Mastering Conveyor Idler Degrees: A Comprehensive Guide
Conveyor systems are crucial in numerous industries, including mining, manufacturing, and logistics, for efficient material handling. Central to these systems are conveyor idlers, which support and guide the conveyor belt, ensuring smooth and reliable operation. The angle at which these idlers are set, known as the conveyor idler degree, plays a pivotal role in the system’s performance and efficiency. Properly selected conveyor idler degrees enhance load distribution, reduce belt wear, and improve material containment, thereby optimizing the overall functionality and lifespan of the conveyor system. Understanding and selecting the correct conveyor idler degree is essential for achieving maximum operational efficiency.
What is a Conveyor Idler?
Definition and Function of Conveyor Idlers
Conveyor idlers are essential components in conveyor systems, designed to support and guide the conveyor belt, ensuring it runs smoothly and efficiently. These cylindrical rollers are strategically placed along the conveyor’s length to carry the load and maintain belt alignment. Conveyor idlers minimize friction between the belt and the conveyor structure, reducing wear and tear and extending the belt’s lifespan. By providing support and stability, idlers play a crucial role in optimizing the conveyor system’s performance and reliability.
Types of Conveyor Idlers
Conveyor idlers come in various types, each designed for specific functions and operational requirements. Understanding these different types is key to selecting the right idler for your conveyor system. The following table outlines the main types of conveyor idlers:
Importance of Idler Placement and Alignment
The placement and alignment of conveyor idlers are critical for the efficient operation of a conveyor system. Proper idler placement ensures that the belt is adequately supported throughout its entire length, preventing sagging and material spillage. Misalignment of idlers can lead to various operational issues, including belt mistracking, increased wear and tear, and reduced system efficiency.
Conveyor Idler Degree and Its Impact
One of the key factors in idler placement is the conveyor idler degree, which refers to the angle at which the idlers are set relative to the horizontal plane. This angle determines the trough depth and shape of the conveyor belt, affecting load distribution and material containment. A correctly selected conveyor idler degree enhances the system’s performance by optimizing belt support and minimizing material spillage. Conversely, an incorrect idler degree can lead to poor belt tracking, increased maintenance costs, and operational inefficiencies.
Optimizing Idler Placement and Alignment
To achieve optimal idler placement and alignment, several factors need to be considered:
- Conveyor Belt Characteristics: The type, width, and thickness of the conveyor belt influence the selection of idler types and their placement. Heavier belts and wider widths require more robust idlers and precise alignment.
- Material Properties: The nature of the material being conveyed, including its size, weight, and abrasiveness, affects idler selection and placement. For instance, impact idlers are essential at loading points where heavy or sharp materials are introduced to the conveyor.
- Conveyor Layout: The design and layout of the conveyor system, including its length, incline, and curvature, determine the number and spacing of idlers. Troughing idlers are typically spaced closer together on the carry side to provide adequate support, while return idlers can be spaced further apart.
- Environmental Conditions: Operating conditions such as temperature, humidity, and exposure to corrosive substances can impact idler performance. Selecting idlers with appropriate coatings and materials can enhance durability and reduce maintenance needs.
Conveyor Idler Degree in Practice
Implementing the correct conveyor idler degree requires careful consideration and precise calculations. Engineers and designers use industry standards and guidelines, such as those provided by the Conveyor Equipment Manufacturers Association (CEMA), to determine the optimal idler angle for specific applications. Factors like belt speed, load capacity, and material characteristics are taken into account to ensure the selected conveyor idler degree maximizes operational efficiency and minimizes potential issues.
Understanding the various types of conveyor idlers and their specific functions is crucial for designing and maintaining efficient conveyor systems. The correct placement and alignment of idlers, particularly with regard to the conveyor idler degree, are essential for achieving optimal performance and longevity of the conveyor system. By carefully selecting and positioning idlers, operators can ensure smooth operation, reduce maintenance costs, and enhance the overall productivity of their material handling processes.
What are Conveyor Idler Degrees
Conveyor idler degrees play a crucial role in the functionality and efficiency of conveyor systems. Understanding this term is essential for anyone involved in conveyor design, maintenance, or operation. This section will delve into the concept of conveyor idler degrees, explaining their significance, how they impact the trough shape of the conveyor belt, and common angles used in conveyor systems.
Explanation of Conveyor Idler Degree
In conveyor systems, the term “conveyor idler degree” refers to the angle at which idlers are installed on the conveyor frame. Idlers are cylindrical rollers that support and guide the conveyor belt along its path. The degree of these idlers is measured from the horizontal plane. It determines the troughing angle of the conveyor belt, which is crucial for ensuring proper belt alignment, material containment, and efficient material transport.
Impact of Idler Angle on Trough Shape
The angle of idlers significantly affects the trough shape of the conveyor belt. Troughing idlers are typically installed at specific angles to create a troughed belt conveyor. This troughed shape allows the conveyor belt to carry more material and prevents spillage along the conveyor length.
- 20-Degree Idlers: This angle is often used for conveying materials with fine particles or granular materials. The trough shape created by 20-degree idlers provides sufficient containment for these types of materials while maintaining a relatively flat profile.
- 35-Degree Idlers: Conveyor systems with 35-degree idlers are commonly used for handling bulk materials such as coal, ore, and aggregates. The steeper angle of 35 degrees allows for greater material containment and higher capacity compared to lower angles.
- 45-Degree Idlers: These idlers are used in applications where steep inclines or vertical lifts are required. The 45-degree angle creates a deep trough that can handle large volumes of material while minimizing the risk of material rollback.
Typical Angles Used in Conveyor Systems
While 20, 35, and 45 degrees are common angles for idlers in conveyor systems, other angles may be used depending on the specific requirements of the application. For example, idlers with angles less than 20 degrees are sometimes used for very fine materials or when space constraints limit the conveyor’s incline.
It’s important to note that the selection of idler angle should be based on factors such as material characteristics, conveyor length, capacity requirements, and environmental conditions. Proper selection and installation of idlers are essential for the smooth and efficient operation of conveyor systems.
Conveyor idler degrees refer to the angle at which idlers are installed on a conveyor frame. This angle determines the trough shape of the conveyor belt, which is critical for material containment and efficient material transport. Common angles used in conveyor systems include 20, 35, and 45 degrees, each serving specific purposes based on material handling requirements. Understanding conveyor idler degrees is key to designing, operating, and maintaining effective conveyor systems.

Conveyor Idler Degree Chart
In the realm of conveyor systems, understanding the significance of a conveyor idler degree chart cannot be overstated. This essential tool serves as a comprehensive guide for selecting the correct idler angles, ensuring optimal conveyor performance and material handling efficiency. Let’s delve into the key aspects of this chart, including its importance, an illustrative example, and practical usage.
Importance of Having a Degree Chart for Selecting the Right Idler Angles
A conveyor idler degree chart is invaluable for several reasons. Firstly, it provides a clear overview of the available idler angles, typically ranging from 10 to 45 degrees, and their respective applications. This clarity is essential for conveyor designers and operators, enabling them to make informed decisions based on the specific requirements of their material handling tasks.
Secondly, the chart serves as a reference tool for ensuring proper conveyor belt tracking and alignment. The angle of the idlers directly influences the shape of the conveyor belt’s trough, which, in turn, affects the way the material is conveyed. Incorrect idler angles can result in belt misalignment, material spillage, and increased wear and tear on the conveyor system. By consulting the degree chart, operators can select the optimal idler angles to mitigate these issues and maintain conveyor efficiency.
Why a Conveyor Idler Degree Chart is Crucial
- Efficiency and Optimization: Using a conveyor idler degree chart helps optimize the performance of the conveyor system by ensuring that the idlers are set at the correct angles. This optimization can lead to improved material containment, reduced spillage, and enhanced load distribution, ultimately boosting the system’s efficiency.
- Standardization: The chart standardizes the selection process, providing a consistent reference that can be used across different projects and applications. This standardization helps in maintaining uniformity and reliability in conveyor system design and operation.
- Time-Saving: Having a readily available degree chart saves time by streamlining the decision-making process. Engineers and operators can quickly refer to the chart to determine the appropriate idler angles, reducing the need for extensive calculations and trial-and-error approaches.
- Cost-Effectiveness: Proper selection of idler angles can prevent issues such as belt misalignment, excessive wear, and material spillage. By using a conveyor idler degree chart, companies can avoid costly repairs and downtime, thereby saving money in the long run.
Example of a Conveyor Idler Degree Chart
A typical conveyor idler degree chart includes various angles and their recommended applications. Here is an example of what such a chart might look like:
A typical conveyor idler degree chart includes a range of idler angles, such as 20, 35, and 45 degrees, along with corresponding descriptions of their applications. For instance, a 20-degree idler angle is commonly used for conveying materials with a moderate abrasiveness and flowability, such as coal, gravel, and sand. On the other hand, a 35-degree idler angle is suitable for handling more abrasive and challenging materials, such as ores and minerals. Finally, a 45-degree idler angle is ideal for conveying sticky or cohesive materials, such as clay or sugar.
How to Use the Chart to Determine the Appropriate Idler Angle
Using a conveyor idler degree chart is a straightforward process that involves identifying the material handling needs and selecting the appropriate idler angle based on the chart’s recommendations. Here’s a step-by-step guide:
- Identify the Material Characteristics: Determine the nature of the material to be conveyed, including its abrasiveness, flowability, and adhesion properties.
- Consult the Degree Chart: Refer to the conveyor idler degree chart to find the recommended idler angle(s) for the identified material characteristics.
- Select the Idler Angle: Choose the idler angle that best suits the material handling needs, considering factors such as material type, conveyor speed, and load capacity.
- Adjust as Necessary: Depending on the specific requirements of the material handling task, you may need to adjust the idler angle or consider other factors, such as idler spacing and roller diameter.
- Monitor Performance: Regularly monitor the conveyor system’s performance to ensure that the selected idler angle is achieving the desired results. Adjustments may be necessary over time to optimize conveyor efficiency.
A conveyor idler degree chart is an indispensable tool for conveyor system design and operation. By understanding its importance, studying its example, and mastering its usage, operators can ensure the smooth and efficient handling of materials, minimizing downtime and maximizing productivity.
Calculation of Conveyor Idler Degrees
In the design and operation of conveyor systems, calculating the idler angles is crucial for ensuring the efficiency and longevity of the system. The idler angles, often referred to as the idler degree, determine the optimal positioning of the idler sets along the conveyor belt. This section will discuss the basic principles, formulas, and factors influencing the calculation of idler angles, along with a step-by-step guide on how to perform these calculations.
Basic Principles and Formulas
The idler angle, denoted by θ (theta), is the angle between the conveyor belt and the vertical plane. It is calculated based on the conveyor’s inclination angle, material properties, belt speed, and other factors. The formula for calculating the idler angle is:
Idler Angle(θ)=arctan(H/L)
Where:
H is the vertical distance between the center of the idler and the conveyor frame.
L is the horizontal distance between the center of the idler and the conveyor frame.
Factors Influencing the Calculation
Several factors influence the calculation of idler angles:
- Material Type: Different materials have varying properties, such as coefficient of friction and bulk density, which affect the idler angles needed for optimal performance.
- Belt Speed: The speed at which the conveyor belt moves impacts the forces acting on the idlers, affecting the required idler angles.
- Load Capacity: The weight of the material being conveyed affects the downward force on the belt, influencing the idler angles.
- Conveyor Inclination Angle: The angle at which the conveyor is inclined affects the vertical and horizontal distances between the idler and the frame.
- Idler Diameter: Larger idler diameters can impact the idler angles due to changes in the belt’s contact with the idler.
- Idler Spacing: The distance between idler sets along the conveyor affects the distribution of forces and thus the required idler angles.
Step-by-Step Guide
Calculating the idler angles involves several steps:
- Determine the Conveyor Inclination Angle: Measure the angle at which the conveyor is inclined from the horizontal.
- Calculate the Vertical Distance (H): Determine the vertical distance between the center of the idler and the conveyor frame.
- Calculate the Horizontal Distance (L): Determine the horizontal distance between the center of the idler and the conveyor frame.
- Use the Formula to Calculate the Idler Angle: Plug the values of H and L into the formula θ=arctan(H/L) to calculate the idler angle in degrees.
- Adjust for Factors: Consider the factors influencing the calculation (material type, belt speed, load capacity, etc.) and adjust the idler angle accordingly.
Calculating the idler angles is essential for the proper functioning of conveyor systems. By understanding the basic principles, formulas, and factors influencing the calculation, engineers and operators can ensure that idlers are positioned correctly, minimizing wear and tear on the system and maximizing efficiency.

Conveyor Idler Degree: Conveyor Idler Frame Dimensions
Conveyor idlers play a crucial role in supporting and guiding the conveyor belt along its path. Understanding the relationship between idler angles and frame dimensions is essential for designing and maintaining efficient conveyor systems. This section explores the key aspects of conveyor idler frame dimensions, including their impact on conveyor performance and the customization options available.
Relationship between Idler Angles and Frame Dimensions
The idler angle refers to the angle at which the idler rolls are installed relative to the horizontal plane. This angle significantly influences the belt’s behavior and the overall conveyor performance. The frame dimensions, including the width and length of the idler frame, are directly related to the idler angle.
In general, the idler angle is determined based on the specific requirements of the conveyor system, such as the material being conveyed, the conveyor speed, and the overall layout of the system. A higher idler angle is often used for conveying materials with larger particle sizes or higher volumes, as it helps prevent material spillage and improves the belt’s ability to carry the load.
Standard Frame Dimensions for Different Idler Angles
Standard idler frame dimensions vary depending on the idler angle and the specific requirements of the conveyor system. conveyor idler degree 20° transition idlers, 35° and 45° troughing idlers, and angled ‘Vee’ return idlers for efficient bulk handling.However, there are some common trends in frame dimensions based on the idler angle:
- 20° Idler Angle: This angle is commonly used for lightweight materials and moderate load capacities. The standard frame width for a 20° idler angle is typically around 450mm to 600mm, with a length ranging from 600mm to 1200mm.
- 30° Idler Angle: A 30° idler angle is suitable for conveying heavier materials and higher load capacities. The standard frame width for a 30° idler angle is usually between 600mm and 750mm, with a length ranging from 900mm to 1800mm.
- 45° Idler Angle: This angle is used for steep incline conveyors or applications where material needs to be lifted vertically. The standard frame width for a 45° idler angle is typically between 750mm and 900mm, with a length ranging from 1200mm to 2400mm.
- Custom Idler Angles: In some cases, conveyor systems may require idler angles that deviate from the standard angles. In such situations, custom idler frames can be designed and manufactured to meet the specific requirements of the application.
Customization Options for Unique Conveyor System Requirements
Customization is key to ensuring that conveyor idler frame dimensions meet the unique requirements of each conveyor system. Some customization options include:
- Frame Material: Idler frames can be constructed from various materials, including steel, stainless steel, and aluminum, depending on the application’s requirements for strength, durability, and corrosion resistance.
- Frame Design: The design of the idler frame can be customized to accommodate special requirements, such as the need for additional support or protection against material spillage.
- Idler Spacing: The spacing between idler rolls can be adjusted to optimize the conveyor’s performance for different types of materials and loading conditions.
- Idler Diameter: The diameter of the idler rolls can be varied to achieve the desired belt tension and support for the conveyed material.
Understanding the relationship between idler angles and frame dimensions is crucial for designing efficient conveyor systems. By choosing the right idler angle and customizing the frame dimensions to meet specific requirements, conveyor operators can ensure smooth and reliable material handling operations.
Conveyor Idler Degree: Selection Criteria
In conveyor systems, idlers play a crucial role in supporting the belt and ensuring proper tracking. Various types of idlers are used based on the specific requirements of the conveyor system. Understanding the different types of idlers and their applications is essential for efficient conveyor operation. This section provides an in-depth look at troughing idlers, return idlers, and impact idlers, discussing their specific use cases, benefits, and selection criteria.
Selection Criteria for Idlers
Selecting the right idler for a conveyor system depends on various factors, including the application, belt speed, material type, and environmental conditions. Here are some key criteria to consider when choosing idlers:
- Load Capacity: Ensure that the idler can support the maximum load of the conveyor system.
- Roller Diameter: Choose the appropriate roller diameter based on the belt width and material weight.
- Material: Select idlers made from durable materials that can withstand the operating conditions.
- Friction: Consider the coefficient of friction between the idler and the belt to minimize energy consumption.
- Environmental Conditions: Choose idlers that are suitable for the temperature, moisture, and corrosive conditions of the operating environment.
Selecting the right type of idler is essential for the efficient and reliable operation of a conveyor system. Troughing idlers, return idlers, and impact idlers each play a crucial role in ensuring the proper functioning of the conveyor belt. Understanding their specific use cases, benefits, and selection criteria is key to optimizing conveyor performance and minimizing maintenance costs.

Practical Considerations of Conveyor Idler Degrees
When it comes to conveyor idler systems, proper installation, maintenance, and alignment are crucial for optimal performance and longevity. Here are twelve tips to ensure your conveyor idlers operate smoothly:
- Quality Idlers: Start with high-quality idlers that match your conveyor’s specifications. Ensure they are correctly rated for the application.
- Proper Installation: Follow the manufacturer’s guidelines for installation, ensuring idlers are aligned and spaced correctly.
- Regular Inspection: Conduct routine inspections to check for wear, damage, or misalignment. Replace any worn or damaged idlers promptly.
- Lubrication: Keep idlers properly lubricated to reduce friction and wear. Use a suitable lubricant recommended by the manufacturer.
- Belt Tracking: Monitor belt tracking regularly and adjust idler alignment if the belt starts to wander off-center.
- Alignment Tools: Use alignment tools such as laser alignment devices to ensure idlers are correctly aligned.
- Cleaning: Keep idlers clean from debris and buildup to prevent damage and ensure smooth operation.
- Avoid Overloading: Ensure the conveyor is not overloaded, as this can lead to excessive wear on idlers.
- Temperature Control: Maintain a consistent temperature in the conveyor environment to prevent thermal expansion and contraction that can affect idler alignment.
- Use Impact Beds: In areas of high impact, consider using impact beds to reduce stress on idlers and extend their lifespan.
- Monitor Belt Tension: Ensure the belt tension is correctly adjusted to prevent excessive strain on idlers.
- Training and Education: Train employees on proper conveyor operation, maintenance, and safety practices to prevent issues and minimize downtime.
Common Issues and Troubleshooting
Even with proper maintenance, issues can arise. Here are seven common problems related to idler angles and alignment, along with troubleshooting methods:
- Misalignment: Check for misalignment by visually inspecting the conveyor. Use alignment tools to correct any misalignment.
- Uneven Wear: Uneven wear on idlers can indicate misalignment or overloading. Check alignment and adjust load distribution if necessary.
- Belt Slippage: Belt slippage can occur due to improper tension or worn idlers. Adjust the tension and replace worn idlers.
- Excessive Noise: Excessive noise can indicate misalignment or worn idlers. Inspect and realign idlers, and replace any worn components.
- Idler Seizure: Idlers can seize due to lack of lubrication or contamination. Clean and lubricate idlers regularly to prevent seizure.
- Idler Damage: Inspect idlers regularly for signs of damage such as cracks or bent rollers. Replace damaged idlers promptly.
- Belt Tracking Issues: Belt tracking problems can be caused by misaligned idlers. Check and adjust idler alignment to resolve tracking issues.
Safety Standards and Best Practices
Safety is paramount when working with conveyor idler systems. Follow these standards and best practices to ensure a safe working environment:
- Guarding: Install guards to prevent contact with moving parts of the conveyor.
- Lockout/Tagout: Implement lockout/tagout procedures when servicing or maintaining the conveyor to prevent accidental startup.
- Training: Train employees on safe operating procedures and the importance of following safety guidelines.
- Regular Inspections: Conduct regular inspections of the conveyor system to identify and address potential safety hazards.
- Emergency Stop Devices: Install emergency stop devices along the conveyor to quickly shut down the system in case of an emergency.
By following these tips and best practices, you can ensure your conveyor idler system operates smoothly, efficiently, and safely.
Conveyor Idler Degree: Conveyor Roller Size Chart
Conveyor rollers play a crucial role in the efficiency and functionality of conveyor systems. One of the key factors in their effectiveness is their size, which must be carefully considered during the design and operation of the conveyor. Understanding the importance of roller size, knowing the standard sizes available, and selecting the appropriate size based on specific conveyor requirements are critical for optimal performance.
Importance of Roller Size in Conveyor Design and Operation
The size of conveyor rollers directly impacts the conveyor’s performance, efficiency, and overall cost-effectiveness. Proper roller size ensures smooth movement of materials along the conveyor, reduces the risk of jams and downtime, and minimizes wear and tear on the conveyor system.
Conveyor idler degree is an essential aspect to consider when designing or operating a conveyor system. The idler degree refers to the angle at which idlers are set on a conveyor belt. Proper idler degree helps to ensure that the belt runs smoothly without slipping or misalignment, thus improving the overall efficiency of the conveyor system.
Detailed Chart Illustrating Standard Conveyor Roller Sizes and Their Applications
Conveyor rollers are available in a variety of standard sizes, each suitable for different applications and conveyor types. Below is a detailed chart illustrating the standard sizes of conveyor rollers and their typical applications:
It is important to note that these are just general guidelines, and specific applications may require different roller sizes based on factors such as load capacity, speed, and conveyor layout.
Guidelines for Selecting the Appropriate Roller Size
When selecting the roller size for a conveyor system, several factors must be considered to ensure optimal performance:
- Load Capacity: The roller size should be able to support the maximum load expected on the conveyor without deformation or failure.
- Conveyor Speed: Higher conveyor speeds may require larger rollers to reduce wear and maintain smooth operation.
- Material Handling: The type of material being conveyed and its characteristics (e.g., size, weight, and abrasiveness) will influence the choice of roller size.
- Conveyor Layout: The layout of the conveyor, including the conveyor idler degree, will affect the roller size needed to ensure proper alignment and movement of the belt.
- Maintenance Requirements: Consideration should be given to the ease of maintenance and replacement of rollers when selecting their size.
By carefully considering these factors and consulting with conveyor experts, it is possible to select the appropriate roller size for any conveyor system, ensuring optimal performance and longevity.
The size of conveyor rollers is a critical factor in the design and operation of conveyor systems. Understanding the importance of roller size, knowing the standard sizes available, and selecting the appropriate size based on specific conveyor requirements are essential for ensuring the efficiency and effectiveness of conveyor systems in various industries.
FAQs about Conveyor Idler Degree
The angle of a troughed conveyor idler refers to the tilt or inclination of the idler sets that support the conveyor belt and give it a trough shape. This angle is vital for the proper function of the conveyor as it influences the capacity, the stability of the load, and the belt’s life. Commonly, troughed conveyor idlers are set at angles of 20, 35, or 45 degrees. These standard angles help to ensure that materials are transported efficiently without spilling over the edges of the belt. The specific angle chosen for a troughed conveyor idler setup depends on several factors, including the type of material being conveyed, the conveyor belt width, and the conveying speed. Custom angles can also be manufactured to meet unique system requirements, ensuring that material handling processes are optimized for specific operational needs.
The angle of an impact idler typically matches that of standard troughing idlers, which are 20, 35, or 45 degrees, to maintain uniformity along the conveyor system. Impact idlers are specialized components situated at points where material fall significantly impacts the conveyor belt, such as loading zones. The purpose of the angle in impact idlers is to complement the trough shape of the belt at these critical points. This design helps in absorbing the shock and dispersing the force of falling materials, protecting the belt and the structure from damage. It’s crucial that the angle of the impact idler syncs with the existing conveyor setup to maintain the material flow efficiently and prevent spillage or undue wear on the conveyor components.
The angle of a conveyor belt, often referred to as the maximum incline angle, is the steepest angle at which the conveyor can operate while still transporting materials effectively and without slide-back. This angle is crucial for designing and setting up conveyors, especially in applications where space is limited or specific material handling is required. Generally, the maximum angle of incline for a conveyor belt depends on the type of material being conveyed and the belt’s surface texture and composition. For non-slippery materials like packed items or dry sand, the angle can be as steep as 30-35 degrees. However, for loose or slippery materials, the maximum incline angle might be less, typically around 20 degrees. Cleated or ribbed belts can increase the maximum conveying angle by reducing material rollback.
The maximum conveyor angle, also known as the maximum angle of inclination, is the steepest angle at which a conveyor system can operate effectively without the material sliding back. This angle varies significantly depending on the material characteristics, such as size, shape, and moisture content, as well as the conveyor belt’s surface texture. Generally, most bulk materials can be conveyed at angles from 0 to 20 degrees. With specialized equipment and considerations, such as using cleated belts or pocket belts, steeper angles up to 90 degrees (vertical conveyance) can be achieved. For standard belt conveyors, the practical maximum angle is often around 15 to 25 degrees for granular and non-slippery materials. Understanding and setting the correct maximum conveyor angle is crucial to prevent spillage, optimize material handling, and ensure the longevity of the conveyor system.
The degree of a carrying idler refers to the angle at which the idler set (which includes multiple rollers) is inclined relative to the horizontal plane. This angle is crucial as it affects the stability and movement of the material being transported on the conveyor belt. Typically, carrying idlers can have different degrees, such as 20°, 35°, or 45°, depending on the specific requirements of the conveyor system and the type of material being conveyed. The degree chosen ensures optimal support and minimizes spillage during the transportation process.
The angle of a conveyor idler refers to the inclination angle of the rollers in the idler set relative to the horizontal plane. This angle is essential for ensuring that the material remains centered on the conveyor belt and is efficiently transported. Common angles for conveyor idlers are 20°, 35°, and 45°, but the specific angle used can vary based on the design of the conveyor system and the type of material being conveyed. The chosen angle helps optimize the load distribution on the belt, reducing spillage and improving the overall efficiency of the conveyor system.
Last Updated on June 28, 2024 by Jordan Smith
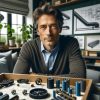
Jordan Smith, a seasoned professional with over 20 years of experience in the conveyor system industry. Jordan’s expertise lies in providing comprehensive solutions for conveyor rollers, belts, and accessories, catering to a wide range of industrial needs. From initial design and configuration to installation and meticulous troubleshooting, Jordan is adept at handling all aspects of conveyor system management. Whether you’re looking to upgrade your production line with efficient conveyor belts, require custom conveyor rollers for specific operations, or need expert advice on selecting the right conveyor accessories for your facility, Jordan is your reliable consultant. For any inquiries or assistance with conveyor system optimization, Jordan is available to share his wealth of knowledge and experience. Feel free to reach out at any time for professional guidance on all matters related to conveyor rollers, belts, and accessories.