Health Conveyor Idler Monitoring System
Conveyor systems are essential in various industries for efficient material handling. At the heart of these systems are conveyor idlers, which support the conveyor belt and ensure smooth operation. Conveyor idlers are crucial in maintaining the belt’s alignment and preventing excessive wear. However, due to their constant movement and load-bearing function, they are prone to wear and failure. This highlights the need for a conveyor idler monitoring system. Such a system continuously monitors the condition of conveyor idlers, detecting potential issues before they lead to system failures. Implementing a conveyor idler monitoring system can significantly enhance the reliability and efficiency of conveyor operations by enabling predictive maintenance and reducing unexpected downtime.
Core Components of a Conveyor Idler Monitoring System
Conveyor idler monitoring system detecting early conveyor idler failures, enhancing productivity, safety, and system reliability. A conveyor idler monitoring system is designed to ensure the smooth operation and longevity of conveyor systems by continuously monitoring the condition of conveyor idlers. This system comprises several critical components that work together to detect potential issues and facilitate timely maintenance.
Overview of Conveyor Idler Monitoring System and Its Typical Components
A conveyor idler monitoring system typically includes sensors, data processing units, and alert mechanisms. These components are strategically placed to monitor various aspects of the conveyor idlers’ performance, such as alignment, temperature, and vibration. The system collects data in real-time, enabling predictive maintenance and reducing the risk of unexpected failures.
Detailed Look at:
Conveyor Idlers and Their Functions
Conveyor idlers play a vital role in the efficient functioning of conveyor systems.
- Supporting the Conveyor Belt: Idlers provide support to the conveyor belt, preventing it from sagging and ensuring smooth material transport.
- Maintaining Belt Alignment: Idlers keep the belt aligned, reducing the risk of spillage and ensuring consistent material flow.
- Load Distribution: Idlers help distribute the load evenly across the belt, minimizing wear and tear on specific sections.
- Reducing Friction: Properly functioning idlers reduce friction between the belt and the rollers, which helps in conserving energy.
- Preventing Overheating: By maintaining optimal contact between the belt and the rollers, idlers prevent the belt from overheating, thus avoiding premature failure.
Conveyor Pulleys and Precision Pulley and Idler Mechanisms
Conveyor pulleys are crucial for driving and redirecting the belt. Precision pulley and idler mechanisms ensure that the belt runs smoothly and efficiently. These mechanisms are designed to handle high loads and reduce vibrations, contributing to the overall stability and performance of the conveyor system. The precision in these components is essential for minimizing wear and ensuring the longevity of both the pulleys and the idlers.
Conveyor Speed Switch and Zero Speed Switch
Speed switches are integral to a conveyor idler monitoring system. They monitor the speed of the conveyor belt to ensure it is operating within the desired range.
- Conveyor Speed Switch: This device detects the belt’s speed and ensures it remains within set parameters. If the belt speed deviates from the norm, the system can trigger an alert or shut down the conveyor to prevent damage.
- Zero Speed Switch: This switch detects the absence of movement. If the belt stops moving unexpectedly, the zero speed switch activates an alert or stops the conveyor to prevent further issues.
These components are essential for maintaining the efficiency and safety of the conveyor system. By integrating a conveyor idler monitoring system, operators can ensure continuous monitoring and timely intervention, thus optimizing the performance and reliability of their conveyor systems.

Conveyor Idler Monitoring System: Condition Monitoring
Condition Monitoring in a Conveyor Idler Monitoring System involves the continuous observation and analysis of the conveyor idlers’ operational parameters to detect any signs of wear, degradation, or imminent failure. The primary objective of condition monitoring is to ensure that the conveyor system operates efficiently, safely, and with minimal unplanned downtime. Below are the key aspects of condition monitoring for conveyor idlers:
1. Parameters Monitored:
- Vibration: Vibration sensors measure the frequency and amplitude of vibrations in the idlers. Abnormal vibration patterns may indicate issues such as bearing wear, misalignment, or an imbalance in the idler rollers.
- Temperature: Temperature sensors monitor the heat generated by the idler bearings. Excessive heat can indicate increased friction due to bearing failure, lack of lubrication, or overloading.
- Noise (Acoustic Emissions): Acoustic sensors detect sound patterns from the idlers. Unusual noises, such as grinding or knocking sounds, can be early indicators of mechanical problems within the idler.
- Load: Load sensors measure the forces exerted on the idlers. Uneven load distribution can suggest issues such as material buildup, belt misalignment, or an uneven surface.
- Belt Alignment: Some systems also monitor the alignment of the conveyor belt relative to the idlers. Misalignment can lead to uneven wear on the idlers and the belt, increasing the risk of failure.
2. Data Collection:
- Sensors continuously collect data on the above parameters, transmitting it to a central control system or data logger for processing. The data collection is often done in real-time, allowing for immediate analysis and response.
3. Real-Time Monitoring:
- The system analyzes the incoming data in real-time to identify any deviations from normal operating conditions. If a parameter exceeds a predefined threshold, the system can flag it as a potential issue.
- Real-time monitoring ensures that any developing problems are detected as soon as possible, allowing for quick intervention before the issue leads to a failure.
4. Trend Analysis:
- Over time, the system compiles historical data on idler performance, allowing for trend analysis. By examining trends in vibration, temperature, and other parameters, the system can identify gradual wear or degradation that might not trigger immediate alarms.
- Trend analysis helps in predicting when an idler might reach the end of its service life, enabling more accurate scheduling of maintenance and replacement activities.
5. Alerts and Notifications:
- If the system detects abnormal conditions, it generates alerts or notifications to inform operators or maintenance personnel. These alerts can be visual (e.g., lights or indicators on a control panel), auditory (e.g., alarms), or digital (e.g., emails, SMS, or notifications in a control system).
- The severity of the alert may vary depending on the level of the detected issue, ranging from warnings (suggesting upcoming maintenance) to critical alarms (indicating the need for immediate action).
6. Predictive Maintenance:
- One of the key benefits of condition monitoring is its role in predictive maintenance. By analyzing trends and deviations in the monitored parameters, the system can predict when an idler is likely to fail or require maintenance.
- Predictive maintenance helps reduce unplanned downtime by allowing maintenance to be scheduled at convenient times, and it extends the overall lifespan of the conveyor system components.
7. Data Logging and Reporting:
- All monitored data is logged for future reference. This historical data can be used to generate detailed reports on idler performance, maintenance history, and overall conveyor system health.
- Reports can help in optimizing maintenance schedules, improving the reliability of the conveyor system, and ensuring compliance with safety standards.
8. Automated Responses:
- In some advanced systems, condition monitoring is integrated with the conveyor’s control system, allowing for automated responses to certain conditions. For example, if a critical temperature threshold is exceeded, the system might automatically stop the conveyor to prevent further damage.
9. Integration with Other Systems:
- Condition monitoring systems can be integrated with other monitoring and control systems within the facility, such as SCADA (Supervisory Control and Data Acquisition) systems. This integration allows for a more holistic approach to monitoring and managing the entire conveyor system and related equipment.
10. Maintenance Planning:
- Based on the data collected and analyzed, the system can suggest specific maintenance actions, such as lubricating bearings, tightening bolts, adjusting alignment, or replacing worn idlers.
- Maintenance planning based on condition monitoring data ensures that maintenance activities are both effective and efficient, focusing resources on areas that need attention.
Condition monitoring in a Conveyor Idler Monitoring System is a proactive approach to maintaining the health and efficiency of conveyor systems. By continuously monitoring key parameters such as vibration, temperature, and load, the system can detect early signs of wear or failure, allowing for timely maintenance and reducing the risk of unplanned downtime. This approach not only enhances the reliability and safety of conveyor operations but also contributes to cost savings by extending the lifespan of critical components.
Health Conveyor Idler Monitoring System
A Health Conveyor Idler Monitoring System is a specialized subset of conveyor health monitoring systems, focusing specifically on the idlers, which are the rollers that support the conveyor belt and guide its movement. Monitoring the health of idlers is crucial because they are critical components that, if they fail, can cause significant damage to the conveyor belt and result in costly downtime.
Key Components and Features
Vibration Sensors:
- These sensors are mounted on the idlers to detect abnormal vibrations, which could indicate issues such as misalignment, bearing failure, or imbalance.
- Abnormal vibrations are a common early sign of idler wear and potential failure.
Temperature Sensors:
- Temperature sensors monitor the heat generated by the idler bearings. Elevated temperatures can signal bearing failure or excessive friction, which needs immediate attention.
- Overheating idlers can lead to fires, especially in environments with combustible materials.
Acoustic Monitoring:
- Acoustic sensors can detect unusual sounds generated by idlers that may indicate wear, misalignment, or other issues.
- These sensors help in identifying problems that might not yet be visible or measurable by vibration or temperature alone.
Load Sensors:
- Load sensors measure the force exerted on the idlers by the conveyor belt. Variations in load can indicate uneven wear, material buildup, or issues with the belt tension.
- Monitoring load ensures that the idlers are not being overstressed, which can lead to premature failure.
Visual Inspection Systems:
- Some systems include cameras or laser-based inspection devices to visually monitor the condition of the idlers, checking for wear, alignment, and physical damage.
Wireless Communication:
- Many idler monitoring systems use wireless communication to transmit data from the sensors to a central monitoring system. This reduces the need for extensive wiring and allows for easier installation and maintenance.
Data Analytics and Predictive Maintenance:
- The system collects and analyzes data from all sensors to predict potential failures and suggest maintenance actions before a breakdown occurs.
- Predictive algorithms can forecast the remaining useful life of idlers based on historical data and current operating conditions.
Integration with Conveyor Control Systems:
- The idler monitoring system can be integrated with the overall conveyor control system, enabling automated shutdowns or alerts if critical thresholds are reached.
Alarms and Notifications:
- The system can be configured to send alerts via email, SMS, or other communication channels when it detects conditions that require immediate attention.
Benefits
- Extended Idler Life:
- By catching issues early, the system helps in extending the operational life of the idlers, reducing the frequency of replacements.
- Reduced Downtime:
- Early detection of potential failures allows for planned maintenance, minimizing the impact on production.
- Enhanced Safety:
- Prevents catastrophic failures that could lead to accidents or fire hazards, especially in volatile environments.
- Cost Savings:
- By preventing unexpected breakdowns and reducing the frequency of idler replacements, the system contributes to significant cost savings over time.
- Improved Conveyor Performance:
- Ensuring that idlers are functioning properly helps maintain optimal conveyor belt performance, improving overall operational efficiency.
Applications
- Mining and Quarrying:
- Where long conveyor belts are used to transport heavy materials, making idler reliability crucial.
- Bulk Material Handling:
- In industries such as agriculture, cement, and power generation, where conveyors handle large volumes of materials.
- Manufacturing:
- Where conveyors are part of assembly lines, and uninterrupted operation is critical to maintaining production schedules.
- Ports and Terminals:
- In facilities where conveyors are used to move cargo, such as coal, ore, or grain, from ships to storage areas.
A Health Conveyor Idler Monitoring System is an essential tool for maintaining the reliability and safety of conveyor systems, particularly in industries where conveyor downtime can result in significant financial and operational losses.

Conveyor Idler Monitoring System: Conveyor Health Monitoring System
A Conveyor Health Monitoring System is a specialized system designed to continuously monitor the condition of conveyor belts and their components in industrial environments. This system helps in maintaining the reliability and efficiency of conveyor operations by providing real-time data and alerts on the health and performance of the conveyor system.
Key Features
Real-Time Monitoring:
- Sensors are installed along the conveyor belt to monitor various parameters such as speed, temperature, vibrations, and load.
- Data is collected continuously and analyzed in real-time to detect anomalies or deviations from normal operating conditions.
Predictive Maintenance:
- The system uses advanced algorithms to predict potential failures before they occur, allowing for planned maintenance activities.
- This helps in reducing unplanned downtime and extends the lifespan of conveyor components.
Vibration Analysis:
- Vibrational sensors detect irregularities in the movement of the conveyor belt or components, which could indicate issues like misalignment, wear, or bearing failure.
Temperature Monitoring:
- Temperature sensors monitor the heat generated by various conveyor components, which can indicate potential overheating or mechanical issues.
Belt Wear and Tear Monitoring:
- The system can measure the thickness and condition of the conveyor belt, helping to identify wear patterns and predict when the belt needs replacement.
Remote Monitoring and Control:
- Many modern systems are equipped with remote monitoring capabilities, allowing operators to access data and control the system from a central control room or even remotely via the internet.
Integration with Existing Systems:
- These systems can often be integrated with existing SCADA (Supervisory Control and Data Acquisition) systems for centralized monitoring and control.
Data Logging and Reporting:
- Historical data is logged and can be used for trend analysis, helping to identify patterns over time and improve the overall maintenance strategy.
Benefits
- Increased Operational Efficiency: By identifying issues early, the system helps in minimizing unplanned downtime and keeps the conveyor system running smoothly.
- Cost Savings: Predictive maintenance reduces the need for emergency repairs and extends the life of conveyor belt components.
- Safety: Early detection of potential issues can prevent accidents and ensure a safer working environment.
- Improved Asset Management: Continuous monitoring and data logging provide valuable insights for managing the lifecycle of conveyor system components.
Applications
- Mining Industry: Where conveyor belts are extensively used to transport materials over long distances.
- Manufacturing: In assembly lines and production plants where conveyors are crucial for moving products and materials.
- Logistics and Warehousing: Where conveyors are used to sort, move, and distribute packages and goods.
Overall, a Conveyor Health Monitoring System is a crucial tool for industries relying on conveyor systems to maintain high productivity and reduce operational risks.
Principle of Conveyor Idler Monitoring System Operation
The principle of operation for a Conveyor Idler Monitoring System involves the continuous collection, analysis, and reporting of data from various sensors installed on or near the idlers. The goal is to detect any abnormalities or deviations in the idler’s performance that could indicate wear, misalignment, or imminent failure. Here’s a breakdown of how the system operates:
1. Sensor Installation:
- Vibration Sensors: Mounted on the idler bearings or the conveyor idler frame, these sensors detect oscillations and vibrations. Abnormal vibration patterns can indicate issues like bearing failure, misalignment, or idler imbalance.
- Temperature Sensors: Attached to the idler bearings, these sensors monitor the temperature. An increase in temperature may indicate excessive friction or a failing bearing, which could lead to a fire or other severe issues.
- Acoustic Sensors: These detect unusual noises from the idler, which can be an early sign of mechanical problems.
- Load Sensors: Positioned under or near the idlers, these sensors measure the load distribution. Uneven load can point to issues like material buildup, belt misalignment, or a failing idler.
- Visual Inspection Systems: Cameras or lasers may be used to visually inspect the idlers for wear, alignment, and surface damage.
2. Data Acquisition:
- The sensors continuously collect data on vibration, temperature, acoustic emissions, and load conditions. This data is either transmitted wirelessly or via wired connections to a central processing unit or control system.
3. Data Analysis:
- Real-Time Analysis: The system processes the incoming data in real-time, comparing it against predefined thresholds and historical data to detect anomalies.
- Trend Analysis: Over time, the system builds a database of idler performance metrics, which can be used to identify trends that indicate gradual wear or degradation.
- Predictive Algorithms: Advanced algorithms analyze the data to predict the remaining useful life of the idlers. These predictions help in scheduling maintenance before a failure occurs.
4. Condition Monitoring:
- The system continuously monitors the condition of the idlers, looking for signs of degradation or failure. This includes monitoring for:
- Increased vibration levels.
- Rising temperatures.
- Unusual acoustic patterns.
- Uneven load distribution.
5. Alerts and Notifications:
- If the system detects any abnormal conditions, it triggers alerts to the operators. These alerts can be in the form of visual alarms on a control panel, emails, SMS, or other notification methods.
- Alerts can range from warnings (indicating that maintenance is needed soon) to critical alarms (indicating that immediate action is required to prevent failure).
6. Reporting and Logging:
- The system logs all data, including normal operating conditions and any detected anomalies. This information is stored for future reference and can be used to generate reports on idler performance, maintenance history, and overall conveyor system health.
- Reports can be used for maintenance planning, compliance with safety regulations, and optimization of conveyor operations.
7. Integration with Conveyor Control Systems:
- The monitoring system can be integrated with the conveyor’s overall control system. In some cases, it may automatically stop the conveyor if a critical failure is detected, preventing further damage or safety risks.
- This integration allows for a coordinated response to any detected issues, ensuring that the entire conveyor system operates smoothly and safely.
8. Maintenance Planning:
- Based on the data collected and analyzed, the system can recommend maintenance actions, such as lubricating bearings, adjusting alignment, or replacing worn idlers.
- The predictive maintenance approach minimizes unplanned downtime and extends the life of the idlers and the conveyor system as a whole.
The principle of a Conveyor Idler Monitoring System is based on the continuous monitoring and analysis of key parameters like vibration, temperature, and load. By detecting abnormalities early, the system helps prevent failures, reduces downtime, and extends the lifespan of conveyor components. Through real-time monitoring, predictive analytics, and integration with conveyor control systems, these systems play a crucial role in maintaining efficient and safe conveyor operations.

Advanced Monitoring Technologies in Conveyor Idler Monitoring System
As technology advances, so do the methods for maintaining and monitoring conveyor systems. A conveyor idler monitoring system now incorporates sophisticated technologies that significantly enhance its effectiveness and reliability.
Acoustic Fiber Optic Monitoring Systems
Acoustic fiber optic monitoring systems are at the forefront of advanced monitoring technologies used in conveyor idler monitoring systems. These systems utilize fiber optic cables to detect acoustic signals generated by conveyor idlers in operation. Here’s how they work:
- Real-Time Monitoring: Fiber optic cables are installed along the length of the conveyor system. These cables detect acoustic signals emitted by the idlers as they rotate.
- Early Detection of Issues: Changes in the acoustic signature can indicate potential issues such as misalignment, bearing failure, or uneven loading. The system can detect these anomalies early, allowing for proactive maintenance.
- Non-Intrusive Installation: The fiber optic cables can be installed without interfering with the conveyor’s operation. This non-intrusive nature ensures that monitoring does not disrupt the material handling process.
- High Sensitivity: Acoustic fiber optic systems are highly sensitive, capable of detecting minute changes in sound patterns. This sensitivity ensures that even minor issues are identified before they escalate.
- Data Analysis and Alerts: The system continuously analyzes the acoustic data and can trigger alerts if abnormal sounds are detected. This real-time data analysis helps in maintaining optimal conveyor performance and preventing unexpected downtimes.
The Role of Precision in Pulley and Idler Design as Detailed in the PPI Idlers Catalog
Precision in the design and manufacturing of pulleys and idlers is crucial for the efficiency of a conveyor idler monitoring system. The PPI (Precision Pulley and Idler) catalog emphasizes the importance of high-quality components in ensuring reliable conveyor operation. Here’s why precision matters:
- Enhanced Durability: Precision-designed pulleys and idlers are built to withstand high loads and harsh operating conditions, extending their lifespan and reducing the frequency of replacements.
- Optimal Performance: High-quality, precisely manufactured components ensure smooth operation, reducing friction and energy consumption.
- Reduced Maintenance: Precision in design minimizes tear and wear on the conveyor belt system, leading to fewer maintenance requirements and lower overall costs.
- Accurate Monitoring: When pulleys and idlers are manufactured with precision, their performance is predictable and consistent. This accuracy is essential for the monitoring system to detect any deviations from normal operation effectively.
- Safety Improvements: Reliable, well-designed components contribute to the overall safety of the conveyor system, preventing accidents caused by component failures.
By integrating advanced technologies like acoustic fiber optic monitoring and emphasizing precision in pulley and idler design, a conveyor idler monitoring system can provide unparalleled monitoring capabilities. These advancements enable real-time tracking, early issue detection, and efficient maintenance, ensuring the conveyor system operates smoothly and reliably.
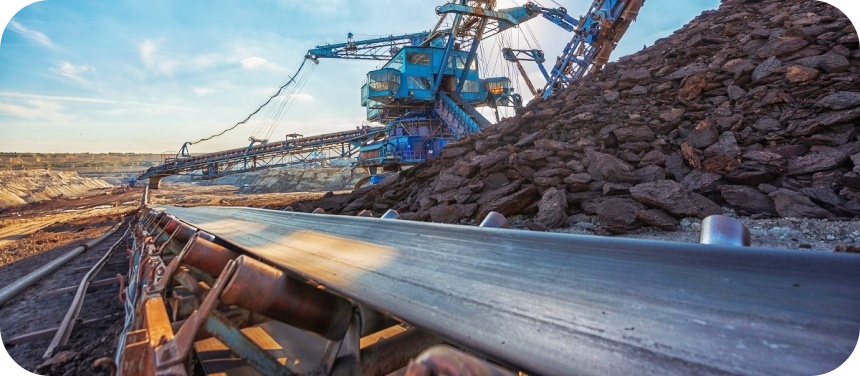
Benefits of Implementing a Conveyor Idler Monitoring System
Implementing a conveyor idler monitoring system offers numerous advantages that enhance the efficiency, safety, and cost-effectiveness of conveyor operations.
How Monitoring Systems Can Reduce Downtime
A conveyor idler monitoring system plays a crucial role in minimizing downtime by providing continuous, real-time data on the condition of idlers. When the system detects anomalies or signs of wear, it triggers alerts, allowing for timely intervention before a minor issue escalates into a major failure. This proactive approach ensures that maintenance can be scheduled during planned downtimes, rather than causing unexpected interruptions to the production process. By reducing unplanned downtimes, the system helps maintain steady production schedules and enhances overall operational efficiency.
The Importance of Predictive Maintenance Enabled by Accurate Monitoring
Predictive maintenance is a critical component of modern industrial operations, and a conveyor idler monitoring system is integral to this strategy. Here are five examples of how accurate monitoring enables predictive maintenance:
- Early Detection of Bearing Wear: The system can detect subtle changes in vibration patterns that indicate bearing wear, allowing maintenance teams to replace bearings before they fail completely.
- Alignment Issues: Continuous monitoring can identify slight misalignments in the conveyor belt, which can be corrected before they cause significant damage or operational inefficiencies.
- Temperature Monitoring: By tracking the temperature of idlers, the system can alert operators to overheating, which can prevent fires or damage to the conveyor belt.
- Load Imbalances: The system can detect uneven load distribution, prompting adjustments that prevent excessive wear on specific idlers and prolong the lifespan of the conveyor components.
- Component Fatigue: Monitoring can reveal signs of metal fatigue or other structural issues in the idlers, enabling preemptive repairs or replacements to avoid catastrophic failures.
Cost Savings and Improved Safety for Operators and Machinery
Implementing a conveyor idler monitoring system leads to significant cost savings and enhances safety for operators and machinery.
- Reduced Maintenance Costs: By identifying issues early and allowing for planned maintenance, the system reduces the frequency and cost of emergency repairs.
- Extended Equipment Lifespan: Predictive maintenance and timely interventions extend the lifespan of conveyor components, reducing the need for expensive replacements.
- Energy Efficiency: Properly maintained idlers and aligned conveyor belts reduce friction and energy consumption, leading to lower operational costs.
- Improved Safety: By preventing unexpected equipment failures, the system reduces the risk of accidents and injuries to operators, creating a safer work environment.
- Operational Efficiency: Continuous monitoring ensures that the conveyor system operates at peak efficiency, minimizing production delays and optimizing throughput.
A conveyor idler monitoring system is an invaluable tool for any operation that relies on conveyor systems. By reducing downtime, enabling predictive maintenance, and providing significant cost savings and safety improvements, such a system enhances the reliability and efficiency of conveyor operations.
Monitoring System Features in Conveyor Idler Monitoring System
A comprehensive conveyor idler monitoring system is equipped with several advanced features that ensure efficient and seamless operation. These features are designed to integrate smoothly with existing conveyor systems, provide non-intrusive monitoring, and deliver real-time data and alerts.
Integration with Existing Conveyor Systems
One of the key features of a conveyor idler monitoring system is its ability to integrate with existing conveyor systems without requiring significant modifications. This integration is crucial for the following reasons:
- Seamless Installation: The monitoring system can be retrofitted to existing conveyor setups, minimizing downtime during installation.
- Compatibility: Designed to work with a variety of conveyor components, including different types of idlers and pulleys, ensuring broad applicability.
- Scalability: The system can be scaled up or down depending on the size and complexity of the conveyor system, making it suitable for both small and large operations.
- Data Integration: It can integrate with existing data management systems, allowing for centralized monitoring and control.
- Cost-Effective: By utilizing existing infrastructure, the system reduces the need for new investments, making it a cost-effective solution.
Non-Intrusive Sensors and How They Communicate Data
The sensors used in a conveyor idler monitoring system are designed to be non-intrusive, ensuring they do not interfere with the conveyor’s operation. Here’s how these sensors function and communicate data:
- Installation: Non-intrusive sensors are mounted on or near the conveyor idlers without requiring modifications to the conveyor idler structure.
- Types of Sensors: These may include vibration sensors, acoustic sensors, and thermal sensors, each monitoring different aspects of idler performance.
- Wireless Communication: Sensors typically use wireless technology to transmit data to a central monitoring unit, eliminating the need for extensive cabling.
- Real-Time Data Transmission: Data is transmitted in real-time, ensuring that any anomalies are detected immediately.
- Low Maintenance: Non-intrusive sensors are generally low maintenance, as they are not exposed to the harsh conditions that conveyor components endure.
Real-Time Tracking and Alerts for Idler Performance
Real-time tracking and alerts are fundamental features of a conveyor idler monitoring system, providing continuous oversight and immediate notifications of any issues. Here’s how these features work:
- Continuous Monitoring: The system continuously tracks the performance of each idler, including parameters such as vibration levels, temperature, and alignment.
- Data Analysis: Advanced algorithms analyze the collected data to identify patterns and detect deviations from normal performance.
- Immediate Alerts: If the system detects any abnormal conditions, it sends immediate alerts to operators via various channels, such as emails, SMS, or on-screen notifications.
- Predictive Insights: By analyzing historical data, the system can provide predictive insights, suggesting when maintenance should be performed to prevent failures.
- User Interface: A user-friendly interface allows operators to view real-time data, historical trends, and alerts, facilitating quick decision-making and response.
The features of a conveyor idler monitoring system, including integration with existing systems, non-intrusive sensors, and real-time tracking and alerts, work together to ensure the smooth and efficient operation of conveyor systems. By providing continuous monitoring and immediate feedback, these systems help in maintaining optimal performance, enhancing safety, and reducing operational costs.

Case Studies and Examples in Conveyor Idler Monitoring System
Examination of Industry Scenarios Where Monitoring Systems Have Been Beneficial
Mining Industry: In large mining operations, conveyor systems are crucial for transporting extracted materials. A conveyor idler monitoring system helped BHP Billiton reduce unexpected downtimes by 40%, significantly improving productivity and ensuring continuous material flow.
Manufacturing Plants: Bosch implemented a conveyor idler monitoring system in their plant that produces automotive parts to track the performance of its conveyor lines. The system detected early signs of misalignment and bearing wear, allowing for timely maintenance and preventing costly production stoppages.
Food Processing Industry: In a Kraft Heinz food processing facility, the conveyor idler monitoring system played a vital role in maintaining hygiene standards. By ensuring that the conveyors operated smoothly and efficiently, the system helped prevent contamination and product spoilage, enhancing overall product quality and safety.
Port Operations: At the Port of Rotterdam, conveyor systems are used to move bulk materials such as grain and coal. The implementation of a monitoring system enabled port operators to identify potential issues before they led to conveyor breakdowns, thereby maintaining the steady flow of goods and minimizing delays.
Logistics and Warehousing: DHL integrated a conveyor idler monitoring system in a large distribution center to manage its extensive conveyor network. The system provided real-time alerts on any deviations from normal operations, allowing the maintenance team to address issues promptly and ensuring the timely delivery of packages.
Success Stories and Testimonials from the Use of Precision Pulley, Idler Products, and Monitoring Systems
The effectiveness of a conveyor idler monitoring system is often reflected in the success stories and testimonials from companies that have adopted these technologies.
- Mining Company Testimonial: “Since implementing the conveyor idler monitoring system, our downtime due to conveyor issues has been cut by nearly half. The system’s real-time alerts and predictive maintenance features have been game-changers for our operation.” – Operations Manager, Leading Mining Company
- Automotive Manufacturer Success Story: An automotive parts manufacturer reported a significant improvement in their production efficiency. The precision pulley and idler products, combined with the monitoring system, enabled them to maintain optimal conveyor performance, resulting in a 25% increase in output.
- Food Processing Facility Feedback: “The conveyor idler monitoring system has greatly enhanced our ability to maintain high hygiene standards. By preventing unexpected conveyor failures, we’ve minimized the risk of contamination and ensured the quality of our products.” – Quality Assurance Manager, Food Processing Company
- Port Operations Case Study: A major port documented their experience with the conveyor idler monitoring system, highlighting how it reduced maintenance costs and improved the reliability of their conveyor systems. The system’s ability to detect issues early prevented major disruptions and facilitated smoother port operations.
- Logistics Center Testimonial: “Integrating the conveyor idler monitoring system into our logistics network has been incredibly beneficial. The system’s real-time tracking and alerts have allowed us to address issues before they impact our operations, ensuring that our distribution process remains efficient and reliable.” – Logistics Director, Major Distribution Center
The implementation of a conveyor idler monitoring system has demonstrated significant benefits across various industries. Through real-time monitoring, predictive maintenance, and improved operational efficiency, these systems have proven to be invaluable in maintaining the smooth operation of conveyor systems. The success stories and testimonials further validate the positive impact of these advanced monitoring technologies.
Choosing the Right Conveyor Idler Monitoring System
Selecting the appropriate conveyor idler monitoring system is crucial for ensuring the efficiency and reliability of your conveyor operations. Here are the key factors to consider and the importance of compatibility with various conveyor components.
Factors to Consider When Selecting an Idler Monitoring System
- Real-Time Monitoring Capabilities: Ensure the system provides real-time data on the condition of idlers. Real-time monitoring allows for immediate detection of issues, enabling prompt maintenance actions and preventing costly downtimes.
- Data Accuracy and Analysis: The monitoring system should offer high accuracy in data collection and robust analytical capabilities. Accurate data helps in identifying even the slightest anomalies, facilitating predictive maintenance and improving overall system reliability.
- Ease of Integration: Choose a monitoring system that can be easily integrated with your existing conveyor infrastructure. This includes compatibility with current sensors, data management systems, and other monitoring equipment to avoid additional costs and complexities.
- Scalability: Opt for a system that can be scaled to match the size and complexity of your conveyor operations. This ensures that as your operations grow, the monitoring system can expand accordingly without requiring a complete overhaul.
- User-Friendly Interface: The system should feature an intuitive and user-friendly interface. Easy access to real-time data, historical trends, and alerts through a simple dashboard can significantly enhance operational efficiency and decision-making.
The Significance of Compatibility with Various Types of Conveyor Tracking Rollers, Speed Switches, and Idlers
- Compatibility with Tracking Rollers: The monitoring system should be compatible with various types of conveyor tracking rollers. This ensures accurate monitoring of belt alignment and helps in maintaining the proper tracking of the conveyor belt, reducing the risk of belt misalignment and wear.
- Integration with Speed Switches: Ensure the system works seamlessly with both conveyor speed switches and zero speed switches. This compatibility is essential for monitoring the speed of the conveyor belt and detecting any deviations from normal operation, which can prevent damage and improve safety.
- Adaptability to Different Idler Types: The system must be adaptable to various types of idlers, including carrying idlers, return idlers, and impact idlers. This flexibility allows for comprehensive monitoring of all idler components, ensuring optimal performance across the entire conveyor system.
- Support for Different Conveyor Systems: The chosen monitoring system should support a range of conveyor systems, from simple belt conveyors to more complex systems involving multiple conveyor types. This versatility ensures that the system can be used across different operations within the same facility.
- Integration with Existing Maintenance Protocols: The monitoring system should integrate with your current maintenance protocols and workflows. This compatibility ensures that data from the monitoring system can be seamlessly incorporated into maintenance schedules, facilitating proactive and efficient maintenance practices.
Choosing the right conveyor idler monitoring system involves careful consideration of factors such as real-time monitoring capabilities, data accuracy, ease of integration, scalability, and user interface. Additionally, ensuring compatibility with various conveyor tracking rollers, speed switches, and idlers is crucial for comprehensive and effective monitoring. By addressing these aspects, you can select a monitoring system that enhances the reliability, efficiency, and safety of your conveyor operations.
Installation and Maintenance of a Conveyor Idler Monitoring System
Basic Guide on Setting Up an Idler Monitoring System
Setting up a conveyor idler monitoring system involves several key steps to ensure it functions effectively and integrates seamlessly with your existing conveyor infrastructure.
- Pre-Installation Assessment: Conduct a thorough assessment of your conveyor system to identify critical points where monitoring will be most beneficial. This includes examining the types of idlers, pulleys, and other components in use.
- Selecting the Right Sensors: Choose appropriate sensors that align with your monitoring needs. These may include vibration sensors, temperature sensors, and acoustic sensors. Ensure that the sensors are compatible with your conveyor idler monitoring system.
- Sensor Placement: Install the sensors at strategic locations on or near the conveyor idlers. Proper placement is crucial for accurate data collection. Sensors should be positioned to capture the most relevant data without interfering with conveyor operations.
- System Integration: Connect the sensors to the central monitoring unit. This often involves setting up wireless communication networks to transmit data from the sensors to the monitoring system. Ensure that the integration process does not disrupt ongoing operations.
- Calibration and Testing: Once installed, calibrate the sensors to ensure they provide accurate readings. Perform initial tests to verify that the system is correctly capturing and analyzing data. Make any necessary adjustments based on the test results.
- User Training: Train your maintenance team and operators on how to use the monitoring system. This includes understanding the user interface, interpreting data, and responding to alerts.
Maintenance Protocols and Best Practices for Ensuring Prolonged System Efficiency
To maintain the efficiency and reliability of your conveyor idler monitoring system, adhere to the following maintenance protocols and best practices:
- Regular System Checks: Perform routine checks on the monitoring system to ensure it is functioning correctly. This includes verifying sensor connections, checking for software updates, and ensuring data accuracy.
- Data Review and Analysis: Regularly review the data collected by the monitoring system. Look for patterns or anomalies that could indicate potential issues with the conveyor idlers. Use this data to make informed maintenance decisions.
- Scheduled Calibration: Periodically calibrate the sensors to maintain their accuracy. Calibration schedules should be based on manufacturer recommendations and operational demands. Regular calibration helps in minimizing false alarms and missed detections.
- Proactive Maintenance: Use the data from the conveyor idler monitoring system to implement proactive maintenance strategies. Address issues before they escalate into major problems, reducing the risk of unexpected downtimes.
- System Upgrades: Stay updated with the latest advancements in monitoring technology. Upgrading your system with new features or improved sensors can enhance its efficiency and effectiveness.
- Documentation and Reporting: Maintain detailed records of all maintenance activities, system checks, and calibrations. Documenting these activities helps in tracking system performance over time and can provide valuable insights for future improvements.
- Operator Feedback: Encourage operators to provide feedback on the system’s performance. They can offer practical insights into how the system is working in real-world conditions and suggest areas for improvement.
The successful installation and maintenance of a conveyor idler monitoring system require careful planning, regular maintenance, and ongoing evaluation. By following the outlined steps and best practices, you can ensure that your monitoring system remains reliable, providing continuous oversight and helping to maintain the optimal performance of your conveyor operations.
Need pricing for conveyor belts? Contact us through the inquiry form.
FAQs About Conveyor Idler Monitoring System
A conveyor idler plays a crucial role in the operation of conveyor systems. Idlers are cylindrical rollers positioned along the length of the conveyor belt to support and guide the belt as it moves. Their primary function is to reduce friction and wear on the belt, ensuring smooth and efficient transportation of materials. Conveyor idlers help maintain the belt’s alignment and stability, preventing it from sagging or becoming misaligned. This is essential for maintaining the conveyor’s operational efficiency and longevity. Additionally, idlers contribute to the even distribution of the load on the belt, reducing the risk of damage and prolonging the life of both the belt and the conveyor system. By minimizing wear and tear, idlers play a significant role in reducing maintenance costs and downtime, making them a vital component in conveyor operations across various industries.
Various sensors are used in conveyor belt monitoring systems to ensure efficient and safe operation. Some common types include:
Vibration Sensors: These sensors detect irregular vibrations that could indicate issues such as misaligned idlers or belt imbalances. They help in identifying problems early, preventing potential damage and downtime.
Temperature Sensors: These are used to monitor the temperature of the conveyor belt and idlers. Excessive heat can indicate friction issues or bearing failures. Temperature sensors help in maintaining optimal operating conditions and preventing overheating.
Acoustic Sensors: These sensors listen for abnormal sounds that might indicate problems with the conveyor components, such as idler or bearing failures. Acoustic sensors are effective in early detection of issues that could lead to significant damage if not addressed promptly.
Proximity Sensors: These are used to monitor the alignment of the belt and idlers. They ensure that the belt stays in the correct position and helps in detecting any misalignment that could lead to belt wear or damage.
Load Sensors: These measure the load on the conveyor belt, helping to prevent overloading and ensuring efficient material handling.
Conveyor idlers come in various types, each designed to perform specific functions and meet different operational requirements:
Carrying Idlers: These idlers support the loaded section of the conveyor belt and are typically placed along the carrying side of the belt. They ensure smooth and stable movement of the materials being transported.
Return Idlers: Positioned on the underside of the conveyor belt, return idlers support the empty belt on its return journey. They help maintain belt alignment and reduce wear and tear on the belt’s return side.
Impact Idlers: Installed at loading points, impact idlers are designed to absorb the shock of material loading, protecting the belt from damage and reducing the impact forces.
Transition Idlers: These idlers are used at the transition points where the conveyor belt changes direction or angle. They help in maintaining the belt’s alignment and prevent spillage.
Training Idlers: Also known as aligning idlers, these idlers help in correcting and maintaining the belt’s alignment throughout its operation. They are crucial in preventing belt misalignment and reducing maintenance issues.
Self-Aligning Idlers: These idlers automatically adjust to ensure proper belt tracking and alignment, reducing the need for manual adjustments and enhancing operational efficiency.
A side guide idler, also known as a guide roller, performs several essential functions in a conveyor system. Its primary purpose is to maintain the alignment of the conveyor belt, ensuring it stays centered as it moves along the conveyor path. This is crucial for preventing the belt from drifting off-track, which can lead to spillage, uneven wear, and potential damage to the belt and other components.
Side guide idlers are strategically placed along the edges of the conveyor belt, providing lateral support and guiding the belt to prevent misalignment. By doing so, they help in maintaining smooth and efficient operation, reducing the risk of downtime and maintenance issues. Additionally, side guide idlers contribute to extending the lifespan of the conveyor belt by minimizing edge wear and tear, which can occur if the belt continuously rubs against the conveyor structure.
In summary, side guide idlers play a vital role in ensuring the stable and efficient operation of conveyor systems by maintaining belt alignment, preventing spillage, and reducing wear and maintenance costs.
Inspecting a conveyor system in a mining or heavy industrial context involves several key steps:
Visual Inspection: Regularly check the belt for signs of wear, tears, or damage. Inspect idlers, pulleys, and other components for misalignment, corrosion, or wear.
Check Belt Tension: Ensure the conveyor belt is properly tensioned. Excess slack can cause slipping or misalignment, while over-tensioning can lead to premature wear.
Lubrication: Inspect and lubricate bearings, gears, and other moving parts as required by the manufacturer’s guidelines.
Alignment: Verify that the belt is properly aligned with the pulleys and idlers to prevent tracking issues.
Check Electrical Components: Inspect motor control panels, sensors, and wiring for signs of wear, corrosion, or damage.
Load Testing: Occasionally run the conveyor under load conditions to check for any performance issues, unusual noises, or vibrations.
Safety Inspections: Ensure all safety guards, emergency stop switches, and protective devices are in place and functioning correctly.
Conveyor tracking refers to the process of maintaining the proper alignment of the conveyor belt on the idlers and pulleys as it moves through the system. Proper tracking ensures that the belt runs straight and does not wander off the track, which can cause damage to the belt, increased wear on components, and potential downtime. Tracking mechanisms may include adjustable idlers, edge guides, or crowned pulleys.
The number of idlers in a conveyor belt system varies depending on the length and design of the conveyor. Idlers are spaced at regular intervals along the conveyor to support the belt and the material being transported. For heavy-duty applications like in mining, the spacing might range from 1 to 1.5 meters (approximately 3 to 5 feet). The total number of idlers will depend on the total length of the conveyor and the specific design requirements.
A common sensor used for tracking rotation in conveyor systems is an encoder. Encoders can be mounted on the motor shaft or conveyor pulleys to monitor the speed and direction of rotation. These sensors provide feedback to the control system, ensuring the conveyor is operating at the correct speed and helping to detect any anomalies in rotation that could indicate potential issues.
The frequency of conveyor inspections depends on the operational demands and the environment in which the conveyor is used. In heavy industrial and mining applications, inspections should typically be conducted:
Daily: Perform basic visual checks and ensure that the system is running smoothly.
Weekly: Conduct a more thorough inspection, checking belt tension, alignment, and the condition of idlers and pulleys.
Monthly: Perform a comprehensive inspection, including electrical components, lubrication of parts, and a detailed review of safety systems.
Annually: Conduct a full system audit, including detailed checks of structural components, load-bearing parts, and overall system performance.
Belt tracking works by adjusting the alignment of the conveyor belt to ensure it stays centered on the conveyor structure. This is achieved through a combination of design features and manual adjustments:
Crowned Pulleys: These have a slight curvature that naturally centers the belt.
Adjustable Idlers: These can be tilted slightly to steer the belt back to the centerline.
Tracking Devices: These can include edge sensors that detect when the belt starts to drift and automatically adjust the tracking mechanisms.
Manual Adjustment: Operators may manually adjust the tension or alignment of the belt to correct any tracking issues.
Proper belt tracking is essential in mining and heavy industry to prevent belt damage, reduce wear on components, and avoid unplanned downtime.
Last Updated on August 14, 2024 by Jordan Smith
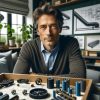
Jordan Smith, a seasoned professional with over 20 years of experience in the conveyor system industry. Jordan’s expertise lies in providing comprehensive solutions for conveyor rollers, belts, and accessories, catering to a wide range of industrial needs. From initial design and configuration to installation and meticulous troubleshooting, Jordan is adept at handling all aspects of conveyor system management. Whether you’re looking to upgrade your production line with efficient conveyor belts, require custom conveyor rollers for specific operations, or need expert advice on selecting the right conveyor accessories for your facility, Jordan is your reliable consultant. For any inquiries or assistance with conveyor system optimization, Jordan is available to share his wealth of knowledge and experience. Feel free to reach out at any time for professional guidance on all matters related to conveyor rollers, belts, and accessories.