Essential Conveyor Belt Tracking Troubleshooting Techniques
Conveyor belt systems are integral to various industries, enabling efficient material handling and transportation. However, maintaining the correct tracking of these belts is crucial for optimal performance. Proper conveyor belt tracking ensures the belt runs smoothly along the intended path, preventing disruptions and potential damage. Incorrect tracking can lead to common problems such as belt misalignment, uneven wear, and operational inefficiencies. Addressing these issues promptly through effective conveyor belt tracking troubleshooting is essential. This comprehensive guide will delve into the importance of accurate tracking, identify common misalignment problems, and provide practical solutions to ensure your conveyor belt system operates flawlessly.
Conveyor Belt Misalignment in Conveyor Belt Tracking Troubleshooting
Conveyor belt misalignment is a common issue in many industrial settings, leading to significant operational inefficiencies and safety hazards. Understanding how conveyor belts can track incorrectly and the implications of these misalignments is essential for effective conveyor belt tracking troubleshooting.
How Conveyor Belts Track Incorrectly
Conveyor belts can track incorrectly due to various reasons, including improper installation, uneven loading, or worn-out components. When a belt does not align properly along the conveyor frame, it may drift to one side or another, resulting in misalignment. This incorrect tracking can cause the belt to rub against the conveyor structure, leading to accelerated wear and tear.
Several factors contribute to improper conveyor belt tracking:
- Poor Belt Tension: Incorrect tension can cause the belt to wander off its path. Too much tension can pull the belt too tight, while too little tension can cause slippage and misalignment.
- Faulty Pulley Alignment: Misaligned pulleys can cause the belt to deviate from its intended path. Even minor deviations in pulley alignment can result in significant tracking problems over time.
- Damaged or Worn Components: Components like rollers, idlers, and bearings can wear out or get damaged, causing the belt to misalign. Regular maintenance checks are essential to identify and replace these components before they cause tracking issues.
- Improper Loading: Uneven loading of materials on the conveyor belt can lead to misalignment. When the load is not distributed evenly, it can cause the belt to skew and track incorrectly.
- Environmental Factors: External factors such as temperature changes, moisture, and debris can affect belt alignment. Environmental conditions must be controlled or mitigated to ensure proper belt tracking.
The Impact of Misaligned Belts on Operations and Safety
Misaligned conveyor belts can have severe consequences for both operations and safety.
- Reduced Efficiency: Misaligned belts can slow down production processes, as the belt may need frequent adjustments to stay on track. This reduces overall operational efficiency and increases downtime.
- Increased Wear and Tear: When a conveyor belt tracks incorrectly, it rubs against the conveyor frame and other components, causing accelerated wear and tear. This leads to more frequent replacements and higher maintenance costs.
- Product Damage: Misalignment can cause products to shift or fall off the belt, resulting in damage and loss. This is particularly problematic in industries handling fragile or perishable goods.
- Safety Hazards: Misaligned belts pose safety risks to workers. A belt that frequently slips or derails can cause accidents, injuries, or even fatalities in severe cases.
- Energy Inefficiency: Misaligned belts require more energy to operate, as additional friction and resistance increase the power needed to drive the belt. This leads to higher energy costs and a larger carbon footprint.
Key Terms Definition: Alignment, Tracking, Misalignment
To effectively address conveyor belt tracking troubleshooting, it is important to understand the key terms associated with belt alignment:
- Alignment: This refers to the proper positioning of the conveyor belt and its components, ensuring the belt runs straight along the intended path without deviation. Proper alignment is critical for optimal belt performance and longevity.
- Tracking: Tracking involves maintaining the belt’s alignment along the conveyor structure. It includes adjusting the belt tension, pulley alignment, and other factors to keep the belt on its designated path. Proper tracking ensures the belt operates smoothly and efficiently.
- Misalignment: Misalignment occurs when the conveyor belt deviates from its intended path. This can result from improper installation, worn-out components, or environmental factors. Misalignment leads to various operational and safety issues, as previously discussed.
Understanding these terms and their implications is crucial for effective conveyor belt tracking troubleshooting. Proper alignment and tracking are essential for maintaining the efficiency, safety, and longevity of conveyor belt systems. Regular maintenance checks, prompt repairs, and careful monitoring of environmental conditions can help prevent misalignment and ensure smooth conveyor belt operations.
Common Conveyor Belt Tracking Problems in Conveyor Belt Tracking Troubleshooting
When it comes to conveyor belt tracking troubleshooting, understanding the common problems that can arise is crucial. These issues often lead to significant operational disruptions and maintenance challenges. This section delves into three prevalent conveyor belt tracking problems: tracking to one side, irregular wear and tear on the belt edges, and slipping off the pulleys.
Conveyor Belt Tracking to One Side
One of the most common issues encountered in conveyor belt tracking troubleshooting is the belt tracking to one side. This problem can occur due to several reasons, including improper belt tension, misaligned pulleys, and uneven loading of the belt.
Causes:
- Improper Belt Tension: When the tension is not evenly distributed across the belt, it can cause the belt to pull to one side. This is often due to uneven tension settings or worn-out tensioners.
- Misaligned Pulleys: If the pulleys are not aligned correctly, the belt will naturally drift towards one side. Even minor misalignments can lead to significant tracking issues over time.
- Uneven Loading: When materials are not loaded evenly onto the belt, it can cause an imbalance, leading to the belt tracking to one side. This is particularly common in systems where materials are manually loaded or when the loading equipment is not properly calibrated.
Solutions:
- Adjust Belt Tension: Regularly check and adjust the belt tension to ensure it is evenly distributed. Replace any worn-out tensioners to maintain proper tension.
- Align Pulleys: Use precision tools to ensure pulleys are aligned correctly. Regularly inspect pulley alignment and make necessary adjustments.
- Even Loading: Ensure materials are loaded evenly across the belt. Calibrate loading equipment to maintain a balanced load distribution.
Irregular Wear and Tear on the Belt Edges
Irregular wear and tear on the belt edges is another common problem addressed in conveyor belt tracking troubleshooting. This issue often results from the belt rubbing against the conveyor structure or other components, leading to accelerated wear.
Causes:
- Belt Misalignment: When the belt is misaligned, it can rub against the conveyor frame, causing irregular wear on the edges.
- Damaged Rollers or Idlers: Worn-out or damaged rollers and idlers can create uneven surfaces, causing the belt to wear irregularly.
- External Debris: Debris and contaminants on the belt or conveyor structure can cause abrasive wear on the belt edges.
Solutions:
- Correct Misalignment: Regularly inspect and adjust the belt alignment to prevent rubbing against the conveyor structure.
- Replace Damaged Components: Inspect rollers and idlers for damage and replace them as needed to ensure a smooth surface for the belt.
- Clean the Conveyor: Implement regular cleaning schedules to remove debris and contaminants that could cause abrasive wear.
Conveyor Belt Slipping Off the Pulleys
A conveyor belt slipping off the pulleys is a severe issue in conveyor belt tracking troubleshooting that can lead to complete system shutdowns. This problem can be caused by various factors, including inadequate tension, misaligned pulleys, and worn-out components.
Causes:
- Inadequate Tension: If the belt tension is too low, it can cause the belt to slip off the pulleys. This can occur due to improper tension settings or worn-out tensioners.
- Misaligned Pulleys: Similar to tracking to one side, misaligned pulleys can cause the belt to slip off the pulleys. Proper alignment is crucial for keeping the belt on track.
- Worn-Out Components: Components such as pulleys, rollers, and bearings can wear out over time, leading to inadequate support and causing the belt to slip off.
Solutions:
- Adjust Belt Tension: Ensure the belt tension is adequate to prevent slipping. Regularly inspect and adjust the tension as needed.
- Align Pulleys: Use precise alignment tools to ensure pulleys are aligned correctly. Regular inspections and adjustments are necessary to maintain proper alignment.
- Replace Worn-Out Components: Regularly inspect and replace worn-out components to ensure the conveyor system functions smoothly.
Conveyor belt tracking troubleshooting involves identifying and addressing common issues such as tracking to one side, irregular wear and tear on the belt edges, and the belt slipping off the pulleys. By understanding the causes and implementing appropriate solutions, you can maintain the efficiency and longevity of your conveyor belt system, ensuring smooth and uninterrupted operations. Regular maintenance and proactive troubleshooting are key to preventing these common problems and optimizing your conveyor belt system’s performance.
Conveyor Belt Tracking Troubleshooting Techniques
Effective conveyor belt tracking troubleshooting is essential for maintaining the efficiency and longevity of your conveyor belt system. This section provides detailed techniques to address common tracking issues, including step-by-step instructions for adjusting the belt and tips for regular maintenance to ensure optimal tracking.
How to Adjust a Conveyor Belt to Run Straight
Proper adjustment of the conveyor belt is crucial to ensure it runs straight and performs efficiently. Here are the steps and tips for centering the belt on the pulley:
Step-by-Step Instructions on Adjusting the Belt Tension and Alignment
- Inspect the Conveyor System: Before making any adjustments, thoroughly inspect the entire conveyor system. Look for signs of wear, damage, or misalignment in the pulleys, rollers, and belt.
- Check the Belt Tension: Use a tension gauge to measure the belt tension. The tension should be uniform across the entire width of the belt. Adjust the tensioners to ensure even tension.
- Align the Pulleys: Use a laser alignment tool or a straight edge to check the alignment of the pulleys. Adjust the pulley positions as needed to ensure they are parallel and aligned with the conveyor frame.
- Center the Belt on the Pulleys: Manually adjust the belt position on the pulleys. This can be done by gradually moving the belt by hand and adjusting the take-up pulley to guide the belt into the correct position.
- Run the Conveyor and Monitor: After making adjustments, run the conveyor and monitor the belt’s movement. Make additional adjustments if necessary to ensure the belt tracks straight.
Tips for Centering the Belt on the Pulley
- Gradual Adjustments: Make small, incremental adjustments to the tension and alignment. Large adjustments can cause the belt to overcorrect and track incorrectly.
- Equal Tension: Ensure that the tension is evenly distributed across the belt. Uneven tension can cause the belt to drift to one side.
- Check for Obstructions: Remove any debris or obstructions that might be causing the belt to misalign. Even small objects can significantly impact belt tracking.
- Use Tracking Rollers: Install tracking rollers to help guide the belt and keep it centered. These rollers can automatically adjust to correct minor misalignments.
- Regular Monitoring: Continuously monitor the belt alignment and tension during operation. Regular checks can help identify and correct issues before they lead to significant problems.
Regular Maintenance for Optimal Tracking
Regular maintenance is a critical aspect of conveyor belt tracking troubleshooting. Implementing a maintenance schedule can prevent tracking issues and prolong the life of your conveyor system.
Scheduled Maintenance Checks: What to Inspect and When
- Daily Inspections: Perform daily visual inspections of the belt, pulleys, rollers, and tensioners. Look for signs of wear, damage, or misalignment.
- Weekly Checks: Conduct more detailed inspections weekly. Check the tension and alignment of the belt, and ensure all components are in good working condition.
- Monthly Maintenance: Perform thorough maintenance checks monthly. Inspect the condition of the rollers, pulleys, and bearings, and replace any worn-out parts.
- Quarterly Overhaul: Every quarter, perform an extensive overhaul of the conveyor system. This includes a complete inspection and maintenance of all components, as well as alignment and tension adjustments.
- Annual Review: Annually, review the overall performance of the conveyor system. Assess the efficiency of the belt tracking and make any necessary upgrades or replacements to improve performance.
How Cleaning and Debris Removal Affect Belt Tracking
- Preventing Obstructions: Regular cleaning prevents debris from accumulating on the belt and conveyor structure, which can cause misalignment.
- Reducing Abrasive Wear: Cleaning removes abrasive particles that can wear down the belt edges and components, reducing the risk of tracking issues.
- Improving Component Lifespan: Keeping the conveyor system clean prolongs the lifespan of components like rollers and pulleys, ensuring they function correctly and support proper belt tracking.
- Enhancing Belt Performance: A clean belt runs more smoothly and efficiently, reducing the likelihood of slippage and misalignment.
- Maintaining a Safe Environment: Regular cleaning maintains a safe working environment by preventing hazards associated with debris and misaligned belts.
Importance of Keeping Surrounding Environment Conducive for Proper Conveyor Belt Function
- Control Temperature: Extreme temperatures can affect the belt material and tension. Maintain a stable temperature in the operating environment to ensure consistent belt performance.
- Manage Humidity: High humidity levels can cause the belt to stretch and slip. Use dehumidifiers to control moisture levels and prevent tracking issues.
- Reduce Dust and Particles: Implement dust control measures to prevent particles from settling on the belt and causing abrasive wear or misalignment.
- Ensure Proper Ventilation: Adequate ventilation helps dissipate heat and maintain an optimal operating environment for the conveyor system.
- Regularly Inspect Surroundings: Regularly inspect the surrounding environment for potential issues that could impact belt tracking, such as structural vibrations or interference from nearby equipment.
By following these conveyor belt tracking troubleshooting techniques, you can ensure that your conveyor belt system operates smoothly and efficiently. Regular maintenance, proper adjustments, and a conducive operating environment are key to preventing and addressing tracking issues.
Advanced Troubleshooting in Conveyor Belt Tracking Troubleshooting
Advanced troubleshooting techniques are essential for addressing more complex conveyor belt tracking issues that go beyond basic maintenance and adjustments. This section provides a detailed guide on identifying and solving intricate tracking problems and offers comprehensive resources for in-depth troubleshooting and adjustments.
Conveyor Belt Problems and Solutions
Advanced conveyor belt tracking troubleshooting involves identifying the root causes of persistent or complex issues and implementing effective solutions. Here are some detailed steps and strategies for solving these problems:
Identifying Complex Tracking Issues
- Persistent Misalignment: When a belt consistently tracks to one side despite regular adjustments, it indicates an underlying problem. Inspect the entire conveyor system for structural misalignments, worn-out components, or improper installation.
- Variable Tracking: If the belt tracking issues vary under different operating conditions, it could be due to changes in load, temperature, or humidity. Monitor these variables to identify patterns and correlations with tracking problems.
- Unusual Wear Patterns: Irregular or unusual wear patterns on the belt edges or surface can indicate misalignment, improper tension, or damaged components. Detailed inspections can help pinpoint the exact cause.
- Frequent Slippage: Frequent slippage of the belt off the pulleys may be due to inadequate tension, pulley misalignment, or excessive load. A thorough examination of these factors is necessary.
- Noise and Vibration: Unusual noises or vibrations during conveyor operation can signal misalignment, damaged rollers, or other issues. Use diagnostic tools to identify and address these problems.
Solving Complex Tracking Issues
- Comprehensive Alignment Check: Use advanced alignment tools like laser alignment systems to ensure all components, including pulleys, rollers, and frames, are perfectly aligned. Regularly recheck alignment after making adjustments.
- Enhanced Tension Management: Implement precise tensioning devices and regularly calibrate them to maintain optimal belt tension. Consider using automatic tensioners for consistent performance.
- Component Replacement and Upgrades: Replace worn-out or damaged components with high-quality parts. Consider upgrading to more durable materials or advanced designs that offer better performance and longevity.
- Load Distribution Optimization: Ensure even load distribution across the belt. Use load sensors and monitoring systems to detect and correct imbalances in real-time.
- Environmental Control: Maintain a stable operating environment by controlling temperature, humidity, and dust levels. Use enclosures or barriers to protect the conveyor system from external environmental factors.
Conveyor Belt Tracking PDF
For those seeking comprehensive resources for in-depth conveyor belt tracking troubleshooting, detailed guides and PDFs can be invaluable. These resources provide step-by-step instructions, diagrams, and best practices for addressing complex tracking issues.
Comprehensive Resources for In-Depth Troubleshooting and Adjustments
- Detailed Guides: Look for PDFs that offer thorough explanations of common and complex tracking issues, complete with illustrations and diagrams. These guides should cover everything from basic adjustments to advanced troubleshooting techniques.
- Step-by-Step Instructions: Ensure the resources provide clear, step-by-step instructions for diagnosing and fixing tracking problems. Detailed procedures help ensure that even complex issues can be addressed systematically.
- Diagnostic Tools: High-quality troubleshooting PDFs often recommend specific diagnostic tools and techniques for identifying problems. These may include laser alignment tools, tension meters, and vibration analyzers.
- Maintenance Schedules: Comprehensive resources should include suggested maintenance schedules and checklists to ensure ongoing belt health and optimal tracking. Regular maintenance is key to preventing future issues.
- Case Studies and Examples: Look for guides that include case studies or real-world examples of tracking issues and solutions. Learning from others’ experiences can provide valuable insights and practical tips.
Accessing Conveyor Belt Tracking PDFs
- Manufacturer Resources: Many conveyor belt manufacturers offer detailed troubleshooting guides and PDFs on their websites. These resources are tailored to their specific products and can be highly useful.
- Industry Publications: Industry publications and websites often provide in-depth articles and downloadable PDFs on conveyor belt maintenance and troubleshooting. These resources are written by experts and cover a wide range of topics.
- Professional Organizations: Organizations like the Conveyor Equipment Manufacturers Association (CEMA) offer comprehensive guides and resources for conveyor belt tracking troubleshooting. These are often available to members or for purchase.
- Online Forums and Communities: Joining online forums and professional communities can provide access to shared resources, including troubleshooting guides and best practices from industry peers.
- Training Programs: Enrolling in training programs or workshops on conveyor belt maintenance and troubleshooting can provide access to exclusive materials and hands-on experience.
Advanced troubleshooting in conveyor belt tracking troubleshooting involves a detailed and systematic approach to identifying and solving complex issues. By utilizing comprehensive resources, detailed guides, and advanced tools, you can effectively address persistent tracking problems and ensure the efficient operation of your conveyor belt system. Regular maintenance and environmental control are also crucial for preventing future issues and maintaining optimal belt performance.
Specific Causes and Fixes in Conveyor Belt Tracking Troubleshooting
One of the most frequent and challenging issues in conveyor belt tracking troubleshooting is when the belt tracks to one side. This problem can lead to inefficiencies, increased wear, and potential safety hazards if not addressed promptly. Understanding the specific causes and implementing the appropriate fixes is essential for maintaining optimal belt performance.
Analyzing Reasons for Unilateral Tracking
Identifying the root causes of a conveyor belt tracking to one side is the first step in troubleshooting. Several factors can contribute to this issue:
- Improper Belt Tension: Uneven tension across the belt width can cause it to drift to one side. If the tension is higher on one side than the other, the belt will naturally move towards the side with less tension.
- Misaligned Pulleys and Rollers: Pulleys and rollers that are not perfectly aligned can force the belt to track incorrectly. Even minor misalignments can lead to significant tracking problems.
- Frame and Structure Issues: If the conveyor frame or structure is not level or has been distorted, it can cause the belt to track to one side. This is often due to installation errors or wear over time.
- Uneven Loading: When the load on the conveyor belt is not evenly distributed, it can create an imbalance that causes the belt to move to one side. This is especially common in systems where the load is manually placed or irregularly shaped.
- Belt Damage or Wear: Physical damage to the belt, such as cuts or tears, can affect its tracking. Worn edges or uneven wear patterns can also contribute to one-sided tracking.
Adjustments and Fixes for One-Sided Tracking Issues
Once the specific causes of unilateral tracking have been identified, appropriate adjustments and fixes can be applied to resolve the issue. Here are detailed steps and solutions:
Correcting Belt Tension
- Measure Tension Across Belt Width: Use a tension gauge to measure the tension at multiple points across the width of the belt. Ensure that the tension is uniform.
- Adjust Tensioners: If the tension is uneven, adjust the tensioners to balance the tension across the belt. Make small adjustments incrementally and recheck the tension until it is even.
- Replace Worn Tensioners: If the tensioners are worn or damaged, replace them to ensure they can maintain consistent tension.
Aligning Pulleys and Rollers
- Inspect Pulley and Roller Alignment: Use a laser alignment tool or a straight edge to check the alignment of all pulleys and rollers. They should be parallel to each other and the conveyor frame.
- Adjust Misaligned Components: If any pulleys or rollers are misaligned, adjust them according to the manufacturer’s specifications. Ensure they are securely fastened in place.
- Regular Alignment Checks: Implement a regular schedule for alignment checks to prevent future misalignment issues.
Addressing Frame and Structure Issues
- Check Conveyor Level: Use a level to check if the conveyor frame is perfectly horizontal. If it is not, adjust the supports or shims to level the frame.
- Inspect for Structural Damage: Look for any signs of structural damage or warping in the conveyor frame. Repair or replace damaged sections as needed.
- Proper Installation: Ensure the conveyor is installed correctly according to the manufacturer’s guidelines. Improper installation can lead to long-term tracking issues.
Ensuring Even Loading
- Distribute Load Evenly: Ensure that materials are loaded evenly across the belt. This may require adjusting loading procedures or equipment.
- Use Load Sensors: Implement load sensors to monitor the distribution of materials on the belt. These sensors can alert operators to imbalances that need to be corrected.
- Regular Training: Train operators on the importance of even loading and the correct methods for placing materials on the conveyor.
Repairing Belt Damage
- Inspect for Damage: Regularly inspect the belt for any signs of physical damage, such as cuts, tears, or worn edges.
- Repair or Replace Damaged Sections: Repair minor damage using belt repair kits or techniques. For severe damage, replace the affected section of the belt.
- Preventive Maintenance: Implement preventive maintenance practices to regularly check and address minor damage before it becomes a major issue.
Effective conveyor belt tracking troubleshooting involves a detailed analysis of the causes of unilateral tracking and the implementation of precise adjustments and fixes. By ensuring proper belt tension, aligning pulleys and rollers, maintaining the structural integrity of the conveyor frame, distributing the load evenly, and repairing belt damage promptly, you can resolve one-sided tracking issues and maintain optimal conveyor performance. Regular maintenance and proactive troubleshooting are essential for preventing future tracking problems and ensuring the efficient operation of your conveyor belt system.
FAQs About Conveyor Belt Tracking Troubleshooting
A conveyor belt not tracking properly can be attributed to several factors. The most common causes include improper belt tension, misaligned pulleys and rollers, and an uneven conveyor frame. Improper belt tension can result from uneven distribution across the belt, leading to one side being tighter than the other, causing the belt to drift. Misaligned pulleys and rollers force the belt off its intended path, and even minor misalignments can cause significant tracking problems. An uneven conveyor frame, whether due to poor installation or wear over time, can also lead to tracking issues. Additionally, external factors like uneven loading of materials and environmental conditions such as dust and debris can affect belt tracking. Regular maintenance and proper installation are crucial to prevent these issues.
Adjusting the tracking on a conveyor belt involves several steps to ensure the belt runs straight and efficiently. First, inspect the entire conveyor system to identify any obvious misalignments or issues with the belt, pulleys, and rollers. Use a tension gauge to measure the belt tension across its width and adjust the tensioners to achieve even tension. Next, align the pulleys and rollers using a laser alignment tool or a straight edge. Ensure they are parallel to each other and the conveyor frame. Make small, incremental adjustments and monitor the belt’s movement. It may be necessary to adjust the take-up pulley to guide the belt into the correct position. Regularly check the alignment and tension during operation and make adjustments as needed. Implementing these steps will help maintain proper belt tracking and prevent operational disruptions.
One of the most common problems with belt conveyors is misalignment, which can lead to several operational issues. Misaligned belts can cause uneven wear, increased friction, and the belt drifting to one side, potentially resulting in damage to the belt and conveyor structure. Other frequent issues include improper belt tension, which can cause slippage or excessive tension leading to belt breakage, and the buildup of debris or contaminants on the belt or conveyor components, which can interfere with smooth operation. Regular maintenance, including checking and adjusting belt tension, aligning pulleys and rollers, and cleaning the conveyor system, is essential to prevent these common problems. Additionally, ensuring proper installation and monitoring the load distribution on the belt can help maintain efficient and trouble-free conveyor operation.
Troubleshooting a conveyor belt involves systematically identifying and addressing any issues affecting its performance. Start by conducting a visual inspection of the entire conveyor system, looking for signs of wear, damage, or misalignment in the belt, pulleys, rollers, and other components. Measure the belt tension and adjust it if necessary to ensure even distribution across the belt width. Check the alignment of the pulleys and rollers using precision tools and make any needed adjustments. Ensure that the conveyor frame is level and free from structural damage. If the belt is tracking to one side, inspect for uneven loading or environmental factors like debris that might be causing the issue. Implement regular maintenance schedules to keep the system clean and in good working condition. If problems persist, consider consulting detailed troubleshooting guides or resources from the conveyor manufacturer for more advanced solutions.
Last Updated on June 11, 2024 by Jordan Smith
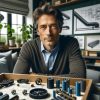
Jordan Smith, a seasoned professional with over 20 years of experience in the conveyor system industry. Jordan’s expertise lies in providing comprehensive solutions for conveyor rollers, belts, and accessories, catering to a wide range of industrial needs. From initial design and configuration to installation and meticulous troubleshooting, Jordan is adept at handling all aspects of conveyor system management. Whether you’re looking to upgrade your production line with efficient conveyor belts, require custom conveyor rollers for specific operations, or need expert advice on selecting the right conveyor accessories for your facility, Jordan is your reliable consultant. For any inquiries or assistance with conveyor system optimization, Jordan is available to share his wealth of knowledge and experience. Feel free to reach out at any time for professional guidance on all matters related to conveyor rollers, belts, and accessories.