Guide to 3 Conveyor Belt Tracking Basics to Follow
In the realm of industrial operations, the efficiency and longevity of conveyor systems hinge significantly on one critical aspect: conveyor belt tracking basics. This foundational element ensures that conveyor belts run smoothly and align correctly along the path of the system, which is vital for maintaining operational efficiency and minimizing downtime. Despite its importance, there are common misconceptions surrounding conveyor belt tracking, with many underestimating its complexity and the precision required to achieve optimal tracking. Some believe that once a conveyor belt is installed, it will automatically align and track properly without further intervention. However, this overlooks the nuanced adjustments and regular maintenance necessary to counteract the natural wear, environmental factors, and load variations that can lead to misalignment. Understanding the basics of conveyor belt tracking is essential for anyone involved in the design, operation, or maintenance of industrial conveyor systems,Master conveyor belt tracking basics with essential tips on adjusting idlers, pulleys, and loading conditions for optimal performance. Setting the stage for more detailed exploration of techniques and solutions to keep these belts on track.
What are Conveyor Belt Tracking Basics
Conveyor belt tracking basics are essential for the smooth operation of a conveyor system. This concept involves aligning and controlling the belt so it runs properly on the rollers and pulleys. Proper tracking is crucial for preventing belt misalignment, material spillage, and potential equipment breakdowns, which can lead to costly operational downtimes. Below, we explore the significance of mastering conveyor belt tracking basics and the fundamental principles that guide effective belt tracking strategies.
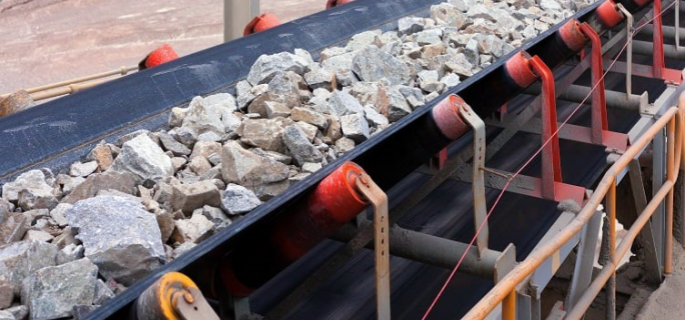
Significance of Conveyor Belt Tracking
Understanding the importance of conveyor belt tracking is key to maintaining efficient conveyor system operations. Here are several reasons why conveyor belt tracking basics are critical:
- Prevents Belt Misalignment: Misalignment can lead to uneven wear and premature belt failure, necessitating costly replacements.
- Reduces Downtime: By minimizing stoppages, properly tracked belts keep production lines running smoothly, enhancing operational efficiency.
- Enhances Safety: Proper tracking decreases the risk of accidents caused by spillage or entanglement with misaligned conveyor parts.
- Improves Material Handling: A well-tracked belt ensures efficient material transport along the conveyor path, preventing spillage or buildup.
- Increases Energy Efficiency: Efficiently running belts require less power, contributing to lower operational costs.
- Protects Conveyor Components: Correct tracking reduces stress on rollers, frames, and other conveyor parts, preventing damage.
- Maintains Product Quality: Gentle and stable handling of products on the conveyor is ensured, avoiding damage.
- Facilitates Predictable Maintenance: Consistent tracking allows for more predictable wear patterns, making maintenance planning easier.
- Enhances Overall System Reliability: A well-maintained tracking system contributes to the overall reliability and longevity of the conveyor system.
Basic Principles Behind Conveyor Belt Tracking
To achieve and maintain proper conveyor belt tracking theory, several foundational principles must be understood and applied:
- Alignment of Conveyor Structure: The basis of effective belt tracking lies in ensuring that the conveyor frame and rollers are precisely aligned to provide a stable path for the belt.
- Correct Roller and Pulley Installation: Rollers and pulleys must be installed squarely in relation to the conveyor frame to assist in maintaining the belt’s path.
- Proper Belt Tensioning: Applying the right amount of tension to the belt is crucial to prevent slippage and misalignment, while avoiding excessive wear.
- Use of Tracking Devices: Implementing devices like tracking idlers and edge guides can help in steering the belt back to its correct path when deviations occur.
- Regular Inspection and Maintenance: Conducting routine inspections allows for the early identification and correction of tracking issues, preventing larger problems.
- Understanding Belt Behavior: Recognizing how different types of belts react under various conditions can aid in selecting the right tracking adjustments.
- Adjustments Must Be Gradual: When adjusting belt tracking, making small, incremental changes is more effective than making large, sudden adjustments.
- Training of Personnel: Ensuring that operators and maintenance staff are knowledgeable about conveyor belt tracking basics is vital for timely issue resolution.
- Consultation with Experts: Seeking advice from conveyor belt manufacturers or specialists can provide valuable insights into solving complex tracking challenges.For example, Gram Conveyor, Dunlop Conveyor Belting, Fenner Dunlop, Continental AG, and Habasit.
- Holistic Approach: Effective belt tracking considers the entire conveyor system, recognizing that each component can influence the belt’s alignment.
By understanding and implementing these conveyor belt tracking basics, facilities can ensure their conveyor systems operate efficiently, safely, and cost-effectively, minimizing downtime and maximizing productivity.
Key Principles for Effective Belt Tracking: Conveyor Belt Tracking Basics
Effective belt tracking is crucial for the smooth operation and longevity of conveyor systems. Understanding the conveyor belt tracking basics is essential for preventing belt misalignment, which can lead to belt damage, decreased efficiency, and increased maintenance costs. Here, we delve into the key principles that underpin effective belt tracking.
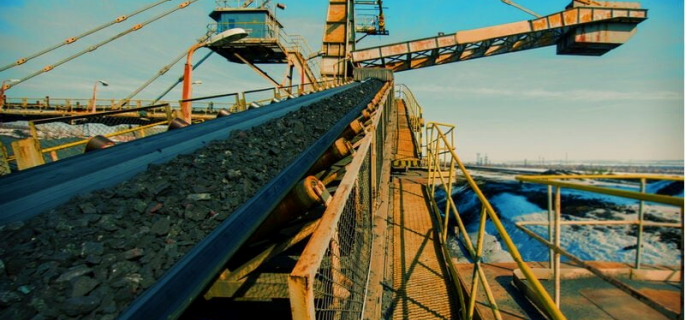
The Fundamental Rule of Belt Tracking
The primary rule of belt tracking is succinctly captured by the principle: “The belt moves toward the end of the roll it contacts first.” This fundamental concept underlies the following points:
- Consistent Contact: Ensuring the belt consistently contacts the same part of the rollers and pulleys is crucial for stable movement.
- Roller Positioning: Rollers should be positioned to guide the belt towards the center, not away from it.
- Belt Tension: Proper tensioning of the belt is essential; too much or too little tension can cause the belt to veer off course.
- Symmetrical Loading: Material should be loaded onto the belt symmetrically to prevent uneven weight distribution, which can affect tracking.
- Regular Inspections: Frequent inspections can identify and correct minor issues before they lead to misalignment.
- Adjustment Capabilities: Conveyor systems should allow for easy adjustments to rollers and pulleys for quick corrections.
- Understanding Belt Behavior: Recognizing how different belts behave under various conditions can aid in troubleshooting tracking issues.
- Training Personnel: Operators should be trained on the basics of belt tracking to identify and correct issues promptly.
- Preventive Maintenance: Regular maintenance schedules can prevent the majority of belt tracking problems before they occur.
Conveyor Structure Alignment
The alignment of the conveyor structure is paramount in ensuring effective belt tracking. Here are eight points highlighting its importance:
- Foundation for Tracking: A true and level conveyor structure provides the foundation for proper belt tracking.
- Minimizes Wear: Correct alignment reduces wear on the belt, rollers, and the structure itself.
- Enhances Efficiency: A well-aligned conveyor operates more efficiently, with less energy consumption and reduced risk of downtime.
- Improves Safety: Proper alignment decreases the risk of belt-related safety incidents.
- Facilitates Uniform Tension: Ensures that belt tension is uniformly distributed along the conveyor’s length.
- Prevents Material Spillage: A misaligned conveyor can lead to material spillage, creating hazards and increasing cleanup costs.
- Longevity of Equipment: Extends the life of the conveyor belt and associated components by reducing unnecessary stress.
- Simplifies Maintenance: A correctly aligned conveyor is easier to maintain and adjust, saving time and resources.
Proper Pulley and Roller Alignment
Ensuring that all pulleys and rollers are square with the frame and parallel to each other is critical for maintaining belt alignment. Here are ten guidelines for proper alignment:
- Use Precision Tools: Employ laser alignment tools or other precision instruments to check alignment.
- Regular Checks: Perform alignment checks regularly and after any maintenance that could affect the conveyor’s geometry.
- Adjust as Needed: Make incremental adjustments and monitor the belt’s response, adjusting further as required.
- Parallel Rollers: Ensure all rollers are parallel to each other and perpendicular to the conveyor’s direction.
- Square Pulleys: Pulleys should be square with the conveyor frame to prevent the belt from drifting.
- Even Tension: Pulleys and rollers should be adjusted to maintain even tension across the belt width.
- Monitor Wear: Check for wear on pulleys and rollers, as this can affect alignment.
- Replace Damaged Components: Replace any damaged or worn components that cannot be properly aligned.
- Training Idlers: Consider using training idlers that automatically adjust to maintain belt alignment.
- Documentation: Keep records of adjustments and maintenance activities to track the conveyor’s performance over time.
Understanding and applying these conveyor belt tracking basics are essential for optimizing the performance and durability of conveyor systems. Regular attention to belt tracking principles can significantly reduce maintenance issues and ensure smooth, efficient operation.
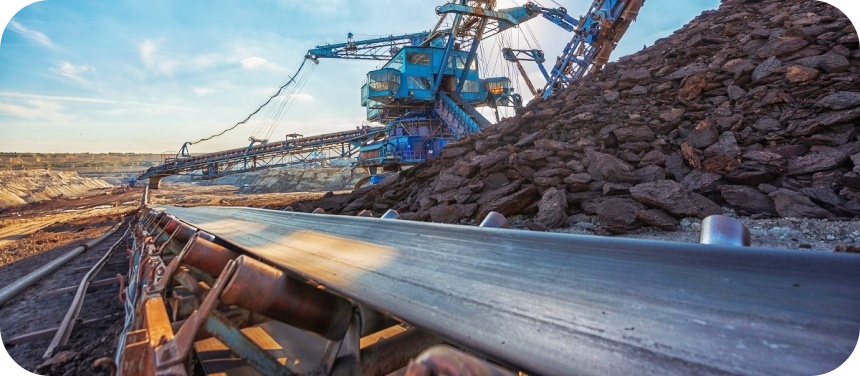
Conveyor Belt Tracking Techniques: Mastering Conveyor Belt Tracking Basics
Ensuring your conveyor belt is properly tracked is crucial for the efficiency, safety, and longevity of your conveyor system. Misalignment can lead to several problems, including belt damage, inefficient operation, and increased maintenance costs. Here, we delve into the conveyor belt tracking basics, focusing on effective techniques to maintain optimal belt performance.
Adjusting Belt Tension
Correct belt tension is vital for maintaining efficient operation and extending the life of the conveyor belt. Too little tension can lead to belt slippage, while too much tension may cause excessive wear on the belt and conveyor components.
- Routine checks are essential for identifying and correcting tension discrepancies.
- Adhering to manufacturer’s guidelines ensures that tension adjustments meet the specific requirements of the conveyor system.
- Conduct Routine Checks: Regular inspections are crucial to detect early signs of improper tension, preventing potential slippage or excessive wear.
- Utilize a Tension Meter: Employing a tension meter for measurements ensures adjustments are based on accurate data, facilitating precise tensioning.
- Follow Manufacturer’s Guidelines: Adherence to the manufacturer’s specifications is essential, as each conveyor system has unique tension requirements based on belt type, length, and operational load.
- Adjust Take-Up Pulleys: Incremental adjustments of take-up pulleys allow for fine-tuning of belt tension, ensuring it’s neither too tight nor too loose.
- Maintain Uniform Tension: Achieving even tension across the belt’s width is critical for uniform wear and consistent tracking, enhancing the belt’s lifespan.
- Monitor Belt Response: After adjustments, closely observe the belt’s operation. Effective tracking and smooth operation indicate proper tension.
- Be Prepared for Multiple Adjustments: Finding the perfect tension setting may require several adjustments, especially after the belt has settled from initial installation or maintenance activities.
- Check for Environmental Factors: Temperature and humidity can affect belt tension. Adjustments might be needed to compensate for changes in environmental conditions.
- Inspect Belt and Pulley Conditions: Worn belts or pulleys can affect tension. Regularly inspect these components for wear and replace them as necessary to maintain proper tension.
- Document Adjustments and Observations: Keeping records of tension adjustments and their effects on conveyor operation can help in establishing best practices and troubleshooting future issues.
- Train Maintenance Staff: Ensuring that all maintenance personnel are trained on the correct procedures for adjusting belt tension and recognizing signs of improper tension can help maintain optimal conveyor performance.
- Consider Automated Tensioning Systems: For high-usage or critical conveyor systems, investing in automated tensioning systems can ensure consistent optimal tension, reducing the need for manual adjustments and increasing system reliability.
Maintaining Cleanliness
Maintaining the cleanliness of a conveyor system is crucial for optimal performance and longevity. Dirt, debris, and material buildup not only pose risks for belt misalignment but can also significantly affect the efficiency and safety of conveyor operations. Here are expanded points on maintaining cleanliness to prevent tracking issues and ensure efficient conveyor operation:
- Implementing a routine cleaning schedule is essential for the consistent removal of debris and prevention of material buildup, which can lead to belt misalignment and efficiency losses.
- Using appropriate cleaning tools ensures that the conveyor belt and components are cleaned effectively without causing damage. Soft brushes and non-abrasive cleaning agents are recommended to protect the belt’s surface.
- Immediate spill management is critical for preventing sticky residues that can adhere to the belt and rollers, causing misalignment and tracking problems.
- Conducting regular inspections for material buildup on rollers, pulleys, and other conveyor components helps identify and address potential issues before they lead to significant problems.
- Ensuring proper drainage is vital to prevent water accumulation on the conveyor belt, which can lead to slippage and affect the belt’s tracking.
- Thoroughly clean transfer points and impact load zone belt support areas to remove any accumulated material that can spill over and contribute to debris buildup along the conveyor path.
- Utilizing belt scrapers at strategic locations to remove material sticking to the belt surface, especially at the discharge end, to maintain belt cleanliness and efficiency.
- Implementing dust control measures, such as dust suppression systems or enclosures, especially in operations involving powdery materials, to minimize airborne particles that can settle on the conveyor and affect its operation.
- Training personnel on cleanliness best practices ensures that all team members understand the importance of maintaining a clean conveyor system and are equipped to take appropriate actions when needed.
- Scheduling downtime for deep cleaning allows for comprehensive cleaning and maintenance activities that cannot be performed during regular operations, ensuring the conveyor system remains in optimal condition.
Conveyor systems can operate more efficiently, with reduced risk of downtime and extended service life. These practices not only contribute to the conveyor’s operational efficiency but also to the safety and cleanliness of the overall work environment.
Training the Conveyor Belt
Training, or aligning, the conveyor belt is essential for central tracking along the conveyor system. Proper alignment reduces wear and extends the belt’s lifespan.
- Correct installation of the conveyor belt is the first step in ensuring proper tracking.
- The conveyor frame and idlers should be checked for level to prevent misalignment.
- Adjusting idlers opposite the direction of drift can correct misalignment.
- Observing belt direction during operation helps in making accurate adjustments.
- Pulleys and rollers should be squared to the belt’s path for optimal tracking.
- Testing and readjusting after initial adjustments ensures the belt tracks correctly.
- Monitoring belt edges for wear or damage can indicate ongoing tracking issues.
- The training process may need to be repeated after maintenance or changes in load conditions.
- Ensure that all personnel involved in the operation and maintenance of the conveyor system are adequately trained in tracking techniques and troubleshooting.
- Be aware of environmental factors such as temperature and humidity, which can affect belt tracking. Make adjustments as needed to accommodate these conditions.
- Use high-quality belts and components to ensure longevity and reliable performance.
By focusing on these conveyor belt tracking basics, you can ensure the efficient and safe operation of your conveyor system, minimizing downtime and maintenance costs. Regular maintenance and adjustments are key to achieving and maintaining optimal belt tracking.
Factors Affecting the Training of a Conveyor Belt:Conveyor Belt Tracking Basics
- Belt Tension:
Correct Tension: Proper tension is crucial; too much causes excessive wear, too little leads to slippage and misalignment.
Even Tension: Uneven tension across the belt’s width can cause it to drift to one side. - Alignment of Conveyor Components:
Frame Squareness: The conveyor frame must be square and level to avoid tracking issues.
Pulley and Roller Alignment: Pulleys and rollers need to be parallel and square with the conveyor frame. - Belt Condition:
Wear and Damage: A belt that is worn or damaged will not track properly, requiring regular inspections and maintenance.
Splicing: Poor splicing techniques can lead to belt misalignment; quality splicing is essential. - Load Distribution:
Center Loading: Material should be loaded in the center of the belt to avoid uneven distribution and drifting.
Consistent Loading: Sudden changes in load can impact belt tracking, so consistent loading conditions are important. - Environmental Factors:
Temperature: Extreme temperatures can cause the belt material to expand or contract, affecting tracking.
Humidity and Moisture: These factors can cause slippage or affect the belt’s material properties. - Belt Type and Quality:
Material and Construction: Using a belt suitable for the specific application and of high quality improves tracking performance.
Compatibility: Ensure the belt is compatible with the conveyor system components. - Cleanliness:
Debris and Buildup: Material buildup on the belt or components can cause tracking issues, necessitating regular cleaning.
Belt Cleaners: Installing belt cleaners helps maintain a clean belt surface. - Use of Tracking Devices:
Training Idlers: Installing training idlers helps keep the belt centered.
Adjustable Rollers: These allow for fine-tuning of the belt alignment. - System Design:
Conveyor Length and Width: The design of the conveyor system, including its length and width, can influence belt tracking. - Regular Maintenance:
Inspection and Adjustments: Regularly inspecting the belt and making necessary adjustments can prevent tracking issues.
Preventive Maintenance Schedule: Following a preventive maintenance schedule helps address potential problems before they become significant.
By addressing these factors, you can enhance the tracking of your conveyor belt, ensuring efficient and reliable operation. Regular monitoring and proactive maintenance are essential for maintaining proper belt alignment and performance.
Troubleshooting Common Tracking Issues: Mastering Conveyor Belt Tracking Basics
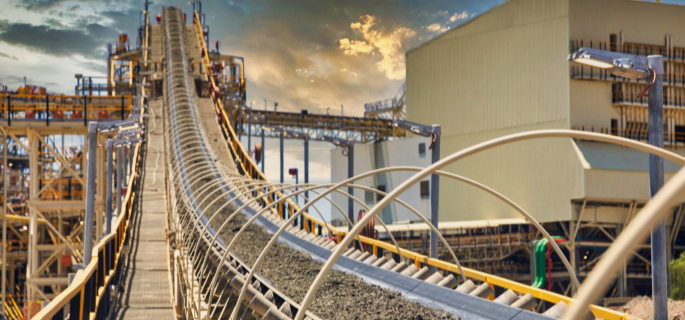
Navigating the complexities of conveyor belt tracking basics is essential for maintaining the operational efficiency and longevity of conveyor systems. Misalignment issues, such as the belt running to one side or exhibiting erratic behavior, can significantly impact the system’s performance. Here, we delve deeper into these common tracking issues, providing detailed causes, corrections, and solutions.
Belt Running to One Side
When a conveyor belt consistently runs to one side at a specific point or along the entire length of the conveyor, it’s crucial to identify the cause and implement the appropriate correction. Here are nine points addressing the causes and corrections:
- Check for Uneven Loading: Ensure materials are evenly distributed across the belt width to prevent imbalance.
- Inspect Idler Alignment: Misaligned idlers can cause the belt to track off to one side. Realign idlers perpendicular to the belt path.
- Examine Frame Squareness: A conveyor frame that’s not square can lead to belt misalignment. Adjust the frame to ensure it’s square and level.
- Adjust Belt Tension: Incorrect belt tension is a common cause of misalignment. Adjust tension evenly across the belt to prevent it from running to one side.
- Clean Build-Up on Rollers: Material build-up on rollers can cause the belt to mistrack. Clean rollers regularly to prevent accumulation.
- Evaluate Pulley Alignment: Ensure drive and tail pulleys are properly aligned with the conveyor frame to facilitate straight belt travel.
- Monitor Wear Patterns: Excessive wear on one side of the belt can indicate tracking issues. Inspect and replace the belt if necessary.
- Implement Training Idlers: Training idlers can help correct minor tracking issues by gently guiding the belt back to the center.
- Review Conveyor Design: Sometimes, the conveyor design may contribute to tracking problems. Consult with a manufacturer for potential design modifications.
Erratic Belt Behavior
Dealing with a conveyor belt that does not follow a consistent pattern due to stiffness or improper loading requires a systematic approach to identify and solve the underlying issues. Here are eight solutions:
- Ensure Proper Belt Installation: Incorrectly installed belts can lead to erratic behavior. Double-check installation against manufacturer guidelines.
- Balance Conveyor Loading: Uneven loading can cause the belt to behave erratically. Ensure materials are centrally loaded.
- Inspect for Belt Damage: Damaged or worn areas on the belt can affect tracking. Inspect and replace the belt as needed.
- Lubricate Conveyor Components: Proper lubrication of rollers and bearings can reduce stiffness and improve belt movement.
- Adjust Conveyor Speed: Sometimes, adjusting the speed of the conveyor can mitigate erratic belt behavior.
- Use Belt Dressings: Belt dressings can improve traction between the belt and pulleys, reducing slippage.
- Regularly Clean the Conveyor: Keeping the conveyor clean helps prevent debris from affecting belt movement.
- Consult with Specialists: Persistent erratic behavior may require expert analysis. Consulting with conveyor specialists can provide targeted solutions.
Mastering conveyor belt tracking basics and addressing common tracking issues effectively can significantly enhance the performance and reliability of your conveyor system. Regular maintenance, combined with a keen understanding of these fundamentals, ensures smooth operation and extends the lifespan of your conveyor belt.
Advanced Conveyor Belt Tracking Solutions: Enhancing Conveyor Belt Tracking Basics
In the pursuit of operational excellence in material handling, delving into advanced conveyor belt tracking solutions is a natural progression from mastering conveyor belt tracking basics. These sophisticated systems are designed to automate the alignment process, significantly reducing manual intervention and enhancing the efficiency and longevity of conveyor systems. Below, we explore two pivotal advancements: the use of tracking rollers and automatic conveyor belt tracking systems.
Use of Tracking Rollers
Tracking rollers represent a significant advancement in conveyor belt tracking technology. These specialized rollers are engineered to automatically adjust the conveyor belt’s path, ensuring it remains centered along the conveyor’s length. Here’s how tracking rollers elevate conveyor belt tracking basics through automation:
- Self-Adjusting Capability: Tracking rollers pivot in response to the belt’s lateral movement, automatically guiding the belt back to its central path.
- Strategic Installation: Positioned at critical points along the conveyor frame, these rollers are crucial for detecting and correcting misalignments early.
- Versatility: Suitable for a wide range of conveyor types and sizes, tracking rollers can be implemented in both new designs and existing systems.
- Reduced Wear and Tear: By maintaining proper alignment, tracking rollers minimize the wear on the belt and conveyor infrastructure, extending their operational life.
- Minimal Maintenance Needs: The self-regulating nature of tracking rollers means they require less maintenance, contributing to lower operational costs.
- Enhanced Operational Safety: Automating belt alignment reduces the need for manual adjustments, enhancing safety by minimizing human interaction with moving parts.
- Improved Efficiency: Consistent belt alignment ensures materials are transported efficiently, reducing spillage and enhancing productivity.
- Ease of Installation: Tracking rollers can be easily installed and adjusted, making them a practical solution for improving conveyor belt tracking.
Automatic Conveyor Belt Tracking Systems
Automatic conveyor belt tracking systems represent the forefront of conveyor belt alignment technology. Utilizing an array of sensors and control mechanisms, these systems offer real-time adjustments to maintain optimal belt alignment. The table below provides an overview of their key features and benefits:
Incorporating advanced conveyor belt tracking solutions into your material handling operations can significantly enhance the reliability and efficiency of your conveyor systems. By building on conveyor belt tracking basics, these innovative solutions automate the alignment process, ensuring smooth, efficient, and safe conveyor operations.
Conveyor Belt Tracking Diagrams and Guides: Implementing Conveyor Belt Tracking Basics
Understanding and implementing conveyor belt tracking basics are crucial for the efficient operation of conveyor systems. Conveyor belt tracking diagrams and guides serve as invaluable tools for maintenance personnel and engineers, offering a visual and technical roadmap to correct belt alignment and prevent common issues associated with misalignment. Here’s how these resources can be pivotal in mastering conveyor belt tracking basics:
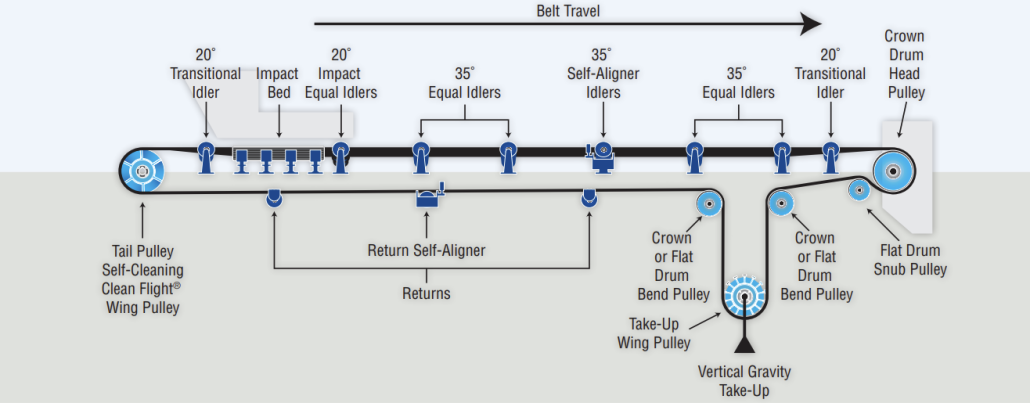
- Visual Reference: Diagrams provide a clear visual reference for the correct path of the conveyor belt along the system. This aids in identifying deviations from the ideal alignment.
- Step-by-Step Guidance: Guides often include step-by-step instructions for adjusting conveyor belts, making it easier for personnel to follow and implement the necessary changes.
- Identification of Components: Detailed diagrams help in identifying key components involved in belt tracking, such as idlers, pulleys, and tensioning devices, and their proper positioning.
- Troubleshooting Assistance: Many guides include troubleshooting sections that address common tracking issues, offering solutions based on the symptoms observed.
- Preventive Maintenance Tips: Guides can offer preventive maintenance tips to keep the conveyor belt properly aligned, reducing the need for frequent adjustments and prolonging the belt’s lifespan.
- Training Tool: Diagrams and guides serve as excellent training materials for new staff, helping them understand the mechanics of conveyor belt tracking and the importance of proper alignment.
- Safety Information: These resources often include safety information, highlighting the risks associated with improper conveyor belt tracking and how to mitigate them.
- Customization Strategies: Some guides provide insights into customizing tracking strategies based on specific conveyor designs or operational requirements, ensuring a tailored approach to belt alignment.
- Performance Optimization: By following the strategies outlined in diagrams and guides, conveyor systems can operate at optimal efficiency, with reduced wear on components and decreased downtime.
- Regulatory Compliance: Diagrams and guides can also help ensure that conveyor belt tracking practices comply with industry standards and regulations, maintaining operational integrity and safety.
Conveyor belt tracking diagrams and guides are essential resources for mastering conveyor belt tracking basics. They not only facilitate a deeper understanding of how to achieve and maintain proper belt alignment but also enhance the overall reliability and safety of conveyor systems. By utilizing these tools, maintenance teams can implement effective belt tracking strategies, ensuring smooth and efficient conveyor operations.
Optimize your production with our expert conveyor belt solutions.
FAQs about Conveyor Belt Tracking Basics
The best way to track a conveyor belt involves a combination of routine maintenance, precise adjustments, and understanding the system’s mechanics. Initially, ensure that the conveyor structure is level and the belt is tensioned correctly, as uneven tension can cause the belt to track off-center. Regularly inspect the belt for wear and damage, and replace parts as necessary. Use tracking rollers and adjust them carefully to guide the belt back to the center. It’s also crucial to keep the belt and all conveyor components clean, as debris can affect tracking. Implementing a systematic approach to monitoring and adjusting the conveyor belt as part of regular maintenance will ensure optimal tracking and extend the lifespan of the belt and conveyor system. This method combines preventive maintenance with responsive adjustments, balancing proactive care with the ability to react to issues as they arise.
Conveyor tracking works by ensuring the belt moves in a straight line along the path intended by the conveyor’s design. This is achieved through a combination of mechanical adjustments, component alignment, and sometimes automated systems for real-time tracking. Mechanical adjustments can include setting the correct tension on the belt, aligning rollers and pulleys so they are perpendicular to the belt’s direction, and using tracking rollers that pivot to guide the belt back to the center. Automated systems may use sensors to detect the belt’s position and make adjustments using actuators. The goal of conveyor tracking is to prevent the belt from drifting off course, which can lead to uneven wear, potential damage to the belt or the conveyed materials, and operational inefficiencies.
The fundamental belt tracking rule is that the belt will move towards the side of the roller or pulley it contacts first. This principle is critical for understanding how to adjust the tracking of a conveyor belt effectively. If the belt is running off to one side, it’s likely making more contact with rollers or pulleys on that side. By adjusting the angle or position of these rollers or pulleys, you can influence the direction the belt moves. For example, if the belt drifts to the right, the rollers on that side may need to be adjusted to guide the belt back towards the center. This rule underscores the importance of precise alignment of all conveyor components to ensure balanced contact and prevent misalignment.
Adjusting conveyor belt alignment is crucial for efficient operation and preventing damage. To start, inspect the conveyor for any obstructions, debris, or worn components that could be affecting alignment. Observe the belt movement to identify the problem area and check for uneven tension. Begin adjustments by loosening and moving the idler rollers on the side where the belt is drifting, then tighten them once adjusted. If necessary, adjust the tail or head pulleys by moving them slightly towards the side where the belt is running off. Fine-tune the belt tension, ensuring it is equal across both sides, and use a belt tension meter if available. After adjustments, run the conveyor and monitor the belt to ensure it tracks properly. Finally, perform a thorough inspection and include regular belt alignment checks in your maintenance routine to prevent future issues.
Conveyor belts are controlled through a combination of mechanical components, sensors, and automation systems. Key mechanical components include motors, drives, pulleys, and rollers. Electric motors, managed by variable frequency drives (VFDs), provide power and precise speed control. Pulleys and rollers guide and support the belt, while tensioning devices maintain proper belt tension to ensure smooth operation.Sensors are critical for providing real-time feedback. Proximity sensors detect the presence of items on the belt, while photoelectric sensors use light beams to monitor object positions and count items. Limit switches indicate the position of objects or the end of travel for moving parts. Load cells measure the weight of items to prevent overloading, and speed sensors monitor belt speed to ensure it operates within the desired range.
Last Updated on August 19, 2024 by Jordan Smith
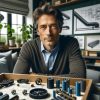
Jordan Smith, a seasoned professional with over 20 years of experience in the conveyor system industry. Jordan’s expertise lies in providing comprehensive solutions for conveyor rollers, belts, and accessories, catering to a wide range of industrial needs. From initial design and configuration to installation and meticulous troubleshooting, Jordan is adept at handling all aspects of conveyor system management. Whether you’re looking to upgrade your production line with efficient conveyor belts, require custom conveyor rollers for specific operations, or need expert advice on selecting the right conveyor accessories for your facility, Jordan is your reliable consultant. For any inquiries or assistance with conveyor system optimization, Jordan is available to share his wealth of knowledge and experience. Feel free to reach out at any time for professional guidance on all matters related to conveyor rollers, belts, and accessories.