Key Benefits of Using a Conveyor Frame Kit
The conveyor frame is a crucial component in modern material transportation systems, providing the necessary support and structure for efficient operation. The quality and material of the conveyor frame play a significant role in ensuring the system’s reliability, durability, and overall performance. Different types of conveyor frames are available in the market, each designed to meet specific industry requirements. These variations include lightweight aluminum frames, robust steel frames, and corrosion-resistant stainless steel frames, catering to diverse operational needs. Selecting the right conveyor frame is essential for optimizing workflow and minimizing maintenance costs in various industrial applications.
Conveyor Frame Kit
Definition and Components of a Conveyor Frame Kit
A conveyor frame kit is a comprehensive assembly package designed to provide all the necessary components for building a custom conveyor frame. These kits typically include side rails, cross members, brackets, mounting hardware, and sometimes pre-fabricated holes for easy assembly. The primary purpose of a conveyor frame kit is to simplify the process of constructing a conveyor system by providing standardized, high-quality components that ensure a robust and reliable frame structure. This modular approach allows for greater flexibility and customization, enabling businesses to tailor their conveyor systems to specific operational needs.
Benefits of Using a Kit for Custom Conveyor Solutions
- Ease of Assembly: Conveyor frame kits, such as those offered by FlexLink and mk North America, are designed for straightforward assembly, reducing the time and labor required to build a conveyor system. The components are pre-engineered to fit together seamlessly, minimizing the need for specialized tools or skills.
- Cost-Effective: By purchasing a complete kit, businesses can often save money compared to sourcing individual components. Companies like Bosch Rexroth offer cost-effective solutions through their conveyor frame kits, reducing procurement costs and ensuring compatibility between parts.
- Customization: Kits from manufacturers like Dorner and Hytrol offer a high degree of flexibility, allowing businesses to customize their conveyor frames to meet specific requirements. This is particularly useful in industries with unique material handling needs.
- Consistency and Quality: Kits are manufactured to stringent quality standards, ensuring that each component meets performance and durability criteria. This consistency enhances the overall reliability of the conveyor system, as seen with products from SpanTech and MayTec.
- Scalability: As businesses grow and their needs evolve, conveyor frame kits from companies like MiTek can be easily expanded or modified. Additional modules can be integrated into the existing system without major overhauls.
- Reduced Downtime: The standardized components and ease of assembly mean that repairs and maintenance can be performed quickly, minimizing downtime and keeping operations running smoothly. Brands like Interroll provide kits that focus on minimizing downtime through easy maintenance.
Applications in Various Industries
- Manufacturing: Conveyor frame kits are widely used in manufacturing plants to transport raw materials, work-in-progress items, and finished products. The modular nature of these kits allows for quick adjustments to meet changing production demands, with companies like Siemens and ABB providing reliable solutions.
- Food and Beverage: In the food and beverage industry, conveyor frame kits from manufacturers like FlexLink and Dorner are essential for maintaining hygienic and efficient transport of products through processing, packaging, and distribution stages.
- Warehousing and Distribution: Warehouses and distribution centers rely on conveyor frame kits from Hytrol and SpanTech to streamline the movement of goods, enhancing order fulfillment speed and accuracy.
- Automotive: In automotive manufacturing, conveyor frame kits support the assembly line process, moving parts and components efficiently through various stages of production. Bosch Rexroth and Siemens are notable suppliers in this sector.
- Pharmaceutical: The pharmaceutical industry uses conveyor frame kits from FlexLink and Dorner to ensure precise and contamination-free transport of medicines and medical devices through production and packaging processes.
- Logistics: Conveyor frame kits play a critical role in logistics, facilitating the smooth movement of parcels and packages in sorting and distribution centers. Brands like Interroll and Hytrol are key players in this industry.
- Mining and Quarrying: In mining and quarrying operations, robust conveyor frame kits from companies like Metso Outotec and FLSmidth are used to transport heavy and abrasive materials, ensuring reliable performance in harsh environments.
- Packaging: The packaging industry benefits from conveyor frame kits from manufacturers like Dorner and FlexLink, which provide efficient and reliable transport solutions for various packaging needs.
Example Products and Manufacturers
- FlexLink X65 Conveyor System: This kit offers a highly flexible and robust solution for various industries, featuring easy assembly and high customization options.
- Dorner 2200 Series Modular Belt Conveyor: Known for its low-profile design and high versatility, this conveyor frame kit is ideal for small to medium-sized applications.
- Hytrol TA Slider Bed Belt Conveyor: A cost-effective solution that provides reliable performance in warehousing and distribution settings.
- Bosch Rexroth TS2plus Transfer System: This kit offers a modular approach to conveyor system design, suitable for a wide range of industrial applications.
- SpanTech EZSpan Plastic Chain Conveyor: Designed for easy maintenance and quick assembly, this conveyor frame kit is perfect for the food and beverage industry.
- Interroll Modular Conveyor Platform (MCP): Featuring a plug-and-play design, this kit ensures minimal downtime and high operational efficiency across various industries.
Conveyor Frame Design
Key Considerations in Designing a Conveyor Frame
Designing a conveyor frame involves multiple considerations to ensure efficiency, durability, and safety. Here are ten key factors:
- Load Capacity: The conveyor frame must support the maximum load it will carry. Overloading can cause structural failure, so accurate load calculations are crucial.
- Material Selection: The choice of material impacts the frame’s strength, weight, and corrosion resistance. Common materials include steel, aluminum, and stainless steel.
- Height and Distance: The frame design must account for the conveyor’s height and the distance it will cover. This ensures stability and efficient operation.
- Environmental Conditions: The frame material and design should withstand the operational environment, whether it’s indoors, outdoors, humid, or exposed to chemicals.
- Ergonomics: An ergonomic design facilitates easy access for maintenance and operation, reducing strain on workers and improving overall efficiency.
- Flexibility and Modularity: The ability to modify or expand the conveyor frame allows for future changes in production needs.
- Cost-Effectiveness: Balancing quality and cost ensures that the conveyor frame provides good value without compromising performance.
- Safety Standards: Compliance with industry safety standards and regulations is essential to prevent accidents and ensure safe operation.
- Ease of Assembly: A design that allows for quick and easy assembly can reduce installation time and costs.
- Maintenance Requirements: Design features that simplify maintenance can reduce downtime and extend the conveyor’s lifespan.
Materials Used and Their Impact on Frame Strength and Durability
The material used in constructing a conveyor frame significantly affects its strength, weight, and resistance to environmental factors. Common materials include:
- Steel: Known for its strength and durability, steel is often used in heavy-duty applications. It is resistant to impact and can support high loads. However, it can be prone to corrosion if not properly treated.
- Aluminum: Lightweight and corrosion-resistant, aluminum is ideal for applications where weight reduction is important. It is easy to work with and provides a good balance of strength and durability.
- Stainless Steel: Offering excellent corrosion resistance, stainless steel is suitable for environments exposed to moisture, chemicals, or extreme temperatures. It is also used in food processing due to its hygienic properties.
Design Aspects Like Load Capacity, Height, and Distance
- Load Capacity: Determining the maximum load capacity involves calculating the total weight the conveyor will carry, including products and any additional forces. The frame must be designed to handle these loads without deformation.
- Height: The height of the conveyor frame affects its stability and the ease of access for workers. Adjustable height features can enhance ergonomics and adaptability to different tasks.
- Distance: The length of the conveyor impacts the design of the frame supports and the type of materials used. Longer distances may require additional supports or stronger materials to maintain stability and prevent sagging.
Importance of Ergonomic and Efficient Design for Maintenance and Operation
- Ease of Access: Designing the conveyor frame with maintenance in mind ensures that components are easily accessible for inspection, repair, or replacement. This reduces downtime and maintenance costs.
- Worker Safety: An ergonomic design minimizes physical strain on workers, reducing the risk of injury and improving overall productivity.
- Operational Efficiency: Efficient design streamlines the movement of goods, reducing bottlenecks and increasing throughput. Features like adjustable height and modular components enhance flexibility and adaptability.
- Maintenance-Friendly Features: Including features like removable side panels, easy-to-clean surfaces, and quick-release components can significantly reduce maintenance time.
- Energy Efficiency: Designing the frame to minimize friction and wear on moving parts can enhance energy efficiency and reduce operational costs.
- Modularity: A modular design allows for easy expansion or reconfiguration of the conveyor system, providing flexibility to adapt to changing production needs.
- Durability and Longevity: Using high-quality materials and robust design principles ensures that the conveyor frame will have a long service life, reducing the need for frequent replacements and associated costs.
Designing a conveyor frame requires careful consideration of various factors, including load capacity, material selection, and ergonomic design. Manufacturers like FlexLink, Bosch Rexroth, and Dorner offer conveyor frame solutions that meet these criteria, ensuring reliable and efficient operation across different industries. By focusing on these key aspects, businesses can optimize their conveyor systems for better performance, safety, and cost-effectiveness.
Conveyor Frame in Space Engineers
Space Engineers as a Sandbox Game
Space Engineers is a popular sandbox game that allows players to build and manage various space-related structures and vehicles. Developed by Keen Software House, this game offers a realistic physics engine that challenges players to create functional and efficient systems in space. Players can mine resources, construct bases, design ships, and explore the vastness of space. The game emphasizes creativity and engineering, making it a favorite among players who enjoy problem-solving and technical challenges.
Importance of Conveyor Frames within the Game for Efficient Resource Transportation
In Space Engineers, conveyor frames are essential components for the transportation of resources and materials. They serve as the backbone of the game’s logistics system, connecting different modules and facilitating the flow of items between storage containers, refineries, assemblers, and other machinery. Efficient conveyor frame designs ensure that resources are transported quickly and reliably, which is crucial for maintaining continuous production and operational efficiency. Without well-designed conveyor frames, players may experience bottlenecks, resource shortages, and operational inefficiencies.
Tips for Designing and Building Conveyor Frames in Space Engineers
- Plan Your Layout: Before constructing conveyor frames, plan the layout of your base or ship. Consider the locations of storage containers, refineries, assemblers, and other machinery to create an efficient transportation network.
- Use Conveyor Hubs: Incorporate conveyor hubs to centralize resource distribution. These hubs can connect multiple conveyor lines, allowing for efficient resource routing.
- Minimize Length: Keep conveyor lines as short as possible to reduce the travel time of resources. Shorter conveyor lines are more efficient and easier to manage.
- Avoid Loops: Ensure that your conveyor network does not form closed loops, which can cause resources to circulate indefinitely without reaching their destination.
- Include Sorters: Use conveyor sorters to direct specific resources to designated containers or machinery. This helps in organizing resources and improving overall efficiency.
- Monitor Flow: Regularly check the flow of resources through your conveyor frames. Use the game’s diagnostic tools to identify and address any blockages or inefficiencies.
- Redundancy: Design redundancy into your conveyor system by creating multiple pathways for resource transportation. This ensures that if one pathway is blocked, resources can still reach their destination through an alternate route.
- Vertical and Horizontal Frames: Utilize both vertical and horizontal conveyor frames to maximize space and improve resource flow within your structures.
- Integrate with Cargo Ships: Design your conveyor frames to integrate seamlessly with cargo ships, enabling efficient loading and unloading of resources.
- Safety Measures: Incorporate safety measures such as conveyor connectors and ejectors to handle excess resources and prevent system overloads.
- Power Efficiency: Optimize the power usage of your conveyor frames by using advanced technology blocks that consume less energy.
- Aesthetic Design: While functionality is paramount, consider the aesthetic design of your conveyor frames to make your base or ship visually appealing.
Examples of Effective Conveyor Frame Designs Used by Players
- Centralized Base Hub: A popular design involves a centralized hub where all conveyor frames converge. This hub connects storage containers, refineries, and assemblers, ensuring efficient resource distribution.
- Vertical Mining Rig: Players often use vertical conveyor frames in mining rigs to transport mined resources from the surface to storage containers located at higher altitudes.
- Compact Ship Conveyor System: In small ships, players design compact conveyor frames that fit within the limited space while ensuring all necessary components are connected.
- Automated Sorting Facility: Some players create automated sorting facilities with conveyor sorters and hubs to efficiently categorize and store resources.
- Redundant Conveyor Network: For large bases or ships, players design redundant conveyor networks with multiple pathways to ensure resource flow even if part of the system fails.
- Mobile Base: In mobile bases, conveyor frames are designed to connect all critical components while allowing the base to move and operate efficiently in different locations.
The design and construction of conveyor frames in Space Engineers are vital for the efficient transportation of resources. By considering factors such as layout planning, use of conveyor hubs, minimizing lengths, and incorporating redundancy, players can create effective and reliable conveyor systems. Examples from the player community demonstrate various innovative designs that enhance resource management and operational efficiency within the game.
Conveyor Frame for Sale
Where to Find Conveyor Frames for Sale
Finding the right conveyor frame for your needs can be a crucial factor in ensuring the efficiency and productivity of your material handling systems. Conveyor frames are available from a variety of suppliers and distributors, each offering different options in terms of materials, sizes, and configurations. You can find conveyor frames for sale through online marketplaces, specialized industrial suppliers, and directly from manufacturers. Websites like ThomasNet and Alibaba provide extensive listings of conveyor frame suppliers, while companies such as FlexLink, Dorner, and Hytrol offer direct purchase options through their websites.
Tips for Selecting the Right Conveyor Frame for Your Needs
- Determine Your Load Requirements: Assess the maximum load your conveyor frame needs to support. Choose a frame that can handle your heaviest loads without compromising stability and durability.
- Consider the Material: Select the appropriate material based on your operational environment. Steel frames are strong and durable, while aluminum frames are lightweight and corrosion-resistant. Stainless steel is ideal for hygienic applications.
- Evaluate the Size and Dimensions: Ensure the conveyor frame dimensions fit within your workspace and meet the requirements of your conveyor system.
- Check for Modular Design: Opt for modular conveyor frames if you anticipate future expansion or reconfiguration. Modular frames allow for easy modifications and scalability.
- Inspect the Quality: Look for frames that are manufactured to high-quality standards. Check for certifications and quality marks to ensure reliability and longevity.
- Assess the Ease of Assembly: Choose conveyor frames that are easy to assemble and disassemble. This can save time and labor costs during installation and maintenance.
- Look for Customization Options: If you have specific requirements, consider suppliers that offer customization options. Tailoring the frame to your needs can enhance efficiency.
- Review Supplier Reputation: Research supplier reviews and ratings to ensure they are reputable and provide good customer service.
- Consider Ergonomics: An ergonomic design can improve worker safety and productivity. Look for frames that allow easy access for maintenance and operation.
- Check Warranty and Support: Ensure the supplier offers a good warranty and technical support in case you encounter any issues with the conveyor frame.
Price Considerations and Factors Influencing Cost
The cost of a conveyor frame can vary widely based on several factors:
- Material: Steel frames are generally more expensive than aluminum frames due to their strength and durability. Stainless steel frames are typically the most costly due to their corrosion resistance and hygienic properties.
- Size and Dimensions: Larger and more complex frames will cost more. Custom sizes and configurations can also add to the price.
- Load Capacity: Frames designed to support heavier loads are built with more robust materials and construction techniques, increasing the cost.
- Customization: Custom-designed frames will generally be more expensive than standard models due to the additional design and manufacturing work involved.
- Supplier and Brand: Established brands with a reputation for quality may charge more for their products. However, this can be worth the investment for the assurance of reliability and support.
- Quantity: Purchasing in bulk can often reduce the price per unit. Consider buying multiple frames at once if you have ongoing or future needs.
- Location and Shipping: Shipping costs can add significantly to the total price, especially for large or heavy frames. Consider local suppliers to minimize shipping expenses.
Recommended Suppliers and Distributors
- FlexLink: Known for their high-quality, modular conveyor systems, FlexLink offers a range of conveyor frames that can be customized to meet specific needs.
- Dorner: Dorner provides a variety of conveyor frames, including options for sanitary and industrial applications. Their frames are known for their durability and ease of assembly.
- Hytrol: A leading manufacturer of conveyor systems, Hytrol offers robust conveyor frames designed for heavy-duty use in various industries.
- SpanTech: SpanTech specializes in unique, customizable conveyor systems. Their conveyor frames are designed for flexibility and efficiency.
- Interroll: Interroll offers a wide range of conveyor frame solutions suitable for different applications, from light-duty to heavy-duty systems.
- Bosch Rexroth: Bosch Rexroth provides conveyor frames known for their precision and quality. They offer modular systems that are easy to expand and customize.
- MayTec: MayTec offers conveyor frames with a focus on modularity and ease of assembly. Their frames are suitable for various industrial applications and can be tailored to specific requirements.
Finding the right conveyor frame for sale involves careful consideration of your specific needs and requirements. By evaluating factors such as load capacity, material, size, and supplier reputation, you can select a conveyor frame that enhances the efficiency and productivity of your operations. Trusted suppliers like FlexLink, Dorner, and Hytrol offer a range of high-quality frames that can be customized to meet your needs.
Roller Conveyors: Conveyor Frame
Roller Conveyors and How They Differ from Other Conveyor Systems
Roller conveyors are a type of material handling system that utilizes a series of cylindrical rollers to transport goods along a horizontal or inclined path. Unlike belt conveyors, which use a continuous belt to move items, roller conveyors rely on the individual rollers’ rotational motion. This design allows for the efficient and smooth movement of various materials, making them ideal for applications where items need to be accumulated, sorted, or redirected. Roller conveyors can be powered or gravity-driven, depending on the specific requirements of the operation.
The key difference between roller conveyors and other conveyor systems lies in their construction and functionality. While belt conveyors are suitable for handling bulk materials and maintaining continuous product flow, roller conveyors excel in environments where flexibility, precision, and handling of diverse products are essential. Additionally, roller conveyors can be easily integrated with other conveyor types, creating a versatile and adaptable material handling solution.
Importance of the Conveyor Frame in the Performance and Longevity of Roller Conveyors
The conveyor frame plays a critical role in the performance and longevity of roller conveyors. A well-designed conveyor frame provides the necessary support and alignment for the rollers, ensuring smooth and efficient operation. Here are six reasons why the conveyor frame is vital:
- Structural Integrity: The conveyor frame ensures the structural integrity of the roller conveyor, preventing deformation and maintaining alignment under load.
- Load Distribution: A robust conveyor frame evenly distributes the load across the rollers, reducing stress on individual components and extending their lifespan.
- Vibration Control: The frame minimizes vibrations and oscillations, which can cause wear and tear on the rollers and other moving parts.
- Stability: A stable conveyor frame prevents the conveyor system from shifting or wobbling during operation, ensuring consistent performance and safety.
- Maintenance Access: A well-designed frame provides easy access for maintenance and inspection, facilitating routine upkeep and minimizing downtime.
- Customization: The conveyor frame can be customized to fit specific operational requirements, such as accommodating different roller sizes, spacing, and load capacities.
Common Applications and Benefits
Roller conveyors are widely used across various industries due to their versatility and efficiency. Here are eight common applications and benefits:
- Manufacturing: Roller conveyors are used in assembly lines to transport products between workstations, improving workflow and productivity.
- Warehousing and Distribution: In warehouses and distribution centers, roller conveyors facilitate the sorting and movement of packages, enhancing order fulfillment speed and accuracy.
- Automotive Industry: Roller conveyors are employed in the automotive industry for transporting parts and assemblies, ensuring efficient production processes.
- Food and Beverage: In the food and beverage sector, roller conveyors handle packaged goods, reducing manual labor and increasing throughput.
- Retail: Retail distribution centers use roller conveyors to sort and distribute products to various locations, streamlining inventory management.
- E-commerce: E-commerce fulfillment centers rely on roller conveyors for quick and efficient order processing, supporting high-volume operations.
- Logistics: Logistics companies use roller conveyors to move goods between transportation vehicles and storage areas, optimizing loading and unloading operations.
- Pharmaceutical: The pharmaceutical industry uses roller conveyors to handle and transport medications and medical supplies, ensuring safe and efficient distribution.
Customization Options and Industry-Specific Solutions
Customization options for roller conveyors allow businesses to tailor their material handling systems to specific needs and operational requirements. Some common customization options include:
- Roller Types: Choose from various roller types, such as gravity rollers, powered rollers, and tapered rollers, to suit different applications.
- Frame Materials: Select frame materials like steel, aluminum, or stainless steel based on the operational environment and load requirements.
- Roller Spacing: Adjust the spacing between rollers to accommodate different product sizes and shapes, ensuring optimal support and transportation.
- Load Capacity: Customize the conveyor frame to handle specific load capacities, enhancing durability and performance for heavy-duty applications.
- Conveyor Length and Width: Modify the conveyor dimensions to fit available space and meet the needs of the production or distribution process.
- Inclines and Declines: Design conveyor frames with inclines or declines to facilitate the movement of products between different heights and levels.
- Modular Design: Implement modular conveyor frames that allow for easy expansion, reconfiguration, and integration with other conveyor systems.
- Industry-Specific Features: Incorporate features tailored to specific industries, such as hygienic design for food processing or static-dissipative materials for electronics manufacturing.
Roller conveyors are a versatile and efficient material handling solution widely used across various industries. The importance of the conveyor frame cannot be overstated, as it significantly impacts the performance and longevity of the system. By understanding the benefits, common applications, and customization options, businesses can select the right conveyor frame to meet their specific needs and enhance their operational efficiency.
Manual Conveyor: Conveyor Frame
Manual Conveyor Systems and Their Typical Uses
Manual conveyor systems are a type of material handling equipment that relies on human effort to move products from one point to another. Unlike automated conveyor systems that use motors and sensors, manual conveyors are typically simpler in design, consisting of components such as rollers, wheels, or skate wheels mounted on a conveyor frame. These systems are ideal for applications where automation is either unnecessary or impractical, providing a cost-effective and flexible solution for material transport.
Manual conveyor systems are commonly used in various industries for tasks such as assembly line operations, packing stations, and temporary material handling setups. Their ease of use and adaptability make them suitable for a wide range of applications, from moving light packages in a warehouse to handling heavy parts in a manufacturing plant. The simplicity of manual conveyors also makes them an excellent choice for environments where space is limited or where frequent changes in the layout are required.
Importance of Frame Stability and Ease of Use
- Structural Support: The stability of the conveyor frame is crucial to ensure the safe and efficient operation of manual conveyor systems. A well-designed frame provides the necessary support to prevent sagging or misalignment, which can cause operational issues.
- Load Capacity: The conveyor frame must be capable of handling the maximum load that will be placed on it. This includes the weight of the materials being transported as well as any additional forces exerted during manual handling.
- Durability: A stable and robust frame increases the durability and longevity of the conveyor system, reducing the need for frequent repairs or replacements.
- Safety: Stability in the conveyor frame minimizes the risk of accidents, such as tipping or collapsing, ensuring a safer working environment.
- Ease of Movement: A well-designed frame ensures smooth and effortless movement of materials, reducing the physical strain on workers and improving overall efficiency.
- Adjustability: Manual conveyor frames that are adjustable in height and length provide greater flexibility, allowing them to be tailored to specific tasks and ergonomic requirements.
- Maintenance: A stable frame with easy access points simplifies maintenance tasks, ensuring that the conveyor system remains in optimal working condition.
- Cost-Effectiveness: Investing in a stable and reliable conveyor frame can lead to long-term cost savings by minimizing downtime and extending the lifespan of the system.
Comparison Between Manual and Automated Conveyor Systems
Industries Where Manual Conveyors Are Most Beneficial
- Manufacturing: In manufacturing plants, manual conveyors are used for moving parts and assemblies between workstations, allowing for flexible and scalable production lines.
- Warehousing: Warehouses utilize manual conveyors for sorting and transporting packages, especially in areas where automation is not feasible or cost-effective.
- Retail: In retail distribution centers, manual conveyors help in sorting and processing products for shipment to various locations, enhancing order fulfillment processes.
- Agriculture: Manual conveyors are used in agricultural settings to move produce and other goods, providing a simple and efficient means of material handling.
- Construction: Construction sites benefit from manual conveyors for transporting materials such as bricks, tiles, and other building supplies, particularly in confined or temporary setups.
- Food and Beverage: The food and beverage industry uses manual conveyors in processing and packaging areas where human oversight is essential, ensuring quality control and adaptability to various products.
Manual conveyor systems offer a practical and cost-effective solution for material handling in a variety of industries. The stability and design of the conveyor frame play a crucial role in ensuring the system’s efficiency, safety, and longevity. By understanding the key differences between manual and automated conveyor systems, businesses can make informed decisions about which type of conveyor best suits their operational needs. Whether in manufacturing, warehousing, retail, agriculture, construction, or the food and beverage industry, manual conveyors provide a versatile and reliable option for enhancing productivity and workflow.
Conveyor Stands: Conveyor Frame
Role of Conveyor Stands in Providing Support and Stability to Conveyor Systems
Conveyor stands play a pivotal role in the functionality of conveyor systems by providing the essential support and stability required for efficient operation. These stands are the backbone of any conveyor setup, ensuring that the conveyor frame is held securely in place and aligned correctly. Without robust conveyor stands, the conveyor frame would lack the necessary foundation, leading to potential misalignments, inefficiencies, and safety hazards.
Conveyor stands help distribute the weight of the load evenly across the conveyor frame, reducing the strain on individual components and extending the lifespan of the system. They also minimize vibrations and movement, which can cause wear and tear on both the conveyor and the items being transported. Moreover, conveyor stands enhance the overall safety of the system by preventing tipping or collapsing, providing a stable and secure environment for material handling.
Types of Conveyor Stands
- Fixed Conveyor Stands: Fixed stands are non-adjustable and are used when the conveyor height and position remain constant. They provide a sturdy and permanent solution for conveyor systems that do not require frequent reconfiguration.
- Adjustable Conveyor Stands: Adjustable stands offer flexibility in height and angle, allowing for customization to meet specific operational needs. These stands are ideal for environments where the conveyor setup may need to be modified regularly to accommodate different products or processes.
- Mobile Conveyor Stands: Mobile stands are equipped with casters or wheels, enabling easy movement and relocation of the conveyor system. They are perfect for temporary setups, such as in assembly lines or workshops where the conveyor needs to be frequently repositioned.
Key Factors to Consider When Choosing Conveyor Stands
- Load Capacity: It is crucial to select conveyor stands that can support the maximum weight of the items being transported. Overloading stands can lead to structural failure and potential safety risks.
- Height Adjustability: Depending on the application, adjustable stands may be necessary to ensure the conveyor frame is at the optimal height for efficient operation and ergonomics.
- Material: The material of the conveyor stands should be durable and suitable for the operating environment. Common materials include steel for heavy-duty applications and aluminum for lighter loads and corrosion resistance.
- Mobility: Consider whether the stands need to be mobile or fixed. Mobile stands offer greater flexibility but may not provide the same level of stability as fixed stands.
- Compatibility: Ensure that the conveyor stands are compatible with the conveyor frame design. Mismatched components can lead to instability and operational issues.
- Environmental Conditions: Take into account the conditions of the operating environment, such as exposure to moisture, chemicals, or extreme temperatures. Stands should be resistant to these factors to ensure longevity and reliability.
Integration with Various Conveyor Frame Designs
The integration of conveyor stands with different conveyor frame designs is essential for creating a cohesive and efficient material handling system. Here are some considerations for integrating stands with various conveyor frames:
- Custom Fit: Conveyor stands should be designed or selected to match the specific dimensions and requirements of the conveyor frame. This ensures a secure fit and optimal support.
- Height and Angle Adjustments: Adjustable stands allow for the customization of the conveyor frame’s height and angle, which can be critical for optimizing the flow of materials and ergonomic working conditions.
- Mounting Options: Depending on the conveyor frame design, stands may need to be mounted using bolts, clamps, or other securing mechanisms. Proper mounting ensures stability and prevents movement during operation.
- Support for Heavy Loads: For conveyor frames designed to carry heavy loads, sturdy and reinforced stands are necessary to provide adequate support and prevent structural failure.
- Alignment: Proper alignment of the conveyor stands with the conveyor frame is crucial to ensure smooth operation. Misalignment can lead to increased wear and tear on the system and potential operational inefficiencies.
- Modularity: In modular conveyor systems, stands should be compatible with various frame sections, allowing for easy assembly, disassembly, and reconfiguration as needed.
- Ease of Maintenance: Conveyor stands should be designed to allow easy access for maintenance and adjustments. This includes features like quick-release mechanisms or accessible mounting points.
- Stability in Motion: For mobile conveyor systems, stands must provide stability during both stationary and moving operations. This may involve locking mechanisms on casters or additional supports.
- Aesthetic and Functional Design: Conveyor stands should complement the overall design of the conveyor frame, both aesthetically and functionally. A well-integrated system enhances the overall appearance and efficiency of the material handling setup.
Conveyor stands are integral to the support and stability of conveyor systems. By understanding the different types of stands, key factors to consider when choosing them, and how to integrate them with various conveyor frame designs, businesses can ensure their material handling systems operate efficiently and safely. Whether in fixed, adjustable, or mobile configurations, the right conveyor stands contribute significantly to the performance and longevity of conveyor systems.
FAQs about Conveyor Frame
A conveyor frame is the structural foundation that supports the conveyor system and its components. It holds the conveyor’s rollers, belts or chains, ensuring they maintain the proper alignment and height to facilitate efficient material transport. Typically made from metals like steel or aluminum, these frames can withstand heavy loads, resist corrosion, and provide stability to the entire system. Customizable to fit various applications, conveyor frames are critical for both the durability and efficiency of a conveyor system.
The constituent components of a conveyor include the frame, which provides the basic structure; the belt or chain, which is the medium for material transit; rollers or pulleys, which facilitate movement and guide the belt’s direction; motors and drive systems, which provide the power needed for motion; control systems, which manage speed and operational functionality; tensioning devices, which keep the belt or chain taut to avoid slipping or sagging; and load-bearing components, such as troughs or carriers, which directly support the items being transported.
Conveyor structure refers to the overall arrangement of the various components that make up a conveyor system. This structure includes the frame, supporting rollers or pulleys, belts or chains, motor, and the control system. It is designed to accommodate the transportation needs of particular materials, considering factors like load weight, distance to be covered, environmental conditions, and the required transportation speed. The structure’s durability and reliability are crucial for maintaining continuous workflow, safety, and efficiency in industrial settings.
In the video game Space Engineers, a conveyor frame is a block used to build intricate connection systems between machines, storage units, and other blocks that require transferring items. They enable players to link various components of their space stations or ships, facilitating the automatic movement of ores, ingots, components, and tools, among others, without manual handling. Conveyor frames play a pivotal role in automating workflows and ensuring resources are efficiently distributed across players’ creations, essential for survival and progression within the game’s engineering and construction-focused environment.
Last Updated on June 7, 2024 by Jordan Smith
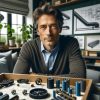
Jordan Smith, a seasoned professional with over 20 years of experience in the conveyor system industry. Jordan’s expertise lies in providing comprehensive solutions for conveyor rollers, belts, and accessories, catering to a wide range of industrial needs. From initial design and configuration to installation and meticulous troubleshooting, Jordan is adept at handling all aspects of conveyor system management. Whether you’re looking to upgrade your production line with efficient conveyor belts, require custom conveyor rollers for specific operations, or need expert advice on selecting the right conveyor accessories for your facility, Jordan is your reliable consultant. For any inquiries or assistance with conveyor system optimization, Jordan is available to share his wealth of knowledge and experience. Feel free to reach out at any time for professional guidance on all matters related to conveyor rollers, belts, and accessories.