Optimizing Operations with Conveyor Belt Tracking Methods
In the intricate world of conveyor systems, the alignment and proper tracking of conveyor belts stand as pivotal elements for operational efficiency and longevity. Despite the advanced engineering behind these systems, conveyor belt tracking issues are often misattributed to the belts themselves, overlooking the critical influence of installation procedures and maintenance practices. This misjudgment underscores a widespread misconception, diverting attention from effective conveyor belt tracking methods that are essential for preventing misalignment and reducing wear and tear. Understanding these methods is vital for anyone involved in the design, operation, or maintenance of conveyor systems. By addressing the root causes of tracking problems, such as improper installation or inadequate tensioning, we can significantly improve conveyor belt performance and durability, ensuring a seamless flow of operations in various industrial applications.
What Is Conveyor Belt Tracking Methods
The efficiency and reliability of conveyor systems heavily rely on the precision of conveyor belt tracking methods. Misalignment, one of the most common issues faced in conveyor operation, can lead to significant problems, including uneven belt wear, product damage, and reduced conveyor belt life. This section delves into the intricacies of conveyor belt tracking issues and underscores the importance of proper alignment for optimal belt performance.
Conveyor belt tracking concerns the methods used to guide a conveyor belt to run straight and true on the pulleys and rollers. When a conveyor belt strays from its intended path, it can lead to operational disruptions, increased maintenance costs, and the potential for hazardous work conditions. Thus, employing effective conveyor belt tracking methods is not just a matter of efficiency; it’s a critical component of operational safety and longevity.
Proper alignment of a conveyor belt is fundamental to its performance. A well-aligned belt ensures smooth operation, reduces the risk of material spillage, and minimizes wear on the belt and the conveyor structure. It’s a common misconception that belts are the sole cause of tracking problems when, in fact, the root causes often lie in improper installation, inadequate tensioning, and the neglect of critical alignment procedures during maintenance and operation phases.
The emphasis on conveyor belt tracking methods is not merely about maintaining the belt’s path but also about optimizing the conveyor’s operational functionality and prolonging the lifespan of the belt and the system as a whole. Effective tracking methods encompass a comprehensive approach, including the correct installation of the conveyor, regular maintenance checks, and the timely adjustment of components prone to wear and misalignment.
Understanding and implementing conveyor belt tracking theory tips are indispensable for ensuring that conveyor systems operate efficiently, safely, and cost-effectively. This foundational knowledge not only helps in troubleshooting and resolving alignment issues but also in designing and maintaining conveyor systems that are resilient, reliable, and capable of meeting the demands of modern industrial operations.
Conveyor Belt Alignment and Adjustment Procedures Utilizing Conveyor Belt Tracking Methods
Achieving and maintaining optimal conveyor belt alignment is a critical aspect of conveyor system maintenance and operation. The precision of conveyor belt tracking tips plays a vital role in this process, guiding the necessary adjustments to ensure that the belt runs correctly along the conveyor’s path. This section provides a detailed step-by-step guide on the conveyor belt alignment procedure, supplemented with diagrams to illustrate the effective application of these conveyor belt tracking methods.
Step 1: Assess the Conveyor Belt Alignment
Before making any adjustments, conduct a thorough assessment of the conveyor belt’s current alignment. This involves inspecting the belt while it’s running, noting any deviations or tendencies to drift to one side. Diagrams can be used to mark the areas of misalignment, serving as a reference for adjustments.
Step 2: Check and Adjust Pulleys and Rollers
The alignment of pulleys and rollers is crucial in guiding the belt correctly. Use a straightedge or laser alignment tool to check that these components are perfectly perpendicular to the belt’s direction. Adjustments should be made to the positioning of pulleys and rollers to correct any misalignments identified in the assessment phase.
Step 3: Ensure Proper Belt Tension
Inadequate tension is a common cause of belt misalignment. Adjust the tensioning mechanism to achieve the recommended tension level for your specific conveyor belt. This step might require iterative adjustments to find the optimal tension that allows for smooth operation without causing undue strain on the belt or the conveyor structure.
Step 4: Implement Tracking Adjustments
Based on the initial assessment, implement tracking adjustments using recognized conveyor belt tracking methods. This may involve adjusting the angle of the idler rollers to guide the belt back towards the center path or utilizing tracking devices designed to apply gentle steering forces to the belt.
Step 5: Monitor and Refine Adjustments
After adjustments have been made, the belt should be monitored over a period of operation to ensure that the alignment has been correctly achieved and maintained. Continuous observation will help in identifying if further refinements are needed, as conveyor belts may require multiple adjustments to settle into the correct alignment.
Step 6: Document Adjustments and Observations
Maintaining records of the adjustments made and the observations noted during the alignment process is crucial for future maintenance activities. This documentation can help in quickly identifying recurring issues and understanding the impact of specific adjustments on the belt’s alignment over time.
Employing effective conveyor belt tracking methods throughout the alignment and adjustment procedures ensures that the conveyor belt operates efficiently, reducing wear and extending the service life of both the belt and the conveyor system. Diagrams and detailed records serve as invaluable tools in this process, providing clear guidance and reference points for maintenance teams and ensuring that the conveyor belt remains in optimal alignment.
Basic vs. Additional Measures for Effective Belt Tracking Utilizing Conveyor Belt Tracking Methods
The implementation of conveyor belt tracking methods can be categorized into basic and additional measures, each playing a critical role in maintaining the optimal performance and longevity of conveyor systems. This section explores six fundamental measures that form the foundation of effective belt tracking under normal operating conditions, alongside four supplementary measures that come into play when these basic strategies prove insufficient.
Basic Measures for Conveyor Belt Tracking
- Proper Installation: Ensuring that all conveyor components are installed correctly is the first step in preventing tracking issues. This includes precise alignment of the frame, pulleys, and rollers to the conveyor’s intended path.
- Regular Inspections: Conducting routine inspections allows for the early detection of potential tracking problems, enabling corrective action before significant misalignment occurs.
- Correct Tensioning: Maintaining the appropriate tension on the conveyor belt is crucial for effective tracking. Too much tension can lead to belt stretch and tracking issues, while insufficient tension can cause the belt to wander off its intended path.
- Alignment Adjustments: Minor adjustments to the conveyor structure, such as squaring the frame and realigning the pulleys and rollers, are essential basic measures for ensuring the belt tracks correctly.
- Cleanliness: Keeping the conveyor belt and components clean is vital. Accumulation of debris can affect the belt’s tracking and lead to premature wear.
- Lubrication: Proper lubrication of moving parts reduces friction and wear, which can influence belt tracking. Ensuring that all parts are adequately lubricated is a fundamental maintenance task.
Additional Measures for Enhanced Belt Tracking
When basic measures are not sufficient to correct or maintain belt alignment, additional measures using advanced conveyor belt tracking methods may be necessary:
- Tension Monitoring Systems: Implementing automated tension monitoring systems can provide real-time adjustments to maintain optimal tension across the conveyor belt, preventing misalignment.
- Edge Guides: In some cases, installing edge guides can help in guiding the belt back to its correct path. However, this method should be used cautiously as it can cause additional wear on the belt edges if overused.
- Tracking Sensors and Controls: Advanced conveyor systems can be equipped with sensors and control systems that detect misalignment and automatically adjust the conveyor to correct the belt’s path.
- Steering Rollers: Steering rollers can actively adjust the direction of the belt as it moves, offering a dynamic solution to tracking issues. These rollers can be adjusted manually or automatically, depending on the system’s design.
- Specialized Belting Materials: Certain applications may benefit from belts made with materials or textures designed to improve tracking. These specialized belts can help in reducing the need for frequent adjustments.
- Engineering Consultation and Custom Solutions: When standard tracking measures are inadequate, consulting with conveyor engineering experts can lead to customized solutions tailored to the specific challenges of the conveyor system.
Incorporating these basic and additional conveyor belt tracking tips ensures that the conveyor operates efficiently, with minimal downtime and maintenance requirements. Understanding when and how to apply these measures is crucial for anyone responsible for the operation and maintenance of conveyor systems, ensuring that the belt remains correctly aligned for optimal performance.
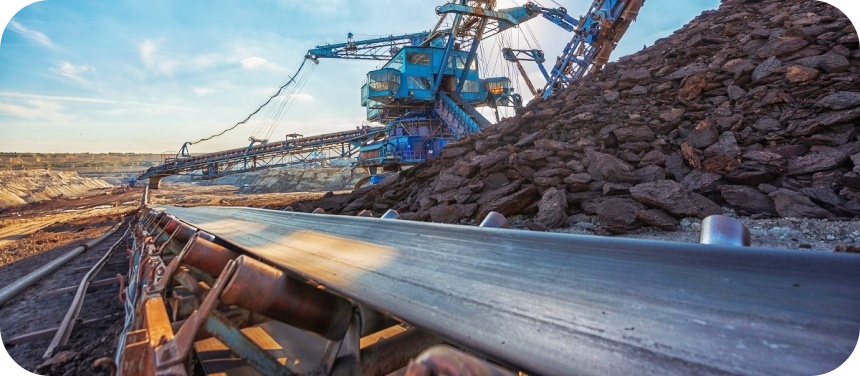
Industrial Conveyor Belt Tracking Methods
In the realm of industrial operations, ensuring the precise tracking of conveyor belts is essential for maintaining efficiency and prolonging equipment life. This section provides a detailed explanation of various industrial conveyor belt tracking tips, employing a table format for clarity. Additionally, it introduces conveyor belt tracking rollers and outlines their eight critical roles in belt alignment.
Common Conveyor Belt Tracking Methods
Roles of Conveyor Belt Tracking Rollers
- Centering: Tracking rollers play a crucial role in guiding the conveyor belt back to its central path, ensuring uniform operation and reducing wear.
- Stabilization: They provide stability to the belt, preventing it from swaying or slipping off the rollers.
- Tension Management: By contributing to the overall tensioning system, tracking rollers help maintain the optimal tension across the belt’s width.
- Load Distribution: Properly aligned tracking rollers ensure even distribution of the conveyed material, preventing off-center loading issues.
- Friction Reduction: By maintaining the belt’s alignment, tracking rollers reduce friction between the belt and other conveyor components, enhancing efficiency.
- Preventative Maintenance: Their role in maintaining alignment minimizes the need for emergency repairs and prolongs the conveyor system’s lifespan.
- Operational Safety: By ensuring smooth and predictable conveyor operation, tracking rollers contribute to a safer working environment.
- Efficiency Enhancement: Optimal belt tracking, supported by tracking rollers, leads to improved operational efficiency and reduced downtime.
Employing these industrial conveyor belt tracking methods and understanding the multifaceted roles of tracking rollers are vital for any facility looking to optimize their conveyor systems. These strategies not only ensure the longevity of the conveyor belt but also enhance safety and efficiency across operations.
Advanced Belt Tracking Techniques Using Conveyor Belt Tracking Methods
In the pursuit of operational excellence, conveyor systems often require more sophisticated solutions to address complex tracking challenges. Advanced belt tracking techniques utilizing specialized conveyor belt tracking methods can significantly enhance system reliability and efficiency. This section explores the nuances of forced belt tracking methods, including the use of V-Guides, crowned pulleys, and the innovation of the Independently Steerable Pulley (ISP) system, tailored for challenging applications.
Forced Belt Tracking Methods
Forced belt tracking methods are engineered solutions that actively guide the conveyor belt to maintain its intended path, crucial for preventing misalignment and reducing wear.
- V-Guide Tracking: V-Guide tracking involves the use of V-shaped profiles affixed to the underside of the conveyor belt. These guides fit into corresponding grooves on the pulleys and rollers, ensuring the belt maintains a straight path. This method is particularly effective in preventing lateral movements of the belt under varying load conditions.
- Crowned Pulleys: Crowned pulleys feature a slightly raised center compared to their edges. The design leverages the belt’s tension to naturally guide it towards the center of the pulley. While simple in concept, the effectiveness of crowned pulleys depends on precise engineering to match the belt’s properties and the system’s operational demands.
- Tracking Rings and Discs: These are added to the pulley system to create a differential in the sliding friction along the belt’s width, guiding the belt back to its correct path. This method is beneficial for belts that experience uneven loading or are prone to environmental factors causing misalignment.
Custom Solutions for Challenging Applications
In scenarios where standard tracking methods are insufficient, custom solutions like the Independently Steerable Pulley (ISP) system offer a revolutionary approach to conveyor belt tracking.
- Independently Steerable Pulley (ISP) System: The ISP system is a cutting-edge solution designed for precise control over the belt’s path. It consists of a pulley that can be independently steered to adjust the belt’s direction, allowing for real-time corrections to alignment issues. This system is invaluable for applications where environmental factors, load variability, and operational dynamics pose complex tracking challenges.
- Integration of Sensor Technology: Advanced tracking systems often incorporate sensor technology to detect misalignment early and automatically initiate corrective actions through mechanisms like the ISP. This proactive approach to conveyor belt tracking ensures continuous operation and reduces the need for manual interventions.
- Custom-Engineered Guides and Rails: For belts with unique designs or those operating in specialized environments, custom-engineered guides and rails can be developed. These are tailored to fit the specific contours and operational requirements of the conveyor system, providing a bespoke solution to tracking issues.
Advanced conveyor belt tracking methods, including forced tracking techniques and custom solutions like the ISP system, represent the forefront of innovation in conveyor technology. These methods ensure that conveyor belts operate smoothly and efficiently, even in the most demanding industrial environments. By addressing the complexities of belt tracking with precision-engineered solutions, businesses can achieve higher operational reliability, reduced maintenance costs, and improved system performance.
Troubleshooting Conveyor Belt Tracking Issues with Conveyor Belt Tracking Methods
Effective troubleshooting of conveyor belt tracking issues is crucial for maintaining the operational efficiency and longevity of conveyor systems. By applying targeted conveyor belt tracking methods, many common problems can be quickly diagnosed and resolved. This section outlines 10 common conveyor belt tracking problems and their solutions, as well as detailed guidance on diagnosing and correcting belts that track to one side.
Common Conveyor Belt Tracking Problems and Solutions
- Belt Misalignment on Start-Up: If the belt tracks off to one side from the beginning, check for proper installation and alignment of all components. Solution: Realign pulleys and idlers according to manufacturer specifications.
- Belt Edges Wearing Prematurely: This issue often results from the belt rubbing against the conveyor frame. Solution: Adjust the idlers or guide rollers to ensure the belt is centered.
- Material Spillage: Misaligned belts can lead to material falling off the conveyor. Solution: Utilize skirting systems and ensure the belt is tracking correctly.
- Belt Slipping on Pulleys: Caused by inadequate tension or pulley misalignment. Solution: Adjust the tension according to the manufacturer’s guidelines and realign pulleys.
- Excessive Energy Consumption: Poorly tracked belts require more energy to operate. Solution: Optimize belt tracking to reduce friction and energy usage.
- Belt Swaying on the Conveyor: Often a result of uneven loading or heavy wear on one side of the belt. Solution: Correct loading procedures and replace the belt if necessary.
- Pulley Bearing Failures: Misalignment can increase stress on bearings. Solution: Ensure pulleys are correctly aligned and replace any damaged bearings.
- Snub Roller Maladjustment: Snub rollers are used to increase the angle of engagement between the belt and pulleys. Misadjustment can affect tracking. Solution: Adjust snub rollers to ensure proper contact with the belt.
- Incorrect Belt Tension: Either too much or too little tension can cause tracking issues. Solution: Use tensioning devices to adjust the belt tension precisely.
- Damaged Belt Structure: Tears or deformations in the belt can lead to misalignment. Solution: Inspect the belt regularly and replace it if damage is significant.
Diagnosing and Correcting Conveyor Belts Tracking to One Side
When a conveyor belt consistently tracks to one side, it indicates an underlying issue that requires immediate attention. The following steps can help diagnose and correct this problem:
- Inspect the Conveyor Structure: Ensure that the frame and all components are level and square. Any structural discrepancies can lead to belt misalignment.
- Check for Loaded Conditions: Observe the belt under loaded conditions, as the weight distribution of the conveyed material can influence tracking.
- Examine Pulleys and Rollers: Look for wear patterns or build-ups that could affect the belt’s path. Clean and replace these components as necessary.
- Adjust Idlers and Tracking Rollers: Misaligned idlers or improperly adjusted tracking rollers can cause the belt to track to one side. Make incremental adjustments and observe the belt’s response.
- Evaluate Belt Tension: Uneven tension across the belt width can lead to tracking issues. Adjust tensioning devices to achieve uniform tension.
- Implement Advanced Conveyor Belt Tracking Methods: For persistent tracking problems, consider employing advanced tracking solutions such as the Independently Steerable Pulley (ISP) system or sensor-based automatic alignment systems.
By systematically addressing these common problems and employing precise conveyor belt tracking methods, operators can ensure that their conveyor systems run smoothly, efficiently, and with minimal downtime. Regular inspections, maintenance, and adjustments are key to preventing and correcting tracking issues, thereby extending the lifespan of the conveyor belt and enhancing overall operational effectiveness.
Improve efficiency with our reliable conveyor belt products.
Maintenance and Monitoring for Optimal Tracking Using Conveyor Belt Tracking Methods
Maintaining optimal tracking of a conveyor belt is not solely about implementing the right conveyor belt tracking methods at the outset; it’s also about the continuous maintenance and monitoring of the system to prevent and address tracking issues proactively. Regular maintenance and cleaning are paramount in preventing tracking problems, ensuring the longevity of the conveyor system, and maintaining operational efficiency. This section underscores the importance of these practices and provides 10 essential tips for ongoing monitoring and adjustment to ensure continuous proper belt tracking.
The Importance of Regular Maintenance and Cleaning
Regular maintenance and cleaning are critical for the effective operation of conveyor belt systems. Dirt, debris, and spillage can affect the belt’s traction and the functioning of pulleys and rollers, leading to misalignment and tracking issues. Moreover, wear and tear on moving parts can alter the alignment of the conveyor structure over time. Implementing a routine maintenance schedule ensures that all components are in good working order and that the conveyor belt remains aligned according to the prescribed conveyor belt tracking methods.
Tips for Ongoing Monitoring and Adjustment
- Establish a Regular Inspection Schedule: Conduct frequent inspections of the belt, pulleys, rollers, and alignment. Early detection of potential issues can prevent more significant problems.
- Keep a Maintenance Log: Document all maintenance activities, adjustments made, and observations about the belt’s performance. This historical record can help identify patterns and predict future issues.
- Clean Regularly: Ensure that the belt and all conveyor components are clean. Use appropriate cleaning tools and methods to remove debris and buildup that could affect tracking.
- Monitor Belt Tension: Check the belt tension regularly to ensure it is within the manufacturer’s recommended range. Adjust as necessary to maintain proper tension.
- Adjust Rollers and Pulleys: Make minor adjustments to rollers and pulleys if you notice the belt starting to drift. Always adjust in small increments and monitor the results.
- Check for Wear and Damage: Inspect the belt and components for signs of wear or damage. Replace parts as needed to ensure optimal performance and alignment.
- Use Alignment Sensors: If available, incorporate alignment sensors and monitoring systems that can automatically alert you to misalignment issues.
- Train Maintenance Personnel: Ensure that all personnel involved in maintenance are trained on the correct conveyor belt tracking tips and understand how to make adjustments properly.
- Evaluate Load Distribution: Regularly check the load distribution on the belt. Uneven loading can cause the belt to track off-center.
- Review Conveyor Design: Periodically review the conveyor design and layout. Modifications or updates might be necessary to accommodate changes in operation or to correct persistent tracking issues.
By prioritizing maintenance and monitoring, utilizing conveyor belt tracking methods effectively, and adhering to these tips for ongoing adjustments, organizations can ensure that their conveyor systems operate smoothly and efficiently. This proactive approach not only extends the life of the conveyor belt but also enhances safety and reduces downtime and operational costs.
FAQs about Conveyor Belt Tracking Methods
The belt tracking method refers to the process and techniques used to ensure that a conveyor belt aligns correctly and runs straight on the pulleys and rollers of a conveyor system. Effective belt tracking is crucial for the smooth operation of a conveyor system, as it prevents the belt from drifting off its intended path, which can lead to operational disruptions, material spillage, and increased wear on the belt and conveyor components. Various methods are employed to achieve proper belt tracking, including the adjustment of pulleys and rollers to correct angles, maintaining appropriate belt tension, and installing guiding mechanisms such as tracking bars, crowned pulleys, or tensioning devices. The choice of method depends on several factors, including the type of belt, conveyor design, and the specific operational conditions of the system. Implementing the correct belt tracking methods is essential for minimizing maintenance issues and extending the lifespan of the conveyor system.
There are several foundational rules for conveyor belt tracking that help maintain the belt’s alignment and functionality. First, it’s crucial to ensure that all components of the conveyor system, including pulleys, rollers, and the belt itself, are installed correctly and aligned perpendicularly to the system’s direction of travel. Second, the belt must be tensioned properly; too much or too little tension can lead to tracking issues. Third, the conveyor structure must be level and square, as any deviation can cause the belt to misalign. Fourth, regular inspections and maintenance are vital; this includes cleaning debris from the belt and components, as well as checking for wear and making necessary adjustments. Lastly, when making adjustments to correct belt tracking, changes should be done gradually and tested thoroughly before making additional adjustments. These rules are essential for preventing tracking problems and ensuring the conveyor operates efficiently and safely.
A belt tracking mechanism refers to the specific components and devices designed to adjust or maintain the alignment of a conveyor belt. These mechanisms can be simple manual adjustments made to rollers or pulleys, or more sophisticated systems that automatically adjust the belt’s position. Common types of belt tracking mechanisms include self-aligning idlers, which pivot to guide the belt back into the correct position, and crowned pulleys, which have a slightly higher diameter in the middle to naturally guide the belt towards the center. Other mechanisms might involve the use of tensioning devices that adjust the belt’s tension asymmetrically across its width, or electronic systems that use sensors to detect misalignment and activate adjustments. The choice of tracking mechanism depends on the specific requirements of the conveyor system, including the type of belt, the materials being conveyed, and the operational environment.
Tracking or centering a conveyor belt involves adjusting the belt and the conveyor’s components so that the belt runs straight and aligned with the system. The process starts with ensuring that all parts of the conveyor are installed correctly and that the structure is level and square. From there, the following steps can be taken: First, adjust the tension of the conveyor belt to the manufacturer’s specifications, as improper tension is a common cause of tracking issues. Second, inspect and adjust the alignment of rollers and pulleys; they should be perpendicular to the direction of belt travel. Third, use tracking devices or mechanisms, such as self-aligning idlers or crowned pulleys, to guide the belt back into the correct position if it begins to drift. Fourth, regularly inspect the belt for wear and damage, as these can affect tracking. Finally, make incremental adjustments and observe the belt’s behavior, making further tweaks as necessary. Effective tracking is a continuous process of monitoring and adjustment to ensure the longevity and efficiency of the conveyor system.
Last Updated on July 16, 2024 by Jordan Smith
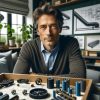
Jordan Smith, a seasoned professional with over 20 years of experience in the conveyor system industry. Jordan’s expertise lies in providing comprehensive solutions for conveyor rollers, belts, and accessories, catering to a wide range of industrial needs. From initial design and configuration to installation and meticulous troubleshooting, Jordan is adept at handling all aspects of conveyor system management. Whether you’re looking to upgrade your production line with efficient conveyor belts, require custom conveyor rollers for specific operations, or need expert advice on selecting the right conveyor accessories for your facility, Jordan is your reliable consultant. For any inquiries or assistance with conveyor system optimization, Jordan is available to share his wealth of knowledge and experience. Feel free to reach out at any time for professional guidance on all matters related to conveyor rollers, belts, and accessories.