Aligning Idlers for Proper Conveyor Idler Angle
Conveyor idler angles play a crucial role in the efficiency and functionality of belt conveyor systems. These angles help in maintaining the proper shape and alignment of the conveyor belt, ensuring smooth material handling and reducing wear and tear. Key terms such as the surcharge angle, angle of repose, and idler alignment are essential in understanding how these systems operate. The correct conveyor idler angle ensures that materials are transported safely and efficiently, preventing spillage and optimizing load distribution. By mastering these concepts, you can enhance the performance and longevity of your conveyor systems.
What are Conveyor Idler Angles?
Definition and Significance of Idler Angles in Conveyor Systems
Conveyor idler angles refer to the specific angles at which the idler rollers are set relative to the horizontal plane of the conveyor belt. These angles are crucial in shaping the belt and influencing the way materials are carried along the conveyor system. Typically, idler angles are measured in degrees and vary depending on the design and requirements of the conveyor system.
The primary significance of conveyor idler angles lies in their ability to maintain the stability and efficiency of the material handling process. By setting the idlers at specific angles, the conveyor belt can form a trough, which helps to center and contain the bulk material being transported. This trough shape minimizes spillage and ensures that materials are evenly distributed across the width of the belt, reducing the likelihood of uneven wear and tear.
The standard idler angles commonly used in conveyor systems are 20°, 35°, and 45°. These angles are selected based on the type of material being transported, the conveyor’s capacity, and the operational requirements. For instance, a 20° idler angle is often used for light, free-flowing materials, while a 35° angle is more suitable for medium-density materials. A 45° angle is typically reserved for heavy, dense materials that require a deeper trough to prevent spillage.
How Idler Angles Affect Material Handling and Belt Performance
The conveyor idler angle plays a pivotal role in material handling and overall belt performance. Here are several ways in which idler angles impact the operation of conveyor systems:
- Material Containment: One of the primary functions of setting the idlers at specific angles is to form a trough that effectively contains the material on the belt. This is particularly important in preventing spillage, especially when transporting fine or granular materials. Proper containment ensures that materials are delivered to their intended destination without loss, thus enhancing the efficiency of the conveyor system.
- Load Distribution: Conveyor idler angles help distribute the load evenly across the belt. An even load distribution minimizes localized stress points on the belt, which can lead to premature wear and potential failure. By maintaining a consistent load distribution, the belt’s lifespan is extended, and maintenance costs are reduced.
- Belt Alignment: The alignment of the conveyor belt is significantly influenced by the idler angles. Properly set idler angles help in maintaining the belt’s central position, preventing it from drifting to one side or the other. This alignment is crucial in avoiding belt mistracking, which can cause material spillage, increased wear on the belt edges, and potential damage to the conveyor structure.
- Energy Efficiency: The angle of the idlers can also impact the energy consumption of the conveyor system. A well-designed idler angle reduces the friction between the belt and the idlers, which in turn lowers the power required to move the belt. This reduction in energy consumption can lead to significant cost savings, particularly in large-scale conveyor operations.
- Capacity and Throughput: Adjusting the conveyor idler angle can also influence the system’s capacity and throughput. A deeper trough (achieved with higher idler angles) can accommodate larger volumes of material, increasing the conveyor’s capacity. This adjustment is essential when designing conveyors for specific material handling requirements, ensuring that the system meets the desired throughput targets.
- Impact on Belt Wear: The conveyor idler angle directly affects the belt’s contact surface with the material. By optimizing the idler angles, the wear on the belt can be evenly distributed, reducing the likelihood of localized wear and extending the belt’s operational life. This optimization is critical in maintaining the conveyor system’s reliability and minimizing downtime due to belt replacements.
- Safety Considerations: Properly set conveyor idler angles enhance the safety of the conveyor system. By ensuring that materials are contained and the belt remains aligned, the risk of accidents caused by material spillage or belt misalignment is significantly reduced. This safety aspect is particularly important in industrial environments where conveyor systems are used extensively.
- Customizability: Conveyor idler angles can be customized to suit specific operational requirements. Depending on the nature of the material, environmental conditions, and desired conveyor performance, idler angles can be adjusted to optimize the system’s efficiency. This customizability allows conveyor designers to tailor the system to meet unique challenges and operational goals.
The conveyor idler angle is a critical factor in the design and operation of conveyor systems. It affects material containment, load distribution, belt alignment, energy efficiency, capacity, and overall system performance. Understanding and optimizing idler angles are essential for ensuring the efficient, reliable, and safe operation of conveyor systems in various industrial applications.
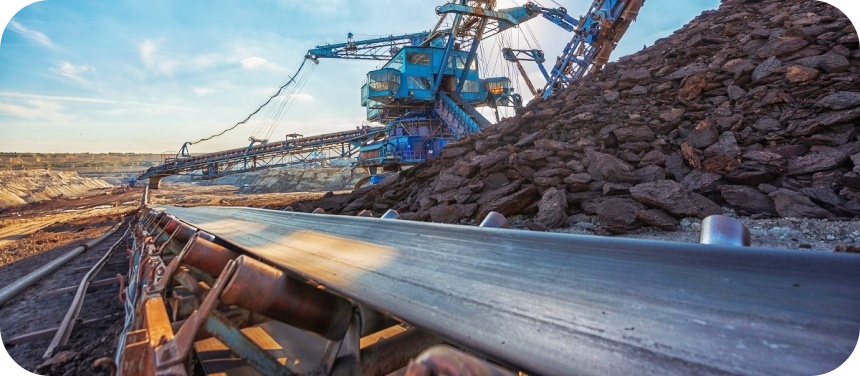
Types of Conveyor Idlers
Description of Various Types of Idlers
Conveyor idlers are essential components in the efficient and reliable operation of conveyor systems. They support the conveyor belt and the materials being transported, ensuring smooth and uninterrupted movement. Understanding the different types of conveyor idlers, including their specific applications and benefits, is crucial for optimizing conveyor system performance.
Troughing Idlers
Troughing idlers are the most commonly used type of idlers in conveyor systems. They are designed to form the conveyor belt into a trough shape, which helps contain and center the material being transported. This design minimizes spillage and ensures that the load is evenly distributed across the belt. Troughing idlers typically come in three-roll or five-roll configurations, with the side rollers set at an angle to create the trough.
The standard conveyor idler angles for troughing idlers are 20°, 35°, and 45°. The choice of angle depends on the nature of the material and the desired capacity of the conveyor system. For example, a 20° angle is suitable for light, free-flowing materials, while a 35° angle is used for medium-density materials, and a 45° angle is ideal for heavy, dense materials.
Impact Idlers
Impact idlers are specifically designed to handle heavy impact loads that occur at loading points where materials are dropped onto the conveyor belt. These idlers are equipped with rubber discs or rings that absorb the impact energy, protecting the belt and reducing the risk of damage. By cushioning the load, impact idlers extend the life of the conveyor belt and improve overall system reliability.
The conveyor idler angle in impact idlers is also important, as it helps in maintaining the belt’s alignment and preventing material spillage. The impact idlers are usually placed at intervals along the conveyor to provide continuous support and protection.
Return Idlers
Return idlers are used on the return side of the conveyor belt to support the empty belt as it returns to the loading point. These idlers can be flat or V-shaped, with the latter design helping to center the belt and prevent misalignment. Return idlers are essential for maintaining the belt’s stability and ensuring smooth operation.
In some cases, return idlers are fitted with rubber rings or discs to prevent material buildup on the idler surface. This design feature reduces the risk of belt damage and improves the efficiency of the conveyor system.
Importance of Selecting the Right Idler for Specific Applications
Selecting the appropriate type of idler for specific applications is crucial for the optimal performance and longevity of conveyor systems. Here are ten reasons why choosing the right idler is important:
- Material Handling Efficiency: The right idler ensures that the material is effectively contained and transported along the conveyor belt. For example, using troughing idlers with the correct conveyor idler angle helps in forming a trough that prevents spillage and ensures even load distribution.
- Belt Protection: Idlers such as impact idlers are designed to protect the conveyor belt from damage caused by heavy impact loads. By absorbing impact energy, these idlers extend the belt’s lifespan and reduce maintenance costs.
- System Reliability: Properly selected idlers contribute to the overall reliability of the conveyor system. Return idlers, for instance, help maintain the alignment of the empty belt, preventing misalignment issues that could lead to system failures.
- Operational Safety: The correct idler configuration enhances the safety of the conveyor system. By preventing material spillage and ensuring belt stability, the risk of accidents and injuries is minimized.
- Energy Efficiency: Using idlers with the appropriate conveyor idler angle reduces friction between the belt and the idlers, lowering the energy required to move the belt. This energy efficiency translates to cost savings, especially in large-scale operations.
- Load Distribution: Troughing idlers with the right angles ensure that the load is evenly distributed across the belt. This even distribution minimizes localized stress points, reducing wear and tear and prolonging the belt’s life.
- Maintenance Reduction: Selecting idlers designed for specific applications, such as impact idlers for heavy loads, reduces the frequency and cost of maintenance. This reduction is due to the idlers’ ability to protect the belt and other conveyor components from damage.
- Customizability: Conveyor systems often require customized idler configurations to meet unique operational requirements. By selecting the right idler types and angles, the system can be tailored to handle specific materials and operating conditions efficiently.
- Capacity Optimization: The use of idlers with appropriate conveyor idler angles can increase the system’s capacity. For instance, a deeper trough formed by higher angle troughing idlers can accommodate larger volumes of material, enhancing the conveyor’s throughput.
- Environmental Adaptability: Different idlers are designed to perform optimally in various environmental conditions. For example, idlers with rubber discs are suitable for wet or sticky materials, as they prevent buildup and ensure smooth operation.
Understanding the different types of conveyor idlers and their specific applications is essential for designing and maintaining efficient conveyor systems. The selection of the right idler, considering factors such as the conveyor idler angle, material characteristics, and operational requirements, plays a critical role in ensuring the system’s reliability, safety, and efficiency.
Surcharge Angle and Angle of Repose in Relation to Conveyor Idler Angle
Explanation of the Surcharge Angle and Its Relevance in Conveyor Systems
The surcharge angle is a critical concept in the design and operation of belt conveyor systems, particularly when considering the conveyor idler angle. The surcharge angle is defined as the angle that the material on a conveyor belt forms with the horizontal while at rest. This angle is significant because it affects how materials are loaded and transported on the conveyor belt.
When materials are loaded onto the belt, they naturally form a pile with a slope that corresponds to the surcharge angle. This angle varies depending on the type of material being conveyed, with finer materials like sand forming a smaller angle and bulkier materials like coal or gravel forming a larger one. Understanding the surcharge angle is crucial because it helps in designing the conveyor system to handle materials efficiently without spillage.
In the context of conveyor idler angles, the surcharge angle influences the selection and arrangement of idlers. Idlers are the rollers or sets of rollers installed on the conveyor frame to support the belt and its load. The conveyor idler angle, or the angle at which these idlers are set, must complement the surcharge angle to ensure stable material transport. If the idler angle is too steep or too flat, it can cause the material to spill or fail to move smoothly along the belt, leading to inefficiencies and potential system failures.
Definition of the Angle of Repose and How It Affects Material Stability on the Belt
The angle of repose is another essential concept related to conveyor systems and conveyor idler angles. The angle of repose is the steepest angle at which a material can be piled without slumping. This angle is determined by the internal friction of the material particles and is a key factor in ensuring the stability of the material on the conveyor belt.
Materials with a high angle of repose are more stable and can be transported at steeper conveyor idler angles without the risk of slipping or spilling. Conversely, materials with a low angle of repose are less stable and require flatter idler angles to maintain their position on the belt. This balance is crucial for the effective and safe operation of the conveyor system.
For instance, materials like grains or powders, which have a lower angle of repose, need idlers set at lower angles to prevent the material from sliding off the belt. On the other hand, bulkier materials like rocks or ores with a higher angle of repose can be transported using idlers set at steeper angles. This adjustment ensures that the material remains stable and securely transported along the conveyor path.
Relevance to Conveyor Idler Angle
Understanding the relationship between the surcharge angle, angle of repose, and conveyor idler angle is vital for designing efficient conveyor systems. When designing a conveyor system, engineers must consider these angles to ensure that materials are loaded and transported effectively without spillage or instability.
The conveyor idler angle must be carefully selected based on the material’s surcharge angle and angle of repose. This selection involves balancing the need for efficient material transport with the need to maintain material stability on the belt. For example, if a material has a high surcharge angle but a low angle of repose, the conveyor idler angle must be set in a way that accommodates both factors to prevent spillage and ensure smooth transport.
Additionally, adjusting the conveyor idler angle can help mitigate issues such as belt misalignment and uneven load distribution. By setting the idlers at the correct angle, the belt can carry the material more evenly, reducing wear and tear on the system and extending its operational life. This adjustment also helps in optimizing the conveyor’s capacity, allowing it to handle larger loads more efficiently.
Practical Applications and Case Studies
To illustrate the importance of understanding surcharge angles, angles of repose, and conveyor idler angles, consider the following case studies:
- Mining Operations: In mining operations, bulk materials such as ores and rocks need to be transported over long distances. These materials typically have high surcharge angles and angles of repose, allowing for steeper conveyor idler angles. By setting the idlers correctly, mining companies can ensure efficient material transport with minimal spillage and maximum load capacity.
- Agricultural Industry: In the agricultural industry, materials like grains and seeds are often conveyed. These materials have lower angles of repose, requiring flatter conveyor idler angles to maintain stability. Properly adjusted idlers prevent grain loss and ensure smooth transport from storage to processing areas.
- Construction Sector: In construction, materials like sand and gravel are commonly transported using conveyors. Sand, with its fine particles and low angle of repose, requires flatter idler angles, while gravel, with a higher angle of repose, can be transported using steeper idlers. Adjusting the idler angles based on these properties ensures efficient and safe material handling on construction sites.
Understanding the surcharge angle and angle of repose is essential for designing and operating effective conveyor systems. These angles directly influence the selection and adjustment of conveyor idler angles, which in turn affect material stability and transport efficiency. By carefully considering these factors, engineers can optimize conveyor systems to handle various materials safely and efficiently, reducing spillage and ensuring smooth operations. Properly designed conveyor idler angles contribute to the longevity and reliability of the conveyor system, making it a critical aspect of material handling in various industries.
Conveyor Idler Angle Calculations
Basic Principles of Calculating Conveyor Idler Angles
Calculating the conveyor idler angle is a crucial aspect of designing an efficient and reliable conveyor system. The idler angle determines the trough shape of the conveyor belt, which in turn affects material handling and belt performance. Here are six basic principles involved in calculating conveyor idler angles:
- Material Characteristics: The type of material being transported greatly influences the choice of the conveyor idler angle. Materials with different densities, particle sizes, and flow characteristics require specific trough angles to ensure efficient handling and minimal spillage. For example, fine, free-flowing materials may only require a shallow trough (20°), whereas bulkier, heavier materials may need a deeper trough (35° or 45°) to prevent spillage.
- Load Distribution: The idler angle must ensure an even distribution of the load across the conveyor belt. This even distribution minimizes localized stress points, which can lead to premature wear and tear on the belt. The load distribution is calculated by considering the weight and volume of the material per unit length of the belt.
- Belt Width: The width of the conveyor belt is a fundamental factor in determining the appropriate idler angle. Wider belts typically require smaller idler angles to form a stable trough, while narrower belts can accommodate steeper angles. The belt width and idler angle together define the cross-sectional area available for material transport.
- Angle Geometry: The geometry of the idler angle calculation involves determining the positioning of the side rollers relative to the center roller to achieve the desired trough shape. The angles are set such that the belt forms a consistent and stable trough along its entire length. Standard configurations include three-roll or five-roll sets, with side rollers typically set at angles of 20°, 35°, or 45°.
- Idler Spacing: The spacing between idler sets along the conveyor’s length also influences the idler angle. Closer spacing provides better support for the belt and helps maintain the trough shape, especially under heavy loads. Conversely, wider spacing may be used for lighter loads but requires careful calculation to ensure the trough remains stable.
- Dynamic Considerations: The dynamic behavior of the conveyor system, including belt speed and load variations, must be considered when calculating the idler angle. Higher belt speeds and fluctuating loads can impact the stability of the trough, necessitating adjustments in the idler angle or spacing to maintain efficient operation.
Factors Influencing Idler Angle Selection
Selecting the appropriate conveyor idler angle involves considering several key factors to ensure optimal system performance. Here are eight factors that influence idler angle selection:
- Material Type: The characteristics of the material being transported—such as bulk density, particle size, moisture content, and flowability—are critical in determining the idler angle. Cohesive or sticky materials may require different trough angles compared to free-flowing materials to prevent buildup and spillage.
- Belt Speed: The speed at which the conveyor belt operates affects the stability of the material on the belt. Higher speeds may require steeper idler angles to ensure the material remains contained within the trough. Conversely, lower speeds may allow for shallower angles without risking spillage.
- Load: The amount of material being transported, measured in terms of weight per unit length of the belt, influences the idler angle. Heavier loads typically necessitate steeper angles to create a deeper trough that can accommodate the increased material volume and prevent overflow.
- Environmental Conditions: Operating conditions such as temperature, humidity, and the presence of corrosive or abrasive materials can affect idler selection. For example, in high-humidity environments, materials may become sticky, requiring adjustments in the idler angle to maintain efficient transport.
- Belt Tension: The tension in the conveyor belt impacts the formation of the trough and the effectiveness of the idler angle. Proper tension must be maintained to ensure the belt conforms to the idler configuration and forms a stable trough. Excessive or insufficient tension can lead to belt misalignment and operational issues.
- Maintenance Considerations: The ease of maintenance and replacement of idlers is an important factor. Systems designed with standard idler angles (such as 20°, 35°, and 45°) may benefit from easier availability of replacement parts and standardized maintenance procedures.
- Conveyor Length and Elevation: The length of the conveyor and any elevation changes along its path can influence the idler angle. Longer conveyors or those with significant elevation changes may require careful calculation of idler angles and spacing to ensure consistent material flow and trough stability throughout the system.
- Cost Considerations: The cost of idler components and the overall design must be balanced against the performance benefits. While higher idler angles may improve material containment, they may also increase the cost of the idler sets and the structural support required. A cost-benefit analysis helps in selecting the most efficient and economical idler angle for the specific application.
Calculating the conveyor idler angle and selecting the appropriate idler configuration are essential steps in designing efficient conveyor systems. By considering material characteristics, belt speed, load, and other factors, the optimal idler angle can be determined to ensure reliable, efficient, and cost-effective material handling. Properly calculated and selected idler angles contribute to the overall performance, longevity, and safety of the conveyor system, making them a critical aspect of conveyor design and operation.
Conveyor Idler Angle Charts and PDFs
Overview of Useful Resources like Idler Angle Charts and PDF Guides
Conveyor idler angles are a crucial component in the design and operation of conveyor systems. To assist engineers and operators in selecting and adjusting these angles, numerous resources are available, including conveyor idler angle charts and PDF guides. These resources provide detailed information on the recommended idler angles for various types of materials and conveyor configurations.
Conveyor Idler Angle Charts:
Conveyor idler angle charts are graphical representations that outline the optimal idler angles for different materials and load conditions. These charts take into account factors such as material bulk density, particle size, and angle of repose. By consulting these charts, engineers can quickly determine the appropriate idler angle settings to ensure efficient and stable material transport.
For example, an idler angle chart may show that for a particular type of coal with a given bulk density and particle size, the recommended idler angle is 20 degrees. For a different material, such as crushed stone, the chart might recommend a steeper angle of 35 degrees. These charts are typically organized in a way that makes it easy to cross-reference different materials and conditions, providing a quick and reliable reference for conveyor design.
PDF Guides:
PDF guides are comprehensive documents that offer in-depth information on conveyor idler angles, including theoretical explanations, practical examples, and case studies. These guides often cover a wide range of topics related to conveyor systems, such as material handling principles, conveyor design standards, and maintenance practices. They serve as valuable resources for both novice and experienced engineers, providing detailed insights into the complexities of conveyor idler angle selection and adjustment.
PDF guides often include sections on:
- The importance of conveyor idler angles in maintaining material stability and preventing spillage.
- Methods for calculating the optimal idler angle based on material properties and conveyor load conditions.
- Best practices for aligning idlers to ensure consistent performance and reduce wear on the conveyor belt.
- Troubleshooting common issues related to incorrect idler angles, such as belt misalignment and uneven load distribution.
How to Utilize These Resources for Effective Conveyor Design
Utilizing conveyor idler angle charts and PDF guides effectively requires a systematic approach. Here are some steps to help you make the most of these resources:
Step 1: Identify Material Properties
The first step in using conveyor idler angle charts and PDF guides is to gather detailed information about the materials you will be conveying. This includes properties such as bulk density, particle size, angle of repose, and moisture content. Understanding these properties is essential for selecting the appropriate idler angles.
Step 2: Consult Conveyor Idler Angle Charts
Once you have identified the material properties, consult the conveyor idler angle charts to determine the recommended idler angles. These charts provide a quick reference for matching material properties with the optimal idler angles. Be sure to cross-reference multiple charts if available, as different charts may offer slightly varying recommendations based on specific conditions.
Step 3: Review PDF Guides for Detailed Insights
After consulting the idler angle charts, review relevant PDF guides to gain a deeper understanding of the theoretical and practical aspects of conveyor idler angles. These guides often provide detailed explanations of the principles behind idler angle selection, as well as practical examples and case studies that illustrate successful implementations.
Step 4: Calculate Optimal Idler Angles
Using the information from the idler angle charts and PDF guides, perform calculations to determine the precise idler angles for your specific conveyor system. This may involve using formulas and equations provided in the guides to account for factors such as conveyor speed, load distribution, and material flow characteristics.
Step 5: Implement and Adjust Idler Angles
With the calculated idler angles in hand, implement the recommended settings on your conveyor system. It is essential to carefully adjust the idlers to the correct angles, as even slight deviations can impact material stability and conveyor performance. Use tools and equipment such as angle finders and alignment gauges to ensure accuracy.
Step 6: Monitor and Maintain
After setting the idler angles, continuously monitor the performance of your conveyor system. Look for signs of belt misalignment, spillage, and uneven load distribution, as these may indicate that the idler angles need further adjustment. Regular maintenance and inspection are crucial for ensuring that the conveyor system operates efficiently and that the idler angles remain correctly set.
Practical Tips for Using Conveyor Idler Angle Charts and PDFs:
- Organize Your Resources: Keep your idler angle charts and PDF guides well-organized and easily accessible. Consider creating a digital library or physical binder where you can quickly reference these documents when needed.
- Stay Updated: Conveyor technology and material handling practices are constantly evolving. Stay updated with the latest versions of idler angle charts and PDF guides, and seek out new resources that may offer improved recommendations and insights.
- Consult Experts: If you encounter complex situations or are unsure about the correct idler angles, do not hesitate to consult with experts in conveyor design and material handling. They can provide valuable advice and help ensure that your conveyor system is optimized for your specific needs.
Conveyor idler angle charts and PDF guides are indispensable tools for designing and maintaining efficient conveyor systems. By providing detailed information on optimal idler angles for various materials and load conditions, these resources help engineers make informed decisions that enhance the performance and reliability of their conveyors. Utilizing these resources effectively involves identifying material properties, consulting charts and guides, performing calculations, and implementing and adjusting idler angles with precision. Regular monitoring and maintenance further ensure that the conveyor system operates smoothly and efficiently, minimizing downtime and maximizing productivity.
Impact of Conveyor Idler Angle on Conveyor Performance
How Different Idler Angles Influence Belt Tracking and Load Distribution
The conveyor idler angle plays a crucial role in the performance of a conveyor system, influencing both belt tracking and load distribution. Properly calculated idler angles ensure that the belt remains centered and that the load is evenly distributed, which are vital for efficient and reliable operation.
Belt Tracking
Belt tracking refers to the ability of the conveyor belt to remain aligned and centered as it moves along the conveyor structure. The conveyor idler angle directly impacts belt tracking in several ways:
- Alignment: The idler angle helps in forming the trough shape of the belt, which naturally guides the material towards the center. This centering effect minimizes the risk of the belt drifting to one side, which can lead to misalignment issues.
- Stability: Idlers set at the correct angle provide stability to the belt by supporting it uniformly. This support helps maintain the belt’s alignment, especially when transporting uneven or shifting loads. If the idler angle is too steep or too shallow, the belt may not form a proper trough, leading to instability and tracking problems.
- Load Impact: When the belt is loaded unevenly or if the material shifts during transport, the idler angle helps in maintaining the belt’s central position. Properly configured idler angles can absorb and distribute the impact of shifting loads, preventing the belt from skewing or running off-track.
Load Distribution
Load distribution is essential for maintaining the structural integrity of the conveyor system and ensuring efficient material transport. The conveyor idler angle significantly influences how the load is distributed across the belt:
- Even Distribution: Idlers set at the correct angle ensure that the material is evenly distributed across the width of the belt. This even distribution reduces the risk of localized stress points, which can cause excessive wear and tear on the belt and other components.
- Trough Formation: The idler angle creates a trough shape that helps contain the material within the belt. This containment prevents spillage and ensures that the load remains centered, contributing to an even load distribution.
- Load Capacity: Different idler angles can accommodate varying load capacities. Steeper angles (e.g., 45°) create deeper troughs, allowing the belt to carry heavier and bulkier materials without spillage. Shallower angles (e.g., 20°) are suitable for lighter, free-flowing materials, ensuring efficient transport without overloading the system.
Examples of Optimal Idler Angles for Various Materials and Conveyor Setups
Selecting the optimal conveyor idler angle depends on the type of material being transported and the specific requirements of the conveyor setup. Here are six examples of how different idler angles can be applied to various materials and setups:
- Free-Flowing Materials: For materials such as grains, pellets, or other free-flowing substances, a 20° idler angle is typically optimal. This angle provides sufficient trough depth to contain the material without causing excessive friction or resistance.
- Medium-Density Materials: Materials like sand, gravel, and crushed stone, which have medium density and particle size, benefit from a 35° idler angle. This angle creates a deeper trough that helps contain these materials while ensuring even load distribution and minimizing spillage.
- Heavy Bulk Materials: For transporting heavy bulk materials such as coal, ore, and large aggregates, a 45° idler angle is often the best choice. The steeper angle forms a deep trough that can handle the high load capacity, preventing spillage and ensuring that the material remains stable on the belt.
- High-Speed Conveyors: Conveyor systems operating at high speeds require careful consideration of idler angles to maintain stability and prevent misalignment. A 35° idler angle is generally suitable for high-speed operations, providing a balance between trough depth and belt stability.
- Inclined Conveyors: For conveyors operating on an incline, the idler angle must be adjusted to ensure that the material does not slide back or spill over. A 35° to 45° idler angle is often used for inclined conveyors, depending on the steepness of the incline and the type of material being transported.
- Specialty Materials: Materials with unique properties, such as sticky or cohesive substances, require specific idler angles to prevent buildup and ensure smooth transport. For example, materials prone to sticking may benefit from a 20° to 35° idler angle, combined with specialized idler designs that reduce material adhesion and buildup.
The conveyor idler angle is a critical factor in the performance of conveyor systems. It influences belt tracking, load distribution, and overall system efficiency. By understanding the impact of different idler angles and selecting the optimal angle for specific materials and setups, conveyor systems can achieve reliable, efficient, and safe operation. Properly configured idler angles contribute to longer belt life, reduced maintenance costs, and improved material handling, making them essential in the design and operation of conveyor systems.
Conveyor Idler Angle Alignment
Importance of Proper Idler Alignment in Maintaining Conveyor Efficiency
Conveyor idler alignment is a critical aspect of conveyor system maintenance and operation. Proper alignment of idlers ensures that the conveyor belt runs smoothly, reduces wear and tear on both the belt and the idlers, and prevents costly downtime due to belt misalignment or failure. One of the key factors influencing conveyor efficiency is the conveyor idler angle, which must be correctly set and aligned to maintain optimal performance.
When the conveyor idler angle is properly aligned, the conveyor system operates more efficiently by reducing friction and resistance. This alignment minimizes the risk of material spillage, belt tracking issues, and uneven load distribution. Misaligned idlers can cause the belt to run off-center, leading to increased wear on the belt edges and potential damage to the conveyor structure. In severe cases, misalignment can cause the belt to slip off the idlers entirely, resulting in significant production stoppages and maintenance costs.
Additionally, proper idler alignment helps in maintaining the correct belt tension, which is crucial for the conveyor’s operational stability. Incorrect belt tension can lead to belt slippage, excessive wear, and increased energy consumption. By ensuring that idlers are properly aligned, you can achieve a balance between belt tension and load distribution, which enhances the overall efficiency and longevity of the conveyor system.
Methods for Aligning Idlers and Ensuring Consistent Performance
Achieving and maintaining proper conveyor idler alignment involves several methods and best practices. Here are the key steps to ensure consistent performance:
Regular Inspections and Maintenance
Conducting regular inspections is the first step in maintaining proper idler alignment. During these inspections, check for signs of misalignment, such as uneven belt wear, tracking issues, and unusual noises. Regular maintenance schedules should include inspecting the condition and alignment of idlers, adjusting them as necessary, and replacing any worn or damaged components.
Use of Alignment Tools and Equipment
Using the right tools and equipment is essential for precise idler alignment. Tools such as laser alignment devices, spirit levels, and straight edges can help ensure that idlers are positioned correctly relative to the conveyor belt. Laser alignment devices, in particular, provide accurate measurements and can help quickly identify misaligned idlers, allowing for precise adjustments.
Proper Installation Practices
Ensuring that idlers are installed correctly from the outset is crucial for long-term alignment. During installation, follow manufacturer guidelines and industry best practices to position idlers at the correct conveyor idler angle. This involves aligning the idlers perpendicular to the conveyor frame and parallel to each other. Proper installation helps prevent initial misalignment issues that can lead to more significant problems over time.
Belt Tracking Devices
Installing belt tracking devices can help maintain proper idler alignment by automatically correcting the belt’s path if it starts to run off-center. These devices use sensors and mechanical adjustments to keep the belt aligned with the idlers, reducing the need for manual intervention and ensuring consistent performance.
Training and Education
Providing training and education to maintenance personnel and operators is essential for maintaining proper idler alignment. Staff should be knowledgeable about the importance of alignment, how to identify misalignment issues, and the correct procedures for adjusting idlers. Regular training sessions and access to up-to-date resources can help ensure that everyone involved in conveyor maintenance understands the critical role of idler alignment.
Alignment Techniques
Several alignment techniques can be used to ensure proper idler alignment, including:
- Visual Inspection: Regular visual inspections can help identify misaligned idlers. Look for signs such as uneven belt wear, material spillage, and belt tracking issues. Use a straight edge or string line to check for alignment along the length of the conveyor.
- Laser Alignment: Laser alignment tools provide precise measurements and are highly effective for aligning idlers. These tools project a laser beam along the conveyor frame, allowing for accurate adjustment of idlers to ensure they are parallel and perpendicular to the belt.
- String Line Method: The string line method involves stretching a string along the length of the conveyor frame, parallel to the belt. By adjusting the idlers to align with the string, you can ensure that they are properly positioned. This method is simple yet effective for maintaining alignment.
- Measuring Tape and Level: Using a measuring tape and spirit level can help ensure that idlers are positioned at the correct height and angle. Measure the distance between idlers and use the level to check that they are aligned both vertically and horizontally.
Continuous Monitoring and Adjustment
Conveyor systems are dynamic and subject to constant movement and vibration. Continuous monitoring and adjustment are necessary to maintain proper idler alignment over time. Use condition monitoring systems to track the performance of the conveyor and identify any alignment issues early. Make adjustments as needed to ensure consistent performance.
Documenting and Recording Alignment Activities
Maintaining detailed records of alignment activities can help track the performance of the conveyor system and identify recurring issues. Document inspections, adjustments, and maintenance activities, including the specific idlers adjusted and the methods used. This documentation can provide valuable insights for future maintenance and help identify patterns that may indicate underlying problems.
Proper conveyor idler alignment is essential for maintaining the efficiency and longevity of conveyor systems. By ensuring that idlers are correctly aligned, you can reduce friction, minimize wear and tear, and prevent costly downtime. The conveyor idler angle plays a crucial role in this process, and it is important to use the right tools, techniques, and practices to achieve and maintain alignment.
Regular inspections, the use of alignment tools, proper installation practices, and continuous monitoring are all critical components of effective idler alignment. Additionally, providing training and education to maintenance personnel and documenting alignment activities can help ensure consistent performance and identify potential issues early.
By prioritizing conveyor idler alignment, you can enhance the reliability and efficiency of your conveyor system, leading to increased productivity and reduced maintenance costs. Remember, a well-aligned conveyor system is not only more efficient but also safer and more durable, making it a vital aspect of material handling operations in various industries.
Case Studies of Conveyor Idler Angle
Real-World Examples of Conveyor Idler Angle Optimization
The optimization of conveyor idler angles plays a crucial role in enhancing the performance and efficiency of conveyor systems across various industries. Here are six real-world examples where adjusting the conveyor idler angle has led to significant improvements:
- Mining Industry: In a large-scale mining operation, the transportation of heavy bulk materials such as ore required the optimization of idler angles to prevent spillage and ensure efficient transport. By adjusting the idler angles to 45°, the system formed a deeper trough that effectively contained the heavy ore, reducing material loss and improving overall conveyor efficiency.
- Cement Production: A cement plant faced challenges with the transport of raw materials, including limestone and clay. The initial setup with a 20° idler angle resulted in frequent spillage and belt misalignment. By switching to a 35° idler angle, the plant achieved better load containment and reduced spillage, leading to smoother operation and lower maintenance costs.
- Agriculture: In a grain processing facility, free-flowing materials like wheat and corn were transported using conveyors with a 20° idler angle. This angle provided sufficient trough depth to contain the grains without causing excessive friction or resistance, ensuring efficient handling and minimizing grain loss.
- Port Terminals: A port terminal handling bulk commodities such as coal and iron ore optimized its conveyor idler angles to manage varying load capacities. For heavier loads, a 45° idler angle was employed, creating a deep trough that could handle the high volume and weight of the materials, reducing spillage and enhancing throughput.
- Recycling Plants: A recycling facility dealing with a mix of materials, including metals, plastics, and paper, optimized its conveyor system by adjusting the idler angles. A 35° angle was found to be ideal for creating a stable trough that could handle the diverse material types, improving material flow and reducing the risk of blockages.
- Food Processing: In a food processing plant, conveyor systems were used to transport various food products. By optimizing the idler angles to 20° for light, free-flowing products like rice and 35° for heavier items like potatoes, the plant achieved efficient material handling with minimal spillage and contamination.
Case Studies Showcasing Improvements
The following case studies highlight the significant improvements in conveyor performance achieved through the adjustment of conveyor idler angles:
Request more details about our Conveyor idler by filling out this form.
- Copper Mine Conveyor System Background: A copper mine experienced frequent material spillage and belt misalignment in its conveyor system, leading to operational inefficiencies and high maintenance costs. Solution: After analyzing the conveyor setup, the idler angles were adjusted from 20° to 45°. This adjustment formed a deeper trough, effectively containing the heavy copper ore. Results: The optimization led to a 30% reduction in material spillage, improved belt alignment, and a 20% increase in overall conveyor throughput.
- Cement Plant Raw Material Handling Background: A cement plant faced issues with the transport of limestone and clay, including frequent spillage and uneven load distribution. Solution: The idler angles were optimized to 35°, creating a stable trough that better contained the raw materials. Results: The plant saw a significant reduction in material spillage, improved load distribution, and a decrease in maintenance downtime, leading to a 15% increase in production efficiency.
- Grain Processing Facility Background: A grain processing facility struggled with efficient transport of wheat and corn, experiencing grain loss and reduced efficiency. Solution: By adjusting the idler angles to 20°, the facility achieved better containment of the free-flowing grains. Results: The optimization resulted in a 25% reduction in grain loss, smoother conveyor operation, and enhanced processing efficiency.
- Port Terminal Bulk Handling Background: A port terminal handling coal and iron ore faced challenges with spillage and load management, affecting throughput. Solution: The idler angles were adjusted to 45° for heavier loads, improving material containment. Results: The terminal experienced a 20% increase in throughput, reduced spillage, and lower operational costs.
- Recycling Facility Conveyor System Background: A recycling facility dealt with blockages and inefficient material flow due to diverse material types. Solution: The idler angles were optimized to 35°, creating a stable trough for mixed materials. Results: The facility achieved a 15% increase in material flow efficiency, fewer blockages, and improved system reliability.
- Food Processing Plant Conveyor Optimization Background: A food processing plant faced challenges with material spillage and contamination during transport. Solution: The idler angles were adjusted to 20° for light products and 35° for heavier items. Results: The plant saw a 20% reduction in spillage, improved hygiene, and enhanced overall efficiency.
Optimizing the conveyor idler angle is a critical aspect of improving conveyor system performance across various industries. By understanding and adjusting the idler angles to suit specific materials and operational requirements, significant improvements in material handling efficiency, load distribution, and overall system reliability can be achieved. These real-world examples and case studies demonstrate the tangible benefits of idler angle optimization, highlighting its importance in the design and maintenance of efficient conveyor systems.
FAQs about Conveyor Idler Angle
The angle of a troughed conveyor idler, crucial for forming the belt into a trough shape, typically ranges between 20, 35, and 45 degrees. These angles help in stabilizing and supporting the belt and the material carried. The choice of angle depends on the type of material transported and other design considerations of the conveyor system. For instance, a shallower angle may suffice for fine, granular materials, while steeper angles can be more effective for larger, lumpier materials. The design of these idlers ensures that they effectively support the load and avoid spillage, increasing the efficiency of material transport.
Impact idlers are designed with angles that can vary between 20 and 45 degrees, much like troughed conveyor idlers. Their primary function is to absorb the shock and impact at loading points where material falls onto the conveyor belt. This reduces wear and extends the lifespan of the belt. The specific angle chosen for an impact idler often aligns with the troughing angles utilized across the conveyor system to ensure consistent support and minimize spillage. Selecting the correct angle for impact idlers is imperative as it significantly influences the conveyor belt’s functionality and durability in handling loads.
The optimal angle for a conveyor belt depends on several factors, including the type of material being transported and the specific requirements of the conveyor system. For general transport, belts may function well at angles up to 20 degrees when equipped with a plain or smooth surface. For materials with a risk of slippage or roll-back, belts with cleats or ribs, designed for higher angles, can be employed, sometimes achieving inclines of up to 45 degrees. It is crucial to consult technical specifications and possibly conduct a material test to determine the most efficient angle for the conveyor, keeping in mind the material’s properties and the conveyor’s design.
The angle of repose in a conveyor refers to the steepest angle at which a piled-up bulk material is stable without slippage or movement down the pile. This angle is key in determining how material behaves when loaded onto a conveyor belt and affects the design of the conveyor system. Typical values for the angle of repose range from about 30 degrees for materials like sand to 45 degrees for angular stones. Conveyors handling materials with a high angle of repose might require specific features like higher sidewalls or ribbed belts to manage the material effectively and prevent spillage. This parameter is crucial for ensuring safe and efficient conveyor operations, particularly when moving bulk materials.
Last Updated on August 16, 2024 by Jordan Smith
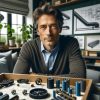
Jordan Smith, a seasoned professional with over 20 years of experience in the conveyor system industry. Jordan’s expertise lies in providing comprehensive solutions for conveyor rollers, belts, and accessories, catering to a wide range of industrial needs. From initial design and configuration to installation and meticulous troubleshooting, Jordan is adept at handling all aspects of conveyor system management. Whether you’re looking to upgrade your production line with efficient conveyor belts, require custom conveyor rollers for specific operations, or need expert advice on selecting the right conveyor accessories for your facility, Jordan is your reliable consultant. For any inquiries or assistance with conveyor system optimization, Jordan is available to share his wealth of knowledge and experience. Feel free to reach out at any time for professional guidance on all matters related to conveyor rollers, belts, and accessories.