Conveyor Belt Tracking Guide
In the realm of material handling and industrial automation, the precision of conveyor belt systems plays a pivotal role in operational efficiency. At the heart of maintaining this precision lies the critical practice of conveyor belt tracking. This guide aims to shed light on the significance of proper alignment and the potential pitfalls that can arise from neglect. Misalignment often leads to uneven belt wear, product damage, or even prolonged downtimes, which can significantly impact productivity and maintenance costs. By adhering to the principles outlined in this conveyor belt tracking guide, facilities can ensure smoother operations, extend the lifespan of their conveyor systems, and mitigate common issues such as belt slippage and misalignment.
What Is the Conveyor Belt Tracking Guide
In the intricate world of conveyor systems, the alignment and proper functioning of the conveyor belt are paramount. This segment of the conveyor belt tracking guide illuminates the essence of what conveyor belt tracking stands for and its critical importance in the seamless operation of conveyor systems.
Definition and Significance of Conveyor Belt Tracking
Conveyor belt tracking is more than just a routine maintenance task; it’s a fundamental aspect that ensures the longevity and efficiency of conveyor systems. Here’s why it holds such significance:
- Foundation of System Efficiency: Conveyor belt tracking is the process of ensuring the belt remains in the intended path and does not drift laterally. This is crucial for the smooth operation of the conveyor system.
- Prevention of Belt Damage: Proper tracking minimizes wear and tear on the belt edges, thereby extending the belt’s lifespan and reducing the need for frequent replacements.
- Material Handling Accuracy: It ensures that materials are transported efficiently and accurately along the conveyor, reducing spillage and wastage.
- Operational Safety: A well-tracked belt minimizes the risk of accidents and enhances the safety of the working environment.
- Cost Efficiency: By reducing the need for repairs and maintenance, effective tracking contributes to overall cost savings.
- Energy Conservation: A misaligned belt can increase resistance and energy consumption. Proper tracking ensures optimal energy use.
- Preservation of Material Quality: It ensures that the materials being transported are not damaged due to misalignment or spillage.
- System Longevity: By reducing stress on the conveyor’s components, proper tracking contributes to the overall durability of the system.
- Operational Reliability: Ensures consistent and reliable operation of the conveyor system, which is crucial for meeting production targets and deadlines.
The Impact of Improper Tracking on Conveyor Belt Efficiency and Lifespan
The consequences of neglecting conveyor belt tracking theory can be far-reaching, affecting not just the conveyor belt but the entire system’s efficiency and lifespan:
- Increased Operational Costs: Misalignment can lead to excessive wear, necessitating frequent belt replacements and repairs.
- Reduced Efficiency: A belt that is not properly tracked can cause slippage and reduced throughput, impacting overall productivity.
- Material Loss and Contamination: Improper tracking can lead to material spillage, resulting in loss of materials and potential contamination of the work environment.
- Component Stress: Misalignment puts additional stress on rollers, bearings, and the conveyor frame, leading to premature failures.
- Safety Hazards: A misaligned belt can pose significant safety risks, including the potential for accidents and injuries.
- Energy Waste: An improperly tracked belt requires more energy to move, leading to higher operational costs and environmental impact.
- Downtime: Correcting issues caused by poor tracking can lead to significant downtime, affecting production schedules and deadlines.
- Reduced System Lifespan: The cumulative effect of these issues can significantly reduce the lifespan of the conveyor system, leading to earlier-than-expected replacements and upgrades.
Understanding the principles laid out in this conveyor belt tracking guide is the first step towards ensuring the longevity and efficiency of your conveyor systems. Proper attention to tracking not only safeguards the conveyor belt but also enhances the overall productivity and safety of the operation.
How to Track a Conveyor Belt
Conveyor belt tracking is essential for maintaining efficient and reliable operation. Here are three easy steps for tracking a conveyor belt:
Step 1: Loosen the Bolts Closest to the Tail Pulley
- Identify the Snub Roller: The snub roller is the primary method for steering the conveyor belt and is located near the tail pulley.
- Loosen the Bolts: While the conveyor is operating, carefully loosen the bolts closest to the tail pulley. This will allow the snub roller to move and adjust the tracking of the belt.
Step 2: Adjust the Snub Roller
- Use a Rubber Mallet: Gently tap the bolts with a rubber mallet in the direction you want the conveyor belt to move. For example, if you want the belt to move to the right, tap the bolts on the left side, and vice versa.
- Observe the Movement: As you tap the bolts, the snub roller will move, causing the belt to shift. Make small adjustments and observe the belt’s movement.
- Re-Tighten the Bolts: Once the snub roller has been adjusted to the desired position, re-tighten the bolts to lock the snub roller in place.
Step 3: Repeat and Fine-Tune
- Measure the Alignment: Check the alignment of the conveyor belt. The center of the belt should be within a quarter inch of the tail pulley’s center.
- Repeat Adjustments: If the belt is not yet properly aligned, repeat steps 1 and 2. Make small, incremental adjustments to avoid overcorrecting.
- Start from the Ends: Begin with the snub rollers closest to the ends of the conveyor and work your way towards the center. This approach ensures a more precise alignment.
By following these three easy steps, you can effectively track your conveyor belt, ensuring it runs smoothly and efficiently. Remember, small adjustments can make a significant difference, so proceed with caution and patience.

5 Steps Conveyor Belt Tracking Process
A 5-step conveyor belt tracking process strikes a balance between thoroughness and simplicity, ensuring effective belt alignment while being manageable. Here’s a detailed 5-step process to help maintain proper conveyor belt tracking:
Step 1: Initial Inspection and Preparation
- Inspect the System: Perform a comprehensive inspection of the conveyor system, including the belt, frame, pulleys, rollers, and tracking devices. Look for signs of wear, damage, misalignment, or debris accumulation.
- Verify Frame Alignment: Use a level and carpenter’s square to ensure the conveyor frame and structure are level and square. Misalignment of the frame can lead to significant tracking issues.
- Check Belt Condition: Examine the belt for any wear, tears, or fraying edges. Address any damage or issues before proceeding.
Step 2: Adjust Belt Tension
- Measure Tension: Use a tension gauge to measure the current belt tension and compare it with the manufacturer’s recommended settings.
- Adjust Tension: If the belt tension is not within the recommended range, adjust it accordingly. Ensure that the tension is uniform across the belt width to prevent uneven wear and tracking problems.
- Recheck Tension: After adjustment, recheck the tension to confirm it is within the correct range.
Step 3: Align and Adjust Pulleys and Rollers
- Alignment Check: Verify that all pulleys and rollers are parallel to each other and perpendicular to the belt centerline. Misaligned pulleys and rollers can cause the belt to track improperly.
- Make Adjustments: If any pulleys or rollers are misaligned, adjust their positions. Use the manufacturer’s guidelines for proper alignment techniques.
- Test Alignment: Run the conveyor at a slow speed to observe the belt’s movement and ensure it is running straight and centered.
Step 4: Utilize Tracking Devices
- Crowned Pulleys: Ensure that crowned pulleys are properly installed and positioned to help center the belt automatically.
- Snub Rollers and Tracking Idlers: Adjust snub rollers and tracking idlers to increase belt wrap angle and improve tracking. These devices can be pivoted or adjusted to guide the belt back to the center.
- Fine-Tune Adjustments: Make small, incremental adjustments to the tracking devices while the conveyor is running at a slow speed. Observe the belt’s response to each adjustment until it tracks consistently in the center.
Step 5: Implement Ongoing Monitoring and Maintenance
- Scheduled Inspections: Establish a routine inspection schedule to regularly check the conveyor system. Look for signs of wear, misalignment, and proper belt tension.
- Preventive Maintenance: Clean the belt and components regularly to prevent debris buildup. Lubricate moving parts and replace any worn or damaged parts before they cause significant issues.
- Monitor Performance: Continuously monitor the conveyor system’s performance. Keep records of any adjustments made and track recurring issues to identify potential long-term solutions.
By following this 5-step process, you can effectively maintain proper conveyor belt tracking, minimize downtime, and extend the lifespan of your conveyor system.
6 Basic Conveyor Belt Tracking Rules to Follow
Following the 6 conveyor belt tracking guide ensuring proper tracking of a conveyor belt is crucial for optimal performance and longevity.Here are six basic rules to follow for effective conveyor belt tracking:
Proper Installation
- Frame Alignment: Ensure the conveyor frame is level and square. Misalignment can lead to tracking issues from the start. Use a spirit level and carpenter’s square to verify the alignment.
- Pulley and Roller Alignment: Confirm that all pulleys and rollers are installed at right angles to the belt centerline and parallel to each other. Misaligned pulleys can cause the belt to run off-center.
Regular Inspections and Maintenance
- Scheduled Inspections: Implement a routine inspection schedule to identify potential issues early. Check the belt for wear, damage, or fraying.
- Component Checks: Inspect pulleys, rollers, and other components for signs of wear or damage. Replace any worn or damaged parts promptly.
- Lubrication: Ensure that all moving parts are properly lubricated according to the manufacturer’s recommendations to prevent excessive wear and tear.
Belt Tension
- Correct Tension: Adjust the belt tension according to the manufacturer’s specifications. Use a tension gauge to measure and set the appropriate tension.
- Avoid Over-Tensioning: Over-tightening can cause unnecessary strain on the belt and components, leading to premature failure.
- Check Regularly: Regularly check the belt tension as it can change over time due to stretching or other factors.
Cleanliness
- Regular Cleaning: Implement a regular cleaning schedule to remove dust, debris, and any buildup from the belt and surrounding area.
- Cleaning Tools: Use appropriate tools such as brushes, scrapers, or compressed air to clean the belt and pulleys without causing damage.
- Prevent Contamination: Ensure that the conveyor system is protected from external contaminants that could cause tracking issues.
Load Distribution
- Central Loading: Ensure that the load is placed centrally on the belt. Uneven loading can cause one side of the belt to bear more weight, leading to tracking issues.
- Load Sensors: Consider using load sensors to monitor and ensure even load distribution across the belt.
- Adjust Loading Practices: If uneven loading is a recurrent issue, adjust loading practices or modify the conveyor system to accommodate more balanced loading.
Adjusting Tracking Devices
- Crowned Pulleys: Use crowned pulleys which are slightly higher in the center to help the belt track correctly. Adjust the pulley position to fine-tune the tracking.
- Snub Rollers: Install snub rollers which are placed close to the head and tail pulleys to increase the belt wrap angle and improve tracking.
- Tracking Idlers: Use tracking idlers that can pivot and guide the belt back to the center. Adjust the angle and position of these idlers to ensure proper tracking.
By thoroughly understanding and implementing these detailed rules, you can significantly improve the performance, reliability, and longevity of your conveyor belt system. Regular monitoring, maintenance, and adjustments are key to avoiding downtime and ensuring efficient operation.

How to Fix Conveyor Belt Tracking
Conveyor belt tracking issues can disrupt operations and lead to increased wear and tear. Here’s a step-by-step guide to fix conveyor belt tracking problems:
Step 1: Inspect the Conveyor System
- Thorough Inspection: Examine the entire conveyor system, including the belt, frame, pulleys, rollers, and tracking devices. Look for signs of wear, damage, or misalignment.
- Cleanliness: Ensure the belt and surrounding components are clean. Remove any debris or buildup that might affect the belt’s movement.
Step 2: Verify Frame and Component Alignment
- Frame Squareness: Use a level and carpenter’s square to ensure the conveyor frame is level and square. Misalignment of the frame can cause significant tracking issues.
- Pulley and Roller Alignment: Check that all pulleys and rollers are aligned parallel to each other and perpendicular to the belt’s centerline. Misaligned pulleys or rollers can cause the belt to track improperly.
Step 3: Check and Adjust Belt Tension
- Measure Tension: Use a tension gauge to measure the current tension of the belt. Compare it with the manufacturer’s recommended tension settings.
- Adjust Tension: Adjust the belt tension as needed, ensuring it is uniform across the belt width. Proper tension is crucial for preventing slippage and ensuring proper tracking.
Step 4: Adjust the Snub Rollers
- Loosen the Bolts: While the conveyor is running, carefully loosen the bolts closest to the snub rollers, usually located near the tail pulley belt conveyor.
- Tap with a Rubber Mallet: Use a rubber mallet to gently tap the bolts in the direction you want the conveyor belt to move. For example, tap the left bolts to move the belt to the right, and vice versa.
- Observe and Adjust: Observe the belt’s movement as you make adjustments. Make small, incremental changes and observe the effects before proceeding with further adjustments.
- Re-Tighten the Bolts: Once the belt is tracking correctly, re-tighten the bolts to lock the snub roller in the new position.
Step 5: Fine-Tune Tracking Devices
- Utilize Tracking Devices: If your conveyor has tracking devices like crowned pulleys or tracking idlers, adjust them as needed. These devices can help guide the belt back to the center.
- Incremental Adjustments: Make small adjustments to tracking devices while the conveyor is running. Continue to monitor the belt’s movement and make further adjustments as necessary.
Step 6: Monitor and Repeat as Necessary
- Measure Alignment: Check the alignment of the conveyor belt regularly. The center of the belt should be within a quarter inch of the tail pulley’s center.
- Repeat Adjustments: If the belt is not yet properly aligned, repeat steps 4 and 5. Continue making small, incremental adjustments to avoid overcorrecting.
- Start from the Ends: Begin adjustments with the snub rollers closest to the ends of the conveyor and work your way towards the center for more precise alignment.
Step 7: Implement Regular Maintenance and Monitoring
- Scheduled Inspections: Establish a routine maintenance schedule to regularly inspect and maintain the conveyor system. Check for signs of wear, misalignment, and proper belt tension.
- Preventive Maintenance: Clean the belt and surrounding components regularly to prevent debris buildup. Lubricate moving parts and replace worn components before they cause significant issues.
- Continuous Monitoring: Keep a close eye on the conveyor system’s performance. Log any adjustments made and track recurring issues to identify potential long-term solutions.
By following this comprehensive guide, you can effectively fix and maintain proper conveyor belt tracking, ensuring smooth and efficient operation.
Essential Components for Effective Belt Tracking in the Conveyor Belt Tracking Guide
Delving deeper into the conveyor belt tracking guide, it becomes evident that the effectiveness of belt tracking hinges on several critical components. Each part plays a unique role in ensuring the conveyor belt remains on its intended path, thereby safeguarding the system’s efficiency and longevity.
Overview of Conveyor Belt Components Crucial for Tracking
- Drive Pulleys: These pulleys provide the primary force for moving the belt. Proper alignment and surface condition of drive pulleys are vital for effective belt tracking.
- Tail Pulleys: Located at the opposite end of the conveyor system, tail pulleys support the returning belt. Their alignment significantly influences belt tracking.
- Idler Rollers: Distributed along the conveyor frame, idler rollers support the belt and products carried on it. Their level and alignment are crucial for maintaining the belt’s path.
- Snub Rollers: Positioned close to the drive and tail pulleys, snub rollers increase the belt’s contact with pulleys, enhancing traction and aiding in tracking.
- Tracking Rollers: Specifically designed for adjusting the belt’s path, tracking rollers can tilt or pivot to guide the belt back to its correct alignment.
- Belt Material: The material and condition of the conveyor belt itself can affect tracking. Stiff or warped belts may resist alignment efforts.
- Tensioning Devices: Proper belt tension is essential for tracking. Tensioning devices ensure the belt is tight enough to maintain contact with rollers and pulleys but not so tight as to cause strain.
- Belt Cleaners: Debris on the belt can lead to tracking issues. Belt cleaners help maintain a clean belt surface, crucial for consistent tracking.
- Conveyor Frame: The structural integrity of the conveyor frame affects all components. A misaligned frame can lead to widespread tracking issues across the system.
Conveyor Belt Tracking Diagram: Visual Guide to Component Interaction
A conveyor belt tracking diagram serves as a crucial educational tool within this conveyor belt tracking guide, offering a clear visual representation of how each component contributes to the overall tracking process. Here’s a breakdown of the key elements depicted in the diagram and their interactions:
- Drive Pulley Alignment: The diagram illustrates the drive pulley’s position and its critical role in initiating the belt’s movement. Proper alignment here sets the tone for the belt’s path.
- Tail Pulley Adjustment: Shows the tail pulley’s adjustment mechanisms that can be used to influence the belt’s tracking at the opposite end of the conveyor.
- Idler Rollers’ Placement: Depicts how idler rollers support the belt’s load and their distribution along the conveyor frame, highlighting the importance of their level and alignment for smooth belt travel.
- Snub Rollers’ Influence: Visualizes the snub rollers’ proximity to the main pulleys and their role in increasing the belt’s contact area with the pulleys, which is vital for maintaining traction and aiding in tracking.
- Tracking Rollers’ Functionality: Demonstrates how tracking rollers can be adjusted to gently guide the belt back to its intended path, showcasing their pivotal role in fine-tuning belt alignment.
- Belt Tensioning Techniques: The diagram provides insight into the mechanisms used for tensioning the belt, ensuring it has enough grip on the pulleys and rollers without overstressing the system.
- Belt Cleaners’ Position: Highlights the placement of belt cleaners and their function in removing debris from the belt, which is essential for preventing tracking issues caused by material buildup.
- Conveyor Frame Integrity: Emphasizes the importance of a straight and well-aligned conveyor frame as the foundation upon which all other components rely for proper function and alignment.
- Interaction Overview: Offers a holistic view of how all these components work in concert to maintain the belt’s alignment, illustrating the dynamic nature of conveyor belt tracking and the necessity of a harmonious interaction between all parts.
This visual guide, as part of the conveyor belt tracking guide, not only aids in understanding the individual roles of each component but also underscores the importance of their coordinated interaction for effective belt tracking. By studying this diagram, individuals responsible for conveyor maintenance and operation can better diagnose and address tracking issues, leading to more efficient and reliable conveyor system performance.
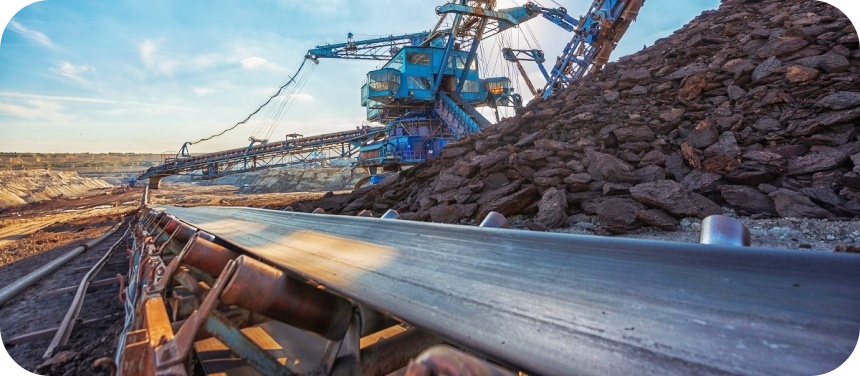
Setting Up Your Conveyor Belt Tracking System in the Conveyor Belt Tracking Guide
Achieving optimal performance from your conveyor system requires a well-executed setup of the conveyor belt tracking system. This crucial aspect of conveyor maintenance ensures the belt remains aligned, preventing unnecessary wear and downtime. This section of the conveyor belt tracking guide will walk you through a detailed, step-by-step process to establish a reliable tracking system for your conveyor belt.
Step-by-Step Conveyor Belt Alignment Procedure
Proper alignment is the cornerstone of effective conveyor belt tracking. The following steps are designed to guide you through the precise alignment of your conveyor belt:
- Initial Inspection: Start with a comprehensive examination of the conveyor’s structure to ensure it is level and square. Any deviations can significantly impact belt tracking.
- Check Pulley Alignment: Inspect all pulleys to confirm they are parallel to each other and perpendicular to the conveyor’s frame. Misalignment here is a common culprit of tracking issues.
- Verify Roller Alignment: Ensure all rollers are correctly positioned and parallel to the conveyor’s longitudinal axis. Misaligned rollers can lead to the belt drifting off course.
- Tension Adjustment: Properly adjust the belt’s tension according to the manufacturer’s specifications. Incorrect tension is a frequent cause of tracking problems.
- Belt Installation: Carefully install the belt, ensuring it is laid out flat without any twists. Initial misalignments can lead to long-term tracking challenges.
- Run the Conveyor: Operate the conveyor at a reduced speed to observe the belt’s behavior. Look for any signs of drifting or misalignment.
- Make Incremental Adjustments: If the belt drifts, apply small adjustments to the pulleys or rollers on the opposite side to gently guide the belt back to its intended path.
- Re-Inspect and Adjust: Continue monitoring the belt’s path, making additional adjustments as necessary. Achieving perfect alignment may require several attempts.
- Final Check: Once aligned, perform a comprehensive check under full operational load to ensure the belt maintains its path under typical working conditions.
How to Adjust a Conveyor Belt to Run Straight: Practical Tips and Adjustments
Ensuring your conveyor belt runs straight is pivotal for operational efficiency. Here are practical tips and adjustments to maintain optimal belt alignment:
- Snub Roller Technique: Utilize snub rollers near the conveyor’s ends to make fine adjustments to the belt’s tracking.
- Tension Method: Increase tension on the side the belt drifts towards to help realign it to the center.
- Debris Removal: Regularly clear the conveyor path of debris that could cause the belt to misalign.
- Component Lubrication: Ensure rollers and pulleys are adequately lubricated to minimize friction that may lead to tracking issues.
- Load Distribution: Maintain even distribution of the load across the belt to prevent tracking problems caused by uneven weight distribution.
- Wear Monitoring: Regularly inspect the belt for wear or damage, as these conditions can affect tracking.
- Manufacturer Guidelines: Always refer to the conveyor manufacturer’s guidelines for specific adjustment techniques.
- Expert Training: Ensure that personnel responsible for adjustments are well-trained in conveyor belt tracking principles.

Utilizing a Conveyor Belt Tracking Guide PDF for Detailed Instructions
A comprehensive conveyor belt tracking guide PDF is an invaluable resource for detailed tracking instructions. Here’s how it can assist in setting up your tracking system:
- Detailed Guidance: The guide provides in-depth instructions for each step of the alignment and tracking process.
- Visual Aids: It includes diagrams and images to help visualize complex procedures and component relationships.
- Troubleshooting: A dedicated section for troubleshooting helps quickly identify and resolve common tracking issues.
- Maintenance Recommendations: The guide outlines maintenance routines to proactively prevent tracking problems.
- Safety Measures: Emphasizes critical safety precautions to protect maintenance personnel during adjustments.
- Tool and Equipment Lists: Offers comprehensive lists of necessary tools and equipment for adjustments and repairs.
- System Customization: Provides tips for tailoring tracking procedures to specific conveyor system types.
- Current Information: The digital format allows for easy updates, ensuring you have access to the latest tracking techniques.
- Easy Access: Being digitally available, the guide ensures that maintenance teams can access the information anytime, anywhere.
By following these guidelines and utilizing the resources provided in the conveyor belt tracking guide PDF, you can establish a robust and reliable conveyor belt tracking system, ensuring the longevity and efficiency of your conveyor operations.
Advanced Conveyor Belt Tracking Guide Solutions
In the realm of material handling, ensuring the smooth and efficient operation of conveyor systems is paramount. This section serves as a comprehensive conveyor belt tracking guide, delving into the sophisticated realm of advanced conveyor belt tracking solutions. Our focus is on the pivotal role of automatic systems and conveyor belt tracking rollers, aiming to enhance understanding and application of these critical components.
Introduction to Automatic Conveyor Belt Tracking Systems
Automatic conveyor belt tracking systems represent a significant leap in conveyor technology. These systems are engineered to automatically adjust the path of the conveyor belt, ensuring optimal alignment without manual intervention. Here are some of the key benefits they offer:
- Reduced Downtime: By maintaining optimal belt alignment, these systems minimize the risk of belt misalignment issues, leading to less downtime for adjustments and repairs.
- Increased Belt Lifespan: Proper alignment reduces uneven wear on the belt, significantly extending its service life.
- Enhanced Safety: Minimizing the risk of belt slippage and misalignment reduces potential safety hazards for workers around the conveyor.
- Improved Productivity: With fewer stoppages for belt corrections, the overall efficiency and throughput of the conveyor system are enhanced.
- Lower Maintenance Costs: The automatic adjustment reduces the need for frequent manual maintenance, leading to cost savings.
- Energy Efficiency: Properly aligned belts require less energy to operate, contributing to energy savings and sustainability goals.
- Protection of Conveyor Infrastructure: By preventing belt wander, the system protects the conveyor frame and structure from damage.
- Adaptability: These systems can adapt to varying operational conditions, ensuring consistent performance under different loads and speeds.
- Advanced Monitoring: Many automatic tracking systems come with integrated monitoring capabilities, providing real-time data on belt performance and health.
The Role of Conveyor Belt Tracking Rollers
Conveyor belt tracking rollers play a crucial role in maintaining the alignment of the conveyor belt, ensuring it runs true along its intended path. Here are several key points highlighting their importance:
- Precision Alignment: These rollers are precisely engineered to guide the belt back to its correct path, preventing drift and misalignment.
- Versatility: Tracking rollers are suitable for various types of conveyor belts and operational environments, making them a versatile solution.
- Low Friction Operation: Designed to minimize friction, these rollers contribute to smoother belt movement and reduced wear.
- Easy Installation and Maintenance: Conveyor belt tracking rollers are typically designed for easy installation and minimal maintenance, enhancing system uptime.
- Durability: Constructed from robust materials, these rollers are built to withstand harsh operational conditions and prolonged use.
- Customization: Tracking rollers can be customized to meet specific conveyor requirements, ensuring optimal performance.
- Self-Cleaning Mechanism: Many models feature self-cleaning designs, preventing the buildup of debris that could affect tracking performance.
- Cost-Effectiveness: By extending the life of the conveyor belt and reducing maintenance needs, tracking rollers offer a cost-effective solution for maintaining belt alignment.
Incorporating advanced conveyor belt tracking solutions, as outlined in this comprehensive conveyor belt tracking guide, is essential for the optimal performance and longevity of conveyor systems. These technologies not only enhance operational efficiency but also contribute to safety and cost savings, making them invaluable in modern material handling applications.
Troubleshooting Common Conveyor Belt Tracking Issues: A Conveyor Belt Tracking Guide
Navigating through the complexities of conveyor belt tracking issues can be daunting. This section of our conveyor belt tracking guide is dedicated to troubleshooting common problems that may arise, ensuring your system remains operational and efficient.
Conveyor Belt Tracking to One Side: Causes and Fixes
When a conveyor belt consistently tracks to one side, it can lead to uneven wear, potential damage to the belt and system, and operational inefficiencies. Here are seven common causes and their respective fixes:
- Misaligned Rollers or Pulleys: Ensure all rollers and pulleys are properly aligned. Misalignment can cause the belt to track off-center.
- Uneven Loading: Ensure material is centrally loaded onto the belt. Uneven loading can cause the belt to drift to one side.
- Worn or Damaged Rollers: Inspect rollers for wear or damage. Replace any defective rollers to prevent them from causing the belt to misalign.
- Incorrect Belt Tension: Adjust the tension of the belt according to manufacturer specifications. Over or under-tensioning can lead to tracking issues.
- Buildup of Material: Clean any buildup of material on rollers, pulleys, and along the conveyor path that may be causing the belt to track incorrectly.
- Belt Splice Issues: Inspect the belt splice for accuracy and integrity. A poorly executed splice can cause the belt to track to one side.
- Structural Issues: Check the conveyor frame and structure for deformities or damage that could be influencing belt tracking. Make necessary repairs or adjustments.
Conveyor Belt Tracking Troubleshooting: Identifying and Solving Frequent Problems
Beyond tracking to one side, there are several other frequent problems that can affect conveyor belt tracking. Here are eight points for comprehensive troubleshooting:
- Belt Slippage: Check for worn pulleys, inadequate tension, or load imbalances that can cause slippage. Address these issues to restore proper tracking.
- Edge Wear: Inspect the belt edges for wear, which can indicate tracking issues. Identify the cause of the edge wear and rectify it to prevent further damage.
- Seized Rollers: Ensure all rollers rotate freely. Replace any seized rollers that could be hindering proper belt movement.
- Incorrect Belt Installation: Verify that the belt has been installed correctly, with the tension and tracking set according to the manufacturer’s guidelines.
- Environmental Factors: Consider environmental factors such as humidity, temperature, and exposure to chemicals that might affect the belt’s tracking.
- Belt Stretching: Monitor the belt for stretching, which can occur over time and affect tracking. Adjust tension or replace the belt if necessary.
- Mechanical Issues: Inspect the conveyor for any mechanical issues, such as loose components or damaged parts, that could be affecting belt tracking.
- Regular Audits: Conduct regular audits of the conveyor system to identify and address any potential tracking issues before they escalate.
By following this comprehensive conveyor belt tracking guide for troubleshooting, you can effectively identify and solve common conveyor belt tracking issues, ensuring the longevity and efficiency of your conveyor system. Regular attention to these aspects will minimize downtime and maintain optimal operation.
Ready to enhance your operations? Contact us now!
Maintenance and Regular Checks: A Conveyor Belt Tracking Guide
Ensuring the longevity and efficiency of your conveyor system involves diligent maintenance and regular checks. This section of our conveyor belt tracking guide focuses on the essential practices for maintaining long-term conveyor belt tracking accuracy and keeping your system aligned over time.
Routine Maintenance: Tips for Ensuring Long-Term Conveyor Belt Tracking Accuracy
Routine maintenance is crucial for the longevity and efficiency of conveyor systems. Here are eight key tips to maintain conveyor belt tracking accuracy:
- Regular Inspections: Conduct thorough inspections of the conveyor belt and its components regularly to identify and address potential issues early.
- Cleanliness: Keep the conveyor belt and surrounding area clean from debris and material spillage that can affect belt tracking.
- Lubrication: Ensure that all moving parts, especially rollers and pulleys, are adequately lubricated to prevent sticking or seizing that can lead to misalignment.
- Tension Monitoring: Monitor and maintain proper belt tension, as over-tensioning or under-tensioning can cause tracking issues.
- Wear and Tear Checks: Regularly check for wear and tear on the belt and replace parts as necessary to prevent tracking problems caused by damaged components.
- Alignment Checks: Periodically verify the alignment of the conveyor structure and adjust as needed to ensure straight and true operation.
- Training Rollers Adjustment: Inspect and adjust training rollers to ensure they are effectively guiding the belt back to the correct path.
- Record Keeping: Maintain detailed records of maintenance activities, issues encountered, and corrective actions taken to help identify patterns and prevent future problems.
Conveyor Belt Tracking Adjustment: Keeping Your System Aligned Over Time
Keeping your conveyor system aligned over time is critical for operational efficiency and belt longevity. Here’s how to maintain alignment:
- Initial Alignment: After installation or major repairs, ensure the conveyor belt is properly aligned before commencing operation.
- Use of Tracking Sensors: Implement tracking sensors and automatic alignment systems that continuously monitor and adjust the belt’s path as needed.
- Regular Re-Calibration: Periodically re-calibrate automatic tracking systems to ensure they are functioning correctly and making accurate adjustments.
- Respond to Changes: Be vigilant and responsive to changes in the conveyor’s operation, such as increased load, which may necessitate alignment adjustments.
- Professional Assessments: Consider periodic assessments by conveyor system specialists who can provide expert insights and adjustments for optimal alignment.
By adhering to these maintenance and regular check practices outlined in this conveyor belt tracking guide, you can ensure the long-term accuracy and efficiency of your conveyor belt tracking. Regular attention and proactive adjustments are key to preventing downtime and extending the life of your conveyor system.

Free Resources and Conveyor Belt Tracking Guide for Effective
In the quest for mastering conveyor belt systems, access to quality resources can significantly ease the learning curve. This section of our comprehensive conveyor belt tracking guide is dedicated to pointing you towards free resources and guides that can enhance your understanding and skills in conveyor belt tracking.
Availability of Free Conveyor Belt Tracking Guides and Where to Find Them
Navigating the world of conveyor belt systems can be made easier with the right resources. Here are eight points highlighting the availability of free conveyor belt tracking guides and where to find them:
- Manufacturer Websites: Many conveyor belt manufacturers offer free guides and resources on their websites, providing valuable insights into proper installation, maintenance, and troubleshooting.
- Industry Associations: Organizations such as the Conveyor Equipment Manufacturers Association (CEMA) often publish free guidelines and technical papers on conveyor belt tracking and maintenance.
- Online Forums and Communities: Platforms like LinkedIn groups or specialized forums can be rich sources of shared documents and personal experiences related to conveyor belt tracking.
- Educational Institutions: Universities and technical colleges with a focus on engineering or material handling may offer free resources or publish student theses on conveyor technology online.
- Government Safety Agencies: Bodies like OSHA in the United States provide guidelines on conveyor safety, which include aspects of belt tracking and maintenance.
- Trade Shows and Conferences: Attending industry events can provide access to free materials, workshops, and seminars on conveyor belt tracking and maintenance.
- YouTube Channels: Several engineering and manufacturing channels on YouTube offer tutorials and visual guides on conveyor belt tracking, free of charge.
- Library and Public Resources: Public libraries and online digital libraries may have access to textbooks, guides, and periodicals on conveyor systems and belt tracking.
Recommended Reading: Conveyor Belt Tracking PDFs and Diagrams for In-Depth Understanding
For those seeking a deeper dive into the intricacies of conveyor belt tracking, here are eight recommended readings, including PDFs and diagrams:
- Conveyor Belt Installation, Maintenance & Troubleshooting Guide: Published by leading manufacturers, this guide covers all aspects of conveyor belt care, including tracking.
- “Belt Conveyors for Bulk Materials“: A publication by CEMA, this book includes a chapter dedicated to belt tracking and alignment.
- The Foundations™ for Conveyor Safety: This comprehensive book from Martin Engineering covers safety aspects of conveyor design, including belt tracking.
- Conveyor Belt Tracking Basics: A detailed PDF guide that explains the fundamentals of conveyor belt tracking and how to troubleshoot common issues.
- Effective Conveyor Belt Tracking: Best Practices & Methodologies: This document delves into various techniques and practices for ensuring optimal belt tracking.
- Conveyor Belt Tracking Adjustment Tension, Alignment,…: A practical guide focusing on how to adjust and align conveyor belts for proper tracking.
- Design and Installation of Conveyor Belt Tracking Systems: This guide explores the design considerations and installation practices for tracking systems.
- Troubleshooting Conveyor Belt Tracking Issues: A targeted guide that provides solutions to common tracking problems, complete with diagrams and step-by-step instructions.
Leveraging these free resources and recommended readings can significantly enhance your understanding and capability in managing conveyor belt tracking challenges. Whether you’re a novice or an experienced professional, these guides offer valuable insights into achieving and maintaining optimal conveyor belt performance.
Case Studies and Real-World Applications in Conveyor Belt Tracking Guide
Delving into the practical aspects of conveyor belt systems, this section of our conveyor belt tracking guide showcases real-world applications and case studies. These narratives not only highlight success stories but also distill valuable lessons from troubleshooting conveyor belt tracking issues across various industries.
Success Stories: How Effective Conveyor Belt Tracking Improved Operations
- Mining Industry Breakthrough: A leading mining company faced frequent belt misalignment, leading to operational downtimes and safety hazards. Implementing an advanced conveyor belt tracking system reduced downtime by 70% and significantly improved safety standards.
- E-commerce Giant Optimization: An e-commerce fulfillment center struggling with package misalignment and sorting inefficiencies integrated a state-of-the-art tracking guide, resulting in a 40% increase in package sorting accuracy and a 30% boost in overall efficiency.
- Food Processing Precision: A food processing plant dealing with contamination due to belt misalignment installed custom-designed tracking rollers, leading to a 100% elimination of contamination issues and a 20% increase in production speed.
- Manufacturing Sector Efficiency: A manufacturing plant experiencing product damage due to belt misalignment incorporated a comprehensive conveyor belt tracking guide, resulting in a 90% reduction in product damage and a 15% increase in production rates.
- Recycling Facility Revamp: A recycling facility plagued by frequent belt derailments and material spillage adopted an innovative tracking solution, leading to a 60% reduction in maintenance costs and a 25% increase in material processing efficiency.
- Airport Baggage Handling System: An airport upgraded its baggage handling system with advanced belt tracking technology, significantly reducing baggage mishandling incidents and improving passenger satisfaction.
Lessons Learned from Conveyor Belt Tracking Troubleshooting in Various Industries
- Proactive Maintenance is Key: Regular inspections and maintenance preempt major tracking issues, ensuring continuous operation and extending belt life.
- Customization for Specific Needs: Tailoring tracking solutions to the specific needs and challenges of an operation can significantly enhance efficiency and reduce downtime.
- Training and Education: Educating staff on the fundamentals of conveyor belt tracking and troubleshooting can empower them to address minor issues promptly, preventing escalation.
- The Importance of Quality Components: Investing in high-quality belts, rollers, and tracking systems pays off in the long run through reduced maintenance costs and downtime.
- Environmental Considerations: Factors such as humidity, temperature, and exposure to chemicals can affect belt tracking; solutions should be adaptable to environmental conditions.
- Technological Integration: Incorporating advanced technologies like sensors and automated tracking systems can lead to significant improvements in tracking accuracy and operational efficiency.
- Collaboration with Experts: Partnering with conveyor belt tracking experts for regular audits and consultations can provide fresh insights and innovative solutions to recurring problems.
These case studies and lessons learned underscore the critical role of effective conveyor belt tracking in enhancing operational efficiency, safety, and profitability across various industries. By adhering to the principles outlined in this comprehensive conveyor belt tracking guide, organizations can achieve optimal performance and longevity from their conveyor systems.
FAQs about Conveyor Belt Tracking Guide
Conveyor belt tracking is governed by a set of best practices and rules designed to ensure that the belt operates efficiently and safely. The primary rule is to ensure that the conveyor belt and all its components are correctly aligned and in good working condition. This includes ensuring that the frame, rollers, pulleys, and the belt itself are level and square to the direction of belt travel. Another crucial rule is to maintain proper belt tension, as both over-tensioning and under-tensioning can lead to tracking issues. Regular inspections and maintenance are also vital to promptly identify and correct any misalignments or wear and tear that could affect tracking. Additionally, the loading of materials onto the belt should be centered to prevent uneven distribution, which can cause the belt to track off to one side. Following these rules helps in minimizing wear on the belt and conveyor components, reducing downtime, and ensuring the safety of the operation.
Tracking a conveyor belt involves adjusting it so that it runs straight and true along the conveyor’s centerline. If the belt drifts to one side or the other, the tracking adjustments depend on the direction of the drift. Generally, if the belt is drifting to the right side of the conveyor (from the perspective of looking along the direction of the belt’s travel), you would adjust the idlers or tracking mechanisms on the right side in a way that encourages the belt to move back towards the center. Conversely, if the belt drifts to the left, adjustments should be made on the left side. It’s important to make small adjustments and observe the belt’s response, as over-adjusting can cause the belt to drift in the opposite direction. The goal is to achieve a balance where the belt remains centered during operation.
Snub rollers are used to increase the angle of wrap on the drive pulley, enhancing the pulley’s grip on the belt. They can also be instrumental in belt tracking. To track a belt using snub rollers, you adjust the position of the snub rollers in a way that gently guides the belt back to its correct path. This is typically done by slightly tilting the snub roller on the side where the belt is drifting away. For example, if the belt is drifting towards the left, the left side snub roller can be adjusted slightly forward, encouraging the belt to move back to the right. It’s crucial to make these adjustments in small increments and monitor the belt’s response to avoid over-correction. Properly adjusted snub rollers can help maintain the belt’s alignment without causing undue stress or damage to the belt.
A belt tracking mechanism refers to the system or components designed to keep the conveyor belt aligned and running straight on the conveyor. This can include a variety of parts such as idlers, tracking rollers, snub rollers, and tensioners, which can be adjusted to influence the belt’s path. Some conveyor systems also incorporate advanced tracking mechanisms like pneumatic or hydraulic trackers, and electronic sensors that detect belt misalignment and automatically adjust the conveyor components to correct the belt’s path. The choice of tracking mechanism depends on the conveyor system’s design, the type of material being transported, and the operational environment. Effective belt tracking mechanisms are crucial for preventing belt drift, reducing wear and tear on the conveyor system, and ensuring efficient and safe operation.
Belt tracking ensures that the conveyor belt runs straight and stays centered on the pulleys. Key principles include maintaining proper tension, ensuring that the frame and pulleys are aligned, and keeping the system clean. Proper installation is critical, with all components aligned and squared. Regular inspections help identify and correct misalignments or wear that can lead to tracking issues. Tracking devices like crowned pulleys and tracking idlers assist in keeping the belt centered. Small, incremental adjustments are preferred over large changes, as even slight misalignments can significantly affect tracking. Consistent load distribution and preventive maintenance are also crucial.
Guide rollers are used in conveyor belt systems to help keep the belt aligned and prevent it from drifting off course. These rollers are typically mounted along the sides of the conveyor belt frame. They come into contact with the edges of the belt, providing lateral support and guidance. Guide rollers are especially useful in applications where the belt may be subjected to side loads or varying loads that can cause misalignment. By maintaining contact with the belt, they help correct deviations and ensure smooth, reliable operation, reducing wear and tear on the belt and other components.
Calculating conveyor belt tension involves determining the necessary force to move the belt and its load. Key factors include the belt’s weight, the weight of the conveyed material, the length of the conveyor, and friction between the belt and the rollers. The formula typically used is T = (F * L) / (2 * π * r), where T is the tension, F is the force required to move the belt, L is the length of the conveyor, and r is the radius of the drive pulley. Manufacturer guidelines and tension gauges can provide more precise tension settings for specific belts and applications.
To get a conveyor belt to run straight, start by ensuring the frame and all components are level and aligned. Adjust the tension so it is even across the belt’s width. Use tracking devices like crowned pulleys and snub rollers to help guide the belt. Make small, incremental adjustments to the tracking devices while the conveyor is running, observing the belt’s movement and correcting any drift. Regularly inspect and maintain the belt and system components to prevent buildup and wear, which can cause misalignment. Consistently load the belt evenly to avoid side forces that can affect tracking.
How tAligning a belt conveyor involves several steps. First, ensure the conveyor frame is level and squared. Check that all pulleys and rollers are aligned parallel to each other and perpendicular to the belt centerline. Adjust the tension to be even across the belt’s width. Use a level and straightedge to verify alignment, making necessary adjustments to pulleys and rollers. Install and correctly position tracking devices like crowned pulleys and snub rollers. Run the conveyor at a slow speed to observe the belt’s movement, making small adjustments as needed to achieve proper alignment.
Methods of belt alignment include manual adjustments, use of tracking devices, and regular maintenance. Manual adjustments involve loosening and repositioning pulleys and rollers to ensure they are parallel and perpendicular to the belt. Tracking devices such as crowned pulleys, snub rollers, and pivoting tracking idlers help guide the belt and correct alignment issues. Regular maintenance involves inspecting and cleaning the system, checking for wear and damage, and ensuring proper belt tension. Advanced methods may include the use of laser alignment tools for precise measurements and adjustments, ensuring optimal belt tracking and performance.
Last Updated on August 2, 2024 by Jordan Smith
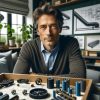
Jordan Smith, a seasoned professional with over 20 years of experience in the conveyor system industry. Jordan’s expertise lies in providing comprehensive solutions for conveyor rollers, belts, and accessories, catering to a wide range of industrial needs. From initial design and configuration to installation and meticulous troubleshooting, Jordan is adept at handling all aspects of conveyor system management. Whether you’re looking to upgrade your production line with efficient conveyor belts, require custom conveyor rollers for specific operations, or need expert advice on selecting the right conveyor accessories for your facility, Jordan is your reliable consultant. For any inquiries or assistance with conveyor system optimization, Jordan is available to share his wealth of knowledge and experience. Feel free to reach out at any time for professional guidance on all matters related to conveyor rollers, belts, and accessories.