Enhancing Efficiency with Conveyor Monitoring System Software
A conveyor monitoring system is an essential component in modern industrial operations, designed to ensure the smooth and efficient functioning of conveyor belt systems. These systems provide real-time data and analytics on the performance and condition of conveyor belts, helping to detect issues such as belt misalignment, slippage, and wear before they escalate into major problems. The significance of a conveyor monitoring system lies in its ability to enhance operational efficiency, reduce downtime, and prevent costly repairs. By continuously monitoring the health of conveyor belts, industries can maintain optimal productivity, ensure safety, and extend the lifespan of their equipment. Implementing a reliable conveyor monitoring system is a proactive step towards achieving seamless material handling processes.
Conveyor Monitoring System Software: Enhancing Efficiency
Key Features and Benefits of Using Conveyor Monitoring System Software
A conveyor monitoring system is essential for ensuring the efficient and reliable operation of conveyor systems in various industries. By leveraging advanced software, businesses can enhance their conveyor monitoring capabilities, leading to improved performance, reduced downtime, and increased safety. Here are the key features and benefits of using conveyor monitoring system software:
- Real-Time Data Collection and Analysis: Conveyor monitoring system software continuously collects data from various sensors and devices installed on the conveyor system. This data includes information on belt speed, load, temperature, vibration, and alignment. Real-time data analysis helps identify potential issues before they lead to failures, allowing for proactive maintenance and minimizing downtime.
- Predictive Maintenance: Advanced conveyor monitoring system software utilizes predictive analytics to forecast potential failures and maintenance needs. By analyzing historical data and identifying patterns, the software can predict when components are likely to fail and schedule maintenance accordingly. Predictive maintenance helps extend the lifespan of conveyor components, reduce unplanned downtime, and optimize maintenance schedules.
- Automated Alerts and Notifications: Conveyor monitoring system software can send automated alerts and notifications to maintenance personnel when potential issues are detected. These alerts can be delivered via email, SMS, or in-app notifications, ensuring that problems are addressed promptly. Automated notifications help prevent minor issues from escalating into major failures, improving overall system reliability.
- Remote Monitoring and Control: Many conveyor monitoring systems offer remote monitoring and control capabilities, allowing operators to oversee conveyor operations from anywhere. This feature is particularly useful for large facilities or remote locations where on-site monitoring may be challenging. Remote access enables real-time monitoring, troubleshooting, and adjustments, enhancing operational efficiency.
- Historical Data and Reporting: Conveyor monitoring system software maintains a comprehensive database of historical data, which can be used for trend analysis and reporting. Detailed reports on conveyor performance, maintenance history, and incident logs provide valuable insights for optimizing operations and improving system reliability. Historical data helps identify recurring issues and track the effectiveness of maintenance activities.
- Integration with Other Systems: Modern conveyor monitoring system software can integrate with other enterprise systems, such as ERP (Enterprise Resource Planning), MES (Manufacturing Execution Systems), and SCADA (Supervisory Control and Data Acquisition). Integration allows for seamless data exchange and centralized control, enhancing overall operational visibility and coordination.
- User-Friendly Interface: User-friendly interfaces, including dashboards and graphical displays, make it easy for operators to monitor conveyor systems and interpret data. Intuitive interfaces provide real-time visualizations of key performance indicators (KPIs), making it easier to identify and address issues. Customizable dashboards allow users to focus on the most relevant data for their specific needs.
- Enhanced Safety: Conveyor monitoring system software helps improve safety by monitoring critical parameters and detecting hazardous conditions. Automated shutdowns can be triggered when unsafe conditions are detected, preventing accidents and protecting workers. Enhanced safety features contribute to a safer working environment and help comply with industry regulations.
- Energy Efficiency: Monitoring energy consumption is another important feature of conveyor monitoring system software. By analyzing energy usage patterns, the software can identify opportunities for improving energy efficiency and reducing operational costs. Energy-efficient operations contribute to sustainability goals and lower the overall carbon footprint.
- Scalability: Conveyor monitoring system software is scalable, allowing businesses to expand their monitoring capabilities as needed. Whether it’s adding new conveyor lines, integrating additional sensors, or expanding to new facilities, the software can accommodate growth and evolving operational requirements.
Conveyor monitoring system software offers numerous features and benefits that enhance the efficiency, reliability, and safety of conveyor operations. By leveraging real-time data, predictive analytics, remote monitoring, and integration capabilities, businesses can optimize their material handling processes and achieve greater operational excellence.
Free Conveyor Monitoring System Options
Exploring Free Options for Conveyor Monitoring Systems and Their Capabilities
For businesses looking to implement conveyor monitoring systems without significant upfront investment, free options are available that offer valuable monitoring capabilities. While free conveyor monitoring systems may not have all the advanced features of commercial solutions, they can still provide essential monitoring and control functions. Here are some free options for conveyor monitoring systems and their capabilities:
- Open Source Conveyor Monitoring Software: Open source software offers a cost-effective way to implement conveyor monitoring systems. These solutions are developed and maintained by communities of developers and are available for free download and use. Open source conveyor monitoring software typically includes basic monitoring features, such as real-time data collection, alerts, and reporting. Users can customize and extend the software to meet their specific needs, leveraging the flexibility and transparency of open source code.
- Free Versions of Commercial Software: Some commercial conveyor monitoring system providers offer free versions or trial versions of their software. These versions may have limited features compared to the full, paid versions but can still provide valuable monitoring capabilities. Free versions often include essential functions such as real-time monitoring, basic alerts, and data logging. Businesses can use these free versions to evaluate the software and determine if it meets their needs before committing to a paid subscription.
- IoT Platforms with Free Tiers: Internet of Things (IoT) platforms often offer free tiers that can be used for conveyor monitoring. IoT platforms enable connectivity and data exchange between conveyor systems and cloud-based monitoring solutions. Free tiers typically include a limited number of devices and data points but provide access to essential monitoring features such as real-time data visualization, alerts, and remote access. Popular IoT platforms with free tiers include ThingSpeak, Adafruit IO, and Blynk.
- Custom-Built Solutions Using Free Tools: Businesses with technical expertise can build custom conveyor monitoring systems using free tools and libraries. For example, free programming languages like Python and JavaScript, along with libraries such as MQTT (Message Queuing Telemetry Transport) and InfluxDB, can be used to create custom monitoring solutions. Additionally, free visualization tools like Grafana can be integrated to display real-time data and generate reports. Custom-built solutions offer maximum flexibility and can be tailored to specific requirements.
- Community-Supported Solutions: Community-supported solutions, often shared on platforms like GitHub and GitLab, provide free conveyor monitoring systems developed by other users. These solutions may include pre-built software, scripts, and documentation for setting up and using the monitoring system. Community-supported solutions benefit from collaborative development and support, making them a valuable resource for businesses seeking cost-effective monitoring options.
Capabilities of Free Conveyor Monitoring Systems
While free conveyor monitoring systems may not have the advanced features of commercial solutions, they still offer essential capabilities that can enhance conveyor operations:
- Real-Time Monitoring: Free monitoring systems can collect and display real-time data from sensors and devices installed on the conveyor system. This data includes key parameters such as belt speed, load, temperature, and vibration, providing valuable insights into conveyor performance.
- Alerts and Notifications: Basic alerting capabilities allow free monitoring systems to send notifications when potential issues are detected. Alerts can be delivered via email, SMS, or in-app notifications, enabling prompt response to address problems and prevent downtime.
- Data Logging and Reporting: Free monitoring systems often include data logging and reporting features, allowing users to store and analyze historical data. Reports can provide insights into conveyor performance, maintenance needs, and trends over time, helping businesses make informed decisions.
- Remote Access: Some free monitoring systems offer remote access capabilities, enabling operators to monitor and control conveyor systems from anywhere. Remote access enhances operational flexibility and allows for timely intervention in case of issues.
- Basic Visualization: Free monitoring systems may include basic visualization tools, such as dashboards and charts, to display real-time data and key performance indicators (KPIs). Visualizations help operators quickly identify and address issues, improving overall efficiency.
- Integration with Other Systems: Depending on the platform, free monitoring systems may support integration with other enterprise systems, such as ERP and MES. Integration enables seamless data exchange and centralized control, enhancing overall operational visibility.
While free conveyor monitoring systems may have limitations compared to commercial solutions, they still provide valuable monitoring and control capabilities that can enhance conveyor operations. Businesses can leverage these free options to implement cost-effective monitoring solutions and improve the efficiency and reliability of their conveyor systems.
Accessing Conveyor Monitoring System PDF Resources
Guide to Obtaining and Utilizing Conveyor Monitoring System PDFs
Conveyor monitoring system PDFs are valuable resources that provide comprehensive information on the design, implementation, and maintenance of conveyor monitoring systems. These documents can include user manuals, technical specifications, installation guides, and best practices. Here is a guide to obtaining and utilizing conveyor monitoring system PDFs:
- Manufacturer Websites: The websites of conveyor monitoring system manufacturers are a primary source for PDF resources. Manufacturers often provide downloadable PDFs that include user manuals, technical datasheets, installation guides, and maintenance instructions. Visit the manufacturer’s website and navigate to the support or resources section to find available PDFs.
- Online Libraries and Databases: Online libraries and databases, such as IEEE Xplore, Google Scholar, and ResearchGate, offer access to research papers, technical articles, and industry standards related to conveyor monitoring systems. These PDFs provide in-depth information on the latest technologies, innovations, and best practices in conveyor monitoring. Access to these databases may require a subscription or institutional access.
- Industry Associations and Standards Organizations: Industry associations and standards organizations, such as the Conveyor Equipment Manufacturers Association (CEMA) and the International Organization for Standardization (ISO), publish guidelines, standards, and technical papers related to conveyor systems. These documents are often available in PDF format and can be accessed through the organization’s website or through membership benefits.
- Technical Forums and Community Websites: Technical forums and community websites, such as Reddit, LinkedIn groups, and specialized conveyor industry forums, are valuable sources of shared knowledge and resources. Members of these communities often share PDFs of user manuals, troubleshooting guides, and best practices. Join relevant forums and participate in discussions to access and share PDF resources.
- Academic Institutions and Libraries: Academic institutions and libraries often have extensive collections of technical documents and research papers related to conveyor monitoring systems. University libraries, in particular, may provide access to PDFs through digital repositories or interlibrary loan services. Contact the library or institution for access to these resources.
Utilizing Conveyor Monitoring System PDFs
Once you have obtained conveyor monitoring system PDFs, here are some ways to utilize them effectively:
- Implementation and Installation: Use installation guides and user manuals to properly set up and configure your conveyor monitoring system. These documents provide step-by-step instructions, wiring diagrams, and calibration procedures to ensure correct installation and optimal performance.
- Troubleshooting and Maintenance: Technical datasheets and maintenance manuals offer valuable information for troubleshooting and maintaining your conveyor monitoring system. Use these PDFs to diagnose issues, perform routine maintenance, and replace components as needed. Regular reference to these documents can help prevent downtime and extend the lifespan of your equipment.
- Training and Education: PDFs such as user manuals and best practice guides can be used for training and educating employees on the operation and maintenance of conveyor monitoring systems. Ensure that all relevant personnel have access to these documents and understand their contents to promote safe and efficient operations.
- Design and Optimization: Research papers, technical articles, and industry standards provide insights into the latest advancements and best practices in conveyor monitoring system design. Use these PDFs to inform the design and optimization of your monitoring system, incorporating new technologies and methodologies to enhance performance.
- Compliance and Standards: Industry standards and guidelines ensure that your conveyor monitoring system complies with relevant regulations and best practices. Refer to PDFs from standards organizations to ensure your system meets safety, performance, and environmental requirements.
- Continuous Improvement: Use technical articles and research papers to stay informed about the latest trends and innovations in conveyor monitoring systems. Continuous learning and application of new knowledge can help you improve your system’s efficiency, reliability, and safety over time.
By obtaining and utilizing conveyor monitoring system PDFs, businesses can access valuable information that supports the effective implementation, maintenance, and optimization of their monitoring systems. These resources provide essential guidance and best practices that enhance the efficiency and reliability of conveyor operations.
Conveyor Monitoring System: Importance of Belt Monitoring Systems
The Role and Importance of Belt Monitoring Systems in Maintaining Conveyor Efficiency
In the world of industrial automation and material handling, a conveyor monitoring system plays a crucial role in ensuring the efficient and reliable operation of conveyor belt systems. Belt monitoring systems are integral to maintaining conveyor efficiency, preventing costly downtime, and enhancing the safety of operations. Here are the key reasons why belt monitoring systems are essential:
- Real-Time Condition Monitoring: Belt monitoring systems provide real-time data on the condition of the conveyor belt, including parameters such as belt speed, tension, temperature, and wear. This continuous monitoring allows for the early detection of issues such as misalignment, slippage, and abnormal wear, enabling timely intervention and maintenance.
- Predictive Maintenance: By analyzing data collected from sensors and other monitoring devices, a conveyor monitoring system can predict potential failures and maintenance needs. Predictive maintenance helps in planning and scheduling maintenance activities before issues escalate, reducing unplanned downtime and extending the lifespan of conveyor components.
- Safety Enhancement: Belt monitoring systems contribute significantly to the safety of conveyor operations. They can detect hazardous conditions such as belt misalignment, excessive vibration, and overheating, triggering automated shutdowns or alerts to prevent accidents. Enhanced safety features protect workers and equipment, ensuring a safer working environment.
- Efficiency Optimization: Monitoring systems help optimize the efficiency of conveyor operations by providing insights into performance metrics and operational parameters. This data-driven approach allows for the fine-tuning of conveyor settings, improving material flow, reducing energy consumption, and maximizing productivity.
- Cost Savings: The implementation of a belt monitoring system can lead to substantial cost savings by reducing maintenance costs, minimizing downtime, and preventing costly repairs. Early detection and resolution of issues prevent major failures that could result in significant financial losses.
- Compliance with Regulations: Many industries are subject to stringent safety and environmental regulations. Belt monitoring systems help ensure compliance with these regulations by maintaining safe and efficient conveyor operations. Compliance with standards reduces the risk of legal penalties and enhances the reputation of the business.
- Data-Driven Decision Making: The data collected by belt monitoring systems provides valuable insights for decision-making. Operators can analyze trends, identify recurring issues, and make informed decisions to improve conveyor performance. This data-driven approach supports continuous improvement and operational excellence.
- Remote Monitoring Capabilities: Advanced belt monitoring systems offer remote monitoring capabilities, allowing operators to oversee conveyor operations from any location. Remote access enhances operational flexibility, enabling real-time monitoring, troubleshooting, and adjustments without the need for on-site presence.
Belt monitoring systems are vital for maintaining the efficiency, safety, and reliability of conveyor operations. By providing real-time condition monitoring, enabling predictive maintenance, enhancing safety, optimizing efficiency, and supporting data-driven decision-making, these systems play a crucial role in the success of industrial material handling processes.
Conveyor Monitoring System: Overview of Conveyor Belt Systems
Detailed Look at Different Types of Conveyor Belt Systems and Their Applications
Conveyor belt systems are essential components of material handling in various industries, enabling the efficient transport of materials over long distances and through complex production processes. There are several types of conveyor belt systems, each designed for specific applications and operational requirements. Here is a detailed overview of different types of conveyor belt systems and their applications:
- Flat Belt Conveyors: Flat belt conveyors are the most common type of conveyor system. They consist of a continuous belt made from materials such as rubber, fabric, or synthetic polymers, which is supported by rollers or a flat pan. Flat belt conveyors are used in a wide range of industries, including manufacturing, warehousing, and logistics, for transporting light to medium-weight materials. They are ideal for moving products along assembly lines, sorting items, and handling packaged goods.
- Modular Belt Conveyors: Modular belt conveyors use interlocking plastic modules to form a continuous belt. These conveyors are highly versatile and can be configured in various shapes, including straight, curved, and inclined paths. Modular belt conveyors are commonly used in the food and beverage industry due to their easy-to-clean design and resistance to moisture and chemicals. They are also suitable for applications that require frequent belt changes or reconfigurations.
- Cleated Belt Conveyors: Cleated belt conveyors feature belts with raised sections, or cleats, that help prevent materials from sliding off during transport. These conveyors are ideal for moving loose or bulk materials, such as grains, coal, and gravel, up inclines. Cleated belt conveyors are widely used in the agriculture, mining, and construction industries to transport materials to different processing stages or storage areas.
- Incline/Decline Belt Conveyors: Incline and decline belt conveyors are designed to transport materials between different elevations. These conveyors are commonly used in manufacturing and packaging facilities to move products between floors or conveyor levels. Incline and decline conveyors can be equipped with cleats or textured belts to ensure that materials remain in place during transport.
- Roller Bed Conveyors: Roller bed conveyors use a series of rollers to support and move the conveyor belt. These conveyors are suitable for transporting heavy or bulky items over long distances. Roller bed conveyors are often used in distribution centers, shipping facilities, and automotive assembly lines to handle large and heavy packages, pallets, and components.
- Wire Mesh Belt Conveyors: Wire mesh belt conveyors use a belt made of interwoven metal wires, creating an open mesh surface. These conveyors are ideal for applications that require ventilation, drainage, or exposure to heat. Wire mesh belt conveyors are commonly used in the food processing, baking, and metalworking industries for tasks such as cooling, drying, and heating products.
- Magnetic Belt Conveyors: Magnetic belt conveyors use magnets embedded in the belt or conveyor frame to transport ferrous materials. These conveyors are used in industries such as recycling, metal fabrication, and automotive manufacturing to move metal parts, scrap, and waste. Magnetic belt conveyors can handle both horizontal and inclined transport, ensuring that metal materials remain securely in place.
- Pneumatic Conveyors: Pneumatic conveyors use air pressure to transport materials through enclosed tubes or ducts. These conveyors are ideal for moving fine or granular materials, such as powders, grains, and pellets, over long distances. Pneumatic conveyors are widely used in the chemical, pharmaceutical, and food processing industries for tasks such as conveying raw materials, loading and unloading containers, and transferring products between processing stages.
- Vacuum Belt Conveyors: Vacuum belt conveyors use suction to hold materials securely on the belt, preventing them from shifting or falling off during transport. These conveyors are suitable for handling lightweight or delicate items that require precise positioning. Vacuum belt conveyors are commonly used in the electronics, printing, and packaging industries for tasks such as assembly, inspection, and packaging.
Applications of Conveyor Belt Systems
Conveyor belt systems are used in a variety of applications across different industries, each tailored to specific operational needs:
- Manufacturing: Conveyor belt systems are essential in manufacturing facilities for transporting raw materials, components, and finished products through various stages of production. They improve efficiency, reduce manual labor, and ensure a smooth and continuous workflow.
- Warehousing and Distribution: In warehousing and distribution centers, conveyor belt systems are used to move goods from receiving areas to storage, sorting, and shipping areas. They help streamline operations, increase throughput, and enhance order accuracy.
- Mining and Quarrying: Conveyor belt systems are used to transport bulk materials, such as ores, coal, and aggregates, from extraction sites to processing plants and storage facilities. They enable efficient and continuous material handling in harsh and demanding environments.
- Food and Beverage: Conveyor belt systems are widely used in the food and beverage industry for tasks such as processing, packaging, and transporting food products. They are designed to meet strict hygiene standards and ensure the safe handling of perishable goods.
- Automotive: In the automotive industry, conveyor belt systems are used to move car parts and assemblies through various production stages, including stamping, welding, painting, and final assembly. They improve production efficiency and ensure consistent quality.
- Recycling and Waste Management: Conveyor belt systems are used in recycling and waste management facilities to sort, separate, and transport recyclable materials and waste. They help optimize the recycling process and reduce manual sorting efforts.
- Pharmaceutical and Chemical: Conveyor belt systems are used in pharmaceutical and chemical industries to transport raw materials, intermediates, and finished products between processing stages. They ensure precise and contamination-free handling of sensitive materials.
Conveyor belt systems are versatile and essential components of material handling operations across various industries. By selecting the appropriate type of conveyor system for specific applications, businesses can enhance efficiency, productivity, and safety in their operations.
Conveyor Belt Rip Detection: Ensuring Safety
Methods and Technologies for Conveyor Belt Rip Detection and Preventing Accidents
Conveyor belt rip detection is a critical aspect of ensuring the safety and reliability of conveyor systems. Rips or tears in conveyor belts can lead to significant operational disruptions, equipment damage, and safety hazards. Implementing effective rip detection methods and technologies is essential for preventing accidents and maintaining efficient operations. Here are some common methods and technologies for conveyor belt rip detection:
- Embedded Sensor Systems: Embedded sensor systems involve integrating sensors directly into the conveyor belt during the manufacturing process. These sensors detect rips or tears by monitoring changes in the belt’s integrity and structure. When a rip is detected, the sensors send signals to the conveyor monitoring system, triggering alerts or automatic shutdowns. Embedded sensor systems provide real-time detection and are highly effective in preventing extensive damage.
- Inductive Loop Systems: Inductive loop systems use inductive loops embedded in the conveyor belt to detect rips or tears. These loops create a continuous electrical circuit that is monitored by the conveyor monitoring system. When a rip occurs, the circuit is broken, and the system detects the interruption. Inductive loop systems are reliable and provide immediate detection of belt rips, allowing for prompt intervention.
- Ultrasonic Detection Systems: Ultrasonic detection systems use ultrasonic waves to monitor the condition of the conveyor belt. Ultrasonic sensors emit high-frequency sound waves that travel through the belt and reflect back to the sensor. Changes in the reflected waves indicate the presence of rips or tears. Ultrasonic detection systems are non-invasive and provide accurate detection of belt damage, ensuring timely maintenance.
- Optical Detection Systems: Optical detection systems use cameras and optical sensors to visually monitor the conveyor belt for rips or tears. These systems capture continuous images of the belt surface and analyze them for signs of damage. When a rip is detected, the system generates alerts for immediate action. Optical detection systems are effective for detecting surface damage and can be integrated with other monitoring technologies for comprehensive belt monitoring.
- Acoustic Emission Systems: Acoustic emission systems use acoustic sensors to detect the sound waves generated by rips or tears in the conveyor belt. These sensors monitor the acoustic signals produced by the belt during operation and identify anomalies that indicate damage. Acoustic emission systems provide real-time detection and can be used in conjunction with other methods for enhanced reliability.
- Magnetic Detection Systems: Magnetic detection systems use magnetic sensors to monitor the integrity of the conveyor belt. These systems detect changes in the magnetic properties of the belt caused by rips or tears. Magnetic detection systems are effective for detecting damage in belts with embedded steel cords or other magnetic materials. They provide immediate detection and can trigger automatic shutdowns to prevent further damage.
- Infrared Detection Systems: Infrared detection systems use infrared sensors to monitor the temperature profile of the conveyor belt. Rips or tears can cause changes in the thermal characteristics of the belt, which are detected by the infrared sensors. These systems provide non-contact detection and can identify damage that may not be visible to the naked eye. Infrared detection systems are effective for continuous monitoring and early detection of belt damage.
Preventing Accidents with Conveyor Belt Rip Detection
Implementing effective conveyor belt rip detection methods is essential for preventing accidents and ensuring the safety of conveyor operations. Here are some key strategies for preventing accidents with conveyor belt rip detection:
- Regular Inspections and Maintenance: Conduct regular inspections and maintenance of conveyor belts to identify and address potential issues before they lead to rips or tears. Regular maintenance helps ensure the integrity of the belt and extends its lifespan.
- Implementing Multiple Detection Methods: Use a combination of rip detection methods to enhance the reliability and accuracy of belt monitoring. Integrating multiple technologies, such as embedded sensors, optical detection, and acoustic emission systems, provides comprehensive coverage and ensures timely detection of damage.
- Automated Shutdowns and Alerts: Configure the conveyor monitoring system to trigger automated shutdowns and alerts when rips or tears are detected. Immediate shutdowns prevent further damage to the belt and reduce the risk of accidents. Alerts notify maintenance personnel to take prompt action.
- Training and Education: Provide training and education to conveyor operators and maintenance personnel on the importance of rip detection and the proper use of monitoring systems. Ensure that staff are familiar with detection methods, response procedures, and safety protocols.
- Data Analysis and Trend Monitoring: Analyze data collected from rip detection systems to identify patterns and trends. Trend monitoring helps predict potential issues and allows for proactive maintenance. Use historical data to improve detection accuracy and optimize maintenance schedules.
- Continuous Improvement: Continuously evaluate and improve rip detection methods and technologies. Stay updated on the latest advancements in rip detection and implement new solutions as needed. Continuous improvement enhances the reliability and effectiveness of conveyor monitoring systems.
Conveyor belt rip detection is a critical component of conveyor monitoring system, ensuring the safety, reliability, and efficiency of conveyor operations. By implementing effective rip detection methods and technologies, businesses can prevent accidents, reduce downtime, and maintain the integrity of conveyor belts. Regular inspections, multiple detection methods, automated shutdowns, training, data analysis, and continuous improvement are key strategies for ensuring effective rip detection and preventing accidents.
FAQs about Conveyor Monitoring System
Conveyor systems rely on various sensors to monitor and control the movement of materials, ensuring efficient and safe operations. Here are some common sensors used in conveyor systems:
Proximity Sensors: These sensors detect the presence or absence of objects on the conveyor belt without direct contact. They are used to start or stop the conveyor, count items, and ensure that materials are correctly positioned. Proximity sensors can be inductive, capacitive, or photoelectric, depending on the application.
Photoelectric Sensors: These sensors use a light beam to detect the presence or absence of objects. When an object interrupts the light beam, the sensor triggers an action, such as stopping the conveyor or diverting items. Photoelectric sensors are widely used for object detection, counting, and positioning.
Weight Sensors (Load Cells): Weight sensors measure the weight of materials on the conveyor belt. They are used to ensure that the conveyor is not overloaded and to monitor the weight of individual items or bulk materials. This helps maintain accurate inventory and prevent equipment damage.
Speed Sensors: Speed sensors monitor the speed of the conveyor belt to ensure it operates within the desired range. They help maintain consistent material flow and detect any deviations that could indicate mechanical issues or potential failures.
Belt Misalignment Sensors: These sensors detect when the conveyor belt is off-track or misaligned. They help prevent damage to the belt and other components by triggering an alarm or stopping the conveyor when misalignment is detected. This ensures smooth and efficient operation.
Temperature Sensors: Temperature sensors monitor the temperature of the conveyor belt and surrounding environment. They are crucial in applications where materials are heated or where the conveyor operates in extreme temperatures. These sensors help prevent overheating and ensure safe operation.
Level Sensors: Level sensors detect the level of materials in hoppers, bins, or on the conveyor belt. They help maintain optimal material flow and prevent overflows or shortages. Level sensors can be ultrasonic, capacitive, or radar-based, depending on the application.
Vibration Sensors: Vibration sensors monitor the vibration levels of the conveyor system. Excessive vibrations can indicate mechanical issues or potential failures. By detecting abnormal vibrations, these sensors help prevent damage and ensure smooth operation.
By using these sensors, conveyor systems can achieve greater efficiency, safety, and reliability, ensuring smooth and uninterrupted material handling operations.
Tracking a conveyor belt is essential for maintaining efficient operation and preventing damage. Proper tracking ensures that the belt runs straight and true along the conveyor system without drifting off course. Here are some best practices for tracking a conveyor belt:
Inspect and Align the Conveyor Frame: The first step in tracking a conveyor belt is to ensure that the conveyor frame is level and square. Any misalignment in the frame can cause the belt to drift. Use a level and measuring tools to check the alignment and make necessary adjustments to the frame and support structures.
Check Pulley Alignment: Misaligned pulleys are a common cause of belt tracking issues. Ensure that all pulleys are aligned parallel to each other and perpendicular to the conveyor frame. Use a straightedge or laser alignment tool to verify pulley alignment and make adjustments as needed.
Adjust Tension: Proper belt tension is crucial for accurate tracking. If the belt is too loose, it can drift off course; if it is too tight, it can cause excessive wear and strain on the conveyor components. Adjust the tensioning mechanism to achieve the correct tension, ensuring the belt is taut but not overly tight.
Install Tracking Devices: Tracking devices, such as crowned pulleys, guide rollers, and edge guides, help keep the belt centered on the conveyor. Crowned pulleys have a slightly curved surface that naturally guides the belt toward the center. Guide rollers and edge guides provide additional support to keep the belt aligned.
Regular Maintenance and Inspection: Regular maintenance and inspection are essential for preventing tracking issues. Inspect the belt, pulleys, and other components for signs of wear, damage, or misalignment. Clean the conveyor system to remove any debris that could affect tracking. Perform routine checks and adjustments to maintain proper alignment and tension.
Use Automatic Tracking Systems: Automatic tracking systems use sensors and actuators to continuously monitor and adjust the belt’s position. These systems can detect misalignment and make real-time adjustments to keep the belt centered. Automatic tracking systems are especially useful in complex or high-speed conveyor applications.
Train and Educate Operators: Proper training and education for conveyor operators are crucial for maintaining accurate belt tracking. Ensure that operators understand the importance of belt tracking and know how to perform basic inspections and adjustments. Provide guidelines and procedures for addressing tracking issues.
Conveyor systems use various types of control systems to manage their operation, ensuring efficient and reliable material handling. The choice of control system depends on the complexity and requirements of the specific application. Here are some common types of control systems used in conveyor systems:
Programmable Logic Controllers (PLCs): PLCs are widely used in conveyor systems due to their flexibility, reliability, and ease of programming. A PLC can control multiple conveyor functions, such as starting and stopping the belt, adjusting speed, and managing sensors and actuators. PLCs can be easily reprogrammed to accommodate changes in the conveyor system or production process, making them ideal for dynamic and complex operations.
Human-Machine Interface (HMI): HMIs provide a user-friendly interface for operators to monitor and control the conveyor system. An HMI typically includes a touchscreen display that shows real-time data, such as conveyor speed, load, and status of sensors and actuators. Operators can use the HMI to make adjustments, troubleshoot issues, and perform maintenance tasks. HMIs enhance the usability and accessibility of the control system.
Supervisory Control and Data Acquisition (SCADA): SCADA systems are used for monitoring and controlling large and complex conveyor systems. SCADA integrates with PLCs and HMIs to provide centralized control and data acquisition. It allows operators to monitor multiple conveyors from a single interface, collect data for analysis, and automate decision-making processes. SCADA systems are commonly used in industries such as mining, manufacturing, and logistics.
Variable Frequency Drives (VFDs): VFDs control the speed and direction of conveyor motors by varying the frequency and voltage supplied to the motor. VFDs provide precise control over conveyor speed, allowing for smooth acceleration and deceleration. They also improve energy efficiency and reduce mechanical stress on the conveyor components. VFDs are often used in conjunction with PLCs and HMIs for advanced control.
Distributed Control Systems (DCS): DCSs are used in large-scale industrial applications where multiple conveyor systems need to be controlled and coordinated. A DCS distributes control functions across multiple controllers, each responsible for a specific part of the conveyor system. This decentralized approach enhances system reliability, scalability, and redundancy. DCSs are commonly used in process industries such as chemical, oil and gas, and power generation.
Embedded Controllers: Embedded controllers are dedicated control units integrated into the conveyor system. These controllers are designed for specific applications and provide real-time control and monitoring. Embedded controllers are often used in simpler conveyor systems where basic control functions are required.
Custom Control Systems: In some cases, custom control systems are developed to meet the unique requirements of a conveyor application. These systems may combine elements of PLCs, HMIs, SCADA, and other control technologies to provide tailored solutions. Custom control systems are designed to optimize performance, enhance flexibility, and address specific operational challenges.
Conveyor tracking is the process of ensuring that the conveyor belt remains properly aligned and centered on the pulleys and rollers, preventing misalignment, damage, and operational disruptions. Proper tracking is essential for the efficient and reliable operation of conveyor systems. Here’s how conveyor tracking works:
Initial Setup and Alignment: Proper tracking begins with the initial setup and alignment of the conveyor system. The conveyor frame, pulleys, and rollers must be installed level and square to ensure that the belt runs straight. During installation, precise measurements and alignment tools, such as laser levels and straightedges, are used to verify the correct positioning of components.
Belt Tensioning: Maintaining the correct tension on the conveyor belt is crucial for tracking. If the belt is too loose, it can drift off course; if it is too tight, it can cause excessive wear and strain on the components. Adjustable take-up units or automatic tensioning systems are used to maintain the appropriate tension, ensuring the belt remains taut and properly aligned.
Tracking Devices: Various tracking devices are used to keep the conveyor belt centered. These include:
Crowned Pulleys: Crowned pulleys have a slightly curved surface that naturally guides the belt toward the center. The curvature creates a self-centering effect, helping to keep the belt aligned.
Guide Rollers: Guide rollers are installed along the sides of the conveyor to provide additional support and alignment. They help prevent the belt from drifting sideways and maintain proper tracking.
Edge Guides: Edge guides are fixed barriers or rollers placed along the edges of the belt. They help keep the belt within its intended path and prevent misalignment.
Continuous Monitoring: Sensors and monitoring systems continuously track the position and alignment of the conveyor belt. Belt misalignment sensors detect any deviation from the center and trigger corrective actions, such as adjusting the tension or realigning the belt. These sensors provide real-time feedback, allowing for immediate intervention and preventing potential issues.
Automatic Tracking Systems: Advanced conveyor systems may include automatic tracking systems that use sensors and actuators to maintain proper alignment. These systems continuously monitor the belt’s position and make real-time adjustments to keep it centered. Automatic tracking systems are particularly useful in high-speed or complex conveyor applications where manual adjustments are impractical.
Regular Maintenance and Inspection: Regular maintenance and inspection are essential for ensuring proper conveyor tracking. Maintenance tasks include checking the alignment of the frame and pulleys, adjusting tension, cleaning the conveyor system, and inspecting components for wear and damage. Routine inspections help identify and address tracking issues before they lead to significant problems.
Operator Training: Proper training and education for conveyor operators are crucial for maintaining accurate tracking. Operators should understand the importance of belt tracking and be familiar with basic inspection and adjustment procedures. Providing guidelines and procedures for addressing tracking issues ensures that operators can quickly and effectively resolve any problems.
Last Updated on June 4, 2024 by Jordan Smith
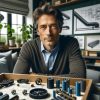
Jordan Smith, a seasoned professional with over 20 years of experience in the conveyor system industry. Jordan’s expertise lies in providing comprehensive solutions for conveyor rollers, belts, and accessories, catering to a wide range of industrial needs. From initial design and configuration to installation and meticulous troubleshooting, Jordan is adept at handling all aspects of conveyor system management. Whether you’re looking to upgrade your production line with efficient conveyor belts, require custom conveyor rollers for specific operations, or need expert advice on selecting the right conveyor accessories for your facility, Jordan is your reliable consultant. For any inquiries or assistance with conveyor system optimization, Jordan is available to share his wealth of knowledge and experience. Feel free to reach out at any time for professional guidance on all matters related to conveyor rollers, belts, and accessories.