Conveyor Idler Roller Design: Standards and Specifications
In the realm of material handling, the design and implementation of conveyor systems are pivotal for operational efficiency. Central to these systems is the concept of conveyor idler roller design, which plays a crucial role in ensuring the smooth and reliable transportation of goods. Idler rollers, often overlooked, are the backbone of any conveyor system, providing critical support to the conveyor belt and the materials being conveyed. Their design and placement directly influence the conveyor’s efficiency, affecting everything from belt health to the energy required to move goods. Understanding the intricacies of idler roller design is essential for optimizing conveyor operations, making it a key area of focus for engineers and system designers aiming to enhance productivity and minimize downtime in industrial settings.
What Are the Types of Conveyor Idlers in Conveyor Idler Roller Design
The intricate world of conveyor idler roller design encompasses a variety of idler types, each tailored to meet specific operational needs within conveyor systems. These idlers play pivotal roles in the functionality and longevity of conveyor belts, influencing factors such as load distribution, belt alignment, and material handling efficiency. Below, we delve into seven key types of conveyor idlers, exploring their unique designs, applications, and benefits.
Trough Idlers: Trough idlers, characterized by their concave shape, are designed to cradle the conveyor belt and materials, promoting stability and reducing spillage. They typically consist of three to five rollers arranged in a ‘trough’ formation, providing ample support for the belt and its contents. This design is particularly beneficial for handling bulk materials, ensuring an even distribution of weight and minimizing wear on the belt.
Flat Return Idlers: Flat return idlers are utilized on the return path of the conveyor belt to support the belt’s underside. Their simplistic design, featuring a single horizontal roller, helps maintain belt integrity by preventing sagging and ensuring smooth operation. These idlers are crucial for the longevity of the conveyor belt, reducing the need for frequent maintenance and replacements.
Impact Idlers: Positioned at loading points where material is dropped onto the belt, impact idlers are designed to absorb the shock and distribute the force of falling materials. Their robust construction minimizes damage to the belt and idler structure, extending the life of the conveyor system. Impact idlers are essential in heavy-duty applications where the conveyor is subjected to high impact forces.
Training Return Idlers: Training return idlers are specialized in correcting misalignments in the conveyor belt’s path. Equipped with a pivoting mechanism, these idlers adjust the belt’s position to ensure it remains centered, preventing edge damage and spillage. Their self-aligning feature is vital for maintaining optimal conveyor performance and reducing downtime caused by misalignments.
Self-Aligning Idlers: Similar to training idlers, self-aligning idlers are designed to automatically correct any misalignment of the conveyor belt. They are typically used in pairs, with one idler pivoting in the direction of belt travel and the other in the opposite direction, ensuring the belt remains centered over long distances.
Spiral Return Idlers: Spiral return idlers feature a unique design with a helical arrangement of the roller surface. This design helps to clean the belt by dislodging and removing accumulated material from the belt’s surface, particularly useful in applications where sticky or wet materials are conveyed.
Guide Idlers: Guide idlers are installed on the sides of the conveyor belt to prevent the belt from wandering off its intended path. They provide lateral support and are especially useful in situations where the conveyor path has curves or the belt is prone to misalignment.
Idlers vs. Rollers: Understanding the Distinction
In the realm of conveyor idler roller design, understanding the nuanced roles and configurations of idlers versus rollers is crucial. Idlers, with their varied types and strategic placements, are key to the conveyor’s structural integrity and operational efficiency. In contrast, rollers focus on the mechanical movement, ensuring the conveyor belt glides smoothly for optimal material transport. This distinction underscores the importance of precise design and selection in creating effective conveyor systems.
Key Factors in Conveyor Idler Roller Design
The design of conveyor idler rollers is a complex process that requires careful consideration of various factors to ensure the conveyor system operates efficiently and reliably. Here, we delve into the key factors in conveyor idler roller design, highlighting the importance of each aspect in maintaining the integrity and functionality of the conveyor system.
Load Capacity Determination: The foundation of idler roller design lies in accurately determining the load capacity. Idler rollers must be capable of supporting the weight of both the conveyor belt and the materials being transported without undergoing deformation. This requires precise calculations to ensure the rollers are robust enough to handle the expected loads over their operational lifespan.
Bearing Selection: Bearings are critical components that facilitate the smooth rotation of idler rollers. The selection of bearings is based on the anticipated loads, operational speeds, and environmental conditions such as dust, moisture, and temperature. High-quality bearings reduce maintenance requirements and extend the life of the idler rollers.
Idler Roller Diameter and Length: The diameter and length of idler rollers directly influence their load-carrying capacity and the distribution of weight across the conveyor belt. Larger diameters and appropriate lengths can enhance the conveyor’s ability to handle heavier loads and distribute them more evenly, reducing the risk of belt sagging and material spillage.
Material Selection: The choice of materials for the roller shell is crucial for withstanding the operational and environmental challenges faced by the conveyor system. Materials such as steel, stainless steel, or composite materials are commonly used for their durability and resistance to wear, corrosion, and impact.
Surface Coating: Surface coatings are applied to idler rollers to improve traction between the roller and the conveyor belt, reduce wear, and prevent the buildup of materials on the roller surface. Coatings such as rubber or polyurethane can significantly enhance the performance and longevity of idler rollers.
Design Types: The specific requirements of the conveyor system dictate the selection of idler roller design. Options include troughing idlers for general support, impact idlers for high-load areas, and return idlers for the underside of the conveyor, among others. Each design type addresses specific operational needs.
Idler Spacing: Optimal idler spacing is essential for maintaining belt stability and preventing sagging. The spacing is determined based on the belt width, load conditions, and the type of idlers used, ensuring even support and minimizing belt deformation.
Shaft Design: The shaft of the idler roller must be designed to withstand torsional forces and provide adequate support to the roller. Material selection and shaft dimensions are critical to prevent bending or failure under load.
Seals and Dust Covers: Protecting the bearings from contaminants such as dust, water, and debris is vital for extending the lifespan of idler rollers. Seals and dust covers prevent the ingress of contaminants, reducing the need for maintenance and replacement.
Minimizing Roller Rotation Resistance: Low roller rotation resistance is key to efficient conveyor operation. Proper bearing selection, lubrication, and alignment reduce resistance, ensuring smooth roller movement and reducing energy consumption.
Impact Resistance: In areas where the conveyor belt receives impact from falling materials, idler rollers must be designed for impact resistance. This involves selecting materials and designs that can absorb and dissipate impact forces, protecting the conveyor belt and structure.
Testing and Prototyping: Rigorous testing and prototyping are integral to the conveyor idler roller design process. These steps validate the design under actual operating conditions, allowing for adjustments and improvements before full-scale production and implementation.
Each factor in conveyor idler roller design plays a pivotal role in the overall performance and reliability of the conveyor system. Careful consideration and optimization of these factors are essential for designing idler rollers that meet the specific needs of the conveyor system, ensuring efficient operation and long service life.
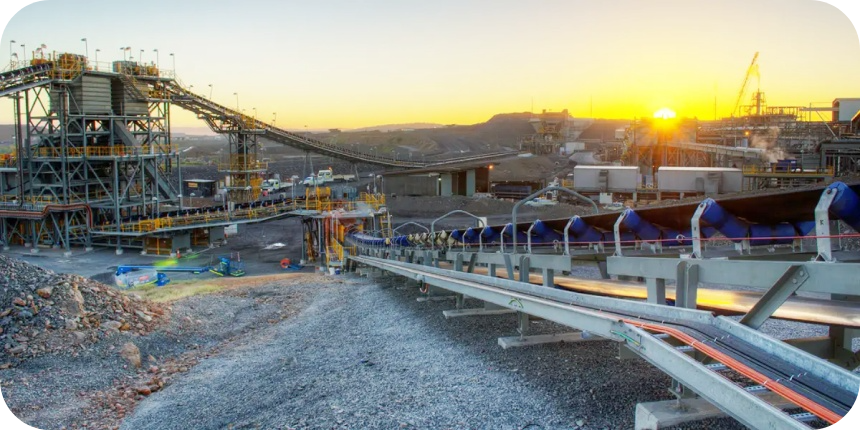
Conveyor Idler Specifications and Standards in Conveyor Idler Roller Design
The realm of conveyor idler roller design is governed by a comprehensive set of specifications and standards that ensure the compatibility, efficiency, and safety of conveyor systems. These guidelines are pivotal in harmonizing various components of conveyor systems, facilitating their seamless integration and operation. Below, we explore the critical specifications and standards that shape the design and application of conveyor idlers.
Key Specifications and Standards
- Dimensional Standards: Establish uniform dimensions for idlers, ensuring interchangeability across different manufacturers and systems.
- Load Capacity Ratings: Define the minimum load capacities idlers must support, tailored to various operational conditions.
- Material Specifications: Specify the materials for idler construction, including criteria for durability, wear resistance, and environmental compatibility.
- Bearing Standards: Detail the requirements for bearings, including types, load ratings, and lubrication, to ensure longevity and reliability.
- Troughing Angles: Standardize the angles for troughing idlers to optimize material carrying capacity and minimize spillage.
- Impact Resistance: Set benchmarks for idlers in high-impact zones, ensuring they can absorb and dissipate forces effectively.
- Seal and Dust Cover Requirements: Outline the specifications for sealing mechanisms to protect bearings from contaminants.
- Roller Diameter and Wall Thickness: Provide guidelines on roller diameters and wall thicknesses to accommodate various belt widths and speeds.
- Testing Protocols: Define the testing procedures for idlers, including load, impact, and endurance tests, to validate their performance.
Importance of Adhering to Standards
- Interchangeability: Standards ensure that idlers from different manufacturers can be used interchangeably, simplifying maintenance and replacements.
- System Compatibility: Adherence to standards guarantees that idlers will function seamlessly within the broader conveyor system, avoiding operational disruptions.
- Safety: Compliance with established standards minimizes the risk of failures that could lead to accidents and injuries.
- Efficiency: Standardized idler designs contribute to optimal conveyor performance, reducing energy consumption and operational costs.
- Durability: Standards for materials and construction ensure that idlers can withstand the rigors of operation, extending their service life.
- Maintenance Simplification: Uniform specifications facilitate easier and more predictable maintenance schedules, reducing downtime.
- Quality Assurance: Adhering to standards is a mark of quality, providing assurance that the idlers meet certain performance and durability benchmarks.
- Regulatory Compliance: In many jurisdictions, following industry standards is a regulatory requirement, ensuring that conveyor systems meet legal safety and performance criteria.
In the intricate landscape of conveyor idler roller design, adherence to specifications and standards is non-negotiable. These guidelines not only ensure the mechanical integrity and performance of idlers but also uphold safety, efficiency, and compatibility across the vast array of conveyor systems in operation. As such, manufacturers, designers, and operators must prioritize these standards in their practices, contributing to the advancement and reliability of material handling technologies.
Installation, Alignment, and Maintenance of Idler Rollers in Conveyor Idler Roller Design
The successful operation of a conveyor system hinges not just on the quality of its components but also on the precision of installation, alignment, and maintenance practices. In the realm of conveyor idler roller design, meticulous attention to these aspects can significantly enhance the system’s efficiency and longevity. Let’s delve into the best practices for installation and alignment, followed by essential maintenance tips to ensure the enduring performance of idler rollers.
Best Practices for Installation and Alignment
- Accurate Placement: Ensure idler rollers are positioned correctly according to the conveyor design specifications to maintain belt stability and even load distribution.
- Level and Square: Idler frames should be installed level and square to the conveyor frame to prevent belt misalignment and uneven wear.
- Proper Troughing Angle: Adhere to the specified troughing angles for idler sets to optimize material handling and minimize spillage.
- Secure Mounting: Fasten idler rollers securely to prevent any movement that could lead to misalignment or operational disruptions.
- Spacing Consistency: Maintain consistent spacing between idlers as per design requirements to ensure uniform support for the conveyor belt.
- Alignment Checks: Regularly check and adjust the alignment of idler rollers to ensure the belt runs centrally along the conveyor path.
- Transition Zones: Pay special attention to idlers in transition zones to ensure they support the belt effectively as it changes from flat to troughed sections and vice versa.
- Use of Alignment Tools: Employ specialized tools and instruments for precise alignment, ensuring that all components are correctly oriented relative to each other.
Maintenance Tips for Extending Idler Roller Life
- Regular Inspections: Conduct routine inspections to identify wear, damage, or misalignment early, allowing for timely corrective actions.
- Lubrication Schedule: Adhere to a regular lubrication schedule based on manufacturer recommendations and operational conditions to ensure smooth roller function.
- Immediate Replacement of Faulty Idlers: Replace damaged, seized, or excessively worn idlers promptly to prevent further damage to the conveyor belt and other components.
- Cleaning Protocols: Implement cleaning protocols to remove debris and materials that could accumulate on idlers, leading to imbalance or operational hindrance.
- Bearing Protection: Ensure seals and dust covers are intact to protect bearings from contaminants, extending their operational life.
- Adjustment of Misaligned Idlers: Realign any idlers that have shifted from their proper position to prevent belt-tracking issues.
- Record Keeping: Maintain detailed records of maintenance activities, replacements, and observations to track the performance and issues over time.
- Training for Maintenance Staff: Provide comprehensive training for maintenance personnel on idler inspection, maintenance, and replacement procedures.
- Use of Quality Spare Parts: Utilize high-quality replacement parts that meet or exceed original specifications to ensure compatibility and reliability.
By adhering to these best practices for installation, alignment, and maintenance within the scope of conveyor idler roller design, conveyor operators can significantly enhance the efficiency, safety, and lifespan of their systems. These practices not only contribute to the smooth operation of the conveyor but also result in considerable cost savings by reducing downtime and extending the service life of the components.
Interested in learning more? Share your contact details, and we’ll send you comprehensive information about our conveyor idler rollers.
Innovations and Trends in Idler Roller Design in Conveyor Idler Roller Design
The landscape of conveyor idler roller design is undergoing a transformative phase, marked by the introduction of groundbreaking materials, innovative designs, and cutting-edge technologies. These advancements are not merely incremental improvements but are redefining the benchmarks for efficiency, durability, and environmental sustainability in conveyor systems. In this section, we will explore the forefront of these innovations and dissect how they are contributing to the enhanced performance and reliability of conveyor systems.
Exploration of New Materials, Designs, and Technologies
The evolution of conveyor idler roller design is characterized by several key developments:
- Composite Materials: The shift towards lightweight composite materials is revolutionizing idler design, offering unmatched corrosion resistance and noise reduction, which are critical for harsh industrial environments.
- 3D Printing: Leveraging 3D printing for idler components is not just accelerating the prototyping phase but also enabling bespoke solutions tailored to specific operational challenges, pushing the boundaries of customization.
- Smart Idlers: The integration of smart technology into idlers, through sensors and IoT connectivity, is paving the way for predictive maintenance, transforming how conveyor systems are monitored and maintained.
- Energy-Generating Idlers: This innovative concept involves capturing the kinetic energy from idler rotation, which can be used to power onboard sensors, marking a leap towards self-sustaining conveyor components.
- High-Durability Coatings: Advanced surface treatments and coatings are being developed to extend idler life by combating wear and environmental degradation, ensuring idlers can withstand the test of time and operation.
- Sealed-for-Life Bearings: The adoption of sealed bearings in idler design is significantly reducing the need for maintenance, making conveyor systems more reliable and cost-effective.
- Anti-Stick Surfaces: Implementing anti-stick technologies on idler surfaces to prevent material buildup is enhancing belt efficiency and reducing the need for manual cleaning.
- Modular Idler Assemblies: The trend towards modular idler designs is simplifying the installation and replacement process, minimizing downtime and enhancing system flexibility.
- Eco-Friendly Materials: The increasing focus on sustainability is driving the use of recycled and environmentally friendly materials in idler construction, aligning conveyor system design with green initiatives.
Contribution to Improved Conveyor System Performance and Reliability
The impact of these innovations on conveyor system performance and reliability is profound:
- Reduced Maintenance Needs: Innovations like sealed-for-life bearings and durable coatings are minimizing maintenance requirements, directly enhancing system uptime and reliability.
- Enhanced Durability: The use of advanced materials and robust designs is significantly extending the service life of idler rollers, contributing to the long-term durability of conveyor systems.
- Improved Efficiency: The introduction of lightweight and energy-efficient idler designs is reducing operational energy demands, leading to more sustainable and cost-effective conveyor operations.
- Real-Time Monitoring: Smart idler technologies are enabling proactive maintenance strategies, allowing for timely interventions that prevent costly downtime and enhance system reliability.
- Noise Reduction: The adoption of noise-dampening materials and designs is improving the working environment around conveyor systems, addressing one of the key concerns in industrial settings.
- Operational Flexibility: Modular and customizable idler designs are offering unprecedented flexibility, accommodating a wide range of materials and operational scenarios with ease.
- Environmental Sustainability: The shift towards eco-friendly materials in idler construction is reducing the environmental footprint of conveyor systems, aligning with global sustainability goals.
- Material Handling Efficiency: Innovations aimed at minimizing material spillage and belt damage, such as anti-stick surfaces and impact-resistant designs, are ensuring smoother and more efficient conveyor operations.
- Cost Savings: The cumulative benefits of these innovations, from reduced energy consumption to lower maintenance costs, are translating into significant cost savings for conveyor system operators.
The ongoing innovations in conveyor idler roller design are not just technical enhancements but are reshaping the operational, environmental, and economic landscape of conveyor systems. These advancements promise to elevate the efficiency, reliability, and sustainability of material handling operations, setting new standards for the industry.
FAQs about Conveyor Idler Roller Design
Idler roller conveyors are integral components of material handling systems, designed to support the conveyor belt and the material being transported. There are several types of idler roller conveyors, each serving a specific purpose within the conveyor system:
Troughing Idlers: These are the most common types used in conveyor systems. Troughing idlers typically consist of three rollers with the outer two set at specific angles to form a trough, supporting the conveyor belt and the material carried. They are primarily used in bulk material handling applications.
Flat Return Idlers: Positioned along the return side of the conveyor belt, flat return idlers support the belt as it loops back to the beginning of the conveyor system. They usually consist of a single flat roller and are essential for maintaining belt integrity and preventing sagging.
Impact Idlers: Installed at loading points where material is dropped onto the conveyor belt, impact idlers are designed to absorb the shock and distribute the force of the falling material. They help in protecting the belt and the structure from damage due to impact.
Self-Aligning Idlers: These idlers are used to correct any misalignment of the conveyor belt. They automatically pivot and guide the belt back to the centerline, preventing it from running off the edges of the conveyor.
Guide Idlers: Positioned on the sides of the conveyor belt, guide idlers provide lateral stability, preventing the belt from wandering off its intended path.
Each type of idler roller conveyor plays a crucial role in the efficiency and longevity of the conveyor system, ensuring smooth operation and minimizing maintenance requirements.
The standard size of an idler roller can vary widely depending on the application, the width of the conveyor belt, and the specific requirements of the material handling system. However, common diameters for idler rollers range from 4 inches (about 100 mm) to 6 inches (about 150 mm). The length of the idler roller is typically determined by the width of the conveyor belt it supports, with standard sizes designed to accommodate belt widths from 18 inches (about 450 mm) to over 96 inches (about 2400 mm).
It’s important to note that while there are standard sizes, idler rollers can be custom-made to fit specific conveyor systems and applications. Manufacturers often provide a range of sizes and configurations to meet the diverse needs of different industries and material handling requirements.
An idler roller works by providing support to the conveyor belt and the material being transported on it. Positioned strategically along the conveyor frame, idler rollers help to distribute the weight of the material evenly, preventing excessive sagging of the belt between supports. This not only ensures smooth and efficient movement of materials but also extends the life of the conveyor belt by reducing wear and tear.
The idler rollers rotate freely on their bearings, allowing the conveyor belt to glide over them with minimal friction. This rotation is crucial for maintaining the speed and efficiency of the conveyor system. In addition to supporting the belt, certain types of idler rollers, such as self-aligning and guide idlers, play a role in maintaining the proper alignment of the conveyor belt, preventing it from drifting off course and potentially causing operational issues or damage to the system.
The diameter of an idler roller is a critical dimension that influences the conveyor system’s capacity, speed, and the overall handling of materials. Common diameters for idler rollers in conveyor systems range from 4 inches (about 100 mm) to 6 inches (about 150 mm), with some heavy-duty applications requiring larger diameters up to 7 inches (about 175 mm) or more.
The choice of idler roller diameter is influenced by several factors, including the type of materials being conveyed, the speed of the conveyor, the width of the conveyor belt, and the spacing between idler rollers. Larger diameters are generally used for heavy-duty applications where they can provide greater support and durability, while smaller diameters are suitable for lighter applications or where space is a constraint.
It’s essential to select the appropriate idler roller diameter for a specific application to ensure optimal performance, efficiency, and longevity of the conveyor system. Manufacturers often offer a range of diameters to accommodate the diverse needs of different conveyor applications.
Last Updated on July 29, 2024 by Jordan Smith
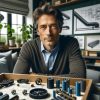
Jordan Smith, a seasoned professional with over 20 years of experience in the conveyor system industry. Jordan’s expertise lies in providing comprehensive solutions for conveyor rollers, belts, and accessories, catering to a wide range of industrial needs. From initial design and configuration to installation and meticulous troubleshooting, Jordan is adept at handling all aspects of conveyor system management. Whether you’re looking to upgrade your production line with efficient conveyor belts, require custom conveyor rollers for specific operations, or need expert advice on selecting the right conveyor accessories for your facility, Jordan is your reliable consultant. For any inquiries or assistance with conveyor system optimization, Jordan is available to share his wealth of knowledge and experience. Feel free to reach out at any time for professional guidance on all matters related to conveyor rollers, belts, and accessories.