Effective Management of Conveyor Belt Transitions
In the world of material handling systems, conveyor belt transitions play a pivotal role in maintaining operational efficiency and the integrity of the conveyor belt. These transitions are the points where the conveyor belt changes from a flat to a troughed configuration, or vice versa, typically at or near the terminal pulleys. The proper design and implementation of conveyor belt transitions are crucial as they help in evenly distributing the stress across the belt, reducing wear and tear, and preventing material spillage. This introduction aims to shed light on the significance of conveyor belt transitions and their fundamental role in ensuring the smooth and effective functioning of conveyor systems in various industrial applications.
What are Conveyor Belt Transitions
Conveyor belt transitions are critical components in the operation of a conveyor belt system. These transitions are the areas where the conveyor belt changes from a flat to a troughed configuration, or vice versa. This change typically occurs at the terminal points of the conveyor system, such as the head or tail pulleys. The purpose of conveyor belt transitions is to ensure a smooth transfer of materials being conveyed and to maintain the integrity and longevity of the belt itself.
Learning Conveyor Belt Transitions
The process of transitioning from a flat to a troughed belt, or the reverse, is not instantaneous. It requires a gradual change over a certain length of the conveyor, known as the “transition distance.” This transition distance is crucial because it helps to distribute the stresses that occur during the change in belt shape. If the transition is too abrupt, it can lead to excessive stress on the belt material, leading to potential damage such as tearing or premature wear.
In a typical conveyor belt transition, the belt starts to gradually conform to the shape of the troughing idlers. This shaping begins at the terminal pulley and continues until the belt has fully adopted the troughed profile. The exact length of the transition distance depends on several factors, including the width and thickness of the belt, the troughing angle, and the material properties of the belt.
Significance of Transition Distance in Conveyor Belt Operations
The transition distance in a conveyor belt system is not a one-size-fits-all measurement. It must be carefully calculated and implemented based on the specific parameters of the conveyor system. A well-designed transition distance ensures that the belt is not subjected to undue stress, which can cause the belt edges to lift or the center to sag. This is particularly important for maintaining the belt’s structural integrity and preventing spillage of materials.
Moreover, the transition distance conveyor belt plays a pivotal role in the overall efficiency of the conveyor system. A correctly implemented transition distance helps in reducing maintenance needs and prolonging the lifespan of the belt. It also contributes to smoother operation, reducing the likelihood of interruptions due to belt misalignment or damage.
Conveyor belt transitions and the associated transition distance are key to the effective and efficient operation of a conveyor belt system. They require careful consideration and design to ensure that the conveyor belt performs optimally, with minimal risk of damage and maximum operational efficiency.
Optimizing Conveyor Systems with Conveyor Belt Transitions and Transition Idlers
In the intricate design of conveyor systems, conveyor belt transitions and transition idlers play a crucial role. These components are essential in supporting the belt as it moves between terminal pulleys and troughed sections, ensuring a smooth transition and maintaining the belt’s structural integrity. Understanding the benefits of transition idlers is key to optimizing conveyor system performance.
- Stress Distribution: Transition idlers help distribute the stress along the belt more evenly. This is particularly important during the transition phase from flat to troughed sections, reducing the risk of belt damage due to concentrated stress points.
- Maintaining Belt Integrity: By providing adequate support, transition idlers prevent excessive sagging or bending of the belt. This support is crucial for maintaining the belt’s shape and structural integrity over time, thereby extending its lifespan.
- Preventing Material Spillage: A well-supported belt through transition idlers ensures that materials remain securely on the belt during the transition phases. This is especially important in troughed sections where the risk of spillage is higher due to the movement and angle of the belt.
- Enhancing Tracking and Alignment: Transition idlers play a significant role in maintaining proper belt tracking and alignment. Misalignment can lead to uneven wear, increased energy consumption, and potential operational hazards. Transition idlers help in keeping the belt aligned as it enters and exits troughed sections.
- Reducing Maintenance and Downtime: By ensuring smooth transitions and reducing the wear and tear on the belt, transition idlers contribute to lower maintenance requirements. This not only saves on repair costs but also minimizes downtime due to maintenance, thereby enhancing overall operational efficiency.
The use of transition idlers in conveyor belt transitions is a critical aspect of conveyor system design. Their role in supporting the belt, distributing stress, maintaining alignment, and preventing material spillage is fundamental to the efficient and long-term operation of conveyor systems.
Conveyor Belt Transitions Diagram and Design
Conveyor belt transitions are a vital aspect of conveyor belt design, ensuring the smooth and efficient operation of the conveyor system. This section delves into the diagrams that illustrate conveyor belt transitions and discusses the key design considerations that ensure effective transition areas.
Conveyor Belt Transitions Diagrams
To fully understand conveyor belt transitions, it’s helpful to refer to detailed diagrams. These diagrams typically show a side view of the conveyor system, highlighting the transition points. In these illustrations, you can see how the belt moves from a flat profile at the tail pulley, gradually conforms to the troughing idlers, and then returns to a flat profile at the head pulley. The diagrams also often indicate the transition distance, showing the gradual change in the belt’s shape over a specified length.
These visual representations are crucial for understanding the dynamics of conveyor belt transitions. They help in visualizing how the belt adapts its shape, ensuring that materials are carried efficiently while minimizing stress and wear on the belt.
Design Considerations for Effective Transition Areas
When designing conveyor belt transitions, several key factors must be considered to ensure their effectiveness:
- Transition Angle: The angle at which the belt transitions from flat to troughed, or vice versa, is critical. This angle should be gradual enough to prevent material spillage and to reduce stress on the belt. A steep transition angle can cause the belt to buckle or warp, leading to potential damage and operational issues.
- Transition Length: The length of the transition area is another crucial factor. It must be long enough to allow the belt to change shape gradually. The required length varies depending on the belt width, material, and operational speed. A longer transition is generally better, as it distributes the stress over a larger area, reducing the risk of belt damage.
- Belt Stiffness and Material Properties: The design must consider the stiffness and material properties of the belt. Different materials will respond differently to the stresses of transitioning, so the design must be tailored to the specific type of belt used.
- Load and Speed Considerations: The amount and type of material being conveyed, along with the speed of the conveyor, will impact the design of the transition area. Heavier loads and higher speeds require more carefully designed transitions to prevent belt damage and ensure smooth operation.
- Environmental Factors: External factors such as temperature, humidity, and exposure to chemicals can also affect the performance of conveyor belt transitions. These environmental conditions should be considered in the design phase to ensure long-term reliability.
The design of conveyor belt transitions is a complex task that requires careful consideration of various factors. Properly designed transitions are essential for the longevity and efficiency of the conveyor belt, ensuring smooth operation and minimizing maintenance requirements. Diagrams play a crucial role in planning and visualizing these transitions, aiding in the creation of effective and reliable conveyor systems.
Calculating Optimal Length for Conveyor Belt Transitions
Understanding and calculating the optimal transition length for conveyor belt transitions is crucial for the efficiency and longevity of conveyor systems. The transition length is the segment of the belt that changes from a flat to a fully troughed profile or vice versa. This section provides guidelines on how to determine this critical measurement and discusses the factors that influence it.
Basic Calculation Principles:
- The transition length primarily depends on the belt width and the troughing angle of the idler. A general rule is that the transition length should be at least 2 to 2.5 times the belt width for troughing angles of 20 to 35 degrees.
- For steeper troughing angles, this length may need to be increased to ensure a smooth transition and avoid overstressing the belt.
Factors Affecting Transition Length:
- Belt Tension: Higher belt tension requires longer transition lengths to distribute the stress more evenly across the belt width. This is crucial to prevent the belt from buckling or suffering from excessive edge stress.
- Load Characteristics: The nature of the material being conveyed impacts the transition length. Heavy or particularly abrasive materials may necessitate longer transitions to reduce wear and tear at these critical points.
- Belt Properties: The flexibility and construction of the conveyor belt material also play a significant role. Stiffer belts, or those with thicker covers or reinforcing layers, typically require longer transitions.
- Conveyor Speed: Higher conveyor speeds can increase the dynamic forces on the belt and material, thereby influencing the required transition length for stable and controlled movement of the load.
Practical Considerations:
- While theoretical calculations provide a starting point, practical considerations such as the specific conveyor configuration, space limitations, and operational requirements should also be taken into account.
- It’s often beneficial to consult with belt manufacturers or specialists who can provide tailored advice based on the specific characteristics of the conveyor system and the material being transported.
Accurately calculating the transition length for conveyor belt transitions is a complex but essential task. It requires consideration of various factors, including belt properties, load characteristics, and operational parameters. Proper determination of this length is key to ensuring the smooth functioning and durability of the conveyor belt system.
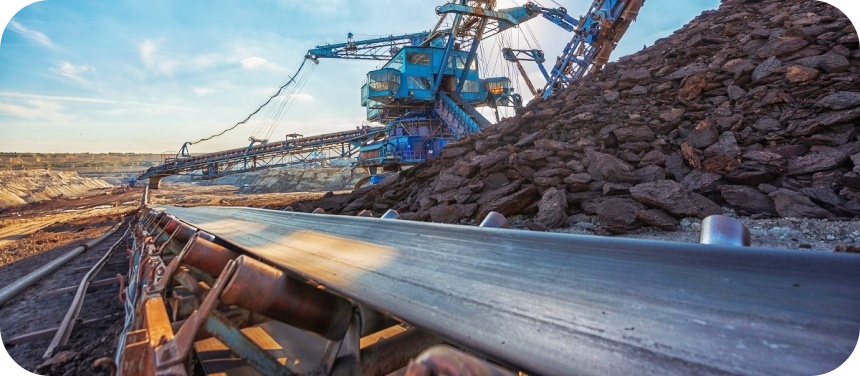
Conveyor Belt Transitions and Transition Plates
In the realm of conveyor belt transitions, transition plates play a pivotal role in ensuring smooth and efficient operation. This section provides an in-depth look at conveyor transition plates, exploring their function and application in various conveyor setups.
Learning Conveyor Transition Plates
Conveyor transition plates are essential components used in conveyor systems to facilitate smooth transitions between different sections of the conveyor belt. These plates are typically installed at points where the conveyor belt transitions from one configuration to another, such as from flat to troughed or from the feeding to the carrying section.
The primary function of transition plates is to bridge the gap between different sections of the conveyor belt. They provide a continuous and smooth surface for products to move over, preventing items from getting stuck or falling through gaps. This is particularly important for small or fragile items that could be damaged or lost during transition points.
Application of Transition Plates in Conveyor Setups
Transition plates find their application in various conveyor setups, each offering specific advantages:
- Flat to Troughed Transitions: In systems where the conveyor belt transitions from a flat to a troughed configuration, transition plates help in guiding the belt into the troughed rollers smoothly. This reduces the stress on the belt and prevents material spillage.
- Feeding Points: At feeding points where materials are loaded onto the conveyor, transition plates ensure that the materials are deposited onto the belt without disruption. This is crucial for maintaining the flow of materials and preventing blockages or buildups.
- Discharge Points: Similarly, at discharge points, transition plates facilitate the smooth offloading of materials from the conveyor belt to the next stage in the process, whether it’s another conveyor, a storage container, or a processing unit.
- Modular Conveyor Systems: In modular conveyor systems, transition plates are particularly advantageous as they allow for flexibility in the design and layout of the conveyor system. They enable smooth transitions between different modules, ensuring a consistent flow of materials.
- Safety and Efficiency: Transition plates not only contribute to the efficiency of material handling but also enhance safety. By providing a stable and continuous surface, they reduce the risk of accidents and material loss, contributing to a safer working environment.
Conveyor transition plates are integral to the functionality of conveyor belt transitions. They ensure the smooth transfer of materials across different sections of the conveyor, enhancing both the efficiency and safety of the conveyor system. Their application varies depending on the specific requirements of the conveyor setup, but their role in facilitating seamless transitions remains consistently vital.
Specialized Conveyor Belt Transitions: Navigating Complex Material Handling
In the intricate world of material handling, specialized conveyor belt transitions, such as 90-degree conveyor transfers, play a pivotal role in optimizing the flow and direction of materials. This section explores these unique transitions and introduces QC Conveyors’ innovative solutions for handling complex conveyor transitions.
90-Degree Conveyor Transfers:
- These specialized transitions are designed to change the direction of the material flow by 90 degrees, which is essential in facilities where space constraints require sharp turns in the conveyor path.
- The design of 90-degree transfers varies, including options like pop-up transfer conveyors, rotary turntables, and slat conveyors, each suited to different types of products and operational needs.
- These transitions are particularly useful in distribution centers, packaging lines, and manufacturing plants where efficient use of space and directional changes are crucial.
Applications in Material Handling:
- 90-degree conveyor transfers are employed in various scenarios, such as redirecting products for sorting, merging multiple conveyor lines, or altering the product orientation for packaging and processing.
- They are designed to handle a wide range of products, from small, lightweight items to larger, heavier goods, ensuring a smooth transition without disrupting the conveyor flow.
QC Conveyors’ Solutions for Complex Transitions:
- QC Conveyors stands out as a provider of innovative conveyor solutions, particularly for challenging transitions.
- Their offerings include advanced conveyor systems with features like tight turn radii, precise product alignment, and gentle handling, ensuring the integrity of the products during transfer.
- QC Conveyors also specializes in custom-designed solutions tailored to specific industry requirements, providing efficient and reliable transitions even in the most complex conveyor layouts.
Specialized conveyor belt transitions, such as 90-degree transfers, are essential components in modern material handling systems. Companies like QC Conveyors are at the forefront of developing advanced solutions that address the challenges of complex conveyor transitions, enhancing efficiency and productivity in various industrial applications.
Best Practices for Ensuring Efficient Conveyor Belt Transitions
In the complex system of conveyor belts, transitions play a crucial role in maintaining efficiency and prolonging the lifespan of the belt. This section compiles best practices and maintenance tips to ensure smooth and efficient conveyor belt transitions, emphasizing the importance of regular inspections and adjustments.
Regular Inspections of Transition Areas:
- Conduct frequent and thorough inspections of transition zones. Look for signs of wear, misalignment, or damage to the belt and idlers.
- Pay special attention to the condition of transition idlers and rollers, as they are critical in supporting the belt during transitions.
Proper Installation and Alignment:
- Ensure that transition idlers and rollers are correctly installed and aligned. Misalignment can cause uneven wear on the belt and lead to premature failure.
- Check that the transition angles and distances are in accordance with the design specifications and adjust as necessary.
Maintaining Optimal Belt Tension:
- Proper belt tension is essential for smooth transitions. Over-tensioning can lead to excessive wear, while under-tensioning can cause the belt to sag and misalign.
- Regularly check and adjust the tension to the manufacturer’s specifications.
Use of Appropriate Transition Idlers:
- Select transition idlers that are suitable for the type of material being conveyed and the specific requirements of the conveyor system.
- Consider adjustable or custom-designed idlers for complex or unique transition requirements.
Training for Operational Staff:
- Ensure that operational staff are trained in the proper handling and maintenance of conveyor belt transitions.
- Regular training helps in early identification of potential issues and proper response to prevent major breakdowns.
Scheduled Maintenance and Record Keeping:
- Implement a scheduled maintenance program for conveyor belt transitions. Regular maintenance helps in identifying issues before they become major problems.
- Keep detailed records of inspections, maintenance, and adjustments. This documentation can be invaluable in troubleshooting and planning future upgrades or replacements.
Discover superior conveyor belts designed for your needs. Reach out to us for more details!
By following these best practices, businesses can ensure that their conveyor belt transitions operate smoothly and efficiently, reducing downtime and maintenance costs while extending the overall life of the conveyor system. Regular inspections, proper alignment, and staff training are key components in achieving optimal performance in conveyor belt transitions.
FAQs about Conveyor Belt Transitions
A conveyor transition refers to the section of a conveyor system where the belt changes its shape or configuration. Typically, this occurs at the terminal points of the conveyor (head or tail pulleys), where the belt shifts from a flat to a troughed profile or vice versa. The transition is a critical part of the conveyor, as it needs to be carefully designed to minimize stress and wear on the belt. The length and design of the transition zone depend on various factors, including belt width, thickness, and material properties.
Transition idlers are specialized rollers used in the transition zones of a conveyor system. They are designed to facilitate the gradual change in the shape of the conveyor belt from flat to troughed or vice versa. Transition idlers typically have adjustable angles and are strategically placed between the standard flat and troughed idlers to support the belt effectively during its transition. This helps in reducing stress and strain on the belt, thereby extending its life and maintaining its integrity.
The movement of a conveyor belt is primarily driven by a motorized system. This system usually consists of a motor that powers a drive pulley. The rotation of the drive pulley imparts motion to the belt, which then moves around the conveyor system. The belt’s movement can be controlled in terms of speed and direction. Additionally, the tension in the belt, maintained by idlers and tensioning systems, is crucial for effective movement and operation of the conveyor system.
Conveyor belt splicing is the process of joining two pieces of a conveyor belt together. This can be done either through mechanical fasteners or by vulcanizing. Mechanical splicing involves using metal hinges or plates to join the belt ends, while vulcanization is a more permanent method that involves heating and chemically bonding the belt ends together. The choice of splicing method depends on various factors like the belt material, the operating environment, and the load the conveyor will carry. Proper splicing is critical for ensuring the strength and longevity of the conveyor belt.
Last Updated on June 21, 2024 by Jordan Smith
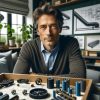
Jordan Smith, a seasoned professional with over 20 years of experience in the conveyor system industry. Jordan’s expertise lies in providing comprehensive solutions for conveyor rollers, belts, and accessories, catering to a wide range of industrial needs. From initial design and configuration to installation and meticulous troubleshooting, Jordan is adept at handling all aspects of conveyor system management. Whether you’re looking to upgrade your production line with efficient conveyor belts, require custom conveyor rollers for specific operations, or need expert advice on selecting the right conveyor accessories for your facility, Jordan is your reliable consultant. For any inquiries or assistance with conveyor system optimization, Jordan is available to share his wealth of knowledge and experience. Feel free to reach out at any time for professional guidance on all matters related to conveyor rollers, belts, and accessories.