Essential Guide to Conveyor Head Pulley Drawing Techniques
When creating a conveyor head pulley drawing, it is crucial to determine the appropriate diameter for optimal performance. Several factors affect the diameter of a head pulley, including the belt tension, speed, load capacity, and the material being transported. The diameter must be calculated accurately to ensure efficient operation and reduce wear and tear on the conveyor belt. To calculate the appropriate diameter, engineers must consider the system’s overall design and operational requirements. Precise conveyor head pulley drawing helps in achieving the correct dimensions, which in turn enhances the reliability and efficiency of the conveyor system. By factoring in these variables, businesses can ensure their conveyor systems operate smoothly and effectively.
Optimizing Conveyor Head Pulley Drawing with Proper Pulley Design
The design and implementation of pulleys, particularly head pulleys, play a crucial role in the efficiency and reliability of conveyor systems. A well-designed pulley ensures smooth operation, reduces maintenance needs, and extends the lifespan of the system. This section will discuss how to enhance conveyor performance with well-designed pulleys and provide maintenance tips for ensuring the longevity and reliability of these components. The importance of detailed and accurate conveyor head pulley drawings will also be highlighted.
Enhancing Conveyor Performance with Well-Designed Pulleys
Proper pulley design is fundamental to the optimal functioning of conveyor systems. A comprehensive conveyor head pulley drawing is essential for visualizing and planning the pulley’s integration into the system. Here are some key considerations and benefits of well-designed pulleys:
Accurate Specifications and Dimensions: The conveyor head pulley drawing should include precise specifications and dimensions, ensuring the pulley fits perfectly within the conveyor system. This accuracy is crucial for preventing misalignment and ensuring smooth belt operation. Dimensions such as the pulley diameter, face width, and shaft size must be carefully calculated based on the specific requirements of the conveyor system.
Material Selection: The materials used in the construction of the head pulley significantly impact its performance and durability. Steel is commonly used for its strength and durability, but other materials such as stainless steel or composites may be used depending on the operating environment. The drawing should specify the materials used for the shell, shaft, and lagging to ensure the pulley can withstand the operational stresses and environmental conditions.
Lagging Design: Lagging, or the covering on the pulley’s surface, enhances the friction between the pulley and the conveyor belt, reducing slippage. The conveyor head pulley drawing should detail the type and thickness of the lagging material. Common materials include rubber and ceramic, each offering different levels of friction and durability. Proper lagging design ensures efficient power transmission and reduces wear on the belt.
Shaft and Bearing Design: The design of the shaft and bearings is critical for the smooth rotation of the pulley. The drawing should include detailed specifications for the shaft diameter, length, and material, as well as the type and placement of bearings. High-quality bearings reduce friction and wear, ensuring reliable pulley operation. The design should also account for the ease of bearing maintenance and replacement.
Alignment and Mounting: Ensuring proper alignment and secure mounting of the head pulley is essential for preventing belt misalignment and operational disruptions. The conveyor head pulley drawing should illustrate the correct alignment of the pulley within the system and the mounting methods used. This may include details on the bearing housings, mounting brackets, and adjustment mechanisms to maintain proper tension and alignment.
Load Distribution: The design should ensure even load distribution across the pulley to prevent localized stress and wear. The drawing should indicate how the load will be distributed and any reinforcements needed to handle high-stress areas. This consideration is crucial for extending the life of both the pulley and the conveyor belt.
Maintenance Tips for Longevity and Reliability of Pulleys
Regular maintenance is vital for ensuring the longevity and reliability of conveyor pulleys. Here are some essential maintenance tips:
Regular Inspections: Conduct regular inspections of the head pulley and related components to identify signs of wear, damage, or misalignment. Inspections should include checking the condition of the lagging, bearings, and shaft, as well as the alignment of the pulley. Early detection of issues can prevent more significant problems and reduce downtime.
Lubrication: Proper lubrication of bearings and other moving parts is crucial for reducing friction and wear. Follow the manufacturer’s recommendations for lubrication intervals and use the specified lubricants. Over-lubrication or under-lubrication can both cause issues, so maintaining the correct balance is essential.
Alignment Adjustments: Periodically check and adjust the alignment of the head pulley to ensure it remains properly aligned with the conveyor belt. Misalignment can cause uneven wear on the belt and pulley, leading to increased maintenance needs and reduced system efficiency. Use the conveyor head pulley drawing as a reference for correct alignment procedures.
Lagging Maintenance: Inspect the lagging for signs of wear or damage and replace it as needed. Worn or damaged lagging can reduce friction and lead to belt slippage. Regularly cleaning the lagging can also help maintain its effectiveness.
Bearing Replacement: Bearings are critical components that require regular attention. Check for signs of bearing wear or failure, such as unusual noises or vibrations. Replace bearings that show signs of wear to prevent more significant issues. Ensure that replacement bearings match the specifications detailed in the conveyor head pulley drawing.
Shaft Condition: Inspect the conveyor roller shaft for signs of wear or damage, such as scoring or bending. A damaged shaft can cause misalignment and increase wear on other components. Replace or repair the shaft as needed to maintain optimal performance.
Documentation and Record Keeping: Maintain detailed records of all inspections, maintenance activities, and replacements. This documentation can help track the condition of the head pulley and identify patterns or recurring issues. Use the conveyor head pulley drawing to reference specific components and ensure accurate record-keeping.
What is Conveyor Head Pulley Drawing
Designing Effective Conveyor Head Pulleys
In the world of material handling, the design of conveyor head pulleys is critical to the efficient and reliable operation of conveyor systems. A well-designed head pulley ensures smooth and consistent belt movement, reduces wear and tear, and minimizes maintenance requirements. This section provides insights into the best practices for designing head pulleys and explores common challenges and solutions in pulley design.
Best Practices for Designing Head Pulleys
Creating an effective conveyor head pulley drawing requires attention to several key factors. Here are some best practices to ensure the design meets operational needs and industry standards:
1. Material Selection:
Choosing the right material for the head pulley is essential for durability and performance. Common materials include steel, stainless steel, and aluminum. Steel is widely used for its strength and cost-effectiveness, while stainless steel offers superior corrosion resistance, making it ideal for harsh environments. Aluminum is lightweight and resistant to corrosion, suitable for specific applications where weight reduction is crucial.
2. Pulley Diameter:
The diameter of the head pulley affects the belt tension and the overall performance of the conveyor system. Larger diameters reduce the bending stress on the belt, extending its lifespan. However, the diameter must be chosen based on the conveyor’s load capacity and the belt’s specifications to ensure optimal performance.
3. Surface Finish:
The surface finish of the head pulley plays a significant role in preventing belt slippage. Smooth finishes reduce wear on the belt but may require additional measures, such as lagging, to enhance grip. Lagging materials, such as rubber or ceramic, are applied to the pulley surface to increase friction and improve traction.
4. Balance and Alignment:
Proper balance and alignment of the head pulley are crucial for minimizing vibration and ensuring smooth belt operation. Unbalanced pulleys can cause excessive wear on the bearings and the belt, leading to premature failures. Precision manufacturing and regular maintenance checks are necessary to maintain proper balance and alignment.
5. Bearing Selection:
Selecting the right bearings for the head pulley is essential for supporting the loads and ensuring reliable operation. Bearings must be chosen based on the load, speed, and environmental conditions. Sealed bearings are often preferred in dusty or wet environments to prevent contamination and extend bearing life.
6. Shaft Design:
The shaft of the head pulley must be designed to withstand the forces exerted by the belt and the conveyed materials. It should be strong enough to support the pulley and the bearings while minimizing deflection. Proper shaft design also ensures that the pulley can handle the start-stop cycles and varying loads without failure.
7. Lagging Application:
Lagging is applied to the head pulley to enhance the friction between the pulley and the conveyor belt. This application prevents slippage, especially in wet or dusty conditions. Rubber lagging is commonly used for general purposes, while ceramic lagging provides higher abrasion resistance and is suitable for heavy-duty applications.
8. Integration with Conveyor System:
The head pulley must be designed to integrate seamlessly with the conveyor system. This includes considering the placement of the pulley, the type of belt used, and the overall conveyor layout. Proper integration ensures that the conveyor system operates efficiently and reduces the risk of mechanical issues.
Common Challenges and Solutions in Pulley Design
Designing conveyor head pulleys comes with its set of challenges. Addressing these challenges effectively ensures the reliability and efficiency of the conveyor system.
1. Preventing Belt Slippage:
One of the most common challenges in pulley design is preventing belt slippage. Slippage can lead to material spillage, reduced efficiency, and increased wear on the belt and pulley. Applying lagging to the head pulley and ensuring proper tensioning of the conveyor belt are effective solutions to this issue. Regular inspections and maintenance also help in identifying and addressing slippage problems early.
2. Managing Wear and Tear:
Head pulleys are subjected to continuous wear and tear due to the constant movement of the conveyor belt and the materials being transported. Selecting durable materials, applying appropriate lagging, and using high-quality bearings can significantly reduce wear and extend the life of the head pulley. Implementing a regular maintenance schedule to inspect and replace worn components is also essential.
3. Ensuring Proper Alignment:
Misalignment of the head pulley can cause belt tracking issues, leading to uneven wear and potential damage to the conveyor system. Precision manufacturing, careful installation, and regular alignment checks are necessary to ensure proper alignment. Using adjustable take-up mechanisms can also help maintain alignment under varying load conditions.
4. Handling High Loads:
In applications involving heavy loads, the head pulley must be designed to handle the increased stress and force. This requires selecting materials and bearings that can support the load and designing the shaft to minimize deflection. Using reinforced pulleys and ensuring proper load distribution across the conveyor belt can also help in managing high loads.
5. Dealing with Environmental Conditions:
Conveyor systems often operate in challenging environmental conditions, such as extreme temperatures, humidity, or exposure to chemicals. Selecting corrosion-resistant materials, using sealed bearings, and applying protective coatings to the head pulley can help mitigate the effects of harsh environments. Designing the pulley to withstand these conditions ensures reliable operation and reduces the risk of corrosion-related failures.
6. Balancing Cost and Performance:
Achieving a balance between cost and performance is a common challenge in pulley design. While high-quality materials and precision manufacturing increase the initial cost, they also enhance the reliability and lifespan of the pulley. Evaluating the total cost of ownership, including maintenance and replacement costs, helps in making informed decisions that balance cost and performance.
7. Adapting to Conveyor System Changes:
Conveyor systems may undergo changes in their operational parameters, such as increased load capacity or changes in the type of materials being transported. Designing head pulleys with flexibility in mind allows for easy adaptation to these changes. Modular designs and adjustable components can help accommodate future modifications without requiring significant redesigns.
8. Ensuring Safety:
Safety is a paramount concern in the design of head pulleys. Ensuring that the pulley is designed to handle the expected loads and operating conditions reduces the risk of mechanical failures and accidents. Incorporating safety features, such as guards and emergency stop mechanisms, enhances the overall safety of the conveyor system.
9. Addressing Space Constraints:
Space constraints can pose challenges in the design and installation of head pulleys. Compact designs that maximize the use of available space while maintaining performance and reliability are essential. Collaborating with conveyor system designers to optimize the layout and placement of the head pulley ensures efficient use of space.
How about Conveyor Head Pulley Drawing
In the design and implementation of conveyor systems, accurately calculating the diameter of conveyor pulleys is essential for ensuring efficient operation and longevity of the equipment. The conveyor head pulley drawing is a crucial tool that provides detailed specifications and helps in visualizing the correct dimensions and placements. This section will explore the key factors in calculating conveyor pulley diameter and provide a step-by-step guide to ensure accurate calculations.
Key Factors in Calculating Conveyor Pulley Diameter
When calculating the diameter of a conveyor pulley, several factors need to be taken into account to ensure that the pulley will operate efficiently and effectively. These factors include:
Belt Width and Type: The width and type of the conveyor belt play a significant role in determining the pulley diameter. Wider belts typically require larger pulleys to prevent excessive bending and to ensure proper support. The belt type, whether it is a flat belt, V-belt, or a timing belt, also influences the diameter due to differing flexing properties and load capacities.
Load Requirements: The weight of the materials being transported on the conveyor system affects the required pulley diameter. Heavier loads necessitate larger pulleys to distribute the weight more evenly and to reduce the strain on the belt and pulley system. This helps in preventing premature wear and extending the life of the components.
Speed of Operation: The operating speed of the conveyor belt is another crucial factor. Higher speeds increase the centrifugal forces on the belt and pulley, which can lead to increased wear and potential slippage. Larger pulley diameters help mitigate these effects by providing a more gradual bend for the belt, reducing stress and improving traction.
Tension and Flexibility: Proper tension is critical for maintaining the efficiency of the conveyor system. Pulley diameter must be calculated to ensure that the belt tension is maintained within optimal ranges. Additionally, the flexibility of the belt material affects how tightly it can bend around the pulleys, influencing the minimum pulley diameter.
Environmental Conditions: The operating environment of the conveyor system, such as temperature, humidity, and exposure to chemicals or abrasive materials, impacts the choice of pulley diameter. Harsh conditions may require larger, more robust pulleys to withstand environmental stresses and to ensure reliable operation.
Safety and Compliance Standards: Adhering to industry safety standards and regulations is essential. The pulley diameter must be calculated to meet these standards, ensuring safe operation and minimizing the risk of accidents. Compliance with standards also ensures the system can handle expected loads and operating conditions without failure.
Step-by-Step Guide to Accurate Pulley Diameter Calculation
Accurately calculating the diameter of a conveyor head pulley requires a systematic approach. Here is a step-by-step guide to help you achieve precise calculations:
Step 1: Determine the Belt Specifications
Start by gathering detailed information about the conveyor belt, including its width, type, thickness, and flexibility. Refer to the manufacturer’s specifications to understand the minimum bend radius and other critical properties.
Step 2: Calculate the Load Requirements
Assess the total load that the conveyor system will carry, including the weight of the materials and any additional forces that might act on the belt, such as incline angles or acceleration forces. Calculate the maximum load capacity to ensure that the pulley can handle the demands of the system.
Step 3: Establish the Operating Speed
Determine the operating speed of the conveyor belt, typically measured in feet per minute (FPM) or meters per second (m/s). This information is crucial for calculating the appropriate pulley diameter to prevent excessive wear and slippage at high speeds.
Step 4: Assess Tension and Flexibility
Evaluate the tension requirements of the conveyor system. This includes understanding the belt’s tensile strength and the necessary tension to keep the belt taut and functioning correctly. Consider the belt’s flexibility to ensure that it can bend appropriately around the pulley without causing undue stress.
Step 5: Factor in Environmental Conditions
Consider the environmental conditions in which the conveyor system will operate. Harsh conditions may necessitate larger pulleys made from more durable materials to withstand the environment and maintain performance.
Step 6: Apply Safety and Compliance Standards
Ensure that your calculations meet all relevant industry safety standards and compliance regulations. This includes checking that the pulley diameter supports safe operation under all expected load and speed conditions.
Step 7: Use the Pulley Diameter Formula
Utilize the following standard formula to calculate the conveyor pulley diameter:
[ D = \frac{(T + K)}{2} ]
Where:
- ( D ) is the pulley diameter.
- ( T ) is the tension factor, which depends on the belt tension and load.
- ( K ) is a constant that accounts for additional factors such as belt type and environmental conditions.
Refer to specific industry guidelines and manufacturer recommendations for precise values of ( T ) and ( K ) based on your conveyor system’s specifications.
Step 8: Verify with Conveyor Head Pulley Drawing
Once the pulley diameter is calculated, verify your results against the conveyor head pulley drawing. The drawing should include all necessary dimensions and specifications to ensure that the pulley fits within the overall design of the conveyor system. Make adjustments as needed to align with the drawing and ensure proper fit and function.
Step 9: Consider Real-World Testing
After finalizing the pulley diameter, consider conducting real-world testing to validate the calculations. Implement a prototype or a test setup to observe the pulley performance under actual operating conditions. This step helps identify any unforeseen issues and allows for fine-tuning before full-scale implementation.
Importance of Conveyor Head Pulley Drawing
In the design and maintenance of conveyor systems, the head pulley and its associated components play a critical role in ensuring efficient and reliable operation. One of the most vital components of the head pulley is the bearing. A detailed conveyor head pulley design is essential for visualizing and accurately implementing these components. This section will discuss the role of bearings in head pulley operation and provide insights on selecting the right bearings for durability and efficiency.
Role of Bearings in Head Pulley Operation
Bearings are integral to the functionality of the head pulley in a conveyor system. Their primary role is to support the rotating shaft, allowing the pulley to turn smoothly with minimal friction. Here’s a closer look at the specific functions of bearings in head pulley operation:
1. Reducing Friction: Bearings significantly reduce the friction between the rotating shaft and the stationary housing. This reduction in friction is crucial for the smooth operation of the pulley, minimizing wear on the shaft and other components, and ensuring efficient power transmission from the drive mechanism to the conveyor belt.
2. Supporting Loads: Bearings support both radial and axial loads exerted on the head pulley. Radial loads are perpendicular to the shaft, while axial loads are parallel. Properly selected bearings can handle these loads effectively, preventing deformation and ensuring the structural integrity of the pulley system.
3. Maintaining Alignment: Bearings help maintain the alignment of the head pulley. Misalignment can cause uneven wear on the belt and pulley, leading to premature failure and increased maintenance costs. High-quality bearings ensure that the pulley remains aligned, providing consistent performance and extending the life of the conveyor system.
4. Absorbing Vibrations: Bearings play a key role in absorbing and dampening vibrations that occur during conveyor operation. This dampening effect reduces the risk of mechanical failure and enhances the overall stability of the conveyor system, ensuring smooth and quiet operation.
5. Enabling Speed Control: Bearings allow the head pulley to operate at various speeds without compromising performance. This flexibility is essential for applications where the conveyor speed needs to be adjusted based on the type of materials being transported or other operational requirements.
Selecting the Right Bearings for Durability and Efficiency
Choosing the right bearings for the head pulley is crucial for maximizing the durability and efficiency of the conveyor system. Here are key considerations for selecting the appropriate bearings:
1. Bearing Type: There are various types of bearings available, each suited for different applications. Common types include ball bearings, roller bearings, and tapered roller bearings. Ball bearings are suitable for light to moderate loads and high-speed applications, while roller bearings are designed for heavier loads and slower speeds. Tapered roller bearings can handle both radial and axial loads, making them ideal for high-load applications.
2. Load Capacity: The load capacity of the bearing is a critical factor. It must be capable of supporting the combined weight of the head pulley, the conveyor belt, and the materials being transported. Overloading the bearing can lead to premature failure, so it’s essential to choose a bearing with an appropriate load rating.
3. Speed Rating: Bearings have specific speed ratings, indicating the maximum rotational speed they can handle. Selecting a bearing with a suitable speed rating for the conveyor’s operating conditions ensures smooth and efficient operation without excessive heat buildup or wear.
4. Material and Construction: The material and construction of the bearing affect its performance and durability. Bearings made from high-quality steel or ceramic materials offer superior strength and wear resistance. Additionally, sealed or shielded bearings protect against contamination from dust, dirt, and moisture, extending the bearing’s lifespan.
5. Lubrication Requirements: Proper lubrication is essential for the smooth operation of bearings. Some bearings are pre-lubricated, while others require regular maintenance. Consider the operating environment and maintenance capabilities when selecting bearings, ensuring that they can be adequately lubricated to prevent friction and wear.
6. Environmental Conditions: The operating environment plays a significant role in bearing selection. Bearings used in harsh conditions, such as high temperatures, corrosive environments, or areas with heavy contamination, require special coatings or materials to withstand these conditions. Stainless steel or coated bearings are often used in such environments to ensure durability and longevity.
7. Compatibility with Conveyor Head Pulley Drawing: Ensure that the selected bearings match the specifications detailed in the conveyor head pulley drawing. The drawing should provide precise measurements and indicate the correct placement and alignment of the bearings. Verifying compatibility with the drawing prevents installation issues and ensures optimal performance.
The Key of Conveyor Head Pulley Drawing
Drive Pulley Conveyor Mechanics
Understanding the mechanics of a drive pulley in conveyor systems is essential for optimizing their performance and efficiency. The conveyor head pulley drawing provides a detailed visual representation of the drive pulley, illustrating its design, placement, and function within the conveyor system. This section explores how the drive pulley powers the conveyor belt and the benefits of using efficient drive pulleys in conveyor systems.
How the Drive Pulley Powers the Conveyor Belt
The drive pulley is a crucial component of a conveyor system, responsible for moving the conveyor belt and, consequently, the materials on it. It is typically located at the head of the conveyor, hence the term “head pulley.” The drive pulley works in conjunction with the motor to propel the belt forward.
Mechanics of the Drive Pulley:
- Motor Connection:
The drive pulley is connected to a motor, usually via a gearbox or a direct drive system. The motor provides the rotational force required to turn the drive pulley. In a typical setup, the motor’s power is transmitted to the pulley through a shaft. - Wrap Angle and Belt Contact:
The conveyor belt wraps around the drive pulley, creating friction between the belt and the pulley surface. This friction is essential for transferring the motor’s rotational force to the belt, causing it to move. The wrap angle, or the extent to which the belt wraps around the pulley, is a critical factor in ensuring sufficient friction. Snub pulleys are often used to increase the wrap angle, enhancing the grip and reducing slippage. - Tension and Traction:
Proper tension is crucial for effective power transmission. The drive pulley, along with the tensioning system (which may include tail pulleys and take-up pulleys), maintains the belt tension. Adequate tension ensures that the belt remains in contact with the drive pulley, preventing slippage and ensuring smooth operation. - Rotation and Belt Movement:
As the motor turns the drive pulley, the frictional grip between the belt and the pulley causes the belt to move. The rotational motion of the pulley is converted into linear motion of the conveyor belt, which transports materials along the conveyor.
Benefits of Using Efficient Drive Pulleys in Conveyor Systems
Efficient drive pulleys are vital for the optimal performance of conveyor systems. Here are the key benefits of using efficient drive pulleys:
1. Improved Energy Efficiency:
Efficient drive pulleys enhance the energy efficiency of conveyor systems. By maximizing the frictional grip and minimizing slippage, these pulleys ensure that the motor’s power is effectively transmitted to the belt. This efficient power transfer reduces energy consumption, lowering operational costs and environmental impact.
2. Enhanced Conveyor Performance:
The use of efficient drive pulleys leads to smoother and more reliable conveyor operation. With reduced slippage and consistent belt movement, the system can handle higher loads and operate at faster speeds without compromising performance. This improvement in performance boosts overall productivity.
3. Extended Component Lifespan:
Efficient drive pulleys reduce the wear and tear on the conveyor belt and other components. By ensuring proper tension and minimizing slippage, these pulleys prevent excessive stress and abrasion on the belt. This extends the lifespan of the belt, pulleys, and bearings, resulting in lower maintenance costs and fewer replacements.
4. Improved Material Handling:
Consistent belt movement is crucial for effective material handling. Efficient drive pulleys maintain steady belt speed and direction, ensuring that materials are transported smoothly and predictably. This consistency reduces the risk of material spillage, blockages, and uneven distribution, enhancing the reliability of the conveyor system.
5. Increased Safety:
Efficient drive pulleys contribute to the overall safety of conveyor systems. Reduced slippage and proper belt tension lower the likelihood of belt failures and operational hazards. This improved safety protects both the equipment and personnel, reducing the risk of accidents and injuries.
6. Versatility Across Applications:
Efficient drive pulleys are versatile and can be used in a wide range of conveyor systems and applications. Whether in mining, manufacturing, packaging, or distribution, these pulleys can be adapted to meet specific operational requirements. Their ability to handle different loads, speeds, and environmental conditions makes them valuable assets in diverse settings.
7. Cost-Effective Operation:
Investing in efficient drive pulleys leads to significant cost savings over time. The initial investment is offset by the reduction in energy consumption, maintenance costs, and downtime. Efficient pulleys also contribute to increased productivity, further enhancing the cost-effectiveness of conveyor systems.
Tail Pulley Role and Functionality
In the design and optimization of conveyor systems, understanding the roles and interactions of key components is crucial. While much attention is often given to the head pulley, the tail pulley plays an equally important role in the overall efficiency and functionality of the system. This section will provide an overview of the tail pulley in conveyor systems and explore the interaction between head and tail pulleys. A detailed conveyor head pulley drawing is essential for visualizing these components and their relationships within the system.
Overview of Tail Pulley in Conveyor Systems
The tail pulley, located at the opposite end of the conveyor from the head pulley, serves several critical functions that contribute to the effective operation of the conveyor system. Here’s a detailed look at the role and functionality of the tail pulley:
1. Belt Tensioning: One of the primary functions of the tail pulley is to maintain the proper tension in the conveyor belt. Proper tensioning is essential to prevent slippage and ensure smooth, consistent belt movement. The tail pulley often incorporates an adjustable mechanism that allows operators to fine-tune the belt tension to match specific operational needs and conditions.
2. Directional Guidance: The tail pulley helps guide the conveyor belt back towards the head pulley after it has completed its transport cycle. This directional guidance ensures that the belt remains aligned and follows the intended path, reducing the risk of misalignment and uneven wear. Proper guidance by the tail pulley is crucial for maintaining the integrity and efficiency of the conveyor system.
3. Load Distribution: The tail pulley supports the return side of the conveyor belt, helping to distribute the weight and load evenly across the system. This distribution is vital for preventing excessive wear on any single component and ensuring a balanced operation. By evenly distributing the load, the tail pulley contributes to the longevity and durability of the conveyor belt and related components.
4. Transition Support: In conveyor systems that handle significant changes in elevation or direction, the tail pulley provides essential support for transitions. It helps to manage the changes in belt direction smoothly, preventing abrupt shifts that could cause damage or operational inefficiencies. The tail pulley’s support in these transitions ensures a continuous, uninterrupted flow of materials.
5. Belt Cleaning and Maintenance Access: The tail pulley is often positioned in a location that allows for easy access to the underside of the conveyor belt. This accessibility is beneficial for cleaning and maintenance purposes, as it enables operators to inspect and service the belt and pulley without extensive disassembly. Regular maintenance facilitated by the tail pulley’s position helps to prevent build-up of debris and maintain the belt’s optimal condition.
Interaction Between Head and Tail Pulleys
The interaction between the head and tail pulleys is fundamental to the effective operation of a conveyor system. Understanding how these components work together is crucial for optimizing performance and ensuring the longevity of the system. Here’s an exploration of this interaction:
1. Coordinated Belt Tensioning: Both the head and tail pulleys play a role in maintaining the correct tension in the conveyor belt. While the tail pulley often provides the initial tensioning, the head pulley, driven by an electric motor, pulls the belt and maintains tension throughout the system. The coordinated effort between these pulleys ensures that the belt remains taut and aligned, preventing slippage and reducing wear.
2. Smooth Material Flow: The head pulley drives the conveyor belt, moving materials from the loading point to the discharge end. The tail pulley guides the belt back towards the head pulley, ensuring a continuous loop. This interaction is essential for maintaining a smooth flow of materials, reducing interruptions, and enhancing overall system efficiency. The head pulley’s role in driving the belt and the tail pulley’s role in guiding it back work in tandem to ensure a consistent material handling process.
3. Load Balancing and Distribution: The head and tail pulleys work together to balance and distribute the load on the conveyor belt. The head pulley manages the drive force and the load’s initial movement, while the tail pulley supports the return side and helps distribute the load evenly. This load balancing is crucial for preventing excessive wear on specific sections of the belt and ensuring a uniform load distribution, which contributes to the longevity and reliability of the system.
4. Alignment and Tracking: Proper alignment and tracking of the conveyor belt are maintained through the combined efforts of the head and tail pulleys. The head pulley sets the direction and initial alignment of the belt, while the tail pulley ensures it remains on track as it returns. Any misalignment detected at the tail pulley can be corrected, preventing further deviation and ensuring the belt runs true along its path. This coordinated tracking is vital for preventing belt drift and maintaining operational efficiency.
5. Energy Efficiency: The interaction between the head and tail pulleys also impacts the energy efficiency of the conveyor system. By ensuring proper tension, alignment, and load distribution, these pulleys reduce the amount of energy required to drive the belt. Efficient interaction between the head and tail pulleys minimizes friction and mechanical resistance, leading to lower energy consumption and reduced operational costs.
6. Maintenance and Longevity: The head and tail pulleys’ roles in maintaining tension, alignment, and load distribution also contribute to the overall maintenance and longevity of the conveyor system. Regular maintenance of these pulleys, guided by a detailed conveyor head pulley drawing, helps to identify and address potential issues before they lead to significant problems. The drawing provides a reference for proper installation, alignment, and servicing of the pulleys, ensuring they function effectively and extend the system’s lifespan.
FAQS about Conveyor Head Pulley Drawing
The head of a conveyor refers to the end of the conveyor system where materials are discharged. This part of the conveyor is critical because it houses the head pulley, which drives the conveyor belt. The head of the conveyor is responsible for ensuring the smooth and controlled release of materials from the belt onto the next stage of the production process or into a storage area. It plays a vital role in the overall efficiency and reliability of the conveyor system. The head includes components such as the head pulley, motor, and any necessary control mechanisms to maintain the correct belt speed and tension. Proper design and maintenance of the conveyor head are crucial to prevent issues like belt misalignment, slippage, or material spillage, ensuring consistent and efficient operation of the entire conveyor system.
A head or drive pulley is the primary component in a conveyor system that provides the driving force for the conveyor belt. Positioned at the discharge end, the drive pulley is connected to a motor that imparts motion to the belt, allowing it to transport materials along the conveyor. The drive pulley is typically larger in diameter than other pulleys in the system to provide better traction and control. It is often covered with a lagging material, such as rubber or ceramic, to increase friction and prevent belt slippage. The drive pulley’s primary role is to ensure smooth and efficient movement of the conveyor belt, maintaining the required speed and tension. It is essential for the overall performance and reliability of the conveyor system, as it directly influences the belt’s operation and the effectiveness of material handling processes.
Designing a conveyor pulley involves several critical steps to ensure it meets the operational requirements and withstands the stresses of the conveyor system. The process begins with determining the pulley’s size, including its diameter and width, based on the conveyor belt’s specifications and the material being transported. The next step is selecting the appropriate materials for the pulley shell, shaft, and end discs, considering factors such as load capacity, environmental conditions, and wear resistance. Engineers must then calculate the pulley’s tension and load-bearing capabilities, ensuring it can handle the forces exerted by the belt and the conveyed materials. The design also includes specifying the type of lagging to enhance friction and prevent slippage. Additionally, the placement and type of bearings are crucial for ensuring smooth rotation and reducing maintenance needs. Finally, finite element analysis (FEA) is often used to simulate and validate the pulley design, ensuring it meets safety and performance standards.
The head pulley of a conveyor is a crucial component positioned at the discharge end of the conveyor system. It is responsible for driving the conveyor belt and is typically larger in diameter compared to other pulleys in the system. The head pulley is connected to a motor, which provides the necessary power to propel the belt and move materials along the conveyor. Its primary function is to ensure the smooth and efficient operation of the conveyor by maintaining the required tension and speed. The head pulley often features a lagging material, such as rubber or ceramic, to increase friction and prevent belt slippage. This component is essential for the overall performance and reliability of the conveyor system, making it a critical part of any material handling operation.
Last Updated on June 17, 2024 by Jordan Smith
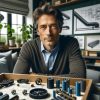
Jordan Smith, a seasoned professional with over 20 years of experience in the conveyor system industry. Jordan’s expertise lies in providing comprehensive solutions for conveyor rollers, belts, and accessories, catering to a wide range of industrial needs. From initial design and configuration to installation and meticulous troubleshooting, Jordan is adept at handling all aspects of conveyor system management. Whether you’re looking to upgrade your production line with efficient conveyor belts, require custom conveyor rollers for specific operations, or need expert advice on selecting the right conveyor accessories for your facility, Jordan is your reliable consultant. For any inquiries or assistance with conveyor system optimization, Jordan is available to share his wealth of knowledge and experience. Feel free to reach out at any time for professional guidance on all matters related to conveyor rollers, belts, and accessories.