Maintenance Tips for Conveyor Drums
Conveyor drums are essential components in conveyor systems, crucial for efficient and reliable material handling across various industries. These drum pulleys drive the conveyor belts, ensuring smooth and consistent movement of materials. From quarries and mining operations to food processing and packaging, conveyor drums play a vital role in maintaining operational efficiency. The versatility and robust construction of conveyor drums make them indispensable in handling heavy loads and challenging environments. This comprehensive guide explores the different types and applications of conveyor drums, providing valuable insights into their design, functionality, and the leading manufacturers who produce them. Discover how conveyor drums can enhance your material handling processes and improve overall productivity.
What Are Conveyor Drum Pulleys
Definition and Function
Conveyor drums are integral to the operation of conveyor systems, serving as the driving force that propels the conveyor belt. A conveyor drum pulley, a specific type of drum pulley, is designed to transmit motion from a motor to the conveyor belt. This action facilitates the continuous movement of materials along the belt, crucial in various industries like mining, manufacturing, and logistics. Conveyor drums are typically positioned at the head and tail of the conveyor system. The head pulley drives the belt forward, while the tail pulley maintains tension and alignment. These components ensure the smooth and efficient operation of conveyor systems, making them indispensable in high-volume material handling environments.
Types of Drum Pulleys
Conveyor drums come in several types, each designed for specific applications and load requirements. The three primary types are:
Standard Drum Pulleys: These are the most common type of conveyor drum pulleys, used in general-purpose conveyor systems. They are typically made from mild steel and are suitable for light to moderate load applications. Companies like Flexco and Martin Sprocket & Gear produce a wide range of standard drum pulleys, known for their reliability and cost-effectiveness.
Heavy-Duty Drum Pulleys: Designed for more demanding applications, heavy-duty drum pulleys are built to withstand higher loads and harsher operating conditions. These pulleys are often used in industries such as mining and construction, where conveyor systems handle large volumes of heavy materials. Heavy-duty drum pulleys are reinforced with thicker materials and advanced construction techniques to ensure durability and longevity. Superior Industries and Baldor-Dodge are renowned manufacturers providing high-quality heavy-duty drum pulleys, capable of supporting significant operational stresses.
Engineered Drum Pulleys: For specialized applications that require custom solutions, engineered drum pulleys are designed to meet specific operational requirements. These pulleys can be tailored in terms of size, material, and construction to fit unique conveyor systems. Engineered drum pulleys are used in environments where standard and heavy-duty pulleys might not suffice, such as in extreme temperature conditions or when handling abrasive materials. Companies like Rulmeca and Van Gorp offer bespoke engineered drum pulleys, ensuring optimal performance in challenging settings.
Construction and Materials
The construction and materials of conveyor drums are critical to their performance and lifespan. The most common materials used in the manufacture of drum pulleys are steel and stainless steel, each offering unique benefits.
Steel Drum Pulleys: Mild steel is the standard material for drum pulleys due to its balance of strength, durability, and cost. Steel drum pulleys are suitable for a wide range of applications, from light industrial uses to more robust operations. The construction process typically involves welding the cylindrical shell to the end discs and then balancing the assembly to ensure smooth rotation. This welding process, often carried out using MIG (Metal Inert Gas) welding techniques, provides a strong and durable joint, essential for withstanding the mechanical stresses of conveyor operation.
Stainless Steel Drum Pulleys: For applications requiring corrosion resistance, such as in food processing or chemical handling, stainless steel drum pulleys are preferred. Stainless steel offers superior resistance to rust and other forms of corrosion, ensuring longevity and hygiene in sensitive environments. Manufacturers like Precision Pulley & Idler (PPI) and Fenner Dunlop produce stainless steel drum pulleys designed to meet stringent industry standards for safety and cleanliness.
Advanced Construction Techniques: Modern drum pulleys often incorporate advanced construction techniques to enhance performance. These include the use of thicker shell materials for increased stress absorption, precision balancing to reduce vibration, and the application of various lagging materials to improve belt traction. Lagging, which involves covering the pulley surface with materials like rubber or ceramic, enhances grip and reduces wear on the conveyor belt.
An example of innovative construction is seen in the products from Continental Conveyor, which offers drum pulleys with ceramic lagging for enhanced durability and performance in abrasive environments. These advanced materials and techniques ensure that conveyor drums can handle high loads and operate efficiently under challenging conditions.
In the realm of conveyor drums, the integration of precise engineering, high-quality materials, and advanced manufacturing processes is key to achieving optimal performance and longevity. This comprehensive understanding of conveyor drum pulleys, from their fundamental functions to the specifics of their construction, underscores their critical role in modern material handling systems.
The Role of Tail Drum Conveyor Drums
Purpose and Placement
Conveyor drums play a crucial role in the efficient operation of conveyor systems, and the tail drum is a vital component of this setup. Positioned at the end of the conveyor system opposite the drive pulley, the tail drum conveyor ensures that the conveyor belt is guided back from the load to the start point of the belt. This cyclical movement is essential for continuous material handling, making tail drums indispensable in various industrial applications.
In conveyor systems, tail drum conveyor drums help maintain the belt’s tension and alignment. By positioning the tail drum at the end of the conveyor, systems like those manufactured by Sandvik and Metso ensure that materials are transported smoothly and efficiently. These companies have tailored their tail drum designs to meet specific industry needs, ensuring reliability and durability in harsh working conditions. For instance, Metso’s tail drums are designed to withstand the rigors of heavy-duty applications, providing consistent performance in mining and aggregate industries.
Tensioning and Alignment
One of the primary functions of tail drum conveyor drums is to maintain the proper tension of the conveyor belt. This is achieved through tensioning mechanisms that adjust the drum’s position, ensuring the belt remains taut and aligned during operation. Proper tensioning is critical for preventing slippage and reducing wear on the belt, which can lead to costly downtime and maintenance issues.
Tail drum conveyor drums are engineered to provide precise tensioning capabilities. For example, Flexco’s tail drum designs incorporate advanced tensioning systems that allow for easy adjustments, enhancing the belt’s lifespan and operational efficiency. These systems are particularly useful in applications where the conveyor belt experiences varying loads and environmental conditions, such as in recycling plants and food processing facilities.
In addition to tensioning, alignment is another key function of tail drum conveyor drums. Misalignment can cause the belt to drift off course, leading to potential damage and operational inefficiencies. Tail drum conveyor drums are designed with alignment features that ensure the belt runs smoothly and stays on track. This is achieved through the use of crowned surfaces or adjustable mechanisms that correct the belt’s path.
Design Variations
Tail drum conveyor drums come in various designs to meet different operational needs and performance requirements. These variations can include differences in size, materials, and additional features such as locking mechanisms and lagging options.
Locking Mechanisms: Tail drum conveyor drums often feature locking mechanisms that secure the drum in place, preventing unwanted movement during operation. These mechanisms are critical for maintaining the drum’s position, especially in high-tension environments. For example, Rulmeca offers tail drums with robust locking systems that ensure stability and reliability in demanding applications.
Lagging Options: Lagging is another important design variation that enhances the performance of tail drum conveyor drums. Lagging involves covering the drum’s surface with a material that increases friction and grip, improving the belt’s traction and reducing slippage. Tail drum conveyor drums can be fitted with various types of lagging, including rubber, ceramic, and polyurethane, each offering different benefits.
Rubber lagging, for instance, provides excellent grip and is suitable for general-purpose applications. Ceramic lagging, on the other hand, offers superior durability and resistance to abrasion, making it ideal for heavy-duty operations. Polyurethane lagging combines the benefits of both rubber and ceramic, providing high wear resistance and good grip. Companies like Precision Pulley & Idler (PPI) and Fenner Dunlop manufacture tail drums with a wide range of lagging options to suit different industry requirements.
Size and Material: The size and material of tail drum conveyor drums can also vary depending on the application. Standard sizes are available for general-purpose use, while custom sizes can be manufactured to meet specific operational needs. The materials used in the construction of tail drums typically include steel and stainless steel, chosen for their strength and durability.
Steel tail drum conveyor drums are commonly used in heavy-duty applications due to their high strength and resistance to impact. Stainless steel drums are preferred in environments where corrosion resistance is critical, such as in food processing and chemical handling industries. The choice of material can significantly impact the drum’s performance and longevity, ensuring it can withstand the specific demands of the operation.
Tail drum conveyor drums are essential components in conveyor systems, providing critical functions such as tensioning, alignment, and improved traction through various design features. Companies like Sandvik, Metso, Flexco, Rulmeca, PPI, and Fenner Dunlop offer a range of tail drum designs tailored to meet the diverse needs of different industries, ensuring reliable and efficient material handling. By understanding the purpose, placement, and design variations of tail drum conveyor drums, industries can optimize their conveyor systems for better performance and reduced maintenance costs.
Detailed Insights into Drum Pulley Drawings for Conveyor Drums
Importance of Accurate Drawings
In the world of conveyor drums, precision and accuracy are paramount. Drum pulley drawings serve as the blueprint for manufacturing these critical components, ensuring that every aspect of the pulley is designed to meet specific operational requirements. Accurate drum pulley drawings are essential because they provide detailed specifications that guide the manufacturing process, from the initial material selection to the final assembly.
Conveyor drums play a vital role in the smooth operation of conveyor systems. For example, companies like Continental Conveyor and Flexco rely on detailed drum pulley drawings to produce high-quality pulleys that meet rigorous industry standards. These drawings include precise measurements and tolerances, ensuring that each drum pulley fits perfectly within the conveyor system, thereby minimizing wear and tear and reducing the likelihood of operational failures.
Without accurate drum pulley drawings, manufacturers risk producing components that do not meet the required specifications, leading to potential issues such as misalignment, excessive wear, and even system breakdowns. This not only increases maintenance costs but can also result in significant downtime, affecting productivity and profitability.
Key Components in Drawings
Drum pulley drawings must include several critical elements to ensure they provide a comprehensive guide for manufacturing. These elements typically encompass dimensions, materials, and shaft details, among other specifications.
Dimensions: Accurate dimensions are crucial in drum pulley drawings. They dictate the size and shape of the pulley, ensuring it fits correctly within the conveyor system. Key dimensions include the diameter and width of the pulley, as well as the size of the bore for the shaft. For instance, Flexco’s drum pulley drawings detail every dimension down to the millimeter, ensuring perfect alignment and fit within the system.
Materials: The choice of materials is another vital aspect included in drum pulley drawings. Materials must be specified to ensure the drum pulley can withstand the operational stresses and environmental conditions it will face. Common materials include mild steel for general applications and stainless steel for environments requiring corrosion resistance. Manufacturers like Rulmeca specify these materials in their drawings to guarantee that the finished product meets the necessary durability and performance standards.
Shaft Details: The shaft is a critical component of the drum pulley, and its details must be meticulously outlined in the drawings. This includes the shaft diameter, length, and keyway dimensions, as well as any specific features such as flanges or locking mechanisms. Precise shaft details ensure that the drum pulley can transmit the required torque without slipping or misalignment. For example, Fenner Dunlop includes detailed shaft specifications in their drum pulley drawings to ensure robust and reliable performance.
Customization and Client Specifications
Customization is a significant aspect of drum pulley manufacturing, allowing manufacturers to tailor their products to meet specific client requirements and industry standards. Drum pulley drawings play a crucial role in this customization process, providing a detailed reference that ensures every aspect of the pulley meets the client’s needs.
Manufacturers such as Sandvik and Metso offer customization options based on detailed drum pulley drawings. These drawings are often created in collaboration with the client, incorporating specific requirements such as unique dimensions, special materials, or additional features like lagging or flanges. For example, a client in the mining industry might require a drum pulley with extra-thick lagging to handle abrasive materials. This requirement would be reflected in the drum pulley drawings, ensuring that the finished product meets the specific demands of the application.
In addition to custom dimensions and materials, drum pulley drawings can also include details about the pulley’s surface finish, balance specifications, and any additional treatments or coatings. These specifications ensure that the drum pulley not only fits within the existing system but also performs optimally under the specific operating conditions it will encounter.
Companies like Superior Industries excel in producing custom drum pulleys based on detailed drawings. Their engineers work closely with clients to develop drum pulley drawings that meet precise specifications, ensuring the final product delivers reliable performance and extended service life. This collaborative approach ensures that every drum pulley is tailored to the unique needs of each application, providing optimal efficiency and durability.
Drum pulley drawings are indispensable in the manufacturing process of conveyor drums, ensuring precision, customization, and adherence to industry standards. By providing detailed specifications on dimensions, materials, and shaft details, these drawings guide manufacturers in producing high-quality drum pulleys that meet specific operational requirements. Companies like Continental Conveyor, Flexco, Rulmeca, Fenner Dunlop, Sandvik, and Superior Industries rely on these drawings to deliver reliable, durable, and efficient drum pulleys for a wide range of industrial applications.
Types of Conveyor Belt Pulleys in Conveyor Drums
Overview of Pulley Types
In conveyor systems, various types of pulleys are essential for driving and maintaining the belt’s movement and alignment. Conveyor drums include multiple pulley types, each designed to address specific operational needs and enhance the system’s efficiency and reliability. Understanding the different types of conveyor belt pulleys within conveyor drums is crucial for selecting the right components for your application. These include drum pulleys, wing pulleys, spiral and helix pulleys, and lagged pulleys, each offering unique features and benefits.
Drum Pulleys
Drum pulleys are the most commonly used type of pulley in conveyor drums. They are cylindrical and come in various sizes to accommodate different conveyor belt widths and load requirements. Drum pulleys are typically made from materials such as mild steel or stainless steel, offering a balance of strength, durability, and cost-effectiveness.
One of the key characteristics of drum pulleys is their ability to provide a smooth and continuous surface for the conveyor belt. This helps in maintaining consistent belt tension and reducing slippage, which is critical for efficient material handling. Drum pulleys are often crowned, meaning they have a slight taper towards the edges, which helps in centering the belt and preventing it from drifting sideways.
For example, companies like Martin Sprocket & Gear and Baldor-Dodge manufacture high-quality drum pulleys designed to meet various industry standards. Martin Sprocket & Gear offers drum pulleys with robust construction and precision balancing, ensuring long service life and minimal maintenance. Baldor-Dodge provides drum pulleys with advanced features such as ceramic lagging, which enhances grip and reduces wear on the belt.
Wing Pulleys
Wing pulleys, also known as self-cleaning pulleys, are designed with a unique construction that helps in reducing material build-up on the pulley surface. They have a series of wings or fins arranged in a helical pattern around the pulley, creating gaps that allow loose material to fall away from the belt. This self-cleaning action prevents material accumulation, which can lead to belt misalignment and increased wear.
The design benefits of wing pulleys make them ideal for applications where the conveyor belt carries bulk materials that can stick to the pulley surface, such as in the mining, aggregate, and recycling industries. The self-cleaning feature helps maintain the conveyor system’s efficiency and reduces the need for frequent cleaning and maintenance.
Superior Industries is a leading manufacturer of wing pulleys, offering products that are engineered for high performance and durability. Their wing pulleys are constructed from heavy-duty materials and are available in various sizes to fit different conveyor systems. The helical design of Superior Industries’ wing pulleys ensures optimal self-cleaning performance, even in the most demanding applications.
Spiral and Helix Pulleys
Spiral and helix pulleys are advanced types of conveyor drums designed to enhance belt performance and longevity. These pulleys feature a helical pattern of steel bars or fins that wrap around the drum in a spiral configuration. This design provides continuous contact with the belt, improving grip and reducing slippage.
One of the main advantages of spiral and helix pulleys is their self-cleaning capability. The helical pattern helps in dislodging material build-up, ensuring that the pulley surface remains clean and free from debris. This feature is particularly beneficial in applications where the belt carries sticky or abrasive materials, such as in the cement and chemical industries.
Rulmeca offers a range of spiral and helix pulleys that are designed for high-efficiency material handling. Their pulleys are made from high-quality materials and are engineered to provide excellent performance in harsh operating conditions. The continuous contact provided by the spiral design ensures maximum belt traction and minimal slippage, resulting in improved conveyor system reliability and reduced maintenance costs.
Lagged Pulleys
Lagged pulleys are another important type of pulley used in conveyor drums. These pulleys are covered with a layer of material, known as lagging, which increases friction between the pulley and the conveyor belt. Lagging materials can include rubber, ceramic, and polyurethane, each offering different benefits depending on the application.
Rubber lagging is the most common type of lagging used on pulleys. It provides excellent grip and is suitable for general-purpose applications. Ceramic lagging offers superior wear resistance and is ideal for heavy-duty applications where the pulley is subjected to high levels of abrasion. Polyurethane lagging combines the benefits of both rubber and ceramic, offering good grip and wear resistance.
The role of lagged pulleys in conveyor drums is to enhance belt traction and reduce slippage, improving the overall efficiency of the conveyor system. Lagged pulleys also help in protecting the belt from damage caused by abrasive materials and reduce noise levels during operation.
Fenner Dunlop is a leading manufacturer of lagged pulleys, offering a wide range of lagging options to suit different industry needs. Their pulleys are designed to provide maximum performance and durability, ensuring reliable operation in even the most challenging environments.
Conveyor drums incorporate various types of pulleys, each designed to meet specific operational needs and improve the performance of conveyor systems. Drum pulleys, wing pulleys, spiral and helix pulleys, and lagged pulleys all play a crucial role in ensuring efficient material handling and reliable operation. Companies like Martin Sprocket & Gear, Baldor-Dodge, Superior Industries, Rulmeca, and Fenner Dunlop offer high-quality pulleys that meet industry standards and provide customized solutions for different applications. Understanding the different types of conveyor belt pulleys within conveyor drums is essential for selecting the right components and optimizing the performance of your conveyor system.
Key Insights into Conveyor Head Pulleys in Conveyor Drums
Primary Function
The conveyor head pulley, a crucial component within conveyor drums, plays a vital role in the overall functioning of a conveyor system. Its primary function is to drive the conveyor belt, providing the necessary traction to move materials efficiently from one point to another. Positioned at the discharge end of the conveyor system, the head pulley is powered by an external drive mechanism, typically an electric motor. This setup ensures that the conveyor belt is pulled forward, maintaining a continuous flow of materials.
In industries such as mining, manufacturing, and logistics, the reliability and efficiency of conveyor drums are paramount. The head pulley’s ability to maintain consistent belt movement is essential for minimizing downtime and maximizing throughput. For instance, in a mining operation, the head pulley must handle heavy loads and abrasive materials without succumbing to wear and tear. Companies like Metso and Sandvik design their conveyor head pulleys with these rigorous demands in mind, ensuring long-lasting performance and minimal maintenance requirements.
Design and Specifications
The design and specifications of conveyor head pulleys are critical to their performance within conveyor drums. Several key features must be considered to ensure optimal functionality, including the diameter, lagging options, and drive mechanisms.
Diameter: The diameter of the head pulley is a crucial factor in its design. A larger diameter provides better traction and reduces the risk of belt slippage. For example, head pulleys with diameters ranging from 200 mm to 1200 mm are common in various industries, with larger diameters preferred for heavy-duty applications. Baldor-Dodge offers a range of head pulleys with different diameters to suit specific operational needs, ensuring efficient belt movement and reduced maintenance.
Lagging Options: Lagging, the material covering the pulley’s surface, significantly impacts the pulley’s performance. Lagging materials, such as rubber, ceramic, and polyurethane, enhance friction between the pulley and the belt, reducing slippage and wear. Rubber lagging is commonly used for general applications due to its cost-effectiveness and good grip. In contrast, ceramic lagging is chosen for its superior abrasion resistance and longevity, making it ideal for mining and other heavy-duty applications. Precision Pulley & Idler (PPI) offers head pulleys with various lagging options tailored to specific industry requirements, ensuring optimal performance and durability.
Drive Mechanisms: The drive mechanism is another critical aspect of head pulley design. It typically involves an electric motor connected to the pulley via a gearbox or direct drive system. The choice of drive mechanism affects the efficiency and reliability of the conveyor system. Direct drive systems are known for their high efficiency and low maintenance requirements, making them a popular choice in modern conveyor systems. Companies like SEW-Eurodrive provide advanced drive solutions that enhance the performance and longevity of conveyor head pulleys.
Applications and Industry Use
Conveyor head pulleys are indispensable in various industries, each with specific requirements that influence the design and selection of conveyor drums. Some of the key industries that rely heavily on conveyor head pulleys include mining, manufacturing, and logistics.
Mining: In the mining industry, conveyor drums must handle heavy loads and harsh operating conditions. Head pulleys in mining conveyors are designed to withstand high levels of abrasion and impact, ensuring reliable performance in transporting minerals and ores. Metso’s head pulleys, for example, are engineered for durability and efficiency, providing mining operations with robust solutions that reduce downtime and maintenance costs.
Manufacturing: The manufacturing industry utilizes conveyor drums to streamline production processes. Head pulleys in manufacturing conveyors are essential for maintaining the continuous movement of materials along production lines. These pulleys must be designed for precision and efficiency to support high-speed operations and varying load capacities. Baldor-Dodge head pulleys are widely used in manufacturing due to their reliability and versatility, catering to different production environments and requirements.
Logistics and Warehousing: In logistics and warehousing, conveyor drums play a crucial role in material handling and distribution. Head pulleys in these systems are designed to ensure smooth and efficient movement of packages and goods. The emphasis is on reliability and minimal maintenance to support continuous operation in fast-paced environments. Companies like Flexco provide head pulleys that meet the rigorous demands of logistics and warehousing, offering solutions that enhance operational efficiency and reduce operational costs.
Conveyor head pulleys within conveyor drums are essential components that drive the belt and ensure the efficient movement of materials across various industries. Their design, including factors like diameter, lagging options, and drive mechanisms, directly influences their performance and reliability. Industries such as mining, manufacturing, and logistics rely on robust and well-designed head pulleys to maintain operational efficiency and reduce downtime. Companies like Metso, Sandvik, Baldor-Dodge, Precision Pulley & Idler (PPI), and Flexco are at the forefront of providing high-quality head pulleys tailored to meet the specific needs of these industries. Understanding the critical role and design considerations of conveyor head pulleys is crucial for optimizing conveyor systems and enhancing overall productivity.
Conveyor Drive Pulleys in Conveyor Drums
Role in Conveyor Systems
Conveyor drive pulleys are fundamental components within conveyor drums, playing a pivotal role in the operation of conveyor systems. Positioned at the head of the conveyor, the drive pulley is responsible for transferring the motor’s power to the conveyor belt, facilitating its continuous movement. This transfer of power is essential for the efficient handling and transportation of materials in various industrial settings.
The drive pulley’s ability to provide consistent and reliable power is crucial for maintaining the conveyor system’s overall efficiency. For instance, in large-scale mining operations, conveyor drums equipped with robust drive pulleys ensure the steady flow of extracted materials, reducing bottlenecks and downtime. Companies like Metso and Sandvik design their conveyor drive pulleys to handle the high demands of such environments, offering solutions that maximize productivity and minimize maintenance costs.
Types of Drive Pulleys
Conveyor drive pulleys come in various types, each tailored to meet specific operational requirements and enhance the performance of conveyor drums. The primary types include motorized and non-motorized drive pulleys.
- Motorized Drive Pulleys
- Also known as drum motors, motorized drive pulleys integrate the motor and the pulley into a single, compact unit. This design offers several advantages, including improved energy efficiency, reduced maintenance, and a streamlined conveyor system. Drum motors are particularly beneficial in environments where space is limited, and a compact solution is required. For example, Interroll and Van der Graaf are leading manufacturers of motorized drive pulleys, providing products that are widely used in food processing, packaging, and material handling industries. These motorized pulleys offer power ratings ranging from 0.1 kW to over 200 kW, catering to a wide range of applications.
- Non-Motorized Drive Pulleys
- These traditional drive pulleys rely on an external motor to drive the conveyor belt. The motor is connected to the pulley via a gearbox or direct drive system. Non-motorized drive pulleys are preferred in applications where larger power outputs are required or where the system’s modularity is crucial. Baldor-Dodge and Martin Sprocket & Gear offer a range of non-motorized drive pulleys designed for heavy-duty applications such as mining, quarrying, and bulk material handling. These pulleys are built to handle high torque and are often equipped with features like ceramic lagging to enhance durability and grip.
Maintenance and Efficiency
Maintaining conveyor drive pulleys is essential for ensuring the optimal performance and longevity of conveyor drums. Regular maintenance practices help prevent unexpected breakdowns and extend the lifespan of the drive pulley, contributing to the overall efficiency of the conveyor system.
Inspection and Cleaning
Routine inspections are necessary to check for signs of wear, damage, or misalignment. Cleaning the drive pulley and the surrounding components helps prevent material build-up that can cause slippage and reduce efficiency. For instance, PPI provides detailed maintenance guidelines for their drive pulleys, emphasizing the importance of regular inspections and cleaning to maintain optimal performance.
Lubrication
Proper lubrication of bearings and other moving parts is crucial to reduce friction and prevent overheating. The frequency and type of lubrication depend on the operating conditions and the manufacturer’s recommendations. Companies like Fenner Dunlop offer drive pulleys with sealed bearings that require minimal maintenance, ensuring smooth operation even in harsh environments.
Alignment and Tensioning
Ensuring that the drive pulley is correctly aligned with the conveyor belt is vital for preventing premature wear and reducing energy consumption. Proper tensioning of the belt also plays a critical role in maintaining efficiency. Misalignment and incorrect tensioning can lead to increased wear on the pulley and the belt, causing frequent maintenance issues. Flexco provides advanced alignment and tensioning tools that help maintain the optimal performance of conveyor drums.
Advanced Monitoring Systems
Implementing advanced monitoring systems can help detect potential issues before they lead to significant problems. These systems can monitor parameters such as temperature, vibration, and load, providing real-time data that helps in predictive maintenance. Superior Industries offers drive pulleys equipped with sensors that monitor critical performance metrics, allowing for proactive maintenance and reducing the risk of unexpected downtime.
Conveyor drive pulleys are indispensable components in conveyor drums, ensuring the efficient transfer of power and the continuous movement of conveyor belts. The choice between motorized and non-motorized drive pulleys depends on the specific operational requirements and constraints of the application. Regular maintenance practices, including inspection, cleaning, lubrication, alignment, and the use of advanced monitoring systems, are essential for maximizing the performance and lifespan of drive pulleys. Leading manufacturers like Metso, Sandvik, Interroll, Van der Graaf, Baldor-Dodge, Martin Sprocket & Gear, PPI, Fenner Dunlop, and Flexco provide high-quality drive pulleys designed to meet the diverse needs of various industries, ensuring reliable and efficient material handling. Understanding the critical role and maintenance requirements of conveyor drive pulleys is key to optimizing conveyor systems and enhancing overall operational efficiency.
Leading Conveyor Drum Manufacturers
Leading Manufacturers
The conveyor drums industry features several top manufacturers known for their expertise, innovation, and reliability. These companies have established themselves as leaders by consistently delivering high-quality products that meet the rigorous demands of various industries. Some of the leading manufacturers of conveyor drums include Metso, Sandvik, Flexco, Precision Pulley & Idler (PPI), and Rulmeca.
Metso: Metso is a global leader in the manufacturing of conveyor drums, providing robust solutions for mining, aggregates, and other heavy industries. With a strong focus on durability and performance, Metso’s conveyor drums are designed to withstand the harshest operating conditions. Their products are known for their exceptional reliability, reducing downtime and maintenance costs for their clients.
Sandvik: Sandvik is another prominent name in the conveyor drums market. They offer a wide range of conveyor drum products designed to enhance operational efficiency in mining and construction industries. Sandvik’s expertise in material science and engineering enables them to produce conveyor drums that deliver superior performance and longevity.
Flexco: Flexco specializes in innovative solutions for conveyor systems, including high-quality conveyor drums. They are renowned for their commitment to improving conveyor efficiency and productivity. Flexco’s conveyor drums are engineered to provide excellent traction and durability, making them suitable for a wide range of applications, from food processing to heavy industrial use.
Precision Pulley & Idler (PPI): PPI is a trusted name in the conveyor components industry, known for their high-performance conveyor drums. Their products are widely used in industries such as agriculture, coal mining, and bulk material handling. PPI’s focus on precision engineering ensures that their conveyor drums offer reliable and efficient performance.
Rulmeca: Rulmeca is a global manufacturer of rollers, motorized pulleys, and conveyor drums. Their products are designed to meet the diverse needs of industries like logistics, manufacturing, and mining. Rulmeca’s conveyor drums are known for their robust construction and innovative features, which help improve the efficiency and longevity of conveyor systems.
Manufacturing Processes
The manufacturing processes for conveyor drums are crucial in determining the quality and performance of the final product. Leading manufacturers employ advanced techniques and stringent quality control measures to ensure their conveyor drums meet high industry standards.
Material Selection and Processing: The first step in manufacturing conveyor drums involves selecting high-quality materials such as mild steel, stainless steel, and other durable alloys. For instance, Sandvik uses specialized steel grades to enhance the strength and wear resistance of their conveyor drums. The raw materials are then processed using state-of-the-art machinery to achieve the desired shape and size.
Precision Engineering: Precision engineering is a hallmark of leading conveyor drum manufacturers. Companies like PPI and Metso utilize advanced computer-aided design (CAD) software to create detailed drum pulley drawings that guide the manufacturing process. These drawings ensure that every component is produced to exact specifications, resulting in a product that offers superior performance and reliability.
Welding and Assembly: Welding is a critical process in the construction of conveyor drums. High-quality welding techniques, such as MIG (Metal Inert Gas) welding, are used to join the drum shell and end discs securely. This ensures the structural integrity and durability of the drum. Manufacturers like Rulmeca employ skilled welders and automated welding systems to achieve consistent and high-quality welds.
Balancing and Testing: After assembly, the conveyor drums undergo balancing to ensure smooth operation. Imbalances can cause excessive vibration and reduce the lifespan of the conveyor system. Leading manufacturers, including Flexco, use dynamic balancing machines to detect and correct any imbalances. Additionally, comprehensive testing is conducted to verify the drum’s performance under various operating conditions.
Quality Control: Quality control is integral to the manufacturing process. Companies like Metso and Sandvik implement rigorous quality control measures at every stage of production. This includes material inspection, dimensional checks, weld quality assessment, and performance testing. These measures ensure that each conveyor drum meets the highest standards of quality and reliability.
Customization and Services
One of the key strengths of leading conveyor drum manufacturers is their ability to provide customized solutions tailored to the specific needs of their clients. This customization extends to various aspects of the conveyor drums, including dimensions, materials, lagging options, and additional features.
Design Consultation: Manufacturers like Flexco and Rulmeca offer design consultation services to help clients select the right conveyor drums for their applications. Their experienced engineers work closely with clients to understand their requirements and recommend the best solutions. This collaborative approach ensures that the conveyor drums are optimized for performance and longevity.
Custom Manufacturing: Custom manufacturing is a significant aspect of the services provided by leading conveyor drum manufacturers. For instance, PPI can produce conveyor drums in non-standard sizes and with unique features to meet the specific needs of different industries. This flexibility allows clients to obtain conveyor drums that perfectly fit their conveyor systems and operational requirements.
Installation Support: In addition to manufacturing, companies like Metso and Sandvik provide installation support to ensure that the conveyor drums are correctly installed and integrated into the conveyor system. This support can include on-site assistance, installation guidelines, and training for maintenance personnel.
After-Sales Services: Comprehensive after-sales services are crucial for maintaining the performance of conveyor drums over their operational life. Leading manufacturers offer maintenance services, spare parts supply, and technical support to help clients keep their conveyor systems running smoothly. For example, Sandvik provides a range of after-sales services, including regular maintenance checks and emergency repair services.
Leading conveyor drum manufacturers like Metso, Sandvik, Flexco, PPI, and Rulmeca are renowned for their expertise, advanced manufacturing processes, and comprehensive customization and support services. Their commitment to quality and innovation ensures that their conveyor drums meet the highest standards of performance and reliability, making them the preferred choice for various industries. By understanding the strengths and capabilities of these manufacturers, clients can make informed decisions and select the best conveyor drums for their specific applications.
FAQs about Conveyor Drums
A drum in a conveyor, often referred to as a conveyor drum, is a cylindrical component that plays a crucial role in the functioning of a conveyor system. Conveyor drums are typically used at the head and tail of the conveyor to drive and redirect the belt. The head drum, also known as the drive drum, is connected to the motor and drives the conveyor belt, ensuring the smooth and consistent movement of materials. The tail drum, on the other hand, provides tension and helps maintain the belt’s alignment. These drums are constructed from materials such as steel or aluminum to withstand heavy loads and harsh operating conditions. Conveyor drums are essential for maintaining the efficiency and reliability of the conveyor system, making them indispensable components in industries like mining, manufacturing, and logistics.
There are various types of conveyors used in different industries, but the three most common types are belt conveyors, roller conveyors, and chain conveyors. Belt conveyors use a continuous belt made of materials such as rubber or PVC to transport items. They are versatile and can handle a wide range of products, making them suitable for industries like food processing, packaging, and mining. Roller conveyors consist of a series of rollers that move products along a flat surface. These are commonly used in warehouses and distribution centers for their ability to handle heavy loads and their ease of maintenance. Chain conveyors use linked chains to move products, ideal for transporting heavy or bulky items. Each type of conveyor has its own set of advantages, and the choice depends on the specific requirements of the application. Conveyor drums are integral parts of these systems, providing the necessary drive and tension for efficient operation.
A conveyor system comprises several key components that work together to ensure smooth operation. The primary parts include the conveyor belt, conveyor drums (head and tail drums), rollers, motor, and frame. The conveyor belt is the surface on which items are transported, made from materials like rubber, fabric, or metal. Conveyor drums, particularly the drive drum, are responsible for moving the belt. The rollers support the belt and help reduce friction, allowing for easier movement. The motor powers the conveyor, providing the necessary force to drive the belt. The frame or structure provides the necessary support and alignment for the entire system. Additional components like idlers, pulleys, and sensors can also be included depending on the complexity and requirements of the conveyor system. Each part is essential for maintaining the efficiency and reliability of the conveyor.
A pulley drum, also known as a conveyor drum, is a cylindrical component that helps guide and drive the conveyor belt in a conveyor system. Pulley drums come in various sizes and configurations, designed to suit different applications and load requirements. The head drum or drive drum is connected to the motor and is responsible for moving the belt. It ensures that the belt moves smoothly and consistently, facilitating the transportation of materials. The tail drum provides tension to keep the belt tight and properly aligned. Pulley drums are typically made from durable materials such as steel or aluminum, capable of withstanding heavy loads and harsh operating conditions. They are essential components in maintaining the functionality and efficiency of conveyor systems, making them vital in industries like mining, manufacturing, and logistics.
Last Updated on June 11, 2024 by Jordan Smith
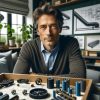
Jordan Smith, a seasoned professional with over 20 years of experience in the conveyor system industry. Jordan’s expertise lies in providing comprehensive solutions for conveyor rollers, belts, and accessories, catering to a wide range of industrial needs. From initial design and configuration to installation and meticulous troubleshooting, Jordan is adept at handling all aspects of conveyor system management. Whether you’re looking to upgrade your production line with efficient conveyor belts, require custom conveyor rollers for specific operations, or need expert advice on selecting the right conveyor accessories for your facility, Jordan is your reliable consultant. For any inquiries or assistance with conveyor system optimization, Jordan is available to share his wealth of knowledge and experience. Feel free to reach out at any time for professional guidance on all matters related to conveyor rollers, belts, and accessories.