Conveyor Pulley Lagging Material Options for Various Applications
Conveyor pulley lagging material is essential for the efficient operation of conveyor systems. This material, applied to the surface of conveyor pulleys, plays a crucial role in enhancing the friction between the pulley and the conveyor belt. By improving grip, conveyor pulley lagging material significantly reduces slippage, which in turn minimizes wear and tear on both the belt and the pulley. This protection extends the lifespan of the conveyor components, ensuring smoother and more reliable operations. Moreover, the right conveyor pulley lagging material helps in distributing load evenly across the belt, reducing the risk of system failures and downtime, thus enhancing the overall efficiency of conveyor systems.
Conveyor Pulley Lagging Material: Comprehensive Guide
When it comes to the efficient operation of conveyor systems, selecting the right conveyor pulley lagging material is paramount. Lagging is the layer of material that is bonded to the shell of a conveyor pulley. This layer serves several purposes, such as increasing the friction between the belt and the pulley, providing a cushioning effect, and protecting the pulley from wear and tear. Here, we delve into the different types of pulley lagging materials and the key factors that should guide your choice for specific applications.
Types of Pulley Lagging
Pulley lagging materials come in various types, each designed to address specific operational requirements and environmental conditions. The primary types of conveyor pulley lagging material include rubber, ceramic, and polyurethane. Each type offers distinct advantages and is suited for different types of conveyor systems.
Rubber Lagging
Rubber lagging is one of the most commonly used types of conveyor pulley lagging material due to its versatility and cost-effectiveness. It can be applied in various thicknesses and patterns, including plain, diamond, and chevron patterns.
- Plain Rubber Lagging: Ideal for general applications where the primary goal is to increase friction and reduce slippage. It’s often used in environments with moderate stress and normal operating conditions.
- Diamond Pattern Rubber Lagging: This type is designed to enhance grip and facilitate water shedding, making it suitable for outdoor applications or environments where water or moisture is present.
- Chevron Pattern Rubber Lagging: Known for its excellent traction capabilities, chevron-patterned rubber lagging is used in heavy-duty applications where high torque and significant belt movement are common.
Ceramic Lagging
Ceramic lagging offers superior wear resistance and increased grip compared to rubber lagging. This type of conveyor pulley lagging material is especially beneficial in harsh environments with high abrasion and where longer service life is required. Ceramic lagging is typically available in two forms:
- Plain Ceramic Lagging: Provides enhanced wear resistance and is ideal for applications with abrasive materials or where the conveyor system operates at high speeds and under high tension.
- Rubber-Ceramic Lagging: This hybrid lagging combines the benefits of rubber and ceramic, offering both cushioning and exceptional grip. It is suitable for heavy-duty applications, such as mining and bulk material handling, where both abrasion resistance and high friction are necessary.
Polyurethane Lagging
Polyurethane lagging is known for its excellent chemical resistance, making it suitable for applications involving exposure to oils, solvents, and chemicals. This type of conveyor pulley lagging material is also appreciated for its durability and ability to maintain performance in extreme temperature conditions.
- Solid Polyurethane Lagging: Ideal for applications requiring a combination of wear resistance and chemical resistance. It’s often used in industries like food processing and chemical manufacturing.
- Profiled Polyurethane Lagging: Designed with specific patterns to enhance grip and facilitate material shedding. This type is used in specialized applications where a high level of customization is needed to meet operational requirements.
Key Factors in Choosing the Appropriate Type for Specific Applications
Selecting the right conveyor pulley lagging material involves considering several critical factors to ensure optimal performance and longevity of the conveyor system. Here are some key factors to guide your decision:
Operational Environment
The environment in which the conveyor operates plays a significant role in determining the appropriate lagging material. For instance, rubber lagging is suitable for general indoor environments, while ceramic lagging is preferred in harsh, abrasive environments. Polyurethane lagging is the best choice for chemically aggressive settings.
Material Being Conveyed
The type of material being transported on the conveyor belt affects the choice of lagging material. Abrasive materials like coal, ore, and minerals necessitate the use of ceramic lagging due to its superior wear resistance. For materials that can cause chemical degradation, polyurethane lagging is ideal.
Conveyor System Load and Speed
The load and speed of the conveyor system influence the choice of conveyor pulley lagging material. High-speed, high-tension systems benefit from the enhanced grip and wear resistance of ceramic lagging. In contrast, rubber lagging is sufficient for systems with moderate loads and speeds.
Maintenance and Durability Requirements
Maintenance intervals and the desired durability of the lagging material should also be considered. Ceramic lagging, though more expensive initially, offers longer service life and reduces downtime due to its durability. Rubber lagging, while less durable, is cost-effective and easier to replace, making it suitable for systems where frequent maintenance is not an issue.
Environmental Conditions
Factors such as temperature, moisture, and exposure to chemicals must be taken into account. Polyurethane lagging excels in extreme temperature conditions and where chemical resistance is necessary. Rubber lagging is versatile but may not perform well under severe environmental stress.
Cost Considerations
Budget constraints often play a crucial role in the selection process. While ceramic lagging offers the best performance in harsh conditions, it is also the most expensive. Rubber lagging provides a cost-effective solution for less demanding environments, and polyurethane lagging sits in the middle with a balance of cost and performance.
Installation and Bonding Techniques
The ease of installation and the bonding techniques required for each type of lagging material can also influence the decision. Rubber lagging can be easily bonded using adhesives, while ceramic lagging often requires more complex bonding techniques. Polyurethane lagging may require specialized installation processes depending on the application.
By understanding these types and factors, businesses can make informed decisions when selecting the appropriate conveyor pulley lagging material for their specific needs. Whether the goal is to enhance grip, reduce wear and tear, or resist chemical degradation, choosing the right lagging material is crucial for the efficiency and longevity of conveyor systems.
Conveyor Pulley Lagging Material: An In-depth Look at Ceramic Pulley Lagging
The selection of appropriate conveyor pulley lagging material is critical to ensuring the efficiency, longevity, and reliability of conveyor systems. One of the most robust solutions available is ceramic pulley lagging, which is particularly well-suited for harsh and abrasive conditions. This section explores the unique properties of ceramic pulley lagging and delves into its two main types: dimple ceramic lagging and smooth ceramic lagging.
Ceramic Pulley Lagging
Ceramic pulley lagging stands out as a superior choice for environments that demand exceptional durability and resistance to wear. This type of conveyor pulley lagging material is specifically engineered to withstand the rigors of heavy-duty operations, offering significant advantages over traditional rubber or polyurethane lagging.
Designed for Harsh, Abrasive Conditions
Ceramic pulley lagging is designed to perform optimally in harsh, abrasive conditions where other materials might fail. Industries such as mining, quarrying, and bulk material handling often encounter extreme wear and tear, which can lead to frequent maintenance and downtime. Ceramic lagging addresses these challenges by providing enhanced wear resistance, thus extending the service life of both the pulley and the conveyor belt.
The ceramic tiles embedded in the lagging material create a tough, wear-resistant surface that can handle the continuous impact and abrasion from heavy, coarse materials. This not only reduces the frequency of replacements but also minimizes the overall maintenance costs associated with conveyor system operations.
Types of Ceramic Pulley Lagging
Ceramic pulley lagging comes in two primary types, each designed to cater to specific operational needs and conditions. Understanding the differences between dimple ceramic lagging and smooth ceramic lagging can help in selecting the right conveyor pulley lagging material for your application.
Dimple Ceramic Lagging
Dimple ceramic lagging is characterized by its surface, which is covered with small, raised dimples or studs. These dimples significantly increase the friction between the pulley and the conveyor belt, enhancing grip and reducing slippage. This type of lagging is particularly suitable for drive pulleys, where maintaining consistent traction is crucial for efficient operation.
- High Friction and Grip: The dimpled surface provides superior grip, making it ideal for drive pulleys that are responsible for moving the conveyor belt. The increased friction ensures that the belt does not slip, even under heavy loads or in wet conditions.
- Suitable for Drive Pulleys: Drive pulleys require a high level of traction to effectively transmit power to the conveyor belt. Dimple ceramic lagging excels in this role, providing the necessary friction to maintain smooth and reliable operation. This is especially important in applications where the conveyor must start and stop frequently or where it handles varying loads.
In addition to its functional benefits, dimple ceramic lagging also contributes to the overall safety of the conveyor system by preventing unexpected belt slippage, which can lead to operational disruptions and potential hazards.
Smooth Ceramic Lagging
Smooth ceramic lagging, as the name suggests, features a smooth surface without the raised dimples. This type of lagging offers a balanced solution for non-drive pulleys, where the primary goals are to reduce belt wear and ensure steady operation.
- Balanced Solution for Non-Drive Pulleys: Smooth ceramic lagging provides adequate grip while minimizing wear and tear on the conveyor belt. This makes it an excellent choice for non-drive pulleys, which support the belt without the need for high friction levels.
- Reducing Belt Wear: The smooth surface of this lagging type helps to reduce the abrasion and wear on the conveyor belt, extending its service life. This is particularly important in systems that transport abrasive materials, as it helps to maintain the integrity of the belt over time.
Smooth ceramic lagging also offers the advantage of easier cleaning and maintenance. The absence of dimples means there are fewer places for material build-up, reducing the risk of contamination and making routine maintenance more straightforward.
What is Conveyor Pulley Lagging Material
When discussing conveyor pulley systems, one crucial component to consider is the conveyor pulley lagging material. The lagging material plays a significant role in enhancing the performance and longevity of the pulley by providing better traction and reducing belt slippage. Various materials are used for lagging, with rubber lagging being one of the most common and cost-effective choices.
Rubber Lagging Pulley
Rubber lagging is a popular choice for conveyor pulley lagging material due to its versatility and cost-effectiveness. It comes in different thicknesses, hardness levels, and groove patterns, catering to various operational requirements. Here, we will explore the primary types of rubber lagging pulley materials and their specific applications.
Plain Rubber Lagging
Plain rubber lagging is often used for non-drive pulleys. It is designed to offer moderate traction, making it suitable for applications where high friction is not a critical requirement. This type of lagging is generally smooth and does not have any grooves or patterns.
Advantages of Plain Rubber Lagging:
- Cost-Effective: Plain rubber lagging is typically more affordable compared to other types of lagging materials, making it a cost-effective option for many industries.
- Easy Installation: Due to its smooth surface, plain rubber lagging is easier to install and maintain, reducing downtime during maintenance.
- Moderate Traction: It provides sufficient traction for non-drive pulleys, ensuring smooth and efficient operation without excessive belt wear.
Plain rubber lagging is particularly advantageous in environments where the conveyor system does not face extreme conditions or where additional traction is unnecessary.
Grooved Rubber Lagging
Grooved rubber lagging is designed to meet higher friction requirements and improve the overall efficiency of the conveyor system. There are various groove patterns available, each serving different purposes:
Diamond Grooved Rubber Lagging
Diamond grooved rubber lagging features a diamond-shaped pattern, which enhances the grip and flexibility of the conveyor pulley lagging material. This type of lagging is ideal for applications requiring increased traction and reduced belt slippage.
Benefits of Diamond Grooved Rubber Lagging:
- Enhanced Grip: The diamond pattern provides excellent grip, preventing belt slippage and ensuring efficient power transmission.
- Flexibility: The grooves allow the lagging to flex, accommodating minor misalignments and irregularities in the pulley surface.
- Water-Shedding Capabilities: The diamond grooves facilitate water shedding, making this lagging suitable for wet or damp environments.
Herringbone Grooved Rubber Lagging
Herringbone grooved rubber lagging features a V-shaped pattern, also known as herringbone, which directs water and debris away from the pulley surface. This design is particularly effective in maintaining traction in wet conditions.
Advantages of Herringbone Grooved Rubber Lagging:
- Optimal Water Shedding: The herringbone pattern efficiently channels water and debris off the pulley surface, preventing slippage and maintaining traction.
- Improved Flexibility: Similar to diamond grooves, the herringbone pattern allows for better flexibility, adapting to the pulley’s surface irregularities.
- Versatility: This type of lagging is versatile and can be used in various applications, from light to heavy-duty conveyor systems.
Chevron Grooved Rubber Lagging
Chevron grooved rubber lagging features a chevron or V-shaped pattern similar to herringbone but typically with a steeper angle. This pattern enhances traction and is particularly useful in high-tension conveyor systems.
Benefits of Chevron Grooved Rubber Lagging:
- Increased Traction: The steep angle of the chevron pattern provides superior grip, reducing belt slippage and enhancing power transmission.
- Effective Water Shedding: Like herringbone and diamond patterns, chevron grooves are effective at shedding water and debris, maintaining optimal pulley performance.
- High-Tension Applications: Chevron grooved rubber lagging is well-suited for high-tension applications where maximum traction is essential.
Considerations for Choosing Conveyor Pulley Lagging Material
Selecting the appropriate conveyor pulley lagging material is crucial for ensuring the efficiency and longevity of the conveyor system. Factors to consider include:
- Operational Environment: The environmental conditions, such as wet or dry, hot or cold, will influence the choice of lagging material and groove pattern.
- Load and Tension: The type of material and groove pattern selected should match the load and tension requirements of the conveyor system.
- Maintenance and Cost: Consider the ease of installation and maintenance, as well as the overall cost-effectiveness of the lagging material.
How about Conveyor Pulley Lagging Material
When discussing conveyor pulley systems, one crucial component to consider is the conveyor pulley lagging material. The lagging material plays a significant role in enhancing the performance and longevity of the pulley by providing better traction and reducing belt slippage. Among the various materials used for lagging, rubber is one of the most common and cost-effective choices.
Rubber Lagging for Conveyor Pulley
Rubber lagging is a popular choice for conveyor pulley lagging material due to its versatility, durability, and cost-effectiveness. This section delves into the properties, advantages, application techniques, and the impact of rubber lagging on conveyor system performance and maintenance.
Properties and Advantages of Rubber Lagging
Rubber lagging provides numerous benefits that make it an ideal choice for conveyor pulley lagging material. Its properties include high elasticity, excellent abrasion resistance, and good tensile strength. These characteristics help in reducing wear and tear on the conveyor belt and pulley, extending their lifespan and improving overall system efficiency.
Advantages of Rubber Lagging:
- Enhanced Traction and Grip:
Rubber lagging significantly improves the traction between the pulley and the conveyor belt. This enhanced grip reduces the chances of belt slippage, ensuring smoother and more efficient operation. - Increased Durability:
The abrasion-resistant properties of rubber lagging help in withstanding the harsh conditions of various industrial environments. This durability results in longer service life for the pulley and belt. - Shock Absorption:
Rubber lagging absorbs shocks and vibrations, reducing the stress on the conveyor system components. This absorption capability is particularly beneficial in heavy-duty applications where the conveyor system is subjected to continuous impact loads. - Noise Reduction:
The use of rubber lagging can significantly reduce the noise generated by the conveyor system. The soft and elastic nature of rubber helps in dampening the sound, creating a quieter working environment. - Cost-Effectiveness:
Rubber lagging is relatively inexpensive compared to other lagging materials. Its long-lasting nature and ease of maintenance contribute to lower operational costs over time.
Application Techniques for Rubber Lagging
Several techniques are employed to apply rubber lagging to conveyor pulleys, including cold bonding, vulcanizing, and grooving. Each method has its advantages and is suitable for different operational requirements.
Cold Bonding
Cold bonding is a commonly used technique for applying rubber lagging. This method involves the use of adhesives to bond the rubber lagging onto the pulley surface without the need for heat. The process is straightforward and cost-effective, making it suitable for many industrial applications.
Advantages of Cold Bonding:
- Ease of Application: The cold bonding process is relatively simple and can be performed on-site, minimizing downtime.
- Cost-Effective: Since it does not require specialized equipment or heat, cold bonding is a cost-effective method.
- Versatility: Cold bonding can be used for a wide range of pulley sizes and types, making it a versatile option.
Vulcanizing
Vulcanizing is another technique used for applying rubber lagging. This method involves the use of heat and pressure to bond the rubber lagging onto the pulley surface. Vulcanizing creates a strong and durable bond, making it suitable for high-tension and heavy-duty applications.
Advantages of Vulcanizing:
- Strong Bond: The heat and pressure used in vulcanizing create a robust and long-lasting bond between the rubber lagging and the pulley.
- High Durability: Vulcanized rubber lagging is highly durable and can withstand extreme conditions, making it ideal for heavy-duty conveyor systems.
- Improved Performance: The strong bond ensures that the rubber lagging remains securely attached, providing consistent performance and reduced maintenance needs.
Grooving
Grooving involves creating patterns or grooves on the surface of the rubber lagging to enhance its traction and water-shedding capabilities. There are various groove patterns, such as diamond, herringbone, and chevron, each serving different purposes.
Advantages of Grooving:
- Enhanced Traction: Grooved patterns improve the grip between the conveyor belt and the pulley, reducing slippage and enhancing efficiency.
- Water-Shedding: Grooves help in directing water and debris away from the pulley surface, maintaining optimal performance even in wet conditions.
- Customized Solutions: Grooving allows for customization based on specific operational needs, providing tailored solutions for different applications.
Impact on Conveyor System Performance and Maintenance
The use of rubber lagging as a conveyor pulley lagging material has a significant impact on the performance and maintenance of conveyor systems. By providing enhanced traction, reducing wear and tear, and improving overall system efficiency, rubber lagging contributes to the reliable and cost-effective operation of conveyor systems.
Performance Enhancement
Reduced Belt Slippage:
The improved traction provided by rubber lagging minimizes belt slippage, ensuring smooth and efficient power transmission. This reduction in slippage helps in maintaining consistent operational speeds and reduces the risk of downtime.
Increased Power Transmission:
The enhanced grip between the pulley and the conveyor belt allows for better power transmission, improving the overall efficiency of the conveyor system. This increased efficiency can lead to higher productivity and reduced energy consumption.
Improved Belt Tracking:
Rubber lagging helps in maintaining proper belt tracking, preventing misalignment and potential damage to the belt and pulley. Proper tracking ensures that the belt runs smoothly and reduces the need for frequent adjustments.
Maintenance Benefits
Extended Service Life:
The durability and abrasion resistance of rubber lagging extend the service life of both the conveyor belt and the pulley. This longevity reduces the frequency of replacements and lowers maintenance costs over time.
Reduced Maintenance Requirements:
Rubber lagging’s shock absorption and noise reduction properties decrease the stress on conveyor system components, resulting in fewer breakdowns and maintenance needs. This reduction in maintenance requirements translates to lower operational costs and increased uptime.
Easy Replacement and Repair:
Rubber lagging can be easily replaced or repaired when necessary. Techniques like cold bonding and vulcanizing allow for quick and efficient application, minimizing downtime during maintenance activities.
Conveyor Pulley Lagging Material: Installation Guide
Proper installation of conveyor pulley lagging material is essential for ensuring the longevity and efficiency of your conveyor system. This guide provides a detailed, step-by-step procedure for installing pulley lagging, covering preparation, bonding, and curing processes. Additionally, it highlights best practices to ensure optimal lagging performance.
Pulley Lagging Procedure PDF
For those seeking an in-depth, visual guide, a pulley lagging procedure PDF can be invaluable. This document should provide clear, illustrated instructions and safety guidelines to help installers execute the process correctly.
Step-by-Step Guide to Installing Pulley Lagging
The installation process of conveyor pulley lagging material involves several crucial steps that must be followed meticulously to achieve the best results. Here is a comprehensive step-by-step guide:
- Preparation
- Safety First: Ensure all safety protocols are in place. Wear appropriate personal protective equipment (PPE) including gloves, goggles, and respiratory masks.
- Surface Cleaning: Clean the pulley surface thoroughly to remove any dirt, rust, or residue. Use a wire brush or grinder to achieve a smooth, clean surface.
- Measurement and Cutting: Measure the pulley circumference and width accurately. Cut the lagging material to the required dimensions, allowing for any necessary overlap.
- Bonding Process
- Adhesive Application: Apply a suitable adhesive to both the pulley surface and the back of the lagging material. Use a brush or roller to ensure even coverage. It’s important to follow the manufacturer’s guidelines regarding adhesive type and application method.
- Lagging Application: Start at one end of the pulley and carefully apply the lagging material, pressing it firmly into place. Ensure there are no air bubbles or gaps between the pulley surface and the lagging.
- Rolling and Pressing: Use a hand roller to press the lagging material firmly against the pulley. This helps to achieve a strong bond and eliminate any air pockets. Apply even pressure across the entire surface.
- Curing Process
- Initial Curing: Allow the adhesive to set for the recommended initial curing time. This can vary depending on the adhesive used, so refer to the manufacturer’s instructions.
- Final Curing: After the initial set time, allow the lagging to cure fully. This process ensures the adhesive bond reaches its maximum strength. Final curing times can range from a few hours to several days, depending on environmental conditions and adhesive specifications.
Best Practices for Ensuring Optimal Lagging Performance
To ensure the best performance and longevity of your conveyor pulley lagging material, it’s crucial to follow these best practices:
Environmental Control
- Temperature and Humidity: Perform the installation in a controlled environment where temperature and humidity levels are within the recommended range. Extreme conditions can affect adhesive performance and curing times.
- Clean Workspace: Maintain a clean and organized workspace to prevent contamination of the adhesive or lagging material. Dust, oil, and other contaminants can weaken the bond and reduce the effectiveness of the lagging.
Proper Adhesive Selection
- Compatibility: Use an adhesive that is compatible with both the pulley material and the lagging material. Different materials may require specific types of adhesives to achieve a strong bond.
- Quality Adhesives: Invest in high-quality adhesives that are known for their performance and durability. Cutting costs on adhesives can lead to premature failures and increased maintenance costs.
Precision in Application
- Even Adhesive Layer: Apply the adhesive in a thin, even layer to both surfaces. Thick or uneven layers can create weak spots and compromise the bond.
- Alignment: Ensure the lagging material is aligned correctly before pressing it onto the pulley. Misalignment can lead to uneven wear and reduced effectiveness.
Regular Inspection and Maintenance
- Routine Checks: Conduct regular inspections of the pulley lagging to identify any signs of wear, detachment, or damage. Early detection of issues can prevent more significant problems and costly downtime.
- Maintenance Schedule: Implement a maintenance schedule that includes periodic reapplication of adhesive or replacement of worn lagging. Consistent maintenance ensures continuous optimal performance.
Training and Expertise
- Skilled Installers: Ensure that personnel involved in the installation are properly trained and experienced. Skilled installers can accurately follow procedures and make adjustments as needed to accommodate specific conditions.
- Ongoing Training: Provide ongoing training to keep installers updated on new techniques, materials, and best practices. Continuous improvement in skills and knowledge leads to better installation outcomes.
Using Appropriate Tools
- Correct Tools: Utilize tools that are specifically designed for lagging installation. Hand rollers, adhesive applicators, and cutting tools should be of high quality and in good condition.
- Tool Maintenance: Regularly inspect and maintain tools to ensure they are functioning correctly. Faulty tools can lead to poor installation quality and potential safety hazards.
Documenting the Process
- Installation Records: Keep detailed records of each installation, including measurements, adhesive types, curing times, and any issues encountered. This documentation can be valuable for future reference and quality control.
- Photographic Evidence: Take photographs of the installation process and the final result. Visual records can help in diagnosing issues and improving future installations.
By adhering to these detailed procedures and best practices, you can maximize the performance and lifespan of your conveyor pulley lagging material. Proper installation not only enhances the efficiency of the conveyor system but also minimizes downtime and maintenance costs, leading to more reliable and cost-effective operations.
Importance of Choosing the Right Conveyor Pulley Lagging Material
Choosing the appropriate conveyor pulley lagging material is crucial for the efficient operation and longevity of conveyor systems. The selection process involves understanding various factors that influence the performance of the lagging material, considering specific application requirements and environmental conditions, and recognizing the benefits of proper lagging in enhancing system efficiency and durability.
Factors Influencing the Selection of Lagging Material
Several factors must be considered when selecting the right conveyor pulley lagging material. These factors ensure that the chosen material meets the operational demands and provides optimal performance.
Operational Load and Tension
The load and tension that the conveyor system will be subjected to play a significant role in determining the appropriate lagging material. High-tension applications require lagging materials with excellent grip and durability to withstand the stress without deteriorating quickly.
Considerations:
- High-Tension Applications: For systems with high load and tension, materials like vulcanized rubber or ceramic lagging are preferable due to their superior strength and durability.
- Low to Moderate Tension Applications: In less demanding environments, plain rubber lagging or other cost-effective materials may suffice, providing adequate traction and longevity.
Environmental Conditions
The working environment of the conveyor system significantly impacts the choice of lagging material. Factors such as temperature, moisture, and exposure to chemicals can affect the performance and lifespan of the lagging.
Considerations:
- Wet Conditions: Grooved rubber lagging, such as diamond or herringbone patterns, is ideal for wet environments as it provides excellent water-shedding capabilities, maintaining traction and preventing slippage.
- High-Temperature Environments: Heat-resistant lagging materials are essential for conveyor systems operating in high-temperature conditions to prevent degradation and ensure consistent performance.
- Chemical Exposure: In environments where the lagging material is exposed to harsh chemicals, choosing a chemically resistant material is crucial to avoid rapid wear and tear.
Material Compatibility
The compatibility of the lagging material with the conveyor belt material is another important factor. Incompatible materials can lead to increased wear, reduced efficiency, and potential damage to the conveyor system.
Considerations:
- Rubber-to-Rubber Compatibility: Rubber lagging is often compatible with rubber conveyor belts, providing a good balance of grip and durability.
- Specialized Materials: For conveyor belts made from specialized materials, it is important to select lagging materials that offer similar properties and compatibility to prevent premature wear and system failure.
Considerations for Specific Applications and Environments
Different industries and applications have unique requirements for conveyor pulley lagging material. Understanding these specific needs helps in selecting the most suitable lagging to ensure optimal performance.
Mining and Heavy Industry
In mining and heavy industry applications, conveyor systems often handle abrasive materials and operate under high-stress conditions. The lagging material must be highly durable and capable of withstanding continuous impact and wear.
Considerations:
- Abrasion Resistance: Rubber lagging with high abrasion resistance is essential to prevent rapid wear and extend the service life of the pulley and belt.
- Impact Absorption: Materials that can absorb shock and impact help in reducing the stress on the conveyor components, enhancing system reliability.
Food and Pharmaceutical Industries
Conveyor systems in the food and pharmaceutical industries require lagging materials that meet strict hygiene and safety standards. These materials must be easy to clean and resistant to contamination.
Considerations:
- Hygienic Materials: FDA-approved rubber or synthetic lagging materials that resist bacterial growth and are easy to sanitize are ideal for these applications.
- Non-Toxicity: The lagging material should be non-toxic and safe for contact with food and pharmaceutical products.
High-Speed Conveyor Systems
High-speed conveyor systems require lagging materials that provide consistent grip and reduce vibration to maintain smooth operation and prevent belt slippage.
Considerations:
- Vibration Dampening: Rubber lagging with good vibration dampening properties helps in maintaining stability and reducing noise in high-speed applications.
- Consistent Traction: Grooved lagging patterns, such as chevron or diamond, provide reliable traction and minimize the risk of slippage at high speeds.
Enhancing Conveyor System Efficiency and Longevity Through Proper Lagging
Proper selection and application of conveyor pulley lagging material can significantly enhance the efficiency and longevity of conveyor systems. The right lagging material reduces maintenance requirements, prevents unexpected downtime, and ensures smooth and reliable operation.
Improved Traction and Power Transmission
By providing better traction, the appropriate lagging material ensures efficient power transmission between the pulley and the conveyor belt. This improvement leads to reduced energy consumption and increased operational efficiency.
Benefits:
- Reduced Slippage: Enhanced grip prevents belt slippage, maintaining consistent operational speeds and reducing wear on the belt and pulley.
- Energy Efficiency: Efficient power transmission reduces the energy required to operate the conveyor system, leading to cost savings.
Extended Service Life
Choosing the right lagging material can extend the service life of both the conveyor belt and the pulley by reducing wear and tear. This extension minimizes the need for frequent replacements and lowers maintenance costs.
Benefits:
- Durability: Durable lagging materials withstand harsh operating conditions, preventing premature wear and extending the lifespan of conveyor components.
- Cost Savings: Reduced maintenance and replacement costs contribute to overall cost savings and improved return on investment.
Maintenance and Downtime Reduction
Proper lagging material reduces the frequency and complexity of maintenance tasks, leading to fewer disruptions and increased productivity.
Benefits:
- Ease of Maintenance: Certain lagging materials, such as rubber, are easy to inspect and maintain, reducing downtime during maintenance activities.
- Reliability: Reliable lagging materials ensure consistent performance, minimizing the risk of unexpected breakdowns and production halts.
FAQS about Conveyor Pulley Lagging Material
Pulley lagging in conveyor systems refers to the application of a protective covering on the surface of conveyor pulleys. This covering, often made of rubber or ceramic materials, enhances the friction between the belt and the pulley, reducing slippage and improving traction. Pulley lagging is crucial in extending the life of the conveyor belt by providing a cushion that absorbs shocks and reduces wear and tear. It also helps in aligning the belt, preventing misalignment issues. Overall, pulley lagging improves the efficiency and reliability of conveyor systems, making them more effective in handling heavy loads.
Conveyor pulleys are typically constructed from high-strength materials such as steel or aluminum to withstand the heavy loads and harsh conditions of industrial environments. The surface of these pulleys can be covered with lagging materials like rubber, polyurethane, or ceramic to enhance performance. Steel is commonly used for its durability and resistance to wear and tear, while aluminum is chosen for its lightweight properties. The choice of material depends on the specific requirements of the conveyor system, including the type of load, operating conditions, and environmental factors.
Ceramic lagging is a type of pulley lagging that involves the use of ceramic tiles embedded in a rubber matrix. This combination provides superior wear resistance and increased traction compared to traditional rubber lagging. Ceramic lagging is especially beneficial in environments where the conveyor system is subjected to heavy loads, high speeds, and abrasive materials. The ceramic tiles are designed to create a high-friction surface, reducing belt slippage and improving the overall efficiency of the conveyor system. This type of lagging is ideal for mining, quarrying, and other demanding industrial applications.
The hardness of pulley lagging varies depending on the material used and the application requirements. Rubber lagging typically has a hardness ranging from 60 to 75 Shore A, providing a good balance of flexibility and durability. Ceramic lagging, on the other hand, offers a much higher hardness, often exceeding 80 Shore D, due to the inherent hardness of ceramic materials. The appropriate hardness level is selected based on the specific needs of the conveyor system, including the type of material being conveyed, the load conditions, and the operating environment. Proper selection ensures optimal performance and longevity of the conveyor system.
Last Updated on June 7, 2024 by Jordan Smith
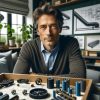
Jordan Smith, a seasoned professional with over 20 years of experience in the conveyor system industry. Jordan’s expertise lies in providing comprehensive solutions for conveyor rollers, belts, and accessories, catering to a wide range of industrial needs. From initial design and configuration to installation and meticulous troubleshooting, Jordan is adept at handling all aspects of conveyor system management. Whether you’re looking to upgrade your production line with efficient conveyor belts, require custom conveyor rollers for specific operations, or need expert advice on selecting the right conveyor accessories for your facility, Jordan is your reliable consultant. For any inquiries or assistance with conveyor system optimization, Jordan is available to share his wealth of knowledge and experience. Feel free to reach out at any time for professional guidance on all matters related to conveyor rollers, belts, and accessories.