Conveyor Belt Weightometer System
In the world of industrial processes and material handling, accurate measurement of bulk materials is essential. The conveyor belt weightometer is a critical tool that ensures precise measurement of materials being transported along a conveyor system. This blog will delve into the intricacies of conveyor belt weightometers, exploring their functionality, benefits, and application in various industries. By understanding how a conveyor belt weightometer operates and its role in improving efficiency and accuracy, businesses can optimize their material handling processes. From installation and calibration to maintenance and troubleshooting, this comprehensive guide will cover all aspects of conveyor belt weightometer systems, providing valuable insights for industrial applications.
What Is the Conveyor Belt Weightometer
A conveyor belt weightometer is an instrument designed to measure the weight of materials being transported on a conveyor belt. It provides real-time data on the mass and flow rate, which is crucial for inventory management, process control, and optimization of material handling operations. The conveyor belt weightometer operates by measuring the load and speed of the conveyor belt and calculating the total material weight. This system is essential in industries like mining, agriculture, and manufacturing, where accurate weight measurement directly impacts productivity and cost efficiency. For example, in mining operations, companies like Rio Tinto and BHP Billiton rely on conveyor belt weightometers to monitor the extraction and transport of minerals, ensuring that they meet production targets and regulatory requirements.
Key Components and Functionality
Weighing Frame
The weighing frame is a critical component of a conveyor belt weightometer, as it houses the load cells and supports the conveyor belt. This structure must be robust and precisely engineered to ensure accurate weight measurements. Typically made from high-strength steel, the weighing frame is designed to withstand the harsh conditions of industrial environments. Companies like Thermo Fisher Scientific and Siemens manufacture advanced weighing frames that incorporate modular designs, allowing for easy installation and maintenance.
Load Cells
Load cells are the heart of the conveyor belt weightometer. These digital sensors measure the weight of the material on the belt by converting the mechanical force exerted by the load into an electrical signal. The accuracy of load cells is paramount, as even slight deviations can lead to significant errors in weight measurement. High-quality load cells, such as those produced by METTLER TOLEDO, offer precision up to ±0.5% of the measured weight. In an agricultural setting, for instance, conveyor belt weightometers equipped with these load cells can accurately track the weight of grains being transported, ensuring precise inventory records and reducing losses.
Speed Sensor
The speed sensor measures the speed of the conveyor belt, a crucial factor in determining the mass flow rate of the material. By combining the speed data with the weight measurements from the load cells, the conveyor belt weightometer calculates the total weight of the transported material. Speed sensors need to be highly responsive and durable, as they operate continuously in demanding conditions. Companies like SRO Technology provide speed sensors that integrate seamlessly with conveyor belt weightometer systems, enhancing their reliability and accuracy.
Controller
The controller is the brain of the conveyor belt weightometer system. It integrates data from the load cells and speed sensors, processing this information to calculate the material’s mass and flow rate. Modern controllers, such as those developed by Avery Weigh-Tronix, feature advanced algorithms and user-friendly interfaces, allowing operators to manage and monitor the conveyor system efficiently. In industrial applications, these controllers can be connected to centralized IT systems, providing real-time data for process optimization and decision-making.
Practical Applications and Industry Examples
Conveyor belt weightometers are employed in a variety of industries to enhance operational efficiency and accuracy. For instance, in the mining sector, conveyor belt weightometers are used to monitor the flow of extracted minerals. Companies like Vale S.A. utilize these systems to ensure that their mining operations are compliant with production quotas and environmental regulations. In the manufacturing industry, conveyor belt weightometers help in batching and blending processes by providing precise measurements of raw materials, thereby improving product consistency and quality.
In the food processing industry, conveyor belt weightometers are used to measure the weight of ingredients in automated production lines. For example, Nestlé employs conveyor belt weightometers in their factories to ensure that each product batch meets the specified weight criteria, thereby maintaining quality standards and minimizing waste.
Benefits of Implementing Conveyor Belt Weightometer Systems
Implementing conveyor belt weightometer systems offers numerous benefits across various industries, particularly in mining, manufacturing, and logistics. Here are some key advantages:
1. Enhanced Accuracy and Efficiency
- Real-time Monitoring: Weightometers provide continuous, real-time data on the material being transported, allowing for precise tracking of material flow and inventory management.
- Improved Process Control: Accurate weight measurements enable better control over production processes, leading to optimized operations and reduced waste.
2. Cost Savings
- Reduced Material Loss: By monitoring the weight of materials, companies can quickly detect and address issues such as spillage or overloading, minimizing material loss.
- Efficient Resource Allocation: Accurate weight data helps in planning and allocating resources more efficiently, reducing operational costs.
3. Improved Product Quality
- Consistent Product Output: Maintaining the correct weight of materials ensures that the final product meets quality standards consistently, reducing the risk of defective products.
- Better Quality Control: Weightometers aid in maintaining stringent quality control by providing accurate data for analysis and adjustments.
4. Enhanced Safety
- Overload Prevention: By monitoring the weight, conveyor systems can be safeguarded against overloading, reducing the risk of equipment failure and associated accidents.
- Compliance with Safety Standards: Accurate weight measurement ensures compliance with industry safety regulations, promoting a safer work environment.
5. Data-Driven Decision Making
- Operational Insights: Weightometers generate valuable data that can be analyzed to gain insights into operational efficiency, helping to identify areas for improvement.
- Informed Decision Making: Real-time and historical weight data support better decision-making processes at both operational and strategic levels.
6. Integration with Automation Systems
- Seamless Integration: Weightometer systems can be integrated with other automation and control systems, enhancing overall operational efficiency.
- Improved Automation: Automated adjustments based on weight data improve the efficiency and reliability of the conveyor system, reducing the need for manual intervention.
7. Environmental Benefits
- Reduced Waste: Precise control of material flow minimizes waste, contributing to more sustainable operations.
- Energy Efficiency: Optimizing the load on conveyor belts can lead to significant energy savings, reducing the environmental footprint.
8. Regulatory Compliance
- Adherence to Regulations: Accurate weight measurement helps ensure compliance with various industry regulations and standards, avoiding potential fines and legal issues.
- Traceability: Weightometers provide traceable data for audits and reporting, supporting regulatory compliance and transparency.
The implementation of conveyor belt weightometer systems can significantly enhance operational efficiency, safety, and cost-effectiveness. By providing accurate, real-time weight data, these systems support better decision-making, improve product quality, and ensure compliance with industry standards, ultimately leading to a more streamlined and profitable operation.
Implementing a conveyor belt weightometer system offers several benefits. Firstly, it enhances inventory management by providing accurate and real-time data on material flow, reducing the risk of overstocking or stockouts. Secondly, it improves process control by enabling precise measurement and regulation of material inputs, which is crucial for maintaining consistent product quality. Thirdly, it optimizes material handling operations by identifying inefficiencies and bottlenecks, allowing for timely interventions and process improvements.
The use of conveyor belt weightometer systems is integral to the success of various industrial processes. By ensuring accurate weight measurements and providing valuable data for process optimization, these systems contribute significantly to operational efficiency, cost savings, and product quality.

Conveyor Belt Weightometer Accuracy
The accuracy of conveyor belt weightometers is crucial for effective material handling and process optimization. Various factors influence the accuracy of these systems, and understanding these can help in achieving precise measurements. Here are some key points to consider:
Factors Affecting Weightometer Accuracy
Calibration
- Regular Calibration: Ensuring the weightometer is regularly calibrated according to the manufacturer’s specifications is essential for maintaining accuracy.
- Load Calibration: Using accurate test weights or certified materials to calibrate the system helps in achieving precise measurements.
Installation
- Proper Alignment: The conveyor belt must be properly aligned to avoid skewing or belt wander, which can affect weight measurements.
- Stable Mounting: The weightometer should be mounted on a stable structure to avoid vibrations and movements that can lead to inaccurate readings.
- Correct Positioning: Positioning the weightometer in a location with consistent belt tension and minimal belt slippage ensures better accuracy.
Environmental Conditions
- Temperature: Temperature variations can affect the performance of the weightometer. Using temperature-compensated load cells can mitigate these effects.
- Humidity and Dust: High humidity and dust levels can affect the sensors and electronics of the weightometer, leading to inaccuracies. Protective enclosures and regular maintenance can help.
- Vibration: Excessive vibrations from nearby equipment can interfere with weight measurements. Ensuring proper isolation and damping can improve accuracy.
Belt Speed and Load Distribution
- Consistent Belt Speed: Variations in belt speed can lead to measurement errors. Using speed sensors to adjust for belt speed changes can enhance accuracy.
- Even Load Distribution: Uneven distribution of material on the conveyor belt can cause inaccurate readings. Implementing measures to ensure even load distribution, such as feeders and spreaders, can help.
Maintenance and Wear
- Regular Maintenance: Routine inspection and maintenance of the weightometer and conveyor belt system are essential to ensure consistent performance and accuracy.
- Wear and Tear: Wear and tear of conveyor components, such as belts and rollers, can affect weight measurements. Timely replacement of worn parts is necessary.
Data Processing and Integration
- Advanced Algorithms: Using advanced data processing algorithms and filters can help in compensating for minor fluctuations and improving overall accuracy.
- System Integration: Integrating the weightometer with other automation and control systems can provide better synchronization and data accuracy.
Achievable Accuracy Levels
- General Accuracy: For many industrial applications, conveyor belt weightometers can achieve accuracy levels of ±0.5% to ±1% of the total load.
- High-Precision Applications: With advanced calibration, proper installation, and optimal environmental conditions, some systems can achieve accuracies better than ±0.25%.
Achieving high accuracy in conveyor belt weightometer systems requires attention to calibration, installation, environmental conditions, belt speed, load distribution, maintenance, and data processing. By addressing these factors, companies can ensure reliable and precise weight measurements, leading to improved operational efficiency and product quality.

Conveyor Belt Weightometer Calibration
Importance of Conveyor Belt Weightometer Calibration
Calibration is essential to maintain the accuracy and reliability of a conveyor belt weightometer. Regular calibration ensures that the weight readings are correct and consistent, which is crucial for maintaining operational efficiency and process control in various industries. Inaccurate measurements can lead to significant issues such as inventory discrepancies, production inefficiencies, and financial losses. For example, in the mining industry, companies like BHP Billiton and Rio Tinto rely on conveyor belt weightometers to measure the quantity of extracted minerals. Any inaccuracy in these measurements can result in regulatory non-compliance and substantial financial penalties.
Regular calibration of a conveyor belt weightometer involves checking and adjusting the system to ensure that it provides accurate weight measurements. This process helps in detecting and correcting any deviations that may have occurred due to wear and tear, environmental factors, or other operational conditions. By maintaining the calibration of their weightometer systems, businesses can ensure that they meet production targets, comply with regulatory standards, and optimize their material handling processes.
Steps for Calibrating a Conveyor Belt Weightometer
Preparation
The first step in calibrating a conveyor belt weightometer is preparation. Ensuring the conveyor is empty and stationary is crucial to obtaining accurate calibration results. This step involves several critical actions:
- Clearing the Conveyor Belt: Remove all materials from the conveyor belt to ensure that no residual weight affects the calibration process. This is particularly important in industries like food processing and pharmaceuticals, where even small quantities of residual materials can impact the accuracy of the weight measurements.
- Securing the Conveyor System: Ensure that the conveyor system is stationary and cannot move during the calibration process. This may involve locking the conveyor’s drive mechanism or using mechanical stops to prevent movement.
- Environmental Considerations: Check the environmental conditions, such as temperature and humidity, which can affect the calibration process. Ensure that the calibration is conducted under stable conditions to avoid variations in the measurements.
Test Weights
Using test weights is a critical part of the calibration process. These weights, with known and certified values, are placed on the conveyor belt to check the accuracy of the weightometer system. The following steps are involved:
- Selection of Test Weights: Choose test weights that are appropriate for the expected load range of the conveyor belt weightometer. For example, if the weightometer is used in a mining operation, the test weights should reflect the typical load of mined materials.
- Placement of Test Weights: Carefully place the test weights at different points on the conveyor belt to ensure that the weightometer system provides consistent readings across the entire belt length. This helps in identifying any discrepancies that may be caused by belt tension or load distribution.
- Recording Initial Readings: Record the initial readings from the weightometer system before making any adjustments. These readings will serve as a baseline to compare against the calibrated values.
Adjustments
Once the initial readings are recorded, adjustments can be made to the weightometer system to align the readings with the known values of the test weights. The following steps outline this process:
- Controller Adjustments: Use the weightometer system’s controller to adjust the calibration settings. This may involve changing the gain, offset, or other parameters to match the known test weights. Companies like Siemens provide advanced controllers with user-friendly interfaces that make these adjustments straightforward.
- Incremental Adjustments: Make small, incremental adjustments to avoid overcompensation, which can lead to further inaccuracies. It is essential to adjust slowly and carefully, verifying the changes after each adjustment.
- Re-checking Readings: After making the adjustments, re-check the readings with the test weights to ensure they match the known values. This step may need to be repeated several times to achieve the desired accuracy.
Verification
The final step in the calibration process is verification. This step ensures that the adjustments made are correct and that the conveyor belt weightometer is accurately calibrated. The following actions are involved:
- Repeating the Test: Repeat the placement of test weights and record the readings again. Verify that the adjusted readings consistently match the known values of the test weights across multiple trials.
- Documentation: Document the calibration process, including the initial readings, adjustments made, and final verified readings. This documentation is crucial for future reference and for maintaining calibration records as required by regulatory standards.
- Regular Calibration Schedule: Establish a regular calibration schedule based on the operational demands and environmental conditions. For instance, a conveyor belt weightometer used in a high-throughput manufacturing plant might require more frequent calibration than one used in a less demanding environment. METTLER TOLEDO recommends calibrating weightometers at least once a month to maintain accuracy.
Proper calibration of a conveyor belt weightometer ensures the system’s reliability and accuracy, which is essential for efficient and effective material handling. By following these detailed steps, businesses can maintain the performance of their conveyor belt weightometer systems, thereby optimizing their operational processes and ensuring compliance with industry standards.

Conveyor Belt Weightometer Basic Methods of Calibration
Calibrating a conveyor belt weightometer is essential for ensuring accurate weight measurements. Here are the basic methods of calibration commonly used:
Static Calibration
Procedure:
- Zero Calibration:
- Ensure the conveyor belt is empty.
- Set the weightometer to zero, ensuring that the system recognizes the weight of the empty belt as the baseline.
- Span Calibration:
- Place a known, certified test weight (or a series of weights) directly on the belt over the weightometer.
- Run the conveyor at its normal operating speed.
- Adjust the weightometer to read the exact value of the test weight.
Advantages:
- Simple and straightforward.
- Provides a direct reference point for the weightometer.
Disadvantages:
- Can be less accurate if the test weight is not evenly distributed or placed correctly.
- Only accounts for static conditions, not dynamic loading variations.
Dynamic Calibration
Procedure:
- Material Testing:
- Run a known quantity of material over the conveyor belt weightometer.
- Measure the weight using an alternative, accurate weighing method (such as a weighbridge or a pre-weighed load).
- Compare the weightometer reading with the known weight and adjust accordingly.
- Simulated Load:
- Use a simulated load that can be evenly distributed over the belt to mimic actual operating conditions.
- Run the simulated load over the weightometer at the normal operating speed.
- Adjust the weightometer based on the known weight of the simulated load.
Advantages:
- More accurate for real-world operating conditions.
- Accounts for dynamic factors such as belt speed and material distribution.
Disadvantages:
- Requires more setup and preparation.
- Can be time-consuming, especially if large quantities of material need to be handled.
Automatic Calibration
Procedure:
- Automated Systems:
- Some advanced weightometer systems have built-in automatic calibration features.
- These systems periodically check and adjust the calibration based on predefined parameters and algorithms.
- May involve using built-in test weights or other reference points automatically applied by the system.
Advantages:
- Reduces the need for manual intervention.
- Ensures consistent calibration over time.
Disadvantages:
- Requires advanced equipment and software.
- May be more costly to implement.
Load Cell Calibration
Procedure:
- Load Cell Verification:
- Check the calibration of the individual load cells used in the weightometer.
- Use certified calibration weights or load cell simulators to verify the accuracy of each load cell.
- Adjust the weightometer readings based on the load cell verification.
Advantages:
- Ensures each component of the weightometer is accurately calibrated.
- Can identify specific issues with individual load cells.
Disadvantages:
- Requires specialized equipment and knowledge.
- May need to be performed more frequently to maintain accuracy.
Best Practices for Calibration
Regular Calibration:
- Establish a routine calibration schedule to ensure ongoing accuracy.
- Frequency of calibration may depend on the operational environment and the criticality of the weight measurements.
Use of Certified Weights:
- Always use certified test weights or calibrated materials for accuracy.
Environmental Considerations:
- Consider the impact of environmental factors such as temperature, humidity, and vibration on calibration.
Documentation:
- Maintain detailed records of all calibration activities, including dates, weights used, adjustments made, and personnel involved.
By following these calibration methods and best practices, you can ensure that your conveyor belt weightometer provides reliable and accurate weight measurements, enhancing operational efficiency and product quality.

Which Conveyor Belt Weightometer Is Right for You
Selecting the right conveyor belt weightometer depends on various factors, including the specific needs of your operation, the type of material being handled, the required accuracy, and the environmental conditions. Here are key considerations and types of weightometers to help you make an informed decision:
Key Considerations
Material Type and Characteristics
- Bulk Density: Know the bulk density of the material to ensure the weightometer can handle the weight per unit length of the belt.
- Material Flow: Consider whether the material is free-flowing or sticky, as this affects the choice of the weightometer.
Conveyor Specifications
- Belt Width and Speed: Ensure the weightometer is compatible with the width and speed of your conveyor belt.
- Capacity: Choose a weightometer that can handle the maximum load capacity of your conveyor system.
Accuracy Requirements
- Determine the level of accuracy required for your application. High-precision applications may need more advanced and sensitive weightometers.
Environmental Conditions
- Temperature: Consider weightometers that can operate accurately within the temperature range of your environment.
- Dust and Moisture: Choose weightometers with appropriate protection against dust and moisture if operating in harsh conditions.
Maintenance and Calibration
- Evaluate the ease of maintenance and calibration of the weightometer to ensure long-term reliability and accuracy.
Selecting the Right Weightometer
- Light-Duty Applications: Single-idler weightometers are typically sufficient for light to moderate applications where high precision is not critical.
- High-Accuracy Needs: For industries like mining and mineral processing, multi-idler weightometers or weigh belt conveyors provide the needed accuracy and reliability.
- Remote and Harsh Environments: Wireless weightometers and nuclear weightometers are well-suited for environments where traditional systems might struggle.
Choosing the right conveyor belt weightometer involves understanding your specific operational needs, environmental conditions, and accuracy requirements. By considering the material type, conveyor specifications, accuracy needs, environmental factors, and maintenance requirements, you can select a weightometer that enhances your operational efficiency and reliability.
Upgrade your operations with our premium conveyor belts today.
Conveyor Belt Weightometer System
Overview of Conveyor Belt Weightometer Systems
Conveyor belt weightometer systems are comprehensive solutions designed to accurately measure the flow of materials on conveyor belts. These systems are essential in industries such as mining, agriculture, and manufacturing, where precise material measurement is crucial for maintaining operational efficiency and process control. A conveyor belt weightometer system typically includes the weightometer itself, speed sensors, and controllers that work together to provide real-time data on the mass and flow rate of materials. For instance, companies like Thermo Fisher Scientific and Siemens offer advanced conveyor belt weightometer systems that integrate seamlessly with existing plant infrastructure, enhancing overall productivity and accuracy.
Components and Configuration
Modular Design
One of the key features of conveyor belt weightometer systems is their modular design. This design allows the system to be customized to fit different conveyor sizes and applications, ensuring that it meets the specific needs of various industries. The modularity of these systems provides several benefits:
- Scalability: Businesses can scale their conveyor belt weightometer systems according to their operational requirements. For example, a small-scale agricultural operation may start with a basic system and expand it as their production volume increases.
- Flexibility: Modular systems can be easily reconfigured or upgraded to accommodate changes in production processes or new material handling requirements. This flexibility is particularly valuable in dynamic industries where process adjustments are frequent.
- Ease of Installation: The modular nature of conveyor belt weightometer systems simplifies the installation process. Companies like SRO Technology offer modular kits that include all necessary components, making it easier for technicians to set up and calibrate the system.
Data Integration
Modern conveyor belt weightometer systems are designed to interface with plant management systems, enabling seamless data flow and integration. This integration is crucial for optimizing process control and enhancing decision-making capabilities. The benefits of data integration include:
- Real-Time Monitoring: By integrating with plant management systems, conveyor belt weightometer systems provide real-time data on material flow, allowing operators to monitor and adjust processes dynamically. For example, in a manufacturing plant, real-time data can help detect and address issues such as material blockages or overflows promptly.
- Automated Reporting: Data integration enables automated reporting of material flow, reducing the need for manual data entry and minimizing the risk of errors. This automation is essential for maintaining accurate inventory records and ensuring regulatory compliance.
- Enhanced Analytics: Integrated conveyor belt weightometer systems can feed data into advanced analytics platforms, providing valuable insights into operational performance. Companies like METTLER TOLEDO offer solutions that include data analytics tools, helping businesses identify trends, optimize processes, and improve overall efficiency.
Maintenance
Regular maintenance is critical to ensuring the longevity and accuracy of conveyor belt weightometer systems. Proper maintenance protocols help prevent unexpected downtime and maintain the system’s performance. Key maintenance practices include:
- Routine Inspections: Conducting regular inspections of the conveyor belt weightometer system components, such as load cells and speed sensors, to identify any signs of wear or damage. For example, Siemens recommends monthly inspections to check for any physical damage or loose connections.
- Calibration: Periodic calibration of the weightometer system is essential to maintain its accuracy. Calibration involves adjusting the system settings to ensure that the weight readings match known reference values. Thermo Fisher Scientific suggests calibrating their conveyor belt weightometer systems at least once every three months.
- Cleaning and Lubrication: Keeping the conveyor belt weightometer system clean and properly lubricated helps prevent mechanical issues and ensures smooth operation. This is particularly important in dusty or abrasive environments, such as mining operations, where debris can accumulate and affect system performance.
- Software Updates: Regularly updating the system’s software to incorporate new features and improvements. These updates can enhance the system’s functionality and ensure compatibility with other integrated systems.
Practical Applications and Industry Examples
Conveyor belt weightometer systems are employed in various industries to enhance operational efficiency and accuracy. In the mining sector, these systems are used to monitor the flow of extracted minerals, ensuring that operations meet production quotas and comply with environmental regulations. For example, Vale S.A. utilizes conveyor belt weightometer systems to track the volume of iron ore transported from its mines. Accurate measurement helps optimize transportation logistics, reduce costs, and ensure compliance with export regulations.
In the manufacturing industry, conveyor belt weightometer systems help in batching and blending processes by providing precise measurements of raw materials. This accuracy is crucial for maintaining product consistency and quality. Procter & Gamble employs these systems in their production lines to ensure that the correct amounts of ingredients are used, resulting in high-quality finished goods and minimal material wastage.
In the food processing industry, conveyor belt weightometer systems measure the weight of ingredients in automated production lines. Nestlé, for example, uses these systems to ensure that each product batch meets specified weight criteria, maintaining quality standards and minimizing waste.
Implementing a conveyor belt weightometer system offers numerous benefits, from enhancing inventory management and process control to optimizing material handling operations. By providing accurate, real-time data on material flow, these systems enable businesses to make informed decisions, improve efficiency, and reduce costs. In industries such as mining, agriculture, and manufacturing, where precise material measurement is crucial, conveyor belt weightometer systems are invaluable tools that contribute significantly to operational success and profitability.
Weightometer Conveyor System
The Importance of Conveyor Belt Weightometer Systems
Conveyor belt weightometer systems are indispensable tools in industries such as mining, agriculture, and manufacturing, where the accurate measurement of material flow is critical for operational efficiency and cost control. These systems enable businesses to monitor the amount of material being transported, providing vital data that supports decision-making processes and ensures regulatory compliance.
In the mining industry, for example, conveyor belt weightometers play a crucial role. Companies like Rio Tinto and BHP Billiton rely on these systems to measure the quantity of minerals extracted and transported. This precise measurement is essential for maintaining production targets and ensuring that operations meet environmental and safety standards. In agriculture, conveyor belt weightometers help farmers and agricultural businesses accurately measure grains and other bulk materials during processing and storage. This accuracy is crucial for maintaining inventory levels and preventing over- or under-supply, which can impact profitability and operational efficiency.
Benefits of Using Conveyor Belt Weightometer Systems
Accuracy
One of the most significant benefits of using conveyor belt weightometer systems is their high accuracy in measuring material weight. These systems utilize advanced load cells and speed sensors to provide precise data on the weight of materials being transported. For instance, METTLER TOLEDO’s load cells offer an accuracy of up to ±0.5%, ensuring that businesses can trust the weight data provided by their conveyor belt weightometer systems. Accurate weight measurement is essential for billing, inventory management, and maintaining the quality of end products. In manufacturing, precise weight data ensures that the correct amounts of raw materials are used in production processes, leading to consistent product quality and reduced material wastage.
Efficiency
Conveyor belt weightometer systems enhance process efficiency by providing real-time data on material flow. This information allows businesses to monitor and adjust their operations dynamically, reducing downtime and increasing productivity. For example, in a manufacturing setting, real-time weight data from a conveyor belt weightometer can help operators detect and address issues such as blockages or material shortages promptly. This proactive approach minimizes interruptions and keeps production lines running smoothly. Additionally, by accurately measuring material flow, businesses can optimize their processes to reduce material wastage and improve overall efficiency.
Integration
Modern conveyor belt weightometer systems can be integrated with IT systems for automated reporting and monitoring. This integration enables businesses to collect and analyze data from their conveyor belt weightometers seamlessly, providing valuable insights into their operations. For example, systems from companies like Thermo Fisher Scientific offer integration capabilities with enterprise resource planning (ERP) and manufacturing execution systems (MES). This integration allows for automated data transfer, reducing the need for manual data entry and minimizing the risk of errors. By having access to real-time data, businesses can make informed decisions, improve process control, and enhance overall operational efficiency.
Practical Applications and Industry Examples
Conveyor belt weightometer systems are employed across various industries to enhance operational efficiency and accuracy. In the mining sector, conveyor belt weightometers are used to monitor the flow of extracted minerals, ensuring that operations meet production quotas and comply with environmental regulations. For example, Vale S.A. utilizes conveyor belt weightometers to track the volume of iron ore transported from its mines. This accurate measurement helps the company optimize its transportation logistics, reduce costs, and ensure compliance with export regulations.
In the manufacturing industry, conveyor belt weightometers help in batching and blending processes by providing precise measurements of raw materials. This accuracy is crucial for maintaining product consistency and quality. For instance, Procter & Gamble employs conveyor belt weightometers in its production lines to ensure that the correct amounts of ingredients are used in its products, resulting in high-quality finished goods and minimal material wastage.
In the food processing industry, conveyor belt weightometers are used to measure the weight of ingredients in automated production lines. Nestlé, for example, uses conveyor belt weightometers to ensure that each batch of its products meets specified weight criteria, maintaining quality standards and minimizing waste.
Enhancing Operational Efficiency with Conveyor Belt Weightometer Systems
Implementing a conveyor belt weightometer system offers numerous benefits, from enhancing inventory management and process control to optimizing material handling operations. By providing accurate, real-time data on material flow, these systems enable businesses to make informed decisions, improve efficiency, and reduce costs. In industries such as mining, agriculture, and manufacturing, where precise material measurement is crucial, conveyor belt weightometer systems are invaluable tools that contribute significantly to operational success and profitability.
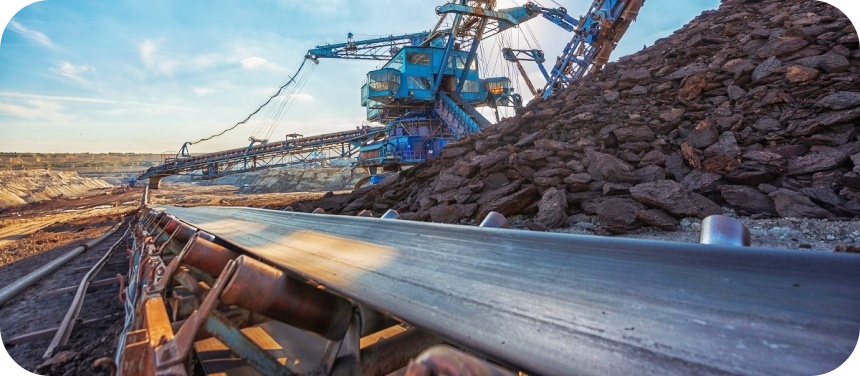
CST Belt Weigher Manual: Operating and Maintenance Guide for Conveyor Belt Weightometer
Introduction to CST Belt Weigher
The CST belt weigher is a widely used model in industries such as mining, agriculture, and manufacturing due to its reliability and accuracy. As a crucial component of a conveyor belt weightometer system, the CST belt weigher provides precise measurements of material flow, which is essential for inventory management, process control, and optimization. Understanding the CST belt weigher manual is vital for ensuring proper operation, calibration, and maintenance of the system. Companies like Siemens and SRO Technology often employ CST belt weighers in their conveyor belt weightometer systems to ensure accurate and efficient material handling.
Key Sections of the CST Belt Weigher Manual
Installation
Installing the CST belt weigher correctly is critical to ensuring its accuracy and reliability. The installation section of the CST belt weigher manual provides a detailed, step-by-step guide to setting up the device on a conveyor system.
- Preparation: Before installation, it is important to ensure that the conveyor belt is properly aligned and tensioned. This helps in avoiding any measurement errors caused by misalignment or slack in the belt.
- Mounting the Weighing Frame: The weighing frame must be securely attached to the conveyor structure. The manual specifies the exact points where the frame should be mounted to minimize vibrations and ensure stable weight readings.
- Connecting Load Cells: The load cells should be carefully installed within the weighing frame. The manual emphasizes the importance of handling these sensitive components with care to avoid damage. For example, Siemens’ CST belt weighers use high-precision load cells that require meticulous installation to maintain their accuracy.
- Wiring and Electrical Connections: Proper wiring is crucial for the functionality of the CST belt weigher. The manual provides detailed instructions on connecting the load cells, speed sensor, and controller to the power supply and data acquisition system. Incorrect wiring can lead to inaccurate readings or system malfunctions.
- Initial Testing: After installation, an initial test run is recommended to ensure that all components are functioning correctly. The manual includes checklists and diagnostic tests to verify the installation.
Calibration
Calibration is a vital process for maintaining the accuracy of a conveyor belt weightometer system. The calibration section of the CST belt weigher manual offers comprehensive instructions on how to calibrate the system to ensure precise measurements.
- Calibration Procedure: The manual outlines a step-by-step procedure for calibrating the CST belt weigher. This includes setting up calibration weights, running the conveyor belt at specific speeds, and adjusting the controller settings to match the known weights.
- Zero Calibration: Ensuring that the conveyor belt weightometer reads zero when there is no material on the belt is crucial. The manual provides detailed instructions on performing zero calibration to eliminate any baseline drift.
- Span Calibration: Span calibration involves adjusting the system to ensure that it accurately measures a known weight. This process is essential for verifying the linearity and accuracy of the weight readings. For example, METTLER TOLEDO recommends performing span calibration at regular intervals to maintain the precision of their conveyor belt weightometer systems.
- Calibration Frequency: The manual specifies the recommended frequency for calibration, which can vary depending on the operational environment and the intensity of use. Regular calibration ensures consistent accuracy and reliability of the weight measurements.
Troubleshooting
The troubleshooting section of the CST belt weigher manual addresses common issues that might arise during the operation of a conveyor belt weightometer system and provides solutions to ensure continuous operation.
- Common Issues: The manual lists common problems such as erratic weight readings, zero drift, and load cell malfunctions. Each issue is accompanied by a detailed explanation of potential causes and recommended solutions. For instance, erratic readings might be caused by loose connections or environmental vibrations, which can be resolved by securing the connections and stabilizing the weighing frame.
- Diagnostic Tools: The manual includes instructions on using diagnostic tools and software to identify and rectify issues. These tools help in pinpointing the exact location and nature of the problem, facilitating quicker and more effective troubleshooting.
- Maintenance Tips: Regular maintenance is crucial for the longevity and reliability of the conveyor belt weightometer system. The manual provides maintenance schedules and tips, such as inspecting load cells for damage, cleaning the weighing frame, and checking electrical connections. Companies like Thermo Fisher Scientific recommend routine maintenance checks to prevent unexpected downtime and ensure optimal performance.
- Technical Support: In cases where troubleshooting steps do not resolve the issue, the manual provides contact information for technical support. Many manufacturers, including Siemens, offer dedicated support services to assist with complex problems and provide spare parts or on-site assistance if needed.
Understanding and following the CST belt weigher manual is essential for the proper operation and maintenance of conveyor belt weightometer systems. By adhering to the installation, calibration, and troubleshooting guidelines, businesses can ensure accurate and reliable measurements, enhancing their overall process efficiency and operational productivity.
MAVIS-ICS-ARM Manual: User Guide for Conveyor Belt Weightometer
Introduction to MAVIS-ICS-ARM System
The MAVIS-ICS-ARM system is an advanced control system designed to enhance the functionality and integration capabilities of conveyor belt weightometers. This sophisticated system provides precise control and monitoring of material flow on conveyor belts, making it indispensable in industries such as mining, manufacturing, and agriculture. By integrating the MAVIS-ICS-ARM system with a conveyor belt weightometer, businesses can achieve higher accuracy in weight measurement, improved data management, and enhanced operational efficiency. Companies like Thermo Fisher Scientific and Siemens use similar advanced control systems to optimize their conveyor belt weightometer operations, ensuring reliable and accurate material handling.
Key Features of MAVIS-ICS-ARM Manual
Setup and Configuration
The setup and configuration section of the MAVIS-ICS-ARM manual provides comprehensive instructions for installing the system and integrating it with a conveyor belt weightometer. Proper setup is crucial for ensuring accurate weight measurements and optimal system performance.
- Initial Setup: This involves unpacking the MAVIS-ICS-ARM components and verifying that all parts are present. The manual provides a detailed checklist to help users confirm that they have all necessary components.
- System Configuration: The configuration process includes connecting the MAVIS-ICS-ARM to the conveyor belt weightometer and other system components. This may involve wiring the load cells, speed sensors, and controllers to the MAVIS-ICS-ARM system. For instance, Siemens recommends using shielded cables to minimize electrical interference and ensure accurate signal transmission.
- Software Installation: The MAVIS-ICS-ARM system requires specific software to function correctly. The manual provides step-by-step instructions for installing the software on a compatible computer or control unit. This software enables users to configure system settings, monitor real-time data, and perform diagnostics.
- Calibration: Initial calibration is necessary to ensure that the system provides accurate weight readings. The manual details the calibration process, including the placement of test weights on the conveyor belt and adjusting the system settings to match the known values of these weights.
Operation
The operation section of the MAVIS-ICS-ARM manual offers a detailed guide on using the system for daily operations. This section is designed to help users maximize the benefits of their conveyor belt weightometer system.
- User Interface: The MAVIS-ICS-ARM system features a user-friendly interface that allows operators to monitor and control the conveyor belt weightometer. The manual explains the various functions and controls available on the interface, including how to start and stop the system, view real-time weight data, and generate reports.
- Monitoring and Alerts: The system is equipped with monitoring capabilities that provide real-time alerts for any anomalies or issues. For example, if the weight measurements deviate from expected values, the system can trigger an alert to notify the operator. This feature is crucial for maintaining operational efficiency and preventing potential problems.
- Data Management: The MAVIS-ICS-ARM system allows users to store and analyze weight measurement data. The manual provides instructions on how to export data to external systems, such as ERP or MES platforms, for further analysis. This capability is essential for businesses that rely on accurate data for decision-making and process optimization.
- Routine Operations: The manual includes guidelines for routine operations, such as regular inspections and basic maintenance tasks. These guidelines help ensure that the system operates smoothly and continues to provide accurate weight measurements.
Maintenance
Maintenance is critical to ensuring the longevity and reliability of the MAVIS-ICS-ARM system. The maintenance section of the manual offers tips and best practices for keeping the system in optimal condition.
- Regular Inspections: Conducting regular inspections of the MAVIS-ICS-ARM system and the conveyor belt weightometer components is essential. The manual provides checklists for inspecting the load cells, speed sensors, wiring, and other critical parts.
- Preventive Maintenance: The manual outlines preventive maintenance tasks, such as cleaning the system components, checking for signs of wear and tear, and ensuring that all connections are secure. For example, Thermo Fisher Scientific recommends performing preventive maintenance at least once a month to prevent unexpected downtime.
- Software Updates: Keeping the system’s software up to date is crucial for maintaining its functionality and performance. The manual includes instructions for downloading and installing software updates, which may include new features, performance improvements, and security enhancements.
- Troubleshooting: The maintenance section also covers troubleshooting common issues that may arise during system operation. The manual provides detailed steps for diagnosing and resolving problems, such as inconsistent weight readings or communication errors between system components.
IPC-14-S Manual: Comprehensive Instructions
The IPC-14-S is another sophisticated control system used in conjunction with conveyor belt weightometers. This manual provides detailed instructions for users to ensure proper installation, operation, and maintenance of the system.
Installation
The installation section of the IPC-14-S manual offers guidelines for setting up the system and integrating it with a conveyor belt weightometer. Proper installation is crucial for ensuring accurate and reliable weight measurements.
- Preparation: Before installation, it is important to review the system requirements and ensure that the installation site is suitable. This includes checking the environmental conditions, power supply, and space availability.
- Mounting the Components: The manual provides detailed instructions for mounting the IPC-14-S components, such as the control unit, load cells, and speed sensors. Proper mounting is essential to minimize vibrations and ensure stable weight readings.
- Wiring and Connections: Correct wiring and connections are critical for the system’s functionality. The manual includes diagrams and step-by-step instructions for connecting the IPC-14-S components to the conveyor belt weightometer and other related systems.
- Initial Testing: After installation, initial testing is necessary to verify that the system is functioning correctly. The manual provides test procedures and checklists to ensure that all components are working as expected.
User Interface
The user interface section explains the interface and controls of the IPC-14-S system, helping users understand how to operate it effectively.
- Overview of Controls: The manual provides an overview of the various controls and displays on the IPC-14-S interface, including buttons, indicators, and menus. Understanding these controls is essential for efficient system operation.
- Navigating the Interface: Detailed instructions on navigating the interface, including how to access different menus, view real-time data, and adjust system settings. This section helps users become proficient in using the IPC-14-S system.
- Customizing Settings: The IPC-14-S system allows users to customize various settings to match their specific operational needs. The manual includes instructions for configuring settings such as calibration parameters, alert thresholds, and data logging options.
Calibration and Maintenance
Calibration and maintenance are critical to ensuring the accuracy and reliability of the IPC-14-S system. This section provides detailed procedures for both.
- Calibration Procedures: The manual outlines the steps for calibrating the IPC-14-S system, including the use of test weights and adjustments to the system settings. Regular calibration is necessary to maintain accurate weight measurements.
- Maintenance Tips: Best practices for maintaining the IPC-14-S system, including regular inspections, cleaning, and preventive maintenance tasks. The manual also provides troubleshooting tips for common issues that may arise during system operation.
- Software Updates: Instructions for updating the system’s software to ensure it remains current and fully functional. Software updates may include performance improvements, new features, and bug fixes.
Understanding and following the MAVIS-ICS-ARM and IPC-14-S manuals are essential for the proper operation and maintenance of conveyor belt weightometer systems. By adhering to the setup, operation, and maintenance guidelines provided in these manuals, businesses can ensure accurate and reliable weight measurements, enhancing their overall operational efficiency and productivity.
FAQs about conveyor belt weightometer
A conveyor belt weightometer measures weight by integrating load cells and speed sensors to calculate the mass of materials on a conveyor belt. The load cells detect the weight of the material as it passes over them, converting the mechanical force into an electrical signal. The speed sensor measures the conveyor belt’s speed. By combining these data points, the weightometer system calculates the total weight and flow rate of the material. This real-time data is crucial for inventory management, process control, and ensuring accurate material handling. Companies like Thermo Fisher Scientific and Siemens provide advanced conveyor belt weightometer systems that offer precise weight measurements and integrate seamlessly with existing plant management systems.
The weight of a conveyor belt weightometer system per meter can vary significantly based on the type and design of the system. Typically, a standard conveyor belt weightometer system can weigh between 20 to 50 kilograms per meter. Factors influencing the weight include the materials used in the construction of the belt, such as rubber, metal, or composite materials, and the additional components like load cells, speed sensors, and controllers. For instance, a heavy-duty industrial conveyor belt used in mining operations might weigh more due to its robust construction to withstand harsh conditions. Accurate information on the weight of a specific conveyor belt weightometer system can usually be found in the product specifications provided by manufacturers like METTLER TOLEDO or Thermo Fisher Scientific.
Calculating the counterweight for a conveyor belt equipped with a weightometer involves balancing the weight of the belt, the materials being transported, and the dynamic forces during operation. The counterweight ensures the belt remains taut and operates smoothly. First, determine the total weight of the belt and the maximum load it will carry. Then, calculate the tension required to keep the belt taut by considering factors such as the belt’s length, the material’s weight, and the conveyor’s incline. The counterweight should be adjusted to counterbalance these forces effectively. Manufacturers often provide detailed guidelines and formulas in their technical manuals to assist in these calculations. For precise calculations, it’s advisable to use specialized software or consult with experts from companies like Siemens or SRO Technology, who have extensive experience in conveyor belt weightometer systems.
A conveyor belt weightometer is used to measure the weight of materials being transported on a conveyor belt in real time. This device is essential in various industries, including mining, agriculture, and manufacturing, where accurate material measurement is critical for process control, inventory management, and operational efficiency. The weightometer provides real-time data on the mass and flow rate of the material, helping businesses monitor production rates, ensure compliance with production targets, and optimize material handling processes. For example, in the mining industry, companies like Rio Tinto and BHP Billiton rely on conveyor belt weightometers to accurately measure the quantity of extracted minerals, ensuring that operations are efficient and compliant with regulatory standards. The data collected by the weightometer can also be integrated into larger plant management systems for enhanced decision-making and process optimization.
To measure the weight of a conveyor belt, you typically use a scale or a weighing system. The methods include:
Static Weighing: The conveyor belt is stopped, and a segment of the belt is placed on a scale to measure its weight directly.
In-line Weighing: Using belt weighers or belt scales that are installed on the conveyor system. These devices measure the weight of the belt as it moves over the scale.
To calculate the counterweight for a conveyor belt, first determine the total load on the belt, including the weight of the belt itself and the material being transported. Calculate the required tension using the formula T=(Wb+Wm)⋅L⋅g/2,
where Wb is the weight of the belt per meter, Wm is the weight of the material per meter, L
is the length of the conveyor, and g is the acceleration due to gravity (9.81 m/s²). The counterweight should be set to 1.5 to 2 times the required tension to account for dynamic conditions and ensure smooth operation.
Weightometers, also known as conveyor belt scales or belt weighers, come in several types, including:
Single-Idler Weightometers: Use one idler to support the belt and measure its weight.
Multi-Idler Weightometers: Use multiple idlers to increase accuracy by averaging the weight over several points.
Fixed Idler Weightometers: The idlers are fixed in place and measure the weight as the belt moves over them.
Suspended Idler Weightometers: The idlers are suspended and provide weight measurements through load cells.
Integrating Weightometers: These systems integrate the weight measurements over time to provide total weight and rate of material flow.
Last Updated on August 8, 2024 by Jordan Smith
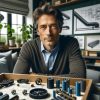
Jordan Smith, a seasoned professional with over 20 years of experience in the conveyor system industry. Jordan’s expertise lies in providing comprehensive solutions for conveyor rollers, belts, and accessories, catering to a wide range of industrial needs. From initial design and configuration to installation and meticulous troubleshooting, Jordan is adept at handling all aspects of conveyor system management. Whether you’re looking to upgrade your production line with efficient conveyor belts, require custom conveyor rollers for specific operations, or need expert advice on selecting the right conveyor accessories for your facility, Jordan is your reliable consultant. For any inquiries or assistance with conveyor system optimization, Jordan is available to share his wealth of knowledge and experience. Feel free to reach out at any time for professional guidance on all matters related to conveyor rollers, belts, and accessories.