Conveyor Drive Pulley Lagging: Types, Options and Benefits
Conveyor drive pulley lagging is a crucial component in the efficient operation of conveyor systems. It involves applying a protective layer to the drive pulleys, which enhances friction and grip, preventing slippage between the belt and the pulley. This protective layer can be made from various materials such as rubber, ceramic, or polyurethane, each offering specific benefits. The importance of conveyor drive pulley lagging in conveyor systems cannot be overstated. It significantly extends the lifespan of both the pulleys and the belts, reduces maintenance costs, and ensures smooth and reliable operation even under harsh conditions, ultimately improving overall productivity and safety.
What is Conveyor Drive Pulley Lagging
Definition and Purpose
Conveyor drive pulley lagging refers to the application of a protective coating or layer to the surface of conveyor drive pulleys. This layer, typically made from materials such as rubber, ceramic, or polyurethane, is designed to increase the friction between the pulley and the conveyor belt. By enhancing friction, pulley lagging ensures that the belt moves smoothly and efficiently without slipping, thereby optimizing the performance of the conveyor system. The primary purpose of conveyor drive pulley lagging is to improve the grip between the pulley and the belt, protect the pulley from wear and tear, and enhance the overall reliability and efficiency of the conveyor system.
Benefits of Using Pulley Lagging
Increased Friction and Grip
One of the most significant benefits of conveyor drive pulley lagging is the increased friction and grip it provides. Without adequate friction, the conveyor belt may slip on the drive pulley, leading to inefficiencies and potential system failures. Lagging materials such as rubber or ceramic increase the surface roughness of the pulley, enhancing the grip and ensuring that the belt remains securely in place. This increased grip is particularly crucial in high-tension applications where the risk of slippage is greater. By providing a reliable friction surface, pulley lagging helps maintain consistent belt movement and reduces the likelihood of operational disruptions.
Extended Pulley and Belt Life
Conveyor drive pulley lagging significantly extends the life of both the pulleys and the conveyor belts. The lagging material acts as a protective barrier that absorbs the wear and tear caused by continuous contact with the belt. This protection is especially important in harsh environments where the pulley is exposed to abrasive materials and extreme conditions. By reducing direct metal-to-belt contact, lagging minimizes the abrasive forces that can cause premature wear and damage to both the pulley and the belt. As a result, the longevity of these components is increased, leading to lower maintenance costs and reduced downtime for replacements.
Improved Water Shedding and Reduced Slippage
In many conveyor systems, especially those operating in wet conditions, water accumulation on the pulley surface can cause slippage and reduce system efficiency. Conveyor pulley lagging enhances friction between the pulley and conveyor belt while protecting the pulley shell, thereby increasing traction and reducing wear on the system components. Conveyor drive pulley lagging, particularly grooved designs like diamond or herringbone patterns, enhances water shedding capabilities. These grooves channel water away from the contact surface, preventing it from forming a lubricating layer that can lead to belt slippage. By effectively managing water dispersion, lagging ensures that the belt maintains optimal traction with the pulley, even in challenging weather conditions. This capability is crucial for outdoor operations and industries where water exposure is frequent.
Enhanced Performance in Harsh Conditions
Conveyor drive pulley lagging is designed to enhance the performance of conveyor systems operating in harsh and demanding conditions. In industries such as mining, aggregate processing, and heavy manufacturing, conveyor systems are often subjected to extreme temperatures, heavy loads, and abrasive materials. Lagging materials, such as ceramic, are highly durable and resistant to these harsh conditions. They provide a robust and resilient surface that can withstand significant wear and impact, ensuring the pulley and belt maintain their integrity and performance. This durability translates into improved reliability and efficiency of the conveyor system, even under the most challenging operational environments.
Types of Conveyor Drive Pulley Lagging
Conveyor drive pulley lagging is essential for enhancing the efficiency, reliability, and longevity of conveyor systems. Various types of pulley lagging materials and designs cater to different operational needs and conditions. Here, we explore the common types of conveyor pulley lagging and their specific features.
Rubber Conveyor Drive Pulley Lagging
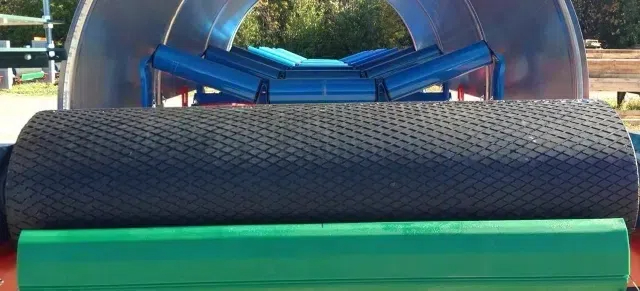
Description of Rubber Lagging Materials and Their Properties
Rubber conveyor drive pulley lagging is a widely used solution for enhancing the performance and longevity of conveyor systems. The rubber lagging material is applied to the surface of conveyor drive pulleys to increase friction, improve traction, and protect the pulley from wear and damage. Rubber lagging is known for its versatility and effectiveness, making it a popular choice in various industries.
Durability and Wear Resistance
One of the key advantages of rubber lagging for conveyor pulley is its durability and wear resistance. Rubber lagging materials are designed to withstand the constant friction and pressure exerted by the conveyor belt and the materials being transported. High-quality rubber lagging is resistant to cuts, abrasions, and impacts, ensuring a long service life even in harsh operating conditions. This durability reduces the frequency of maintenance and replacements, leading to lower operational costs and increased system reliability.
Cost-Effectiveness and Availability
Rubber lagging conveyor pulleys are also highly cost-effective and readily available. Compared to other lagging materials like ceramic or polyurethane, rubber is more affordable, making it an attractive option for many businesses. Additionally, rubber lagging is widely available in various forms, thicknesses, and patterns, allowing for easy customization to meet specific application needs. This availability ensures that companies can quickly source and install the appropriate lagging for their conveyor systems, minimizing downtime and optimizing productivity.
Different Types of Rubber Lagging
Rubber lagging is one of the most popular choices for conveyor drive pulley lagging due to its versatility, cost-effectiveness, and durability. It comes in two primary forms: plain rubber lagging and grooved rubber lagging.
Plain Rubber for Non-Drive Pulleys
Plain rubber lagging is typically used on non-drive pulleys, where the primary function is to protect the pulley surface and prevent rapid belt wear rather than providing additional grip. Non-drive pulleys, also known as idler pulleys, do not contribute to the movement of the conveyor belt but serve to guide and support it.
- Characteristics: Plain rubber lagging offers a smooth, even surface that reduces wear and tear on the belt. It is usually made from durable rubber compounds that can withstand the environmental conditions of the conveyor system.
- Applications: This type of lagging is ideal for applications where the pulley does not require enhanced friction, such as in return pulleys, snub pulleys, and bend pulleys. By providing a protective layer, plain rubber lagging extends the life of the pulley and reduces maintenance costs.
Grooved Rubber for Drive Pulleys to Improve Traction and Water Dispersion
Grooved rubber lagging is designed for drive pulleys, which are responsible for propelling the conveyor belt. The grooves in the rubber surface increase the friction between the pulley and the belt, improving traction and preventing slippage. There are several patterns of grooved rubber lagging, each with unique benefits.
- Diamond Grooved Rubber Lagging: The diamond pattern is one of the most common and effective designs for improving traction. The intersecting grooves create a crisscross pattern that enhances the grip on the belt, reducing the risk of slippage. Additionally, the diamond grooves help disperse water and debris, maintaining optimal performance in wet conditions.
- Herringbone Grooved Rubber Lagging: The herringbone pattern features angled grooves that point in the direction of belt travel. This design provides excellent traction and a self-cleaning effect, channeling water and dirt away from the pulley surface. Herringbone grooved lagging is particularly useful in environments with significant material buildup.
- Chevron Grooved Rubber Lagging: Chevron grooves combine the benefits of both diamond and herringbone patterns. The V-shaped grooves offer superior traction and water dispersion, making them suitable for heavy-duty applications where maximum grip is essential.
Ceramic Conveyor Drive Pulley Lagging
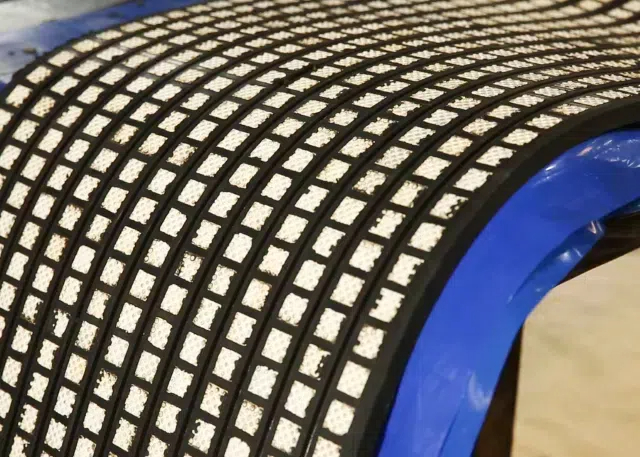
Overview of Ceramic Lagging
Ceramic conveyor drive pulley lagging is renowned for its exceptional durability and high friction properties, making it an ideal choice for demanding applications where enhanced performance and longevity are required. This type of lagging involves embedding ceramic tiles into a rubber matrix, which is then applied to the surface of conveyor drive pulleys. The combination of ceramic and rubber offers superior wear resistance and friction, ensuring that conveyor systems operate efficiently even under harsh conditions.
Durability and Long Service Life
One of the most significant advantages of ceramic conveyor drive pulley lagging is its outstanding durability and long service life. Ceramic tiles are highly resistant to wear and abrasion, which makes them suitable for environments where the pulley is exposed to abrasive materials and high-impact forces. The robust nature of ceramic lagging ensures that it can withstand the rigors of continuous operation without deteriorating, reducing the frequency of maintenance and replacements.
The longevity of ceramic lagging translates into substantial cost savings over time. Although ceramic lagging may have a higher initial cost compared to other materials, its extended service life and reduced maintenance requirements make it a cost-effective solution in the long run. By minimizing downtime and maintenance expenses, ceramic lagging helps maintain consistent productivity and efficiency in conveyor operations.
High Friction and Grip
Ceramic conveyor drive pulley lagging is specifically designed to provide high friction and grip, preventing belt slippage and ensuring smooth and reliable operation. The ceramic tiles embedded in the lagging surface increase the coefficient of friction between the pulley and the conveyor belt, which is crucial for maintaining optimal belt tension and preventing slippage.
This enhanced grip is particularly beneficial in high-tension applications and environments where the conveyor belt is subjected to heavy loads and extreme conditions. By improving traction, ceramic lagging ensures that the conveyor belt moves consistently and efficiently, reducing the risk of operational disruptions and enhancing overall system performance.
Comparison Between Smooth and Dimple Ceramic Lagging
Smooth Ceramic Lagging
Smooth ceramic lagging provides a balance between grip and wear resistance. It consists of smooth ceramic tiles embedded in a rubber matrix, offering a durable surface that resists wear and tear. This type of lagging is ideal for applications where high friction is needed without the risk of damaging the belt.
Dimple Ceramic Lagging
Dimple ceramic lagging features raised dimples on the ceramic tiles, which press into the belt to provide increased grip. This design offers maximum friction, making it suitable for high-tension applications where belt slippage is a significant concern. However, the aggressive grip can cause more wear on the belt, so it is essential to consider the specific operational requirements.
Ceramic conveyor drive pulley lagging is available in two primary configurations: smooth ceramic lagging and dimple ceramic lagging. Each type offers distinct advantages and is suited to specific operational requirements.
Semi-Ceramic Lagging in Conveyor Drive Pulley Lagging
Semi-ceramic lagging is an advanced type of pulley lagging that combines the benefits of traditional rubber lagging with the enhanced performance characteristics of ceramic tiles. This hybrid lagging is designed to provide superior traction and durability in demanding conveyor system applications.
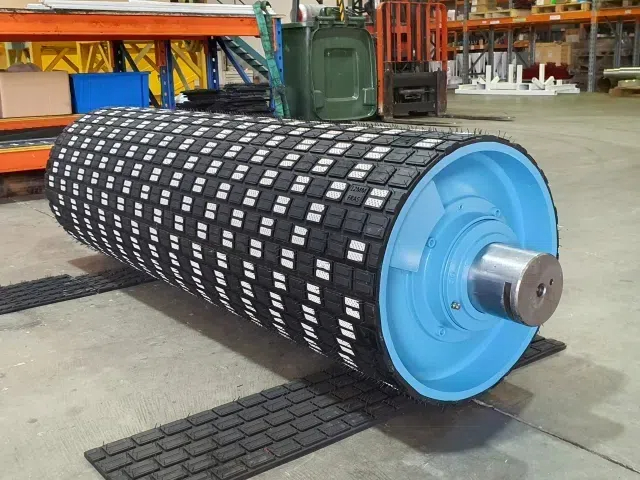
What is Semi-Ceramic Lagging?
Semi-ceramic lagging consists of a rubber matrix embedded with ceramic tiles. The ceramic tiles are strategically placed within the rubber to provide enhanced grip and wear resistance. This combination leverages the elasticity and shock-absorbing properties of rubber with the hardness and abrasion resistance of ceramic, making it ideal for high-stress environments.
Advantages of Semi-Ceramic Lagging
- Enhanced Traction: The ceramic tiles significantly increase the friction between the pulley and the conveyor belt. This improved grip reduces belt slippage, ensuring more efficient power transmission and smoother operation.
- Increased Durability: The ceramic elements provide exceptional resistance to wear and abrasion, extending the lifespan of the lagging. This durability is particularly beneficial in applications with high material loads and harsh operating conditions.
- Improved Performance: Semi-ceramic lagging offers better performance under heavy loads and in wet or muddy conditions. The combination of rubber and ceramic ensures consistent traction, even when the belt surface is contaminated.
- Reduced Maintenance: Due to its robust construction, semi-ceramic lagging requires less frequent maintenance and replacement compared to traditional rubber lagging. This reduction in downtime leads to improved operational efficiency and cost savings.
- Shock Absorption: The rubber component of the lagging provides excellent shock absorption, protecting the pulley and belt from impacts and reducing vibration. This feature helps in maintaining the integrity of the conveyor system and minimizing wear on other components.
- Versatility: Semi-ceramic lagging is suitable for a wide range of applications, including mining, power generation, and heavy industrial environments. It can be customized to fit various pulley sizes and configurations, offering flexibility in its application.
Semi-ceramic lagging in conveyor drive pulleys provides a superior solution for improving traction, durability, and overall performance in challenging conditions. Its unique composition offers the best of both worlds, combining the resilience of rubber with the toughness of ceramic.
Polyurethane/Plastic Lagging
Polyurethane or plastic lagging is gaining popularity for specific applications due to its excellent wear resistance and ability to handle extreme environmental conditions. These materials are particularly suitable for operations involving corrosive substances or where high impact resistance is required. Polyurethane lagging offers a smooth surface that minimizes belt wear and can be used in both drive and non-drive pulleys. However, it can be more challenging to install and remove compared to rubber lagging. Polyurethane and plastic lagging are alternative materials used in conveyor drive pulley lagging, offering distinct advantages, especially in harsh and demanding environments.
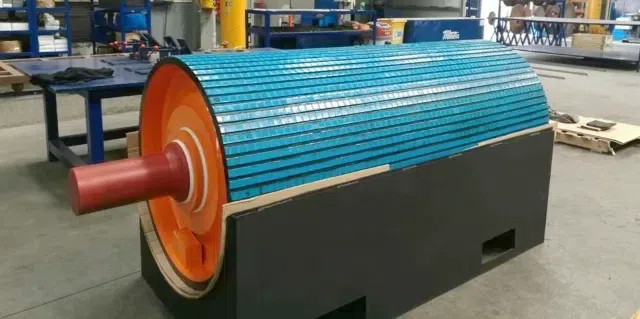
Benefits and Challenges
Benefits:
- High Durability: Polyurethane and plastic lagging are known for their exceptional wear resistance. They can withstand heavy abrasion and impact, making them ideal for applications where the pulley is exposed to harsh conditions and abrasive materials.
- Chemical Resistance: These materials are resistant to a wide range of chemicals, including oils, solvents, and acids. This resistance makes polyurethane and plastic lagging suitable for environments where chemical exposure is a concern.
- Reduced Belt Wear: Polyurethane and plastic lagging provide a smooth and consistent surface that minimizes wear on the conveyor belt. This feature helps extend the life of the belt, reducing maintenance costs and downtime.
- Temperature Resistance: Polyurethane and plastic lagging can perform well in a broad range of temperatures, maintaining their properties in both high and low-temperature environments. This flexibility makes them suitable for various industrial settings.
Challenges:
- Installation Complexity: Installing polyurethane and plastic lagging can be more complex compared to rubber lagging. These materials often require specialized adhesives and precise application techniques to ensure a secure bond and proper alignment.
- Higher Initial Cost: The initial cost of polyurethane and plastic lagging is generally higher than that of rubber lagging. While the long-term benefits may offset this cost, the initial investment can be a consideration for some businesses.
- Limited Flexibility: Unlike rubber, polyurethane and plastic lagging are less flexible, which can make them challenging to install on pulleys with complex shapes or irregular surfaces.
Replaceable Rim Lagging
Replaceable rim lagging is a modular approach to conveyor drive pulley lagging, offering easy maintenance and replacement without the need for extensive downtime or specialized tools.
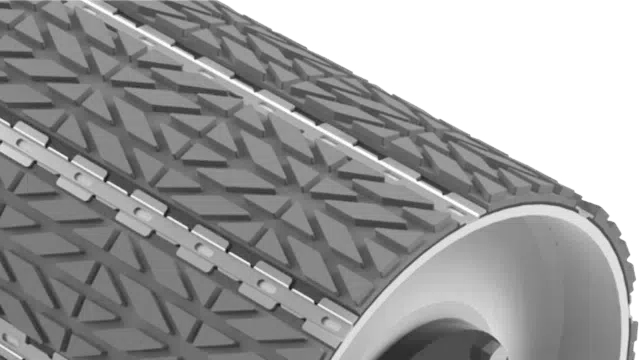
Easy Replacement and Maintenance
Benefits:
- Quick Replacement: One of the most significant advantages of replaceable rim lagging is the ease and speed of replacement. The lagging is designed in segments or sections that can be quickly removed and replaced without dismantling the entire pulley. This feature is particularly beneficial in reducing downtime and maintaining continuous operations.
- Cost-Effective Maintenance: Because only the worn or damaged segments need to be replaced, rather than the entire lagging, maintenance costs are significantly reduced. This segmented approach allows for targeted maintenance, extending the overall life of the lagging system.
- Versatility: Replaceable rim lagging can be customized to fit various pulley sizes and configurations. This adaptability makes it suitable for a wide range of applications, from light-duty to heavy-duty industrial operations.
- Enhanced Performance: Replaceable rim lagging often incorporates advanced materials and designs that provide superior grip, durability, and resistance to wear and tear. This performance enhancement ensures efficient and reliable conveyor system operation.
Challenges:
- Initial Setup: The initial installation of replaceable rim lagging can be more time-consuming and require precise alignment and fitting to ensure optimal performance. However, once installed, the benefits of quick and easy replacement outweigh the initial setup challenges.
- Segment Compatibility: Ensuring compatibility and proper fitting of replacement segments is crucial for maintaining the integrity and performance of the lagging system. Using high-quality, compatible segments from reputable manufacturers is essential to avoid potential issues.
Weld-On Head Pulley Lagging
Weld-on head pulley lagging involves attaching lagging materials directly to the pulley shell through welding. This method provides a permanent solution that is highly durable and suitable for extreme conditions. Weld-on lagging is typically used in heavy-duty applications where the pulley is subject to high stresses and wear. The primary advantage of weld-on lagging is its longevity and robustness, ensuring minimal maintenance and extended service life.
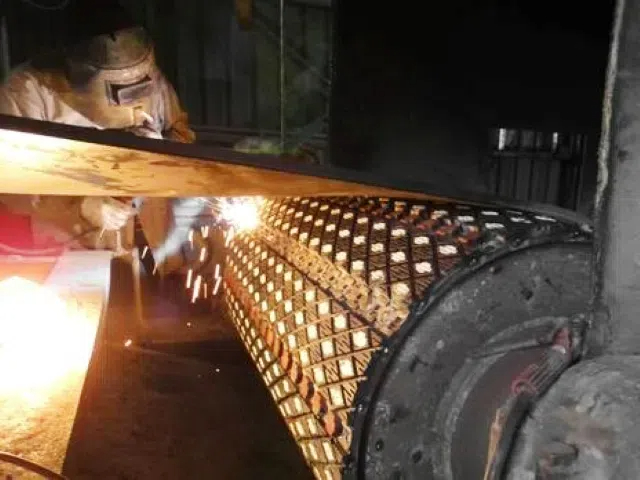
Bonded Lagging in Conveyor Drive Pulley Lagging
Bonded lagging is a type of conveyor pulley lagging where the lagging material is permanently bonded to the pulley surface. This method ensures a strong, durable connection between the pulley and the lagging material, providing enhanced performance and longevity for conveyor systems.
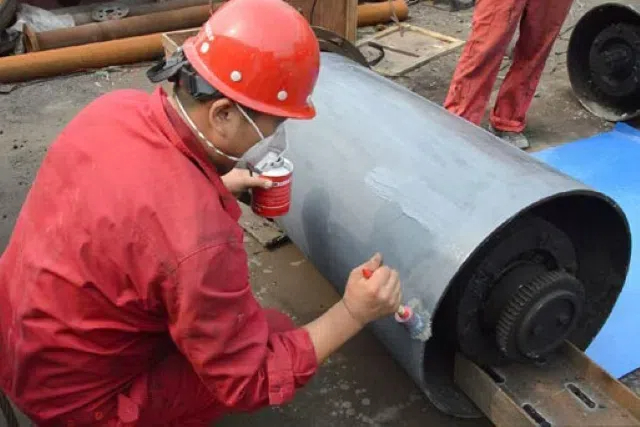
What is Bonded Lagging?
Bonded lagging involves the application of a lagging material, such as rubber or ceramic, which is chemically or mechanically bonded to the surface of the pulley. This process creates a seamless and robust attachment, ensuring that the lagging remains securely in place during operation. The bonding can be achieved through various methods, including vulcanization (for rubber) or the use of high-strength adhesives and mechanical fastening systems.
Advantages of Bonded Lagging
- Enhanced Adhesion: The bonding process creates a strong, uniform adhesion between the lagging material and the pulley surface. This reduces the risk of delamination or separation, ensuring consistent performance over the lifespan of the pulley.
- Improved Durability: Bonded lagging is designed to withstand harsh operating conditions, including high loads, abrasive materials, and extreme temperatures. This durability extends the service life of the pulley and reduces maintenance requirements.
- Superior Traction: The bonded lagging material, whether rubber or ceramic, enhances the friction between the pulley and the conveyor belt. This increased traction minimizes belt slippage and improves the efficiency of power transmission.
- Reduced Wear and Tear: By providing a protective layer between the pulley and the conveyor belt, bonded lagging reduces wear and tear on both components. This not only extends the life of the pulley but also helps maintain the integrity of the conveyor belt.
- Customizable Solutions: Bonded lagging can be tailored to specific applications and operational requirements. Different materials, thicknesses, and surface patterns (e.g., smooth, grooved, or diamond-shaped) can be used to optimize performance for various industries and conditions.
- Enhanced Shock Absorption: Rubber bonded lagging, in particular, offers excellent shock absorption properties. This helps to protect the pulley and belt from impacts and reduces vibrations, leading to smoother operation and less strain on the conveyor system.
- Ease of Maintenance: The secure attachment of bonded lagging means that it is less likely to require frequent maintenance or replacement. This leads to reduced downtime and lower maintenance costs over time.
- Versatility: Bonded lagging is suitable for a wide range of applications, including mining, material handling, and industrial processing. Its ability to be customized and its robust performance make it an ideal choice for various conveyor systems.
Bonded lagging in conveyor drive pulleys provides a reliable and durable solution for improving traction, reducing wear, and enhancing the overall efficiency of conveyor systems. Its strong adhesion and customizable features make it a versatile and effective option for demanding applications.
Vulcanized Lagging in Conveyor Drive Pulley Lagging
Vulcanized lagging is a type of pulley lagging in which the lagging material, typically rubber, is chemically bonded to the pulley surface through a process known as vulcanization. This method ensures a strong, durable connection that enhances the performance and longevity of conveyor systems.
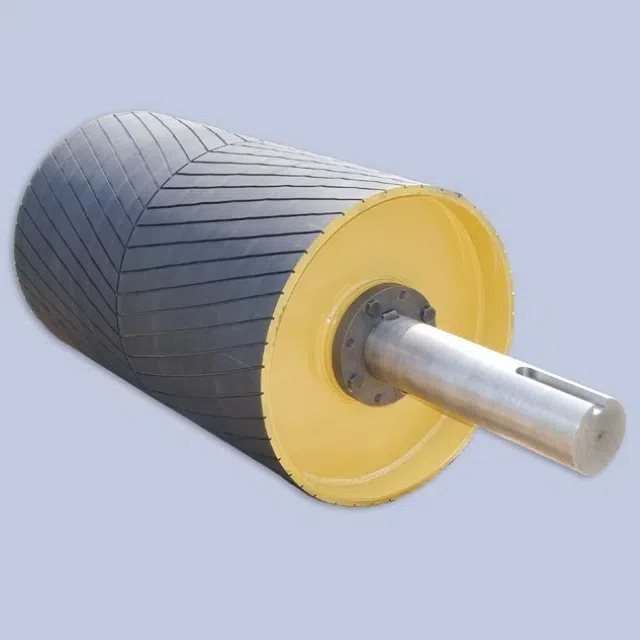
What is Vulcanized Lagging?
Vulcanized lagging involves the application of a raw rubber layer to the surface of the pulley, followed by curing it under heat and pressure in a vulcanizing press. This process transforms the rubber into a tough, elastic material that is tightly bonded to the pulley. Vulcanization creates a seamless and integrated layer that adheres exceptionally well to the pulley surface, providing superior traction and protection.
Advantages of Vulcanized Lagging
- Strong Adhesion: The vulcanization process creates a chemical bond between the rubber and the pulley surface, resulting in a highly durable and cohesive layer. This strong adhesion prevents the lagging from peeling or delaminating under operational stresses.
- Enhanced Traction: Vulcanized rubber lagging significantly increases the friction between the pulley and the conveyor belt. This enhanced grip reduces belt slippage, leading to more efficient power transmission and smoother operation of the conveyor system.
- Improved Durability: The vulcanized rubber layer is resistant to wear, abrasion, and impact. This durability extends the lifespan of both the pulley and the conveyor belt, reducing the frequency of maintenance and replacement.
- Protection Against Damage: Vulcanized lagging protects the pulley from various forms of damage, including abrasion, corrosion, and material build-up. This protection helps maintain the structural integrity of the pulley over time.
- Shock Absorption: The rubber material used in vulcanized lagging provides excellent shock absorption properties. This helps to cushion the impacts and vibrations that occur during conveyor operation, protecting both the pulley and the belt from excessive wear.
- Consistent Performance: Because vulcanized lagging is a seamless and integrated layer, it provides consistent performance across the entire surface of the pulley. This uniformity ensures reliable traction and reduces the risk of localized wear or damage.
- Customizability: Vulcanized lagging can be tailored to meet specific operational requirements. Various rubber compounds and surface patterns (e.g., plain, grooved, or diamond-shaped) can be used to optimize performance for different applications and conditions.
- Resistance to Environmental Conditions: The vulcanized rubber layer is resistant to harsh environmental conditions, such as extreme temperatures, moisture, and chemicals. This makes it suitable for use in a wide range of industrial environments.
- Reduced Maintenance Costs: The durability and strong adhesion of vulcanized lagging lead to lower maintenance requirements and extended intervals between replacements. This results in reduced downtime and overall maintenance costs.
Vulcanized lagging in conveyor drive pulleys offers a robust and reliable solution for enhancing traction, protecting the pulley, and improving the efficiency and longevity of conveyor systems. Its strong adhesion, durability, and customizability make it an ideal choice for demanding applications.
Which Pulley Lagging Should I Use?
Pulley lagging depends largely on the application and conveyor design. It is important to understand the operating conditions, product wear, pulley type, belt operating speed, and tension when choosing which type of pulley lagging to use.
Conveyor Drive Pulley Lagging Procedure
Step-by-Step Guide to the Pulley Lagging Installation Process
Proper installation of conveyor drive pulley lagging is crucial to ensure optimal performance and longevity of the conveyor system. Here is a detailed, step-by-step guide to the pulley lagging installation process.
Preparation
Removing Old Lagging, Paint, and Primer
The first step in the conveyor drive pulley lagging installation process is to prepare the pulley surface. Begin by removing any old lagging, paint, and primer. Use appropriate tools such as scrapers, wire brushes, or chemical strippers to ensure that all residues are completely removed. This step is essential to provide a clean and smooth surface for the new lagging material to adhere to.
Sandblasting the Pulley Surface
Once the old materials are removed, the pulley surface must be thoroughly cleaned and roughened to enhance adhesion. Sandblasting is the most effective method for this. Sandblasting not only removes any remaining contaminants but also creates a rough texture on the pulley surface, which helps the adhesive bond more effectively. Ensure that the entire surface, including the edges, is evenly blasted.
Applying Metal Primer
After sandblasting, the next step is to apply a metal primer to the pulley surface. The primer acts as a bonding agent between the metal and the adhesive. Use a primer recommended by the adhesive manufacturer and apply it evenly across the entire pulley surface and edges. Allow the primer to dry completely according to the manufacturer’s instructions before proceeding to the next step. Proper curing of the primer is essential to ensure maximum adhesion.
Installation
Applying Adhesive
With the pulley surface prepared and primed, it’s time to apply the adhesive. Select an adhesive that is compatible with both the pulley material and the lagging material. Apply the adhesive uniformly to the entire pulley surface, ensuring complete coverage. Follow the adhesive manufacturer’s guidelines for the application method, which may involve using a brush, roller, or trowel. Be mindful of the working time of the adhesive to ensure it remains tacky during the lagging application.
Attaching the Lagging Material
Once the adhesive is applied, carefully attach the lagging material to the pulley. Start at one end and press the lagging material firmly onto the adhesive-coated pulley surface. Use a rolling tool to apply even pressure and remove any air bubbles trapped between the lagging and the pulley. Ensure that the lagging material is aligned correctly and covers the entire pulley surface without gaps. For grooved or patterned lagging, ensure the grooves are oriented in the correct direction for optimal performance.
Ensuring Proper Alignment and Tension
Proper alignment and tension of the lagging material are crucial for the conveyor system’s efficient operation. Check the alignment of the lagging material to ensure it is straight and centered on the pulley. Any misalignment can cause uneven wear and reduce the effectiveness of the lagging. If necessary, adjust the tension to ensure the lagging material is taut and securely bonded to the pulley surface.
Final Steps
Curing Time and Testing
After the lagging material is installed, allow the adhesive to cure according to the manufacturer’s recommendations. The curing time can vary depending on the adhesive type and environmental conditions. Once cured, perform a thorough inspection of the lagging installation. Check for any areas where the adhesive may not have bonded correctly or where the lagging material may have lifted. Address any issues promptly to ensure a secure bond.
Regular Inspection and Maintenance Tips
To maintain the performance and longevity of the conveyor drive pulley lagging, regular conveyor belt inspection and maintenance are essential. Inspect the lagging periodically for signs of wear, damage, or delamination. Clean the pulley and lagging surface regularly to remove any buildup of material that could affect performance. Additionally, check the tension and alignment of the lagging material during routine maintenance to ensure it remains secure and effective.
Conveyor Drive Pulley Lagging Rubber Sheet
Detailed Information About Rubber Lagging Sheets
Rubber sheets for conveyor drive pulley lagging are essential components in enhancing the efficiency and lifespan of conveyor systems. These sheets provide a protective layer to the pulley surface, increasing friction and preventing slippage. Understanding the different types, thicknesses, and application methods of rubber lagging sheets is crucial for optimizing conveyor system performance.
Types and Thicknesses Available
Rubber lagging sheets come in various types and thicknesses, each designed to meet specific operational requirements and environmental conditions. The primary types of rubber lagging sheets include:
- Plain Rubber Sheets: These sheets provide a smooth, uniform surface that offers good wear resistance and moderate friction. They are typically used on non-drive pulleys to protect against wear without the need for additional grip.
- Grooved Rubber Sheets: These sheets feature patterns such as diamond, herringbone, or chevron grooves, which enhance friction and water dispersion. Grooved rubber sheets are ideal for drive pulleys where increased grip and reduced slippage are critical.
- Ceramic-Embedded Rubber Sheets: These sheets combine rubber with ceramic tiles to provide exceptional wear resistance and high friction. They are suitable for high-tension applications and environments where the pulley is exposed to abrasive materials.
The thickness of rubber lagging sheets can vary depending on the specific requirements of the conveyor system. Common thicknesses range from 6mm to 25mm. Thicker sheets offer greater durability and wear resistance but may require more precise installation techniques to ensure proper adhesion and alignment.
Application Methods
Applying rubber lagging sheets to conveyor drive pulleys involves several steps to ensure a secure and effective bond. The application methods can vary based on the type of rubber sheet and the operational conditions of the conveyor system. The general application process includes:
- Surface Preparation: The pulley surface must be thoroughly cleaned and prepared to ensure proper adhesion. This involves removing any old lagging, paint, or debris and sandblasting the surface to create a rough texture for better bonding.
- Primer Application: A primer is applied to the cleaned pulley surface to enhance the adhesive bond between the rubber sheet and the pulley. The primer should be allowed to dry completely according to the manufacturer’s instructions.
- Adhesive Application: An appropriate adhesive is evenly applied to both the pulley surface and the rubber sheet. The type of adhesive used can vary based on the rubber sheet material and operational conditions.
- Lagging Installation: The rubber sheet is carefully aligned and pressed onto the pulley surface. Rolling tools or mechanical presses are used to apply even pressure, ensuring that the rubber sheet is securely bonded and free of air bubbles.
- Curing: The adhesive must be allowed to cure according to the manufacturer’s specifications. Proper curing is essential for achieving a strong, durable bond.
Advantages of Using Rubber Sheets for Pulley Lagging
Rubber sheets offer several advantages when used for conveyor drive pulley lagging, making them a popular choice across various industries.
Customization Options
One of the key benefits of rubber lagging sheets is their customization options. Rubber sheets can be tailored to meet the specific requirements of different conveyor systems, including customized thicknesses, groove patterns, and material compositions. This flexibility allows for the optimization of lagging performance based on the unique demands of each application. Customization ensures that the lagging provides the right balance of friction, durability, and wear resistance.
Flexibility and Ease of Installation
Rubber sheets are highly flexible, making them easy to work with during installation. This flexibility allows for a snug fit around the pulley surface, ensuring comprehensive coverage and protection. Additionally, rubber sheets can be easily cut and shaped to fit pulleys of various sizes and configurations, simplifying the installation process.
The ease of installation also means that maintenance and replacement of rubber lagging can be performed more quickly and efficiently. Reduced installation time translates to less downtime for the conveyor system, maintaining productivity and operational efficiency.
Conveyor drive pulley lagging options extend beyond traditional rubber and ceramic materials, offering innovative solutions such as polyurethane/plastic lagging and replaceable rim lagging. These additional options provide unique benefits that can enhance the performance, durability, and maintenance efficiency of conveyor systems. Polyurethane and plastic lagging offer high durability, chemical resistance, and reduced belt wear, making them suitable for harsh environments. On the other hand, replaceable rim lagging provides easy maintenance, cost-effective replacement, and enhanced versatility, ensuring minimal downtime and continuous operation.
Choosing the right conveyor drive pulley lagging option depends on specific operational needs, environmental conditions, and budget considerations. By understanding the benefits and challenges of each type, businesses can make informed decisions to optimize their conveyor systems’ performance and longevity. Investing in advanced lagging options can lead to significant improvements in efficiency, reliability, and overall cost savings, contributing to the long-term success of conveyor operations.
Importance and Reasons for Conveyor Drive Pulley Lagging
Increased Friction
- Enhanced Traction: The primary importance of conveyor drive pulley lagging is to increase friction between the pulley and the conveyor belt. This enhanced traction prevents the belt from slipping, ensuring smooth and efficient operation.
- Optimized Performance: By maintaining consistent grip, the lagging optimizes the performance of the conveyor system, especially in high-speed applications where slippage can be a significant issue.
Prevention of Belt Slippage
- Operational Efficiency: Preventing belt slippage is crucial for maintaining the efficiency of the conveyor system. Slippage can lead to interruptions, misalignment, and operational delays, all of which can be costly.
- Consistent Movement: Lagging ensures that the conveyor belt moves consistently without sudden stops or jerks, which is vital for processes that rely on steady material flow.
Extended Belt Life
- Reduced Wear and Tear: Lagging protects the belt from direct contact with the pulley, reducing wear and tear. This is especially important in applications with high rotational speeds, where the belt is subjected to greater stress.
- Cost Savings: By extending the life of the belt, lagging reduces the frequency of belt replacements, leading to significant cost savings over time.
Protection for Conveyor Components
- Minimized Equipment Wear: Quality lagging materials protect the pulley and other conveyor components from abrasion and damage. This helps maintain the integrity of the equipment and reduces the need for frequent repairs.
- Longevity of System: Protecting the conveyor components with lagging contributes to the overall longevity of the system, ensuring that it operates efficiently for a longer period.
Investment in Quality Components
- Business Efficiency: Investing in quality conveyor components, including lagging, maximizes the value of your application. High-quality lagging materials ensure reliable and efficient operation, reducing downtime and improving productivity.
- Return on Investment: While there may be an initial cost for high-quality lagging, the long-term benefits in terms of reduced maintenance, fewer replacements, and enhanced operational efficiency provide a substantial return on investment.
Adaptability to High-Speed Applications
- Handling High Rotational Speeds: Lagging is particularly important for applications that require high rotational speeds. It ensures that the belt maintains traction even at higher speeds, preventing slippage and maintaining operational integrity.
- Improved Safety: By preventing slippage and ensuring smooth operation, lagging also contributes to the safety of the conveyor system, reducing the risk of accidents and equipment damage.
The importance of conveyor drive pulley lagging lies in its ability to enhance traction, prevent belt slippage, extend the life of the belt, protect conveyor components, and represent a wise investment in quality equipment. These benefits collectively contribute to improved operational efficiency, cost savings, and the longevity of the conveyor system.
Conveyor Drive Pulley Lagging Applications
Conveyor drive pulley lagging is utilized across a wide range of industries to enhance the performance and durability of conveyor systems. Here are some key applications:
Mining Industry
- Ore Handling: Lagging is essential in the mining industry for handling abrasive materials like coal, ores, and minerals. It helps in reducing slippage and wear, ensuring smooth operation under harsh conditions.
- Material Transfer: In mines, conveyor systems are used to transfer materials over long distances. Lagging ensures consistent traction and reduces maintenance needs.
Power Generation
- Coal Conveyance: Power plants that rely on coal as a fuel source use conveyors to transport coal to boilers. Pulley lagging enhances grip, preventing slippage and ensuring continuous feed to the boilers.
- Ash Handling: After combustion, the removal of ash is facilitated by conveyors. Lagging helps manage this process efficiently, even in the presence of abrasive ash particles.
Agriculture
- Grain Transportation: In agricultural settings, conveyor systems are used for transporting grains and other bulk agricultural products. Lagging prevents belt slippage and protects both the belt and pulley from damage caused by dust and debris.
- Fertilizer Handling: Conveyors used for handling fertilizers benefit from lagging due to its ability to withstand the corrosive nature of these materials.
Manufacturing and Processing
- Assembly Lines: In manufacturing, conveyor systems are integral to assembly lines. Lagging ensures that belts run smoothly and consistently, maintaining production efficiency.
- Food Processing: Food processing plants use conveyors to move products through various stages of production. Lagging materials that are food-safe help in maintaining hygiene and preventing contamination.
Construction
- Aggregate Transport: Construction sites use conveyors to move aggregates like sand, gravel, and crushed stone. Pulley lagging provides the necessary traction and durability to handle these heavy, abrasive materials.
- Cement Production: In cement plants, conveyors are used to transport raw materials and finished products. Lagging helps in managing the heavy loads and reducing wear and tear on the system.
Ports and Shipping
- Bulk Material Handling: Ports use conveyor systems to handle bulk materials such as grains, coal, and ores. Lagging ensures efficient loading and unloading processes by providing consistent traction.
- Cargo Management: In shipping terminals, conveyor systems facilitate the movement of cargo. Lagging enhances the performance of these systems, ensuring quick and efficient handling of goods.
Chemical Industry
- Corrosive Materials: In the chemical industry, conveyors transport various corrosive materials. Lagging materials that are resistant to chemicals protect the pulley and extend the life of the conveyor system.
- Powder Handling: For the transportation of powders and fine particles, lagging helps in maintaining consistent movement and preventing material buildup on the pulley.
Conveyor drive pulley lagging is crucial in a variety of applications across multiple industries. It enhances the efficiency, reliability, and longevity of conveyor systems by providing better traction, reducing wear, and protecting the components from damage.
FAQs about Conveyor Drive Pulley Lagging
Pulley lagging in a conveyor system refers to the process of covering the surface of conveyor pulleys with a layer of material. This material is typically rubber, ceramic, or polyurethane and serves several critical functions. The primary purpose of pulley lagging is to increase the friction between the pulley and the conveyor belt. This enhanced friction improves the traction of the pulley, preventing slippage and ensuring efficient power transmission. Additionally, pulley lagging protects the pulley surface from wear and tear, extending its lifespan and reducing maintenance costs. It also helps in water shedding, reducing the risk of belt slippage in wet conditions. By improving the grip and durability of the conveyor system, pulley lagging enhances the overall performance and reliability of the conveyor, making it an essential component in various industrial applications.
Removing pulley lagging involves several steps to ensure that the pulley surface is properly prepared for new lagging. First, it is essential to safely shut down the conveyor system and disconnect any power sources to prevent accidents. The next step is to carefully cut and peel off the existing lagging material. This can be done using a utility knife or a specialized cutting tool. It’s important to work slowly and methodically to avoid damaging the pulley surface. Once the old lagging is removed, any remaining adhesive or residue on the pulley surface must be cleaned off. This can be achieved using a solvent or adhesive remover, along with scrapers or wire brushes. After cleaning, the pulley surface should be inspected for any damage or wear. Any necessary repairs should be made before applying new lagging. Finally, the pulley should be sandblasted or roughened to ensure proper adhesion of the new lagging material.
Pulley lagging materials vary based on the specific requirements of the conveyor system and the operating environment. The most common materials used for pulley lagging are rubber, ceramic, and polyurethane. Rubber lagging is the most widely used due to its excellent flexibility, durability, and cost-effectiveness. It provides good friction and is suitable for a wide range of applications. Ceramic lagging, on the other hand, is known for its superior wear resistance and high friction properties. It is ideal for heavy-duty applications where maximum grip and longevity are required. Polyurethane lagging is another option, offering excellent abrasion resistance and flexibility. It is often used in applications where chemical resistance is important. Each material has its unique advantages and is selected based on factors such as load capacity, operating conditions, and maintenance requirements. Choosing the right lagging material is crucial for optimizing the performance and lifespan of the conveyor system.
Applying pulley lagging involves a systematic process to ensure optimal performance and durability. The first step is to prepare the pulley surface by cleaning it thoroughly and removing any old lagging material, adhesive, or contaminants. The pulley surface should then be roughened using sandblasting or a grinding tool to create a texture that promotes better adhesion. Next, an adhesive primer is applied to the pulley surface and allowed to dry according to the manufacturer’s instructions. The lagging material, usually cut to the appropriate size, is then coated with adhesive on the side that will contact the pulley. Once the adhesive is tacky, the lagging material is carefully aligned and applied to the pulley, ensuring there are no air bubbles or gaps. The lagging should be pressed firmly against the pulley, using a roller or similar tool to ensure even contact. After application, the pulley lagging must be allowed to cure for the recommended period before the conveyor system is restarted. Regular inspection and maintenance will help ensure the lagging remains effective and extends the pulley’s service life.
The lagging rubber on a drum pulley is a layer of rubber or other material applied to the surface of the pulley to enhance its grip and protect it from wear and damage. This rubber layer increases the friction between the pulley and the conveyor belt, which helps prevent slippage and ensures smooth operation. Lagging also acts as a protective barrier, safeguarding the pulley from abrasion, corrosion, and other forms of wear that can occur during regular use. By improving traction, lagging reduces the load and wear on the conveyor system components, such as belts, bearings, and take-up units, ultimately extending their service life. Different types of lagging, such as plain, grooved, or diamond-patterned, can be used depending on the specific application and operating conditions to optimize performance and efficiency.
The driven pulley rotates slower than the driver pulley primarily due to the difference in their sizes and the mechanical advantage created by the pulley system. This phenomenon is explained by the principles of gear ratios or pulley diameters in a belt and pulley system. When the driver pulley, which is attached to the power source, rotates, it transfers motion to the belt, which in turn drives the driven pulley. If the driven pulley has a larger diameter than the driver pulley, it will rotate slower because a greater circumference requires more time to complete one revolution. This reduction in speed is beneficial in many applications as it can increase torque, allowing the driven pulley to handle greater loads with reduced rotational speed, which can be crucial for machinery requiring high torque and low-speed operations.
Hot vulcanized pulley lagging is a process used to apply a durable and high-friction rubber layer to the surface of a conveyor pulley. The process begins with thoroughly cleaning and preparing the pulley surface to ensure optimal adhesion. A layer of raw rubber is then applied to the pulley shell, followed by wrapping the pulley in a specially designed curing tape. The pulley is placed in a vulcanizing press, where it is subjected to high temperatures and pressure. This environment causes the raw rubber to undergo a chemical reaction known as vulcanization, which transforms it into a tough, elastic material that strongly bonds to the pulley surface. The result is a seamless, wear-resistant layer that provides excellent traction and protects the pulley from damage. Hot vulcanized lagging is preferred for its superior durability and performance in harsh operating conditions.
To increase pulley speed, you can either decrease the size of the driver pulley or increase the size of the driven pulley. This adjustment alters the gear ratio between the pulleys, leading to a higher rotational speed for the driven pulley. Another method is to increase the speed of the motor or power source driving the pulley system. Using a variable frequency drive (VFD) can also help by allowing precise control over the motor speed, thereby increasing the pulley speed as needed. Ensuring that the belt is properly tensioned and in good condition can also prevent slippage, which can contribute to maintaining or increasing pulley speed. It’s important to consider the impact of increased speed on the overall system, including potential increases in wear and the need for adequate lubrication and cooling.
Several factors can reduce the efficiency of a pulley system. Friction is a primary factor; while some friction is necessary for the pulley to function, excessive friction can lead to energy loss as heat. Misalignment of the pulleys and shafts can also cause inefficiency, as it creates additional friction and uneven wear on the belts and pulleys. Poor maintenance, such as lack of lubrication or accumulation of dirt and debris, can further hinder the smooth operation of the pulley system. Belt slippage due to improper tension or worn belts can also reduce efficiency by preventing effective power transmission. Additionally, load imbalances and using pulleys that are not appropriately sized or designed for the specific application can contribute to reduced efficiency and increased wear and tear on the system.
The efficiency of a pulley system is primarily affected by two factors: friction and mechanical advantage.
Friction: While some friction is necessary for the operation of a pulley system, excessive friction between the pulleys, belts, or ropes can lead to energy loss. This friction generates heat and wear, reducing the system’s overall efficiency. Proper lubrication, alignment, and maintenance are essential to minimize unnecessary friction and ensure smooth operation.
Mechanical Advantage: The design and configuration of the pulley system determine its mechanical advantage, which is the ratio of the output force to the input force. Systems with higher mechanical advantage require less input force to lift a given load, thus operating more efficiently. However, achieving a high mechanical advantage often involves using multiple pulleys, which can introduce additional friction points and complexity. Balancing these factors is crucial to optimizing the efficiency of the pulley system.
Last Updated on August 12, 2024 by Jordan Smith
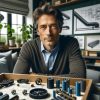
Jordan Smith, a seasoned professional with over 20 years of experience in the conveyor system industry. Jordan’s expertise lies in providing comprehensive solutions for conveyor rollers, belts, and accessories, catering to a wide range of industrial needs. From initial design and configuration to installation and meticulous troubleshooting, Jordan is adept at handling all aspects of conveyor system management. Whether you’re looking to upgrade your production line with efficient conveyor belts, require custom conveyor rollers for specific operations, or need expert advice on selecting the right conveyor accessories for your facility, Jordan is your reliable consultant. For any inquiries or assistance with conveyor system optimization, Jordan is available to share his wealth of knowledge and experience. Feel free to reach out at any time for professional guidance on all matters related to conveyor rollers, belts, and accessories.