Revolutionising Conveyor Belt Tracking Devices and Alignment Systems
In the realm of material handling and automation, the efficiency and longevity of a conveyor system significantly hinge on the precision of conveyor belt alignment. This is where the role of conveyor belt tracking devices becomes paramount across various industries, from manufacturing to logistics. These devices are crucial for correcting and maintaining the belt’s alignment, thereby preventing common issues such as product spillage, belt wear, and extensive damage to the conveyor infrastructure. Misalignment, even to a minor degree, can lead to operational disruptions, increased maintenance costs, and potential safety hazards. Thus, implementing effective conveyor belt tracking devices is not just a matter of enhancing operational efficiency but also of safeguarding the integrity of the conveyor system and ensuring workplace safety.
The Basics of Conveyor Belt Tracking Devices
Conveyor belt tracking theory is a critical component in the efficient operation of conveyor systems, directly impacting their performance and longevity. It involves the continuous alignment of the conveyor belt to prevent it from drifting off its intended path. This alignment is crucial not only for the safety of the operations but also for maintaining the quality of the materials being transported. The introduction of conveyor belt tracking devices has revolutionized the way conveyor systems are managed, offering a proactive solution to a problem that can cause significant operational disruptions. Below, we explore the essence of conveyor belt tracking, its paramount importance in conveyor system operations, and the key factors that influence its effectiveness.
Definition and Significance
Conveyor belt tracking devices ensure the belt moves in a straight line and stays aligned with the conveyor’s intended path. This alignment is not just about preventing the belt from slipping off the conveyor’s rollers; it’s about ensuring the smooth, efficient, and safe operation of the conveyor system. Here are eight points that highlight the significance of conveyor belt tracking system operations:
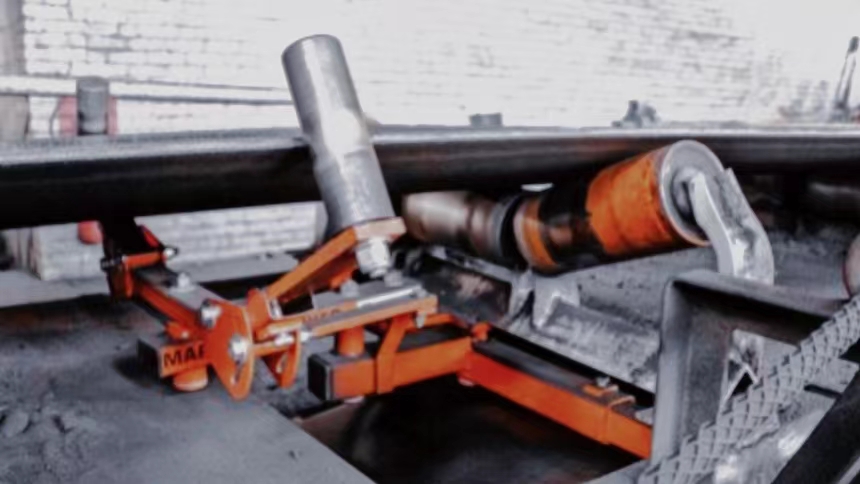
- Prevents Belt Misalignment: Conveyor belt tracking devices are essential for preventing the belt from slipping off the rollers, which can cause significant damage to both the belt and the conveyor structure.
- Reduces Maintenance Costs: Proper tracking minimizes the need for frequent maintenance and replacements, thereby reducing operational costs.
- Enhances Safety: By ensuring that the belt operates within its intended path, these devices significantly reduce the risk of accidents and injuries.
- Improves Productivity: A well-aligned conveyor belt ensures that materials are transported efficiently, without interruption, enhancing overall productivity.
- Protects Conveyor Belt: Correct tracking reduces wear and tear on the belt, extending its lifespan.
- Prevents Product Loss: By keeping the belt aligned, tracking devices help prevent spillage of materials being conveyed.
- Ensures Quality Control: Proper alignment means products are less likely to be damaged during transport, maintaining quality control.
- Optimizes Operational Efficiency: Conveyor belt tracking devices contribute to the smooth operation of the entire system, preventing downtime and ensuring continuous flow of operations.
Factors Affecting Conveyor Belt Tracking
Several factors can influence the tracking of a conveyor belt, from mechanical adjustments to environmental conditions. Understanding these factors is crucial for maintaining optimal performance of conveyor belt tracking devices:
- Belt Tension: Incorrect tension can cause the belt to wander off its intended path. Proper tensioning is crucial for effective tracking.
- Roller Alignment: Misaligned rollers can lead to belt drift. Ensuring that all rollers are properly aligned is essential for maintaining the belt’s path.
- Material Build-up: Accumulation of debris on rollers or the belt itself can affect tracking. Regular cleaning is necessary to prevent misalignment.
- Belt Splicing Accuracy: Improperly spliced belts can cause uneven tension and misalignment. Precision in belt splicing is critical for tracking.
- Wear and Tear: Over time, wear on the belt and conveyor components can affect tracking. Regular inspections and maintenance are required to address wear-related issues.
- Side Loading: Introducing materials to the belt from the side can push the belt off track. Proper loading techniques must be employed to prevent this.
- Environmental Factors: Conditions such as humidity, temperature, and exposure to chemicals can affect the belt’s material and, subsequently, its tracking.
By addressing these factors and implementing conveyor belt tracking devices, conveyor systems can achieve higher efficiency, safety, and reliability, marking a significant step forward in the management and operation of material handling systems.
Types of Conveyor Belt Tracking Devices
Conveyor belt tracking devices are essential components in the efficient operation of conveyor systems, ensuring the belt remains aligned with the conveyor’s intended path. These devices are crucial for preventing belt misalignment, which can lead to operational disruptions, increased maintenance costs, and potential safety hazards. Let’s explore the various types of conveyor belt tracking devices available.
Mechanical Tracking Devices
Mechanical tracking devices are the foundation of conveyor belt alignment solutions, offering straightforward, reliable methods for maintaining the correct path of the belt.
Conveyor Belt Trainer Roller
- Functionality: These rollers are strategically placed to gently guide the conveyor belt back to its correct path, adjusting automatically to correct any misalignment.
- Design: Typically includes a pivoting mechanism that responds to the belt’s movement, directing it towards the center of the conveyor.
- Installation: Can be installed at various points along the conveyor system, particularly near the head and tail pulleys where misalignment is most likely to occur.
- Adjustability: Offers adjustable tension settings to accommodate different belt widths and thicknesses.
- Durability: Constructed from robust materials capable of withstanding the harsh conditions of industrial environments.
- Cost-effectiveness: Provides a cost-effective solution for maintaining belt alignment without the need for complex machinery or constant manual adjustments.
Conveyor Belt Self Alignment System
- Automation: Utilizes sensors and control mechanisms to automatically detect and correct belt misalignment, reducing the need for manual intervention.
- Integration: Easily integrates into existing conveyor systems, offering a seamless solution for ongoing belt alignment issues.
- Precision: Delivers precise adjustments to the conveyor belt’s path, ensuring optimal alignment and reducing wear and tear.
- Reliability: Designed to operate reliably in a wide range of industrial environments, from light-duty applications to heavy-duty operations.
- Safety: Enhances operational safety by minimizing the risk of belt-related accidents and injuries.
- Efficiency: Improves overall conveyor system efficiency by ensuring continuous, uninterrupted operation.
Advanced Tracking Solutions
In the evolving landscape of conveyor system management, advanced tracking solutions represent the cutting edge of technology, seamlessly blending innovation with operational efficiency. These solutions, including the Pneumatic Belt Tracking System and Conveyor Belt Tracking Sensor, are designed to address the complex challenges of belt misalignment with precision and adaptability. By leveraging the latest advancements in technology, these systems offer a proactive approach to maintaining conveyor belt alignment, ensuring that operations run smoothly and without interruption. Let’s delve deeper into these advanced solutions and explore how they redefine conveyor belt tracking.
Pneumatic Belt Tracking System
- Operation: Employs air pressure, controlled by sensors, to gently steer the belt back into alignment, offering a responsive solution to belt misalignment.
- Responsiveness: Provides quick and precise adjustments to the belt’s position, ensuring minimal downtime and disruption to operations.
- Versatility: Suitable for a wide range of conveyor belt sizes and types, including heavy-duty belts.
- Maintenance: Requires minimal maintenance, with most systems designed for easy access to components for routine checks.
- Energy Efficiency: Utilizes energy-efficient components, reducing operational costs associated with belt alignment corrections.
Conveyor Belt Tracking Sensor
- Technology: Incorporates advanced sensors that continuously monitor the belt’s position, providing real-time data for immediate correction of misalignment.
- Integration: Can be integrated into both new and existing conveyor systems, offering a modern solution to belt alignment issues.
- Accuracy: Delivers high levels of accuracy in belt alignment, reducing the risk of damage to the belt and conveyor infrastructure.
- Data Analysis: Some systems offer data analysis capabilities, allowing for predictive maintenance and early detection of potential issues.
- Customization: Can be customized to suit specific conveyor system requirements, including belt width, speed, and environmental conditions.
Specialized Tracking Devices
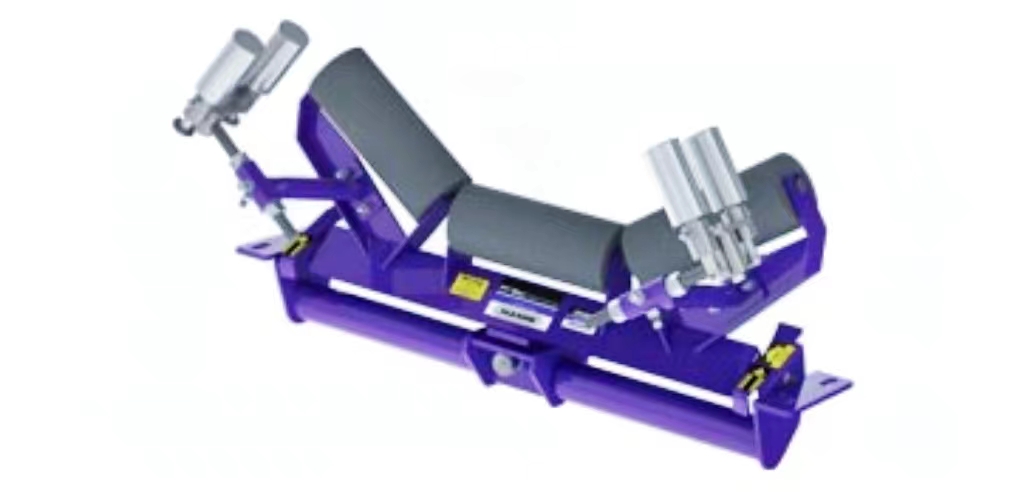
In the realm of conveyor system management, ensuring the precise alignment of the conveyor belt is paramount for operational efficiency and longevity. Specialized tracking devices have been developed to address the unique challenges of belt misalignment, each designed with specific features to cater to the diverse needs of various industrial environments. Below, we delve into the details of some of these specialized conveyor belt tracking devices, highlighting their innovative designs, functionalities, and the distinct advantages they offer.
Flexco Belt Tracker
- Innovation: Flexco’s belt trackers are known for their innovative design, which actively corrects misalignment without damaging the belt.
- Durability: Built to withstand the demanding conditions of various industrial environments, ensuring long-term reliability.
- Ease of Installation: Designed for easy installation and adjustment, reducing downtime associated with belt alignment corrections.
- Compatibility: Compatible with a wide range of belt widths and types, offering versatile solutions for different conveyor systems.
Conveyor Belt Gripper
- Functionality: Grippers provide a quick and effective means of correcting belt alignment manually or automatically, ideal for temporary adjustments.
- Application: Particularly useful during maintenance operations or in sections of the conveyor where precise control over the belt’s position is necessary.
- Design: Features a robust design that securely grips the belt, allowing for accurate alignment adjustments without stopping the conveyor.
- Flexibility: Can be used as a standalone solution or in conjunction with other conveyor belt tracking devices for enhanced alignment control.
Conveyor Components Company Model TA
- Automatic Tensioner: Utilizes an automatic tensioner that ensures consistent belt tension, crucial for maintaining alignment over long distances.
- Sensor Integration: Can be integrated with various types of sensors for real-time tracking adjustments, enhancing the precision of belt alignment.
- Energy Efficient: Operates with minimal energy consumption, contributing to lower operational costs and environmental impact.
- Customizable Options: Offers a range of customizable options, including different sensor types and mounting configurations, to meet specific conveyor system requirements.
Kinder Australia K-Commander® Control Series
- Engineered for Precision: Specifically designed to control belt tracking at critical conveyor transfer points, ensuring smooth transition and alignment.
- Adjustable Guide Rollers: Features adjustable guide rollers that accommodate various belt widths and thicknesses, offering a customized alignment solution.
- Robust Construction: Built to withstand the demanding conditions of heavy-duty industrial environments, ensuring durability and operational longevity.
- Installation Flexibility: Can be installed in both single-direction and reversible conveyor systems, providing a versatile solution for belt tracking.
Martin Engineering Belt Tracker
- Innovative Design: Utilizes a unique, patented design, detailed in the conveyor belt design manual, that automatically adjusts the belt’s position without requiring manual intervention.
- High Compatibility: Works effectively with both single-direction and reversible conveyor belts, making it versatile for various applications.
- Durability: Constructed with high-quality materials resistant to wear and tear, ensuring long-term reliability under harsh operational conditions.
- Ease of Installation: Designed for straightforward installation, minimizing downtime and allowing for quick integration into existing conveyor systems.
ASGCO Tru-Trainer®
- Responsive Tracking: Features a pivoting and tilting action that responds immediately to belt misalignment, gently guiding the belt back to center.
- Versatile Application: Suitable for both above-ground and underground operations, catering to a wide range of industries from mining to material handling.
- Low Maintenance: Requires minimal maintenance due to its high-quality construction and self-cleaning design, which prevents material build-up.
- Safety Enhancement: By maintaining proper belt alignment, it significantly reduces the risk of material spillage and associated safety hazards.
These conveyor belt tracking devices, from mechanical solutions to advanced and specialized systems, offer comprehensive options for maintaining optimal belt alignment in conveyor systems across various industries. Each device has its unique features and benefits, allowing for tailored solutions to meet the specific needs of different conveyor operations.
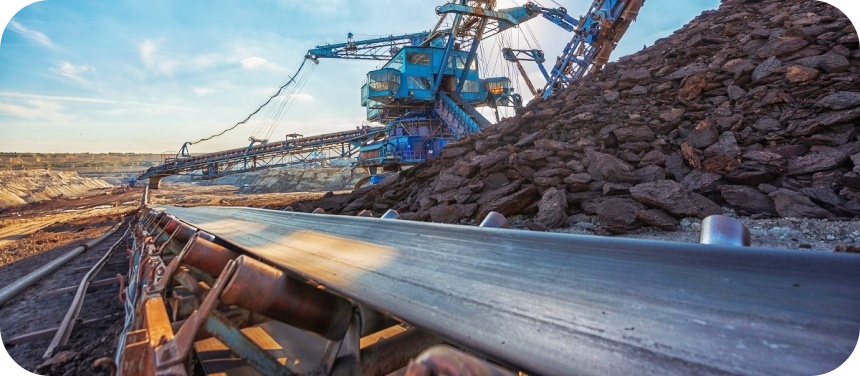
Benefits of Using Conveyor Belt Tracking Devices
Improved Efficiency
One of the most significant benefits of using conveyor belt tracking devices is the enhancement of operational efficiency. Conveyor belt tracking devices are designed to ensure that the conveyor belt remains aligned and follows the correct path. When a conveyor belt is misaligned, it can lead to various issues such as spillage, increased friction, and uneven wear. These problems can cause frequent stops in production to address and fix the issues, resulting in considerable downtime.
By maintaining proper belt alignment, conveyor belt tracking devices minimize these disruptions. They ensure that the belt runs smoothly and consistently, which enhances the overall efficiency of the operation. The reduced downtime means that the production process can continue without unnecessary interruptions, leading to higher productivity and throughput.
Moreover, conveyor belt tracking devices help in maintaining the correct tension and alignment of the belt, which reduces the strain on the belt and other components of the conveyor system. This leads to smoother operation and less energy consumption. The optimization of energy use further contributes to operational efficiency, as it reduces the operational costs associated with energy consumption.
In addition, the use of these tracking devices simplifies the maintenance process. With the belt properly aligned, there is less need for frequent adjustments and repairs. This not only saves time but also allows maintenance personnel to focus on other critical areas of the operation, thereby improving overall efficiency.
Safety Enhancement
Safety is a paramount concern in any industrial setting, and conveyor belt tracking devices play a crucial role in enhancing workplace safety. Belt misalignment can lead to several hazardous situations. For instance, a misaligned belt can cause spillage of materials, which can create slip-and-fall hazards for workers. In more severe cases, it can lead to the conveyor belt itself becoming damaged or derailed, posing serious risks to personnel working nearby.
Conveyor belt tracking devices help mitigate these risks by ensuring that the belt stays in its proper path. This reduces the chances of spillage and other issues that could lead to accidents. By maintaining a clean and orderly work environment, these devices help prevent accidents and injuries, contributing to a safer workplace.
Furthermore, properly aligned conveyor belts reduce the wear and tear on the system, which minimizes the risk of sudden failures or breakdowns. This is particularly important in environments where heavy machinery and equipment are used, as a sudden failure can have catastrophic consequences. By preventing such incidents, conveyor belt tracking devices help protect both the workers and the equipment.
Cost Savings
The long-term cost benefits of using conveyor belt tracking devices are substantial. One of the primary ways these devices save costs is by reducing wear and tear on the conveyor belt and associated components. When a conveyor belt is misaligned, it can cause uneven wear on the belt, pulleys, and rollers. This uneven wear can lead to the premature failure of these components, necessitating costly repairs or replacements.
By keeping the belt properly aligned, conveyor belt tracking devices ensure that the wear is evenly distributed across the belt and other components. This prolongs the lifespan of the conveyor system and reduces the frequency and cost of maintenance. Over time, the savings from reduced maintenance and replacement costs can be significant.
Additionally, the improved operational efficiency provided by these devices translates into cost savings. Reduced downtime means that the production process is more consistent and reliable, leading to higher output and revenue. The optimization of energy use also contributes to cost savings, as less energy is wasted due to friction and other inefficiencies caused by misalignment.
In the long run, the investment in conveyor belt tracking devices pays off through lower operational costs, reduced maintenance expenses, and a longer lifespan for the conveyor system. These savings can be reinvested into other areas of the business, further enhancing productivity and profitability.
Conveyor Belt Tracking Devices for Sale
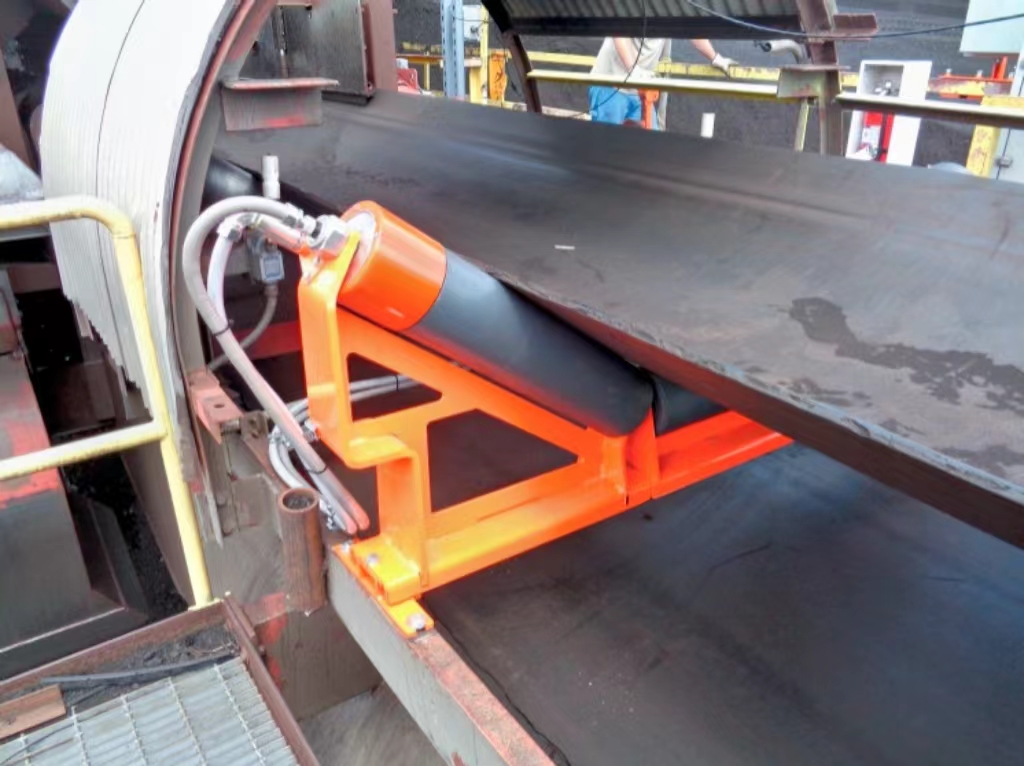
Market Overview
The market for conveyor belt tracking devices is extensive and diverse, catering to various industries such as manufacturing, mining, logistics, and food processing. Finding conveyor belt tracking devices for sale is relatively straightforward, with multiple channels available to potential buyers. These channels include specialized industrial equipment suppliers, online marketplaces, direct manufacturer sales, and equipment auctions.
Industrial equipment suppliers often have dedicated sections for conveyor belt tracking devices, providing a range of options from different manufacturers. These suppliers typically offer both new and used devices, catering to different budget requirements and operational needs. Suppliers like Grainger, MSC Industrial Supply, and Motion Industries are well-known for their comprehensive catalogs and expert advice.
Online marketplaces such as Amazon, eBay, and Alibaba provide an accessible platform for purchasing conveyor belt tracking devices. These platforms allow buyers to compare prices, read reviews, and evaluate various options before making a purchase. Additionally, these marketplaces often feature sellers from around the world, increasing the chances of finding the specific device needed.
Direct sales from manufacturers are another viable option. Many manufacturers have e-commerce websites where they list their products, including detailed specifications and pricing. Purchasing directly from manufacturers like Flexco, Martin Engineering, and Tru-Trac ensures that buyers receive high-quality, reliable devices with the added benefit of manufacturer support and warranties.
Equipment auctions, both online and in-person, also offer conveyor belt tracking devices for sale. These auctions are a good place to find high-quality used devices at competitive prices. Companies like Ritchie Bros. Auctioneers and EquipNet host regular auctions featuring a wide range of industrial equipment, including conveyor belt tracking devices.
Key Suppliers
Several major suppliers and manufacturers dominate the market for conveyor belt tracking devices. These companies are known for their innovative products, quality assurance, and comprehensive customer support.
- Flexco: Flexco offers a wide range of belt tracking products designed to handle various belt widths and speeds. Their products are known for their durability and effectiveness in maintaining belt alignment.
- Martin Engineering: Martin Engineering provides advanced belt tracking systems that incorporate patented technologies to ensure continuous and precise belt alignment. Their products are widely used in heavy-duty applications and are known for their reliability.
- Tru-Trac: Tru-Trac specializes in conveyor belt tracking solutions that are easy to install and maintain. Their products are designed to operate in harsh conditions and provide immediate adjustment to misalignment.
- Richwood: Richwood offers a variety of belt tracking devices that are suitable for different types of conveyor systems. Their products are recognized for their robust construction and long service life.
- CenTrax: CenTrax is known for its multi-roller belt tracking systems that correct misalignment on both the carrying and return strands of the conveyor. Their innovative design ensures maximum performance and reliability.
- Benetech: Benetech provides comprehensive conveyor belt tracking solutions, including both standard and custom-designed devices. Their products are built to handle the most demanding conditions and offer maintenance-free operation.
Buying Tips
Selecting the right conveyor belt tracking device requires careful consideration of several factors to ensure optimal performance and longevity.
- Assess Your Needs: Begin by evaluating the specific needs of your conveyor system. Consider factors such as belt width, belt speed, load weight, and the environmental conditions in which the device will operate. This will help narrow down the options to those that are best suited for your application.
- Compatibility: Ensure that the tracking device is compatible with your existing conveyor system. Check the device’s specifications, including dimensions, mounting requirements, and integration capabilities. Consulting with a technician or the manufacturer can provide valuable insights into compatibility.
- Quality and Durability: Look for devices from reputable manufacturers known for their quality and durability. High-quality tracking devices are constructed from robust materials that can withstand harsh conditions and provide long-lasting performance.
- Ease of Installation and Maintenance: Consider the ease of installation and maintenance of the tracking device. Devices that are easy to install and require minimal maintenance can save time and reduce operational disruptions. Look for products with clear installation instructions and available support from the manufacturer.
- Customer Reviews and Testimonials: Reading customer reviews and testimonials can provide valuable insights into the performance and reliability of the tracking device. Look for feedback from other users in similar industries or applications to gauge the effectiveness of the device.
- Manufacturer Support and Warranty: Opt for devices that come with a warranty and robust manufacturer support. This ensures that you have access to technical assistance and replacement parts if needed, enhancing the longevity and reliability of the device.
- Cost vs. Value: While cost is an important consideration, it should not be the only factor. Evaluate the overall value of the device, including its features, durability, and support. Investing in a high-quality tracking device can provide long-term savings by reducing downtime and maintenance costs.
By carefully considering these factors, businesses can select the right conveyor belt tracking devices to enhance their operations, improve efficiency, and ensure reliable performance.
Used Conveyor Belt Tracking Devices
Availability
The market for used conveyor belt tracking devices is robust, catering to industries looking to optimize their operations without incurring the high costs associated with purchasing brand-new equipment. These used devices are widely available through various channels, including specialized equipment resellers, online marketplaces, industrial auctions, and direct sales from companies upgrading their systems.
Online marketplaces such as eBay, Craigslist, and industry-specific platforms like Machinio and EquipNet offer a broad selection of used conveyor belt tracking devices. These platforms provide detailed listings that include photos, specifications, and seller contact information, making it easy for buyers to find and evaluate potential purchases.
Industrial auctions, both online and in-person, are another valuable source for used conveyor belt tracking devices. These auctions often feature equipment from businesses that are downsizing, upgrading, or liquidating assets, providing an opportunity to acquire high-quality devices at competitive prices.
Direct sales from companies upgrading their conveyor systems also present an excellent opportunity to purchase used conveyor belt tracking devices. These companies may offer their old equipment at a discounted rate, providing a cost-effective solution for other businesses.
Advantages
One of the primary advantages of purchasing used conveyor belt tracking devices is cost savings. New tracking devices can be quite expensive, and the price can be prohibitive for smaller companies or those with limited budgets. By opting for used devices, businesses can acquire the necessary equipment at a fraction of the cost, allowing them to allocate funds to other critical areas of their operations.
In addition to cost savings, used conveyor belt tracking devices often come with the advantage of immediate availability. Unlike new devices, which may have lead times due to manufacturing and shipping, used devices are typically ready for immediate purchase and deployment. This can be particularly beneficial in situations where a quick replacement or upgrade is needed to minimize downtime.
Another advantage is the potential to acquire high-quality, well-maintained devices. Many used conveyor belt tracking devices come from reputable manufacturers known for their durable and reliable products. If the previous owner has maintained the equipment properly, these used devices can offer many more years of effective service. Furthermore, buying from reputable resellers often includes a limited warranty or guarantee, providing additional peace of mind.
Considerations
While there are numerous advantages to purchasing used conveyor belt tracking devices, there are also important considerations to keep in mind to ensure a successful acquisition.
First and foremost, the condition of the device is paramount. Potential buyers should thoroughly inspect the equipment for any signs of wear and tear, damage, or degradation that could impact performance. This may include checking for rust, ensuring that moving parts are not excessively worn, and confirming that all components are present and functional. In cases where an in-person inspection is not possible, requesting detailed photos and maintenance records from the seller can be helpful.
Compatibility is another crucial factor to consider. Conveyor systems vary widely in their design and specifications, so it is essential to ensure that the used conveyor belt tracking device is compatible with the existing system. This includes verifying dimensions, mounting requirements, and integration capabilities. Consulting with a knowledgeable technician or the device manufacturer can provide valuable insights into compatibility issues.
Buyers should also consider the device’s history and provenance. Understanding the previous usage of the device can provide insights into its remaining lifespan and potential performance issues. For instance, a device that has been used in a high-stress, demanding environment may have more wear and shorter remaining lifespan compared to one used in a less strenuous setting.
Additionally, it’s important to evaluate the availability of spare parts and support for the used device. Some older models may have limited parts availability, making repairs and maintenance more challenging. Ensuring that spare parts are readily available can help maintain the device’s functionality over the long term.
Purchasing used conveyor belt tracking devices can offer significant cost savings and immediate availability, making it an attractive option for many businesses. However, it is essential to carefully consider the device’s condition, compatibility, history, and parts availability to ensure a successful investment. By taking these factors into account, businesses can effectively integrate used conveyor belt tracking devices into their operations, enhancing efficiency and performance while managing costs.
Tips for Selecting the Right Conveyor Belt Tracking Devices
Choosing the appropriate conveyor belt tracking devices is crucial for ensuring the efficient and safe operation of conveyor systems. The selection process involves considering various factors to find a solution that meets the specific needs of your conveyor system. Here are seven key points to consider when selecting the right conveyor belt tracking device:
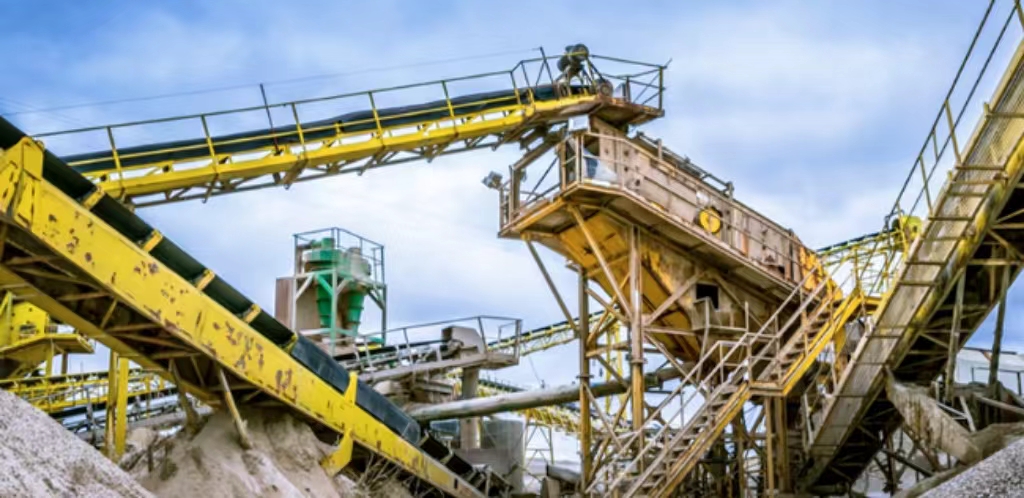
- Type of Conveyor System: The design and functionality of the conveyor system play a significant role in selecting a tracking device. Different systems, such as flat belt conveyors, roller conveyors, or modular belt conveyors, may require specific types of tracking devices tailored to their unique mechanics and operational dynamics.
- Belt Material: The material of the conveyor belt affects which tracking device will be most effective. Materials like rubber, PVC, or fabric have different properties and behaviors under operational stress, influencing the choice of tracking device. Some devices are better suited for heavy-duty materials, while others are designed for lighter, more delicate belts.
- Operational Environment: The environment in which the conveyor operates can significantly impact the choice of conveyor belt tracking devices. Factors such as exposure to water, chemicals, extreme temperatures, or abrasive materials necessitate tracking devices that can withstand these conditions without degrading.
- Specific Alignment Challenges: Understanding the particular alignment issues faced by your conveyor system is crucial. Issues such as consistent belt drift, uneven load distribution, or frequent changes in direction or elevation require specialized tracking solutions designed to address these challenges effectively.
- Conveyor Belt Width and Speed: The width and speed of the conveyor belt must be considered to ensure the selected tracking device can accommodate the belt’s dimensions and operational pace. Devices vary in their capacity to handle different belt widths and speeds, affecting their efficiency and effectiveness.
- Maintenance and Adjustability: Consider the ease of maintenance and adjustability of the tracking device. Systems that allow for easy adjustments and have low maintenance requirements can reduce downtime and operational costs. Devices with simple, robust designs tend to be easier to maintain and adjust.
- Cost and ROI: While the initial cost is an important consideration, it’s also crucial to evaluate the potential return on investment (ROI) that a tracking device offers. Factors such as reduced downtime, extended belt life, and decreased maintenance costs contribute to the overall ROI. Selecting a device that offers the best balance between upfront costs and long-term savings is essential.
When selecting conveyor belt tracking devices, it’s important to conduct a thorough analysis of your conveyor system’s specific needs and challenges. Consulting with manufacturers or specialists can provide valuable insights and recommendations tailored to your system. By carefully considering these factors, you can ensure that you choose the most appropriate and effective tracking device for your conveyor system, enhancing its efficiency, safety, and longevity.
Installation and Maintenance of Conveyor Belt Tracking Devices
The proper installation and maintenance of conveyor belt tracking devices are critical to ensuring the optimal performance and longevity of these systems. By following a set of guidelines, you can enhance the efficiency and reliability of your conveyor belt tracking devices, ensuring they function effectively over their operational lifespan.
Installation Tips for Conveyor Belt Tracking Devices
- Understand the Manufacturer’s Instructions: Before installation, thoroughly review the manufacturer’s instructions. Each conveyor belt tracking device may have unique installation requirements based on its design and intended use.
- Ensure Proper Placement: The effectiveness of conveyor belt tracking devices heavily depends on their placement along the conveyor system. Install the devices at critical points where misalignment is most likely to occur, such as near the head and tail pulleys.
- Align the Conveyor Structure: Before installing conveyor belt tracking devices, ensure that the conveyor structure itself is properly aligned. Misalignment of the conveyor frame can undermine the effectiveness of tracking devices.
- Calibrate Devices Accurately: Proper calibration of conveyor belt tracking devices is essential for their optimal performance. Follow the manufacturer’s guidelines for calibration to ensure the devices can correctly detect and correct belt misalignment.
- Test Before Full Operation: After installation, conduct tests under various operating conditions to ensure the conveyor belt tracking devices are functioning as expected. This may include running the conveyor at different speeds or with different loads.
- Train Maintenance Personnel: Ensure that maintenance personnel are trained on the specific conveyor belt tracking devices installed. Understanding how these devices function and are adjusted is crucial for ongoing maintenance and troubleshooting.
Need conveyor belts? Reach out for expert assistance.
Maintenance Best Practices
- Regular Inspections: Conduct regular inspections of conveyor belt tracking devices to identify any signs of wear or damage early. This includes checking for any mechanical wear, proper alignment, and responsiveness to belt misalignment.
- Clean Devices Regularly: Accumulation of dust, debris, or residues can affect the performance of conveyor belt tracking devices. Implement a regular cleaning schedule to maintain their functionality.
- Monitor Performance: Continuously monitor the performance of conveyor belt tracking devices. This can involve checking for consistent belt alignment, listening for unusual noises, and observing the correction of any misalignment.
- Replace Worn Parts Promptly: If inspection reveals worn or damaged parts, replace them promptly to prevent further damage or inefficiency. Use only manufacturer-recommended parts for replacements to ensure compatibility and reliability.
- Keep Records of Maintenance: Maintain detailed records of all maintenance activities, including inspections, cleanings, adjustments, and part replacements. This documentation can help identify patterns or recurring issues that may require further attention.
- Seek Manufacturer Support When Needed: If you encounter issues with conveyor belt tracking devices that cannot be resolved through routine maintenance, do not hesitate to contact the manufacturer for support. They can provide expert advice, additional troubleshooting tips, or professional maintenance services.
By adhering to these installation and maintenance guidelines, you can ensure that your conveyor belt tracking devices operate efficiently and effectively, contributing to the overall performance and safety of your conveyor system.
Case Studies and Success Stories of Conveyor Belt Tracking Devices
The implementation of conveyor belt tracking devices across various industries has led to significant improvements in operational efficiency, safety, and system longevity. Here are six real-world examples demonstrating how these devices have successfully addressed alignment challenges, showcasing the versatility and effectiveness of conveyor belt tracking solutions.
1. Mining Industry: Enhanced Safety and Reduced Downtime
RockSolid Mining Ltd., a large mining operation, faced frequent belt misalignment, leading to considerable downtime and significant safety risks. The installation of advanced pneumatic belt tracking systems from TrackTech Solutions allowed for real-time adjustments to belt alignment. This drastically reduced downtime caused by misalignments and enhanced worker safety. The system’s ability to adjust automatically to varying loads and operational conditions proved invaluable in the demanding mining environment.
2. Food Processing Facility: Improved Hygiene and Productivity
FreshFoods Processing Inc. faced challenges with belt misalignment, contributing to product spillage and contamination risks. By integrating conveyor belt tracking sensors from HygieneBelt Systems, the facility was able to maintain precise belt alignment, significantly reducing spillage and improving overall hygiene. The sensors’ real-time monitoring and adjustment capabilities ensured continuous, efficient operation, directly impacting productivity and compliance with stringent hygiene standards.
3. Packaging Industry: Increased Throughput and Reduced Maintenance
PackMaster Ltd. struggled with frequent belt misalignments, causing product damage and requiring constant maintenance. The adoption of Flexco Belt Trackers addressed these issues by providing durable, reliable alignment correction. The trackers’ innovative design minimized wear on the belt and conveyor structure, leading to increased throughput and significantly lower maintenance costs.
4. Automotive Manufacturing: Precision Alignment in Assembly Lines
In the assembly line of AutoPrecision GmbH, precise belt alignment was crucial for the accurate positioning of components. The implementation of conveyor belt self-alignment systems from AlignTech Automotive ensured that the assembly line operated with high precision, eliminating alignment-related disruptions. This precision directly contributed to the quality of the final product and the efficiency of the assembly process.
5. Material Handling: Enhanced Operational Flexibility
FlexiTrans Solutions, a material handling facility, required a flexible solution to accommodate the diverse sizes and weights of materials being transported. Conveyor belt grippers from GripTech Industries were introduced at critical transfer points, offering the needed adjustability and control. These devices provided temporary, yet effective, corrections to belt alignment, allowing the facility to maintain smooth operations across its diverse range of materials.
6. Recycling Plant: Addressing Heavy-Duty Alignment Challenges
EcoCycle Recycling Plant dealt with heavy-duty materials and faced persistent belt alignment issues, leading to operational inefficiencies and increased wear on equipment. The installation of robust, specialized tracking devices from HeavyTrack Systems brought about a significant improvement. These devices were able to withstand the harsh operational conditions, ensuring consistent belt alignment and extending the lifespan of both the belt and the conveyor system.
These case studies highlight the transformative impact of conveyor belt tracking devices across a spectrum of industries. By addressing specific alignment challenges, these devices not only enhance operational efficiency and safety but also contribute to significant cost savings and productivity improvements. The success stories underscore the importance of selecting the right tracking solution tailored to the unique needs of each conveyor system.
FAQs about Conveyor Belt Tracking Devices
The optimal method for tracking a conveyor belt involves a combination of proper installation, regular maintenance, and the use of appropriate conveyor belt tracking devices. Initially, ensuring that the conveyor belt is correctly installed, with the frame squared and the rollers and pulleys aligned, is fundamental. Regular maintenance should include checking belt tension, alignment, and the condition of the belt and rollers to prevent misalignment issues.
Incorporating advanced conveyor belt tracking devices, such as self-aligning rollers, pneumatic tracking systems, or electronic sensors, significantly enhances the belt’s tracking. These devices automatically adjust the belt’s position to keep it aligned, reducing the need for manual intervention and minimizing downtime. The choice of tracking device depends on the specific requirements of the conveyor system, including the type of belt, operational environment, and the nature of the materials being transported. Consulting with a specialist or the conveyor system manufacturer can provide tailored advice on the best tracking solution for your system.
Sensors on a conveyor belt are critical components used for monitoring various aspects of conveyor operation, including speed, alignment, and the presence of objects on the belt. These sensors can be categorized based on their function:
Speed Sensors: Measure the speed of the conveyor belt to ensure it operates within the specified limits, contributing to the efficiency and safety of the system.
Alignment Sensors: Detect misalignment of the conveyor belt and provide signals to tracking devices or control systems to correct the belt’s path.
Proximity Sensors: Identify the presence or absence of objects on the conveyor, useful in applications requiring precise item counting or spacing.
Load Sensors: Monitor the weight or load on the conveyor belt, aiding in the prevention of overloading and potential damage to the system.
The integration of these sensors into a conveyor system allows for real-time monitoring and control, enhancing operational efficiency, safety, and maintenance processes.
The roller used specifically for tracking a conveyor belt is known as a “tracking roller” or “guide roller.” These rollers are designed to ensure that the conveyor belt maintains its intended path along the conveyor frame. Tracking rollers are typically installed at strategic points along the conveyor system where misalignment is most likely to occur, such as near the head and tail pulleys.
Tracking rollers can be self-aligning, where their design allows them to pivot or tilt in response to the belt’s movement, guiding the belt back to its correct position. The effectiveness of tracking rollers in maintaining belt alignment is enhanced when used in conjunction with other conveyor belt tracking devices, such as sensors or pneumatic systems, providing a comprehensive solution to belt misalignment issues.
A belt tracker is a device or system designed to maintain the alignment of a conveyor belt, ensuring it runs straight and true along the conveyor frame. Belt trackers detect when the conveyor belt begins to drift off its intended path and make the necessary adjustments to realign the belt. These devices can be mechanical, such as tracking rollers or self-aligning idlers, or more advanced solutions like pneumatic tracking systems or electronic sensors.
The primary goal of a belt tracker is to prevent the common issues associated with belt misalignment, including uneven belt wear, damage to the conveyor structure, product spillage, and increased maintenance costs. By ensuring consistent belt alignment, belt trackers contribute to the operational efficiency, safety, and longevity of conveyor systems across various industries.
Conveyor tracking is the process of ensuring that a conveyor belt runs straight and true along its path. This is crucial to prevent the belt from drifting to one side, which can cause damage to the belt and the equipment, as well as reduce efficiency. Tracking involves adjusting the belt’s tension, alignment, and the position of rollers or pulleys. Proper tracking ensures that the belt moves smoothly without excessive wear and tear. Advanced tracking systems may use sensors and automatic adjustments to maintain optimal alignment.
Keeping a conveyor belt on track involves several steps. First, ensure that the belt is properly tensioned. Too much or too little tension can cause the belt to drift. Next, check the alignment of the pulleys and rollers; they should be square to the belt’s direction of travel. Adjust these components if necessary. Regular maintenance is also crucial; keep the belt and rollers clean and free of debris. Additionally, use tracking devices or guides, such as crowned pulleys or edge guides, to help maintain the belt’s position. In more advanced systems, sensors and automated tracking systems can be employed to continuously monitor and adjust the belt alignment.
Conveyor belt safety devices are essential for protecting both the equipment and the workers who operate it. These devices include emergency stop buttons, safety pull cords, and limit switches, which can immediately halt the belt in case of an emergency. Guarding devices, such as safety guards and barriers, prevent access to dangerous areas of the conveyor. Belt misalignment switches and speed sensors are used to detect and correct operational issues that could lead to accidents. Additionally, interlock systems ensure that the conveyor cannot operate unless all safety guards are in place. Safety awareness training and regular maintenance are also key components of a comprehensive conveyor safety program.
Last Updated on June 21, 2024 by Jordan Smith
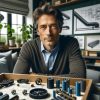
Jordan Smith, a seasoned professional with over 20 years of experience in the conveyor system industry. Jordan’s expertise lies in providing comprehensive solutions for conveyor rollers, belts, and accessories, catering to a wide range of industrial needs. From initial design and configuration to installation and meticulous troubleshooting, Jordan is adept at handling all aspects of conveyor system management. Whether you’re looking to upgrade your production line with efficient conveyor belts, require custom conveyor rollers for specific operations, or need expert advice on selecting the right conveyor accessories for your facility, Jordan is your reliable consultant. For any inquiries or assistance with conveyor system optimization, Jordan is available to share his wealth of knowledge and experience. Feel free to reach out at any time for professional guidance on all matters related to conveyor rollers, belts, and accessories.