Preventing Conveyor Idler Failure: Tips & Tricks
In bulk material handling, conveyor idlers are fundamental for the seamless operation of conveyor belts. Yet, the occurrence of conveyor idler failure poses significant operational challenges. These failures not only disrupt the flow of operations but also incur high costs and elevate safety risks. Conveyor idler failure can lead to extensive downtime, necessitating urgent repairs and replacements, which can be costly. More critically, such failures can compromise worker safety, making it imperative to address them promptly. Understanding the causes and implementing effective preventive measures are key to mitigating the risks associated with conveyor idler failure, ensuring both the efficiency and safety of conveyor systems.
What is Conveyor Idler Failure
Conveyor idler failure is a significant setback that can disrupt the smooth functioning of a conveyor belt system, leading to potential downtime, operational inefficiency, and increased maintenance costs. Idler failure typically occurs due to excessive wear, lack of maintenance, material buildup causing imbalances, or bearing failures within the idlers themselves. Over time, the stress from carrying heavy loads, exposure to abrasive materials, or even environmental factors like moisture and temperature fluctuations can degrade idler integrity. When idlers fail, they can cause misalignment of the conveyor belt, uneven belt wear, or even unexpected halts in conveyor operation. Recognizing the early signs of idler wear or damage and implementing a regular maintenance schedule are critical steps in mitigating the risk of idler failure and ensuring the longevity and reliability of the conveyor system.
Symptoms of Conveyor Idler Failure
- Belt Misalignment: This is often the first sign of conveyor idler failure. Misaligned idlers cause the belt to drift off its intended path, leading to uneven wear on the edges, potential product spillage, and increased strain on other conveyor components.
- Unusual Noises: Sounds like grinding, squealing, or thumping from the conveyor system often indicate that idlers are not rotating smoothly. These noises can be due to worn-out bearings, misaligned rollers, or seized idlers.
- Increased Power Consumption: A failing idler increases resistance on the belt, requiring more energy to maintain the same speed. This can be observed as an unexplained rise in power usage by the conveyor system.
- Visible Wear and Tear: Physical signs of wear, such as cracks on the idler surface, rust, or accumulation of material residues, indicate deteriorating idler condition. Excessive dust or material buildup around idlers can also be a sign of failing bearings.
Common Causes of Idler Failure
- Improper Installation: Incorrect installation can lead to several issues, such as misalignment, inadequate tension, or uneven distribution of load. Idlers installed at improper angles or intervals can significantly shorten their lifespan and efficiency.
- Excessive Load: Overburdening the conveyor system can lead to rapid wear and tear of idlers. Exceeding the load capacity can cause the idlers to deform or break, leading to system failure.
- Environmental Factors: Exposure to harsh elements like moisture, extreme temperatures, and corrosive materials can lead to rusting or degradation of idler materials. In environments with high levels of dust or particulate matter, idlers can seize if not properly sealed or maintained.
- Lack of Maintenance: Regular maintenance is crucial for early detection of issues. Neglecting maintenance can lead to severe wear and tear, resulting in unexpected breakdowns. Routine checks should include cleaning, lubrication, and inspection for signs of wear or damage.
By thoroughly understanding the symptoms and causes of conveyor idler failure, maintenance teams can take proactive steps to prevent downtime and extend the life of conveyor systems. Regular inspections, adherence to load specifications, and environmental considerations are key to maintaining optimal conveyor performance.
Detailed Analysis of Conveyor Idler Failure Causes
In addressing conveyor idler failure, a detailed analysis reveals several contributing factors that span mechanical, material, and environmental influences. Each plays a significant role in the overall performance and longevity of conveyor idlers.
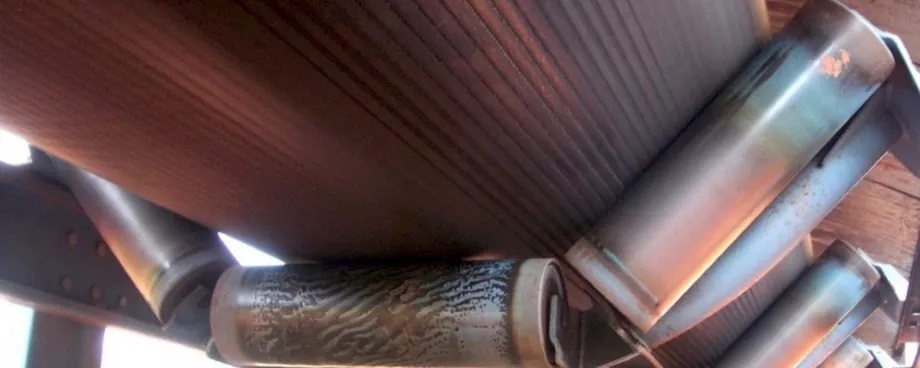
Mechanical and Operational Causes:
- Misalignment: One of the primary mechanical causes of conveyor idler failure is misalignment. When idlers are not aligned with the belt’s path, it leads to uneven wear, increased friction, and stress on the idlers and belt. Misalignment can stem from improper installation, settling of the foundation, or shifts in the conveyor structure.
- Improper Tensioning: Adequate tension is crucial for the smooth operation of conveyor belts. Over-tensioning can lead to excessive pressure on idlers, resulting in premature wear and failure. Conversely, under-tensioning can cause slippage and misalignment, contributing to idler damage.
- Incorrect Pulley Sizes: Pulleys that are not appropriately sized for the conveyor system can lead to belt slippage or excessive tension. Both scenarios put undue stress on idlers, hastening their wear and failure.
Material and Design Factors:
- Material Quality: The durability and performance of conveyor idlers heavily depend on the quality of materials used in their construction. Poor quality or unsuitable materials can lead to faster degradation, corrosion, and ultimately, failure.
- Design Flaws: Idlers must be designed to accommodate the specific demands of the conveyor system, including load capacity and belt speed. Design flaws such as inadequate bearing size, improper sealing, or insufficient structural support can all lead to premature idler failure.
Environmental and External Factors:
- Temperature and Humidity: Extreme temperatures can affect the material properties of idlers, making them more susceptible to wear and failure. High humidity levels or exposure to corrosive substances can lead to rust and corrosion, particularly in metal components.
- Dust and Particulate Matter: In many industrial environments, dust and particulate matter can accumulate on and around idlers. Without regular cleaning, this buildup can lead to increased friction and wear, or even seize the idler’s rotation, leading to conveyor idler failure.
Understanding these detailed causes of conveyor idler failure is essential for diagnosing issues, implementing effective maintenance strategies, and designing more resilient conveyor systems. By addressing these factors, industries can enhance the reliability and efficiency of their conveyor operations, reducing downtime and maintenance costs.
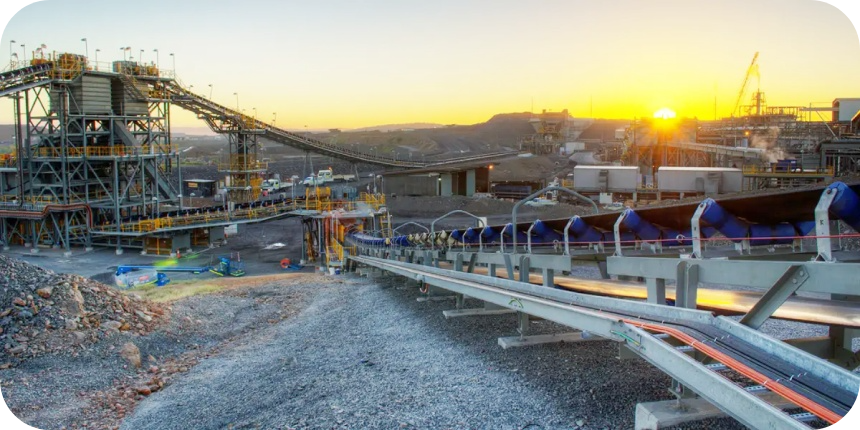
Preventing and Addressing Conveyor Idler Failure
Regular Inspection and Maintenance:
- Detailed Visual Inspections: Conduct thorough inspections focusing on signs of wear like cracks, corrosion, or misshapen idlers. Examine for any material buildup that could hinder idler functionality.
- Operational Functionality Checks: Regularly listen for unusual sounds indicating bearing problems. Test each idler for ease of rotation and signs of seizing or resistance.
- Comprehensive Maintenance Schedule: Implement a systematic maintenance plan, including cleaning of idlers, lubrication of bearings, and timely replacement of worn or damaged idlers. Maintain detailed records of each inspection to monitor idler condition and predict future maintenance needs.
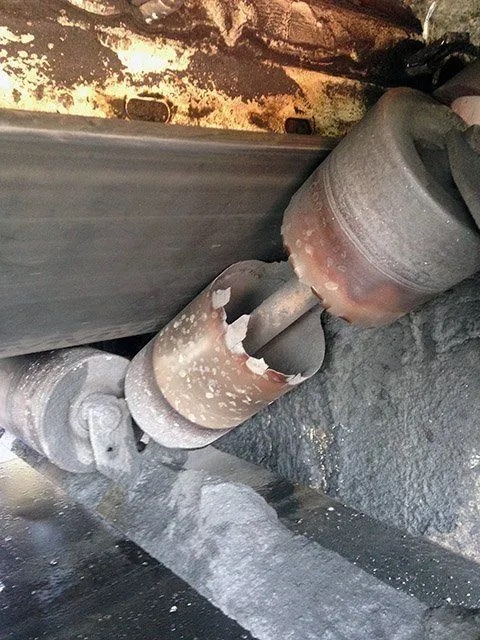
Proper Installation and Alignment:
- Precision in Installation: Ensure idlers are installed accurately, aligned with the belt’s path, and perpendicular to the conveyor’s direction. Utilize precise measuring and leveling tools for correct placement.
- Ongoing Alignment Monitoring: Regularly check and adjust the alignment of idlers to prevent belt misalignment, which can cause uneven wear and efficiency loss.
- Training and Expertise: Provide comprehensive training for installation teams, emphasizing the critical nature of precise idler installation and alignment for conveyor efficiency.
Load Management and Stress Reduction:
- Even Load Distribution: Strategically distribute the load across the belt to avoid excessive pressure on individual idlers, which can lead to premature failure.
- Adherence to Load Specifications: Strictly follow the conveyor system’s specified load capacity to prevent overloading, which can strain idlers and other conveyor components.
- Automated Load Monitoring: Implement advanced systems for real-time load monitoring and adjustment, ensuring balanced load distribution and minimizing stress on idlers.
Upgrading Idler Technology:
- Innovative Idler Designs: Invest in the latest idler technologies, such as self-aligning models, idlers with enhanced bearing designs, and superior sealing mechanisms to increase lifespan and efficiency.
- Utilizing Advanced Alignment Technologies: Consider state-of-the-art solutions like Multi-Pivot Belt Trackers for optimal belt alignment, reducing wear on idlers.
- Material Selection for Specific Needs: Choose idlers constructed from materials that best suit the operational environment, whether for durability, corrosion resistance, or weight considerations.
Environmental Protection and Adaptation:
- Corrosion-Resistant Idlers: In environments with high humidity or corrosive elements, opt for idlers made from stainless steel or with protective coatings to prevent rust and degradation.
- Effective Dust and Debris Control: Implement robust dust management strategies to prevent buildup on idlers, which can lead to increased wear or operational hindrance.
- Adapting to Extreme Temperatures: Select idlers designed to perform reliably in extreme temperatures, ensuring consistent operation in varying environmental conditions.
By thoroughly addressing these key areas, the risk of conveyor idler failure can be significantly minimized. This proactive approach not only enhances the reliability and efficiency of the conveyor system but also extends the lifespan of the idlers, ensuring smoother, uninterrupted operations.
Troubleshooting Specific Conveyor Idler Failure Issues
In addressing conveyor idler failure, it’s crucial to tackle specific issues such as roll wear, bearing life, and belt misalignment with targeted solutions.
1. Addressing Roll Wear and Seizure:
- Combatting Roll Wear: Regularly inspect rolls for signs of wear and replace them as needed. Use wear-resistant materials for rolls in high-abrasion areas. Ensure proper alignment and tensioning of the belt to reduce uneven wear.
- Resolving Idler Seizure: Regular lubrication of idler bearings can prevent seizure. Clean idlers regularly to remove debris that could cause jamming. If seizure occurs, inspect for and remove foreign objects, then check and replace damaged bearings.
- Fixing Frame Buckle: Strengthen idler frames by using more robust materials or adding stiffeners. Regularly inspect frames for signs of buckling and address any underlying causes, such as excessive load or impact.
2. Tackling Reduced Bearing Life and High Power Absorption:
- Extending Bearing Life: Implement a lubrication schedule tailored to the operating environment. Use sealed or shielded bearings in dusty or wet conditions. Regularly inspect bearings for wear and replace them before failure.
- Reducing Power Absorption: Ensure idlers are correctly aligned and rotating freely to minimize resistance. Use energy-efficient bearings and idler designs. Regularly clean and maintain idlers to prevent buildup that increases power consumption.
3. Repairing Belt Damage and Misalignment:
- Correcting Belt Damage: Inspect the belt for damage such as tears or fraying. Repair minor damage with belt repair kits or patches. For significant damage, consider replacing the belt section.
- Realignment Techniques: Regularly check and adjust idler alignment to prevent belt drift. Use self-aligning idlers or tracking systems for continuous alignment correction. Train maintenance staff on proper alignment techniques to ensure quick resolution of misalignment issues.
By systematically addressing these specific conveyor idler failure issues, maintenance teams can significantly enhance the reliability and efficiency of conveyor systems. Regular inspections, proactive maintenance, and using the right components and techniques are key to preventing and resolving these common idler problems.
15 Common Causes of Conveyor Idler Failure and Troubleshooting Methods
The failure of a conveyor idler can result from several factors, each potentially disrupting your operation’s smooth functioning, causing downtime, or even safety hazards. These causes range from bearing failures and excessive wear to operational aspects such as overloading or inadequate maintenance. However, each problem has corresponding troubleshooting methods, which, if implemented promptly, can restore your conveyor system’s normal functioning and possibly prevent future failures. Here, we will explore 15 common causes of conveyor idler failure and provide an overview of their troubleshooting methods.
While these methods serve as a common guideline, it is always crucial to couple them with a comprehensive preventive maintenance strategy tailored to your system’s unique requirements. This practice will help avoid unexpected downtime, keep your conveyor system in optimum condition, and potentially extend its lifespan.
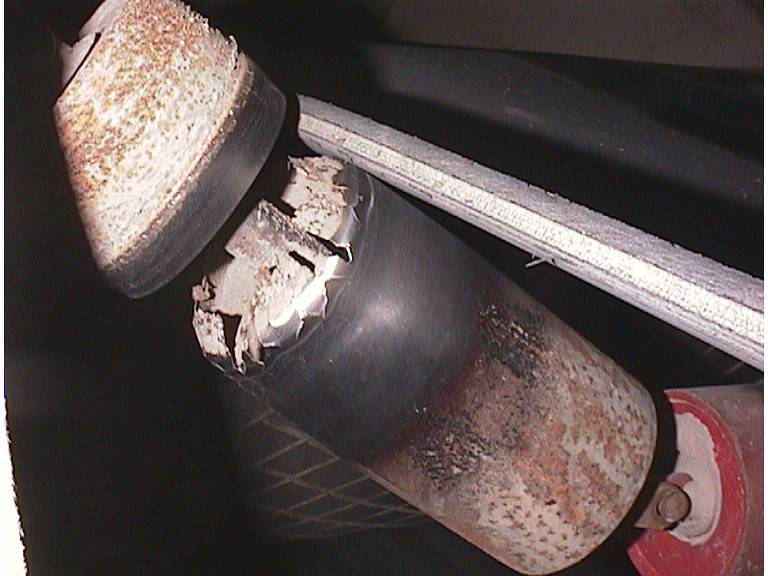
Advanced Solutions and Innovations in Conveyor Idler Failure
In addressing conveyor idler failure, the industry is witnessing a surge in advanced solutions and innovations that significantly enhance idler performance and longevity. These advancements are pivotal in mitigating the common issues associated with conveyor idler failure.
1. Self-Aligning Idlers: These idlers automatically adjust their position to maintain proper alignment of the conveyor belt. This innovation significantly reduces the risk of belt misalignment, one of the primary causes of conveyor idler failure.
2. High-Performance Materials: The use of advanced materials in idler construction, such as composite materials or reinforced polymers, offers increased resistance to wear, corrosion, and environmental impacts. These materials extend the life of idlers and reduce the frequency of replacements.
3. Smart Idler Technologies: Incorporating sensors and IoT (Internet of Things) technology, smart idlers can provide real-time monitoring of idler performance. This technology enables early detection of issues like increased vibration, temperature changes, or excessive wear, allowing for proactive maintenance before failures occur.
4. Improved Bearing Designs: Bearings are critical to idler functionality. Innovations in bearing design, including better sealing and lubrication systems, have significantly increased bearing life and, by extension, the life of the idlers.
5. Energy-Efficient Idlers: New designs focus on reducing the power consumption of conveyor systems. These idlers are designed to minimize friction and resistance, leading to lower energy costs and improved overall efficiency of the conveyor system.
By integrating these advanced solutions and innovations, industries can significantly reduce the incidence of conveyor idler failure, leading to more reliable, efficient, and cost-effective conveyor system operations. These technological advancements not only address the current challenges but also pave the way for future developments in conveyor system maintenance and management.
The comprehensive management of conveyor idler failure is paramount in maintaining the efficiency and safety of conveyor systems. Proactive measures, including regular inspections, proper installation, and prompt responses to early signs of wear and malfunction, are crucial in preventing idler failures. The impact of such failures extends beyond mere operational disruptions; it encompasses significant safety risks and financial implications. Therefore, a proactive approach to idler failure management is not just a maintenance task but a critical aspect of operational integrity and safety.
Adopting a holistic approach to conveyor system maintenance is essential for optimal performance. This involves not only addressing immediate mechanical issues but also considering advanced solutions and innovations that enhance the longevity and reliability of conveyor idlers. By integrating smart technologies, high-performance materials, and innovative designs, conveyor systems can achieve higher efficiency and reduced downtime. Ultimately, the goal is to ensure that conveyor systems are not only functional and efficient but also safe and cost-effective in the long term. Embracing these principles in conveyor idler failure management will lead to more sustainable and successful operations in various industrial settings.
Choose our conveyor idlers for exceptional durability and cost-effectiveness!
FAQs on Conveyor Idler Failure
The primary function of a conveyor idler is to provide support and shape to the conveyor belt, ensuring smooth and efficient transportation of materials. Conveyor idlers are cylindrical rods that are strategically placed along the length of the conveyor belt. They play a crucial role in maintaining the belt’s tension and alignment, which are essential for the proper functioning of the conveyor system. Idlers also help to distribute the weight of the load evenly across the belt, reducing wear and tear and extending the belt’s lifespan. Additionally, they minimize the friction between the belt and the conveyor structure, thereby reducing power consumption and enhancing the overall efficiency of the system. In summary, conveyor idlers are vital components that contribute to the stability, efficiency, and longevity of conveyor systems.
Poor alignment of idlers or take-up devices in a conveyor system can be indicated by several conditions. One of the most common signs is belt misalignment, where the belt drifts off to one side of the conveyor. This can lead to uneven wear on the edges of the belt and increased strain on the conveyor structure. Another indicator is abnormal wear patterns on the idlers themselves, suggesting that they are not properly aligned with the belt’s path. Excessive noise or vibration during operation can also signal misalignment issues, as can the frequent slippage or tracking problems of the belt. Additionally, if the conveyor belt consistently requires re-tensioning or if there are visible signs of material spillage along the conveyor path, these may also point to alignment problems with the idlers or take-up devices.
Conveyor belts can fail in several ways, each of which can significantly impact the efficiency and safety of a conveyor system. One common failure mode is belt tearing or ripping, often caused by sharp objects or heavy impacts. Another is belt delamination, where layers of the belt material separate, usually due to excessive tension or poor quality materials. Abrasion and wear are also common, especially in systems that handle abrasive materials or operate under high friction conditions. Misalignment is another failure mode, where the belt drifts off its intended path, leading to uneven wear and potential damage. Additionally, belt slippage, often caused by insufficient tension or poor grip on the pulleys, can lead to reduced efficiency and increased wear. Lastly, environmental factors like temperature, moisture, and chemical exposure can degrade the belt material, leading to premature failure.
The two major causes of belt slippage in conveyor systems are insufficient tension and poor pulley condition. Insufficient tension means that the belt is not tight enough to grip the pulleys properly, causing it to slip or slide instead of moving smoothly. This can happen due to stretching of the belt over time, improper initial tensioning, or elongation due to heavy loads. The second major cause, poor pulley condition, refers to situations where the pulleys are worn, dirty, or improperly aligned. Worn pulleys with a smooth surface provide less grip for the belt, leading to slippage. Similarly, pulleys covered in dust, dirt, or debris can reduce friction between the belt and the pulley, causing the belt to slip. Proper maintenance, including regular cleaning and alignment checks, is essential to prevent these issues.
The idler shaft is a critical component of a conveyor idler, responsible for supporting the idler rolls and facilitating their rotation. It is the central axis around which the idler rolls spin, allowing the conveyor belt to move smoothly over them. The idler shaft is typically mounted within bearings, which enable it to rotate freely while supporting the weight of the belt and the materials being transported. This rotation is crucial for reducing friction between the belt and the idler, thereby minimizing wear and tear on both the belt and the idler rolls. The shaft must be robust and precisely manufactured to ensure it can withstand the load and the operational stresses of the conveyor system. In summary, the idler shaft plays a vital role in the functionality and efficiency of conveyor idlers, contributing to the overall performance of the conveyor system.
One of the most common issues with belt conveyors is misalignment. Misalignment of the conveyor belt can result from various factors, including uneven loads, unsynchronized roller speeds, worn parts, or lack of regular maintenance. When the belt becomes misaligned, it can lead to other serious problems such as belt damage, material spillage, and increased wear and tear on other parts of the conveyor system.
Another typical problem is belt slippage. This can happen when the belt and conveyor rollers do not have adequate grip to drive the belt around the conveyor effectively. Slippage usually results from a lack of tension or a load that’s too heavy.
Clogged rollers also present a frequent challenge. Dirt, debris, or accumulated material can jam the rollers, which can cause the belt to slip, trip, or eventually stop running.
Similarly, inadequate lubrication can accelerate wear and tear on moving parts and potentially lead to system failure. Hence, regular cleaning, lubrication and maintenance are crucial for the optimal operation of a belt conveyor system.
Lastly, belt wear and tear is a common problem. High loads, constant use, and harsh operating conditions can wear down the conveyor belt over time, leading to reduced performance and eventually, the need for replacement.
Each of these issues can severely impact the efficient operation of a belt conveyor, leading to downtime, repair costs, and potentially compromising worker safety. Therefore, it’s critical to address any problems promptly and conduct regular preventive maintenance.
Last Updated on June 7, 2024 by Jordan Smith
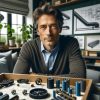
Jordan Smith, a seasoned professional with over 20 years of experience in the conveyor system industry. Jordan’s expertise lies in providing comprehensive solutions for conveyor rollers, belts, and accessories, catering to a wide range of industrial needs. From initial design and configuration to installation and meticulous troubleshooting, Jordan is adept at handling all aspects of conveyor system management. Whether you’re looking to upgrade your production line with efficient conveyor belts, require custom conveyor rollers for specific operations, or need expert advice on selecting the right conveyor accessories for your facility, Jordan is your reliable consultant. For any inquiries or assistance with conveyor system optimization, Jordan is available to share his wealth of knowledge and experience. Feel free to reach out at any time for professional guidance on all matters related to conveyor rollers, belts, and accessories.