Conveyor Idler Structure: A Comprehensive Guide
A conveyor idler structure is a critical component of conveyor systems, designed to support and guide the conveyor belt during material transport. Conveyor idlers are cylindrical rollers positioned along the length of the conveyor to minimize resistance and wear on the belt. The conveyor idler structure plays a pivotal role in maintaining the belt’s alignment and ensuring smooth, efficient operation. By providing consistent support, the idler structure helps to prevent belt sagging and reduces the risk of material spillage, thereby enhancing the overall performance and longevity of the conveyor system.
Components of Conveyor Idler Structure
The conveyor idler structure is composed of several critical components that work together to support and guide the conveyor belt, ensuring efficient material transport. Understanding these components is essential for designing and maintaining effective conveyor systems. The main components of the conveyor idler structure include the idler frame, rollers, bearings, and frame dimensions. Each plays a vital role in the functionality and reliability of the conveyor system.
Idler Frame
The idler frame is the foundational component of the conveyor idler structure. It serves as the support framework that holds the rollers in place and ensures they are properly aligned. The idler frame must be robust and durable, capable of withstanding the continuous operational stresses and environmental conditions. It is typically made from high-quality steel or other strong materials to provide the necessary strength and rigidity.
The primary function of the idler frame is to maintain the proper spacing and positioning of the rollers. This alignment is crucial for the smooth movement of the conveyor belt, minimizing the risk of misalignment, belt wear, and potential system failures. Additionally, the frame must be designed to facilitate easy maintenance and replacement of rollers and bearings, contributing to the overall efficiency and longevity of the conveyor system.
Rollers
Rollers are cylindrical components mounted on the idler frame, and they are the primary elements that directly interact with the conveyor belt. Rollers in the conveyor idler structure are responsible for supporting the belt and the materials being transported, reducing friction and ensuring smooth motion. Rollers are typically made from materials such as steel, rubber, or other composites, chosen based on the specific application requirements.
There are various types of rollers used in conveyor idler structures, including carrying rollers, return rollers, impact rollers, and training rollers. Carrying rollers support the loaded side of the belt, return rollers support the empty side, impact rollers absorb the impact of falling materials at loading points, and training rollers help to keep the belt aligned. Each type of roller plays a specific role in enhancing the performance and reliability of the conveyor system.
Bearings
Bearings are critical components within the rollers of the conveyor idler structure. They facilitate the smooth rotation of the rollers, reducing friction and wear. Bearings must be selected based on their load-carrying capacity, durability, and ability to operate under varying environmental conditions, such as temperature fluctuations and exposure to dust and moisture.
There are several types of bearings used in conveyor idlers, including ball bearings, roller bearings, and plain bearings. Ball bearings are commonly used due to their ability to handle both radial and axial loads efficiently. Roller bearings are suitable for heavy-duty applications, offering high load-carrying capacity and durability. Plain bearings are used in specific applications where simplicity and cost-effectiveness are prioritized. The choice of bearing type directly impacts the performance and maintenance requirements of the conveyor idler structure.
Frame Dimensions
The dimensions of the idler frame are crucial for the optimal performance of the conveyor system. The frame dimensions must be carefully chosen to ensure proper support and alignment of the rollers and the conveyor belt. Key dimensions include the width, height, and length of the frame, as well as the spacing between the rollers.
Selecting the right frame dimensions involves considering factors such as the belt width, the load capacity, the type of materials being transported, and the specific application requirements. A well-designed frame with appropriate dimensions ensures that the conveyor belt is adequately supported, reducing the risk of sagging and misalignment. This, in turn, enhances the overall efficiency and reliability of the conveyor system.
Importance of Choosing the Right Frame Dimensions
Choosing the correct frame dimensions for the conveyor idler structure is critical for several reasons. Firstly, proper frame dimensions ensure that the conveyor belt remains correctly aligned, preventing issues such as belt drift and uneven wear. This alignment is essential for maintaining the efficient operation of the conveyor system and avoiding costly downtime and repairs.
Secondly, the right frame dimensions contribute to the structural integrity of the conveyor system. An adequately sized frame provides the necessary support for the rollers and bearings, preventing excessive stress and potential failures. This structural integrity is particularly important in heavy-duty applications where the conveyor system must handle significant loads and harsh operating conditions.
Lastly, selecting the appropriate frame dimensions enhances the overall safety of the conveyor system. A well-designed idler frame minimizes the risk of mechanical failures, reducing the likelihood of accidents and injuries. By ensuring that the conveyor belt operates smoothly and efficiently, the right frame dimensions also contribute to the safe and reliable transport of materials.
The components of the conveyor idler structure, including the idler frame, rollers, bearings, and frame dimensions, play a critical role in the functionality and reliability of conveyor systems. Each component must be carefully selected and designed to ensure optimal performance, efficiency, and safety. Understanding the importance of these components and their interactions is essential for maintaining and improving conveyor system operations.
Conveyor Idler Structure: Types of Idlers
Understanding the different types of idlers within the conveyor idler structure is essential for optimizing the performance and efficiency of conveyor systems. Idlers can be classified based on their design, function, and application, each serving specific roles to ensure smooth and reliable operation of the conveyor belt. This section provides a detailed overview of the main types of idlers, including carrying idlers and return idlers, and compares their suitability for various conveyor systems.
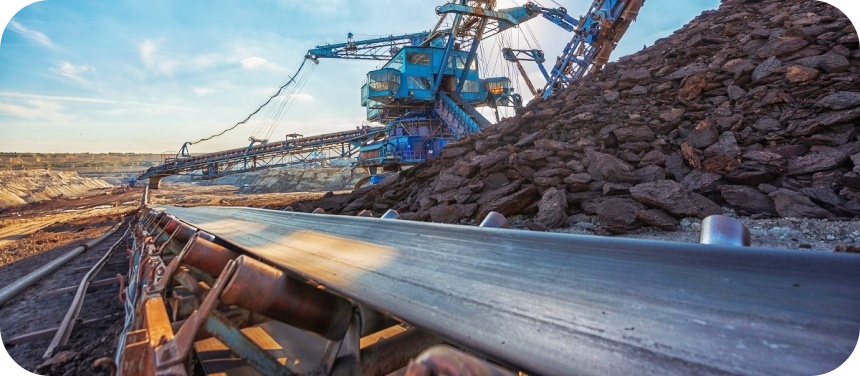
Classification of Idlers
Idlers are classified into several categories based on their design and function within the conveyor idler structure. The primary types include carrying idlers, return idlers, impact idlers, training idlers, and transition idlers. Each type is designed to address specific challenges and requirements in material transport.
- Carrying Idlers: These idlers support the loaded side of the conveyor belt and are essential for maintaining the belt’s alignment and carrying capacity.
- Return Idlers: These idlers support the empty, returning side of the belt, ensuring it remains aligned and tensioned.
- Impact Idlers: Located at loading points, these idlers are designed to absorb the impact of heavy, falling materials to protect the belt and other components.
- Training Idlers: These idlers help correct any misalignment of the belt by guiding it back to its proper path.
- Transition Idlers: Positioned at the transition points of the conveyor system, these idlers help the belt transition from one section to another smoothly.
Carrying Idlers
Carrying idlers are a crucial component of the conveyor idler structure. They are designed to support the loaded side of the conveyor belt, ensuring that the belt remains aligned and that the materials being transported are properly supported. Carrying idlers typically consist of three rollers arranged in a trough shape, which helps to cradle the belt and keep it centered.
Roles and Characteristics
- Support and Alignment: Carrying idlers provide continuous support to the belt, preventing sagging and maintaining proper alignment. This is essential for efficient material transport and minimizing wear on the belt.
- Load Distribution: By cradling the belt, carrying idlers distribute the load evenly across the belt’s width, reducing stress and extending the belt’s lifespan.
- Versatility: Carrying idlers are suitable for a wide range of materials and applications, making them a versatile choice for various conveyor systems.
Return Idlers
Return idlers support the empty side of the conveyor belt as it returns to the loading point. They play a vital role in maintaining the belt’s alignment and tension, ensuring smooth operation of the conveyor system.
Roles and Characteristics
- Belt Support: Return idlers prevent the belt from sagging and maintain proper tension, which is crucial for efficient operation and minimizing wear.
- Alignment Maintenance: By keeping the belt aligned, return idlers help prevent issues such as belt drift and uneven wear, which can lead to costly downtime and repairs.
- Durability: Return idlers are typically made from durable materials to withstand the continuous wear and tear of supporting the returning belt.
Impact Idlers
Impact idlers are specifically designed to absorb the impact of heavy, falling materials at loading points. They are a critical component of the conveyor idler structure, protecting the belt and other components from damage.
Roles and Characteristics
- Impact Absorption: Impact idlers have a reinforced design with shock-absorbing properties to handle the high impact forces of falling materials.
- Belt Protection: By absorbing the impact, these idlers protect the belt from punctures and other damage, extending its lifespan and reducing maintenance costs.
- Enhanced Durability: Impact idlers are constructed from high-strength materials to withstand harsh operating conditions and heavy loads.
Training Idlers
Training idlers are designed to help maintain the proper alignment of the conveyor belt. They are essential for correcting any misalignment that may occur during operation, ensuring the belt remains on its intended path.
Roles and Characteristics
- Alignment Correction: Training idlers adjust the belt’s path, guiding it back to its proper alignment and preventing issues such as belt drift and uneven wear.
- Improved Efficiency: By maintaining proper alignment, training idlers enhance the overall efficiency of the conveyor system and reduce the risk of downtime due to belt misalignment.
- Adaptability: Training idlers are adaptable to various conveyor systems and can be adjusted to suit specific operational needs.
Transition Idlers
Transition idlers are positioned at the transition points of the conveyor system, where the belt changes from one section to another. They help ensure a smooth transition, minimizing the risk of belt damage and material spillage.
Roles and Characteristics
- Smooth Transition: Transition idlers support the belt during changes in direction or elevation, ensuring a smooth and seamless transition between sections.
- Belt Protection: By providing continuous support, these idlers protect the belt from damage caused by abrupt changes in direction or elevation.
- Versatility: Transition idlers can be used in various conveyor systems, accommodating different belt widths and load capacities.
Comparison of Different Types of Idlers
Choosing the right type of idler for a conveyor system depends on various factors including the nature of the material being transported, the conveyor’s operational environment, and specific application requirements. Below is a comparison table highlighting the key attributes of different types of idlers:
By understanding the various types of idlers and their specific roles within the conveyor idler structure, businesses can optimize their conveyor systems for better performance, efficiency, and longevity. Proper selection and maintenance of idlers are key to minimizing downtime and ensuring smooth operations.
Specifications of Conveyor Idler Structure
Understanding the specifications of the components within the conveyor idler structure is crucial for designing and maintaining efficient conveyor systems. These specifications include key parameters such as roller diameter, roller length, and bearing type. Matching these specifications to the conveyor system requirements ensures optimal performance, longevity, and reduced maintenance costs. This section provides an in-depth look at common conveyor idler specifications, their importance, and their impact on conveyor efficiency and maintenance.
Overview of Common Specifications
The specifications of the conveyor idler structure encompass various dimensions and characteristics that define the performance and suitability of idlers for specific applications. The primary specifications to consider include roller diameter, roller length, and bearing type.
Roller Diameter
The roller diameter is a critical specification in the conveyor idler structure. It determines the amount of surface area in contact with the conveyor belt and impacts the roller’s ability to support the load. Common roller diameters range from 50 mm to 200 mm, with larger diameters used for heavier loads and longer conveyor systems.
- Smaller Diameters: Suitable for light to medium loads and shorter conveyor systems. They offer lower rotational inertia, which can lead to reduced energy consumption.
- Larger Diameters: Ideal for heavy loads and longer conveyor systems. They provide greater load-bearing capacity and durability, reducing the frequency of maintenance and replacements.
Roller Length
Roller length is another vital specification that affects the conveyor idler structure. It is determined by the width of the conveyor belt and the load distribution requirements. Roller lengths typically correspond to standard belt widths, such as 600 mm, 800 mm, 1000 mm, and wider.
- Standard Lengths: Matched to common belt widths, ensuring uniform support across the belt’s surface.
- Custom Lengths: Designed for specific applications where unique belt widths or load distributions are required. Custom lengths ensure optimal performance and prevent belt sagging or misalignment.
Bearing Type
The type of bearing used in the rollers of the conveyor idler structure significantly impacts the performance, efficiency, and maintenance requirements. Bearings facilitate the smooth rotation of rollers, reducing friction and wear. Common bearing types include ball bearings, roller bearings, and plain bearings.
- Ball Bearings: Widely used due to their ability to handle both radial and axial loads efficiently. They offer smooth operation and are suitable for most standard applications.
- Roller Bearings: Provide high load-carrying capacity and durability, making them ideal for heavy-duty applications. They can handle larger loads and are more resistant to shock and impact.
- Plain Bearings: Used in specific applications where simplicity and cost-effectiveness are prioritized. They are less common in heavy-duty conveyor systems due to their limited load-carrying capacity and higher friction.
Importance of Matching Idler Specifications to Conveyor System Requirements
Selecting the appropriate specifications for the conveyor idler structure is essential for ensuring that the conveyor system operates efficiently and reliably. Matching idler specifications to the specific requirements of the conveyor system involves considering factors such as load capacity, belt speed, environmental conditions, and the type of materials being transported.
- Load Capacity: The idler specifications must be capable of supporting the maximum load of the conveyor system. This includes selecting the right roller diameter and bearing type to handle the expected weight and distribution of the materials.
- Belt Speed: Higher belt speeds require idlers with specifications that can minimize friction and heat generation. This often involves choosing bearings with lower friction coefficients and rollers with suitable diameters to reduce rotational resistance.
- Environmental Conditions: Conveyor systems operating in harsh environments, such as extreme temperatures, high humidity, or dusty conditions, require idler specifications that can withstand these challenges. This includes selecting materials and bearings that offer corrosion resistance and durability.
- Material Type: The characteristics of the transported materials, such as size, weight, and abrasiveness, influence the choice of idler specifications. Heavy, abrasive materials may necessitate larger roller diameters and more robust bearings.
Impact of Idler Specifications on Conveyor Efficiency and Maintenance
The specifications of the conveyor idler structure have a direct impact on the efficiency and maintenance requirements of the conveyor system. Properly selected idler specifications can enhance the overall performance of the conveyor, reduce energy consumption, and minimize downtime and maintenance costs.
Conveyor Efficiency
- Reduced Friction: Selecting the right bearing type and roller diameter can significantly reduce friction between the rollers and the conveyor belt. Lower friction results in smoother operation and reduced energy consumption.
- Optimized Load Distribution: Matching the roller length to the belt width ensures uniform load distribution, preventing belt sagging and misalignment. This contributes to smoother material transport and reduced wear on the belt and idlers.
- Improved Alignment: Correctly specified idlers maintain proper belt alignment, reducing the risk of belt drift and uneven wear. This ensures consistent performance and reduces the likelihood of operational interruptions.
Maintenance Requirements
- Durability: Idlers with appropriate specifications, such as larger diameters and robust bearings, are more durable and resistant to wear and tear. This reduces the frequency of maintenance and replacements, lowering overall maintenance costs.
- Ease of Maintenance: Idler frames designed for easy access and replacement of rollers and bearings facilitate quicker maintenance procedures. This minimizes downtime and ensures that the conveyor system can return to operation promptly.
- Longer Lifespan: Properly matched idler specifications contribute to the longevity of both the idlers and the conveyor belt. By reducing wear and stress on these components, the overall lifespan of the conveyor system is extended.
Understanding and selecting the right specifications for the conveyor idler structure is crucial for optimizing the performance, efficiency, and maintenance of conveyor systems. Key specifications such as roller diameter, roller length, and bearing type must be carefully matched to the specific requirements of the conveyor application. By doing so, operators can ensure smooth and reliable material transport, reduce energy consumption, and minimize maintenance costs, ultimately enhancing the overall effectiveness of the conveyor system.
Conveyor Idler Structure: Conveyor Roller Size
Conveyor rollers play a crucial role in the efficiency and performance of conveyor systems. Proper roller size selection is paramount in ensuring smooth operation and minimizing maintenance requirements. This section delves into the importance of roller size in conveyor design and operation, provides a detailed chart illustrating standard conveyor roller sizes and their applications, and offers guidelines for selecting the right roller size based on conveyor requirements.
Importance of Roller Size in Conveyor Design and Operation
The size of conveyor rollers directly impacts the overall functionality and efficiency of a conveyor system. Here are seven key reasons why roller size is crucial:
- Load Capacity: Larger rollers can typically handle heavier loads, which is essential in industries requiring the transportation of bulky or heavy materials.
- Conveyor Speed: Roller size influences conveyor speed. Smaller rollers allow for higher speeds, while larger rollers are better suited for slower conveyors.
- Durability: Properly sized rollers are more durable and have a longer service life, reducing downtime and maintenance costs.
- Material Compatibility: Different materials and surface finishes are available for rollers, with size playing a role in selecting the most suitable material for the application.
- Energy Efficiency: Roller size impacts the amount of energy required to operate the conveyor system, with larger rollers generally requiring less energy.
- Noise and Vibration: Roller size can affect the noise and vibration levels of the conveyor, with larger rollers often producing less noise and vibration.
- Alignment and Tracking: Properly sized rollers contribute to better conveyor belt alignment and tracking, reducing the risk of belt damage and misalignment issues.
Guidelines for Selecting the Right Roller Size Based on Conveyor Requirements
When selecting the right roller size for a conveyor system, consider the following guidelines:
- Load Capacity: Determine the maximum load the conveyor will carry and select rollers that can support this load.
- Conveyor Speed: Choose rollers that allow the conveyor to operate at the desired speed without compromising efficiency or safety.
- Material Handling Needs: Consider the size, shape, and weight of the materials being transported, as well as any special requirements such as high temperatures or corrosive environments.
- Environmental Factors: Take into account factors such as temperature, humidity, and exposure to chemicals, as these can affect roller performance and durability.
- Maintenance Requirements: Select rollers that are easy to maintain and replace to minimize downtime and maintenance costs.
By carefully considering these factors and consulting the provided chart, you can select the right roller size to optimize your conveyor system’s performance and longevity.
The size of conveyor rollers is a critical aspect of conveyor design and operation. Proper roller size selection can enhance load capacity, conveyor speed, durability, material compatibility, energy efficiency, and alignment, ultimately leading to a more efficient and reliable conveyor system. Refer to the guidelines and chart provided to select the right roller size for your specific conveyor requirements.
Conveyor Idler Structure: Return Idler Belt Conveyor
Return idlers play a crucial role in supporting the return side of a conveyor belt, ensuring smooth operation and efficient material transport. Understanding their role, types, and the importance of proper alignment and maintenance is essential for maximizing conveyor efficiency and longevity.
Role of Return Idlers
Return idlers are key components of a conveyor idler structure, providing support to the return side of the conveyor belt. They help maintain proper tension in the belt, ensuring it stays aligned and centered on the conveyor frame. Without effective return idlers, the belt can sag, mistrack, or even come off the conveyor, leading to downtime and potential damage to the belt and other conveyor components.
Description of Different Types of Return Idlers
Return idlers come in various types, each designed for specific applications and conveyor configurations. Some common types include:
- Flat Return Idlers: These idlers have a flat surface and are used in applications where the conveyor belt returns on itself. They provide support and help maintain belt alignment.
- V-Return Idlers: Also known as V-return idlers, these idlers have a V-shaped design that helps center the belt on the conveyor. They are ideal for applications where belt tracking is critical.
- Rubber Disc Return Idlers: These idlers feature rubber discs mounted on the roller, providing cushioning and impact resistance. They are often used in applications where the conveyor belt carries heavy or sharp-edged materials.
- Training Return Idlers: These idlers are designed to help train the belt and keep it centered on the conveyor. They are often used in conjunction with other types of return idlers to ensure proper belt alignment.
- Troughing Return Idlers: These idlers have a troughed design that helps guide the belt on its return path. They are commonly used in applications where the conveyor belt carries bulk materials.
Importance of Proper Alignment and Maintenance
Proper alignment and maintenance of return idlers are critical for ensuring conveyor efficiency and prolonging the life of the conveyor system. Misaligned or poorly maintained return idlers can lead to increased wear and tear on the belt, increased energy consumption, and reduced overall efficiency.
Regular inspection and maintenance of return idlers are essential. This includes checking for signs of wear, damage, or misalignment and taking corrective action as needed. Proper alignment can be achieved through the use of alignment devices or by adjusting the idler frame and brackets.
Return idlers are an integral part of conveyor idler structures, providing support and ensuring the smooth operation of the conveyor belt. Understanding the role of return idlers, the different types available, and the importance of proper alignment and maintenance is essential for maximizing conveyor efficiency and longevity.
Conveyor Idler Structure: Carrying Idler Roller
Carrying idler rollers play a crucial role in supporting the loaded side of a conveyor belt in a conveyor idler structure. Their design and construction are pivotal in ensuring smooth and efficient operation of the conveyor system. Selecting the right carrying idler roller is essential for specific conveyor applications to prevent issues such as belt misalignment, excessive wear, and increased power consumption.
Function of Carrying Idlers in Supporting the Loaded Side of the Conveyor Belt
Carrying idler rollers are positioned along the conveyor frame to support the loaded side of the conveyor belt and prevent sagging or excessive sag. They are strategically placed to evenly distribute the load and minimize the stress on the belt. The primary functions of carrying idlers include:
- Supporting the Belt: Carrying idlers provide a stable support surface for the conveyor belt, ensuring it remains flat and evenly tensioned, which is crucial for proper material handling.
- Reducing Belt Sag: By supporting the loaded side of the belt, carrying idlers help reduce sagging, which can lead to spillage and material accumulation.
- Improving Belt Tracking: Properly aligned carrying idlers contribute to better belt tracking, reducing the risk of belt damage and premature wear.
- Minimizing Material Spillage: By maintaining proper belt alignment and tension, carrying idlers help minimize material spillage along the conveyor route.
- Enhancing Conveyor Efficiency: Well-designed carrying idlers reduce the friction between the belt and the idler rollers, improving the overall efficiency of the conveyor system.
- Extending Belt Life: By reducing stress and wear on the belt, carrying idlers help extend the operational life of the conveyor belt, reducing maintenance costs.
Design and Construction of Carrying Idler Rollers
The design and construction of carrying idler rollers are critical aspects that directly impact the performance and longevity of the conveyor system. Key considerations in the design and construction of carrying idler rollers include:
- Roller Diameter: The diameter of the carrying idler roller is crucial in determining the load-carrying capacity of the roller. Larger diameter rollers can support heavier loads and reduce the stress on the belt.
- Roller Material: Carrying idler rollers are typically made from materials such as steel, rubber, or a combination of both. The material selection depends on factors such as the application, load capacity, and environmental conditions.
- Bearing Type: The type of bearings used in carrying idler rollers influences their durability and efficiency. Common bearing types include ball bearings and roller bearings, each offering different levels of load capacity and resistance to contamination.
- Sealing Mechanism: Proper sealing of the bearings is essential to prevent contamination from dust, moisture, and other environmental factors, which can lead to premature failure of the bearings.
- Roller Length and Shaft Diameter: The length of the carrying idler roller and the diameter of its shaft are critical in determining the roller’s strength and load-carrying capacity.
- Roller Configuration: Carrying idler rollers can be configured in various ways, such as flat idlers, trough idlers, and impact idlers, each designed for specific applications and load conditions.
- Roller Spacing: The spacing between carrying idler rollers is crucial in ensuring proper belt support and load distribution. The spacing should be carefully calculated based on the conveyor design and material characteristics.
- Impact Rating: Some carrying idler rollers are designed to withstand impact loads, such as those encountered in loading zones or when handling heavy, abrasive materials.
- Lubrication Requirements: Proper lubrication of carrying idler rollers is essential to reduce friction, prevent overheating, and extend the life of the rollers and bearings.
Importance of Selecting the Right Carrying Idler Roller
Selecting the right carrying idler roller is critical for the efficient and reliable operation of a conveyor system. The importance of selecting the right carrying idler roller for specific conveyor applications includes:
- Optimal Performance: The right carrying idler roller ensures optimal performance of the conveyor system, including smooth operation, minimal downtime, and reduced maintenance costs.
- Extended Equipment Life: Properly selected carrying idler rollers can help extend the life of the conveyor belt, idler rollers, and other components, reducing the need for frequent replacements.
- Improved Safety: Well-designed carrying idler rollers contribute to a safer working environment by reducing the risk of belt misalignment, material spillage, and equipment failure.
- Energy Efficiency: The right carrying idler roller can help reduce power consumption by minimizing friction between the belt and the idler rollers, improving the overall energy efficiency of the conveyor system.
- Cost Savings: Selecting the right carrying idler roller can result in cost savings over the long term, including reduced maintenance costs, fewer replacement parts, and increased productivity.
Carrying idler rollers are essential components of conveyor systems, providing support and stability to the conveyor belt. Their design, construction, and selection are critical in ensuring the smooth and efficient operation of the conveyor system. Properly designed and selected carrying idler rollers can improve conveyor performance, extend equipment life, and reduce maintenance costs, making them crucial elements in any conveyor idler structure.
Fill Out the Form for a Personalized SMA Rotary Joint Quote.
FAQs about Conveyor Idler Structure
Conveyor idlers, essential to the functioning of conveyor systems, are cylindrical rods that support the conveyor belt and the material being conveyed. The main components of a conveyor idler are:
Tubes: These are the shells or cylindrical parts that make contact with the conveyor belt, providing a smooth surface for the belt to roll on.
Shafts: Shafts are long, round bars that connect to the conveyor frame and provide an axis around which the tubes rotate.
Bearings: Bearings sit inside the idler’s housing and allow the tubes to spin freely around the shaft. They’re critical for reducing friction and wear.
Seals: Seals protect the bearings from contaminants such as dust and water, ensuring that the idler can operate smoothly under various conditions.
Rollers: These are typically set at either end of the tube and ride along the conveyor’s rails to allow for a better and more controlled roll under load.
Endcaps: Endcaps are placed at the ends of the tubes to contain the bearings and seals; sometimes, they also help to maintain the structural integrity of the idler.
Lubrication: This isn’t a physical part, but it’s vital to the longevity of the idler, ensuring smooth operation and minimizing wear.
The combined function of these parts is to provide a stable, rotating base for the conveyor belt, ensuring efficient movement of materials.
The structure of a conveyor system is designed to create an efficient method for moving goods and materials along a predefined path. The main structural components include:
Frame: This is the principal structure that supports all the other elements of a conveyor system, typically made of metal or durable materials.
Belt: The conveyor belt is the continuous loop that transports materials; made from various materials depending on the application, such as rubber, PVC, or synthetic fabrics.
Drive System: The system includes motors and gearboxes that provide the motion necessary to move the belt.
Pulleys and Rollers: Pulleys drive the belt and maintain tension, while rollers support the belt and materials being transported.
Take-up Unit: This component ensures proper tensioning of the conveyor belt, enabling consistent movement and preventing slippage.
Electrical Components: Sensors, switches, control panels, and other electronics regulate conveyor speed, detect load weights, and manage the overall operation.
Guardrails: These safety features prevent materials from falling off the belt and also protect workers from moving parts.
Discharge and Feeding Points: Specific areas are designated for loading materials onto the belt (feeding) and offloading them (discharge).
Each of these structural elements plays a vital role in the function of a conveyor system, contributing to the overall efficiency and safety of material handling operations.
Idler frames are supports that keep conveyor idlers in place, maintaining the shape and tension of the conveyor belt. The frames vary according to the application, with each designed for specific load requirements and operational conditions. The different types of idler frames include:
CEMA Frames: Designed in accordance with CEMA standards, these frames accommodate various belt widths and are used in general material handling applications.
Offset Frames: These allow for an idler arrangement that can promote better belt training and material disposal, especially useful in reducing the buildup of materials.
Inline Frames: Commonly used for general purposes, inline frames support idlers directly above the location they are mounted.
Picking and Feeding Frames: Specifically designed for sections of the conveyor where materials are loaded or unloaded, these provide better access for these operations.
Low Profile Frames: Ideal for tight spaces where regular frame sizes do not fit. They’re also used where material needs to be as close to the ground as possible.
Garland and Catenary Frames: Suited for heavy-duty applications, these allow the belt to flex and absorb impacts, especially useful in mining operations.
Knowing the types of idler frames available helps in selecting the right one for the conveyor system in question, based on the needs of the operation.
Idlers play an essential role in the control and support of the conveyor belt. There are several different types, each designed for specific conditions and functions:
Flat/Carrying Idlers: Used to support the weight of the belt and the material being transported, typically mounted at intervals along the conveyor.
Impact Idlers: Constructed with resilient materials, they absorb shocks from heavy loads and are often located at loading and receiving points.
Guide Idlers: Positioned on the sides of the belt, these idlers ensure that the conveyor stays centered and prevents misalignment.
Return Idlers: These idlers support the belt on its journey back to the start after it has dropped off the bulk materials.
Self-aligning Idlers: Engineered to automatically maintain the alignment of the belt, minimizing drift and potential damage.
Spiral Idlers: Their unique design helps to clean the underside of the conveyor belt, further aiding in preventing misalignment due to material build-up.
Suspended/Garland Idlers: Comprising several rolls hanging from a chain, they provide flexible support and are used on heavy-duty conveyors with large lump materials.
Selecting the proper type of idler is crucial for optimizing the performance and longevity of a conveyor belt system, ensuring smooth operations and minimal maintenance needs.
Last Updated on July 30, 2024 by Jordan Smith
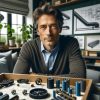
Jordan Smith, a seasoned professional with over 20 years of experience in the conveyor system industry. Jordan’s expertise lies in providing comprehensive solutions for conveyor rollers, belts, and accessories, catering to a wide range of industrial needs. From initial design and configuration to installation and meticulous troubleshooting, Jordan is adept at handling all aspects of conveyor system management. Whether you’re looking to upgrade your production line with efficient conveyor belts, require custom conveyor rollers for specific operations, or need expert advice on selecting the right conveyor accessories for your facility, Jordan is your reliable consultant. For any inquiries or assistance with conveyor system optimization, Jordan is available to share his wealth of knowledge and experience. Feel free to reach out at any time for professional guidance on all matters related to conveyor rollers, belts, and accessories.