Conveyor Belt Cleaning Systems: Conveyor Belt Wipers
Conveyor belt wipers are essential components in the maintenance and operation of conveyor belt systems. Conveyor belt wipers remove carryback, enhance material flow, prevent buildup, and improve conveyor system efficiency and safety. These devices are designed to clean the surface of conveyor belts, removing any debris, material buildup, and contaminants that can affect the efficiency and lifespan of the conveyor system. Properly maintained conveyor belt wipers ensure smooth operation, reduce wear and tear on the belt, and prevent downtime caused by belt malfunctions. In industries where conveyor belts are integral to production, the use of effective conveyor belt wipers is critical to maintaining optimal productivity and ensuring the longevity of the conveyor system.
Features & Benefits of Conveyor Belt Wipers
Features of Conveyor Belt Wipers
- High-Quality Materials: Conveyor belt wipers are made from durable, wear-resistant materials such as polyurethane, rubber, or specially treated polymers. These materials ensure longevity even under harsh working conditions.
- Effective Debris Removal: The wipers are designed to efficiently remove debris, dust, and other materials from the conveyor belt surface. This helps in maintaining the cleanliness and efficiency of the belt system.
- Customizable Design: Conveyor belt wipers can be customized to fit various belt sizes and types, ensuring a perfect fit for any specific conveyor system.
- Easy Installation and Maintenance: The wipers are designed for easy installation and minimal maintenance, reducing downtime and ensuring continuous operation.
- Resistant to Harsh Environments: These wipers are built to withstand extreme temperatures, chemicals, and abrasive materials, making them suitable for a wide range of industrial applications.
- Improved Belt Tracking: By maintaining a clean belt surface, the wipers help in reducing belt misalignment, which can lead to increased wear and tear.
- Low Friction Design: The wipers are engineered with a low-friction design, which minimizes drag on the belt and reduces energy consumption.
Benefits of Conveyor Belt Wipers
- Enhanced Belt Longevity: By keeping the conveyor belt clean, the wipers significantly reduce the wear and tear on the belt, extending its service life and reducing replacement costs.
- Improved Operational Efficiency: Clean conveyor belts operate more smoothly, reducing the likelihood of blockages, misalignments, or breakdowns, which can lead to costly production stoppages.
- Reduced Maintenance Costs: With less debris on the belt, there is a lower risk of damage to the belt and other components, leading to fewer maintenance requirements and lower overall maintenance costs.
- Safety Improvements: Clean conveyor systems are safer for workers, as they reduce the risk of slipping or tripping due to material buildup. This also minimizes the potential for accidents.
- Energy Efficiency: The low-friction design of the wipers reduces the energy required to run the conveyor system, contributing to lower operational costs and improved energy efficiency.
- Versatile Applications: Conveyor belt wipers are suitable for use in a wide range of industries, including mining, agriculture, manufacturing, and logistics, making them a versatile solution for various material handling needs.
- Environmental Benefits: By preventing material spillage and dust generation, conveyor belt wipers help in maintaining a cleaner work environment and reduce the environmental impact of operations.
These features and benefits highlight the importance of conveyor belt wipers in maintaining the efficiency, safety, and longevity of conveyor systems across various industries.

Conveyor Belt Wipers Specifications
Conveyor Belt Wipers Specifications
Material Composition:
- Polyurethane: Hardness range of 60-95 Shore A, known for its excellent wear resistance and flexibility.
- Rubber: Typically made of natural or synthetic rubber, with hardness ranging from 40-80 Shore A.
- Specialized Polymers: Engineered polymers for specific applications, offering superior resistance to chemicals and extreme temperatures.
Operating Temperature Range:
- Standard materials: -20°C to 80°C (-4°F to 176°F)
- High-temperature materials: up to 200°C (392°F) for specialized applications.
Wiper Blade Thickness:
- Ranges from 5 mm to 20 mm depending on the specific application and material used.
Blade Width:
- Available in standard widths from 50 mm to 300 mm, customizable according to the conveyor belt width.
Length:
- Standard lengths range from 500 mm to 3000 mm, but can be cut to fit the specific dimensions of the conveyor belt.
Mounting Style:
- Bolt-On: Easy installation with bolts directly to the conveyor frame.
- Clamp-On: Quick-release clamps for easy removal and adjustment.
- Spring-Loaded: Automatically adjusts to belt wear for consistent pressure and cleaning performance.
Compatibility:
- Compatible with belt speeds up to 5 m/s (16.4 ft/s).
- Suitable for use with a variety of conveyor belt materials, including fabric-reinforced, steel-cord, and PVC belts.
Pressure Rating:
- Can be adjusted to apply pressure ranging from 5 to 20 PSI, depending on the material type and debris to be removed.
Chemical Resistance:
- Resistant to a wide range of chemicals, including oils, acids, alkalis, and solvents, depending on the material used.
- Abrasion Resistance:
- High resistance to wear and tear, with an average abrasion loss of less than 100 mm³ according to DIN 53516 standard.
- Installation Requirements:
- Requires minimal tools and can typically be installed within 30 minutes, depending on the conveyor system.
- Customization Options:
- Custom shapes, sizes, and materials are available to meet specific operational requirements.
- Color coding available for different material types for easy identification.
These specifications provide a comprehensive overview of the technical parameters and options available for conveyor belt wipers, ensuring that they can be tailored to meet the specific needs of various industrial applications.

Materials of Conveyor Belt Wipers
Polyurethane (PU):
- Properties: Polyurethane is a highly durable material with excellent wear and abrasion resistance. It offers good flexibility, tear strength, and resilience, making it suitable for continuous contact with conveyor belts.
- Applications: Commonly used in industries where durability and long service life are critical, such as mining, quarrying, and heavy-duty manufacturing.
- Advantages: High resistance to oil, grease, and solvents, as well as excellent performance across a broad temperature range.
Natural Rubber:
- Properties: Natural rubber is known for its flexibility, tensile strength, and abrasion resistance. It provides a soft touch against the conveyor belt, minimizing damage.
- Applications: Often used in industries such as agriculture, food processing, and light manufacturing where gentle yet effective cleaning is required.
- Advantages: Good resistance to water and most organic compounds, with excellent elasticity that helps maintain consistent contact with the belt surface.
Neoprene Rubber:
- Properties: Neoprene is a synthetic rubber with moderate flexibility and good resistance to oils, chemicals, and weathering. It is also flame retardant and maintains stability over a wide temperature range.
- Applications: Suitable for environments where exposure to oil, grease, and harsh chemicals is common, such as automotive manufacturing, chemical processing, and heavy industrial applications.
- Advantages: High chemical resistance and durability, with the added benefit of being flame retardant.
Silicone Rubber:
- Properties: Silicone rubber offers excellent heat resistance, remaining flexible at both high and low temperatures. It is also highly resistant to chemicals, weathering, and UV light.
- Applications: Used in applications where temperature extremes are common, such as in food processing, pharmaceuticals, and electronics manufacturing.
- Advantages: Non-toxic, heat-resistant, and suitable for use in cleanroom environments. It also has excellent flexibility and elongation properties.
EPDM Rubber (Ethylene Propylene Diene Monomer):
- Properties: EPDM rubber is highly resistant to ozone, UV radiation, and weathering. It also exhibits good resistance to chemicals and has a high degree of flexibility and elasticity.
- Applications: Ideal for outdoor applications and environments exposed to harsh weather conditions, such as power plants, water treatment facilities, and agricultural operations.
- Advantages: Excellent weatherability, chemical resistance, and flexibility over a wide temperature range.
Thermoplastic Elastomers (TPE):
- Properties: TPE materials combine the characteristics of rubber and plastic, offering flexibility, durability, and chemical resistance. They are also recyclable and can be easily molded into various shapes.
- Applications: Used in environments where flexibility and recyclability are important, such as in packaging, automotive, and consumer goods manufacturing.
- Advantages: Recyclable, customizable, and provides a good balance between flexibility and strength.
Nylon:
- Properties: Nylon is a synthetic polymer known for its high strength, stiffness, and wear resistance. It has low friction, which helps in smooth operation against the conveyor belt.
- Applications: Suitable for high-friction applications, such as in material handling, textile production, and packaging.
- Advantages: High mechanical strength, excellent abrasion resistance, and low friction coefficient, leading to minimal wear on both the wiper and conveyor belt.
UHMWPE (Ultra-High-Molecular-Weight Polyethylene):
- Properties: UHMWPE is an extremely tough plastic with high abrasion resistance, low friction, and excellent impact strength. It also has good resistance to chemicals and moisture.
- Applications: Commonly used in industries like mining, bulk material handling, and food processing where durability and low maintenance are key.
- Advantages: Very low friction, high resistance to wear and impact, and excellent performance in wet environments.
Each of these materials is chosen based on the specific demands of the application, ensuring that the conveyor belt wipers perform optimally under various conditions.
Conveyor Belt Wipers: Efficiency of Conveyor Belt Cleaner Brushes
Conveyor belt cleaner brushes play a crucial role in maintaining the efficiency and cleanliness of conveyor systems. These brushes are designed to remove debris, dust, and other unwanted materials from the conveyor belt’s surface, ensuring smooth operation and preventing damage to the belt and other components. The effectiveness of these brushes directly impacts the performance and longevity of the conveyor system.
Design and Functionality
The design of conveyor belt cleaner brushes is tailored to meet specific cleaning requirements. They are typically made from durable materials like nylon or polypropylene, which provide the necessary stiffness and flexibility to clean various types of conveyor belts. The brushes are installed at strategic points along the conveyor system, usually near the head pulley, tail pulley, or return side of the belt. Their primary function is to dislodge and remove any material that sticks to the belt surface.
Impact on Efficiency
The efficiency of conveyor belt cleaner brushes is measured by their ability to keep the belt clean with minimal maintenance. A clean belt reduces the risk of material carryback, which can cause buildup and blockages in the system. This, in turn, minimizes downtime and increases the overall productivity of the conveyor system. By preventing material buildup, the brushes also help maintain the belt’s traction, reducing the likelihood of slippage and enhancing the belt’s operational efficiency.
Types of Conveyor Belt Cleaner Brushes
There are various types of conveyor belt cleaner brushes, each designed for specific applications:
- Rotary Brushes: These are cylindrical brushes that rotate as the belt moves, providing continuous cleaning action. They are ideal for removing fine particles and dust from the belt surface.
- Static Brushes: These brushes remain stationary and are typically used for heavier cleaning tasks. They are effective at removing larger debris and sticky materials from the belt.
- Combination Brushes: These brushes combine the features of both rotary and static brushes, offering versatile cleaning capabilities for different types of conveyor belts.
Maintenance and Replacement
Regular maintenance of conveyor belt cleaner brushes is essential to ensure their efficiency. Over time, the bristles of the brushes can wear down or become clogged with debris, reducing their effectiveness. Routine inspections and cleaning of the brushes can help maintain their performance. Additionally, timely replacement of worn-out brushes is crucial to prevent damage to the conveyor belt and maintain optimal cleaning efficiency.
Environmental Considerations
Conveyor belt cleaner brushes contribute to a cleaner work environment by reducing dust and debris in the vicinity of the conveyor system. This not only improves air quality but also enhances the safety of workers by minimizing the risk of accidents caused by material buildup. In industries where hygiene is paramount, such as food processing and pharmaceuticals, these brushes play a vital role in maintaining sanitary conditions.
Advantages of Heavy Duty Conveyor Belt Wipers
Heavy duty conveyor belt wipers offer numerous benefits for industrial applications, making them an essential component of many conveyor systems. These wipers are specifically designed to handle the rigors of heavy-duty operations, providing reliable and efficient cleaning performance. Here, we explore the various advantages of using heavy duty conveyor belt wipers in industrial settings.
Durability and Longevity
One of the primary advantages of heavy duty conveyor belt wipers is their durability. Made from robust materials such as urethane or reinforced rubber, these wipers can withstand harsh operating conditions and prolonged use. Their high resistance to abrasion, chemicals, and extreme temperatures ensures a long service life, reducing the frequency of replacements and associated downtime.
Effective Cleaning Performance
Heavy duty conveyor belt wipers are engineered to provide effective cleaning performance, even in the most demanding environments. Their design allows them to remove stubborn materials, such as sticky substances, wet sludge, and abrasive particles, from the conveyor belt surface. This helps maintain a clean belt, preventing material carryback and reducing the risk of blockages and system malfunctions.
Enhanced Safety
By keeping the conveyor belt clean, heavy duty conveyor belt wipers enhance the safety of the conveyor system. A clean belt reduces the risk of material spillage and buildup, which can lead to slips, trips, and falls. Additionally, these wipers help prevent damage to the belt and other components, reducing the likelihood of costly repairs and accidents caused by equipment failure.
Improved Efficiency and Productivity
The use of heavy duty conveyor belt wipers contributes to improved efficiency and productivity in industrial operations. By preventing material buildup and ensuring a clean belt, these wipers help maintain optimal belt traction and alignment. This minimizes slippage and misalignment, allowing the conveyor system to operate smoothly and efficiently. As a result, production rates are increased, and operational costs are reduced.
Versatility
Heavy duty conveyor belt wipers are versatile and can be used in a wide range of industrial applications. They are suitable for various types of conveyor belts, including flat belts, trough belts, and modular belts. Their adaptability makes them ideal for industries such as mining, quarrying, cement production, steel manufacturing, and bulk material handling, where heavy-duty cleaning is required.
Ease of Installation and Maintenance
Installing and maintaining heavy duty conveyor belt wipers is relatively straightforward. Most wipers are designed for easy attachment to the conveyor system, with adjustable brackets and mounting hardware. This simplifies the installation process and allows for quick replacements when necessary. Additionally, regular maintenance of these wipers is minimal, involving routine inspections and occasional adjustments to ensure optimal cleaning performance.
Environmental Benefits
Heavy duty conveyor belt wipers contribute to environmental sustainability by reducing material waste and promoting cleaner work environments. By effectively removing debris from the conveyor belt, these wipers help minimize dust and particulate emissions, improving air quality and reducing the environmental impact of industrial operations. Furthermore, the durability of these wipers reduces the need for frequent replacements, resulting in less material waste and lower environmental footprint.

Choosing the Best Conveyor Belt Wipers
Selecting the best conveyor belt wipers for specific needs and environments requires careful consideration of several factors. The right choice can significantly impact the performance, efficiency, and longevity of the conveyor system. Here are some guidelines to help you choose the best conveyor belt wipers for your application.
Application Requirements
The first step in choosing the best conveyor belt wipers is to understand the specific requirements of your application. Consider the type of materials being transported, the operating conditions, and the desired cleaning performance. For instance, if you are dealing with abrasive materials, you will need wipers made from highly durable materials that can withstand wear and tear. Similarly, if the environment involves exposure to chemicals or extreme temperatures, choose wipers that are resistant to these conditions.
Material Selection
The material of the conveyor belt wipers plays a crucial role in their performance and longevity. Common materials used for wipers include:
- Urethane: Known for its excellent abrasion resistance and flexibility, urethane is suitable for applications involving abrasive materials and high impact loads. It also offers good chemical resistance and can operate in a wide temperature range.
- Reinforced Rubber: This material provides a good balance of durability and flexibility, making it ideal for heavy-duty applications. Reinforced rubber wipers are resistant to chemicals, oils, and extreme temperatures, ensuring reliable performance in harsh conditions.
- Nylon and Polypropylene: These materials are commonly used for lighter cleaning tasks. They offer good stiffness and flexibility, making them effective at removing fine particles and dust from the conveyor belt surface.
Consider the Belt Type and Configuration
Different types of conveyor belts require different types of wipers. Ensure that the wipers you choose are compatible with the belt type and configuration. For example:
- Flat Belts: Wipers for flat belts should have a design that ensures even contact with the belt surface for effective cleaning.
- Trough Belts: These belts require wipers that can conform to the curved surface of the belt, providing thorough cleaning across the entire width.
- Modular Belts: Wipers for modular belts need to be able to navigate the gaps and joints between the belt segments, ensuring no material is left behind.
Evaluate the Installation and Maintenance Requirements
When choosing conveyor belt wipers, consider the ease of installation and maintenance. Look for wipers that come with adjustable brackets and mounting hardware for easy attachment to the conveyor system. Additionally, consider the maintenance requirements of the wipers. Opt for wipers that are designed for minimal maintenance, with features like self-adjusting mechanisms that compensate for wear and ensure consistent cleaning performance.
Check the Manufacturer’s Reputation and Support
Selecting conveyor belt wipers from a reputable manufacturer can make a significant difference in the quality and performance of the product. Research the manufacturer’s reputation, read customer reviews, and check for certifications or industry standards that the products meet. Additionally, consider the level of support provided by the manufacturer, including warranty, technical assistance, and availability of replacement parts.
Cost Considerations
While cost should not be the sole deciding factor, it is important to consider the overall value that the conveyor belt wipers offer. Compare the initial cost of the wipers with their expected lifespan, maintenance requirements, and performance benefits. Investing in high-quality wipers may have a higher upfront cost but can lead to long-term savings through reduced maintenance, fewer replacements, and improved conveyor system efficiency.
Customized Solutions
In some cases, standard conveyor belt wipers may not meet the specific needs of your application. In such instances, consider opting for customized wipers that are tailored to your requirements. Many manufacturers offer customization options, allowing you to specify the material, dimensions, and design features that best suit your conveyor system.
Environmental and Safety Considerations
Finally, take into account the environmental and safety aspects of the conveyor belt wipers. Choose wipers that contribute to a cleaner work environment by effectively controlling dust and debris. Additionally, ensure that the wipers comply with safety regulations and standards to protect workers and prevent accidents.
Choosing the best conveyor belt wipers involves a thorough evaluation of various factors, including application requirements, material selection, belt type, installation and maintenance, manufacturer’s reputation, cost, customization options, and environmental and safety considerations. By carefully considering these factors, you can select conveyor belt wipers that provide optimal cleaning performance, enhance the efficiency and longevity of your conveyor system, and contribute to a safer and cleaner work environment.
Importance of Conveyor Belt Wipers Rubber
Role of Conveyor Belt Wiper Rubber in Enhancing Durability and Performance
Conveyor belt systems are the lifeblood of many industrial processes, from mining and manufacturing to food processing and logistics. These systems ensure the continuous movement of materials, maintaining the efficiency and productivity of operations. However, the longevity and effectiveness of a conveyor belt system hinge on various components, among which conveyor belt wipers play a crucial role. Specifically, the rubber used in conveyor belt wipers significantly impacts their durability and performance.
Composition and Properties of Conveyor Belt Wiper Rubber
Conveyor belt wiper rubber is specially formulated to withstand the harsh conditions in which conveyor systems operate. This rubber needs to be resilient enough to handle continuous friction, varying temperatures, and exposure to different materials and chemicals. High-quality wiper rubber is typically made from a blend of natural and synthetic rubbers, designed to offer optimal abrasion resistance and flexibility.
Key properties of effective conveyor belt wiper rubber include:
- Abrasion Resistance: The primary function of conveyor belt wipers is to scrape off material buildup from the belt surface. High abrasion resistance ensures that the wiper can perform this task efficiently over an extended period without significant wear and tear.
- Flexibility: To effectively clean the belt, the wiper rubber must conform to the belt’s surface contours. Flexibility allows the wiper to maintain continuous contact with the belt, ensuring thorough cleaning.
- Chemical Resistance: Conveyor systems often handle materials that can be chemically reactive. The wiper rubber must resist degradation when exposed to these substances to maintain its effectiveness and longevity.
- Temperature Stability: Conveyor systems can operate in extreme temperatures, from the cold environments of refrigerated warehouses to the high heat of foundries. Wiper rubber must retain its properties across this temperature range to function correctly.
Enhancing Durability with High-Quality Wiper Rubber
The durability of conveyor belt wipers largely depends on the quality of the rubber used. Investing in high-quality wiper rubber can lead to significant long-term savings by reducing the frequency of replacements and minimizing downtime for maintenance. Here are some ways high-quality rubber enhances the durability and performance of conveyor belt wipers:
- Extended Service Life: Superior rubber compounds can endure prolonged exposure to harsh operating conditions without deteriorating, ensuring the wipers remain effective for longer periods.
- Reduced Maintenance Costs: Durable wiper rubber reduces the need for frequent maintenance and replacements, thereby cutting down on associated labor and material costs.
- Improved Belt Protection: High-quality wiper rubber ensures that the conveyor belt surface remains clean and free of debris, reducing wear and tear on the belt itself. This protection extends the life of the entire conveyor system.
- Consistent Performance: Reliable rubber compounds maintain their properties over time, ensuring that the wipers consistently perform their cleaning function effectively, regardless of the operating conditions.
Role in Enhancing Overall Conveyor System Efficiency
The efficiency of a conveyor system is directly linked to the cleanliness of the conveyor belt. Material buildup can lead to various issues, including belt misalignment, increased energy consumption, and even system shutdowns due to blockages. Conveyor belt wipers, equipped with high-quality rubber, play a pivotal role in preventing these problems.
By effectively removing material buildup, conveyor belt wipers help maintain optimal belt traction and alignment, reducing the risk of operational disruptions. This efficiency not only enhances productivity but also contributes to safer working conditions by minimizing the chances of material spillage and associated hazards.
Conveyor Belt Wipers: Comprehensive Conveyor Belt Cleaning System
Description of a Complete Conveyor Belt Cleaning System and Its Components
A conveyor belt cleaning system is essential for maintaining the efficiency, longevity, and safety of conveyor belt operations. Such a system typically integrates multiple components, each designed to address specific aspects of belt cleanliness. The following sections provide a detailed description of the key components of a comprehensive conveyor belt cleaning system and their roles.
Primary Belt Cleaners
Primary belt cleaners, also known as pre-cleaners, are installed on the head pulley just below the material discharge point. Their primary function is to remove the bulk of the carryback material from the belt. These cleaners often feature a sturdy blade made from wear-resistant materials, such as polyurethane or carbide, which scrapes off the larger chunks of material.
Secondary Belt Cleaners
Secondary belt cleaners are installed further along the belt, typically after the primary cleaner, to remove any residual material that the primary cleaner might have missed. These cleaners often have more flexible blades, made from materials like rubber or polyurethane, which can conform to the belt surface for a more thorough cleaning. Secondary cleaners are crucial for ensuring that even the finest particles are removed from the belt.
Tertiary Belt Cleaners
In some applications, a tertiary belt cleaner may be used to provide an additional layer of cleaning. These cleaners are typically installed near the return side of the belt and are designed to remove any remaining material, ensuring the belt is as clean as possible before it makes its way back to the loading point.
Plows and Scrapers
Plows and scrapers are auxiliary cleaning devices installed along the return side of the conveyor belt. Plows, often positioned at points where the belt changes direction, prevent material from becoming trapped between the belt and the pulley, which can cause belt misalignment and damage. Scrapers are used to remove stubborn material from the belt surface and are often made from durable materials like metal or hard plastic.
Conveyor Belt Wipers
Conveyor belt wipers are integral components of a belt cleaning system. These wipers, typically made from high-quality rubber, are designed to provide continuous cleaning of the belt surface. Installed at various points along the conveyor, wipers help to remove finer particles and debris that other cleaning devices might miss. Their role is critical in maintaining a clean belt, preventing buildup, and ensuring the smooth operation of the conveyor system.
Belt Washing Systems
In environments where materials are particularly sticky or difficult to remove, a belt washing system may be employed. These systems use water, combined with brushes and cleaning agents, to wash away stubborn residues. The water used in these systems is often recycled, making them an environmentally friendly option. Belt washing systems are particularly useful in industries such as mining and food processing, where cleanliness is paramount.
Dust Suppression Systems
Dust suppression systems are another important component of a comprehensive conveyor belt cleaning system. These systems use water or chemical sprays to minimize dust generation during material handling. Reducing dust not only improves air quality and working conditions but also helps to prevent material buildup on the conveyor belt.
Integration and Automation
Modern conveyor belt cleaning systems are increasingly integrated and automated to enhance efficiency and reduce manual intervention. Sensors and control systems can monitor the cleanliness of the belt, adjusting the operation of cleaning devices as needed. Automation ensures consistent cleaning performance and allows for predictive maintenance, helping to address potential issues before they lead to downtime.
Benefits of a Comprehensive Cleaning System
A well-designed and properly maintained conveyor belt cleaning system offers numerous benefits, including:
- Improved Efficiency: By keeping the conveyor belt clean, the system operates more efficiently, reducing energy consumption and increasing throughput.
- Extended Equipment Life: Clean belts experience less wear and tear, extending the life of the conveyor system and reducing the need for costly repairs and replacements.
- Enhanced Safety: Clean conveyor belts reduce the risk of material spillage and dust generation, creating a safer working environment for personnel.
- Cost Savings: Reduced maintenance and downtime translate into significant cost savings over the life of the conveyor system.
- Compliance: In industries where cleanliness and environmental regulations are stringent, a comprehensive cleaning system ensures compliance with all relevant standards.
How to Replace Conveyor Belt Wipers Blades
Steps to Replace Conveyor Belt Wiper Blades
Replacing conveyor belt wiper blades is a straightforward process that can be done with minimal tools and downtime. Here’s a step-by-step guide:
1. Safety First
- Turn Off the Conveyor: Ensure the conveyor belt is completely shut down and locked out to prevent accidental startup.
- Wear Protective Gear: Use appropriate personal protective equipment (PPE), such as gloves, safety glasses, and hard hats, to protect yourself during the replacement process.
2. Inspect the Wiper Assembly
- Examine the Wiper: Before removing the old blade, inspect the entire wiper assembly for any damage or wear. Check the mounting brackets, tensioners, and support arms for signs of corrosion, bending, or other issues.
- Identify the Blade Type: Make sure you have the correct replacement blade that matches the existing wiper blade’s type, size, and material.
3. Remove the Old Wiper Blade
- Loosen the Tension: If the wiper blade assembly has tensioners, use the appropriate tool (usually a wrench or ratchet) to relieve the tension. This will make it easier to remove the old blade.
- Unbolt or Unclamp the Blade: Depending on the mounting style (bolt-on, clamp-on, or spring-loaded), either unbolt or release the clamps holding the blade in place. For spring-loaded systems, carefully release the spring tension to avoid injury.
- Remove the Blade: Slide or lift the old blade out of the assembly. Take note of the orientation and positioning of the old blade to ensure the new blade is installed correctly.
4. Clean the Wiper Assembly
- Remove Debris: Clean the wiper assembly, including the mounting brackets, tensioners, and support arms, to remove any accumulated debris, dust, or residue. This ensures a smooth installation of the new blade.
- Inspect for Wear: While cleaning, inspect the assembly components for wear or damage. Replace any worn or damaged parts before installing the new blade.
5. Install the New Wiper Blade
- Position the New Blade: Align the new blade with the mounting points on the assembly. Make sure the blade is positioned correctly with the wiping edge facing the conveyor belt.
- Secure the Blade: Attach the new blade using the bolts or clamps, depending on the mounting style. Ensure it is securely fastened and properly aligned with the belt surface.
- Tighten Tensioners: For tensioned systems, carefully reapply the tension to the blade using the appropriate tool. Ensure that the tension is evenly distributed along the blade to maintain consistent pressure on the belt.
6. Test the Installation
- Manually Rotate the Belt: Before turning on the conveyor, manually rotate the belt to ensure the blade makes even contact with the belt surface and there are no obstructions.
- Check Alignment: Ensure the blade is properly aligned and not causing any misalignment of the belt. Adjust as necessary.
- Test Run: Once everything is in place, turn on the conveyor at a low speed to check the performance of the new blade. Watch for smooth operation and effective cleaning.
7. Final Adjustments
- Fine-Tune Tension: After the test run, if necessary, make final adjustments to the blade tension or alignment to optimize performance.
- Tighten All Fasteners: Double-check that all bolts, clamps, and tensioners are securely tightened
8. Routine Maintenance
- Monitor Performance: Regularly inspect the new wiper blade during routine maintenance checks to ensure it continues to perform effectively.
- Adjust as Needed: Make periodic adjustments to the blade tension or alignment to compensate for wear and maintain optimal performance.
By following these steps, you can ensure a smooth and efficient replacement of conveyor belt wiper blades, helping to maintain the performance and longevity of your conveyor system.
Maintenance Tips for Conveyor Belt Wipers
Practical Advice on How to Maintain and Extend the Life of Conveyor Belt Wipers
Maintaining conveyor belt wipers is crucial for ensuring the efficiency and longevity of conveyor systems. Proper maintenance not only extends the life of the wipers themselves but also enhances the overall performance of the conveyor system. Here are some practical tips on how to maintain and extend the life of conveyor belt wipers.
Regular Inspection
Regular inspection of conveyor belt wipers is essential to identify wear and tear, misalignment, and other issues that can affect performance. Inspections should be conducted as part of routine maintenance schedules and whenever there is a noticeable change in the conveyor’s operation.
- Visual Inspection: Look for signs of wear on the wiper blades, such as cracks, chips, or excessive abrasion. Also, check for buildup of materials around the wiper, which can indicate that the wiper is not effectively cleaning the belt.
- Alignment Check: Ensure that the wiper blades are properly aligned with the belt. Misalignment can cause uneven wear on the blades and reduce cleaning efficiency. Adjust the wipers as necessary to maintain optimal contact with the belt surface.
- Tension Adjustment: Check the tension of the wiper blades to ensure they are applying the correct pressure to the belt. Over-tensioned blades can cause excessive wear, while under-tensioned blades may not clean effectively. Use manufacturer guidelines to set the correct tension.
Cleaning and Lubrication
Regular cleaning and lubrication of conveyor belt wipers are essential to maintain their performance. Removing accumulated debris and ensuring smooth operation can significantly extend the life of the wipers.
- Debris Removal: Clean the wiper blades and surrounding components regularly to remove any material buildup. This prevents debris from causing additional wear on the blades and ensures effective cleaning.
- Lubrication: Lubricate moving parts of the wiper assembly, such as hinges and pivot points, to ensure smooth operation. Use appropriate lubricants recommended by the manufacturer to avoid damaging the wiper materials.
Blade Replacement
Timely replacement of worn wiper blades is crucial to maintaining cleaning efficiency and preventing damage to the conveyor belt. Here are some guidelines for blade replacement:
- Monitor Wear: Keep track of the wear rate of the wiper blades and replace them when they reach the end of their service life. Manufacturers typically provide guidelines on the expected lifespan of their wiper blades based on operating conditions.
- Use Quality Replacements: Always use high-quality replacement blades that match the specifications of the original equipment. Using inferior or mismatched blades can reduce cleaning efficiency and increase wear on the belt.
- Proper Installation: Ensure that replacement blades are installed correctly and aligned properly with the belt. Follow the manufacturer’s installation instructions to avoid common installation errors that can affect performance.
Preventive Maintenance
Implementing a preventive maintenance program for conveyor belt wipers can help identify and address potential issues before they lead to significant problems. Preventive maintenance includes:
- Scheduled Inspections: Conduct regular inspections of the entire conveyor system, including the wipers, according to a predetermined schedule. This helps detect early signs of wear and allows for timely intervention.
- Condition Monitoring: Use sensors and monitoring equipment to track the condition of the wipers and the belt. Automated monitoring systems can provide real-time data on wiper performance and alert maintenance personnel to potential issues.
- Record Keeping: Maintain detailed records of maintenance activities, including inspections, repairs, and replacements. This information can help identify patterns of wear and inform future maintenance decisions.
Training and Best Practices
Ensuring that maintenance personnel are well-trained in the proper care and maintenance of conveyor belt wipers is essential for maximizing their lifespan. Here are some best practices for training and maintenance:
- Manufacturer Training: Take advantage of training programs offered by wiper manufacturers. These programs often provide valuable insights into the proper maintenance and operation of their products.
- Maintenance Manuals: Use manufacturer-provided maintenance manuals as a reference for best practices and troubleshooting tips. These manuals contain detailed information on the care and maintenance of specific wiper models.
- Regular Updates: Stay informed about new maintenance techniques and products by participating in industry events, subscribing to trade publications, and engaging with manufacturers. Continuous learning helps ensure that maintenance practices are up-to-date and effective.
Maintaining conveyor belt wipers is a critical aspect of ensuring the efficiency, safety, and longevity of conveyor systems. By following these practical maintenance tips—regular inspection, cleaning and lubrication, timely blade replacement, preventive maintenance, and proper training—operations can significantly extend the life of conveyor belt wipers and enhance the overall performance of the conveyor system. Investing in high-quality wiper rubber and adhering to best maintenance practices ultimately leads to reduced operational costs, improved productivity, and a safer working environment.
FAQs about Conveyor Belt Wipers
Conveyor belt wheels are commonly referred to as pulleys or rollers. These components play a crucial role in the operation of the conveyor belt system. Pulleys, specifically, can be classified into two main types: drive pulleys and idler pulleys. The drive pulley is connected to the motor and provides the power needed to move the belt, while idler pulleys support the belt and help maintain proper tension and alignment. Rollers, on the other hand, are cylindrical components placed along the conveyor system to support the belt and reduce friction, ensuring smooth movement of the materials being transported.
A conveyor belt system consists of several essential parts, each serving a specific function. The main components include:
Conveyor Belt: The continuous loop of material that transports items.
Drive Pulley: Powers the movement of the belt, connected to the motor.
Idler Pulleys: Support the belt and help maintain tension and alignment.
Motor: Provides the necessary power to drive the conveyor belt.
Frame: Provides structural support and stability for the entire system.
Belt Tensioning Device: Adjusts the tension of the conveyor belt to prevent slippage.
Rollers: Support the belt and reduce friction, allowing smooth movement.
Control System: Manages the operation of the conveyor belt, including speed and direction.
Belt Cleaner: Removes debris and residues from the belt surface.
Safety Devices: Ensure safe operation by stopping the belt in emergencies.
Each part is vital for the efficient and reliable operation of the conveyor belt system.
A scraper in a belt conveyor is a device used to clean the surface of the conveyor belt. It is typically installed near the discharge end of the conveyor, where the material is unloaded. Scrapers remove residual materials, debris, and build-up that can adhere to the belt, ensuring a clean surface for the next load. By preventing material accumulation, scrapers help maintain the efficiency and longevity of the conveyor system, reducing the risk of belt damage and minimizing downtime for cleaning. They are crucial for applications where cleanliness is paramount, such as in the food, pharmaceutical, and mining industries.
Cleaning conveyor belt rubber is essential for maintaining the efficiency and longevity of the conveyor system. Here are the steps to effectively clean a conveyor belt rubber:
Regular Cleaning Schedule: Establish a routine based on the belt’s usage and environment.
Remove Loose Debris: Use brushes, air blowers, or vacuum cleaners to remove loose dirt and debris from the belt surface.
Apply Cleaning Solution: Use a mild detergent mixed with water to clean the belt. Avoid harsh chemicals that could damage the rubber.
Scrub the Belt: Use a soft brush or cloth to scrub the belt, paying attention to areas with stubborn residues.
Rinse Thoroughly: Rinse the belt with clean water to remove any soap residue.
Dry Completely: Ensure the belt is completely dry before restarting the conveyor to prevent slippage and corrosion.
Last Updated on August 26, 2024 by Jordan Smith
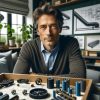
Jordan Smith, a seasoned professional with over 20 years of experience in the conveyor system industry. Jordan’s expertise lies in providing comprehensive solutions for conveyor rollers, belts, and accessories, catering to a wide range of industrial needs. From initial design and configuration to installation and meticulous troubleshooting, Jordan is adept at handling all aspects of conveyor system management. Whether you’re looking to upgrade your production line with efficient conveyor belts, require custom conveyor rollers for specific operations, or need expert advice on selecting the right conveyor accessories for your facility, Jordan is your reliable consultant. For any inquiries or assistance with conveyor system optimization, Jordan is available to share his wealth of knowledge and experience. Feel free to reach out at any time for professional guidance on all matters related to conveyor rollers, belts, and accessories.