Conveyor Belt Tracking Procedure to Follow
In the realm of material handling and industrial operations, the efficiency and longevity of conveyor systems hinge significantly on the precision of the conveyor belt tracking procedure. This critical process ensures that conveyor belts run smoothly and align correctly along their intended path, minimizing downtime and maximizing productivity. However, without proper attention to conveyor belt tracking, systems are prone to a host of issues, including uneven belt wear, product misalignment, and potential damage to the conveyor infrastructure. These common issues not only lead to operational inefficiencies but can also result in costly repairs and maintenance. Understanding and implementing a meticulous conveyor belt tracking procedure is, therefore, essential for any facility relying on conveyor systems for their daily operations.
What Is Conveyor Belt Tracking
Conveyor belt tracking is the process of aligning and maintaining a conveyor belt in the correct path during its operation. Proper tracking is crucial to ensure the belt runs efficiently and to prevent damage to the belt and the conveyor system. Here are the key aspects of conveyor belt tracking:
Key Aspects of Conveyor Belt Tracking
Alignment:
- Ensuring the conveyor belt is centered and aligned properly on the conveyor structure.
- Misalignment can cause the belt to drift off-center, leading to potential damage and inefficiency.
Tension:
- Proper tensioning of the belt is essential to maintain the correct tracking.
- Over-tensioning or under-tensioning can lead to tracking issues.
Components:
- Rollers, pulleys, and other components must be aligned and in good condition.
- Misaligned or worn-out components can cause the belt to run off track.
Regular Maintenance:
- Regular inspection and maintenance of the conveyor system help in identifying and correcting tracking issues early.
- Ensuring that all parts are functioning correctly and are free from obstructions.
Load Distribution:
- Evenly distributing the load on the conveyor belt helps maintain proper tracking.
- Uneven loading can cause the belt to drift to one side.
Environmental Factors:
- Factors such as temperature, humidity, and dust can affect belt tracking.
- Proper environmental controls and protective measures can mitigate these effects.
Methods for Tracking Adjustment
Adjusting Idlers:
- Adjusting the position of the idlers to guide the belt back to the center.
- This is usually done by moving the end of the idler frame in small increments.
Adjusting Pulleys:
- Pulleys, especially the drive and tail pulleys, can be adjusted to help steer the belt.
- Adjustments are typically made by moving the pulley shafts to achieve the desired belt position.
Use of Tracking Devices:
- Installing tracking devices like sensors and automatic belt trackers to monitor and adjust the belt’s position automatically.
Maintaining proper conveyor belt tracking is vital for the longevity and efficiency of the conveyor system. Regular inspections and adjustments can help ensure smooth operation and reduce the risk of costly repairs or downtime.
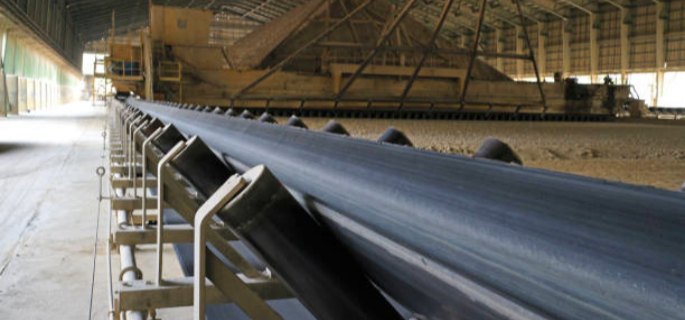
Importance of the Conveyor Belt Tracking Procedure
The conveyor belt tracking procedure is an essential aspect of managing and maintaining efficient conveyor system operations. It involves the alignment and adjustment of the conveyor belt to ensure it runs straight and true along the conveyor framework. This procedure is critical for preventing belt drift — the tendency of a belt to move sideways, which can lead to several operational challenges. Here are nine key points highlighting the significance of this procedure in industrial operations:
- Prevents Belt Damage: Proper execution of the conveyor belt tracking procedure minimizes wear and tear on the belt edges, significantly extending the belt’s lifespan.
- Reduces Downtime: By ensuring smooth belt operation, the procedure decreases the likelihood of unscheduled maintenance and downtime.
- Enhances Safety: Misaligned belts can lead to spillage of materials, creating slip hazards and potentially dangerous working conditions.
- Improves Productivity: A well-tracked belt moves products more efficiently, reducing bottlenecks and increasing throughput.
- Maintains Product Quality: Accurate tracking prevents products from being damaged due to misalignment or falling off the conveyor.
- Saves Operational Costs: Minimizing wear and tear, reducing downtime, and enhancing productivity all contribute to lower operational costs.
- Facilitates Predictable Maintenance: With regular tracking checks, maintenance can be planned and executed predictably, avoiding emergency repairs.
- Optimizes Energy Use: A misaligned belt requires more energy to move. Proper tracking ensures the conveyor system operates efficiently, using less energy.
- Supports Automation: In automated systems, precise execution of the conveyor belt tracking procedure is essential for accurate positioning and handling of goods.
Several factors can influence conveyor belt misalignment and tracking problems, each requiring careful consideration during the conveyor belt tracking procedure:
- Improperly Installed or Adjusted Pulleys and Rollers: Misaligned pulleys and rollers can cause the belt to drift off its intended path.
- Uneven Loading: Loading materials unevenly across the belt’s width can lead to tracking issues and increased wear on one side.
- Worn or Damaged Components: Worn-out bearings, rollers, or pulleys can affect the belt’s alignment.
- Belt Tensioning Issues: Incorrectly tensioned belts can lead to slippage or excessive wear, affecting tracking.
- Structural Misalignments: If the conveyor frame is not level or square, it can lead to belt tracking problems.
- Environmental Factors: Dust, moisture, and other environmental factors can affect the belt’s grip on the pulleys and rollers, leading to misalignment.
- Belt Splicing and Joint Issues: Improperly executed belt splices or joints can create uneven thickness, causing the belt to track off-center.
- Accumulation of Debris: Build-up of material on the rollers, pulleys, or along the conveyor path can obstruct smooth belt movement and affect tracking.
Understanding and addressing these factors are crucial steps in the conveyor belt tracking procedure, ensuring the conveyor system operates efficiently and reliably.
Steps for Conveyor Belt Tracking Procedure
Conveyor belt tracking involves several steps to ensure the belt runs correctly on the conveyor system. Here’s a detailed guide on how to track a conveyor belt:
Steps for Conveyor Belt Tracking
Pre-Inspection
- Turn off the conveyor and ensure it’s safe to work on.
- Inspect the belt and conveyor system for any visible damage or issues.
- Check the belt tension to make sure it’s within the manufacturer’s recommended range.
- Inspect rollers and pulleys for alignment and condition. Replace any worn-out components.
Initial Setup
- Center the belt: Manually align the belt in the center of the conveyor system.
- Check the belt tension: Ensure it’s evenly distributed across the width of the belt.
Adjusting the Idlers
- Locate the return idlers: These are the rollers that guide the return side of the belt.
- Adjust the idlers: Loosen the mounting bolts and shift the idler frame. For example, if the belt is tracking to the left, move the right end of the idler frame forward (towards the belt travel direction). Tighten the bolts after making adjustments.
Adjusting the Pulleys
- Drive and tail pulleys: These pulleys can also be adjusted to help with tracking.
- Shift the pulley shaft: If the belt is moving to one side, move the corresponding end of the pulley shaft in the direction of the belt travel. For instance, if the belt is moving to the left, move the right end of the pulley shaft forward.
Testing and Fine-Tuning
- Turn on the conveyor: Run the conveyor at a slow speed and observe the belt tracking.
- Make incremental adjustments: If the belt is still not centered, make small adjustments to the idlers and pulleys. It’s important to make adjustments incrementally and allow time for the belt to respond.
Load Distribution
- Ensure even load: Check that the load on the belt is evenly distributed. Uneven loading can cause tracking issues.
- Adjust the loading system: If necessary, modify the loading system to ensure an even distribution of the load on the belt.
Automatic Tracking Devices
- Install tracking devices: Consider using belt tracking devices such as sensors and automatic trackers, which can help maintain the belt’s position without manual intervention.
Regular Maintenance and Monitoring
- Regular inspections: Periodically inspect the belt and conveyor components for alignment, tension, and wear.
- Maintenance schedule: Develop and follow a maintenance schedule to keep the conveyor system in optimal condition.
- Adjust as needed: Make adjustments as needed based on observations during regular operation.
Common Issues and Troubleshooting
- Belt Running Off to One Side: Adjust the idlers or pulleys as described to bring the belt back to center.
- Uneven Belt Wear: Check for misalignment and adjust accordingly. Inspect and replace any worn components.
- Belt Slippage: Ensure the belt tension is correct and adjust the drive pulley as needed.
- Noise and Vibration: Check for alignment issues and ensure all components are securely fastened.
Proper conveyor belt tracking is essential for the efficient and safe operation of a conveyor system. By following these steps and conducting regular maintenance, you can ensure your conveyor belt runs smoothly and stays in the correct path.
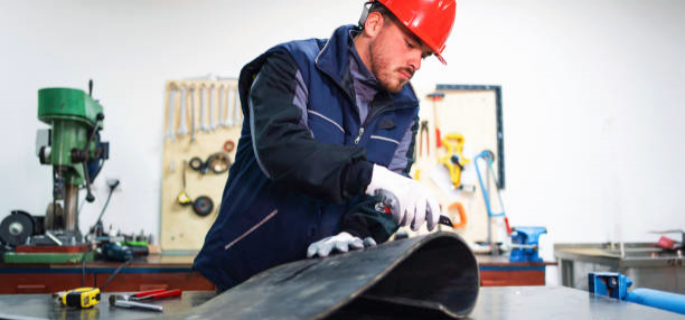
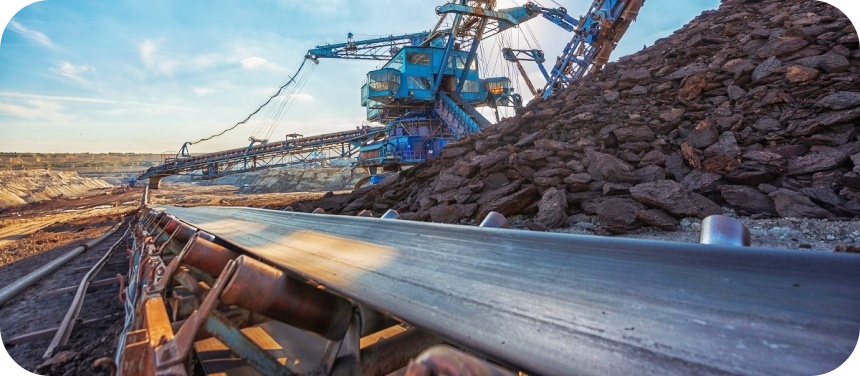
Conveyor Belt Tracking Procedure Basic Techniques
The conveyor belt tracking procedure is a critical maintenance task that ensures the longevity and efficiency of conveyor systems. Proper conveyor belt tracking theory prevents the belt from drifting off its intended path, which can cause significant operational disruptions. This guide outlines the essential steps and techniques involved in the conveyor belt tracking procedure, ensuring your conveyor system operates smoothly and reliably.
Initial Setup and Pre-Tracking Checks
Before diving into the tracking adjustments, it’s crucial to perform some preliminary checks and setup tasks to ensure the conveyor system is properly prepared for tracking.
- Ensuring the Conveyor Structure is Stable and Level: A misaligned or unstable structure can cause the belt to track incorrectly. Use a spirit level to check the conveyor frame and adjust the legs or supports as necessary to achieve a level structure.
- Verifying the Alignment of Pulleys and Rollers: Misaligned pulleys and rollers are common causes of tracking issues. Inspect the alignment of all pulleys and rollers, ensuring they are perpendicular to the direction of the belt travel and parallel to each other.
- Importance of Cleanliness for Effective Tracking: Debris, dust, and material buildup on the conveyor belt, pulleys, or rollers can affect the belt’s tracking. Clean the belt and all components thoroughly to remove any obstructions that could influence the belt’s path.
Basic Conveyor Belt Tracking Techniques
Once the initial checks are completed, you can proceed with the actual tracking adjustments. Here are some fundamental techniques involved in the conveyor belt tracking procedure:
Adjusting Tension and Alignment
- Rule 1: Adjusting Belt Tension to Correct Tracking: Often, simply adjusting the tension of the conveyor belt can resolve tracking issues. If the belt is tracking to one side, increase the tension on the opposite side to gently guide the belt back to the center. This adjustment should be done gradually and in small increments to avoid overcompensating.
- Use of Cylindrical-Conical Pulleys for Self-Tracking Effects: Cylindrical-conical or crowned pulleys are designed to naturally guide the belt towards the center. The diameter of these pulleys gradually increases towards the middle, creating a subtle steering effect that encourages the belt to align itself centrally.
Utilizing Tracking Systems and Devices
- Introduction to Guiding Pulleys (Control Pulleys) and Their Role in Belt Tracking: Guiding pulleys, also known as control pulleys, are adjustable pulleys placed at strategic points along the conveyor to influence the belt’s direction. By adjusting the angle and position of these pulleys, you can correct minor tracking issues without altering the tension of the entire system.
- The Impact of Inclined Rollers on Belt Tracking: Inclined rollers can be installed on the return side of the conveyor belt to exert a gentle guiding force on the belt. By angling these rollers in the direction you wish to steer the belt, you can achieve effective tracking correction. This technique is particularly useful for longer conveyor systems where other methods may be less effective.
Implementing these steps and techniques as part of your regular maintenance routine will help ensure that your conveyor belt tracking procedure is successful, leading to a more efficient and reliable conveyor system.
Advanced Solutions in the Conveyor Belt Tracking Procedure
The conveyor belt tracking procedure is not only about manual adjustments and regular maintenance. In complex or critical applications where precision is paramount, advanced solutions come into play. These solutions often involve automated systems and sophisticated tracking technologies designed to ensure optimal performance and reliability of conveyor belts in various industrial settings.
Overview of Automatic Belt Control Systems for Critical Tracking Problems
Automatic belt control systems represent a leap forward in the conveyor belt tracking procedure. These systems are engineered to detect and correct misalignment issues autonomously, minimizing the need for manual intervention and significantly reducing downtime. Here are eight key aspects of automatic belt control systems:
- Integrated Sensors: These systems utilize advanced sensors to continuously monitor the belt’s position and detect deviations from the intended path.
- Real-Time Adjustments: Upon detecting misalignment, the system instantaneously activates mechanisms to adjust the belt’s position, ensuring it remains on the correct trajectory.
- Precision Tracking: Automatic control systems offer a high degree of precision, capable of making minute adjustments that manual methods might miss.
- Reduced Wear and Tear: By maintaining optimal alignment, these systems reduce the wear on the belt and conveyor components, extending their lifespan.
- Enhanced Safety: Automatic systems reduce the risk of accidents associated with manual tracking adjustments, promoting a safer working environment.
- Data Collection and Analysis: Beyond tracking, these systems can collect data on the conveyor’s performance, aiding in predictive maintenance and operational efficiency.
- Customizable Settings: Operators can program the system according to specific operational needs, allowing for flexibility in various industrial applications.
- Integration with Existing Systems: Many automatic belt control systems are designed to integrate seamlessly with existing conveyor setups, making them a versatile solution for upgrading conveyor belt tracking procedures.
Discussion on Belt Tracking Systems and Their Applications in Complex Conveyor Setups
In complex conveyor setups, where the layout involves curves, inclines, or long distances, maintaining proper belt alignment can be particularly challenging. Advanced belt tracking systems are designed to address these challenges, offering solutions that ensure smooth and efficient operations. Here are nine points highlighting their applications and benefits:
- Curved Conveyor Applications: Advanced tracking systems are adept at maintaining belt alignment on curved conveyors, where traditional tracking methods may fall short.
- High-Speed Operations: In high-speed applications, even minor misalignments can lead to significant issues. Automated tracking systems provide the rapid response needed to correct deviations in real-time.
- Heavy Load Handling: Conveyors that handle heavy or uneven loads require robust tracking solutions to prevent slippage and misalignment.
- Long-Distance Conveying: Over long distances, maintaining consistent belt tracking becomes increasingly complex. Advanced systems offer continuous monitoring and adjustment along the entire conveyor length.
- Inclined and Declined Conveying: Gravity can exacerbate tracking issues on inclined or declined conveyors. Automated systems compensate for these forces, ensuring the belt remains centered.
- Variable Load Conditions: Systems that can adapt to changes in load conditions provide a dynamic solution for applications where the weight and distribution of materials can vary significantly.
- Environmental Considerations: In environments where dust, moisture, or temperature extremes are present, advanced tracking systems offer resilience and reliability.
- Integration with Material Handling Systems: Advanced tracking solutions can be integrated with other material handling systems for synchronized operation, enhancing overall efficiency.
- Compliance with Industry Standards: For industries with strict regulatory requirements, such as food processing or pharmaceuticals, advanced tracking systems ensure compliance by maintaining precise control over conveyor belt alignment.
The conveyor belt tracking procedure, when implemented with advanced solutions, not only addresses the immediate challenges of belt misalignment but also contributes to the long-term reliability and efficiency of conveyor systems in complex setups. These advanced solutions represent a significant investment in operational excellence, safety, and productivity.
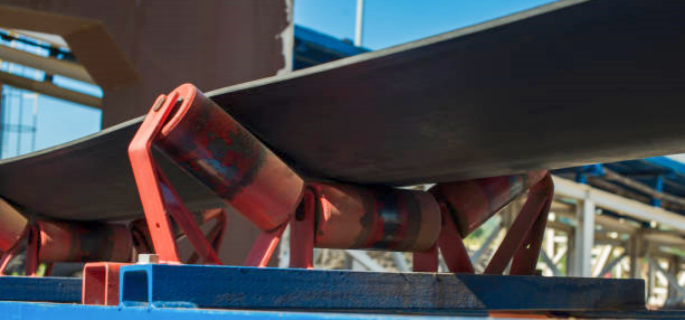
Implementing the Conveyor Belt Tracking Procedure: Alignment and Adjustment Techniques
The conveyor belt tracking procedure is pivotal in ensuring the seamless operation of conveyor systems. This section provides an in-depth look at the alignment and adjustment techniques essential for maintaining optimal conveyor belt performance.
Implementing Conveyor Belt Alignment Procedure PDFs for Precise Adjustments
Conveyor belt alignment procedure PDFs are invaluable resources that offer step-by-step guidance for precise belt adjustments. Here are nine critical points typically covered in these documents:
- Comprehensive Inspection: Begin with a thorough inspection of the conveyor for any signs of damage, wear, or misalignment that could impact performance.
- Accurate Measurement Techniques: Detailed instructions on employing tools like laser aligners or string lines to measure belt alignment accurately.
- Diagnosing Misalignment Types: Guidelines for identifying various misalignment issues, whether they are lateral, angular, or a combination of both.
- Belt Tension Adjustment: Step-by-step procedures for adjusting belt tension to correct misalignment, including tips for finding the ideal tension level.
- Squaring the Conveyor Frame: Instructions on ensuring the conveyor frame and rollers are perfectly square, a critical factor for proper belt tracking.
- Pulleys and Rollers Alignment: Techniques for aligning pulleys and rollers to ensure they are parallel and perpendicular to the conveyor’s direction of travel.
- Addressing Edge Wear: Solutions for dealing with edge wear, which often signals underlying misalignment issues.
- Regular Maintenance and Lubrication: Recommendations for ongoing maintenance and lubrication to prevent future alignment problems.
- Documentation of Adjustments: The importance of keeping detailed records of all adjustments and maintenance activities for future reference.
Practical Tips and Techniques for Adjusting a Conveyor Belt to Run Straight
Adjusting a conveyor belt to run straight is crucial for the efficiency and longevity of the conveyor system. Here are nine practical tips and techniques integral to the conveyor belt tracking procedure:
- Loosening Take-Up Bolts: Start adjustments by loosening the bolts on the take-up assembly to allow for belt movement.
- Incremental Adjustments: Make small, incremental adjustments to the tracking and observe the effects, avoiding large changes that might overshoot the correction.
- Ensuring Proper Belt Tension: Check that the belt is neither too tight nor too loose, as incorrect tension can lead to tracking issues.
- Utilizing Snub Rollers: Adjust snub rollers near where the belt begins to drift to gently guide it back towards the center.
- Clearing Debris: Remove any debris or material buildup from the belt and rollers, as this can cause the belt to track off-center.
- Inspecting Belt Edges: Regularly check the belt edges for wear or damage that could influence tracking.
- Balancing Load Distribution: Ensure that materials are evenly distributed across the belt to prevent uneven tracking.
- Realigning Pulleys and Rollers: Verify and adjust the alignment of pulleys and rollers to ensure they are perpendicular to the belt’s path.
- Continuous Observation: After making adjustments, run the conveyor belt and closely observe its behavior, making further adjustments as necessary until the belt runs straight.
By meticulously following the steps outlined in conveyor belt alignment procedure PDFs and adhering to the conveyor belt tracking procedure, operators can ensure their conveyor belts are correctly aligned and adjusted. This dedication not only enhances the conveyor system’s efficiency and durability but also promotes safety and minimizes operational downtime.
How to Fix Conveyor Belt Tracking Procedure
Fixing conveyor belt tracking involves identifying the issue and making necessary adjustments to ensure the belt stays aligned. Here’s a step-by-step guide on how to fix conveyor belt tracking:
Step-by-Step Guide to Fix Conveyor Belt Tracking
1. Turn Off and Secure the Conveyor
- Turn off the conveyor and ensure it’s locked out and tagged out (LOTO) to prevent accidental startup.
- Ensure the conveyor is empty and safe to work on.
2. Inspect the Conveyor System
- Check the belt: Look for signs of damage, uneven wear, or foreign objects.
- Inspect rollers and pulleys: Ensure they are free from debris and properly aligned.
- Check belt tension: Verify that the belt is neither too tight nor too loose.
3. Center the Belt
- Manually adjust the belt to ensure it’s centered on the conveyor system.
4. Adjust the Idlers
- Locate the return idlers: These are typically found on the return side of the belt.
- Adjust the idlers: If the belt is tracking to one side, move the end of the idler frame on the opposite side forward (towards the direction of belt travel). For example, if the belt is running to the left, move the right side of the idler frame forward. Tighten the bolts after adjustments.
- Adjust snub idlers: These are placed close to the drive and tail pulleys to help with tracking. Adjust them similarly to return idlers.
5. Adjust the Pulleys
- Drive and tail pulleys: These can be adjusted to influence tracking.
- Shift the pulley shaft: Move the end of the pulley shaft on the side where the belt is tracking off. For instance, if the belt is moving to the left, move the right end of the drive pulley shaft forward.
6. Check and Adjust the Load Distribution
- Evenly distribute the load: Ensure that the load on the belt is evenly distributed. Uneven loading can cause tracking issues.
- Adjust the loading system: Modify the loading system if necessary to achieve even load distribution.
7. Fine-Tuning
- Turn on the conveyor: Run the conveyor at a slow speed and observe the belt’s movement.
- Make incremental adjustments: Continue to make small adjustments to the idlers and pulleys until the belt is tracking correctly. Allow time for the belt to respond to each adjustment before making further changes.
8. Use Automatic Tracking Devices
- Install tracking devices: Consider using sensors and automatic belt trackers to monitor and adjust the belt’s position automatically.
9. Regular Maintenance and Monitoring
- Regular inspections: Periodically check the belt and conveyor components for alignment, tension, and wear.
- Follow a maintenance schedule: Develop and adhere to a maintenance schedule to keep the conveyor system in optimal condition.
- Adjust as needed: Make necessary adjustments based on observations during regular operation.
Common Issues and Solutions
- Belt Running to One Side: Adjust the idlers or pulleys as described to bring the belt back to center.
- Uneven Belt Wear: Check for misalignment and correct it. Inspect and replace any worn components.
- Belt Slippage: Ensure the belt tension is correct and adjust the drive pulley if necessary.
- Noise and Vibration: Check for alignment issues and ensure all components are securely fastened.
Fixing conveyor belt tracking is a critical maintenance task that ensures the efficient and safe operation of your conveyor system. By following these steps and conducting regular inspections and adjustments, you can keep your conveyor belt running smoothly and aligned correctly.
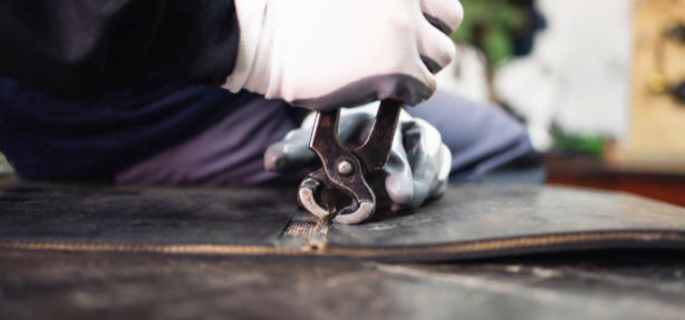
Contact us to find the perfect conveyor belt for your needs.
Mastering the Conveyor Belt Tracking Procedure: Diagrams and Troubleshooting
The conveyor belt tracking procedure is essential for the smooth and efficient operation of conveyor systems. This comprehensive guide focuses on utilizing conveyor belt tracking diagrams for visual guidance and addresses common troubleshooting scenarios, providing practical solutions to maintain optimal belt performance.
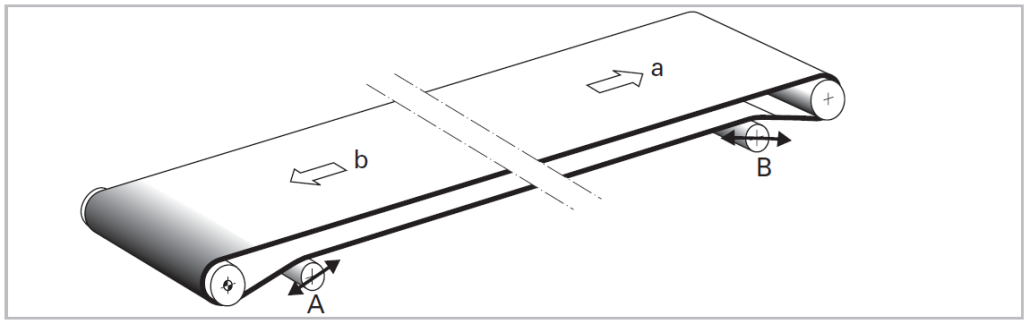
Utilizing Conveyor Belt Tracking Diagrams for Visual Guidance on Proper Setup and Adjustment
Conveyor belt tracking diagrams are invaluable tools within the conveyor belt tracking procedure, offering clear visual representations of the correct setup and adjustments needed for optimal performance. Here are eight critical aspects of how these diagrams can be effectively used:
- Component Identification: Diagrams assist in recognizing crucial tracking components, such as idlers, rollers, and tensioners, essential for proper belt alignment.
- Alignment Verification: They offer a visual checklist for verifying the alignment of all system components to ensure they are correctly positioned perpendicular to the belt’s trajectory.
- Tensioning Methods: Illustrations depict the correct methods to apply tension to the belt, preventing issues like slippage or excessive tension that could lead to misalignment.
- Roller Orientation: Provide guidance on the accurate positioning and orientation of rollers to direct the belt towards the center path.
- Pulley Adjustment Techniques: Show detailed procedures for adjusting pulleys to achieve balanced tension across the conveyor belt’s width.
- Troubleshooting Visuals: Include sections dedicated to troubleshooting, visually outlining common issues and their direct solutions.
- Belt Installation and Replacement: Step-by-step visual guides for correctly installing or replacing conveyor belts to start off with proper alignment.
- Maintenance and Inspection Points: Highlight essential maintenance and inspection areas to regularly check for potential wear or misalignment affecting the belt’s tracking.
Common Conveyor Belt Tracking Troubleshooting Scenarios and Solutions
Troubleshooting is a critical component of the conveyor belt tracking procedure. Below are eight frequent issues encountered with conveyor belts, alongside their solutions:
- Belt Drifting to One Side: Inspect and realign any misaligned rollers or pulleys. Confirm that the conveyor frame is level and squared.
- Excessive Belt Wear: Check for incorrect belt tension or misaligned parts causing the belt to contact the conveyor frame. Adjust as necessary.
- Slippage at the Drive Pulley: Enhance tension or inspect the drive pulley for wear, replacing it if needed. Adding lagging material may improve grip.
- Material Spillage: Ensure the belt is properly centered, and loading chutes are aligned with the belt’s trajectory to avoid off-center loading.
- Belt Squealing: Investigate for overtensioning or misaligned components that may cause unnecessary friction and adjust accordingly.
- Frequent Belt Misalignment: Regularly inspect and maintain all conveyor components for wear and proper alignment. Consider installing automatic conveyor belt tracking devices for continuous adjustments.
- Inconsistent Belt Speed: Verify motor performance and check for mechanical binding or obstructions in the conveyor path that may affect movement.
- Belt Edge Damage: Look for and correct any misalignments or sharp edges on the conveyor frame that may come into contact with the belt edges.
By adhering to the guidance provided by conveyor belt tracking diagrams and addressing troubleshooting scenarios with the suggested solutions, operators can ensure their conveyor systems operate efficiently, reducing downtime and maintenance costs.
Maintenance and Regular Checks for Optimal Tracking in the Conveyor Belt Tracking Procedure
The conveyor belt tracking procedure is not only about making adjustments when issues arise but also about preventing those issues through regular maintenance and checks. This proactive approach ensures the conveyor belt remains aligned, reducing the need for emergency interventions and maintaining operational efficiency.
Importance of Regular Maintenance Checks to Prevent Tracking Issues
Regular maintenance checks are crucial for the longevity and efficiency of conveyor systems. Here are eight points highlighting their importance in preventing tracking issues:
- Early Detection of Misalignment: Regular inspections allow for the early detection of minor misalignments before they escalate into major issues, preventing downtime.
- Prolonged Belt Life: By identifying and correcting tracking issues early, regular maintenance checks help prolong the life of the conveyor belt.
- Reduced Wear on Components: Maintenance checks help identify parts that are causing excessive wear on the belt, allowing for timely replacements or adjustments.
- Improved Safety: Regular maintenance reduces the risk of accidents caused by belt misalignment, such as spillages that could lead to slip hazards.
- Consistent Productivity: By ensuring that the conveyor belt is always running straight, regular checks maintain consistent productivity levels.
- Energy Efficiency: A well-aligned belt requires less energy to move, leading to energy savings and reduced operational costs.
- Compliance with Warranty Requirements: Many conveyor system warranties require regular maintenance, including belt tracking checks, to remain valid.
- Documentation for Troubleshooting: Regular maintenance creates a history of the conveyor’s condition, which can be invaluable for troubleshooting future issues.
Conveyor Belt Tracking PDFs and Guides as Resources for Ongoing Maintenance
Conveyor belt tracking PDFs and guides are essential resources for implementing a comprehensive maintenance program. Here are eight points on how these resources can support ongoing maintenance efforts:
- Step-by-Step Instructions: These documents often provide detailed instructions for conducting maintenance checks and making adjustments, ensuring that even less experienced staff can perform these tasks effectively.
- Troubleshooting Tips: Many guides include troubleshooting sections, helping maintenance personnel quickly identify and resolve common tracking issues.
- Customized Maintenance Schedules: Some PDFs offer templates for creating customized maintenance schedules based on the specific type of conveyor system and its usage patterns.
- Visual Aids: Diagrams and photographs in these guides help clarify the procedures and illustrate what properly aligned components should look like.
- Safety Guidelines: They include safety precautions to be taken while performing maintenance and adjustments, protecting workers from potential hazards.
- Tool Lists: Guides often list the tools and equipment needed for maintenance and tracking adjustments, ensuring that personnel have everything they need before starting the work.
- Record-Keeping Templates: Some resources provide templates for documenting maintenance activities, which can help track the conveyor system’s history and identify patterns in wear or misalignment.
- Updates on Best Practices: As conveyor technology evolves, these documents are updated with the latest best practices and innovations in belt tracking procedures, keeping maintenance teams informed.
By incorporating regular maintenance checks into the conveyor belt tracking procedure and utilizing available PDFs and guides, organizations can ensure their conveyor systems operate smoothly, efficiently, and safely over the long term. These practices not only prevent tracking issues but also contribute to the overall reliability and productivity of the conveyor system.
FAQs about Conveyor Belt Tracking Procedure
Conveyor belt tracking is governed by a set of fundamental rules designed to ensure the belt operates smoothly and efficiently. The first rule is to ensure that all components of the conveyor system, including pulleys, rollers, and the belt itself, are correctly aligned and level. Misalignment is a primary cause of tracking issues, leading to uneven wear, potential damage to the belt, and operational inefficiencies. The second rule involves maintaining proper belt tension. Too much tension can lead to excessive wear and tear on the conveyor components, while too little tension can cause the belt to slip off the pulleys. The third rule emphasizes the importance of cleanliness. Debris, dust, and material spillage on the belt or within the conveyor system can significantly impact the belt’s tracking ability. Regular cleaning and maintenance are crucial to prevent these issues. Adhering to these rules helps prevent downtime, extends the lifespan of the conveyor belt, and ensures the system operates at peak efficiency.
Belt tracking is performed through a series of adjustments and checks aimed at ensuring the conveyor belt runs straight and true along the conveyor system. The process begins with a thorough inspection of the conveyor belt and its components to identify any signs of misalignment or wear that could affect tracking. Following this, adjustments are made to the belt’s tension and the alignment of rollers and pulleys. This may involve repositioning rollers, adjusting tensioning devices, or even replacing worn components. The goal is to achieve even tension across the width of the belt and ensure all parts are aligned correctly.
After adjustments are made, the belt is monitored while in operation to observe its tracking behavior. Further fine-tuning may be necessary to achieve optimal alignment. This iterative process requires patience and precision but is essential for maintaining the efficiency and longevity of the conveyor system.
Conveyor tracking works by continuously monitoring and adjusting the path of the conveyor belt to ensure it remains aligned with the intended direction of travel. This is achieved through a combination of mechanical adjustments and, in more advanced systems, automated controls.
Mechanical adjustments involve aligning the conveyor’s rollers and pulleys so that they are perpendicular to the belt’s direction and parallel to each other. This alignment provides a stable base that guides the belt and prevents it from drifting. In automated conveyor tracking systems, sensors are used to detect the belt’s position and movement. If the belt begins to drift from its intended path, the system automatically makes adjustments to the conveyor’s components to realign the belt. This might include adjusting roller angles, modifying tension, or repositioning pulleys. Automated tracking systems provide real-time adjustments, ensuring the belt remains correctly aligned under varying operational conditions.
Adjusting the tracking on a conveyor belt involves several steps to correct any misalignment and ensure the belt runs straight. Initially, inspect the conveyor for any obvious signs of misalignment or damage to the belt, rollers, or frame. If the conveyor frame is not level or square, adjustments should be made to rectify this as it forms the foundation for proper belt tracking. Next, examine the rollers and pulleys to ensure they are correctly aligned and perpendicular to the belt’s direction. Misaligned rollers can be adjusted by loosening their mounting bolts and gently repositioning them until they are parallel with the conveyor frame.
For tension adjustments, locate the tensioning mechanism, which is typically found at the end of the conveyor. Adjust the tension evenly on both sides of the conveyor to prevent the belt from tracking to one side. After making these adjustments, run the conveyor belt and observe its path. It may take several small adjustments to achieve perfect alignment. Remember, patience and precision are key to successful belt tracking adjustments.
Last Updated on July 25, 2024 by Jordan Smith
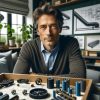
Jordan Smith, a seasoned professional with over 20 years of experience in the conveyor system industry. Jordan’s expertise lies in providing comprehensive solutions for conveyor rollers, belts, and accessories, catering to a wide range of industrial needs. From initial design and configuration to installation and meticulous troubleshooting, Jordan is adept at handling all aspects of conveyor system management. Whether you’re looking to upgrade your production line with efficient conveyor belts, require custom conveyor rollers for specific operations, or need expert advice on selecting the right conveyor accessories for your facility, Jordan is your reliable consultant. For any inquiries or assistance with conveyor system optimization, Jordan is available to share his wealth of knowledge and experience. Feel free to reach out at any time for professional guidance on all matters related to conveyor rollers, belts, and accessories.