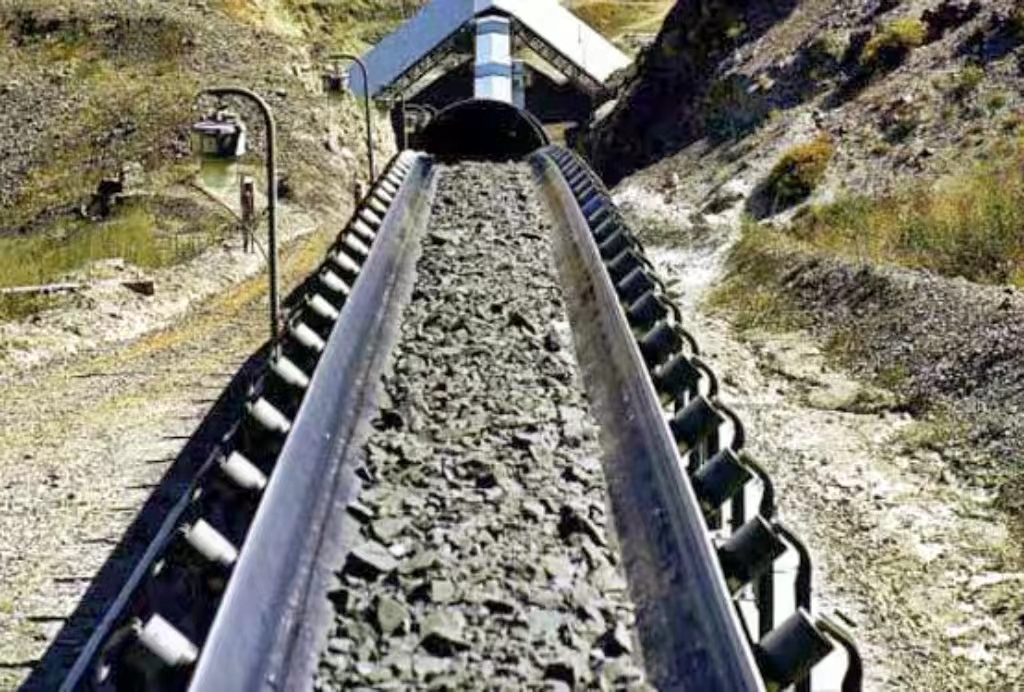
Tools:
Calipers:
Calipers are a versatile tool that can measure the thickness of a conveyor belt with high precision. They are particularly useful for measuring thinner belts and smaller areas where detailed accuracy is required.
Micrometers:
Micrometers offer an even higher level of precision than calipers, making them ideal for measuring the thickness of thicker or more robust conveyor belts. They are capable of providing readings to the nearest hundredth or thousandth of a millimeter.
Techniques:
Multiple Measurement Points:
To get an accurate representation of the belt’s thickness, it is important to take measurements at multiple points along the belt. This helps to account for any variations in thickness due to wear, damage, or manufacturing inconsistencies.
Averaging for Accuracy:
By averaging the measurements taken from different points along the belt, you can obtain a more accurate overall thickness. This method reduces the impact of any anomalies or localized wear.
Importance of Regular Thickness Checks to Maintain Belt Performance
Regularly checking the thickness of a conveyor belt is crucial for maintaining its performance and extending its lifespan. Here are some key reasons why:
Early Detection of Wear and Tear:
Regular thickness measurements can help detect early signs of wear and tear, allowing for timely maintenance and repairs. This can prevent minor issues from developing into major problems that could lead to costly downtime.
Ensuring Consistent Performance:
By monitoring the thickness of the belt, you can ensure that it continues to operate efficiently and effectively. Any significant deviations from the standard thickness can indicate potential issues that need to be addressed.
Safety:
Conveyor belts that are worn or damaged can pose a safety risk to workers. Regular thickness checks help to ensure that the belt remains in good condition and safe to use.
Cost Savings:
Preventive maintenance based on regular thickness checks can save money in the long run by avoiding expensive emergency repairs and extending the life of the conveyor belt.
Step-by-Step Guide on How to Measure Belt Thickness
Follow these steps to measure the thickness of a conveyor belt accurately:
Gather Tools:
Ensure you have the appropriate measuring tool, either a caliper or a micrometer, that is properly calibrated.
Select Measurement Points:
Identify several points along the conveyor belt to take measurements. Avoid the edges, as they might be uneven or more worn than the rest of the belt.
Prepare the Belt:
If the belt is in use, ensure the conveyor system is turned off and the belt is stationary. This ensures safety and accurate measurements.
Measure the Thickness:
Place the caliper or micrometer perpendicular to the belt surface at the first measurement point. Close the tool gently until it just touches the belt surface without compressing the material.
Record the measurement displayed on the tool.
Repeat Measurements:
Move to the next measurement point and repeat the process. Take measurements at multiple points along the length and width of the belt.
Calculate the Average:
Once you have collected all the measurements, calculate the average thickness by summing all the readings and dividing by the number of measurement points.
Compare to Specifications:
Compare the average thickness to the belt’s original specifications or standard thickness guidelines provided by the manufacturer. Note any significant deviations, which could indicate wear or the need for replacement.
Document the Results:
Keep a record of the measurements and any observations for future reference. This documentation can help track the wear over time and inform maintenance decisions.
By following these steps, you can ensure that your conveyor belt thickness measurements are accurate and consistent, helping to maintain the performance and longevity of the belt. Regular monitoring and maintenance are key to avoiding unexpected failures and ensuring the smooth operation of your conveyor system.
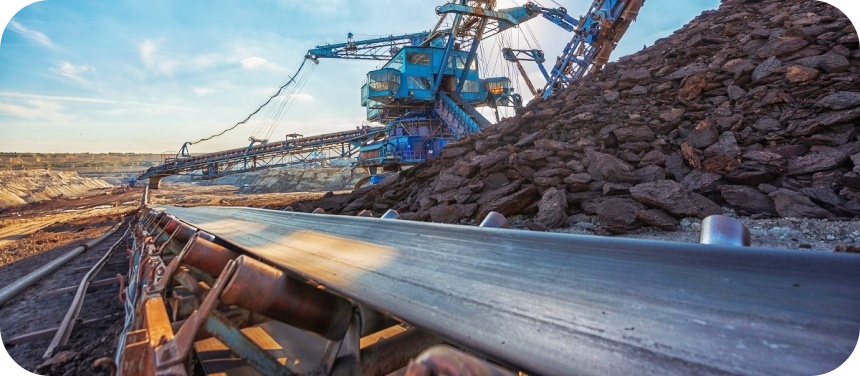
Practical Applications and Considerations for Conveyor Belt Thickness
In the world of conveyor belts, understanding the practical applications and considerations of conveyor belt thickness is crucial for optimal performance and durability. This section delves into the specifics of various ply conveyor belts and how environmental factors and application-specific requirements influence the selection of the appropriate thickness of conveyor belt.
Detailed Discussion on Specific Ply Conveyor Belts and Their Applications
- 2 Ply Conveyor Belts: These belts are typically thinner and more flexible, suitable for light-duty applications such as food processing, packaging, and light material handling. Their thinner design allows for better handling of small items and smoother operation in systems requiring frequent starts and stops.
- 3 Ply Conveyor Belts: Offering a balance between thickness and flexibility, 3 ply belts are commonly used in medium-duty applications. They are well-suited for agricultural, woodworking, and general manufacturing where moderate loads are transported.
- 4 Ply Conveyor Belts: These are designed for heavier loads and more demanding applications, such as mining, heavy manufacturing, and bulk material handling. The increased thickness provides enhanced durability and resistance to wear and tear in harsh conditions.
- 5 Ply Conveyor Belts: These are the thickest and most robust, ideal for extremely heavy-duty applications like heavy mining, quarrying, and where large volumes of material are moved. Their thickness ensures longevity under the stress of large, abrasive, or sharp materials.
Environmental Considerations
The choice of conveyor belt thickness is significantly affected by environmental factors. For instance:
High-Temperature Environments: Thicker belts are often required in these settings to prevent heat-induced degradation.
Chemical Exposure: Certain industries involve exposure to chemicals where thicker, specially coated belts are necessary to withstand corrosion.
Outdoor Use: Belts used outdoors need to be thicker to resist weather-related wear, such as UV damage or extreme temperature fluctuations.
Guidelines for Selecting the Appropriate Width and Thickness
When selecting a conveyor belt, consider the following guidelines:
- Assess the Load: Understand the weight, size, and nature of the material to be conveyed. Heavier, larger, or more abrasive materials typically require thicker belts.
- Consider the Conveyor System: The length of the conveyor system and the speed at which it operates can influence the thickness required. Longer systems and higher speeds often necessitate thicker belts.
- Evaluate Environmental Conditions: Assess the operational environment, including temperature, exposure to chemicals, and the presence of moisture or UV light.
- Match Belt Width and Thickness: Ensure that the belt width is appropriate for the load and the system. A wider belt might require increased thickness to distribute the load evenly.
The selection of the right conveyor belt thickness is a multifaceted decision that depends on the specific application, the environment in which the belt will operate, and the nature of the materials being conveyed. Understanding these factors ensures that the chosen belt not only meets the operational demands but also maintains its integrity and efficiency over time.
Maintenance and Longevity of Conveyor Belts Considering Conveyor Belt Thickness
The longevity and efficient operation of a conveyor belt are heavily influenced by its thickness. Choosing the right conveyor belt thickness is not only about immediate operational needs but also about long-term maintenance and durability. This section explores the maintenance practices crucial for different types of conveyor belts based on their thickness and material, aiming to maximize their lifespan and efficiency.
Importance of Choosing the Right Thickness for Belt Longevity and Efficient Operation
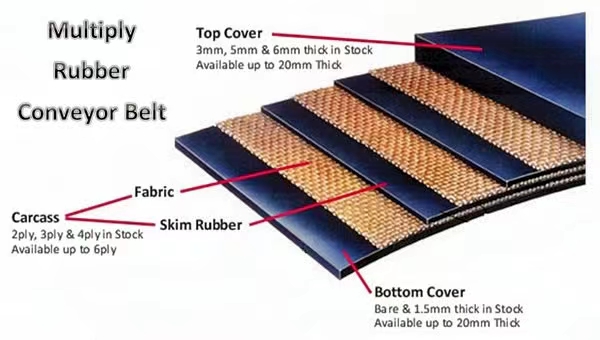
A thicker conveyor belt generally offers greater durability and resistance to wear, tear, and puncture, especially in heavy-duty applications like mining or construction. However, it’s important to balance thickness with the specific needs of the operation, as an overly thick belt can lead to increased energy consumption and strain on conveyor system components.
Conversely, a thinner belt may be more suitable for lighter-duty applications but may require more frequent maintenance or replacement. The key is to select a thickness that provides the necessary strength without overburdening the system.
Tips on Maintaining Different Types of Conveyor Belts Based on Their Thickness and Material
Tips on Maintaining Different Types of Conveyor Belts Based on Their Thickness and Material
- Regular Inspection and Cleaning: Regardless of thickness, all conveyor belts should be regularly inspected for signs of wear, damage, or misalignment. Cleaning is also crucial to remove any materials that could degrade the belt over time.
- Monitoring Belt Tension: Proper tension is vital for all belts. Over-tensioning a thick belt can cause excessive wear on conveyor rollers and bearings, while under-tensioning can lead to slippage and inefficient operation.
- Addressing Environmental Factors: For belts used in harsh environments (like extreme temperatures or exposure to chemicals), special care should be taken to ensure that the belt’s material and thickness are suitable for these conditions. Additional protective measures, such as coatings or enclosures, may be required.
- Lubrication of Components: The conveyor system’s rollers, bearings, and other moving parts should be regularly lubricated to reduce friction and wear, which is especially important for thicker, heavier belts.
- Replacement Planning: Even with the best maintenance, conveyor belts will eventually wear out. Planning for replacement, particularly for thicker, heavy-duty belts, is essential to avoid unexpected downtime.
The maintenance and longevity of a conveyor belt are closely tied to its thickness. The right thickness not only ensures the belt’s optimal performance and durability but also influences the maintenance strategies required to keep the conveyor system running smoothly and efficiently. By following these maintenance tips and understanding the needs specific to their conveyor belt’s thickness and material, operators can significantly extend the lifespan of their conveyor systems.
FAQs on Conveyor Belt Thickness
The appropriate thickness of a conveyor belt depends on various factors, including the type of material being transported, the distance of transport, the load capacity, and the specific conditions of the environment in which it operates. In general, light-duty applications, such as packaging or food processing, may require thinner belts for flexibility and precision, while heavy-duty applications, like mining or construction, typically need thicker belts for durability and strength. The right thickness is crucial to balance the belt’s durability, efficiency, and operational costs. Consulting with belt manufacturers and referring to industry standards can provide guidance in making the best choice for a specific application.
A 3 ply conveyor belt typically has a thickness ranging from around 5 to 10 millimeters, but this can vary based on the materials used and the specific construction of the belt. The thickness of the top cover for specialized conveyor belts should not be less than 4.5mm, with upper and bottom covers in multiples of 1.5. Each ‘ply’ refers to a layer of material, usually fabric or rubber, that makes up the belt. The three layers combined provide a balance of strength, flexibility, and durability. This type of belt is commonly used in medium-duty applications, handling moderately heavy or abrasive materials. The specific thickness required in any given application depends on several factors, including the weight of the materials being transported and the conditions of use.
A 2 ply conveyor belt is generally thinner than a 3 ply belt, with a thickness usually ranging from about 2 to 5 millimeters. This type of belt is designed for lighter applications and is made up of two layers of material. 2 ply belts are often used in settings where flexibility and lightness are more important than the ability to handle heavy loads. These belts are suitable for industries such as food processing, packaging, or light manufacturing, where they handle smaller, less abrasive materials. As with any conveyor belt, the exact thickness can vary based on the specific materials and design of the belt.
Mining conveyor belts are designed for heavy-duty and high-capacity applications, thus they are significantly thicker than standard conveyor belts. The thickness of a mining conveyor belt can range from around 10 millimeters to over 20 millimeters. These belts are built to withstand the harsh conditions of mining operations, including the impact and abrasion of heavy, coarse materials. The increased thickness provides the necessary durability and strength required for such demanding applications. The exact thickness needed in a mining environment will depend on several factors, including the type of materials being transported, the distance of transport, and the specific demands of the mining operation.
The standard thickness of a conveyor belt can vary depending on the type and application of the belt. For instance:
General-purpose conveyor belts: Typically range from 5 to 12 millimeters in thickness.
3 ply conveyor belts: Generally have a thickness ranging from 5 to 10 millimeters.
Specialty conveyor belts: Such as heat-resistant, cold-resistant, oil-resistant, and acid-resistant belts, may have customized thicknesses as per specific application requirements. The thickness of the top cover for these belts can vary based on customer needs and the specific demands of the working environment.
Checking the thickness of a conveyor belt is an essential part of maintenance to ensure optimal performance and longevity. Here are the steps to accurately measure belt thickness:
Gather Tools:
Use a precise measuring tool such as a caliper or a micrometer.
Ensure the tool is calibrated correctly before use.
Select Measurement Points:
Choose several points along the belt to measure, including areas that may experience the most wear and tear.
Avoid measuring at the belt edges as they might be uneven.
Measure the Belt:
Place the caliper or micrometer perpendicular to the belt surface.
Gently close the tool until it touches the belt surface without compressing the material.
Read and record the measurement.
Repeat for Accuracy:
Take multiple measurements at different points along the belt to ensure accuracy.
Calculate the average thickness from these measurements to get a consistent reading.
Compare to Specifications:
Compare the measured thickness to the belt’s original specifications or standard thickness guidelines provided by the manufacturer.
Note any significant deviations, which could indicate wear or the need for replacement.
Regular Inspections:
Regularly check the belt thickness as part of a routine maintenance schedule to detect wear early and maintain optimal performance.
Last Updated on June 24, 2024 by Jordan Smith
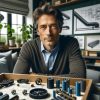
Jordan Smith, a seasoned professional with over 20 years of experience in the conveyor system industry. Jordan’s expertise lies in providing comprehensive solutions for conveyor rollers, belts, and accessories, catering to a wide range of industrial needs. From initial design and configuration to installation and meticulous troubleshooting, Jordan is adept at handling all aspects of conveyor system management. Whether you’re looking to upgrade your production line with efficient conveyor belts, require custom conveyor rollers for specific operations, or need expert advice on selecting the right conveyor accessories for your facility, Jordan is your reliable consultant. For any inquiries or assistance with conveyor system optimization, Jordan is available to share his wealth of knowledge and experience. Feel free to reach out at any time for professional guidance on all matters related to conveyor rollers, belts, and accessories.