Conveyor Belt Torque Calculation And Load Torque Required
In the realm of material handling and industrial automation, conveyor belt systems stand as the backbone, facilitating the seamless movement of goods across various stages of production and distribution. At the heart of optimizing these systems lies the critical process of conveyor belt torque calculation, a mathematical determination that ensures the machinery operates within its optimal power range. Precise torque calculation is not just a technical necessity; it’s a strategic tool that significantly enhances system efficiency. By accurately determining the torque required to move materials, engineers can design systems that consume less energy, maintain consistent performance, and minimize the wear and tear on mechanical components. This foundational step in conveyor belt design and maintenance ensures longevity and reliability, making it indispensable in the pursuit of operational excellence and sustainability in material handling operations.
What Is Conveyor Belt Torque Calculation
The process of conveyor belt torque calculation is a critical aspect of conveyor belt system design and operation. It involves determining the rotational force required to move the conveyor belt and, consequently, the load it carries. This calculation is fundamental because it affects nearly every aspect of conveyor belt performance, from energy consumption to operational efficiency and lifespan. Below, we explore the significance of torque in conveyor belt operations and the various factors that influence it, providing a comprehensive understanding of why belt conveyor torque calculation is indispensable.
What is Torque?
Torque is a measure of the rotational force applied to an object. It is a vector quantity, meaning it has both magnitude and direction. In simple terms, torque can be thought of as the twisting force that causes an object to rotate around an axis.
Torque is a fundamental concept in mechanics that describes the rotational effect of a force. It is crucial in various applications, from everyday tools to complex machinery, and understanding torque is essential for analyzing and designing systems involving rotational motion.
The Significance of Torque in Conveyor Belt Operations
Before diving into the specifics, it’s essential to acknowledge the overarching importance of torque in the functionality of conveyor systems. Torque represents the force that drives the conveyor belt forward, making its calculation a cornerstone of system design. Here are several points that highlight its significance:
- Energy Consumption: Accurate conveyor belt torque calculation ensures that the system uses just the right amount of energy to move the load, avoiding wastage and optimizing operational costs.
- Operational Speed: The torque directly influences how fast a conveyor belt can move, affecting the throughput and overall productivity of the system.
- Load Management: Correct torque calculations are crucial for handling different load weights, ensuring the conveyor operates reliably under various conditions.
- Durability: Properly calculated torque can reduce the strain on the conveyor system, decreasing wear and tear on components and extending their service life.
- Safety: Adequate torque ensures smooth starts and stops, enhancing the safety of operations by reducing the risk of accidents.
- Control and Precision: It allows for precise control over the conveyor’s movements, which is particularly important in applications requiring high accuracy.
- Startup Efficiency: Calculating the correct starting torque is vital for overcoming inertia and ensuring the conveyor belt starts smoothly, even when fully loaded.
Factors Influencing Conveyor Belt Torque
Understanding the factors that impact conveyor belt torque calculation is key to designing and operating efficient conveyor systems. These factors include:
- Motor Specifications: The characteristics of the motor, such as its power and efficiency, play a significant role in determining the available torque.
- Pulley Dimensions: The size of the pulleys affects the torque transmission, with larger pulleys capable of delivering more torque.
- Belt Speed Requirements: The desired or required speed of the conveyor belt influences the amount of torque needed, especially for acceleration and maintaining constant speeds.
- Load Characteristics: The weight and type of material being transported directly affect the torque requirements of the system.
- Frictional Forces: The friction between the belt and the pulleys or rollers impacts the amount of torque needed to move the belt.
- Conveyor Belt Size: The length and width of the conveyor belt contribute to the overall mass that needs to be moved, influencing torque.
- Incline Levels: Conveyors operating on an incline require additional torque to overcome gravitational forces.
- Environmental Conditions: External conditions such as temperature and humidity can alter the belt’s properties and, by extension, the torque calculation.
- Operational Dynamics: The operational pattern of the conveyor, including starts, stops, and speed variations, affects the cumulative torque requirements.
Through a detailed understanding of conveyor belt torque calculation, engineers and operators can ensure that conveyor belt systems are designed and operated for maximum efficiency, reliability, and safety. This foundational knowledge is crucial for optimizing the performance and longevity of conveyor systems in various industrial applications.
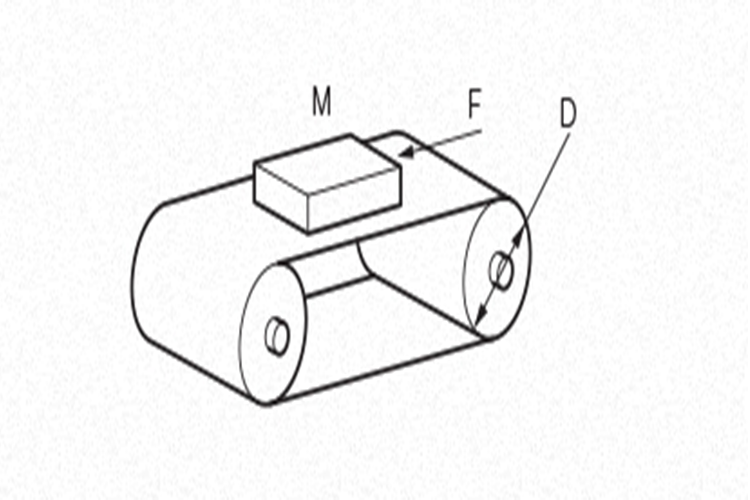
What is Load Torque?
Load torque is the torque required to overcome the resistance or load applied to a motor or mechanical system to perform work. It represents the amount of rotational force needed to keep an object or system moving at a constant speed or to accelerate it. In essence, load torque is the external torque that the motor or system must counteract to maintain its operation.
Key Concepts of Load Torque:
Definition:
- Load torque ((TL)) is the torque exerted by the load on the motor shaft or system, which must be overcome by the motor’s torque to achieve and maintain the desired motion.
Components of Load Torque:
- Frictional Torque: The torque needed to overcome friction within the system, such as bearings, gears, and other mechanical interfaces.
- Inertial Torque: The torque required to accelerate or decelerate the load, which depends on the mass and distribution of the load.
- Resistive Torque: The torque needed to overcome external resistances, such as gravity, air resistance, or any other opposing forces.
Units:
- Load torque is measured in the same units as torque, typically Newton-meters (Nm) in the SI system or pound-feet (lb-ft) in the Imperial system.
Calculating Load Torque:
The total load torque ((TL)) can be calculated by summing the individual components of torque that oppose the motion:

Applications of Load Torque:
Electric Motors:
- In electric motors, load torque is a critical parameter for selecting the appropriate motor size and type. The motor must provide enough torque to overcome the load torque and achieve the desired performance.
Mechanical Systems:
- Load torque is essential in designing and analyzing mechanical systems, such as conveyors, lifts, and machinery, where accurate calculation ensures efficient and reliable operation.
Vehicles:
- In automotive engineering, understanding load torque is crucial for drivetrain design, affecting acceleration, towing capacity, and overall vehicle performance.
Practical Example:
Consider a conveyor belt system:
- Frictional Torque: The torque needed to overcome the friction between the belt and the rollers.
- Inertial Torque: The torque required to accelerate the conveyor belt and any load it carries.
- Resistive Torque: The torque needed to lift a load if the conveyor is inclined.
The motor driving the conveyor belt must generate enough torque to counteract these components to keep the belt moving smoothly.
Load torque is the torque that a motor or system must overcome to perform work against resistance. It includes contributions from friction, inertia, and other resistive forces. Accurately determining load torque is crucial for the proper design and operation of motors and mechanical systems, ensuring they can handle the required loads efficiently and reliably.
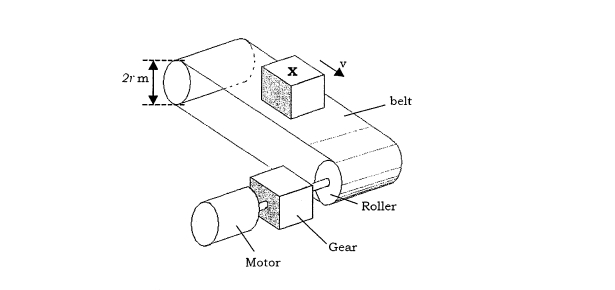
Key Parameters for Conveyor Belt Torque Calculation
The accuracy of conveyor belt torque calculation hinges on understanding and integrating several key parameters. These parameters are fundamental to determining the precise torque needed for the conveyor belt to function efficiently under various conditions. Each of these factors plays a crucial role in the overall calculation, influencing the required torque in unique ways.
Mass to Move (M): The mass of the load that the conveyor belt needs to move is a primary determinant of the required torque. A heavier load demands more torque to initiate movement and maintain a constant speed. The relationship between mass and torque is direct; as the mass increases, the torque needed to move the conveyor belt also increases. This parameter is especially critical in industries where the conveyor must handle varying load weights regularly.
Diameter of Drive Drum (D): The diameter of the drive drum affects the mechanical advantage that the conveyor system has over the load. A larger diameter drum requires less torque to move the same amount of mass compared to a smaller drum. This is because the larger radius of the drum distributes the force over a larger area, reducing the load on any single point. Consequently, the diameter of the drive drum is a vital factor in conveyor belt torque calculation, influencing the efficiency and capability of the conveyor belt to start and move the load.
Belt Speed (S): The speed at which the conveyor belt operates (belt speed) directly impacts the torque requirements. Higher speeds require more torque to overcome the inertia of the stationary load and to maintain continuous movement, especially in the case of heavy loads. The belt speed parameter must be carefully balanced with the torque capacity of the system to ensure optimal performance without overloading the motor.
Coefficient of Friction (μ): The coefficient of friction between the conveyor belt and the drive drum plays a significant role in torque calculation. A higher coefficient of friction means that less torque is needed to move the belt because the increased frictional force between the belt and drum translates into more efficient motion transfer. Conversely, a lower coefficient of friction requires more torque to achieve the same level of motion, as slippage between the belt and drum is more likely to occur.
Angle of Incline (A): The angle of incline of the conveyor belt system significantly affects the torque needed. Conveying materials uphill requires more torque due to the added force of gravity acting against the motion of the load. The steeper the incline, the greater the gravitational force that the system must overcome, and thus, the higher the torque requirement. This parameter is crucial in designing conveyor systems that are capable of efficiently transporting materials across different elevations.
A comprehensive understanding of these key parameters is essential for accurate torque calculation for conveyor belt. By carefully considering each factor, engineers can design conveyor systems that are not only efficient and reliable but also capable of meeting the specific demands of their operational environment.
Methods for Conveyor Belt Torque Calculation
Conveyor Belt Torque Calculation
Calculating the torque required for a conveyor belt system involves understanding the forces acting on the conveyor and the characteristics of the belt and load. Here’s a step-by-step guide to calculate conveyor belt torque:
Key Parameters:
- Conveyor Length (L): The length of the conveyor belt in meters.
- Conveyor Speed (v): The speed at which the conveyor belt moves, in meters per second (m/s).
- Load Mass (m): The mass of the load on the conveyor belt in kilograms (kg).
- Belt Mass (m_b): The mass of the conveyor belt itself in kilograms per meter (kg/m).
- Gravity (g): The acceleration due to gravity, approximately (9.81 \, \text{m/s}^2).
- Friction Coefficient (μ): The coefficient of friction between the conveyor belt and the rollers or between the belt and the load.
- Roller Diameter (D_r): The diameter of the conveyor rollers in meters.
Step-by-Step Calculation:
Calculate the Total Load on the Conveyor (F_total):
The total load is the sum of the mass of the conveyor belt and the mass of the load it carries.

Where:
- (m) is the mass of the load in kg.
- (m_b) is the mass of the belt per meter in kg/m.
- (L) is the length of the conveyor belt in meters.
- (g) is the gravitational constant (9.81 m/s²).
Calculate the Frictional Force (F_friction):
The frictional force is the product of the total load and the friction coefficient.

Where:
- (\mu) is the coefficient of friction.
Calculate the Torque (T):
The torque required to overcome the frictional force and move the conveyor belt can be calculated using the roller diameter.

Where:
- (Dr) is the diameter of the rollers.
Example Calculation:
Assume:
- Conveyor Length ((L)) = 20 meters
- Conveyor Speed ((v)) = 2 m/s
- Load Mass ((m)) = 500 kg
- Belt Mass ((m_b)) = 10 kg/m
- Gravity ((g)) = 9.81 m/s²
- Friction Coefficient ((\mu)) = 0.02
- Roller Diameter ((D_r)) = 0.2 meters
Total Load (F_total):

Frictional Force (F_friction):

Torque (T):

So, the torque required to move the conveyor belt is approximately 13.734 Nm.
To calculate the torque for a conveyor belt system, you need to determine the total load, the frictional force, and the dimensions of the rollers. By applying these parameters to the formulas, you can accurately calculate the torque needed to drive the conveyor belt. This helps in selecting the appropriate motor and ensuring the efficient operation of the conveyor system.
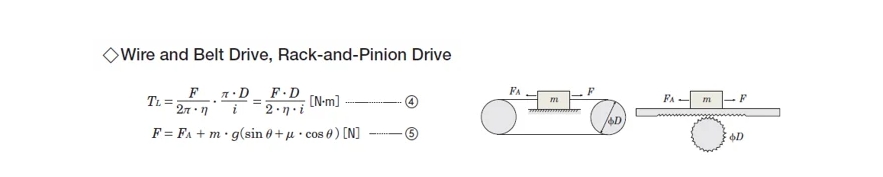
The Appropriate Starting Method
The conveyor belt torque calculation is essential for selecting the appropriate starting method for conveyor belt systems. Each starting method impacts the torque and the mechanical stress on the system differently. Understanding these methods and their effects on torque can significantly enhance system performance and longevity.
Direct-on-Line Starter
- Immediate Full Torque: Delivers full torque instantly, which can cause significant mechanical stress on the conveyor components.
- High Starting Current: Draws a large starting current, typically 6 to 10 times the motor’s full load current, impacting electrical components.
- Potential for Damage: The sudden jolt of torque can lead to wear and tear on belts, pulleys, and motors over time.
- Simple Control: Offers less complexity in control, making it straightforward but less flexible.
- Cost-Effective: Generally, the most cost-effective option due to its simplicity.
- Not Suitable for Heavy Loads: May not be suitable for conveyor systems that start under heavy loads due to the high mechanical stress involved.
- Energy Intensive: The high starting current can lead to energy waste and higher operational costs.
- Limited Applications: Best suited for applications where the conveyor starts without load or with a light load.
Star-Delta Starter
- Reduced Starting Current: Lowers the starting current to about one-third that of a direct-on-line start, reducing electrical stress.
- Gradual Torque Increase: Provides a smoother ramp-up of torque, minimizing mechanical stress.
- Complexity in Wiring: More complex wiring and control circuitry compared to direct-on-line starters.
- Energy Efficiency: More energy-efficient during startup, reducing operational costs.
- Limited Torque Availability: Initial torque may be insufficient for starting heavy loads.
- Automatic Transition: Switches from star to delta configuration automatically, optimizing torque as the motor gains speed.
- Moderate Cost: More expensive than direct-on-line starters but offers significant benefits in reducing mechanical and electrical stress.
- Suitable for Medium Loads: Ideal for conveyor systems that do not require full torque at startup.
Soft Starter
- Precise Torque Control: Allows for precise control over the starting torque, significantly reducing mechanical stress.
- Adjustable Start and Stop: Provides adjustable start and stop times, offering smooth ramp-up and ramp-down.
- Reduced Starting Current: Significantly reduces the starting current, minimizing electrical stress and potential for voltage drops.
- Energy Savings: Leads to energy savings due to efficient use of power during startup.
- Flexibility: Offers flexibility in adjusting settings to match specific conveyor load requirements.
- Higher Initial Cost: More expensive upfront cost compared to other starters but offers savings in maintenance and energy.
- Protection Features: Often includes additional protection features for the motor and conveyor system.
- Ideal for Heavy Loads: Best suited for applications requiring the conveyor to start under heavy loads with minimal stress.
Pulley Torque Ratio
- Influence on Torque Distribution: The ratio between the drive pulley and the driven pulley directly affects how torque is distributed across the conveyor system.
- Optimization of System Performance: Adjusting the pulley torque ratio can optimize the performance, allowing for smoother operation and reduced wear on the system.
- Customization for Load Requirements: By customizing the pulley ratio, systems can be tailored to specific load requirements, enhancing efficiency and reliability.
- Impact on Belt Speed: Changes in the pulley torque ratio can also impact the belt speed, which must be considered in the conveyor belt torque calculation to maintain desired operational speeds.
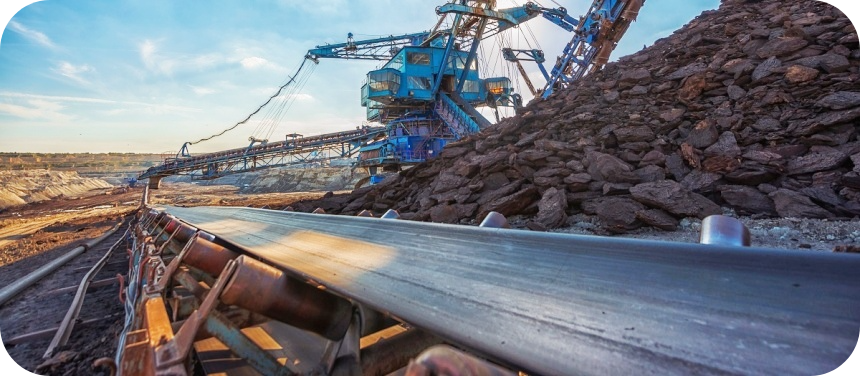
Each method and factor in conveyor belt torque calculation plays a crucial role in the design and operation of conveyor systems, influencing their efficiency, reliability, and longevity. Understanding these aspects allows for informed decisions in selecting the appropriate starting method and optimizing system design for specific application requirements.
Tools and Calculators for Conveyor Belt Torque Calculation
In the realm of conveyor belt design and maintenance, the precision of conveyor belt torque calculation is paramount. Fortunately, a variety of tools and calculators are available to assist engineers and technicians in accurately determining the required torque for their conveyor systems. Each tool offers unique advantages, catering to different aspects of conveyor belt torque calculation.
Conveyor Belt Torque Calculation PDFs
PDF resources provide comprehensive guides and formulas for conveyor belt torque calculation. These documents often include theoretical backgrounds, step-by-step calculation procedures, and examples of how to apply formulas in real-world scenarios. They serve as an invaluable resource for in-depth understanding, perfect for those looking to deepen their knowledge or solve specific, complex problems in conveyor belt design.
Metric Conveyor Belt Torque Calculation
For engineers and technicians working in metric units, specific calculators and formulas are tailored to metric measurements. These tools facilitate conveyor belt torque calculation by allowing inputs in meters, kilograms, and seconds, eliminating the need for unit conversion and reducing the potential for errors. This adaptation ensures accuracy and convenience for a global audience.
Conveyor Belt Torque Calculation Excel
Excel spreadsheets are a versatile tool for conveyor belt torque calculation. They allow for the input of various parameters and automatic computation of torque requirements. Users can customize these spreadsheets with specific formulas, enabling the analysis of different scenarios and the comparison of various design options. Excel’s ability to handle complex calculations and present data visually makes it an essential tool for detailed planning and optimization.
Conveyor Belt Torque Calculation Calculator
Online calculators offer a quick and user-friendly way to estimate conveyor belt torque calculation. These tools typically provide fields for entering key parameters such as belt speed, load weight, and pulley diameter, delivering instant torque estimates. While not as detailed as manual calculations, online calculators are excellent for preliminary assessments and quick checks.
5 Online Conveyor Belt Torque Calculation Calculators
Here are five online calculators that could assist in general torque calculations, along with their advantages, disadvantages, and URLs:
OMNI Calculator – Mechanic Calculators
Advantages:
- User-friendly interface with explanations for each parameter.
- Wide variety of mechanical calculators which could be adapted for torque calculations.
Disadvantages:
- May not have a dedicated conveyor belt torque calculator.
- Some calculations might require more parameters than the calculator asks for.
Engineering ToolBox – Rotating Masses Torque Calculator
Advantages:
- Provides basic torque calculations which could be adapted for conveyor belts.
- Offers a range of other related engineering calculators.
Disadvantages:
- The interface is quite basic and might not be very intuitive.
- Lacks specific conveyor belt torque calculation defaults.
Advantages:
- Simple calculator to estimate belt drive parameters which may include torque.
- Free and accessible without requiring personal information.
Disadvantages:
- Lacks detailed customization for specific conveyor scenarios.
- Interface is basic and may lack comprehensive tutorial support.
Calculator Edge – Mechanical Engineering Calculators
Advantages:
- Consists of various calculators that could be relevant to mechanical components and torque.
- Detailed inputs for thorough calculations.
Disadvantages:
- Complexity may be overwhelming for simple calculations.
- Might not have a calculator specifically for conveyor belt torque.
Blocobuster – Torque Calculator
Advantages:
- Provides a simple interface to calculate torque.
- Straightforward calculation output.
Disadvantages:
- Not dedicated to conveyor belts so it requires knowledge to adapt it properly.
- Limited parameters for more complex calculations.
Before using any of these calculators for conveyor belt calculations, it’s essential to understand the context and correct formulae to use. Torque calculations for conveyor belts can depend on several factors, including the motor type, pulley geometry, belt mass, friction coefficients, and other variables unique to the system in question. It is often recommended that you consult with a mechanical engineer or an expert in conveyor systems for precise calculations tailored to your specific application.
V-Belt Torque Calculator
Specialized calculators for V-belt systems focus on the unique requirements of V-belt driven conveyor systems. These calculators consider the specific geometry and friction characteristics of V-belts, providing more accurate torque calculations for these types of systems. They are an essential resource for engineers working with V-belt conveyor systems, ensuring optimal design and operation.
Each of these tools plays a critical role in ensuring the accurate conveyor belt torque calculation, facilitating the design, optimization, and maintenance of efficient, reliable conveyor systems. By leveraging these resources, professionals can ensure their conveyor systems are designed to meet the specific demands of their operations, maximizing productivity and minimizing downtime.
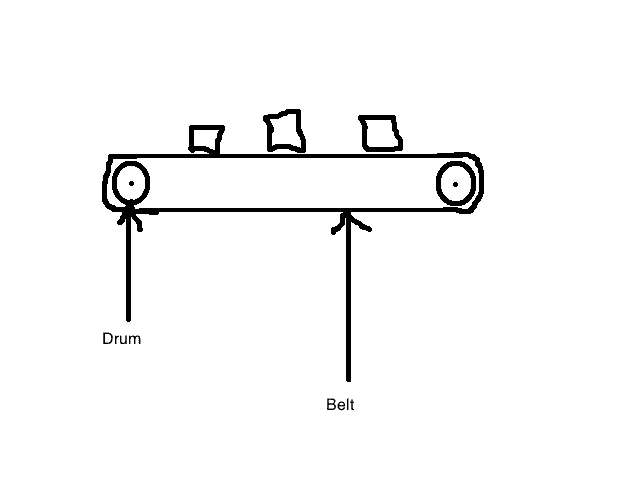
Practical Applications of Conveyor Belt Torque Calculation
The practical application of conveyor belt torque calculation is crucial for the design, operation, and maintenance of conveyor belt systems in various industries. Through real-world case studies and strategic adjustments, the importance of accurately calculating and applying torque settings is highlighted, ensuring optimal performance and longevity of conveyor systems.
Case Study: Enhancing Conveyor System Reliability through Accurate Torque Calculation
This case study highlights a significant challenge faced by a large-scale distribution center, plagued by frequent conveyor belt failures. The investigation into these failures revealed that the heart of the problem lay in the conveyor belt torque calculation. Here are the key points that outline the process of identifying and rectifying the issue, leading to improved system performance:
- Initial Problem Identification: The distribution center experienced recurrent conveyor belt failures, causing considerable downtime and operational inefficiencies. This situation prompted a thorough examination of the conveyor system to identify the underlying causes.
- Diagnosis of Incorrect Torque Calculation: A detailed analysis revealed that the core issue was an improper conveyor belt torque calculation. The miscalculation led to excessive stress on both the belt and the mechanical components of the conveyor system.
- Evaluation of System Parameters: Engineers conducted a comprehensive review of critical system parameters, including the load weight the conveyor was designed to handle, the operational speed of the belt (belt speed), the diameters of the drive and driven pulleys, and the coefficient of friction between the belt and pulleys.
- Identification of Mismatched Motor: The investigation uncovered that the motor in use was not suitable for the required operational demands. Its torque output did not align with the needs of the conveyor belt, especially considering the load and speed requirements.
- Optimization of Pulley Sizes: Alongside motor evaluation, the engineers also discovered that the sizes of the pulleys were not optimized for the system. This misalignment contributed to the undue stress and inefficiency of the conveyor belt operation.
- System Redesign and Component Upgrades: Armed with this analysis, the engineering team proceeded to redesign the conveyor system. This redesign included the installation of a motor that was more appropriately matched to the system’s torque requirements and the optimization of pulley sizes to ensure a more efficient transmission of power.
- Significant Reduction in Downtime: Following the implementation of these changes, the distribution center observed a remarkable 40% reduction in system downtime. This improvement was a direct result of alleviating the excessive mechanical stress that had been placed on the conveyor belt and its components.
- Enhanced Efficiency and Extended Lifespan: Beyond reducing downtime, the adjustments led to a substantial increase in the overall efficiency of the conveyor system. Moreover, the lifespan of the conveyor belt itself was significantly extended, demonstrating the profound impact of accurate conveyor belt torque calculation on the operational reliability and longevity of conveyor systems.
This case study underscores the critical importance of precise torque calculation in the design and maintenance of conveyor belt systems. By addressing the torque calculation inaccuracies, the distribution center not only solved the immediate issue of frequent failures but also achieved long-term operational improvements.
Adjusting Torque Settings for Optimal Performance and Longevity
- Regular Monitoring: Continuously monitor the conveyor system’s performance to identify any signs of overloading or underperformance, which could indicate incorrect torque settings.
- Load Analysis: Regularly analyze the load being transported on the conveyor belt. Changes in the type or weight of the material can necessitate adjustments in torque settings to maintain optimal performance.
- Speed Adjustments: Consider the operational speed of the conveyor belt. If the system frequently starts and stops or changes speed, adjusting the torque settings can help minimize wear and tear on the belt and mechanical components.
- Environmental Considerations: Account for environmental factors such as temperature and humidity, which can affect the material properties of the belt and, consequently, the friction coefficient. Adjust torque settings to compensate for these changes.
- Maintenance Checks: Incorporate torque setting adjustments as part of regular maintenance routines. Ensuring that all components are in good working condition can help maintain the desired torque levels.
- Use of Soft Starters: Implement soft starters to gradually apply torque, reducing mechanical stress during startup and stopping phases. This can extend the lifespan of the conveyor belt and associated mechanical components.
- Pulley Ratio Optimization: Review and adjust the pulley torque ratio as needed. A well-optimized pulley system can significantly impact the overall torque distribution and efficiency of the conveyor system.
- Training and Documentation: Ensure that operational and maintenance staff are well-trained in understanding and adjusting torque settings. Keeping detailed documentation of changes and their impacts can help refine future adjustments.
Through these practical applications and adjustments, the significance of conveyor belt torque calculation becomes evident. Accurately calculated and applied torque settings are fundamental to achieving a balance between operational efficiency and the longevity of conveyor belt systems, ultimately contributing to the success and reliability of industrial operations.
Advanced Topics in Conveyor Belt Torque Calculation
The intricacies of conveyor belt torque calculation extend into specialized areas, necessitating advanced tools and comprehensive guides to address specific application needs and challenges. These advanced topics not only deepen our understanding of conveyor system dynamics but also enhance our ability to design more efficient and reliable systems.
Pulley Torque Calculator and Timing Belt Torque Calculator
In the intricate world of conveyor systems, the conveyor belt torque calculation plays a pivotal role in ensuring the seamless operation of pulley and timing belt mechanisms. These specialized calculators are designed to address the unique challenges posed by different conveyor setups, providing precise torque values that are crucial for the system’s efficiency and longevity.
- Customization for Application Specifics: Tailored to accommodate the distinct operational parameters of pulleys and timing belts, ensuring accurate torque calculations for each specific application.
- Precision in Design: Essential for systems requiring exact synchronization, these calculators offer the precision needed for optimal design and operation.
- Material Consideration: They take into account the material properties of conveyor belts and pulleys, such as elasticity and friction, which significantly influence torque requirements.
- Environmental Factors: Adapt torque calculations to environmental conditions that may affect the performance of pulleys and timing belts.
- Operational Efficiency: By ensuring accurate torque calculation, these tools help optimize the efficiency of conveyor systems, preventing over or underestimation of torque needs.
- Maintenance Planning: Facilitate predictive maintenance by estimating the wear and tear on pulleys and belts based on torque exertion, aiding in scheduling maintenance activities.
- Safety Enhancements: By preventing overloading and slippage, these calculators contribute to the overall safety of conveyor operations.
- Cost Savings: Optimize motor and material selection to prevent over-engineering, leading to significant cost savings in the long run.
Load Torque Calculator
Understanding the impact of the load on torque requirements is crucial for designing a conveyor system that operates efficiently under various conditions. The Load Torque Calculator provides a comprehensive analysis of how different loads influence the system’s torque needs, ensuring the conveyor is adequately powered for its intended tasks.
- Comprehensive Load Analysis: Offers an in-depth look at how the type, weight, and distribution of loads affect torque requirements.
- Dynamic vs. Static Loads: Distinguishes between the effects of dynamic and static loads on both starting and running torque.
- Acceleration Impact: Considers how the acceleration rate of the conveyor belt influences the overall torque needed for smooth operation.
- Frictional Forces: Accounts for the friction between the load and the conveyor, which varies with material type and condition, impacting torque calculations.
- Load Stability: Evaluates the effects of load stability and distribution on torque needs to ensure even handling and prevent system strain.
- Operational Speed Considerations: Analyzes the relationship between the conveyor’s operational speed and its torque requirements, particularly in high-speed applications.
- Material Compatibility: Looks at how the compatibility of load materials with the conveyor belt affects torque needs.
- Efficiency Optimization: Aims to optimize system efficiency by accurately matching torque to load requirements, enhancing performance and energy use.
- Safety and Reliability: By ensuring the conveyor is neither underpowered nor overpowered for its load, these calculations enhance both safety and reliability.
Conveyor Motor Calculation PDF
Selecting the right motor based on the system’s torque needs is a critical step in designing an efficient conveyor system. The Conveyor Motor Calculation PDF serves as a detailed guide, offering step-by-step instructions and formulas for choosing a motor that matches the conveyor’s requirements, ensuring optimal performance and energy efficiency.
- Motor Type Selection: Guides through the process of selecting the appropriate motor type (AC, DC, servo, etc.) for the conveyor, based on torque needs.
- Power Rating Considerations: Explains how to match motor power ratings with the calculated torque requirements to ensure efficient operation.
- Speed-Torque Curve Analysis: Provides insights into using speed-torque curves for motor selection, ensuring the motor can handle the load at various speeds.
- Energy Efficiency: Focuses on selecting motors that offer optimal energy efficiency for the calculated torque, reducing operational costs.
- Environmental Adaptability: Offers advice on choosing motors suited to the conveyor’s operational environment, such as waterproof or dustproof options.
- Control System Compatibility: Discusses the importance of motor compatibility with the conveyor’s control system for precise torque management.
- Installation and Maintenance: Covers aspects of motor installation and maintenance influenced by torque needs, ensuring long-term system reliability.
- Cost-Benefit Analysis: Assists in performing a cost-benefit analysis, weighing the initial investment against long-term benefits in efficiency and maintenance.
- Future-Proofing: Advises on selecting motors that can accommodate future changes in torque requirements, ensuring the system’s adaptability.
Each of these advanced topics in conveyor belt torque calculation underscores the importance of detailed planning and precise calculations in the design and optimization of conveyor systems. By leveraging these specialized tools and comprehensive guides, professionals can ensure their conveyor systems are efficient, reliable, and capable of meeting the specific demands of their operational environment.
Maximize productivity with our customized conveyor belt solutions. Act now!
FAQs about Conveyor Belt Torque Calculation
Calculating torque for a belt conveyor involves understanding the mechanical components and the load it needs to move. The basic formula to calculate the torque ((T)) at the drive pulley of a belt conveyor is (T = F \times r), where (F) is the total tangential force exerted by the belt on the pulley and (r) is the radius of the pulley. The force ((F)) can be determined by the sum of the tension on the tight side of the belt ((T_1)) and the tension on the slack side of the belt ((T_2)), divided by the radius of the pulley. However, this is a simplified approach, and real-world calculations must consider factors such as the weight of the load, the belt speed, the coefficient of friction between the belt and the pulley, and any incline the conveyor may be operating on. Advanced calculations may also account for the dynamic behavior of the conveyor during starting and stopping phases, where the starting torque required can be significantly higher than the torque needed during continuous operation
The formula for the torque of a belt in a conveyor system is closely related to the formula for calculating torque in general but tailored to the specifics of a conveyor belt system. It is expressed as (T = F_b \times r), where (T) is the torque, (F_b) is the force exerted by the belt on the pulley, and (r) is the radius of the pulley. The force exerted by the belt ((F_b)) is influenced by the tension difference between the tight side and the slack side of the belt, which can be affected by the load weight, the belt’s material properties, and the operational speed of the conveyor. Accurately calculating this force requires a comprehensive understanding of the system’s mechanical properties and operational conditions.
The general formula for calculating torque ((T)) is (T = F \times r \times \sin(\theta)), where (F) is the force applied, (r) is the distance from the pivot point to the point where the force is applied, and (\theta) is the angle between the force vector and the lever arm. In many applications, including conveyor belts, the angle ((\theta)) is 90 degrees, which simplifies the formula to (T = F \times r) because (\sin(90^\circ) = 1). This formula is fundamental in understanding how different forces and distances from the pivot point affect the torque required for various applications, from simple mechanical systems to complex industrial machinery.
The starting torque required for a conveyor belt is the torque needed to overcome the inertia of the conveyor and its load at startup. This torque is typically higher than the torque required during continuous operation due to the initial resistance to motion. Calculating load torque involves considering W: Mass of load: kg,μ: Friction coefficient, D: Roller diameter, and F: External force, crucial for determining conveyor belt starting and continuous torque requirements.
Additionally, factors such as the acceleration rate desired and the presence of any inclines the conveyor must operate on will affect the starting torque. A precise calculation of starting torque is crucial for selecting an appropriate motor and drive system that can handle the conveyor’s requirements without excessive wear or energy consumption.
You will need to know a considerable number of values of the actual design and also the purpose. For example what weight will be carried as both units and also multiple units if required. Is the load dropped onto or placed onto the rollers. Is the conveyor stopped and started while carrying a load. How fast does it need to be. If connected with other conveyors is it the same speed as generally it must be at least as fast as the previous unit and slower than others after it. What drive is preferable. Chain or belt. What type of chain drive serpentine or parasite. What is the construction of the rollers and the material required such as plastic steel or stainless steel. How wide. How long. How high. What is the roller spacing. Are the rollers of special type smooth grip face spiral diabolo. Are they angle against a back fence. What is the power source.
Every element will have an effect in how well or even if the conveyor will work but you will also need to have a margin of extra power.
I have worked with conveyors which have broken daily and sometimes many times in a day. Old yes worn yes bad design yes. Cheap yes. But not in the long term.
There is an excellent but expensive book which describes every aspect of conveyor design called the conveyor design handbook. If you can get a copy you will find everything you could ever need to know and more.
To calculate the total mass or load of a conveyor for load torque calculation, you need to consider both the mass of the conveyor belt itself and the mass of the load it carries. Here’s a step-by-step method to determine the total mass:
Key Parameters:
Load Mass (𝑚m): The mass of the load being transported on the conveyor, in kilograms (kg).
Belt Mass per Unit Length (𝑚
𝑏mb): The mass of the conveyor belt per meter length, in kilograms per meter (kg/m).
Length of Conveyor (𝐿L): The length of the conveyor belt, in meters (m).
Last Updated on August 20, 2024 by Jordan Smith
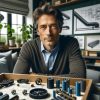
Jordan Smith, a seasoned professional with over 20 years of experience in the conveyor system industry. Jordan’s expertise lies in providing comprehensive solutions for conveyor rollers, belts, and accessories, catering to a wide range of industrial needs. From initial design and configuration to installation and meticulous troubleshooting, Jordan is adept at handling all aspects of conveyor system management. Whether you’re looking to upgrade your production line with efficient conveyor belts, require custom conveyor rollers for specific operations, or need expert advice on selecting the right conveyor accessories for your facility, Jordan is your reliable consultant. For any inquiries or assistance with conveyor system optimization, Jordan is available to share his wealth of knowledge and experience. Feel free to reach out at any time for professional guidance on all matters related to conveyor rollers, belts, and accessories.