The Future of Conveyor Belt Welder: Trends and Predictions
In the realm of industrial operations, the importance of a conveyor belt welder cannot be overstated. These specialized tools play a pivotal role in the maintenance and efficiency of conveyor belt systems, which are integral to numerous industries ranging from mining to food processing. A conveyor belt welder is designed to swiftly and effectively join and repair conveyor belts, ensuring minimal downtime and maintaining the continuous flow of operations. Their ability to provide on-site, quick fixes not only saves time but also significantly reduces potential losses due to halted production. This introduction aims to shed light on the critical function that conveyor belt welders serve in keeping industrial conveyor systems running smoothly and efficiently.
Types of the Conveyor Belt Welder
The world of material handling and industrial processes has seen significant advancements with the introduction of various types of conveyor belt welders. These specialized devices play a crucial role in the maintenance, repair, and fabrication of conveyor belts, ensuring efficiency and longevity in numerous industries. Below, we explore the different types of conveyor belt welders, each designed to cater to specific needs and belt types.
Flat Belt Welder The flat belt welder is a pivotal tool in the realm of conveyor belt maintenance and fabrication. This type of conveyor belt welder is specifically designed to handle the demands of flat belts, which are commonly used in industries such as packaging, food processing, and manufacturing.
- Description and Applications: A flat belt welder typically features a robust design that can withstand the rigors of industrial environments. It is equipped with specialized heating elements and pressure systems to ensure a strong and durable bond. The primary application of this welder is to join or repair flat conveyor belts, often made of materials like PVC or polyurethane. Its precision and efficiency make it an indispensable tool for minimizing downtime and maintaining continuous production lines.
Polyurethane Belt Welder Polyurethane belts, known for their flexibility and durability, require a specific type of welding tool for effective maintenance. The polyurethane belt welder is designed to cater to these unique requirements.
- Features and Suitability for Specific Belt Types: This conveyor belt welder is characterized by its ability to deliver clean and strong welds on polyurethane belts. It often comes with adjustable temperature controls and a specialized welding head, making it suitable for various thicknesses and widths of polyurethane belts. The precision and control offered by this welder make it ideal for applications in food processing, pharmaceuticals, and other sectors where hygiene and precision are paramount.
Round Belt Welding Kit Round belts, often used in conveying systems that require flexibility and durability, necessitate a unique approach to welding. The round belt welding kit is an essential tool for this purpose.
- Components and Usage: This kit typically includes a heat wand, a cutting tool, and a welding jig. The heat wand is designed to melt the ends of the round belt precisely, while the jig ensures proper alignment during the welding process. The cutting tool is used to trim the belt to the desired length. This type of conveyor belt welder is invaluable in industries like textile, printing, and packaging, where round belts are prevalent. Its ease of use and portability make it a popular choice for on-site repairs and adjustments.
The selection of the right conveyor belt welder is crucial for the efficient and effective maintenance of different types of conveyor belts. Each welder type offers unique features and is suited for specific belt materials and applications, ensuring that conveyor systems remain operational with minimal downtime.
Conveyor Belt Welder Price Factors: Cost Variations
The price of a conveyor belt welder is influenced by several key factors, making it essential for businesses to understand what drives these cost variations. Firstly, the type of conveyor belt welder plays a significant role in determining its price. Manual welders, generally more affordable, are suitable for smaller operations or less frequent use. On the other hand, automated or semi-automated welders, while more expensive, offer higher efficiency and precision, especially beneficial for larger-scale operations or frequent welding needs.
Another critical factor affecting the price is the technology and features incorporated into the welder. Advanced models equipped with features like temperature control, automatic pressure adjustment, and digital interfaces command higher prices due to their enhanced capabilities and ease of use. Additionally, the build quality and brand reputation also contribute to the cost. Renowned brands known for durability and reliability might offer their equipment at a premium, but this often translates into longer service life and better performance.
The size and capacity of the conveyor belt welder also impact its price. Larger welders designed for wider belts or heavy-duty use are typically more expensive than smaller, more basic models. Furthermore, the material compatibility of the welder – whether it can handle various types of conveyor belt materials – can also influence its cost.
In terms of cost-effectiveness, while higher-priced conveyor belt welding machine may seem like a significant initial investment, they can offer greater value in the long run through durability, efficiency, and lower maintenance costs. Conversely, more affordable models might be cost-effective for businesses with limited welding needs or smaller operations.
When considering a conveyor belt welder, it’s important to weigh these price factors against the specific needs and scale of your operation. Understanding the balance between price, features, and long-term benefits is key to making a cost-effective decision.
Conveyor Belt Welder Kits
The use of a conveyor belt welder is essential in the maintenance and repair of conveyor belts in various industrial settings. These welding kits come in different types, each designed to cater to specific belt materials and applications. Understanding the contents and unique features of these kits is crucial for effective and efficient belt repairs.
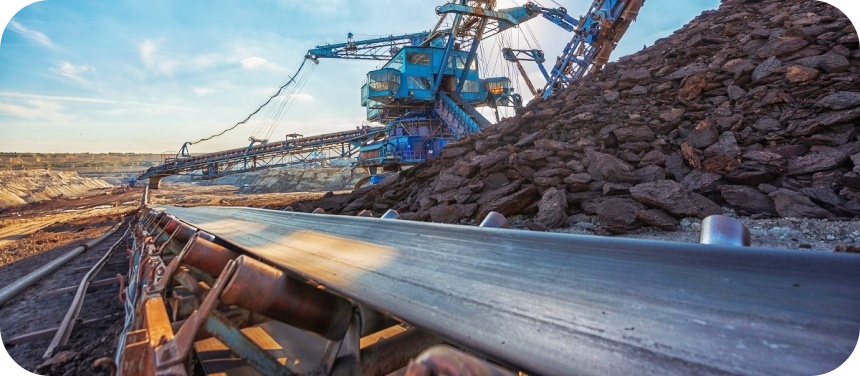
Flat Belt Welding Kit
A flat belt welding kit is an indispensable tool for those who work with flat conveyor belts. The contents of this kit typically include a high-precision welding iron, a heat-resistant welding clamp, and a cutting tool. These components are specifically designed to handle the unique properties of flat belts, such as their thickness and material composition.
The primary application of this kit is in the repair and joining of flat belts, which are commonly used in material handling and packaging industries. The precision tools in the kit allow for a seamless welding process, ensuring a strong and durable bond. This is particularly important in applications where the integrity of the belt is crucial for maintaining a smooth and uninterrupted operation.
Polyurethane Belt Welding Kit
When it comes to welding polyurethane belts, a specialized polyurethane belt welding kit is required. This kit stands out due to its specialized tools that cater to the unique properties of polyurethane, a material known for its flexibility and strength.
The kit typically includes a specially designed welding iron that operates at the optimal temperature for polyurethane, ensuring a strong bond without damaging the belt. It also contains a precision cutter for clean cuts and a heat-resistant press to hold the belt in place during the welding process. The advantage of using this kit lies in its ability to produce a nearly invisible seam, maintaining the belt’s flexibility and strength. This is particularly beneficial in applications where the conveyor belt undergoes constant bending and flexing.
Round Belt Welding Kit
The round belt welding kit is distinct from other conveyor belt welder kits due to its specialized design for round belts, often used in applications requiring high flexibility and durability. This kit typically includes a unique welding tool that conforms to the round shape of the belt, ensuring an even and consistent weld.
Unlike flat belt kits, the round belt welding kit often comes with a range of adapters to accommodate different diameters of round belts. This versatility is crucial in industries where machinery requires varying sizes of round belts. The kit’s design ensures a strong and uniform weld, critical for the longevity and performance of round belts in dynamic and high-stress environments.
Each type of conveyor belt welder kit is designed with specific applications and belt materials in mind. Choosing the right kit is essential for ensuring effective repairs and maintenance, ultimately contributing to the longevity and efficiency of conveyor belt systems in various industrial applications.
Choosing the Best Conveyor Belt Welder
Selecting the best conveyor belt welder is a critical decision for businesses that rely on efficient and reliable conveyor systems. The right welder not only ensures the longevity of the conveyor belt but also maintains the smooth operation of the entire conveying system. Here, we delve into the criteria and top features to consider when choosing the most suitable conveyor belt welder for your needs.
Criteria for Selecting the Best Conveyor Belt Welder
- Compatibility with Belt Material: The foremost criterion is the compatibility of the welder with the specific materials of your conveyor belts. Different welders are designed for various materials like PVC, polyurethane, or polyester. Ensure that the welder you choose is suitable for the type of belts used in your facility.
- Welding Precision and Strength: The quality of the weld is paramount. Look for a conveyor belt welder that offers precise control over temperature and pressure, as these factors significantly influence the strength and durability of the weld.
- Ease of Use and Portability: In many industrial settings, the ability to perform quick and efficient repairs on-site is crucial. A user-friendly, portable conveyor belt welder can save valuable time and reduce downtime.
- Adjustability and Versatility: A versatile welder that can handle different widths and thicknesses of belts, and is adjustable for various types of welds, can be a cost-effective investment, especially for facilities with diverse conveyor systems.
- Durability and Maintenance Needs: Industrial environments can be harsh. Choose a welder that is built to last and requires minimal maintenance, ensuring long-term reliability and reduced operational costs.
Overview of Top Features to Look for
- Advanced Control Systems: Modern conveyor belt welders come with advanced control systems for precise temperature and pressure adjustments, ensuring high-quality welds.
- Automated Features: Some high-end models offer automated features that can significantly speed up the welding process and reduce the likelihood of human error.
- Safety Mechanisms: Safety should never be compromised. Look for welders with built-in safety features like emergency stop buttons, heat shields, and automatic cool-down functions.
- Energy Efficiency: Energy-efficient models not only reduce operational costs but also support sustainable practices.
- After-Sales Support and Warranty: Good after-sales support and a solid warranty can be indicative of the manufacturer’s confidence in their product. It also ensures peace of mind in case of any issues.
Choosing the best conveyor belt welder involves a careful consideration of the material compatibility, welding quality, ease of use, versatility, and durability of the equipment. Additionally, advanced features, safety mechanisms, energy efficiency, and reliable after-sales support are crucial factors that contribute to the overall value and effectiveness of the welder in your conveyor belt maintenance toolkit.
Leading Conveyor Belt Welder Manufacturers: Industry Innovators
The market for conveyor belt welders is diverse, with several leading manufacturers standing out due to their innovative approaches and reliable products.
Mafdel’s Approach to Conveyor Belt Welding:
- Mafdel is renowned for its advanced conveyor belt welding technology. They offer a range of welders that cater to different industrial needs, from lightweight to heavy-duty applications.
- Their product range includes both manual and automated welders, known for their efficiency and durability. Mafdel’s welders are designed to ensure precise and strong welds, contributing to the longevity of conveyor belts.
- The company also focuses on user-friendly designs, making their equipment accessible to operators with varying levels of expertise.
Habasit Belt Welder:
- Habasit is another key player in the conveyor belt welder market, known for its high-quality welding solutions.
- Their belt welders are praised for features like precise temperature control, speed, and consistent welding quality, making them a preferred choice in industries where accuracy is paramount.
- Habasit has built a strong market reputation for reliability and customer service, offering tailored solutions to meet specific conveyor belt welding requirements.
Other Notable Manufacturers in the Market:
- Beyond Mafdel and Habasit, the market includes other notable manufacturers such as Flexco, Forbo Siegling, and Thermofix. Each of these companies brings unique technologies and specialties to their conveyor belt welders, catering to a wide range of industrial applications.
- These manufacturers are known for their innovation in conveyor belt welding technology, continually evolving their product lines to meet the changing demands of various industries.
When selecting a conveyor belt welder, it’s important to consider the specific needs of your operation and the strengths of each manufacturer. Companies like Mafdel and Habasit lead the way with their advanced technologies and customer-focused solutions, but the market offers a variety of options to suit different requirements and budgets.
Advanced Features in Modern Conveyor Belt Welder
The landscape of conveyor belt maintenance and fabrication has been revolutionized by the modern conveyor belt welder, which incorporate advanced features and innovations. These advancements not only enhance the efficiency and quality of welding but also contribute significantly to the ease of operation and overall productivity in various industrial settings. Let’s delve into the key innovations in conveyor belt welding technology and the pivotal role of automation and precision in this domain.
Innovations in Conveyor Belt Welding Technology
- Enhanced Heat Control: The modern conveyor belt welder comes equipped with sophisticated heat control mechanisms. This allows for precise temperature regulation, which is crucial for creating strong and durable welds without damaging the belt material.
- Integrated Pressure Systems: The latest models feature advanced pressure systems that ensure uniform pressure distribution during the welding process. This uniformity is essential for achieving consistent weld quality across the entire seam.
- Customizable Welding Programs: Many contemporary conveyor belt welders offer programmable settings. This feature allows operators to save specific welding parameters for different types of belts, streamlining the welding process for various applications.
- Improved Safety Features: Safety has been a significant focus in the development of modern welders. Features like automatic shut-off, heat shields, and emergency stop buttons are now standard, ensuring operator safety during the welding process.
The Role of Automation and Precision in Welding
- Automation in Conveyor Belt Welders: Automation plays a crucial role in modern conveyor belt welders. Automated systems can precisely control the welding parameters, leading to consistent and high-quality welds. This reduces the reliance on manual skills and minimizes the potential for human error.
- Precision in Welding: Precision is paramount in conveyor belt welding. The latest welders are designed to provide exact alignment and pressure, ensuring that the weld is not only strong but also aesthetically pleasing. This is particularly important in industries where the appearance of the belt is as crucial as its functionality.
- Quality Control and Reproducibility: With advanced features, modern conveyor belt welders ensure that each weld is reproducible and meets high-quality standards. This consistency is vital for industries that require uniformity across multiple conveyor systems.
- Efficiency and Productivity: The integration of automation and precision in conveyor belt welders significantly boosts efficiency. Faster welding times, reduced need for reworks, and the ability to handle complex welding tasks easily contribute to higher productivity levels.
The advanced features in modern conveyor belt welders, marked by innovations in technology, automation, and precision, have dramatically transformed the process of conveyor belt welding. These developments not only enhance the quality and durability of the welds but also contribute to increased safety, efficiency, and productivity in various industrial applications. As technology continues to evolve, we can expect even more sophisticated and efficient conveyor belt welders in the future.
Need More Details? Fill Out Our Inquiry Form for Conveyor Belts.
Maintenance and Safety in the Conveyor Belt Welder
Maintaining and operating a conveyor belt welder safely is crucial in any industrial setting. Proper maintenance ensures the longevity and efficiency of the welding equipment, while adherence to safety precautions is vital for protecting workers from potential hazards associated with the welding process.
Best Practices for Maintaining Conveyor Belt Welders
Regular maintenance of a conveyor belt welder is essential for its optimal performance and longevity. Here are some best practices:
- Routine Inspection: Regularly inspect the conveyor belt welder for any signs of wear or damage. Check the welding iron, clamp, and any other components for functionality.
- Cleanliness: Keep the welder clean from any debris or dust. Accumulation of materials can affect the performance and may pose a fire hazard.
- Proper Storage: Store the conveyor belt welder in a dry, clean environment to prevent rusting or degradation of its parts.
- Regular Calibration: Ensure that the welding temperature and pressure are regularly calibrated according to the manufacturer’s specifications. This is crucial for achieving strong and durable welds.
- Component Replacement: Replace any worn or damaged parts promptly. Using damaged equipment can lead to poor welds and can be a safety hazard.
- Professional Servicing: Have the conveyor belt welder serviced by a professional periodically to ensure it remains in good working condition.
Safety Precautions During the Welding Process
Safety is paramount when operating a conveyor belt welder. Here are key precautions to follow:
- Personal Protective Equipment (PPE): Always wear appropriate PPE, including heat-resistant gloves, eye protection, and a face shield.
- Ventilation: Ensure proper ventilation in the welding area to avoid the inhalation of harmful fumes.
- Fire Safety: Keep a fire extinguisher nearby and ensure the welding area is free from flammable materials.
- Training: Only trained and qualified personnel should operate the conveyor belt welder. This ensures that they are aware of the operational procedures and safety measures.
- Emergency Procedures: Be familiar with emergency procedures in case of an accident. Quick and appropriate responses can prevent serious injuries.
- Electrical Safety: Regularly inspect electrical cords and connections for damage. Ensure the welder is properly grounded to prevent electrical shocks.
By following these maintenance and safety guidelines, the risk of accidents and equipment failure can be significantly reduced. Regular upkeep and responsible handling of the conveyor belt welder are essential for a safe and productive working environment.
FAQs about Conveyor Belt Welder
Welding a conveyor belt involves several steps. First, prepare the belt ends by skiving or cutting them to create a smooth, even surface. Then, align the belt ends and use a belt welding tool, typically a heat press or vulcanizer, to apply heat and pressure. This process melts the belt material, allowing the ends to fuse together. It’s crucial to maintain proper alignment and pressure to ensure a strong, durable bond.
The best tool for cutting a conveyor belt depends on the belt’s material and thickness. For most standard belts, a sharp utility knife or a specialized belt cutting tool is sufficient. For thicker or reinforced belts, you may need a more robust tool like an electric belt cutter or a high-torque rotary cutter. Always ensure the tool is sharp and designed for the specific type of belt material.
To use a belt welder, start by preparing the belt ends as per the manufacturer’s instructions. Position the belt ends in the welder, ensuring they are properly aligned. Set the welder to the correct temperature and pressure settings for your belt material. Activate the welder to apply heat and pressure, which will melt and fuse the belt ends. After the welding cycle, allow the joint to cool under pressure to form a solid bond. Always follow the specific instructions of your belt welder model.
Welding a plastic conveyor belt typically involves a process similar to welding other types of belts but with a focus on the specific properties of plastic. Clean and prepare the belt ends, ensuring they are cut straight and fit together without gaps. Use a plastic belt welding tool, which often includes a heat source and a press. The tool applies controlled heat to melt the plastic, and then pressure is applied to fuse the belt ends together. It’s important to use the right temperature and pressure settings for the type of plastic your belt is made of.
Last Updated on July 23, 2024 by Jordan Smith
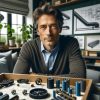
Jordan Smith, a seasoned professional with over 20 years of experience in the conveyor system industry. Jordan’s expertise lies in providing comprehensive solutions for conveyor rollers, belts, and accessories, catering to a wide range of industrial needs. From initial design and configuration to installation and meticulous troubleshooting, Jordan is adept at handling all aspects of conveyor system management. Whether you’re looking to upgrade your production line with efficient conveyor belts, require custom conveyor rollers for specific operations, or need expert advice on selecting the right conveyor accessories for your facility, Jordan is your reliable consultant. For any inquiries or assistance with conveyor system optimization, Jordan is available to share his wealth of knowledge and experience. Feel free to reach out at any time for professional guidance on all matters related to conveyor rollers, belts, and accessories.