Comprehensive Guide to Conveyor Idler Storage Solutions
Conveyor idlers are essential components in belt conveyor systems, serving to support and guide the belt during its operation. These cylindrical rollers are strategically placed to ensure the smooth movement of materials, minimizing wear and tear on the belt and maintaining efficient operation. Proper conveyor idler storage is crucial to maintaining their functionality and extending their lifespan. Storing idlers correctly prevents damage and degradation, which can lead to costly downtime and repairs. Emphasizing the significance of proper storage and maintenance, this guide provides best practices to ensure your conveyor idlers remain in optimal condition, ultimately enhancing operational efficiency and productivity in your conveyor system.
Essential Knowledge for Effective Conveyor Idler Storage
Proper conveyor idler storage is crucial for maintaining the efficiency and longevity of conveyor systems. Understanding the different types of idlers and their specific applications can significantly enhance storage practices. This section provides a comprehensive overview of the various types of idlers used in belt conveyors, detailing their characteristics and typical uses.
Troughing Idler
Troughing idlers are among the most common idlers used in belt conveyor systems. They consist of a set of rollers, typically three, arranged in a trough shape that supports the conveyor belt on the carrying side. This design helps to form a trough shape in the belt, which increases the carrying capacity and helps to keep the material centered on the belt. Troughing idlers are ideal for transporting bulk materials, as they provide excellent support and help prevent spillage.
- Applications: Troughing idlers are typically used in bulk material handling applications such as mining, agriculture, and construction. They are essential for systems that need to transport large volumes of loose materials efficiently.
- Storage Tips: When it comes to conveyor idler storage for troughing idlers, ensure they are stored in a dry environment to prevent rust and corrosion. Properly stack and support the idlers to avoid any deformation of the rollers.
Flat Return Idler
Flat return idlers are used on the return side of the conveyor belt, providing support and keeping the belt in alignment as it returns from the discharge point to the loading point. Unlike troughing idlers, flat return idlers consist of a single roller that supports the belt flat. This design helps maintain belt tension and prevents sagging.
- Applications: Flat return idlers are commonly used in systems where maintaining belt tension and alignment on the return side is crucial. They are often found in various industries, including manufacturing, mining, and material processing.
- Storage Tips: For conveyor idler storage of flat return idlers, it is important to store them horizontally to prevent the rollers from bending. Ensure they are kept in a clean, dry area to avoid contamination and rust.
Impact Idler
Impact idlers are designed to absorb the impact of heavy, falling materials at loading points, thereby protecting the conveyor belt from damage. These idlers feature rollers with rubber discs or a cushioned surface to absorb shock and reduce wear and tear on the belt.
- Applications: Impact idlers are typically used at loading points where the belt is subjected to heavy impacts from falling materials. They are essential in industries like mining, quarrying, and bulk material handling where the belt is exposed to significant impact forces.
- Storage Tips: Proper conveyor idler storage for impact idlers involves keeping them in an environment where they are not exposed to extreme temperatures or direct sunlight, as this can degrade the rubber components. Store them on a flat surface to prevent deformation.
Self-aligning Idlers
Self-aligning idlers are designed to correct any misalignment of the conveyor belt. These idlers automatically adjust and pivot to guide the belt back into proper alignment, preventing issues such as belt tracking and reducing wear on the edges of the belt.
- Applications: Self-aligning idlers are used in conveyor systems where maintaining belt alignment is critical. They are particularly useful in long conveyor runs and in industries where belt misalignment can lead to significant operational issues.
- Storage Tips: For effective conveyor idler storage of self-aligning idlers, ensure they are stored in a way that allows for easy access and inspection. Keep them in a dry, clean environment to prevent any buildup of dust or debris that could affect their alignment mechanisms.
Best Practices for Conveyor Idler Storage
Understanding the types of conveyor idlers and their applications is only part of the equation. Proper conveyor idler storage practices are essential to ensure these components remain in optimal condition and ready for use when needed. Here are some general tips for storing various types of conveyor idlers:
- Indoor Storage: Whenever possible, store idlers indoors in a controlled environment. This helps prevent exposure to moisture, dust, and temperature extremes that can cause rust, corrosion, or degradation of rubber components.
- Outdoor Storage: If indoor storage is not an option, take precautions to protect idlers stored outdoors. Cover them with tarps or other protective coverings to shield them from the elements. Elevate idlers off the ground to prevent water accumulation and ensure proper air circulation.
- Regular Inspections: Conduct regular inspections of stored idlers to check for signs of damage, rust, or other issues. Address any problems immediately to prevent further deterioration.
- Proper Stacking and Support: When stacking idlers, ensure they are properly supported to prevent bending or deformation. Use racks, shelves, or pallets designed to handle the weight and shape of the idlers.
- Labeling and Organization: Clearly label stored idlers with relevant information such as type, size, and intended application. This helps with organization and ensures that the correct idlers are easily accessible when needed.
By following these best practices for conveyor idler storage, you can maintain the quality and functionality of your idlers, reducing the risk of downtime and extending the lifespan of your conveyor system components.
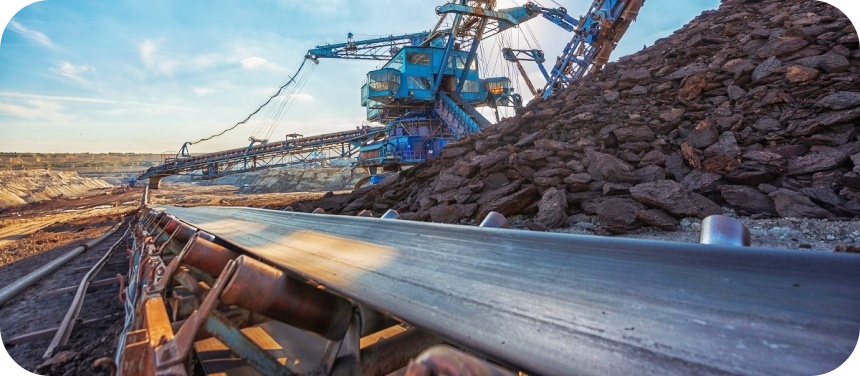
Ensuring Optimal Conveyor Idler Storage
Understanding the dimensions of conveyor idler frames and rollers is essential for effective conveyor idler storage. Proper knowledge of these dimensions ensures that idlers are stored correctly, preventing damage and facilitating easy access and setup when needed. This section delves into the standard dimensions of conveyor idler frames and rollers, provides a comprehensive overview of conveyor roller size charts, and emphasizes the importance of knowing these dimensions for proper storage and setup.
Standard Conveyor Idler Frame Dimensions
Conveyor idler frames are the structures that support and house the rollers, providing stability and alignment for the conveyor belt. Standard dimensions of idler frames vary depending on the type and application of the conveyor system. These dimensions are crucial for ensuring compatibility with the conveyor belt and the specific operational requirements.
- Width: The width of the idler frame is determined by the width of the conveyor belt it supports. Standard widths include 18 inches, 24 inches, 36 inches, 48 inches, and 60 inches. This dimension ensures that the belt is properly supported and guided along its path.
- Height: The height of the idler frame affects the belt’s alignment and tension. Common heights are 6 inches, 8 inches, and 10 inches. Proper height ensures that the belt maintains the correct tension and alignment, reducing wear and tear.
- Length: The length of the idler frame is typically designed to accommodate multiple rollers. Standard lengths include 24 inches, 36 inches, 48 inches, and 60 inches. This dimension ensures that the idler frame can support the required number of rollers for optimal belt support.
- Material Thickness: The material thickness of the idler frame impacts its durability and load-bearing capacity. Common thicknesses are 3/16 inch, 1/4 inch, and 3/8 inch. Thicker materials provide greater strength and longevity, especially in heavy-duty applications.
- Mounting Holes: The placement and size of mounting holes on the idler frame are essential for secure installation. Standard hole sizes include 1/2 inch, 5/8 inch, and 3/4 inch. Properly positioned mounting holes ensure easy and secure attachment to the conveyor structure.
Overview of Conveyor Roller Size Chart
Conveyor rollers come in various sizes and specifications to suit different applications. A conveyor roller size chart helps users understand the different specifications and fittings, ensuring they select the right rollers for their system.
- Roller Diameter: The diameter of conveyor rollers can range from 1.5 inches to 6 inches. Smaller diameters are typically used for light-duty applications, while larger diameters are suitable for heavy-duty and bulk material handling.
- Roller Length: The length of conveyor rollers can vary from 12 inches to 72 inches. The length is chosen based on the width of the conveyor belt and the type of materials being transported.
- Shaft Diameter: The shaft diameter is a critical dimension that affects the roller’s load-bearing capacity and rotational stability. Common shaft diameters include 0.75 inches, 1 inch, and 1.25 inches.
- Bearing Type: Conveyor rollers can be equipped with different types of bearings, such as ball bearings, roller bearings, and plain bearings. The choice of bearing type affects the roller’s load capacity, rotational speed, and maintenance requirements.
- Roller Material: The material of the conveyor roller impacts its durability and suitability for specific applications. Common materials include steel, stainless steel, and rubber-coated steel. Each material offers different benefits in terms of wear resistance, corrosion resistance, and impact absorption.
Importance of Knowing Dimensions for Proper Storage and Setup
Understanding the dimensions of conveyor idler frames and rollers is crucial for proper conveyor idler storage and setup. Proper storage practices ensure that idlers remain in good condition, ready for installation and operation when needed.
- Preventing Damage: Proper knowledge of idler dimensions helps in selecting appropriate storage methods that prevent damage. For example, storing rollers horizontally on racks that match their length and diameter prevents bending and deformation.
- Space Optimization: Knowing the dimensions of idlers allows for efficient use of storage space. Properly sized storage racks and shelves can be designed to accommodate specific idler sizes, maximizing storage capacity and organization.
- Easy Identification: Clearly labeling stored idlers with their dimensions and specifications ensures that the right components are easily identified and accessed when needed. This reduces downtime and improves efficiency during maintenance and installation.
- Compatibility Check: Understanding idler dimensions ensures compatibility with the conveyor system. Before installation, verifying that the stored idlers match the required dimensions prevents installation errors and operational issues.
- Safety Considerations: Proper storage practices based on idler dimensions enhance safety by preventing the risk of accidents caused by improperly stored components. For example, heavy rollers should be stored on low racks to prevent injury from lifting and handling.
Proper conveyor idler storage is essential for maintaining the efficiency and longevity of conveyor systems. By understanding the standard dimensions of conveyor idler frames and rollers, and utilizing size charts to select the appropriate components, businesses can ensure that their idlers are stored correctly and ready for use. This not only prevents damage and extends the lifespan of the idlers but also enhances operational efficiency and safety.
Best Practices for Conveyor Idler Storage
Proper conveyor idler storage is essential to maintain their functionality and longevity. Whether stored indoors or outdoors, following best practices ensures that idlers remain in optimal condition, ready for use when needed. This section outlines the proper methods for storing various types of idlers, providing detailed indoor storage recommendations and outdoor storage precautions.
Proper Methods for Storing Various Types of Idlers
Storing conveyor idlers correctly involves considering factors such as the type of idler, environmental conditions, and handling practices. The goal is to prevent damage, degradation, and ensure easy access and identification.
- Organized Layout: Arrange idlers in an organized manner, grouping them by type and size. This facilitates easy access and prevents the risk of damage due to improper stacking or handling.
- Labeling and Documentation: Clearly label stored idlers with relevant information, such as type, dimensions, and intended use. Maintain a storage inventory to track the condition and location of each idler, making it easier to manage and retrieve them when needed.
- Protective Coverings: Use protective coverings like tarps or shrink wrap to shield idlers from dust, moisture, and contaminants. This is especially important for idlers with rubber components that can degrade over time when exposed to harsh environmental conditions.
- Proper Support: Store idlers on racks or pallets that provide adequate support and prevent deformation. Avoid stacking idlers directly on the ground, as this can lead to damage and make them difficult to handle.
- Regular Inspections: Conduct regular inspections of stored idlers to check for signs of damage, corrosion, or other issues. Address any problems immediately to prevent further deterioration and ensure the idlers are in good condition when needed.
Indoor Storage Recommendations
Indoor storage is the preferred method for conveyor idler storage, as it provides a controlled environment that protects idlers from the elements.
- Temperature Control: Maintain a stable temperature in the storage area to prevent thermal expansion and contraction, which can cause stress and damage to idlers. Ideal storage temperatures range from 50°F to 70°F (10°C to 21°C).
- Humidity Control: Keep humidity levels low to prevent rust and corrosion, especially on metal components. Use dehumidifiers or climate control systems to maintain humidity levels below 50%.
- Clean Environment: Ensure the storage area is clean and free from dust, dirt, and other contaminants. Regularly clean the storage space and use air filtration systems to minimize airborne particles that can settle on idlers.
- Ventilation: Provide adequate ventilation to prevent the buildup of moisture and ensure good air circulation. This helps to keep the storage area dry and reduces the risk of mold and mildew growth.
- Lighting and Accessibility: Ensure the storage area is well-lit and easily accessible. Good lighting and clear pathways make it easier to identify and retrieve stored idlers, reducing the risk of accidents and damage during handling.
Outdoor Storage Precautions
While indoor storage is ideal, outdoor storage may be necessary in some situations. When storing idlers outdoors, take the following precautions to minimize degradation and protect the idlers from environmental damage:
- Elevated Storage: Store idlers on raised platforms or pallets to keep them off the ground. This prevents direct contact with soil and water, reducing the risk of corrosion and contamination.
- Weather Protection: Use weather-resistant coverings such as tarps, plastic sheeting, or custom-made covers to shield idlers from rain, snow, and UV radiation. Ensure the coverings are securely fastened to prevent them from being blown away by wind.
- Drainage: Ensure the outdoor storage area has proper drainage to prevent water accumulation around the stored idlers. Avoid low-lying areas where water can pool and cause rust and corrosion.
- Regular Maintenance: Conduct regular maintenance checks to inspect the condition of the coverings and the idlers themselves. Look for signs of wear, rust, and other damage, and take corrective action as needed.
- Security Measures: Implement security measures such as fencing, locks, and surveillance cameras to protect stored idlers from theft and vandalism. Outdoor storage areas can be more vulnerable to security risks, so it’s important to take precautions.
Proper conveyor idler storage is critical to maintaining the functionality and longevity of these essential components. By following best practices for both indoor and outdoor storage, you can protect idlers from damage, ensure they remain in optimal condition, and enhance the efficiency of your conveyor system. Whether you’re storing troughing idlers, flat return idlers, impact idlers, or self-aligning idlers, these guidelines will help you maintain their quality and readiness for use, ultimately contributing to the overall success of your operations.
Ideas for Efficient Conveyor Idler Storage
Efficient conveyor idler storage is crucial for maintaining operational efficiency and ensuring that idlers are readily available and in good condition when needed. By implementing creative and scalable storage solutions, businesses can optimize their storage space and improve their overall workflow. This section explores various storage options, including racks and shelving, and provides insights into scalable solutions for different business sizes.
Creative and Efficient Storage Solutions for Used Conveyor Idlers
Storing used conveyor idlers requires innovative solutions to maximize space utilization and maintain the integrity of the idlers. Here are some creative and efficient storage solutions:
- Vertical Racking Systems: Vertical racking systems are an excellent solution for storing conveyor idlers in limited space. By storing idlers vertically, businesses can make better use of their available height, freeing up floor space for other uses. These racks are designed to support the weight of the idlers and can be adjusted to accommodate different sizes.
- Modular Shelving Units: Modular shelving units offer flexibility and scalability for conveyor idler storage. These units can be customized to fit the specific dimensions of the idlers and can be easily reconfigured as storage needs change. Modular shelving is particularly useful for businesses with varying inventory levels, as it allows for easy expansion or contraction of storage space.
- Pallet Racking: Pallet racking systems are ideal for storing large quantities of conveyor idlers. By placing idlers on pallets, businesses can use forklifts or pallet jacks to move and organize the idlers efficiently. This method is particularly beneficial for warehouses and distribution centers where quick access to idlers is essential.
- Cantilever Racks: Cantilever racks are designed to store long, bulky items such as conveyor idlers. These racks have arms that extend from a central column, providing support without obstructing access. Cantilever racks are perfect for storing idlers of various lengths and diameters, making it easy to organize and retrieve them as needed.
- Mobile Storage Units: Mobile storage units, such as rolling racks or carts, offer flexibility and mobility for conveyor idler storage. These units can be easily moved around the facility, allowing workers to transport idlers to different areas as needed. Mobile storage units are particularly useful in dynamic environments where storage needs frequently change.
Scalable Storage Solutions for Different Business Sizes
The size and scale of a business significantly impact its storage needs. Implementing scalable storage solutions ensures that businesses of all sizes can efficiently store their conveyor idlers. Here are some considerations for different business sizes:
- Small Businesses: Small businesses with limited space can benefit from compact and flexible storage solutions. Vertical racking systems and modular shelving units are ideal for maximizing vertical space and adapting to changing storage needs. Additionally, mobile storage units can provide flexibility and ease of access in smaller facilities.
- Medium-Sized Businesses: Medium-sized businesses often require a combination of storage solutions to accommodate their growing inventory. Pallet racking systems and cantilever racks offer the necessary capacity and organization for larger quantities of idlers. Modular shelving units can be used to store smaller quantities or specialty idlers, providing a versatile and scalable storage solution.
- Large Enterprises: Large enterprises with extensive storage needs can benefit from high-capacity storage systems such as pallet racking and cantilever racks. These systems provide the necessary support for heavy loads and large volumes of idlers. Automated storage and retrieval systems (AS/RS) can further enhance efficiency by streamlining the process of storing and retrieving idlers, reducing labor costs and improving accuracy.
- Scalability Considerations: When selecting storage solutions, it’s important to consider scalability. Businesses should choose storage systems that can be easily expanded or reconfigured as their needs grow. Modular shelving units and vertical racking systems offer excellent scalability, allowing businesses to add more units or adjust configurations as their inventory increases.
- Customization and Flexibility: Customizable storage solutions provide the flexibility needed to accommodate different types and sizes of conveyor idlers. By investing in adjustable racks and shelves, businesses can ensure that their storage systems can adapt to various idler dimensions and specifications. This flexibility is crucial for maintaining an organized and efficient storage area.
Implementing efficient conveyor idler storage solutions is essential for maintaining operational efficiency and ensuring the longevity of stored idlers. By utilizing creative storage options such as vertical racking systems, modular shelving units, pallet racking, cantilever racks, and mobile storage units, businesses can optimize their storage space and improve accessibility. Additionally, scalable storage solutions allow businesses of all sizes to adapt their storage systems to meet changing needs, ensuring that idlers are stored safely and efficiently. Investing in flexible and customizable storage solutions not only enhances the organization of conveyor idlers but also contributes to the overall success of the business.
Fill Out the Inquiry Form for Conveyor Belt Availability and Pricing.
FAQs About Conveyor Idler Storage
Proper storage of conveyor belts is crucial to maintain their quality and ensure optimal performance when they are eventually put into use. To store conveyor belts correctly, follow these guidelines:
Clean Before Storage: Ensure the conveyor belt is clean and free of any residues or materials that could cause damage or degrade the belt material over time.
Dry Environment: Store the conveyor belts in a cool, dry environment away from direct sunlight, heat sources, and moisture. Excessive heat and humidity can cause the belts to warp, crack, or deteriorate.
Flat or Vertical Position: Conveyor belts should be stored in a flat, horizontal position or rolled and placed on a pallet. If rolled, the belt should be stored vertically on its edge, not laid flat. This prevents the belt from developing flat spots and helps maintain its shape.
Avoid Heavy Loads: Do not place heavy objects on top of the conveyor belts during storage, as this can cause deformation or damage.
Regular Inspections: Periodically inspect the stored conveyor belts for any signs of damage, such as cracks, fraying, or warping. Address any issues promptly to prevent further degradation.
By adhering to these storage practices, you can extend the lifespan of your conveyor belts and ensure they remain in good working condition when needed.
An idler in a conveyor system is a crucial component that supports the conveyor belt and the load being transported. Idlers are typically composed of rollers that are mounted on a frame and positioned at intervals along the length of the conveyor. They serve several important functions:
Support the Belt: Idlers provide support to the conveyor belt, ensuring it remains aligned and moves smoothly along the conveyor structure.
Reduce Friction: By reducing friction between the conveyor belt and the rollers, idlers help to minimize wear and tear on the belt, thereby extending its lifespan.
Guide the Belt: Idlers help guide the conveyor belt, keeping it centered and preventing it from drifting off track, which can cause operational issues and potential damage.
Distribute Load: Idlers distribute the load evenly across the width of the conveyor belt, preventing excessive stress on specific areas and ensuring efficient material handling.
There are different types of idlers, including troughing idlers, flat return idlers, impact idlers, and self-aligning idlers, each designed for specific applications and load requirements. Proper maintenance and alignment of idlers are essential to ensure the efficient and reliable operation of a conveyor system.
The distance between carrying idlers, also known as idler spacing, varies depending on several factors, including the type of material being transported, the load weight, the belt width, and the conveyor design. Generally, carrying idlers are spaced at regular intervals along the length of the conveyor to provide adequate support and ensure smooth operation. Here are some typical guidelines for idler spacing:
Light Loads: For light loads, carrying idlers may be spaced closer together, typically around 3 to 4 feet apart. This helps to ensure that the belt remains properly supported and minimizes sagging.
Medium Loads: For medium loads, the spacing between carrying idlers is often increased to around 4 to 6 feet. This spacing provides a balance between adequate support and cost-efficiency.
Heavy Loads: For heavy loads, carrying idlers may be spaced further apart, typically around 5 to 7 feet. This allows the conveyor system to handle higher weights without compromising the belt’s integrity.
Special Applications: In certain applications, such as high-speed conveyors or those with steep inclines, the spacing between carrying idlers may be adjusted to accommodate specific operational requirements.
It is important to refer to the conveyor manufacturer’s guidelines and specifications to determine the appropriate idler spacing for your specific conveyor system. Proper idler spacing ensures that the conveyor belt is adequately supported, reducing the risk of belt damage and improving overall system performance.
Idlers play a vital role in the operation and efficiency of a conveyor system. Their primary functions include:
Supporting the Conveyor Belt: Idlers support the conveyor belt, ensuring it remains level and stable as it moves along the conveyor structure. This helps prevent sagging and maintains the belt’s proper alignment.
Reducing Friction: By providing a rolling surface for the conveyor belt, idlers reduce friction between the belt and the conveyor frame. This minimizes wear and tear on the belt and extends its lifespan.
Guiding the Belt: Idlers help guide the conveyor belt and keep it centered on the conveyor structure. This prevents belt misalignment, which can cause operational issues and potential damage to the system.
Distributing the Load: Idlers distribute the weight of the material being transported evenly across the width of the conveyor belt. This helps to prevent excessive stress on specific areas of the belt, ensuring efficient material handling.
Absorbing Impact: Impact idlers, specifically designed for loading zones, absorb the impact of material being loaded onto the conveyor belt. This protects the belt from damage and reduces the risk of spillage.
Different types of idlers are used in various sections of a conveyor system, including troughing idlers for load-bearing sections, return idlers for the return run, and self-aligning idlers for correcting belt misalignment. Proper maintenance and alignment of idlers are essential to ensure the efficient and reliable operation of a conveyor system.
Last Updated on July 30, 2024 by Jordan Smith
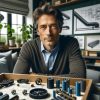
Jordan Smith, a seasoned professional with over 20 years of experience in the conveyor system industry. Jordan’s expertise lies in providing comprehensive solutions for conveyor rollers, belts, and accessories, catering to a wide range of industrial needs. From initial design and configuration to installation and meticulous troubleshooting, Jordan is adept at handling all aspects of conveyor system management. Whether you’re looking to upgrade your production line with efficient conveyor belts, require custom conveyor rollers for specific operations, or need expert advice on selecting the right conveyor accessories for your facility, Jordan is your reliable consultant. For any inquiries or assistance with conveyor system optimization, Jordan is available to share his wealth of knowledge and experience. Feel free to reach out at any time for professional guidance on all matters related to conveyor rollers, belts, and accessories.