Guide to Conveyor Belt Training Rollers
Conveyor belt training rollers play a crucial role in maintaining efficient conveyor belt systems. They are essential components that ensure the smooth and accurate alignment of conveyor belts, preventing costly downtime and ensuring maximum productivity. Conveyor belt training rollers are designed to guide the belt and correct any misalignment that could lead to material spillage, belt damage, or system inefficiency. By keeping the conveyor belt centered on the structure, these rollers improve the belt’s longevity, reduce maintenance costs, and optimize performance. Understanding the various types of conveyor belt training rollers and their specific applications is vital for selecting the right solution to maintain a seamless conveyor belt operation.
Types of Conveyor Belt Training Rollers
Understanding the different types of conveyor belt training rollers is essential for anyone involved in the maintenance or management of a conveyor belt system. Each type of roller serves a unique purpose and is crucial for various operational requirements, enhancing both the functionality and longevity of the conveyor system.
Standard Training Rollers
Standard training rollers are fundamental components of conveyor belt systems. These rollers are typically used to support the conveyor belt and its load while maintaining the belt’s alignment. They are characterized by their robust construction and can be made from materials such as steel or plastic, depending on the application. Common uses include installations in lightweight to medium-duty conveyor systems where minimal adjustment is required.
Self-Aligning Rollers
Self-aligning rollers are specially designed to correct any misalignment of the conveyor belt automatically. These rollers pivot and tilt to guide the belt back to the center of the conveyor system. The mechanisms involved usually include a central roller with a pair of self-aligning idler rollers on either side. The advantages of self-aligning rollers are significant, as they reduce wear and tear on the belt, decrease downtime caused by misalignments, and extend the overall lifespan of the conveyor system.
Side Guide Rollers
Side guide rollers are used to ensure that the conveyor belt does not wander too far from its intended path. They are installed along the sides of the conveyor frame and gently guide the belt without causing damage. These rollers are particularly useful in applications where the conveyor path includes sharp turns or where the belt is subject to strong lateral forces. The specific design of side guide rollers helps prevent the belt from slipping off the track and reduces instances of uneven wear or damage.
Drive Rollers
Drive rollers are critical in providing the motive force required to move the conveyor belt. They are connected to the conveyor’s motor and gearbox, transferring power from the drive unit to the conveyor belt. Drive rollers are designed to have a high coefficient of friction with the conveyor belt to prevent slippage. They play a vital role in the overall efficiency of the conveyor system, influencing both the speed and the handling capacity of the belt.
Each type of these conveyor belt training rollers is essential for optimizing the performance and efficiency of conveyor systems across various industries. By understanding their roles and functionalities, operators can ensure smoother operations and reduced operational costs.
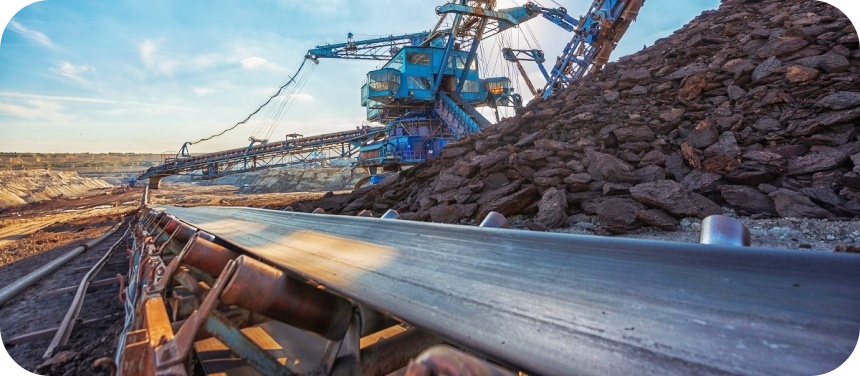
Key Features and Specifications of Conveyor Belt Training Rollers
When choosing conveyor belt training rollers, understanding their key features and specifications is crucial to ensure the best fit for your conveyor system. Here are the essential aspects to consider:
Roller Diameter
- Roller diameters vary depending on the type of conveyor system and application.
- Common diameters range from 50 mm to 300 mm.
- Larger diameter rollers offer better support for heavier loads, while smaller diameter rollers are suitable for lighter loads and tight spaces.
Material Types
- Steel Rollers: Durable and ideal for heavy-duty applications. Resistant to impact and suitable for industries like mining and steel mills.
- Rubber-Coated Rollers: Provide improved grip and protection against abrasion. Ideal for delicate or high-precision handling.
- Plastic Rollers: Lightweight, corrosion-resistant, and suitable for lighter loads. Commonly used in food processing or chemical industries.
- Nylon Rollers: Resistant to abrasion, chemicals, and corrosion, making them ideal for medium to heavy loads.
Belt Width Compatibility
- Conveyor belt training rollers are designed to accommodate varying belt widths.
- Self-Aligning Trough Roller: Suitable for belts ranging from 400 mm to 2200 mm.
- Trough Friction Idler, Self-Aligning Roller: Supports belts from 400 mm to 1400 mm.
- Trough Tapered Idler, Self-Aligning Roller: Compatible with belt widths from 800 mm to 2000 mm.
- Return Training Roller (1 or 2 rollers): Fits belts from 400 mm to 2200 mm.
Standards and Certifications
Quality conveyor belt training rollers adhere to strict standards and certifications to ensure safety, durability, and efficiency:
- DIN (German Institute for Standardization): German standard ensuring high product quality.
- CEMA (Conveyor Equipment Manufacturers Association): American standard that focuses on design and manufacturing best practices.
- JIS (Japanese Industrial Standards): Japanese standard emphasizing precision and quality.
- AS (Australian Standards): Australian guidelines for conveyor equipment quality.
- SANS-SABS (South African National Standards): Ensures compliance with South African industry standards.
- GOST (Russian State Standards): Russian standard emphasizing reliability and robustness.
- AFNOR (Association Française de Normalisation): French standard highlighting quality and efficiency.
Understanding the specifications and features of conveyor belt training rollers is crucial for optimal belt alignment, system efficiency, and safety. Choosing rollers that meet industry standards guarantees better performance and longer service life, ensuring your conveyor system operates at peak efficiency.
Advantages of Using High-Quality Conveyor Belt Training Rollers
Investing in high-quality conveyor belt training rollers can greatly enhance the efficiency and longevity of your conveyor system. Here are some key benefits:
Reduced Maintenance Costs
- Precision Alignment: High-quality conveyor belt training rollers ensure accurate belt alignment, minimizing belt drift and reducing wear and tear on both the rollers and the belt itself.
- Durability: Premium materials, such as steel or rubber coatings, provide excellent resistance to abrasion and impact, reducing the frequency of roller replacements.
- Lower Energy Consumption: Proper alignment reduces friction, resulting in lower energy consumption and improved system efficiency.
Increased Efficiency
- Continuous Operation: Properly aligned belts experience fewer interruptions, leading to a smoother material flow and increased productivity.
- Reduced Material Spillage: With high-quality conveyor belt training rollers, material spillage is minimized, improving overall efficiency and reducing cleanup costs.
- Consistent Belt Tracking: Ensures that the belt remains centered, even under varying loads, preventing downtime due to misalignment.
Prolonged Lifespan of Conveyor Belts
- Reduced Belt Wear: Accurate belt tracking reduces edge wear and prevents excessive stretching, significantly extending belt life.
- Less Downtime: Fewer maintenance stops mean longer operational periods, ultimately leading to a more cost-effective system.
Case Studies and Industry Examples
- Mining Industry – Rio Tinto: Rio Tinto, a mining giant, installed high-quality training rollers from Rulmeca on their conveyor belts to tackle misalignment issues. The rollers ensured smooth belt tracking across the rugged mining environment, drastically reducing belt edge wear and maintenance costs.
- Steel Mills – ArcelorMittal: At ArcelorMittal’s steel mills, conveyor belt training rollers from Fenner Dunlop significantly improved belt tracking, reducing spillage and improving the operational uptime of the conveyor systems. The steel mills reported increased belt lifespan due to decreased friction between belts and rollers.
- Logistics Sector – UPS: UPS, a global leader in logistics, implemented conveyor belt training rollers from Martin Engineering in their sorting facilities. The investment ensured smooth package movement, reducing belt stoppages and ultimately improving their package processing efficiency.
- Cement Manufacturing – Holcim: Holcim, a prominent cement manufacturer, employed conveyor belt training rollers from Continental AG. The company’s high-quality rollers allowed for precise belt alignment, enabling efficient material transport and reducing conveyor belt maintenance costs, which is critical given the abrasive nature of cement.
Conveyor belt training rollers are indispensable for maintaining efficient and safe conveyor operations. The cases mentioned illustrate how industries benefit from investing in high-quality rollers, ultimately reducing costs, improving productivity, and prolonging conveyor belt life.
Pricing and Availability of Conveyor Belt Training Rollers
Navigating the pricing and availability of conveyor belt training rollers is crucial for making informed purchasing decisions. This section provides an overview of the general pricing trends for different types of training rollers and offers practical tips on where to find and purchase these essential components.
General Pricing Trends
- Standard Training Rollers: Typically the most economical option, prices for standard training rollers can range from $15 to $50 per roller, depending on material and size specifications.
- Self-Aligning Rollers: Due to their complex design and enhanced functionality, self-aligning rollers are priced higher, generally between $50 and $200 per roller.
- Side Guide Rollers: These specialized rollers vary in price from $30 to $150 each, influenced by their design to prevent lateral movements of the conveyor belt.
- Drive Rollers: As critical components that drive the conveyor belt, these rollers can cost anywhere from $100 to $500, depending on their size and the specific motor integration.
Tips on Finding and Purchasing Conveyor Belt Training Rollers
- Online Marketplaces: Large platforms like Amazon, Alibaba, or industry-specific online stores often offer a wide range of conveyor belt training rollers.
- Manufacturer Websites: Directly purchasing from manufacturers can often provide customized solutions and potentially lower prices due to the absence of middleman fees.
- Local Industrial Suppliers: Checking with local suppliers can offer the advantage of viewing the product in person and easier return processes if needed.
- Trade Shows and Expos: These events are excellent for networking with manufacturers and suppliers and often provide opportunities to negotiate deals or bulk purchases.
- Ask for Referrals: Other industry professionals can provide referrals to trusted suppliers they have worked with in the past.
- Check Distributor Networks: Many manufacturers have official distributors that can offer local support and quicker delivery options.
- Online Forums and Industry Groups: Joining forums like LinkedIn groups or specialized industry forums can provide insights and recommendations on where to buy the best conveyor belt training rollers.
- Compare Prices and Reviews: Use comparison sites to check for competitive pricing and read customer reviews to ensure quality and reliability.
- Local Hardware Stores: Some local hardware stores might carry standard conveyor belt rollers, although they may have less selection than specialized suppliers.
- Specialty Conveyor System Providers: These providers often offer comprehensive solutions, including the sale of conveyor rollers and full system setups.
Ensuring you know where and how to source the right conveyor belt training rollers can save time and money while enhancing the efficiency and longevity of your conveyor system. With the right approach, finding high-quality rollers that meet your specific needs can be straightforward and cost-effective.
Installation and Maintenance Tips for Conveyor Belt Training Rollers
Proper installation and maintenance of conveyor belt training rollers are essential for maximizing their effectiveness and extending their lifespan. This section provides detailed guidance on both aspects to ensure optimal performance and reliability of your conveyor system.
Installation Tips for Conveyor Belt Training Rollers
- Follow Manufacturer’s Instructions: Always start by reading and adhering to the manufacturer’s installation guidelines to ensure correct setup.
- Proper Alignment: Ensure that the conveyor belt training rollers are perfectly aligned with the conveyor frame. Misalignment can cause rapid wear and tear.
- Check Roller Level: Use a level tool to confirm that the rollers are installed horizontally. This prevents uneven belt wear and reduces the risk of derailing.
- Secure Mounting: Tighten all mounting bolts and brackets to secure the rollers firmly. This prevents shifting during operation.
- Adjust Tension: Properly adjust the tension of the conveyor belt to avoid slippage or excessive wear on the rollers and the belt.
- Test Before Full Load: Run the conveyor belt empty after installation to check for any unusual noises or movements. Adjust as necessary before adding a full load.
- Positioning of Self-Aligning Rollers: When installing self-aligning rollers, ensure they are positioned at critical points where misalignments are likely to occur, such as load points and changes in direction.
- Safety First: Always ensure that all safety measures are followed during installation to protect personnel. Disconnect power to the conveyor system before starting any work.
Maintenance Best Practices for Conveyor Belt Training Rollers
- Regular Inspections: Schedule regular inspections to check for wear, damage, or misalignment of the rollers and the conveyor belt. Early detection can prevent costly repairs and downtime.
- Lubrication: Regularly lubricate the rollers according to the manufacturer’s recommendations. Proper lubrication reduces friction and wear, and prolongs the life of the rollers.
- Cleanliness: Keep the rollers and the conveyor belt clean from debris and dust. Accumulated dirt can impair roller function and belt alignment.
- Replacement of Worn Rollers: Replace rollers that show significant wear or damage. Worn rollers can impair the conveyor belt’s alignment and cause further damage to the system.
- Tension Adjustment: Periodically check and adjust the tension of the conveyor belt to ensure it is not too tight or too loose, which can lead to wear and inefficiency.
- Record Keeping: Maintain records of maintenance and replacements. This helps in predicting wear patterns and planning future maintenance.
By following these installation and maintenance tips, you can ensure that your conveyor belt training rollers perform optimally, leading to a more efficient, reliable, and long-lasting conveyor system.
Fill out the form to receive a detailed brochure on our conveyor belts.
FAQs about Conveyor Belt Training Rollers
Conveyor belts require specific types of rollers to function effectively and efficiently. The choice of roller can vary based on the application, load, speed, and environment in which the conveyor will operate. Common types include:
Gravity Rollers: Ideal for manual movement or where the belt moves by force of gravity. These are cost-effective and suitable for lightweight packages and products.
Drive Rollers: Featuring internal motors, these rollers propel the conveyor belt and control its movement. They are used in automated conveyor systems.
Impact Rollers: Situated at the loading points where material is dropped onto the belt, impact rollers help absorb the shocks and stresses, protecting the belt from damage.
Troughing Rollers: They shape the belt into a trough for bulk transport, ensuring materials stay on the belt and do not spill over the sides.
Each type serves its unique purpose, ensuring the conveyor system runs smoothly and efficiently.
Tracking a conveyor belt to ensure it runs correctly involves specific rollers known as tracking or guide rollers. These rollers help maintain the belt’s alignment and prevent it from wandering off its intended path. For precise tracking, V-guided rollers are often used. They are designed with a groove in the center that matches a complementary V-shaped guide attached to the bottom of the conveyor belt. This design ensures the belt remains centered and reduces the risk of misalignment, which can lead to wear, tear, or damage to the conveyor system.
The primary purpose of rollers in a conveyor system is to support and move the conveyor belt or products placed directly on the rollers. They facilitate smooth and efficient transportation of materials from one point to another within a facility. Beyond material transport, rollers serve several important functions:
Reducing Friction: Rollers minimize the friction between the conveyor belt and the supporting structure, which helps in increasing the lifespan of the belt.
Supporting Weight: They bear the load of the materials being transported, ensuring the belt remains evenly supported and preventing sagging.
Aiding in Product Sorting and Direction Changes: Specialized rollers can help in sorting products or changing the direction of travel without manual intervention.
Facilitating Speed Control: In powered conveyor systems, motorized rollers can regulate the speed of the belt, thus controlling the rate at which materials move through a process or facility.
Training a conveyor belt involves adjusting the belt and roller alignment to ensure the belt runs straight and true. This is crucial for preventing material spillage, reducing wear on the belt and rollers, and minimizing energy consumption. The process typically involves several steps:
Inspect and Adjust Rollers: Ensure that all rollers are correctly aligned and parallel to each other and the belt’s travel direction.
Center the Belt on the Conveyor: Adjust the idlers and rollers to center the belt. Start with the idlers closest to the end of the conveyor and work towards the center.
Check for Material Build-up: Material accumulation on rollers can cause the belt to misalign. Clean any build-up off the rollers and the belt.
Monitor Belt Tension: Incorrect belt tension can lead to slippage or misalignment. Adjust the tension so that the belt operates smoothly without excessive sag or tightness.
Successful training requires regular monitoring and adjustments to adapt to changes in operating conditions and wear over time.
Last Updated on August 27, 2024 by Jordan Smith
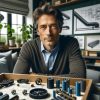
Jordan Smith, a seasoned professional with over 20 years of experience in the conveyor system industry. Jordan’s expertise lies in providing comprehensive solutions for conveyor rollers, belts, and accessories, catering to a wide range of industrial needs. From initial design and configuration to installation and meticulous troubleshooting, Jordan is adept at handling all aspects of conveyor system management. Whether you’re looking to upgrade your production line with efficient conveyor belts, require custom conveyor rollers for specific operations, or need expert advice on selecting the right conveyor accessories for your facility, Jordan is your reliable consultant. For any inquiries or assistance with conveyor system optimization, Jordan is available to share his wealth of knowledge and experience. Feel free to reach out at any time for professional guidance on all matters related to conveyor rollers, belts, and accessories.