Conveyor Idler Bearing: Key Components Beneath the Belt
Conveyor idler bearings are pivotal components in the world of material handling, playing a crucial role in the smooth and efficient operation of conveyor systems. Conveyor idler bearing is integral to the conveyor idler rollers, ensuring that they rotate effectively, thereby facilitating the movement of the conveyor belt with minimal friction and resistance. The performance and longevity of a conveyor system heavily depend on the quality and maintenance of these bearings.
Understanding Conveyor Idler Bearing: Definition, Function, and Role in Material Handling
Conveyor idler bearings are key elements in the operation of conveyor systems, particularly in the realm of material handling. Conveyor idler bearings enable idler rollers to rotate smoothly, supporting the conveyor belt and reducing friction for efficient movement.
Definition and Function in Material Handling
Definition: Conveyor idler bearings are mechanical devices that provide a low-friction surface for the idler rollers to rotate against. They are typically cylindrical or spherical and are housed within the idler assembly. These bearings are crucial for the smooth operation of the conveyor belt, as they allow the rollers to turn without excessive resistance.
Function: The main function of conveyor idler bearings is to minimize the friction that occurs when the idler rollers rotate. This is essential for the efficient movement of the conveyor belt, especially over long distances or when transporting heavy loads. By reducing friction, these bearings help in conserving energy and reducing wear on the conveyor system.
Role in Maintaining Conveyor Belt Tension and Path
Conveyor Belt Tension: Idler bearings are instrumental in maintaining the appropriate tension of the conveyor belt. Properly functioning bearings ensure that the idler rollers provide consistent and even support to the belt. This uniform support is necessary to prevent issues like belt slippage, excessive stretching, or sagging, all of which can affect the efficiency and lifespan of the conveyor system.
Conveyor Belt Path: The alignment and placement of conveyor idler bearings are critical in maintaining the desired path of the conveyor belt. The bearings must be precisely positioned within the conveyor idler assembly to ensure that the belt remains aligned and follows its intended trajectory. This alignment is crucial for the even distribution of materials on the belt and to prevent spillage or uneven wear.
Types of Conveyor Idler Bearings: Diversity for Various Applications
Conveyor systems, integral to material handling across numerous industries, rely heavily on various types of idler bearings. Conveyor idler bearings are designed to meet the specific needs of different conveyor applications, ensuring efficiency and longevity of the conveyor belts.
Different Types of Idler Bearing
1. Sealed-Type Deep Groove Ball Bearings: These are among the most commonly used bearings in conveyor systems. Known for their versatility, these bearings are designed to handle both radial and axial loads efficiently. The sealed design helps in preventing the ingress of contaminants, thus prolonging the bearing’s life. They are particularly useful in environments where the conveyor system is exposed to dust and moisture.
2. Spherical Roller Bearings: Ideal for heavy-load applications, spherical roller bearings can accommodate misalignment while handling high radial loads. This makes them suitable for conveyors that undergo heavy stress, such as those in mining and quarrying operations.
3. Tapered Roller Bearings: These bearings are designed to handle large radial and thrust loads, making them suitable for applications where the conveyor belt experiences significant force or load. Their tapered design allows them to efficiently manage the combination of radial and axial loads.

Specific Idler Bearings for Various Conveyor Applications
Troughing Idlers: These idlers, used to shape the conveyor belt into a trough for transporting bulk materials, typically employ spherical roller bearings or deep groove ball bearings. The choice depends on the load and speed of the conveyor. The bearings in these idlers must be capable of handling both the weight of the materials and the dynamic forces exerted by the moving belt.
Impact Idlers: Positioned at the loading points where material is dropped onto the belt, impact idlers require robust bearings that can absorb significant shock and impact. Spherical roller bearings are often used in these idlers due to their high load-carrying capacity and ability to tolerate misalignment.
Return Idlers: These idlers support the return path of the conveyor belt and generally face less load compared to carrying idlers. Sealed-type deep groove ball bearings are commonly used in return idlers for their efficiency and durability in less demanding conditions.
Each type of idler bearing offers unique advantages and is chosen based on the specific requirements of the conveyor application, including load capacity, belt speed, environmental conditions, and the nature of the materials being transported. Understanding the characteristics and suitable applications of these bearings is crucial for ensuring the optimal performance and longevity of conveyor systems.
Conveyor Idler Bearing Specifications: Size, Selection Factors, and Design Insights
Conveyor Idler Bearing Size Chart and Dimensions
Size Chart and Dimensions: Conveyor idler bearings come in various sizes and dimensions, tailored to different types of conveyor systems. A size chart typically includes the bearing’s outer diameter, inner diameter, width, and load rating. These dimensions are critical in ensuring that the bearing fits perfectly within the idler assembly and can adequately support the conveyor belt and the materials being transported.
Custom Dimensions: In some cases, bearings may need to be custom-sized to fit specific conveyor idler rollers, especially in custom or specialized conveyor systems. This requires precise measurements and an understanding of the load and speed requirements of the conveyor.
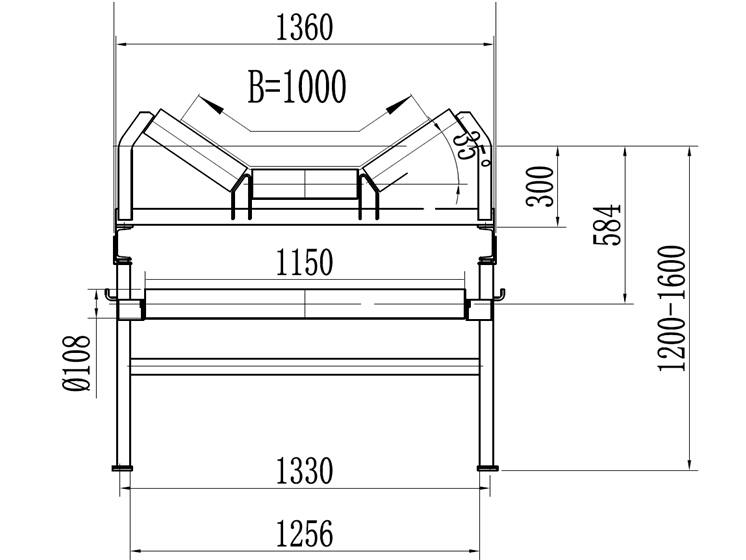
Factors Influencing the Selection of Idler Bearings
Load Capacity: One of the primary factors in selecting idler bearings is their load capacity. Bearings must be able to support the weight of the conveyor belt and the materials being transported without deforming or failing. The load capacity of the bearing should align with the maximum expected load on the conveyor system.
Speed: The operational speed of the conveyor belt also influences the choice of bearings. Higher speeds require bearings that can handle higher rotational forces and have lower friction coefficients to minimize heat generation and wear.
Environmental Conditions: The operating environment is a crucial consideration. Bearings used in environments with high levels of dust, moisture, or corrosive materials may need enhanced sealing and corrosion-resistant materials to ensure longevity and reliability.
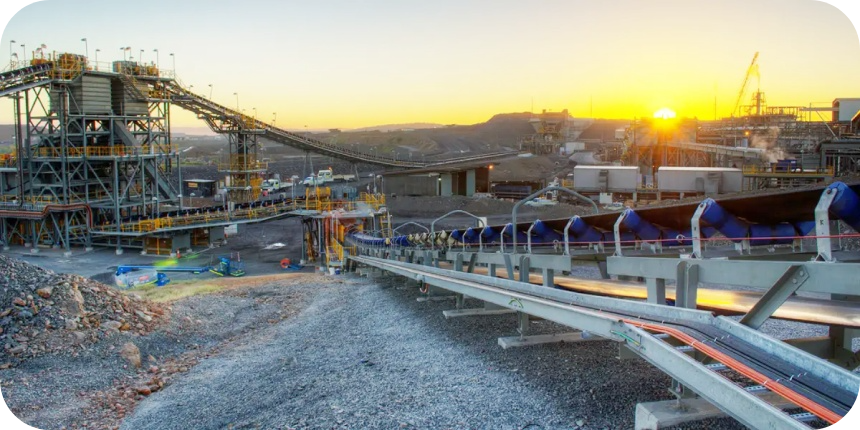
Insights into the Design and Material of Conveyor Idler Rollers
Design Considerations: The design of conveyor idler rollers must complement the bearings used. This includes aspects like the roller’s shell thickness, shaft size, and the type of sealing system employed. The design should ensure that the bearings are adequately protected and can operate efficiently under the given load and environmental conditions.
Material Selection: The materials used for idler rollers and bearings are selected based on the application and environmental factors. Common materials include steel for high-strength applications and polymers or composites for corrosion resistance and lighter weight. The material choice impacts the bearing’s durability, weight, and overall performance of the conveyor system.
Conveyor Idler Bearing Replacement and Maintenance: Ensuring Longevity and Efficiency
Guidelines for Replacement of Conveyor Idler Bearings
When to Replace: Conveyor idler bearings should be replaced as part of regular maintenance schedules or when signs of wear and tear are evident. Common indicators include unusual noises (like grinding or squeaking), visible damage to the bearing, or a decrease in conveyor efficiency. A preventive maintenance schedule, based on the manufacturer’s recommendations and the specific operating conditions, is ideal for timely replacements.
How to Replace: Replacing conveyor idler bearings involves several steps
1. Safety First: Ensure the conveyor system is turned off and locked out to prevent accidental start-up.
2. Access the Bearing: Remove the conveyor belt or the idler assembly to access the bearings.
3. Remove the Old Bearing: Gently extract the old bearing, paying attention to its positioning and noting any spacers or seals present.
4. Install the New Bearing: Install the new bearing following the orientation of the previous one, making sure it is correctly positioned and all parts are properly aligned.
5. Reassemble: Reassemble the idler and conveyor belt, ensuring everything is aligned and tightened to the correct specifications.
Tips for Maintaining Idler Bearings
Regular Inspection: Conduct regular inspections to check for signs of wear, misalignment, or damage. Pay special attention to noise, vibration, and changes in performance.
Lubrication: Lubricate the bearings as per manufacturer’s instructions, using the right lubricant in appropriate amounts to prevent over-lubrication.
Cleanliness: Keep the conveyor and its components clean. Dirt, dust, and debris can lead to premature bearing failure.
Alignment and Tension: Regularly check the alignment of the conveyor idler rollers and the tension of the belt. Misalignment or incorrect tension can put extra stress on the bearings.
Identifying and Troubleshooting Common Issues
Symptoms of a Bad Idler Pulley Bearing
Unusual noises like grinding, squealing, or rattling.
Excessive heat generation from the bearing area.
Visible wear or damage to the bearing.
Irregular movement or seizing of the idler roller.
Troubleshooting
Noise or Vibration: Check for lubrication issues or physical damage to the bearing.
Heat Generation: Inspect for over-lubrication, misalignment, or overloading.
Seized Roller: Look for contamination, lack of lubrication, or physical damage.
Practical Applications and Case Studies: Conveyor Idler Bearings in Action
Real-World Examples of Conveyor Idler Bearing Applications
1. Mining Industry: In mining operations, conveyor systems are used to transport heavy and abrasive materials over long distances. Idler bearings in these conveyors must withstand heavy loads and abrasive conditions. Spherical roller bearings are commonly used for their ability to handle misalignment and heavy loads, ensuring smooth operation in the harsh mining environment.
2. Agriculture: Conveyors in agriculture are used for moving grain and other products. Here, durability and resistance to dust and debris are crucial for idler bearings. Sealed-type deep groove ball bearings are often chosen for their ability to protect against contaminants while providing reliable performance.
3. Manufacturing and Packaging: Conveyor systems in manufacturing and packaging facilities often require high precision and speed. Tapered roller bearings are used in these applications for their ability to handle combined loads and high speeds, ensuring efficient and consistent movement of goods.
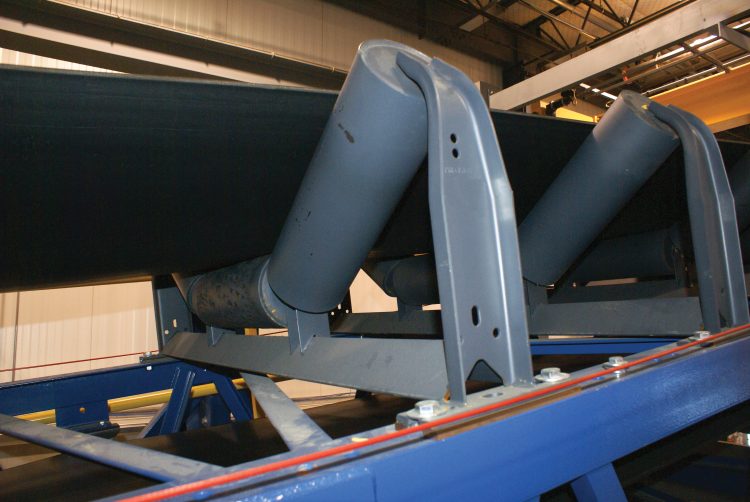
Case Studies Highlighting the Importance of Correct Idler Bearing Selection and Maintenance
Bulk Material Handling Facility: A facility experienced frequent conveyor breakdowns due to bearing failures. Investigation revealed that the idler bearings were not suited for the high load and abrasive conditions. Switching to spherical roller bearings designed for high-load applications significantly reduced downtime and maintenance costs.
Food Processing Plant: A food processing plant faced issues with conveyor belt misalignment and premature bearing wear. The problem was traced back to improper idler bearing selection and poor maintenance practices. Implementing a regular maintenance schedule and selecting bearings suitable for the operating conditions (sealed bearings for protection against food particles and moisture) led to improved conveyor reliability and efficiency.
E-commerce Fulfillment Center: An e-commerce fulfillment center needed to increase the speed of their conveyor systems to handle peak demand. The existing bearings were not capable of handling the increased speed, leading to overheating and failures. Upgrading to high-speed tapered roller bearings, along with enhanced lubrication practices, allowed the center to increase conveyor speeds while maintaining reliability.
These real-world examples and case studies underscore the critical importance of selecting the right conveyor idler bearings for specific industry applications and the necessity of regular maintenance. Correct bearing selection and diligent maintenance are key to avoiding costly downtime, extending the life of conveyor systems, and ensuring smooth and efficient operations across various industries.
Future Trends in Conveyor Idler Bearing Technology
Emerging Trends and Technologies in Conveyor Idler Bearings
1. Smart Technology Integration: The integration of smart sensors and IoT (Internet of Things) technology in conveyor idler bearings is a significant trend. These smart bearings can monitor their own condition, including temperature, vibration, and load capacity, providing real-time data for predictive maintenance. This technology helps in identifying potential issues before they lead to system failures, thereby reducing downtime and maintenance costs.
2. Advanced Materials and Coatings: Advancements in bearing materials and coatings are enhancing strength-to-weight ratios, wear resistance, and friction reduction, while new coatings improve durability in extreme temperatures and corrosive conditions.
3. Energy-Efficient Designs: There is a growing focus on designing conveyor idler bearings that are more energy-efficient. This includes optimizing bearing designs to reduce friction and energy loss, which not only saves energy but also reduces the heat generated, thereby prolonging the life of the bearings.
Optimize operations with our advanced conveyor idlers. Act fast and connect!
Sustainability and Efficiency in Future Idler Bearing Designs
Eco-Friendly Materials: The trend towards sustainability is driving the use of eco-friendly materials in bearing manufacturing. This includes recycled materials and those with a lower environmental impact in terms of production and disposal.
Reduced Lubrication Needs: The development of self-lubricating bearings or those requiring less frequent lubrication contributes to sustainability. This reduces the environmental impact associated with lubricant disposal and minimizes the need for maintenance.
Lifecycle Analysis and Circular Economy: Future designs are expected to focus more on the entire lifecycle of the bearings, from production to disposal. This aligns with the principles of the circular economy, aiming to create products that are more sustainable throughout their lifecycle.
Energy Conservation: With the increasing focus on energy conservation, future conveyor idler bearings are likely to be designed for maximum efficiency. This includes reducing the overall weight of the bearings and optimizing their design to minimize energy consumption during operation.
FAQs about Conveyor Idler Bearing
An idler in a conveyor system is a roller, usually cylindrical, that supports the conveyor belt and guides its movement without driving it.
Typically, sealed-type deep groove ball bearings are used in idlers for their ability to handle both radial and axial loads efficiently.
Conveyors commonly use deep groove ball bearings, spherical roller bearings, and tapered roller bearings, depending on the load and application.
In conveyor systems, various types of bearings are utilized to ensure smooth, efficient, and reliable operation. The selection of bearings depends on factors such as the load capacity, speed of operation, environmental conditions, and maintenance requirements. The most common types of bearings used in conveyors include:
Ball Bearings: Suitable for low to medium load applications and capable of handling both radial and axial loads efficiently.
Roller Bearings: They are preferred for applications subjected to high radial loads and are available in cylindrical, spherical, and tapered variations to cater to different operational needs.
Spherical Roller Bearings: Ideal for accommodating misalignment and shaft deflection while handling high loads, common in bulk material handling conveyors.
Needle Roller Bearings: Used in applications where space is constrained, offering high load capacity and stiffness.
Plain Bearings (Bushings): Simple in design and used in non-rotating or slow-speed applications, providing a cost-effective solution for load support.
Proper bearing selection and maintenance are vital for the longevity and efficiency of conveyor systems, impacting overall operational productivity and downtime.
Idlers support the conveyor belt and control its path, providing a smooth surface for the belt to travel over and helping to maintain tension and alignment.
There are several types of idlers, including carrying idlers, return idlers, impact idlers, self-aligning idlers, and troughing idlers.
A conveyor idler typically consists of a cylindrical roller, a frame or bracket to hold the roller, bearings inside the roller, and shafts connecting the roller to the frame.
An idler bearing is an integral component often found in machinery, particularly in conveyor systems, automotive engines, and various pulley applications. Its primary function is to guide and support a rotating shaft or belt. In essence, it serves as a pivot or guide that facilitates the smooth and efficient operation of the mechanical system it’s part of. The design of an idler bearing is crucial for minimizing friction and wear, thereby extending the operational lifespan of the machinery. It typically consists of a sealed bearing unit that is pressed into a housing, which can be made from various materials depending on the application requirements. The selection of an idler bearing is critical, as it must withstand the operational loads, speeds, and environmental conditions it will be exposed to, ensuring reliability and performance of the overall system.
A conveyor idler is a mechanical component used extensively in bulk material handling systems, especially in conveyor belt systems. It is primarily designed to support the conveyor belt and the material being transported along the length of the conveyor. A typical conveyor idler consists of a cylindrical shape known as a drum or a roll, mounted on bearings that allow it to rotate freely. Conveyor idlers are strategically placed along the conveyor frame to ensure that the belt maintains the correct tension, alignment, and does not sag excessively under the weight of the material. There are different types of conveyor idlers, such as impact idlers, which absorb the shock of heavy materials falling on the conveyor belt, and return idlers, which support the belt on its return journey. The design and spacing of these idlers can significantly influence the efficiency and durability of a conveyor system.
The tensioner bearing plays a crucial role in automotive and industrial applications, serving primarily to maintain the correct tension on belts and chains within various systems, such as the timing belt in car engines or the drive belts in mechanical systems. This is essential for ensuring that the belt or chain operates smoothly, efficiently, and without slippage or excessive wear. The appropriate tension maintained by the tensioner bearing helps in achieving optimal performance of the system it is part of, contributing to the overall reliability and longevity of the machinery. Beyond maintaining tension, tensioner bearings also compensate for wear and stretch that occur over time in belts and chains, and aid in vibration dampening. The tensioner itself usually consists of a pulley mounted on a spring-loaded arm or a hydraulic actuator, with the bearing allowing the pulley to rotate freely under the tension.
Last Updated on June 6, 2024 by Jordan Smith
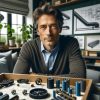
Jordan Smith, a seasoned professional with over 20 years of experience in the conveyor system industry. Jordan’s expertise lies in providing comprehensive solutions for conveyor rollers, belts, and accessories, catering to a wide range of industrial needs. From initial design and configuration to installation and meticulous troubleshooting, Jordan is adept at handling all aspects of conveyor system management. Whether you’re looking to upgrade your production line with efficient conveyor belts, require custom conveyor rollers for specific operations, or need expert advice on selecting the right conveyor accessories for your facility, Jordan is your reliable consultant. For any inquiries or assistance with conveyor system optimization, Jordan is available to share his wealth of knowledge and experience. Feel free to reach out at any time for professional guidance on all matters related to conveyor rollers, belts, and accessories.