Diagnosis and Resolution Conveyor Belt Tracking Issues
Conveyor belt systems are the lifeline of a wide range of industries, from manufacturing and mining to airports and supermarkets. These systems facilitate the efficient transport of goods and materials over short to long distances within a facility. However, the smooth operation of a conveyor belt system hinges on proper alignment and tracking. Conveyor belt tracking issues can lead to significant operational disruptions, affecting the throughput and efficiency of the entire operation. Understanding and addressing these tracking issues is crucial for maintaining the operational efficiency of conveyor systems. Ensuring that the conveyor belt runs straight and true is a fundamental aspect of conveyor system maintenance, directly impacting productivity, safety, and the bottom line of businesses relying on these systems.
Conveyor Belt Tracking Principles
The Principle of Balanced Forces
A conveyor belt naturally seeks a position where all forces acting on it are balanced. This principle dictates that the belt will adjust its path to achieve equilibrium. Consequently, the alignment of the conveyor’s structural components—frames and pulleys—must be precise and robust to support the belt’s movement effectively. From installation, the initial setup is crucial as it sets the foundation for the belt’s tracking behavior.
Importance of Proper Alignment
Proper alignment of frames and pulleys is essential to ensure the belt follows a consistent path. Misalignment can lead to uneven distribution of forces, causing the belt to drift off course. This drift can result in increased wear and tear, reduced efficiency, and potential safety hazards. Therefore, ensuring that all components are perfectly aligned during installation helps prevent these issues and maintains smooth operation.
First Contact on Idlers
The belt’s movement is influenced by its initial contact with an idler. This first point of contact determines the belt’s subsequent path and tracking behavior. If the idler is misaligned, it can set the belt on a trajectory that leads to continuous tracking issues. Hence, the installation and alignment of idlers are critical in establishing a stable and predictable belt path.
Tracking Tolerance
In practice, conveyor belts have an allowable tracking tolerance of ± 25 mm. This means that minor deviations within this range are acceptable and do not pose significant risks to site operations. However, consistent monitoring and maintenance are necessary to ensure that the belt remains within this tolerance. Regular adjustments and inspections can help detect and correct any deviations before they escalate into more serious problems.
What Are Conveyor Belt Tracking Issues
Conveyor belt tracking issues refer to problems that arise when the belt does not run in a straight line on the conveyor system. These issues occur when the belt drifts from its intended path, leading to misalignment that can have a cascading effect on the entire conveyor system’s operation. Misalignment not only disrupts the flow of materials but can also cause significant damage to the belt and the conveyor structure, leading to costly downtime and repairs.
The impact of conveyor belt tracking problems extends beyond the immediate physical damage. Misalignment can lead to uneven wear on the belt and the conveyor rollers, premature belt failure, and even pose safety risks to operators due to the potential for material spillage and the creation of trip hazards. Furthermore, when the belt is not aligned correctly, the efficiency of the material handling process is compromised, which can affect the overall productivity of the operation.
conveyor belt tracking issues: belt damage, crooked splice, off-center loading, misaligned frame, improper tension, debris, pulley issues.
Identifying conveyor belt tracking issues early is crucial to maintaining the health and efficiency of the conveyor system. Here are five common signs that indicate tracking problems:
- Belt Drifts to One Side: One of the most obvious signs of a tracking issue is when the belt consistently drifts or moves to one side of the conveyor frame.
- Edges of the Belt are Frayed or Damaged: Misalignment can cause the edges of the belt to rub against the conveyor frame or other components, leading to fraying or damage.
- Material Spillage: When the belt does not track straight, materials can spill over the edges, creating safety hazards and requiring additional cleanup.
- Increased Wear on Rollers and Bearings: Misaligned belts can cause uneven wear on rollers and bearings, leading to premature failure and the need for replacement.
- Abnormal Noise: Unusual noises coming from the conveyor system, such as squealing or grinding, can indicate that the belt is not tracking correctly.
Addressing conveyor belt tracking issues promptly can prevent these symptoms from escalating into more significant problems, ensuring the conveyor system operates smoothly and efficiently.
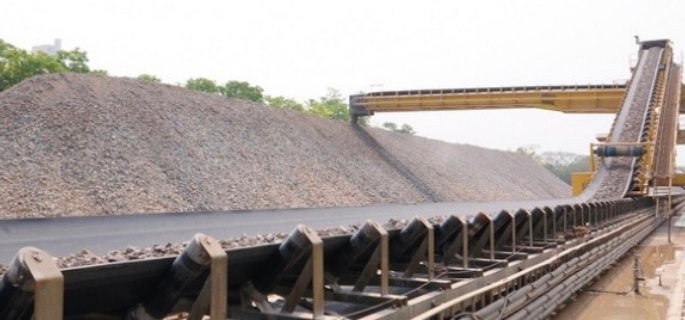
How to Diagnose and Fix Common Conveyor Belt Tracking Issues
Diagnosing and fixing common conveyor belt tracking issues involves a systematic approach. Here’s a step-by-step guide:
Diagnosing Conveyor Belt Tracking Issues
Visual Inspection:
- Inspect the entire length of the conveyor belt for signs of misalignment, damage, or uneven wear.
Check Belt Tension:
- Verify that the belt is neither too tight nor too loose. Uneven tension can cause the belt to drift.
Inspect Pulleys and Rollers:
- Ensure all pulleys and rollers are properly aligned and free of debris.
Observe Load Distribution:
- Check if the load is evenly distributed across the belt. Uneven loading can cause tracking issues.
Check for Contamination:
- Look for any dirt, debris, or buildup on the belt, rollers, and pulleys.
Inspect Belt Edges:
- Examine the edges of the belt for fraying or damage, which can indicate alignment problems.
Fixing Conveyor Belt Tracking Issues
Adjust Belt Tension:
- If the belt is too tight or too loose, adjust the tension according to the manufacturer’s specifications.
Align Pulleys and Rollers:
- Realign any misaligned pulleys and rollers to ensure they are parallel and square to the conveyor frame.
Clean the Conveyor System:
- Remove any debris or buildup from the belt, rollers, and pulleys. Regular cleaning prevents tracking issues.
Correct Load Distribution:
- Adjust the loading process to ensure the load is evenly distributed across the width of the belt.
Install Tracking Devices:
- Use tracking devices such as training idlers or belt positioners to help keep the belt aligned.
Check and Adjust the Belt Splice:
- Ensure the belt splice is properly aligned and in good condition. Misaligned splices can cause tracking problems.
Regular Maintenance:
- Implement a regular maintenance schedule to check and adjust the conveyor system, ensuring all components are in proper working order.
Common Tools and Techniques
Squaring the Belt:
- Ensure the belt is properly squared before installation. Use a square tool to measure and cut accurately.
Laser Alignment Tools:
- Utilize laser alignment tools for precise pulley and roller alignment.
Edge Guides:
- Install edge guides to keep the belt centered.
Training Idlers:
- Use training idlers that automatically adjust to correct belt misalignment.
By following these steps, you can diagnose and fix common conveyor belt tracking issues, ensuring smooth and efficient operation of your conveyor system. Regular inspections and maintenance are key to preventing tracking problems and prolonging the life of your conveyor belt.

Causes of Conveyor Belt Tracking Issues
Understanding the root causes of conveyor belt tracking problems is essential for diagnosing and correcting misalignment problems effectively. These issues can stem from a variety of factors, each affecting the belt’s ability to track along the center of the conveyor system. Here, we delve into the main causes leading to conveyor belt tracking issues and explain how each one impacts the belt’s alignment and overall system performance.
Belt Damage and Wear
Over time, conveyor belts can suffer from wear and tear due to continuous use, exposure to harsh environments, or carrying abrasive materials. Damage such as tears, cuts, or worn edges can disrupt the belt’s balance and cause it to veer off its intended path. Additionally, worn areas may create uneven surfaces that affect the belt’s contact with rollers and pulleys, leading to misalignment.
Incorrectly Installed or Aligned Pulleys
Pulleys play a critical role in guiding and supporting the conveyor belt, ensuring it runs straight along the conveyor’s length. Incorrectly installed or misaligned pulleys can cause the belt to track off-center. This misalignment might be due to improper installation, where pulleys are not parallel to each other or perpendicular to the conveyor frame. Over time, pulleys can also become misaligned due to operational stresses or wear, exacerbating conveyor belt tracking issues.
Material Buildup and Debris
Accumulation of material and debris on the conveyor belt, pulleys, or rollers can significantly impact belt tracking. Material buildup can create uneven surfaces on the belt or pulleys, leading to an imbalance that causes the belt to drift. Debris can also obstruct the smooth rotation of rollers and pulleys, further contributing to tracking problems. Regular cleaning and maintenance are crucial to prevent material buildup from causing conveyor belt tracking issues.
Off-Center Loading of Goods
The way goods are loaded onto the conveyor belt can also lead to tracking problems. Off-center loading can exert uneven forces on the belt, causing it to misalign. For instance, if materials are consistently loaded onto one side of the belt, it can stretch or wear unevenly, leading to a natural drift towards the overloaded side. Ensuring that materials are evenly distributed and centered as they are loaded onto the belt is vital for maintaining proper alignment.
Each of these causes can independently or collectively contribute to conveyor belt tracking problems, disrupting the efficiency and safety of conveyor operations. Identifying and addressing these root causes is crucial for preventing misalignment and ensuring the longevity and reliability of conveyor systems. Regular inspections, proper installation and maintenance, and adherence to operational best practices can mitigate the risk of conveyor belt tracking issues, maintaining optimal performance and productivity.
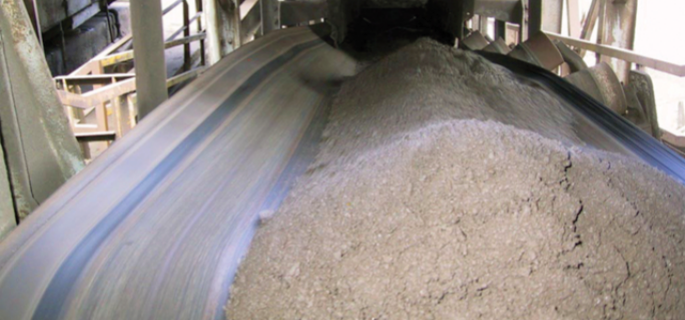
Conveyor Belt Tracking Solutions
Addressing conveyor belt tracking problems effectively requires a combination of manual adjustments, regular maintenance, and, in some cases, the integration of advanced automatic tracking systems. By implementing these solutions, operations can minimize downtime, reduce wear and tear on the conveyor system, and improve overall efficiency. Here’s how to tackle conveyor belt tracking issues with both manual and automatic solutions.
Adjusting the Conveyor Belt to Run Straight
Manual adjustments are often the first step in correcting conveyor belt tracking issues. These adjustments can be made by following a systematic approach to realign the belt and ensure it runs straight along the conveyor’s path. Here is a step-by-step guide on making these adjustments:
- Inspect the Conveyor Frame and Pulleys: Ensure that the conveyor frame is level and the pulleys are aligned correctly. Misalignment here can cause the belt to track off-center.
- Adjust the Tension: Incorrect tension can lead to belt slippage or tracking problems. Adjust the tension so that the belt is tight enough to avoid slippage but not so tight that it causes excessive wear.
- Reposition the Rollers and Idlers: Misaligned rollers and idlers can steer the belt off its intended path. Adjust these components so they are square with the frame and parallel to each other.
- Check for Debris and Clean Regularly: Remove any debris that might be causing the belt to misalign. Regular cleaning of the belt and components can prevent material buildup that leads to tracking issues.
The importance of regular conveyor belt inspections and maintenance cannot be overstated. Routine checks allow for the early detection of potential problems and the opportunity to make adjustments before significant issues arise. This proactive approach can save time and resources in the long run.
Automatic Conveyor Belt Tracking Systems
As technology advances, more operations are turning to automatic conveyor belt tracking systems as a solution to conveyor belt tracking issues. These systems use sensors and control mechanisms to detect misalignment and automatically adjust the belt’s position to keep it running straight. Here are some benefits of using automatic systems over manual adjustments:
- Consistency and Precision: Automatic systems provide consistent and precise adjustments that can be difficult to achieve manually. They continuously monitor the belt’s position and make real-time adjustments to maintain proper alignment.
- Reduced Downtime: By automatically correcting misalignment, these systems can reduce the downtime associated with manual adjustments and tracking issues. This leads to increased productivity and efficiency.
- Lower Maintenance Costs: Automatic tracking systems can extend the life of the conveyor belt and reduce wear on other components, leading to lower maintenance costs over time.
- Enhanced Safety: Reducing the need for manual adjustments decreases the risk of injuries associated with maintenance activities. Automatic systems provide a safer solution for maintaining belt alignment.
Implementing automatic conveyor belt tracking systems, alongside regular inspections and maintenance, offers a comprehensive approach to solving conveyor belt tracking issues. By combining the reliability of manual adjustments with the precision and efficiency of automatic systems, operations can ensure their conveyor belts run smoothly and effectively, minimizing the impact of tracking issues on their overall productivity.
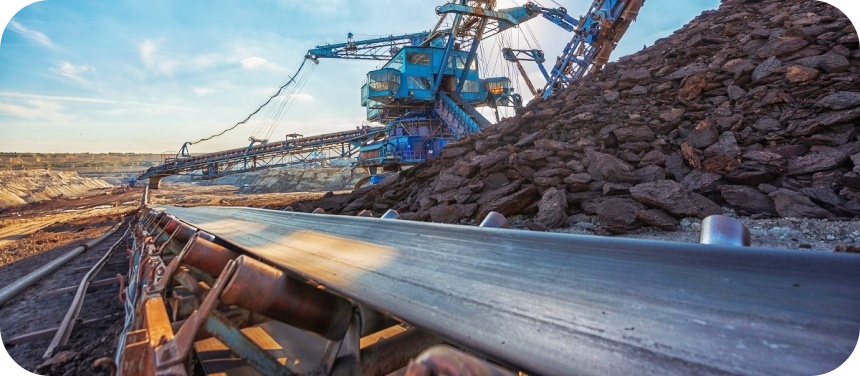
Preventive Measures to Avoid Conveyor Belt Tracking Issues
Preventive measures are crucial in mitigating conveyor belt tracking issues before they escalate into more significant problems that can disrupt operations. A proactive approach involving regular maintenance, inspection, and adherence to proper installation and alignment procedures can significantly reduce the incidence of tracking issues. Here’s how to implement these preventive measures effectively.
Regular Maintenance and Inspection
Implementing a preventive maintenance program is essential for the longevity and efficiency of conveyor belt systems. This program should include routine checks and servicing to ensure all components are in optimal condition and functioning correctly. Here’s how to implement such a program:
- Schedule Regular Inspections: Set a regular schedule for inspecting the conveyor system. This could be daily, weekly, or monthly, depending on the operation’s scale and the system’s usage intensity.
- Focus on Key Components: During inspections, pay close attention to the belt, pulleys, and rollers, as these are critical to proper belt tracking. Look for signs of wear, damage, or misalignment.
- Document Inspections and Maintenance: Keep records of all inspections, maintenance activities, and repairs. This documentation can help identify patterns or recurring issues, facilitating more targeted interventions.
Proper Installation and Alignment
Correct installation and alignment of conveyor belts and their components are foundational to preventing tracking issues. Misalignment from the outset can lead to chronic problems that are difficult to correct later. Here are guidelines for ensuring proper installation and alignment:
- Follow Manufacturer’s Guidelines: Always adhere to the installation instructions provided by the conveyor system’s manufacturer. These guidelines are designed to ensure that every component is correctly positioned and aligned.
- Use Alignment Tools: Utilize tools and technologies designed for conveyor alignment, such as laser alignment tools, to ensure precision. These tools can help achieve the correct alignment of pulleys and the conveyor frame.
- Refer to Conveyor Belt Alignment Procedure PDFs: Many manufacturers and industry organizations provide detailed PDF guides on proper conveyor belt alignment procedures. These documents offer step-by-step instructions and best practices for ensuring your conveyor belt is correctly installed and aligned from the start.
- Train Maintenance Staff: Ensure that those responsible for installation and maintenance are adequately trained in conveyor belt alignment techniques. Proper training helps prevent errors that could lead to tracking issues.
By implementing regular maintenance and inspection routines and ensuring proper installation and alignment, operations can significantly reduce the risk of conveyor belt tracking issues. These preventive measures not only extend the life of the conveyor system but also enhance safety and efficiency, contributing to smoother, more reliable operations.
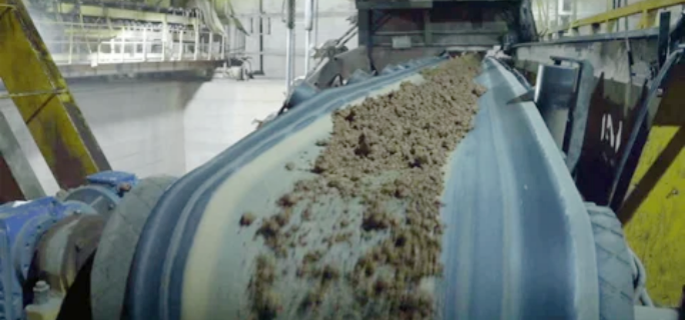
Advanced Solutions and Technologies
In the quest to solve conveyor belt tracking issues, the industry has seen significant advancements in technology and design. These innovations not only address current tracking challenges but also pave the way for more efficient, reliable conveyor systems in the future. Here, we explore some of the advanced solutions and technologies that are changing the landscape of conveyor belt tracking.
Specialty Conveyors and Modular Systems
One of the most notable advancements is the development of specialty conveyors and modular conveyor systems. These systems are designed with flexibility and precision in mind, allowing for easy adjustments and modifications to accommodate various materials and operational requirements. Specialty conveyors often come equipped with built-in tracking capabilities, reducing the likelihood of misalignment and the associated conveyor belt tracking issues. Modular systems, on the other hand, offer the advantage of interchangeable parts and sections, making it simpler to replace or upgrade components that may contribute to tracking problems.
Impact of Innovative Materials and Designs on Tracking Stability
The use of innovative materials and designs has also had a significant impact on improving conveyor belt tracking stability. For instance, belts made from new, more durable materials can withstand harsher operating conditions without stretching or warping, which are common causes of misalignment. Additionally, the introduction of belts with unique surface patterns and profiles can enhance grip and traction on pulleys and rollers, further stabilizing the belt’s path.
Engineers and designers are continually exploring new materials and structural designs that reduce the weight of conveyor components, decrease friction, and increase the overall efficiency of the system. These innovations not only address conveyor belt tracking issues but also contribute to energy savings and extended equipment life.
Discussion on the Future of Conveyor Belt Tracking Technologies
Looking ahead, the future of conveyor belt tracking technologies appears promising, with several areas of potential breakthroughs. Artificial intelligence (AI) and machine learning (ML) are beginning to make their way into conveyor system design and operation, offering the possibility of predictive maintenance and real-time adjustments based on continuous monitoring of belt behavior and conditions. This could lead to systems that automatically adjust for optimal tracking without human intervention.
Furthermore, the integration of Internet of Things (IoT) devices and sensors into conveyor systems can provide detailed data on the conveyor’s performance, including tracking accuracy. This data can be used to fine-tune the system for better alignment and to predict when maintenance or adjustments are needed, thereby preventing downtime and reducing the incidence of conveyor belt tracking issues.
As these advanced solutions and technologies continue to evolve, the industry can expect to see conveyor systems that are not only more reliable and efficient but also easier to maintain and adjust. This progress will significantly reduce the challenges associated with conveyor belt tracking problems, ensuring smoother operations and longer-lasting conveyor systems.
Troubleshooting Common Conveyor Belt Tracking Issues
Conveyor belt tracking issues can lead to a variety of operational challenges, including belts that track to one side, material spillage, carryback, seized rollers, and belt slippage. Addressing these problems promptly can prevent further damage and ensure the conveyor system operates efficiently. Here’s how to troubleshoot some of these common problems.
Conveyor Belt Tracking to One Side
When a conveyor belt consistently tracks to one side, it can cause uneven wear on the belt and the conveyor structure, leading to premature failure. Causes of this issue often include misaligned rollers or pulleys, improper belt tension, or an unevenly loaded belt. To fix belts that track to one side, ensure that all rollers and pulleys are properly aligned and that the belt tension is adjusted correctly. Additionally, make sure that the material is loaded centrally on the belt to prevent uneven weight distribution.
Material Spillage and Carryback
Material spillage and carryback can create safety hazards, increase maintenance requirements, and lead to conveyor belt tracking problems. Solutions for preventing material loss and ensuring clean operation include installing skirt boards along the edges of the conveyor belt to contain the material, using belt cleaners to remove material sticking to the belt, and ensuring proper loading zone design to minimize spillage. Regular inspections and maintenance of these components are crucial to prevent material spillage and carryback.
Seized Rollers and Belt Slippage
Seized rollers can cause the conveyor belt to mistrack, wear unevenly, and even tear, while belt slippage indicates a lack of proper tension or grip between the belt and pulleys. To identify issues with rollers and belt tension, inspect the conveyor for any rollers that do not rotate freely and adjust the tensioning devices to ensure the belt is tight enough to prevent slippage but not so tight as to cause excessive wear. Replacing seized rollers and ensuring proper belt tension can significantly reduce the risk of conveyor belt tracking issues and belt slippage.
Troubleshooting these common problems need to follow conveyor belt tracking theory to identifying the root causes of conveyor belt tracking issues and implementing the appropriate fixes. Regular inspections, proper installation and alignment, and timely maintenance are key to preventing these issues from affecting the efficiency and longevity of conveyor systems. By addressing these challenges proactively, operations can minimize downtime, reduce maintenance costs, and ensure a smooth, efficient conveyor system.
FAQs about Conveyor Belt Tracking Issues
How do you fix a conveyor belt tracker?
Fixing a conveyor belt tracker involves several steps aimed at identifying and correcting misalignments that cause the belt to drift off its intended path. The first step is to inspect the conveyor for any visible signs of misalignment or damage to the belt, rollers, or frame. If the conveyor frame is not level or square, adjustments should be made to realign it. Pulleys and rollers should be checked to ensure they are properly aligned and rotating freely. Tension on the belt is another critical factor; too much or too little tension can lead to tracking issues. Adjusting the tension to the manufacturer’s specifications can often correct tracking problems. Additionally, ensuring that the belt is loaded centrally can prevent uneven weight distribution from pulling the belt off track. Regular maintenance and cleaning to remove debris and buildup on the belt and pulleys can also prevent tracking issues. In some cases, installing tracking devices or guides may be necessary to keep the belt aligned. It’s important to follow a systematic approach and make adjustments gradually, checking the belt’s alignment after each adjustment.
The belt tracking problem refers to the issue of a conveyor belt not staying aligned with the conveyor structure, causing it to drift or track off to one side. This misalignment can lead to several operational problems, including uneven belt wear, damage to the belt and conveyor components, material spillage, and reduced efficiency of the conveyor system. Belt tracking problems can be caused by a variety of factors, including improper installation, worn or damaged conveyor components, incorrect belt tension, and uneven loading of materials on the belt. Addressing belt tracking issues is crucial for maintaining the performance and longevity of a conveyor system. It involves inspecting and adjusting the conveyor’s components, such as rollers, pulleys, and the belt itself, to ensure they are correctly aligned and functioning as intended.
The most common problem of belt conveyors is misalignment, which can manifest as belt tracking issues, where the belt does not run straight along the conveyor frame. This can lead to uneven belt wear, increased maintenance costs, and operational downtime. Other common problems include belt slippage, where the belt does not grip the pulleys properly, leading to loss of motion or excessive wear; material spillage, where materials fall off the belt, creating safety hazards and requiring additional cleanup; and blockages or jams, where debris or materials obstruct the conveyor path, causing the system to stop. Wear and tear on conveyor components, such as rollers, bearings, and pulleys, can also lead to decreased efficiency and the need for frequent replacements. Regular maintenance and inspections are essential to identify and address these issues promptly to ensure the conveyor operates smoothly and efficiently.
The two major causes of belt slippage are improper belt tension and pulley wear. Improper belt tension, whether too high or too low, can prevent the belt from gripping the pulleys correctly, leading to slippage. If the tension is too low, the belt cannot form an adequate grip on the pulleys, causing it to slip under load. Conversely, if the tension is too high, it can stretch the belt, reducing its ability to maintain proper contact with the pulleys and potentially leading to slippage. Pulley wear is another significant cause of belt slippage. Over time, pulleys can become worn or coated with material buildup, reducing their ability to effectively grip the belt. Worn pulleys may have a smooth surface that lacks the necessary friction for proper belt traction, causing the belt to slip, especially under heavy loads or during startup. Addressing these issues involves adjusting the belt tension to the correct level and replacing or cleaning worn pulleys to restore proper belt grip and prevent slippage.
Need durable and efficient belts? Contact us now!
Last Updated on July 16, 2024 by Jordan Smith
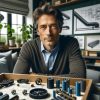
Jordan Smith, a seasoned professional with over 20 years of experience in the conveyor system industry. Jordan’s expertise lies in providing comprehensive solutions for conveyor rollers, belts, and accessories, catering to a wide range of industrial needs. From initial design and configuration to installation and meticulous troubleshooting, Jordan is adept at handling all aspects of conveyor system management. Whether you’re looking to upgrade your production line with efficient conveyor belts, require custom conveyor rollers for specific operations, or need expert advice on selecting the right conveyor accessories for your facility, Jordan is your reliable consultant. For any inquiries or assistance with conveyor system optimization, Jordan is available to share his wealth of knowledge and experience. Feel free to reach out at any time for professional guidance on all matters related to conveyor rollers, belts, and accessories.