Tail Drum Conveyor and Conveyor Head Drum Overview
A conveyor head drum is a critical component in conveyor systems, responsible for driving the conveyor belt and ensuring smooth and efficient material movement. Located at the discharge end of the conveyor, the conveyor head drum plays a vital role in maintaining the tension and alignment of the belt. Its importance in material handling cannot be overstated, as it directly impacts the system’s operational efficiency and reliability. In industrial processes, the conveyor head drum facilitates the seamless transportation of goods, enhancing productivity and reducing downtime. Understanding its function and significance is essential for optimizing conveyor system performance.
Various Conveyor Head Drum Sizes
The conveyor head drum is a critical component in any conveyor system, and selecting the appropriate size is essential for ensuring optimal performance and longevity of the system. Conveyor head drums come in various sizes, each designed to meet specific operational requirements. The size of the head drum directly affects the conveyor belt’s tension, speed, and the overall efficiency of the conveyor system.
Standard Sizes
Conveyor head drums are available in a range of standard sizes. The diameter and face width are the two main dimensions to consider:
- Diameter: The diameter of the conveyor head drum can vary significantly, typically ranging from 6 inches (150 mm) to 48 inches (1200 mm) or more. The choice of diameter depends on the conveyor system’s design and the type of material being transported. Larger diameters are generally used for heavy-duty applications and long conveyor belts, as they provide greater surface area for driving the belt and handling higher tension.
- Face Width: The face width, or the width of the drum that comes into contact with the conveyor belt, also varies. It ranges from 12 inches (300 mm) to over 72 inches (1800 mm). The face width must match the width of the conveyor belt to ensure proper alignment and prevent belt slippage or misalignment.
Custom Sizes
In addition to standard sizes, conveyor head drums can be custom-made to fit specific applications. Custom sizes are often required for unique conveyor system designs or for handling specific materials that have unusual dimensions or weight characteristics. Customization can involve altering the diameter, face width, or even the material and construction of the drum to meet particular needs.
Factors Influencing Size Selection
When choosing the right size for a conveyor head drum, several factors must be considered:
- Material Type and Load: The type of material being transported and its weight are crucial in determining the appropriate size of the head drum. Heavy materials require larger drums to handle the increased load and tension.
- Conveyor Length and Speed: The length of the conveyor system and the desired speed of operation influence the size of the head drum. Longer conveyors and higher speeds typically require larger drums to maintain efficiency and reduce wear.
- Environmental Conditions: The operating environment, including temperature, humidity, and exposure to corrosive substances, can impact the choice of drum size and material. For harsh environments, drums made from corrosion-resistant materials and with appropriate size specifications are essential.
- Belt Specifications: The specifications of the conveyor belt, including its width, thickness, and tensile strength, must align with the size of the head drum. Ensuring compatibility between the belt and drum is critical for smooth operation and longevity.
- System Design and Layout: The overall design and layout of the conveyor system, including the space available for the head drum and the configuration of other components, will also influence the selection of drum size.
Selecting the appropriate size for a conveyor head drum involves considering the material type and load, conveyor length and speed, environmental conditions, belt specifications, and system design. By carefully evaluating these factors, businesses can ensure that their conveyor systems operate efficiently and reliably.
Steps for Conveyor Head Drum Replacement
Replacing a conveyor head drum is a significant maintenance task that requires careful planning and execution. Proper replacement ensures the continued efficiency and longevity of the conveyor system. The following steps provide a detailed guide for replacing a conveyor head drum:
Step 1: Preparation and Safety Measures
Before beginning the replacement process, it is essential to prepare adequately and implement safety measures:
- Shutdown the System: Ensure the conveyor system is completely shut down and isolated from power sources. Lockout/tagout procedures should be followed to prevent accidental startup during the replacement process.
- Safety Equipment: Equip all personnel involved in the replacement with appropriate personal protective equipment (PPE), including gloves, safety glasses, hard hats, and steel-toed boots.
- Gather Tools and Materials: Collect all necessary tools and materials, including wrenches, alignment tools, lifting equipment, new head drum, and any replacement components such as bearings or shafts.
Step 2: Remove the Conveyor Belt
The first major task in replacing the head drum is to remove the conveyor belt:
- Release Belt Tension: Loosen the tensioning devices to relieve tension on the conveyor belt. This can be done using the appropriate tools to adjust the take-up units or tensioning mechanisms.
- Disconnect the Belt: Carefully disconnect the conveyor belt from the head drum and other pulleys. This may involve unfastening belt splices or disconnecting mechanical fasteners.
- Support the Belt: Use temporary supports or stands to hold the conveyor belt in place once it is disconnected from the head drum. This prevents the belt from sagging or getting damaged during the replacement process.
Step 3: Remove the Existing Head Drum
With the belt safely out of the way, proceed to remove the existing head drum:
- Disconnect Drive Mechanism: Detach the drive motor, gearbox, and any other components connected to the head drum. This may involve removing belts, chains, or couplings.
- Remove Mounting Bolts: Use wrenches to remove the bolts and nuts securing the head drum to its mounting brackets or frame. Ensure all fasteners are carefully collected and stored for reuse if applicable.
- Lift the Head Drum: Employ lifting equipment such as a hoist or crane to lift the head drum out of its position. Take care to balance the drum to avoid accidents or damage to adjacent components.
Step 4: Install the New Head Drum
With the old head drum removed, it’s time to install the new one:
- Position the New Drum: Use lifting equipment to position the new head drum in place. Ensure it is properly aligned with the conveyor frame and other components.
- Secure the Drum: Reattach the mounting bolts and nuts to secure the new head drum to its brackets or frame. Use torque wrenches to apply the correct amount of torque to each fastener.
- Reconnect Drive Mechanism: Reattach the drive motor, gearbox, and any other components to the new head drum. Ensure all connections are secure and properly aligned.
Step 5: Reinstall the Conveyor Belt
Once the new head drum is securely in place, reinstall the conveyor belt:
- Align the Belt: Carefully align the conveyor belt with the new head drum and other pulleys. Ensure the belt runs straight and true along its path.
- Reconnect the Belt: Reconnect the conveyor belt by refastening belt splices or mechanical fasteners. Ensure the belt ends are securely joined.
- Tension the Belt: Adjust the tensioning devices to apply the correct amount of tension to the conveyor belt. Proper tension is crucial for preventing slippage and ensuring smooth operation.
Step 6: Final Checks and Testing
Before putting the conveyor system back into operation, perform final checks and testing:
- Inspect All Components: Thoroughly inspect all components to ensure they are correctly installed and secure. Check for any loose bolts, misalignments, or potential issues.
- Test Run: Conduct a test run of the conveyor system to verify that the new head drum operates correctly. Observe the belt movement, listen for unusual noises, and check for proper tension and alignment.
- Adjustments: Make any necessary adjustments based on the test run observations. Ensure the conveyor system operates smoothly and efficiently before resuming full operation.
Replacing a conveyor head drum involves careful preparation, removal of the existing drum, installation of the new drum, and thorough testing. Following these steps ensures a smooth and efficient replacement process, minimizing downtime and maintaining the conveyor system’s performance.
Conveyor Head Drum: Functions of a Conveyor Drum Pulley
A conveyor drum pulley, also known as a head drum, is a vital component in conveyor systems. It serves several crucial functions that contribute to the movement and efficiency of the conveyor system. Understanding these functions helps in appreciating the importance of the drum pulley in industrial applications.
Driving the Conveyor Belt
The primary function of a conveyor drum pulley is to drive the conveyor belt. Positioned at the discharge end of the conveyor system, the drum pulley is connected to a motor that provides the necessary rotational force. This force is transferred to the conveyor belt, causing it to move and transport materials along the conveyor path. The drum pulley’s smooth surface ensures effective contact with the belt, reducing slippage and maintaining consistent movement.
Maintaining Belt Tension
Another critical function of the conveyor drum pulley is to maintain proper tension on the conveyor belt. Proper belt tension is essential for preventing slippage and ensuring efficient material transport. The drum pulley helps to keep the belt taut, allowing it to grip the pulley surface effectively and move smoothly. Tensioning devices, such as take-up units, work in conjunction with the drum pulley to achieve the desired belt tension.
Guiding the Conveyor Belt
The conveyor drum pulley also plays a crucial role in guiding the conveyor belt along its intended path. Proper alignment of the belt is essential for preventing misalignment, which can lead to uneven wear, increased friction, and potential damage to the belt and other components. The drum pulley helps to guide the belt and keep it centered on the conveyor frame, ensuring smooth and efficient operation.
Providing Traction and Reducing Wear
The surface of the conveyor drum pulley is often coated with lagging material, such as rubber or ceramic, to enhance traction and reduce wear. Lagging provides a high-friction surface that improves the drum pulley’s grip on the conveyor belt, reducing the likelihood of slippage. Additionally, lagging helps to absorb the impact and wear that would otherwise affect the metal surface of the pulley, extending its lifespan and maintaining optimal performance.
Supporting the Conveyor System
The conveyor drum pulley provides structural support to the conveyor system.
It bears the load of the materials being transported and helps to distribute this load evenly across the conveyor belt. The pulley’s robust construction and precise alignment ensure that it can handle the operational stresses and maintain the conveyor system’s stability and efficiency.
Facilitating Material Discharge
Positioned at the discharge end of the conveyor system, the drum pulley facilitates the smooth discharge of materials. As the conveyor belt reaches the drum pulley, it transitions from a horizontal to a more inclined or vertical position, allowing materials to be effectively offloaded. The drum pulley’s design and surface characteristics ensure that materials are discharged efficiently, minimizing spillage and optimizing the overall material handling process.
Ensuring Smooth Operation
Overall, the conveyor drum pulley ensures the smooth operation of the conveyor system. By driving the conveyor belt, maintaining tension, guiding the belt, providing traction, supporting the system, and facilitating material discharge, the drum pulley plays a central role in achieving efficient and reliable material transport. Regular maintenance and proper selection of the drum pulley are essential for maintaining the conveyor system’s performance and minimizing downtime.
The conveyor drum pulley is a critical component that drives the conveyor belt, maintains tension, guides the belt, provides traction, supports the system, and facilitates material discharge. Understanding its functions helps in appreciating its importance in conveyor systems and highlights the need for regular maintenance and proper selection to ensure optimal performance.
Conveyor Head Drum: Overview of Tail Drum Conveyor
In the realm of conveyor systems, understanding the roles of various components is crucial for maintaining efficiency and reliability. The tail drum conveyor, along with the conveyor head drum, plays a significant part in the overall functionality of the system. This section provides a detailed overview of the tail drum conveyor, highlighting its role and importance in conjunction with the conveyor head drum.
What is a Tail Drum Conveyor?
The tail drum conveyor, often referred to as the tail pulley, is located at the opposite end of the conveyor system from the conveyor head drum. Its primary function is to provide tension to the conveyor belt, ensuring it remains taut and aligned during operation. The tail drum conveyor is a non-powered pulley, meaning it is not driven by a motor but rotates freely as the belt moves over it.
Role in Conveyor Systems
The tail drum conveyor plays several critical roles within the overall conveyor system:
- Tensioning the Belt: The tail drum conveyor helps maintain the necessary tension in the conveyor belt. Proper tension is essential to prevent slippage, ensure accurate tracking, and reduce wear on the belt and other components.
- Guiding the Belt: It aids in guiding the conveyor belt back to the head drum, ensuring the belt runs smoothly and stays aligned. This reduces the risk of the belt drifting off course and causing operational issues.
- Supporting the Belt: The tail drum conveyor supports the belt and the materials being transported, ensuring a smooth and consistent movement. This support helps in minimizing material spillage and maintaining the efficiency of the conveyor system.
Interaction with Conveyor Head Drum
The tail drum conveyor works in tandem with the conveyor head drum to form a complete and efficient conveyor system. While the conveyor head drum drives the belt and provides the necessary force to move materials, the tail drum conveyor ensures the belt remains taut and aligned. This interplay between the two drums is crucial for the smooth operation of the conveyor system.
Belt Tension and Alignment: The conveyor head drum and tail drum conveyor must be properly aligned and tensioned to ensure optimal performance. If the belt is too loose, it can slip on the head drum, reducing efficiency and causing potential damage. Conversely, if the belt is too tight, it can cause excessive wear on the components and increase energy consumption.
Load Distribution: The tail drum conveyor helps distribute the load evenly across the conveyor system. By supporting the belt at the return end, it ensures that the load is carried smoothly from the head drum to the tail drum, minimizing the risk of overloading and potential damage.
Operational Efficiency: The interaction between the conveyor head drum and tail drum conveyor is essential for maintaining operational efficiency. A well-balanced system reduces downtime, minimizes maintenance requirements, and enhances the overall productivity of the material handling process.
Types of Tail Drum Conveyors
Tail drum conveyors come in various types and designs, each suited to specific applications and operational requirements. Some common types include:
- Standard Tail Drum Conveyors: These are the most commonly used type, designed for general-purpose applications. They provide adequate tension and alignment for most conveyor systems and are suitable for transporting a wide range of materials.
- Winged Tail Drum Conveyors: Winged tail drum conveyors feature a unique design with wings or fins that help shed material buildup. This design is particularly useful in applications where the conveyor belt is exposed to sticky or abrasive materials, as it prevents material buildup and reduces maintenance requirements.
- Lagged Tail Drum Conveyors: Lagged tail drum conveyors have a rubber or polyurethane coating that provides additional grip and reduces slippage. This type is ideal for applications where the belt needs extra traction to prevent slipping, such as in wet or oily environments.
Maintenance and Inspection
Regular maintenance and inspection of the tail drum conveyor are crucial for ensuring its optimal performance and longevity. Key maintenance tasks include:
- Checking Tension: Regularly check the tension of the conveyor belt to ensure it is within the recommended range. Adjust the tension as needed to prevent slippage and maintain alignment.
- Inspecting Alignment: Inspect the alignment of the tail drum conveyor and make any necessary adjustments to ensure the belt runs smoothly and stays on track.
- Lubricating Bearings: Ensure the bearings of the tail drum conveyor are properly lubricated to reduce friction and prevent wear. Regular lubrication helps extend the lifespan of the bearings and ensures smooth operation.
- Cleaning the Drum: Keep the tail drum conveyor clean and free from material buildup. Regular cleaning prevents material accumulation, which can cause the belt to slip or become misaligned.
The tail drum conveyor is an essential component of conveyor systems, working in conjunction with the conveyor head drum to ensure efficient and reliable material handling. By maintaining proper tension, guiding the belt, and supporting the load, the tail drum conveyor plays a critical role in the overall functionality of the conveyor system. Regular maintenance and inspection are key to ensuring its optimal performance and longevity, contributing to the smooth and efficient operation of the material handling process.
Conveyor Head Drum: Importance of Conveyor Head Pulley
The conveyor head pulley, also known as the drive pulley, is a vital component in conveyor systems. It is responsible for driving the conveyor belt and ensuring the smooth and efficient movement of materials. This section highlights the importance of the conveyor head pulley and its impact on the performance and reliability of conveyor operations.
What is a Conveyor Head Pulley?
The conveyor head pulley is the powered pulley located at the discharge end of the conveyor system. It is connected to a motor, which drives the pulley and, in turn, moves the conveyor belt. The conveyor head pulley is typically larger in diameter compared to other pulleys in the system, providing the necessary torque to drive the belt and transport materials efficiently.
Role in Conveyor Systems
The conveyor head pulley plays several critical roles within conveyor systems:
- Driving the Belt: The primary function of the conveyor head pulley is to drive the conveyor belt. The motor connected to the pulley provides the necessary power to move the belt, enabling the transportation of materials from one point to another.
- Providing Traction: The conveyor head pulley provides the necessary traction to move the belt and the materials on it. The surface of the pulley is often coated with rubber or other high-friction materials to enhance grip and reduce slippage.
- Ensuring Belt Alignment: Proper alignment of the conveyor belt is essential for smooth operation. The conveyor head pulley helps maintain the alignment of the belt, preventing it from drifting off course and causing operational issues.
Impact on Performance and Reliability
The conveyor head pulley has a significant impact on the overall performance and reliability of conveyor operations. Its role in driving the belt and maintaining alignment directly influences the efficiency and productivity of the material handling process.
Efficient Material Movement: A well-designed and properly maintained conveyor head pulley ensures efficient material movement. By providing the necessary power and traction, it enables the conveyor system to transport materials smoothly and efficiently, reducing downtime and increasing productivity.
Reduced Slippage: Slippage is a common issue in conveyor systems, leading to reduced efficiency and potential damage to the belt and other components. The conveyor head pulley, with its high-friction surface, minimizes slippage, ensuring reliable and consistent operation.
Enhanced Durability: The durability of the conveyor head pulley is crucial for the longevity of the conveyor system. A robust and well-maintained pulley can withstand the stresses of continuous operation, reducing the need for frequent replacements and maintenance.
Improved Safety: Safety is a critical concern in conveyor operations. The conveyor head pulley plays a vital role in maintaining the stability and alignment of the belt, reducing the risk of accidents and ensuring a safe working environment.
Types of Conveyor Head Pulleys
Conveyor head pulleys come in various types and designs, each suited to specific applications and operational requirements. Some common types include:
- Standard Head Pulleys: These are the most commonly used type, designed for general-purpose applications. They provide adequate traction and alignment for most conveyor systems and are suitable for transporting a wide range of materials.
- Winged Head Pulleys: Winged head pulleys feature a unique design with wings or fins that help shed material buildup. This design is particularly useful in applications where the conveyor belt is exposed to sticky or abrasive materials, as it prevents material buildup and reduces maintenance requirements.
- Lagged Head Pulleys: Lagged head pulleys have a rubber or polyurethane coating that provides additional grip and reduces slippage. This type is ideal for applications where the belt needs extra traction to prevent slipping, such as in wet or oily environments.
Maintenance and Inspection
Regular maintenance and inspection of the conveyor head pulley are crucial for ensuring its optimal performance and longevity. Key maintenance tasks include:
- Checking Alignment: Regularly check the alignment of the conveyor head pulley and make any necessary adjustments to ensure the belt runs smoothly and stays on track.
- Inspecting Surface: Inspect the surface of the pulley for wear and damage. Replace the pulley or apply a new coating if necessary to maintain optimal traction.
- Lubricating Bearings: Ensure the bearings of the conveyor head pulley are properly lubricated to reduce friction and prevent wear. Regular lubrication helps extend the lifespan of the bearings and ensures smooth operation.
- Cleaning the Pulley: Keep the conveyor head pulley clean and free from material buildup. Regular cleaning prevents material accumulation, which can cause the belt to slip or become misaligned.
The conveyor head pulley is a critical component in conveyor systems, playing a vital role in driving the belt and ensuring efficient and reliable material movement. Its impact on performance, durability, and safety underscores the importance of proper maintenance and inspection. By understanding the functions and importance of the conveyor head pulley, businesses can optimize their conveyor operations, enhancing productivity and reducing downtime.
Conveyor Head Drum: Features of Conveyor Head and Tail Pulley
Conveyor systems rely on a combination of components to function efficiently, with the conveyor head and tail pulleys being two of the most crucial elements. These pulleys play significant roles in driving and supporting the conveyor belt, ensuring smooth and reliable material handling. This section discusses the key features of both conveyor head and tail pulleys and how these features enhance the efficiency and longevity of the conveyor system.
Key Features of Conveyor Head Pulley
The conveyor head pulley, located at the discharge end of the conveyor, is responsible for driving the belt and moving materials. Some of its key features include:
- High-Traction Surface: The surface of the conveyor head pulley is often coated with high-friction materials such as rubber or polyurethane. This coating provides the necessary grip to drive the belt, reducing slippage and ensuring consistent material movement.
- Durable Construction: Conveyor head pulleys are constructed from robust materials like steel or stainless steel to withstand the stresses of continuous operation. The durable construction ensures long service life and reduces the need for frequent replacements.
- Lagging Options: Lagging refers to the addition of a layer of material to the surface of the pulley to increase friction and reduce wear. Various lagging options are available, including ceramic, rubber, and polyurethane, each offering specific benefits for different applications.
- Bearing Support: High-quality bearings are essential for the smooth rotation of the conveyor head pulley. These bearings are designed to handle high loads and reduce friction, enhancing the pulley’s efficiency and lifespan.
- Dynamic Balancing: To ensure smooth operation, conveyor head pulleys undergo dynamic balancing. This process involves adjusting the weight distribution of the pulley to minimize vibrations and reduce wear on the belt and other components.
Key Features of Tail Drum Conveyor
The tail drum conveyor, located at the return end of the conveyor system, provides tension and alignment for the belt. Its key features include:
- Non-Powered Operation: Unlike the conveyor head pulley, the tail drum conveyor is not powered and rotates freely. Its primary function is to provide tension and guide the belt back to the head pulley.
- Adjustable Positioning: The tail drum conveyor often features adjustable positioning mechanisms that allow operators to fine-tune the belt tension and alignment. This adjustability is crucial for maintaining optimal belt performance.
- Winged Design Options: Some tail drum conveyors feature a winged design with fins or wings that help shed material buildup. This design is particularly beneficial in applications involving sticky or abrasive materials, as it prevents accumulation and reduces maintenance.
- Robust Construction: Like the head pulley, the tail drum conveyor is constructed from durable materials to withstand the demands of the conveyor system. The robust construction ensures longevity and reliable performance.
- Bearing Support: High-quality bearings are also essential for the tail drum conveyor. These bearings support the free rotation of the pulley, reducing friction and wear on the belt.
Enhancing Efficiency and Longevity
The features of both conveyor head and tail pulleys contribute significantly to the efficiency and longevity of the conveyor system. By understanding these features, businesses can optimize their conveyor operations and achieve better performance.
Improved Traction and Reduced Slippage: The high-traction surfaces and lagging options available for conveyor head pulleys ensure that the belt moves smoothly without slipping. This improved traction enhances the efficiency of material movement and reduces the risk of belt damage.
Durability and Reduced Maintenance: The durable construction of both head and tail pulleys ensures that they can withstand the rigors of continuous operation. This durability reduces the frequency of replacements and maintenance, leading to lower operational costs.
Optimal Belt Tension and Alignment: The adjustable positioning and robust design of the tail drum conveyor help maintain optimal belt tension and alignment. Proper tension and alignment are crucial for preventing belt drift, reducing wear, and ensuring smooth operation.
Enhanced Safety: The features of both pulleys contribute to a safer working environment. By maintaining proper belt tension and alignment, the risk of accidents and operational disruptions is minimized, ensuring a safer and more reliable conveyor system.
The conveyor head drum and tail pulleys are integral components of conveyor systems, each playing a crucial role in driving, tensioning, and aligning the conveyor belt. Their key features, including high-traction surfaces, durable construction, and adjustable positioning, enhance the efficiency and longevity of the conveyor system. By understanding and leveraging these features, businesses can optimize their material handling processes, improving productivity and reducing downtime. Proper maintenance and inspection of these pulleys are essential for ensuring their continued performance and reliability, contributing to the overall success of conveyor operations.
FAQs about Conveyor Head Drum
A head drum conveyor refers to the primary pulley at the discharge end of a conveyor system. The head drum, also known as the head pulley, is responsible for driving the conveyor belt and is typically connected to a motor that provides the necessary power for the belt’s movement. The head drum is a critical component in the conveyor system as it is where the belt transitions from carrying material to discharging it. The design and material of the head drum are crucial for ensuring efficient operation, minimizing wear, and extending the lifespan of both the belt and the drum itself.
The head of a conveyor is the end part of the conveyor system where the head pulley or drum is located. This is the discharge point where materials being transported by the conveyor belt are offloaded. The head section is equipped with the drive motor and mechanisms that power the conveyor belt. The head is designed to handle the highest tension and load within the system, as it drives the entire belt’s movement. Proper maintenance and alignment of the head components are essential for the smooth operation and efficiency of the conveyor system.
The head pulley, also known as the drive pulley, serves a critical function in a conveyor system. Its primary purpose is to drive the conveyor belt, ensuring the continuous movement of materials along the belt. Positioned at the conveyor’s discharge end, the head pulley is connected to the motor, which provides the rotational force needed to move the belt. The head pulley also plays a significant role in maintaining the belt’s tension and alignment, which is vital for preventing slippage and ensuring efficient operation. Additionally, it helps guide the belt back into the return path after discharging the materials.
A drum pulley and a wing pulley are both types of pulleys used in conveyor systems, but they serve different purposes and have distinct designs.
Drum Pulley: A drum pulley has a solid cylindrical shape and is used primarily as a head or tail pulley in conveyor systems. Its smooth surface provides a continuous contact area with the conveyor belt, ensuring effective drive and minimal belt wear. Drum pulleys are ideal for applications requiring high tension and consistent performance.
Wing Pulley: A wing pulley, on the other hand, features a unique design with wings or fins extending from the central hub to the outer rim. This design helps in shedding materials that might accumulate on the pulley, which can be particularly useful in applications with bulk, sticky, or abrasive materials. Wing pulleys are often used in the tail or bend sections of conveyor systems where material buildup is a concern.
Both types of pulleys are crucial for the efficient operation of conveyor systems, with drum pulleys providing driving force and stability, while wing pulleys help in maintaining cleanliness and preventing material buildup.
Last Updated on August 15, 2024 by Jordan Smith
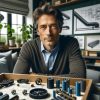
Jordan Smith, a seasoned professional with over 20 years of experience in the conveyor system industry. Jordan’s expertise lies in providing comprehensive solutions for conveyor rollers, belts, and accessories, catering to a wide range of industrial needs. From initial design and configuration to installation and meticulous troubleshooting, Jordan is adept at handling all aspects of conveyor system management. Whether you’re looking to upgrade your production line with efficient conveyor belts, require custom conveyor rollers for specific operations, or need expert advice on selecting the right conveyor accessories for your facility, Jordan is your reliable consultant. For any inquiries or assistance with conveyor system optimization, Jordan is available to share his wealth of knowledge and experience. Feel free to reach out at any time for professional guidance on all matters related to conveyor rollers, belts, and accessories.