Choosing the Best Conveyor Impact Bed for Your System
A conveyor impact bed is a crucial component in conveyor systems, designed to absorb the shock and impact of falling materials at transfer points. By cushioning the load, the conveyor impact bed protects the conveyor belt from damage and reduces maintenance costs. These beds are especially important in industries handling heavy and abrasive materials, such as mining and aggregates. Implementing a conveyor impact bed enhances the overall efficiency of material handling systems by minimizing belt wear and tear, preventing spillage, and ensuring smoother operation. The use of impact beds not only extends the lifespan of conveyor belts but also improves workplace safety and reduces downtime, contributing to more reliable and cost-effective operations.
Conveyor Impact Bed: Enhancing Belt Longevity and Efficiency
In industrial material handling, ensuring the longevity and efficiency of conveyor impact bed is paramount. A key component that significantly contributes to these goals is the conveyor impact bed. By absorbing and dissipating the energy from falling materials, a conveyor impact bed minimizes damage and enhances the performance of the belt conveyor system. This section will delve into the importance of conveyor scrapers in material handling, examining their role in maintaining clean and efficient conveyor systems and exploring the various types of conveyor scrapers and their applications.
Importance of Conveyor Scrapers in Material Handling
Conveyor scrapers are essential components in material handling, playing a crucial role in maintaining the cleanliness and efficiency of conveyor systems. Their primary function is to remove any residual material that adheres to the conveyor belt after the discharge point, ensuring that the belt remains clean and operational.
Role of Conveyor Scrapers in Maintaining Clean and Efficient Conveyor Systems
Conveyor scrapers are vital for several reasons:
Preventing Material Build-up: One of the primary functions of conveyor scrapers is to prevent the build-up of material on the conveyor belt. When materials adhere to the belt, they can accumulate over time, leading to various issues such as belt misalignment, increased wear, and reduced efficiency. Scrapers ensure that the belt is free from residual material, maintaining optimal performance and reducing the need for frequent cleaning and maintenance.
Reducing Wear and Tear: Continuous material build-up on the conveyor belt can cause significant wear and tear on both the belt and the conveyor components. This build-up can lead to increased friction and abrasion, which accelerates the deterioration of the belt and other parts. By effectively removing residual material, conveyor scrapers help to minimize wear and tear, extending the lifespan of the conveyor system and reducing maintenance costs.
Enhancing Operational Efficiency: Clean conveyor belts operate more efficiently than those with residual material. Material build-up can cause the belt to run slower and require more energy to operate, leading to higher operational costs. Conveyor scrapers ensure that the belt remains clean and free from obstructions, allowing for smooth and efficient operation. This enhanced efficiency translates to increased productivity and lower energy consumption.
Improving Safety: Residual material on conveyor belts can pose significant safety hazards. Accumulated material can fall off the belt, creating a slippery and dangerous work environment. Additionally, excessive material build-up can lead to belt misalignment, which can cause accidents and injuries. Conveyor scrapers help to maintain a clean and safe work environment by preventing material accumulation and ensuring that the conveyor system operates safely.
Types of Conveyor Scrapers and Their Applications
There are several types of conveyor scrapers, each designed to meet specific needs and applications. Understanding the different types of scrapers and their uses can help in selecting the most appropriate scraper for a particular conveyor system.
Primary Scrapers: Primary scrapers, also known as pre-cleaners, are installed at the discharge point of the conveyor belt. Their primary function is to remove the bulk of the material that adheres to the belt after it discharges the material load. Primary scrapers are typically made from durable materials such as polyurethane or tungsten carbide, which are capable of withstanding the harsh conditions of industrial applications. These scrapers are essential for preventing large chunks of material from sticking to the belt and causing subsequent problems.
Secondary Scrapers: Secondary scrapers, or secondary cleaners, are installed after the primary scrapers. Their role is to remove any residual material that the primary scrapers might have missed. Secondary scrapers are usually made from softer materials such as rubber or polyurethane, allowing them to make closer contact with the belt and remove finer particles. These scrapers are crucial for ensuring that the belt is thoroughly cleaned and free from any remaining material.
Tertiary Scrapers: In some applications, a third set of scrapers, known as tertiary scrapers or fin cleaners, may be used. These scrapers provide an additional level of cleaning, ensuring that the conveyor belt is completely free from any residual material. Tertiary scrapers are typically made from the same materials as secondary scrapers and are used in applications where maintaining a clean belt is critical for operational efficiency and safety.
V-Plow Scrapers: V-plow scrapers are designed to remove material from the return side of the conveyor belt, preventing it from building up on the return rollers and causing damage. These scrapers are installed in a V-shaped configuration, which allows them to effectively divert material off the belt. V-plow scrapers are particularly useful in applications where the belt carries sticky or abrasive materials that can adhere to the return side of the belt.
Brush Scrapers: Brush scrapers use rotating brushes to clean the conveyor belt. These scrapers are particularly effective at removing fine particles and sticky materials that may be difficult to remove with traditional scrapers. Brush scrapers are often used in applications where hygiene is critical, such as in food processing and pharmaceutical industries, as they provide a gentle yet effective cleaning action.
Segmented Scrapers: Segmented scrapers consist of multiple segments that can move independently of each other. This design allows the scraper to conform to the contours of the conveyor belt, ensuring consistent contact and effective cleaning. Segmented scrapers are ideal for belts with irregular surfaces or belts that experience significant fluctuations in tension.
What is Conveyor Impact Bed
Superior Impact Bed Designs
Impact beds are crucial components in conveyor systems, designed to absorb the impact of falling materials and protect the conveyor belt from damage. Superior impact beds are renowned for their innovative designs and exceptional performance, significantly enhancing the efficiency and longevity of conveyor operations. This section explores the innovative features of superior impact beds and how they contribute to reducing maintenance costs and downtime.
Innovative Features of Superior Impact Beds for Enhanced Performance
Superior impact beds are engineered with several innovative features that set them apart from conventional impact beds. These features are designed to provide optimal protection, improve performance, and ensure the durability of the conveyor system.
1. Robust Construction:
Superior impact beds are built using high-strength materials, typically heavy-duty steel for the frames, providing a solid and stable foundation. This robust construction ensures that the impact beds can withstand the harsh conditions of industrial environments, such as mining and quarrying, without deforming or failing under heavy impact forces.
2. Energy-Absorbing Impact Bars:
The impact bars used in superior impact beds are designed to absorb and dissipate the energy from falling materials, reducing the force transmitted to the conveyor belt. These bars often feature a top layer of ultra-high molecular weight (UHMW) polyethylene, which provides a smooth surface for the belt to glide over, and a bottom layer of resilient rubber or similar material that enhances shock absorption. This combination effectively mitigates impact forces and protects the conveyor belt from damage.
3. Modular Design:
One of the standout features of superior impact beds is their modular design. This design allows for easy installation, maintenance, and customization. Modular components can be quickly replaced or reconfigured as needed, minimizing downtime and maintenance efforts. This flexibility is crucial for operations that require quick adjustments and repairs to maintain productivity.
4. Adjustable Supports:
Superior impact beds are equipped with adjustable supports that can be fine-tuned to match the contour of the conveyor belt. These supports ensure consistent contact and impact absorption across the entire width of the belt, preventing belt sagging and reducing the risk of material spillage. Properly adjusted supports also contribute to improved belt tracking and reduced wear.
5. Enhanced Safety Features:
Safety is a critical consideration in the design of superior impact beds. These beds are designed to prevent sudden failures and reduce the likelihood of accidents caused by belt damage. By effectively absorbing impact forces and maintaining belt integrity, superior impact beds enhance the overall safety of conveyor systems, protecting both equipment and personnel.
How Superior Impact Beds Reduce Maintenance Costs and Downtime
The innovative features of superior impact beds not only enhance performance but also lead to significant reductions in maintenance costs and operational downtime. Here’s how:
1. Prolonged Conveyor Belt Life:
By absorbing the impact forces of falling materials, superior impact beds protect the conveyor belt from excessive wear and damage. This protection extends the lifespan of the belt, reducing the frequency of replacements and the associated costs. The durable construction of the impact bars also ensures that they can withstand repeated impacts without deteriorating, further contributing to the longevity of the conveyor system.
2. Minimized Downtime:
The modular design of superior impact beds allows for quick and easy replacement of individual components. This feature is particularly beneficial when repairs are needed, as it minimizes the downtime required to get the conveyor system back up and running. Operations can replace worn or damaged impact bars without having to disassemble the entire impact bed, ensuring that maintenance activities are completed swiftly and efficiently.
3. Reduced Maintenance Efforts:
Superior impact beds are designed for easy maintenance, with accessible components that can be inspected and replaced without extensive disassembly. This ease of maintenance reduces the time and labor required to keep the impact beds in optimal condition, allowing maintenance teams to focus on other critical tasks. Regular inspections and timely replacements of impact bars and supports ensure that the impact bed continues to provide effective protection, preventing unexpected breakdowns and costly repairs.
4. Enhanced Operational Efficiency:
By preventing material spillage and maintaining proper belt alignment, superior impact beds contribute to smoother and more efficient conveyor operations. This efficiency reduces the strain on other conveyor components, such as rollers and pulleys, which in turn decreases the overall maintenance requirements of the conveyor system. Improved operational efficiency also leads to higher productivity, as materials are transported more reliably and with fewer interruptions.
5. Lower Total Cost of Ownership:
Investing in superior impact beds can lead to lower total cost of ownership for conveyor systems. The initial investment in high-quality impact beds is offset by the savings in maintenance costs, reduced downtime, and extended equipment life. Over time, the benefits of superior impact beds translate into significant cost savings and improved profitability for industrial operations.
How about ASGCO Impact Beds: Quality and Reliability
In the realm of material handling, the durability and efficiency of conveyor belts are paramount to maintaining seamless operations and minimizing downtime. The ASGCO impact bed conveyor is a critical component designed to absorb the shock of falling materials, thereby protecting conveyor belts from damage and enhancing their longevity. This section will explore the key features and benefits of ASGCO impact beds and provide case studies showcasing their effectiveness in various industrial applications.
Key Features and Benefits of ASGCO Impact Beds
ASGCO impact beds are engineered to provide superior protection and durability in some of the most demanding industrial environments. Here are the key features and benefits that set ASGCO impact beds apart:
Innovative Design: The design of ASGCO impact beds incorporates heavy-duty steel frames combined with advanced energy-absorbing materials. This combination ensures that the impact beds can withstand substantial impact forces while providing consistent support across the conveyor belt. The robust construction is critical for maintaining the integrity of the conveyor system under heavy loads and continuous operation.
High-Quality Materials: ASGCO uses top-grade materials, such as UHMW (Ultra High Molecular Weight) polyethylene and rubber, for the impact bars. These materials are chosen for their superior wear resistance, impact absorption, and long service life. The use of high-quality materials ensures that the impact beds can endure harsh operational conditions, thereby reducing maintenance needs and extending the life of the conveyor belt.
Customizability: ASGCO impact beds are highly customizable to meet the specific needs of various applications. They can be tailored in terms of size, configuration, and material composition to suit different conveyor widths, load types, and operational environments. This flexibility makes ASGCO impact beds suitable for a wide range of industries, from mining and aggregate processing to power generation and manufacturing.
Enhanced Belt Protection: The primary benefit of ASGCO impact beds is the enhanced protection they provide to conveyor belts. By absorbing and distributing the energy from falling materials, these impact beds prevent tears, punctures, and excessive wear on the belt. This protection is crucial for maintaining the operational efficiency of conveyor systems and reducing the frequency of belt replacements.
Improved Material Flow: ASGCO impact beds help to maintain a smooth and consistent material flow by providing a stable surface for the conveyor belt. This stability reduces the risk of material spillage and ensures that the materials are transported efficiently from one point to another. Improved material flow translates to higher productivity and fewer interruptions in the production process.
Reduced Maintenance and Downtime: The durability and reliability of ASGCO impact beds result in lower maintenance requirements and reduced downtime. The impact beds are designed for easy installation and maintenance, with features such as slide-out service bars that facilitate quick and efficient replacement of worn parts. By minimizing maintenance needs, ASGCO impact beds help to keep conveyor systems running smoothly and reduce overall operational costs.
Case Studies Showcasing the Effectiveness of ASGCO Impact Beds
The effectiveness of ASGCO impact beds is demonstrated through numerous case studies across different industries. These real-world examples highlight how ASGCO impact beds have improved operational efficiency, reduced maintenance costs, and extended the life of conveyor belts.
Mining Industry Case Study
A major mining operation in North America faced significant challenges with their conveyor systems due to the impact of large, heavy ore. The frequent belt damage and maintenance issues resulted in costly downtime and reduced productivity. After installing ASGCO impact beds at critical transfer points, the mining operation experienced a marked improvement in conveyor belt performance. The impact beds effectively absorbed the shock of falling ore, preventing belt tears and punctures. This led to a significant reduction in maintenance costs and downtime, allowing the mine to operate more efficiently and increase its output.
Aggregate Processing Case Study
An aggregate producer in the Midwest struggled with excessive wear and frequent belt replacements due to the abrasive nature of the materials being processed. The company decided to install ASGCO impact beds to protect their conveyor belts and enhance the durability of their system. The impact beds provided the necessary cushioning and support, drastically reducing belt wear and extending the lifespan of the conveyor system. As a result, the aggregate producer saw a significant decrease in maintenance costs and an increase in operational efficiency, enabling them to meet production targets more consistently.
Power Generation Case Study
A coal-fired power plant in the Southeast faced challenges with their coal handling system, particularly at transfer points where heavy coal loads caused frequent belt damage. The installation of ASGCO impact beds provided a robust solution to this problem. The impact beds absorbed the impact of the coal, protecting the conveyor belts from damage and ensuring a smooth material flow. This improvement led to a reduction in downtime and maintenance costs, enhancing the overall efficiency of the coal handling process and supporting the plant’s continuous operation.
Cement Industry Case Study
A cement plant in Europe was experiencing significant belt damage and material spillage due to the impact of heavy clinker loads. To address these issues, the plant installed ASGCO impact beds at key transfer points. The impact beds effectively cushioned the impact of the clinker, preventing belt damage and reducing material spillage. This not only improved the cleanliness and safety of the work environment but also extended the life of the conveyor belts. The plant reported a notable reduction in maintenance costs and downtime, leading to more reliable and efficient operations.
Recycling Industry Case Study
A large recycling facility on the West Coast was dealing with frequent belt damage due to the varied and sometimes sharp materials processed through their conveyor system. The installation of ASGCO impact beds provided a significant improvement. The impact beds absorbed the shock from falling materials, protecting the belts from damage and ensuring consistent operation. The facility experienced a reduction in belt replacements and maintenance needs, resulting in lower operational costs and higher productivity.
Food Processing Industry Case Study
In the food processing industry, maintaining clean and efficient conveyor systems is critical. A major food processing plant in the Midwest utilized ASGCO impact beds to enhance their conveyor system’s performance. The impact beds provided effective cushioning for heavy and bulk food products, preventing belt damage and ensuring smooth material flow. This improvement contributed to a more efficient and reliable production process, reducing downtime and maintenance costs while maintaining high product quality.
The Keys of Conveyor Impact Bed
Slider/Impact Bed Combination Systems
Conveyor systems are vital in many industries for efficient material handling. Among the various components that enhance the performance and longevity of these systems, the impact beds for conveyorsplays a crucial role. A notable innovation in this area is the slider/impact bed combination system, which integrates the functionalities of both slider beds and impact beds to offer superior protection and efficiency.
Understanding the Functionality and Benefits of Slider/Impact Bed Combinations
A slider/impact bed combination system is designed to provide comprehensive support and protection for the conveyor belt, especially at loading points where the impact from falling materials is highest. This system combines the cushioning effect of impact beds with the smooth, continuous support of slider beds, ensuring that the conveyor belt remains protected and operates efficiently.
Functionality:
- Impact Absorption: The impact bed component of the combination system absorbs the shock and energy from falling materials. This is achieved through the use of energy-absorbing impact bars, typically made from ultra-high molecular weight (UHMW) polyethylene on top and a resilient material like rubber beneath. These bars dissipate the energy and reduce the impact force transferred to the belt.
- Continuous Support: The slider bed component provides a flat, continuous surface that supports the conveyor belt. This continuous support prevents belt sagging and reduces the risk of material spillage, ensuring that the belt runs smoothly and remains aligned.
- Combined Benefits: By integrating these two functionalities, the slider/impact bed combination system ensures that the belt is protected from impact damage while also maintaining optimal tension and alignment. This dual functionality helps to extend the life of the conveyor belt and reduces maintenance requirements.
Benefits:
- Enhanced Belt Protection: The combination of impact absorption and continuous support protects the conveyor belt from both impact damage and wear caused by sagging or misalignment. This results in a longer lifespan for the belt and reduced maintenance costs.
- Improved Material Handling Efficiency: With a slider/impact bed combination system, materials are less likely to spill or cause damage to the belt. This leads to more efficient material handling, reducing downtime and increasing overall productivity.
- Versatility: These systems can be customized to fit various conveyor setups and are suitable for a wide range of materials, from fine powders to heavy, abrasive rocks. Their versatility makes them ideal for numerous applications across different industries.
- Reduced Downtime: The durability and reliability of slider/impact bed combination systems mean fewer unexpected breakdowns and repairs. This reliability translates into less operational downtime and higher efficiency.
- Ease of Maintenance: These systems are designed for easy maintenance, with modular components that can be quickly inspected and replaced if necessary. This ease of maintenance ensures that the conveyor system remains in optimal condition with minimal effort.
Applications Where Slider/Impact Bed Systems Excel
Slider/impact bed combination systems are particularly effective in applications where materials are loaded onto the conveyor belt from significant heights or where the conveyed materials are heavy and abrasive. Here are some specific applications where these systems excel:
1. Mining and Quarrying:
In mining and quarrying operations, materials such as ores, rocks, and minerals are often dropped onto conveyor belts from considerable heights. The heavy and abrasive nature of these materials can cause significant impact damage to the belt. Slider/impact bed combination systems provide the necessary protection to absorb these impacts and support the belt, ensuring continuous and efficient operation.
2. Aggregate Processing:
Aggregate processing involves handling materials like sand, gravel, and crushed stone, which can be rough on conveyor systems. The combined cushioning and support of slider/impact bed systems help to manage the impact and reduce wear on the belts, improving the efficiency and longevity of the conveyor system.
3. Bulk Material Handling:
Industries that handle bulk materials, such as coal, grain, and cement, benefit greatly from slider/impact bed combination systems. These systems ensure that the conveyor belts remain stable and aligned under heavy loads, preventing spillage and maintaining smooth operations.
4. Recycling and Waste Management:
In recycling and waste management facilities, conveyor belts often transport various materials, including metals, plastics, and glass. The slider/impact bed combination system protects the belt from the impact of heavy or sharp objects and ensures that materials are conveyed efficiently without causing damage to the system.
5. Ports and Terminals:
Ports and terminals that handle the loading and unloading of bulk materials from ships and trucks require robust conveyor systems. Slider/impact bed combination systems provide the necessary support and impact protection to handle these demanding operations, ensuring smooth and reliable material transfer.
The Types of Conveyor Impact Bed
Flexco Impact Bed Solutions
Flexco is a leading provider of innovative solutions for conveyor belt maintenance and optimization. Their impact beds are designed to absorb shock and protect conveyor belts from damage during material loading. This section delves into the features and advantages of Flexco impact beds, and explores their real-world applications across various industries.
Features and Advantages of Flexco Impact Beds
Flexco impact beds are engineered to deliver superior performance in demanding material handling environments. Here are some key features and advantages that set Flexco conveyor impact bed apart:
1. Robust Construction:
Flexco impact beds are built with high-strength materials, ensuring durability and long service life. The frames are typically made from heavy-duty steel, providing a stable foundation capable of withstanding the harsh conditions of industrial environments. This robust construction ensures that the impact beds can absorb substantial impact forces without deforming or failing.
2. Energy-Absorbing Impact Bars:
The impact bars used in Flexco impact beds are designed to absorb and dissipate the energy from falling materials, reducing the force transmitted to the conveyor belt. These bars often feature a top layer of ultra-high molecular weight (UHMW) polyethylene, which provides a smooth surface for the belt to glide over, and a bottom layer of resilient rubber or similar material that enhances shock absorption. This combination effectively mitigates impact forces and protects the conveyor belt from damage.
3. Modular Design:
One of the standout features of Flexco impact beds is their modular design. This design allows for easy installation, maintenance, and customization. Modular components can be quickly replaced or reconfigured as needed, minimizing downtime and maintenance efforts. This flexibility is crucial for operations that require quick adjustments and repairs to maintain productivity.
4. Adjustable Supports:
Flexco impact beds are equipped with adjustable supports that can be fine-tuned to match the contour of the conveyor belt. These supports ensure consistent contact and impact absorption across the entire width of the belt, preventing belt sagging and reducing the risk of material spillage. Properly adjusted supports also contribute to improved belt tracking and reduced wear.
5. Enhanced Safety Features:
Safety is a critical consideration in the design of Flexco impact beds. These beds are designed to prevent sudden failures and reduce the likelihood of accidents caused by belt damage. By effectively absorbing impact forces and maintaining belt integrity, Flexco impact beds enhance the overall safety of conveyor systems, protecting both equipment and personnel.
6. Easy Maintenance:
Maintenance is simplified with Flexco impact beds, thanks to their modular and accessible design. The impact bars can be easily inspected and replaced without the need for extensive disassembly. This ease of maintenance reduces downtime and ensures that the conveyor system remains operational for longer periods.
7. Versatility:
Flexco impact beds are versatile and can be used in a variety of applications, from mining and quarrying to material processing and bulk handling. Their robust design and effective impact absorption make them suitable for handling a wide range of materials, including heavy ores, coal, aggregates, and more.
8. Improved Operational Efficiency:
By preventing material spillage and maintaining proper belt alignment, Flexco impact beds contribute to smoother and more efficient conveyor operations. This efficiency reduces the strain on other conveyor components, such as rollers and pulleys, which in turn decreases the overall maintenance requirements of the conveyor system. Improved operational efficiency also leads to higher productivity, as materials are transported more reliably and with fewer interruptions.
9. Reduced Maintenance Costs:
The durable construction and effective impact absorption of Flexco impact beds significantly reduce the need for frequent maintenance and repairs. This durability translates to lower maintenance costs and extended equipment life, providing a high return on investment for industrial operations.
10. Environmental Sustainability:
Flexco impact beds are designed with sustainability in mind. The use of durable materials and efficient design reduces waste and extends the lifespan of conveyor components. Additionally, by preventing material spillage, these impact beds help maintain a cleaner work environment, contributing to overall environmental sustainability.
Real-World Applications of Flexco Impact Beds in Various Industries
Flexco impact beds are used in a wide range of industries, demonstrating their versatility and effectiveness in real-world applications. Here are some examples of how Flexco impact beds are utilized across different sectors:
1. Mining and Quarrying:
In mining and quarrying operations, materials such as ores, rocks, and minerals are often dropped onto conveyor belts from considerable heights. The heavy and abrasive nature of these materials can cause significant impact damage to the belt. Flexco impact beds provide the necessary protection to absorb these impacts and support the belt, ensuring continuous and efficient operation. By mitigating impact forces, these impact beds extend the lifespan of the conveyor belt and reduce maintenance costs.
2. Aggregate Processing:
Aggregate processing involves handling materials like sand, gravel, and crushed stone, which can be rough on conveyor systems. Flexco impact beds help to manage the impact and reduce wear on the belts, improving the efficiency and longevity of the conveyor system. The adjustable supports and modular design of Flexco impact beds allow for easy customization and maintenance, ensuring optimal performance in aggregate processing operations.
3. Bulk Material Handling:
Industries that handle bulk materials, such as coal, grain, and cement, benefit greatly from Flexco impact beds. These systems ensure that the conveyor belts remain stable and aligned under heavy loads, preventing spillage and maintaining smooth operations. The robust construction and energy-absorbing features of Flexco impact beds make them ideal for handling a wide range of bulk materials in various industrial settings.
4. Recycling and Waste Management:
In recycling and waste management facilities, conveyor belts often transport various materials, including metals, plastics, and glass. Flexco impact beds protect the belt from the impact of heavy or sharp objects and ensure that materials are conveyed efficiently without causing damage to the system. The versatility and durability of Flexco impact beds make them suitable for the diverse material handling needs of recycling and waste management operations.
5. Ports and Terminals:
Ports and terminals that handle the loading and unloading of bulk materials from ships and trucks require robust conveyor systems. Flexco impact beds provide the necessary support and impact protection to handle these demanding operations, ensuring smooth and reliable material transfer. The easy maintenance and modular design of Flexco impact beds make them ideal for the dynamic and high-volume environments of ports and terminals.
6. Cement Industry:
The cement industry involves the transportation of raw materials, clinker, and finished cement products. Flexco impact beds help manage the impact forces associated with the heavy and abrasive nature of these materials. By providing consistent support and protection to the conveyor belt, Flexco impact beds enhance the efficiency and reliability of cement production operations.
7. Power Plants:
Power plants that rely on conveyor systems for coal transportation benefit from the robust design and impact absorption capabilities of Flexco impact beds. These impact beds protect the conveyor belts from the impact of heavy coal loads, ensuring continuous and efficient operation. The enhanced safety features of Flexco impact beds also contribute to the overall safety of power plant operations.
FAQS about Conveyor Impact Bed
A slider bed conveyor is a type of belt conveyor that uses a flat, stationary surface (the bed) to support the belt and the materials being transported. Unlike roller conveyors, which use a series of rollers to move the belt, slider bed conveyors rely on the friction between the belt and the bed surface. This design provides a smooth and continuous surface for the belt, making it ideal for transporting small or irregularly shaped items that might get caught or damaged on roller conveyors. Slider bed conveyors are commonly used in industries such as packaging, manufacturing, and distribution, where they handle a variety of materials, including boxes, packages, and loose items. The main advantages of slider bed conveyors include their simplicity, ease of maintenance, and ability to handle a wide range of products. They are particularly effective in applications where the conveyor needs to operate at a relatively low speed and with a consistent, flat surface.
An impact roller on a belt conveyor is a type of idler roller designed to withstand the impact and shock loads at the loading points of the conveyor system. These rollers are constructed with a robust core, often made of steel, and are covered with a thick layer of shock-absorbing material, such as rubber. The primary purpose of impact rollers is to protect the conveyor belt from damage caused by the falling material, ensuring that the belt remains in good condition and operates smoothly. By absorbing the energy from the impact, these rollers reduce wear and tear on the belt and minimize maintenance costs. Impact rollers also help maintain the belt’s alignment, preventing issues like mistracking and spillage. They are essential in applications where the conveyor system handles heavy, abrasive, or large-sized materials.
Impact bars for conveyors are components designed to provide cushioning and protection for the conveyor belt at loading points. These bars are typically made from a combination of materials, including a top layer of low-friction polyethylene and a bottom layer of high-impact rubber. The polyethylene layer allows the conveyor belt to glide smoothly over the bars, while the rubber layer absorbs the shock and impact from falling materials. The primary function of impact bars is to prevent damage to the conveyor belt, such as punctures, tears, and excessive wear. They also help in maintaining the alignment and stability of the belt, reducing the risk of material spillage and improving overall system efficiency. Impact bars are a crucial component in heavy-duty conveyor systems, particularly in industries dealing with bulk materials and harsh operating conditions.
A conveyor impact bed is a specialized piece of equipment used in conveyor systems to protect the conveyor belt from damage caused by falling materials. Positioned at critical transfer points, the impact bed absorbs the shock and energy generated when materials are loaded onto the belt. This absorption is achieved through the use of impact bars or pads, which are typically made of rubber or a similar shock-absorbing material. The primary functions of an impact bed include extending the life of the conveyor belt, reducing maintenance costs, and minimizing material spillage. By providing a stable and cushioned support, impact beds ensure the smooth and efficient operation of the conveyor system, making them essential in industries such as mining, aggregate, and construction, where heavy and abrasive materials are commonly handled.
Last Updated on August 15, 2024 by Jordan Smith
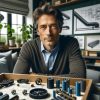
Jordan Smith, a seasoned professional with over 20 years of experience in the conveyor system industry. Jordan’s expertise lies in providing comprehensive solutions for conveyor rollers, belts, and accessories, catering to a wide range of industrial needs. From initial design and configuration to installation and meticulous troubleshooting, Jordan is adept at handling all aspects of conveyor system management. Whether you’re looking to upgrade your production line with efficient conveyor belts, require custom conveyor rollers for specific operations, or need expert advice on selecting the right conveyor accessories for your facility, Jordan is your reliable consultant. For any inquiries or assistance with conveyor system optimization, Jordan is available to share his wealth of knowledge and experience. Feel free to reach out at any time for professional guidance on all matters related to conveyor rollers, belts, and accessories.