Conveyor Belt Tracking System |Conveyor Belt Tracker
Conveyor belt systems are integral components of many industrial processes, serving as efficient means of transporting materials and goods across various stages of production and distribution. The effectiveness and longevity of these systems heavily depend on the proper alignment and tracking of the conveyor belts. Misalignment can lead to increased wear and tear, operational disruptions, and unwanted spillage, making the maintenance of belt alignment a critical aspect of conveyor system management. This is where conveyor belt tracking systems come into play. These systems are designed to ensure the continuous and correct alignment of the belt, thereby reducing wear, preventing spillage, and enhancing the overall efficiency of the conveyor system. By automatically adjusting the belt’s position to maintain its central alignment, conveyor belt tracking system plays a pivotal role in the smooth operation of conveyor belt systems, ensuring they operate at peak efficiency while minimizing maintenance requirements and downtime.
What Is Conveyor Belt Tracking
What is Conveyor Belt Tracking?
Conveyor belt tracking refers to the process of ensuring that a conveyor belt runs straight and remains centered on its path. Proper tracking prevents the belt from drifting to one side, which can lead to a host of operational problems, including spillage, excessive wear, and damage to the conveyor system itself. A well-maintained conveyor belt tracking system is crucial for the efficient operation of industrial processes.
Definition and Purpose
A conveyor belt tracking system is designed to keep the conveyor belt aligned and centered as it moves through its cycle. This system incorporates various mechanical components and technologies to detect and correct any misalignment, ensuring smooth and uninterrupted operation. The primary purpose of a conveyor belt tracking system is to prevent the belt from drifting off course, which can cause operational inefficiencies, safety hazards, and increased maintenance costs.
Key Components and How They Work Together
A conveyor belt tracking system typically includes several key components that work in tandem to maintain proper belt alignment:
- Sensors: These devices detect any deviation in the belt’s alignment. They can be mechanical sensors that physically contact the belt or non-contact sensors that use optical or ultrasonic technology.
- Tracking Rollers: Positioned at strategic points along the conveyor, these rollers adjust the belt’s path when misalignment is detected. They can be angled or pivoted to steer the belt back to the correct position.
- Control Units: These units process data from the sensors and command the tracking rollers to make necessary adjustments. Advanced systems may include feedback loops for continuous monitoring and adjustment.
- Actuators: These are mechanical devices that move the tracking rollers based on commands from the control unit. They ensure precise and timely corrections to keep the belt aligned.
These components work together to detect and correct any deviations in the belt’s path, ensuring it remains centered and runs smoothly. This coordination is essential for maintaining the efficiency and safety of the conveyor system.
Impact on Productivity and Maintenance
Implementing an effective conveyor belt tracking system has a significant impact on both productivity and maintenance. Here are some of the key benefits:
- Increased Productivity: A properly aligned conveyor belt reduces downtime and ensures a smooth flow of materials. This leads to higher throughput and more consistent production rates.
- Reduced Spillage: Misaligned belts often result in material spillage, which not only wastes resources but also requires additional labor to clean up. A tracking system minimizes spillage, leading to more efficient operations.
- Extended Belt Life: Constant misalignment causes uneven wear and tear on the belt, shortening its lifespan. By keeping the belt properly aligned, a tracking system helps extend its life, reducing the frequency of replacements and associated costs.
- Lower Maintenance Costs: Misaligned belts can cause damage to the conveyor structure and components, leading to costly repairs. A conveyor belt tracking system reduces the need for frequent maintenance, saving time and money.
A conveyor belt tracking system is essential for maintaining the efficiency, safety, and longevity of conveyor operations. By preventing misalignment, these systems enhance productivity, reduce spillage, extend belt life, and lower maintenance costs, making them a vital component in industrial settings.
The Basics of Conveyor Belt Tracking System
Understanding conveyor belt tracking theory and conveyor belt tracking systems fundamentals is essential for ensuring the efficient and safe operation of conveyor belt systems.A conveyor belt tracking system provides immediate, continuous precision adjustment of wandering conveyor belts. And help get a mistracking conveyor belt back on track. These systems are crucial for maintaining the alignment of the conveyor belt, thus preventing a myriad of operational issues. Here are the critical points that underline the importance of conveyor belt tracking systems and the common issues arising from misaligned conveyor belts:
- Ensures Continuous Alignment: A conveyor belt tracking system is specifically designed to keep the conveyor belt aligned on its path, preventing it from drifting off to the sides, which can cause uneven wear or damage to the belt edges.
- Minimizes Material Spillage: Proper alignment through a conveyor belt tracking system significantly reduces the chances of material spillage, which can lead to loss of materials and necessitate additional cleanup efforts.
- Reduces Equipment Wear: By keeping the belt aligned, conveyor belt tracking systems help in reducing the wear and tear on the conveyor belt and the rollers, prolonging their lifespan and reducing maintenance costs.
- Enhances Operational Safety: Misalignment can lead to safety hazards, including the risk of accidents from materials falling off the belt. A conveyor belt tracking system helps in mitigating these risks by ensuring the belt remains properly aligned.
- Improves System Efficiency: An aligned conveyor belt operates more smoothly and efficiently, facilitating the uninterrupted flow of materials and improving overall system productivity.
- Lowers Maintenance Demands: With reduced wear and tear and fewer instances of material spillage, conveyor belt tracking systems contribute to lower maintenance requirements and costs.
- Prevents Structural Damage: Continuous misalignment can cause damage to the conveyor structure itself. A conveyor belt tracking system helps in preventing such damage, safeguarding the investment in the conveyor system.
- Optimizes Energy Usage: Properly aligned belts require less energy to operate, as there is minimal resistance and friction. This efficiency translates into lower energy costs and a smaller environmental footprint.
The absence of an effective conveyor belt tracking system can lead to several common issues, including increased wear on the conveyor belt, higher risk of material spillage, potential safety hazards, and increased maintenance and operational costs. Each of these points underscores the indispensable value of conveyor belt tracking systems in maintaining the efficiency, safety, and longevity of conveyor belt operations.
Types of Conveyor Belt Tracking System
The effectiveness of conveyor belt systems in various industrial applications hinges on the precision of conveyor belt tracking systems. These systems are essential for maintaining the alignment of the conveyor belt, ensuring it operates smoothly and efficiently. There are several types of conveyor belt tracking systems, each with unique mechanisms and benefits, designed to meet the diverse needs of different conveyor operations.
Manual vs. Automatic Tracking Systems
When it comes to conveyor belt tracking systems, there are two primary types: manual and automatic. Each type has its own set of characteristics, advantages, and ideal applications. Understanding the differences between these systems can help in choosing the best option for your specific needs.
Manual Tracking Systems:
- Operation: Require human intervention to adjust the alignment of the conveyor belt.
- Components: Typically include basic mechanical adjustments, such as guiding rollers and tensioners.
- Cost: Generally less expensive initially, but may incur higher long-term costs due to frequent manual adjustments and potential downtime.
- Suitability: Best suited for smaller, simpler conveyor systems with less frequent misalignment issues.
Automatic Tracking Systems:
- Operation: Use sensors and actuators to continuously monitor and adjust the belt alignment without human intervention.
- Components: Include advanced technologies such as sensors, control units, and actuators that work together to maintain proper alignment.
- Cost: Higher initial cost, but offer savings in the long run due to reduced maintenance and downtime.
- Suitability: Ideal for larger, more complex conveyor systems with frequent or severe alignment issues.
Manual adjustments require operators to periodically inspect and adjust the conveyor belt’s alignment by manipulating rollers and the belt’s tension. While this method offers direct control, it is time-consuming and less precise.
Automatic conveyor belt tracking systems, on the other hand, offer significant advantages:
- Continuous Alignment: They continuously monitor and adjust the belt’s alignment without the need for manual intervention, ensuring constant operation.
- Reduced Downtime: By automatically correcting misalignments, these systems minimize operational disruptions.
- Lower Maintenance Costs: Automatic adjustments reduce the wear and tear on the belt and conveyor components, extending their lifespan.
- Increased Safety: Reduces the risk of accidents associated with manual adjustments.
- Enhanced Efficiency: Ensures the conveyor belt operates at optimal speeds, improving throughput.
- Energy Savings: Proper alignment reduces energy consumption by minimizing friction and resistance.
- Improved Product Quality: Prevents damage to materials being transported due to misalignment.
- Scalability: Easily integrated into larger automation systems, allowing for scalability in industrial operations.
Pneumatic Belt Tracking Systems
Pneumatic conveyor belt tracking systems utilize air pressure to maintain the belt’s alignment. They are particularly effective in environments where precision and responsiveness are critical.
- Rapid Response: Quick adjustments to belt alignment in response to the slightest deviations.
- Low Maintenance: Fewer moving parts reduce the need for maintenance.
- Highly Adjustable: Can be finely tuned for specific operational requirements.
- Environmentally Resistant: Effective in harsh or wet environments.
- Energy Efficient: Uses minimal energy to operate.
- Versatile Applications: Suitable for lightweight to medium-weight belts.
- Safety: Reduces the need for manual intervention, enhancing safety.
- Durability: Designed to withstand continuous use in industrial settings.
Conveyor Belt Tracking Rollers
Conveyor belt tracking rollers are specially designed rollers that help maintain the belt’s alignment by guiding it back to the center path if it starts to drift.
- Self-Adjusting: Rollers automatically adjust the belt’s position.
- Low Friction: Designed to minimize friction and wear on the belt.
- Easy Installation: Can be retrofitted to existing conveyor systems.
- Versatile: Suitable for various belt widths and speeds.
- Durable: Made from materials resistant to wear and corrosion.
- Preventative Maintenance: Help identify alignment issues before they cause significant damage.
- Cost-Effective: A cost-efficient solution for maintaining belt alignment.
- Improved Conveyor Performance: Enhances the overall performance and reliability of the conveyor system.
Belt Tracking Sensors
Conveyor belt tracking sensors utilize advanced technology to detect misalignments and initiate corrections, ensuring the belt remains centered.
- Real-Time Monitoring: Continuously monitor the belt’s position.
- Precision: Offer high levels of alignment accuracy.
- Adaptability: Can be programmed for different conveyor specifications.
- Early Detection: Identify potential misalignment issues early.
- Integration: Easily integrated into existing control systems.
- Data Collection: Collect data for predictive maintenance and operational analysis.
- Versatility: Suitable for various industries and belt types.
- Reduced Manual Inspection: Minimize the need for physical inspections.
- Enhanced Safety: Lower the risk of accidents related to belt misalignment.
Conveyor Belt Trainers
Conveyor belt trainers are specialized conveyor belt tracking devices designed to correct misalignments through gentle guidance, focusing on minimal intervention for maximum effect.
- Proactive Alignment: Actively maintain the belt’s central alignment.
- Minimal Contact: Reduce wear by minimizing contact with the belt.
- Long-Term Solution: Offer a sustainable solution to alignment issues.
- Ease of Installation: Simple to install and adjust.
- Compatibility: Work with a wide range of belt sizes and types.
- Low Maintenance: Require minimal upkeep.
- Efficiency: Improve the conveyor’s operational efficiency.
- Cost Savings: Reduce costs associated with misalignment damages.
- Safety Improvements: Enhance operational safety by preventing misalignment-related incidents.
Each type of conveyor belt tracking system offers unique benefits, tailored to different operational needs and environments. From manual to highly sophisticated sensor-based systems, the choice of a conveyor belt tracking system significantly impacts the efficiency, safety, and maintenance costs of conveyor operations.

5 Basic Conveyor Belt Tracking Rules To Follow
Proper conveyor belt tracking is essential for efficient operation and minimizing downtime in industrial settings. Adhering to a few basic rules can ensure your conveyor belt tracking system functions smoothly. Here are five fundamental rules to follow:
Rule 1: Ensure the Conveyor Structure is Stable and Rigid
A stable and rigid supporting structure is the foundation of an effective conveyor belt tracking system. Any movement or flexing in the structure can lead to misalignment. Here’s how to ensure stability:
- Solid Construction: Use high-quality materials and ensure that all structural components are securely fastened.
- Regular Inspections: Perform routine checks to identify any signs of wear, loosening, or damage in the conveyor structure.
- Avoid Modifications: Unplanned modifications to the structure can affect the alignment and stability of the system.
Rule 2: Align Pulleys and Rollers Correctly
Proper alignment of pulleys and rollers is crucial for maintaining belt tracking. Misaligned components can cause the belt to drift off-center. Follow these steps to ensure correct alignment:
- Square to the Belt Path: Ensure that all pulleys and rollers are square to the conveyor belt’s running direction.
- Use Alignment Tools: Utilize straight edges, laser levels, or alignment tools to check and adjust the alignment.
- Secure Fastenings: Make sure all mounting bolts and brackets are tightened properly to prevent movement.
Rule 3: Maintain Appropriate Belt Tension
Correct belt tension is vital for effective tracking. Too much or too little tension can lead to misalignment and excessive wear. Here’s how to maintain proper tension:
- Measure Tension: Use a tension gauge to measure the belt tension according to the manufacturer’s specifications.
- Adjust Gradually: Make incremental adjustments to the tension to achieve the desired level, and avoid sudden changes that can cause belt damage.
- Check Regularly: Regularly monitor the tension and adjust as needed to compensate for belt stretch or other factors.
Rule 4: Keep the Conveyor Clean
Cleanliness is essential for optimal conveyor belt tracking. Dirt, debris, and build-up on the belt or conveyor components can lead to misalignment. Ensure cleanliness with these practices:
- Regular Cleaning: Implement a routine cleaning schedule to remove any accumulated dirt or debris from the belt and surrounding components.
- Use Scrapers and Brushes: Install belt scrapers and brushes to continuously clean the belt as it runs.
- Inspect Frequently: Frequently inspect the conveyor for any signs of material build-up and clean as necessary.
Rule 5: Load Materials Evenly
Even loading is crucial for maintaining proper belt tracking. Uneven loads can cause the belt to shift and drift off-center. Follow these guidelines to ensure even loading:
- Centralize Loads: Ensure that materials are loaded evenly across the width of the conveyor belt.
- Adjust Loading Points: If materials consistently load off-center, adjust the loading points or chutes to distribute the load more evenly.
- Monitor and Correct: Continuously monitor the loading process and make corrections as needed to maintain even distribution.
Adhering to these five basic rules can significantly enhance the performance of your conveyor belt tracking system. Ensuring a stable structure, correct alignment of pulleys and rollers, maintaining proper belt tension, keeping the conveyor clean, and loading materials evenly will help keep your conveyor system running smoothly and efficiently. Regular inspections and maintenance are key to preventing tracking issues and minimizing downtime, ultimately leading to a more productive and cost-effective operation.
How to Adjust a Conveyor Belt to Run Straight
Proper alignment is crucial for the effective operation of any conveyor belt tracking system. Misalignment can cause a variety of issues, including material spillage, excessive wear on the belt, and damage to the conveyor structure. Here’s a comprehensive guide on how to manually adjust a conveyor belt to ensure it runs straight.
Step-by-Step Adjustment Procedure
Preparation and Safety Measures:
- Ensure the conveyor is turned off and locked out to prevent accidental startup.
- Gather necessary tools and protective gear before starting the adjustment process.
Identify the Misalignment Issue:
- Inspect the entire length of the conveyor belt to identify areas where the belt is off-center.
- Note any visible damage or excessive wear on the belt or the structure that might be causing the misalignment.
Adjust the Tail Pulley:
- Loosen the bolts holding the tail pulley in place. The tail pulley is located at the end of the conveyor belt where the belt returns to the start.
- Use a rubber mallet to gently tap the tail pulley in the direction opposite to the belt’s misalignment.
- Make small, incremental adjustments and check the belt’s position frequently to avoid over-correction.
Adjust the Snub Rollers:
- Snub rollers are positioned near the head and tail pulleys to help guide the belt. Loosen the mounting bolts on the snub roller that is closest to the area of misalignment.
- Adjust the snub roller by rotating it slightly to change the angle of contact with the belt.
- Tighten the bolts once the belt is centered and recheck the alignment.
Align the Return Idlers:
- Check the alignment of the return idlers located on the underside of the conveyor belt.
- Loosen the mounting brackets and adjust the idlers so they are perpendicular to the belt’s travel path.
- Retighten the brackets and ensure the idlers are evenly spaced to provide uniform support.
Detailed Guide on Manual Adjustment Techniques
Manual adjustment of a conveyor belt tracking system involves precise and careful handling to ensure accurate alignment. Here’s a detailed guide:
Initial Assessment:
- Visually inspect the belt and its components for any signs of wear or damage that might affect tracking.
- Use a straight edge or laser level to check the alignment of the pulleys and rollers.
Step-by-Step Adjustment:
- Begin with the tail pulley, as it has the most significant impact on tracking. Adjust it first, then move to the head pulley if necessary.
- Always make small adjustments and observe the belt’s reaction. It’s better to make multiple minor corrections than one large adjustment.
Fine-Tuning:
- After initial adjustments, run the conveyor belt at its normal operating speed and load.
- Observe the belt for any drifting or misalignment and make further adjustments as needed.
- Continue fine-tuning the pulleys, rollers, and idlers until the belt runs smoothly and stays centered.
Tools and Equipment Needed for Proper Alignment
To achieve precise alignment, the following tools and equipment are essential:
- Wrenches and Sockets: For loosening and tightening bolts on pulleys, rollers, and idlers.
- Rubber Mallet: To gently tap and adjust components without causing damage.
- Straight Edge or Laser Level: For checking the alignment of pulleys and rollers.
- Measuring Tape: To ensure consistent spacing and positioning of components.
- Protective Gear: Including gloves, safety glasses, and hard hats for safety during adjustments.
Tips for Ensuring Accurate Adjustments
- Consistency is Key: Make small, consistent adjustments rather than large, erratic ones.
- Double-Check Measurements: Always verify your adjustments with measuring tools to ensure accuracy.
- Document Changes: Keep a record of all adjustments made for future reference and troubleshooting.
- Monitor Regularly: Even after achieving proper alignment, regularly inspect the conveyor belt tracking system to maintain optimal performance.
- Seek Professional Help: If persistent issues arise, consider consulting with a professional or the conveyor system manufacturer for specialized assistance.
By following these detailed steps and using the right tools, you can effectively adjust your conveyor belt tracking system to ensure it runs straight and efficiently, minimizing downtime and maintenance costs.
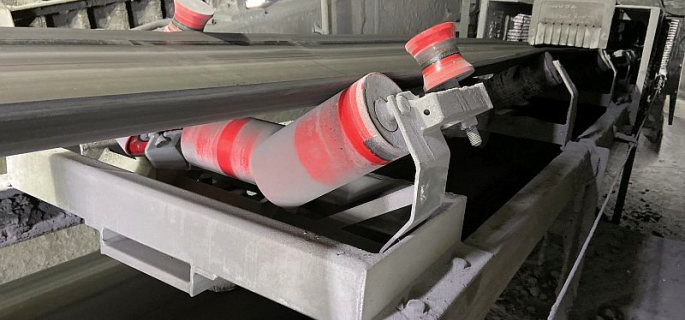
Key Features of Effective Conveyor Belt Tracking Systems
Effective conveyor belt tracking systems are essential for the smooth operation of conveyor belts, ensuring they remain aligned, which in turn minimizes downtime and maximizes productivity. The key features of these systems are critical in achieving optimal performance and reliability. Here are eight key features that define effective conveyor belt tracking systems:
- Automatic Adjustments: One of the most crucial features of an effective conveyor belt tracking system is its ability to make automatic adjustments. This ensures continuous, real-time realignment of the conveyor belt, eliminating the need for manual intervention and significantly reducing the risk of misalignment-related issues.
- Durability and Reliability: The design and construction of a conveyor belt tracking system greatly influence its durability and reliability. Systems made from high-quality materials that can withstand the harsh conditions of industrial environments are less likely to fail and require less maintenance over their lifespan.
- Compatibility with Various Belt Sizes and Types: An effective conveyor belt tracking system must be adaptable to different conveyor belt dimensions and materials. This flexibility ensures that the system can be implemented across various industries and applications, making it a versatile solution for conveyor belt alignment.
- Safety and Efficiency Improvements: Properly aligned conveyor belts are less prone to slippage, material spillage, and other operational hazards, thereby enhancing workplace safety. Additionally, efficient conveyor belt tracking systems contribute to smoother operations, reducing energy consumption and increasing throughput.
- Easy Integration: Effective conveyor belt tracking systems should be easy to integrate with existing conveyor systems without requiring extensive modifications. This allows for seamless implementation and minimizes disruptions to operations.
- Sensitivity to Misalignment: High-quality conveyor belt tracking systems are highly sensitive to even minor misalignments. This sensitivity ensures that corrections are made promptly before misalignments can escalate into more significant issues.
- Minimal Maintenance Requirements: Systems designed to operate with minimal maintenance not only reduce downtime but also lower the overall cost of ownership. Features such as self-lubricating components and wear-resistant materials contribute to a system’s low maintenance needs.
- User-Friendly Interface: An effective conveyor belt tracking system should come with a user-friendly interface, allowing operators to easily monitor the system’s status and make adjustments as necessary. This accessibility ensures that operators can quickly respond to any issues that may arise.
These key features collectively ensure that a conveyor belt tracking system can provide continuous, reliable service, maintaining the alignment of the conveyor belt and thereby enhancing the efficiency, safety, and productivity of conveyor operations. The incorporation of these features into a conveyor belt tracking system is essential for meeting the demands of modern industrial applications.
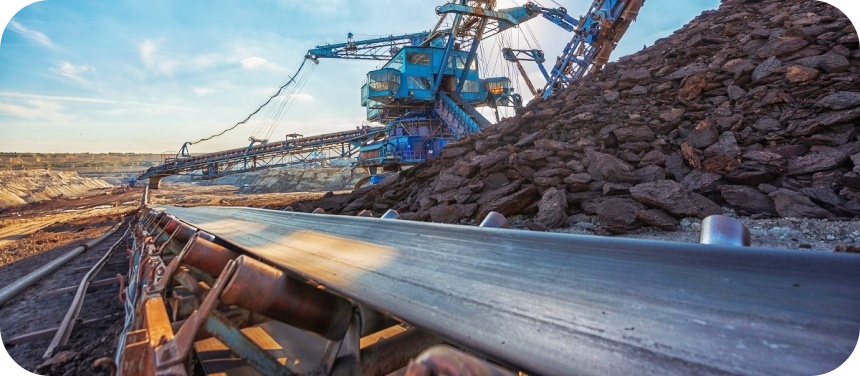
Leading Solutions in Conveyor Belt Tracking System
The efficiency and safety of conveyor systems significantly depend on the precision of conveyor belt tracking. Misalignment can lead to increased wear, material spillage, and potential safety hazards. Recognizing this, several companies have developed leading solutions in conveyor belt tracking system, each with unique features and benefits. These systems are designed to ensure optimal belt alignment, enhancing the operational efficiency and longevity of conveyor systems.
Flexco’s Approach
Flexco stands out in the conveyor belt tracking market with its innovative solutions, including belt positioners, trackers, and trainers. Their systems are designed to address the common challenges of belt misalignment in various industrial settings.
- Pivot and Tilt Technology: Automatically adjusts the belt’s position to ensure it remains centered.
- Durable Construction: Built to withstand harsh industrial environments, ensuring long-term reliability.
- Easy Installation: Designed for quick and straightforward installation, minimizing downtime.
- Versatile Application: Suitable for a wide range of belt widths and speeds.
- Reduced Belt Wear: Minimizes the wear on the belt by keeping it properly aligned.
- Improved Safety: Reduces the risk of accidents associated with belt misalignment.
- Energy Efficiency: Promotes smoother operation, reducing energy consumption.
- Maintenance Friendly: Easy to maintain, reducing long-term operational costs.
Eckels-Bilt Automatic Belt Trackers
Eckels-Bilt offers a comprehensive range of automatic belt tracking systems that are engineered to provide precise belt alignment under various operational conditions.
- Automatic Detection and Correction: Continuously monitors and corrects belt misalignment, ensuring optimal performance.
- Wide Range of Applications: Effective in both light-duty and heavy-duty environments.
- Increased Conveyor Belt Life: Reduces wear and tear on the belt, extending its operational lifespan.
- Lower Maintenance Costs: Decreases the need for manual adjustments and repairs.
- High Adaptability: Compatible with different conveyor belt sizes and materials.
- Enhanced Operational Efficiency: Maintains smooth and consistent belt movement.
- Robust Design: Built to endure the demands of continuous industrial use.
- Safety Improvement: Minimizes the risk of spillage and accidents related to misalignment.
Martin® Tracker™
Martin Engineering’s Martin® Tracker™ is renowned for its patented steering/training system, which ensures the belt remains on its intended path.
- Patented Steering/Training System: Offers precise, immediate adjustments for optimal alignment.
- Immediate Correction: Detects and corrects misalignments as they occur.
- Durable and Reliable: Engineered for durability in the toughest environments.
- Easy to Install: Can be quickly and easily installed on existing conveyor systems.
- Minimizes Material Spillage: Keeps materials on the belt, reducing waste and cleanup.
- Extends Belt and Component Life: Reduces wear on the belt and conveyor components.
- Energy Efficient: Ensures the conveyor operates efficiently, saving energy costs.
- Safety Enhancements: Designed to improve the overall safety of the conveyor operation.
Flexco PT Smart Belt Trainer
Flexco PT Smart Belt Trainer
- Features: Utilizes Pivot and Tilt technology for immediate response to misalignment.
- Benefits: Suitable for belts with a maximum tension of up to 1600 PIW and widths from 18 to 72 inches. Provides reliable tracking for medium-duty applications.
Flexco PTEZ Belt Trainer
Flexco PTEZ Belt Trainer
- Features: Designed for belts with a maximum tension of up to 2400 PIW. Incorporates advanced sensor technology for precise tracking.
- Benefits: Ideal for heavy-duty applications, with a belt width range of 18 to 84 inches. Offers robust performance and longevity.
Tru-Trac Return Tracker
Tru-Trac Return Tracker
- Features: Uses a patented system to provide continuous adjustment and alignment.
- Benefits: Suitable for various belt widths and operating conditions. Known for its durability and maintenance-free operation.
Martin Tracker HD
Martin Tracker HD
- Features: Heavy-duty design for wider, thicker belts moving at higher speeds.
- Benefits: Ensures optimal tracking for high-load applications. Reduces edge damage and maintenance expenses.
Benetech MaxZone Tracker
Benetech MaxZone Tracker
- Features: Robust construction with hardened steel components.
- Benefits: Provides instant response to misalignment, suitable for belts ranging from 450mm to 2600mm in width. Low maintenance and high durability.
These leading solutions in conveyor belt tracking systems demonstrate the industry’s commitment to innovation and safety. By incorporating such technologies, companies can significantly improve the reliability, efficiency, and safety of their conveyor operations, ensuring materials are transported smoothly and effectively throughout their processes.
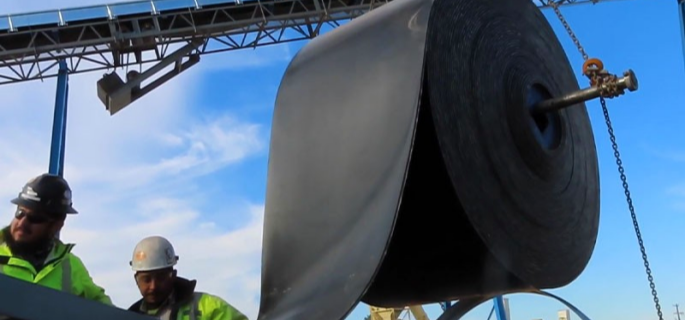
Troubleshooting Common Tracking Issues in a Conveyor Belt Tracking System
Ensuring that a conveyor belt tracking system operates efficiently is critical for minimizing downtime and maintaining productivity. Misalignment issues can cause significant problems, but with a systematic approach to troubleshooting, these can be effectively addressed.
Identifying and Resolving Misalignment Problems
Common Causes of Misalignment
Misalignment in a conveyor belt tracking system can result from various factors. Identifying the root cause is the first step in troubleshooting. Here are some common causes:
- Improper Installation: Incorrect installation of pulleys, idlers, or rollers can lead to tracking issues.
- Belt Tension: Uneven or inadequate belt tension can cause the belt to drift off-center.
- Worn Components: Worn or damaged pulleys, rollers, and bearings can impact alignment.
- Material Build-up: Accumulation of dirt, debris, or material on components can alter the belt path.
- Off-Center Loading: Uneven loading of materials can cause the belt to shift to one side.
- Environmental Factors: Temperature changes, moisture, and other environmental conditions can affect belt tracking.
Step-by-Step Troubleshooting Guide
Step 1: Initial Inspection
- Safety First: Ensure the conveyor is turned off and locked out.
- Visual Check: Inspect the entire conveyor system for visible signs of wear, damage, or debris.
- Component Check: Examine pulleys, idlers, and rollers for proper alignment and condition.
Step 2: Checking Belt Tension
- Measure Tension: Use a tension gauge to check if the belt tension is within the manufacturer’s recommended range.
- Adjust Tension: If the tension is uneven, adjust it using the tensioning mechanism until it is uniform across the belt.
Step 3: Cleaning and Maintenance
- Clean Components: Remove any build-up of dirt, debris, or material from pulleys, rollers, and the belt itself.
- Lubricate Bearings: Ensure that all bearings are properly lubricated to prevent friction and wear.
Step 4: Aligning Pulleys and Rollers
- Use a Straight Edge or Laser Level: Check the alignment of all pulleys and rollers. They should be square to the conveyor frame and parallel to each other.
- Adjust as Needed: Loosen the mounting bolts and adjust the components until they are properly aligned, then retighten the bolts securely.
Step 5: Load Distribution
- Check Loading Practices: Ensure that materials are loaded evenly across the width of the belt.
- Adjust Loading Points: If materials are consistently loaded off-center, adjust the loading points or chutes to distribute the load more evenly.
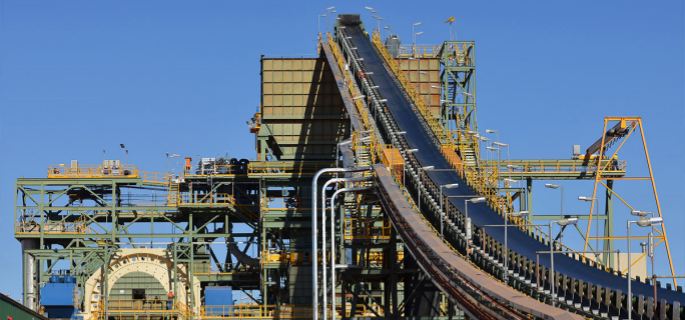
Installation and Maintenance of Conveyor Belt Tracking System
Ensuring the optimal performance of conveyor belt tracking systems involves two critical phases: proper installation and diligent maintenance. These phases are foundational to achieving a seamless operation, minimizing downtime, and extending the lifespan of conveyor systems. The installation process lays the groundwork for the tracking system’s functionality, requiring precision and adherence to best practices. Following installation, routine maintenance becomes the key to sustaining performance and preventing the premature wear of both the conveyor belt and the tracking system. Below, we delve into detailed tips and practices for both installation and maintenance, aiming to provide a comprehensive guide for achieving the best outcomes with conveyor belt tracking systems.
Installation Tips for Conveyor Belt Tracking Systems
The installation of conveyor belt tracking systems is a pivotal step that determines the efficiency and effectiveness of the conveyor operation. A well-executed installation not only ensures optimal performance from the outset but also reduces the need for corrective maintenance down the line. Here are essential tips to consider:
- Alignment Check: Begin with a thorough check to ensure the conveyor frame and pulleys are perfectly aligned. Misalignments can significantly hinder the tracking system’s effectiveness.
- Follow Manufacturer Instructions: Strict adherence to the manufacturer’s installation guidelines is crucial to avoid common pitfalls and ensure the system is set up correctly.
- Proper Tensioning: Correctly tensioning the conveyor belt is vital, as improper tension can negatively impact the tracking system’s ability to function.
- Sensor Positioning: Accurately position any sensors to effectively detect belt misalignment, a crucial step for systems relying on sensor technology.
- Test Before Full Operation: Conduct controlled tests to observe the tracking system’s performance, making adjustments as necessary before full-scale operation.
- Training for Personnel: Ensure that installation personnel are well-trained and understand the conveyor belt tracking system’s mechanics and requirements.
- Use of Correct Tools: Employ the appropriate tools and equipment for the installation to prevent damaging the tracking system’s components.
- Environmental Considerations: Account for the operating environment’s conditions, such as temperature and humidity, which can affect the system’s performance.
- Regular Inspection Post-Installation: Implement a schedule for regular post-installation inspections to ensure ongoing correct alignment and functionality.
Routine Maintenance Practices for Conveyor Belt Tracking Systems
After a successful installation, maintaining the conveyor belt tracking system is paramount to ensure its long-term reliability and efficiency. Routine maintenance practices are essential for preventing operational issues and extending the system’s lifespan. Here are key maintenance practices:
- Regular Inspections: Perform regular inspections to identify early signs of wear, tear, or misalignment, allowing for timely corrective actions.
- Cleanliness: Maintain cleanliness around the conveyor belt and tracking system to prevent debris accumulation that could affect operation.
- Lubrication: Regularly lubricate moving parts to reduce friction and wear, crucial for the system’s longevity.
- Tension Monitoring: Continuously monitor and adjust the belt’s tension to ensure it remains within optimal parameters for tracking performance.
- Component Replacement: Promptly replace any worn or damaged components to maintain the system’s integrity and functionality.
- Update Training: Keep maintenance personnel informed about the latest best practices and technological advancements in conveyor belt tracking maintenance.
- Record Keeping: Keep detailed maintenance records, including inspections, repairs, and replacements, to track the system’s health and performance over time.
- Feedback Loop: Establish a feedback mechanism with operators to quickly identify and address any issues or inefficiencies with the tracking system.
- Emergency Preparedness: Develop emergency procedures for addressing sudden misalignments or system failures to minimize downtime and potential damage.
By following these comprehensive installation and maintenance guidelines, organizations can maximize the effectiveness and longevity of their conveyor belt tracking systems, ensuring smooth and efficient conveyor operations.
Case Studies and Success Stories of Conveyor Belt Tracking System
The implementation of advanced conveyor belt tracking systems has proven to be a game-changer for businesses across various industries. These systems not only enhance operational efficiency but also significantly reduce maintenance costs and downtime. Below are real-world examples showcasing the benefits businesses have experienced from integrating sophisticated conveyor belt tracking systems into their operations.
- Mining Sector Transformation: A leading mining company faced frequent conveyor belt misalignments, leading to substantial material spillage and downtime. After installing a state-of-the-art conveyor belt tracking system, they reported a 75% reduction in downtime and a significant decrease in spillage, resulting in improved safety and a boost in overall productivity.
- E-commerce Giant Optimizes Sortation Facility: An e-commerce giant struggled with package misrouting due to conveyor belt misalignments in their vast sortation facility. The implementation of an automatic conveyor belt tracking system streamlined their operations, reducing misrouted packages by over 90% and increasing sortation accuracy and efficiency.
- Food Processing Facility Enhances Hygiene and Efficiency: A food processing plant dealing with strict hygiene standards integrated a conveyor belt tracking system designed for easy cleaning and minimal maintenance. This move not only ensured compliance with hygiene regulations but also resulted in a 20% increase in production efficiency due to reduced downtime and maintenance needs.
- Automotive Manufacturer Cuts Costs: An automotive manufacturing plant implemented a custom conveyor belt tracking system to handle the precise movement of parts along the assembly line. This solution reduced belt wear and tear by 40% and cut maintenance costs by 30%, showcasing the system’s impact on operational cost savings.
- Recycling Plant Sees Environmental and Economic Gains: A recycling facility faced challenges with belt misalignment causing material spillage and contamination. The installation of an environmentally friendly conveyor belt tracking system significantly reduced spillage, improving material recovery rates and reducing environmental impact, while also yielding economic benefits from increased material salvage.
- Airport Baggage Handling System Upgrade: A major international airport upgraded its baggage handling system with advanced conveyor belt tracking technology. This enhancement led to a 50% reduction in baggage handling issues, improving passenger experience and operational reliability, especially during peak travel seasons.
- Cement Industry Efficiency Boost: A cement manufacturing plant struggling with dust and debris affecting their conveyor belts’ alignment installed a rugged conveyor belt tracking system. The new system was resistant to harsh conditions, leading to a 60% decrease in unscheduled maintenance and a significant increase in production uptime.
These case studies underscore the versatility and effectiveness of conveyor belt tracking system across different sectors. By addressing specific challenges related to belt misalignment, these systems not only improve operational efficiency and safety but also contribute to significant cost savings and productivity gains. The success stories highlight the critical role of advanced conveyor belt tracking system in optimizing conveyor operations and achieving business objectives.
Discover premium conveyor belts – contact us today!
Get customized conveyor belt solutions – reach out now!
FAQs about Conveyor Belt Tracking System
The best way to track a conveyor belt involves a combination of proper installation, regular maintenance, and the use of appropriate tracking systems. Initially, ensure that all pulleys, rollers, and other components are aligned and square to the belt’s running direction. Use a straight edge or laser level for precise alignment. Regularly check and adjust belt tension to ensure it is even across the width of the belt. Implement a routine cleaning schedule to remove any build-up of dirt or debris that could affect alignment. For more advanced tracking, consider using automatic conveyor belt tracking systems that use sensors and actuators to continuously monitor and adjust the belt’s position. These systems provide real-time corrections and are particularly beneficial for large or complex conveyor systems. Lastly, ensure that materials are loaded evenly onto the belt to prevent shifting and misalignment. By following these steps, you can maintain optimal belt tracking and improve the efficiency and longevity of your conveyor system.
Conveyor tracking works by ensuring the belt remains centered and runs along its intended path without drifting to one side. This process typically involves several key components and technologies. Sensors are used to detect any deviation in the belt’s position. These sensors can be mechanical, optical, or ultrasonic, depending on the system. When a misalignment is detected, the sensors send a signal to a control unit, which processes the information and commands actuators to adjust tracking rollers or pulleys. These adjustments are made in real-time to correct the belt’s path and bring it back to the center. Some systems use pivoting rollers or tilting mechanisms to guide the belt. In more advanced systems, feedback loops continuously monitor the belt’s position, ensuring immediate and precise corrections. This automation reduces the need for manual intervention, minimizes downtime, and extends the life of the conveyor belt by preventing excessive wear and tear caused by misalignment.
Tracking a conveyor belt with return rollers involves ensuring that these rollers are correctly aligned and positioned to maintain the belt’s proper path. Start by inspecting the return rollers for any signs of wear, damage, or debris accumulation that could affect their performance. Next, ensure that the rollers are mounted squarely to the conveyor frame and parallel to each other. Use a straight edge or alignment tool to verify their position. Adjust the return rollers by loosening their mounting bolts and carefully repositioning them to correct any misalignment. Make small adjustments and observe the belt’s response to avoid over-correction. Return rollers can also be angled slightly in the direction of belt travel to help guide the belt back to the center. Regularly monitor the system and make adjustments as necessary to maintain optimal alignment. Additionally, maintaining even belt tension and ensuring proper loading practices can help keep the belt aligned and running smoothly with the aid of return rollers.
A conveyor belt delivery system is an automated system designed to transport materials or products efficiently within a facility. These systems are widely used in various industries, including manufacturing, warehousing, and logistics, to streamline the movement of goods from one point to another. The core component of a conveyor belt delivery system is the conveyor belt itself, which is a continuous loop of material that moves over rollers or pulleys. The belt is driven by a motorized pulley or drive roller that powers the belt’s movement. Conveyor belt delivery systems can be customized with different types of belts, such as flat, modular, or cleated, to handle specific materials and applications. They can also include additional features like sorting mechanisms, automated controls, and sensors to optimize efficiency and accuracy. By automating the transport process, conveyor belt delivery systems reduce manual labor, increase throughput, and improve overall operational efficiency. These systems are essential for modern industrial and commercial operations, providing a reliable and cost-effective solution for material handling.
Last Updated on June 21, 2024 by Jordan Smith
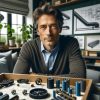
Jordan Smith, a seasoned professional with over 20 years of experience in the conveyor system industry. Jordan’s expertise lies in providing comprehensive solutions for conveyor rollers, belts, and accessories, catering to a wide range of industrial needs. From initial design and configuration to installation and meticulous troubleshooting, Jordan is adept at handling all aspects of conveyor system management. Whether you’re looking to upgrade your production line with efficient conveyor belts, require custom conveyor rollers for specific operations, or need expert advice on selecting the right conveyor accessories for your facility, Jordan is your reliable consultant. For any inquiries or assistance with conveyor system optimization, Jordan is available to share his wealth of knowledge and experience. Feel free to reach out at any time for professional guidance on all matters related to conveyor rollers, belts, and accessories.