Standard Sizes of Conveyor Pulley Shaft Material
Selecting the right conveyor pulley shaft material is crucial for ensuring the durability and efficiency of conveyor systems. The material affects the shaft’s strength, resistance to wear and corrosion, and overall performance. Using high-quality conveyor pulley shaft material can significantly reduce maintenance costs, extend the lifespan of the system, and improve operational efficiency. This overview highlights the key considerations when choosing conveyor pulley shaft materials and the benefits of making an informed selection for optimal system performance.
Types of Used Conveyor Pulley Shaft Material
Used Conveyor Pulley Shaft Material: Types and Benefits
Conveyor pulley shafts are a critical component in conveyor systems, ensuring the smooth operation and longevity of the entire setup. The choice of material for these shafts plays a significant role in determining their performance and durability. When sourcing used conveyor pulley shaft material, it’s essential to understand the types of materials commonly used, their benefits, and the sources from which they can be procured.
Common Types of Conveyor Pulley Shaft Material
- Carbon Steel:
- Description: Carbon steel is a widely used material for conveyor pulley shafts due to its excellent strength and toughness. It contains carbon and iron, making it durable and suitable for high-load applications.
- Benefits: High strength, good wear resistance, cost-effective, and widely available.
- Applications: Suitable for heavy-duty conveyor systems in industries such as mining, construction, and manufacturing.
- Alloy Steel:
- Description: Alloy steel is carbon steel that has been alloyed with other elements such as chromium, molybdenum, or nickel to improve its mechanical properties.
- Benefits: Enhanced strength, toughness, and resistance to wear and fatigue compared to standard carbon steel.
- Applications: Ideal for high-stress applications where enhanced performance and durability are required, such as in mining and heavy industrial environments.
- Stainless Steel:
- Description: Stainless steel is an alloy of iron with a minimum of 10.5% chromium, known for its corrosion resistance and strength.
- Benefits: Excellent resistance to corrosion and rust, hygienic, and easy to clean. It also maintains strength at high temperatures.
- Applications: Commonly used in food processing, pharmaceutical, and chemical industries where hygiene and corrosion resistance are crucial.
- Aluminum:
- Description: Aluminum is a lightweight metal with good strength-to-weight ratio and corrosion resistance.
- Benefits: Lightweight, resistant to corrosion, easy to machine, and excellent thermal conductivity.
- Applications: Suitable for applications where weight reduction is important, such as in packaging and aerospace industries.
- Composite Materials:
- Description: Composite materials are made from two or more constituent materials with different physical or chemical properties.
- Benefits: High strength-to-weight ratio, corrosion resistance, and can be tailored for specific applications.
- Applications: Used in specialized applications where traditional metals may not provide the required performance characteristics, such as in high-corrosion or high-impact environments.
Sourcing Used Conveyor Pulley Shaft Material
- Industrial Auctions and Liquidation Sales:
- Description: These events often feature used industrial equipment, including conveyor pulley shafts, sold at competitive prices.
- Benefits: Potential to find high-quality materials at lower costs, especially from reputable companies liquidating their assets.
- Considerations: Ensure thorough inspection and verification of material quality before purchase.
- Online Marketplaces:
- Description: Platforms such as eBay, Alibaba, and specialized industrial equipment websites list used conveyor pulley shaft materials.
- Benefits: Wide range of options, ability to compare prices and specifications, and convenience of online shopping.
- Considerations: Verify seller credibility and request detailed product information and history.
- Local Scrap Yards and Recycling Centers:
- Description: These facilities often receive and resell used industrial materials, including conveyor pulley shafts.
- Benefits: Potential for cost savings and support for recycling and sustainability efforts.
- Considerations: Requires careful inspection to ensure the material meets quality and performance standards.
- Industrial Equipment Suppliers:
- Description: Some suppliers specialize in used or refurbished industrial equipment and components.
- Benefits: Access to high-quality materials with potential warranties or guarantees.
- Considerations: Typically more reliable than informal sources, but may come at a higher cost.
Understanding the different types of conveyor pulley shaft materials and their benefits is crucial when sourcing used materials. Carbon steel, alloy steel, stainless steel, aluminum, and composite materials each offer unique advantages for specific applications. By leveraging sources such as industrial auctions, online marketplaces, local scrap yards, and specialized suppliers, businesses can find reliable used conveyor pulley shaft materials that meet their operational needs. Ensuring thorough inspection and verification of material quality is essential to secure the best value and performance.
Finding Reliable Conveyor Pulley Shaft Material Suppliers
Conveyor Pulley Shaft Material Suppliers: Guide to Identifying and Choosing
Selecting reliable suppliers for conveyor pulley shaft materials is vital for ensuring the quality and longevity of your conveyor systems. The right supplier will provide high-quality materials that meet your specific requirements, helping to maintain efficient operations and reduce downtime. This section provides a guide on identifying and choosing reliable conveyor pulley shaft material suppliers, including tips for evaluating supplier credibility.
Identifying Reliable Suppliers
- Industry Reputation:
- Description: Suppliers with a strong industry reputation are often more reliable and provide high-quality materials.
- Tips: Look for suppliers with positive reviews, testimonials, and a history of serving reputable clients. Industry awards and certifications can also indicate a trustworthy supplier.
- Product Range and Specialization:
- Description: Suppliers that specialize in conveyor pulley shaft materials or have a broad product range are likely to have the expertise and resources to meet your needs.
- Tips: Evaluate the supplier’s product catalog to ensure they offer the specific materials and specifications required for your application.
- Certifications and Compliance:
- Description: Suppliers that adhere to industry standards and possess relevant certifications are more likely to provide high-quality materials.
- Tips: Check for certifications such as ISO, ASME, and ASTM, which indicate compliance with international quality and safety standards.
Evaluating Supplier Credibility
- Quality Assurance and Testing:
- Description: Reliable suppliers should have stringent quality assurance processes and provide materials that have undergone rigorous testing.
- Tips: Request information on the supplier’s quality control procedures and ask for test reports or material certifications to verify the quality of the products.
- Customer Service and Support:
- Description: A supplier’s commitment to customer service and support is a good indicator of their reliability.
- Tips: Assess the responsiveness and helpfulness of the supplier’s customer service team. Reliable suppliers will provide prompt assistance and be willing to address any concerns or issues.
- Supply Chain Stability:
- Description: Suppliers with stable and well-managed supply chains are more likely to deliver materials on time and without disruptions.
- Tips: Inquire about the supplier’s supply chain practices, including their relationships with raw material providers and their ability to manage inventory and logistics effectively.
- References and Case Studies:
- Description: References from other clients and detailed case studies can provide insights into the supplier’s performance and reliability.
- Tips: Ask for references and case studies related to projects similar to yours. Contact the references to get firsthand feedback on the supplier’s quality, delivery, and customer service.
Tips for Choosing the Right Supplier
- Define Your Requirements:
- Description: Clearly defining your requirements will help you identify suppliers that can meet your specific needs.
- Tips: List all the specifications, including material type, dimensions, load capacity, and any special requirements. Share this information with potential suppliers to ensure they can provide the appropriate materials.
- Request for Quotes (RFQs):
- Description: Requesting quotes from multiple suppliers allows you to compare prices, lead times, and other terms.
- Tips: Prepare detailed RFQs and send them to a shortlist of suppliers. Evaluate the quotes based on not just price but also delivery times, payment terms, and any value-added services offered.
- Conduct Site Visits:
- Description: Visiting the supplier’s facilities can provide valuable insights into their operations and capabilities.
- Tips: Schedule site visits to assess the supplier’s production processes, quality control measures, and overall operational efficiency. This firsthand observation can help you make a more informed decision.
- Establish Long-Term Relationships:
- Description: Building long-term relationships with suppliers can lead to better terms, improved communication, and more reliable supply.
- Tips: Choose suppliers that you can work with over the long term. Establish clear communication channels and foster a collaborative relationship to ensure mutual success.
Finding reliable suppliers for conveyor pulley shaft materials involves identifying reputable suppliers, evaluating their credibility, and choosing those that meet your specific requirements. Key factors to consider include industry reputation, product range, certifications, quality assurance, customer service, supply chain stability, and references. By defining your requirements, requesting quotes, conducting site visits, and establishing long-term relationships, you can select suppliers that provide high-quality materials, ensuring the efficiency and reliability of your conveyor systems.
Standard Conveyor Pulley Shaft Material Sizes
Conveyor Pulley Shaft Material Sizes: Explanation of Standard Sizes and Selection Criteria
Selecting the appropriate size for conveyor pulley shafts is crucial for ensuring the efficient and reliable operation of conveyor systems. Standard sizes for conveyor pulley shaft materials are designed to meet common industrial requirements and simplify the selection process. This section provides an explanation of standard conveyor pulley shaft material sizes and offers guidance on how to select the appropriate size for specific applications.
Standard Sizes for Conveyor Pulley Shaft Materials
- Diameter:
- Description: The diameter of the shaft is a critical dimension that affects the pulley’s ability to handle loads and transmit power. Standard shaft diameters are typically specified in millimeters (mm) or inches (in).
- Common Sizes: Standard diameters for conveyor pulley shafts range from 50 mm (approximately 2 inches) to 200 mm (approximately 8 inches) or more, depending on the application and load requirements.
- Length:
- Description: The length of the shaft must be sufficient to accommodate the width of the conveyor pulley and the bearings or other mounting components.
- Common Sizes: Standard lengths vary widely based on the width of the conveyor belt and the design of the conveyor system. Typical lengths range from 500 mm (approximately 20 inches) to 2000 mm (approximately 80 inches) or more.
- Keyway Dimensions:
- Description: Keyways are slots cut into the shaft to accommodate keys, which help lock the pulley to the shaft and transmit torque.
- Common Sizes: Keyway dimensions are standardized to ensure compatibility with keys and keyseats. Common keyway widths range from 10 mm to 40 mm, with depths proportional to the shaft diameter.
Selecting the Appropriate Size for Conveyor Pulley Shafts
- Load Capacity:
- Description: The shaft must be able to handle the maximum load applied by the conveyor belt and transported materials. This includes both static and dynamic loads.
- Selection Criteria: Calculate the expected load and select a shaft diameter that provides adequate strength and rigidity. Refer to load capacity charts and manufacturer recommendations to ensure the shaft can handle the specified loads.
- Operating Speed:
- Description: The rotational speed of the conveyor pulley affects the selection of shaft size, as higher speeds require greater strength to withstand centrifugal forces and minimize deflection.
- Selection Criteria: Determine the operating speed of the conveyor system and choose a shaft diameter that can safely handle the speed without excessive deflection or vibration.
- Environmental Conditions:
- Description: Environmental factors such as temperature, humidity, and exposure to corrosive substances can impact the performance and durability of the shaft material.
- Selection Criteria: Select materials and sizes that are suitable for the specific environmental conditions. For example, stainless steel shafts are preferred in corrosive environments, while larger diameters may be needed for high-temperature applications.
- Compatibility with Bearings and Housings:
- Description: The shaft must be compatible with the bearings and housings used in the conveyor system to ensure proper alignment and smooth operation.
- Selection Criteria: Ensure that the selected shaft diameter and length match the specifications of the bearings and housings. Check manufacturer guidelines for recommended shaft sizes and tolerances.
- Safety Factors:
- Description: Applying safety factors ensures that the shaft can handle unexpected loads or stresses without failure, providing a margin of safety for reliable operation.
- Selection Criteria: Incorporate appropriate safety factors into the design calculations. Common safety factors range from 1.5 to 3, depending on the criticality of the application and the potential consequences of shaft failure.
Selecting the appropriate size for conveyor pulley shafts involves considering factors such as load capacity, operating speed, environmental conditions, compatibility with bearings and housings, and safety factors. Standard sizes for conveyor pulley shaft materials, including diameter, length, and keyway dimensions, provide a reference framework for selection. By carefully evaluating these factors and consulting with manufacturers or engineering experts, businesses can ensure that they choose the right shaft sizes for their conveyor systems, optimizing performance and reliability.
Selecting Heavy Duty Conveyor Pulley Shaft Material
Insights into Selecting Materials for Heavy Duty Conveyor Pulley Shafts
Choosing the appropriate heavy duty conveyor pulley shaft material is critical for ensuring the reliability and longevity of conveyor systems, especially in demanding industrial environments. The material must withstand high loads, resist wear and corrosion, and maintain structural integrity under extreme conditions.
Key Characteristics of Heavy Duty Conveyor Pulley Shaft Material
- Strength and Durability
- High Tensile Strength: The material must possess high tensile strength to withstand the heavy loads and stresses exerted during operation. This ensures the shaft does not deform or fail under pressure.
- Impact Resistance: Materials with high impact resistance can absorb and dissipate energy without fracturing, which is essential in environments where sudden loads or shocks are common.
- Wear Resistance
- Abrasion Resistance: The shaft material should resist wear caused by friction and contact with other components. High abrasion resistance minimizes wear and extends the life of the shaft.
- Hardness: Materials with higher hardness levels tend to have better wear resistance, making them suitable for heavy duty applications.
- Corrosion Resistance
- Oxidation Resistance: The ability to resist oxidation prevents the material from rusting, which can weaken the shaft and cause failures.
- Chemical Resistance: In environments where the shaft is exposed to chemicals, choosing a material with excellent chemical resistance is crucial to prevent degradation.
- Fatigue Strength
- Endurance Limit: Materials with high fatigue strength can endure cyclic loading and unloading without experiencing fatigue failures, which is important for the long-term reliability of the shaft.
Common Materials for Heavy Duty Conveyor Pulley Shafts
- Alloy Steel
- Chromium-Molybdenum Steel: Known for its excellent strength, toughness, and wear resistance, chromium-molybdenum steel is a popular choice for heavy duty shafts.
- Nickel-Chromium Steel: Offers high hardness and excellent wear resistance, making it suitable for high-stress applications.
- Stainless Steel
- Austenitic Stainless Steel: Provides excellent corrosion resistance and moderate strength, ideal for environments with high moisture or chemical exposure.
- Martensitic Stainless Steel: Known for its high hardness and strength, this material is suitable for applications requiring superior wear resistance.
- Carbon Steel
- High-Carbon Steel: Offers good strength and wear resistance, suitable for heavy duty applications where cost-effectiveness is also a consideration.
Performance Criteria for Selecting Materials
- Load-Bearing Capacity
- The material must support the maximum load expected in the application without deforming or failing.
- Environmental Conditions
- Consider the operating environment, including exposure to moisture, chemicals, and temperature extremes, to choose a material that can withstand these conditions.
- Maintenance and Longevity
- Select materials that minimize maintenance requirements and offer long service life to reduce downtime and replacement costs.
Selecting the right heavy duty conveyor pulley shaft material involves understanding the specific demands of the application and choosing materials that offer the necessary strength, durability, and resistance to wear and corrosion. By focusing on key characteristics and performance criteria, businesses can ensure the reliability and longevity of their conveyor systems.
Top Conveyor Pulley Shaft Material Manufacturers
Overview of Leading Manufacturers of Conveyor Pulley Shaft Materials
Choosing a reliable manufacturer for conveyor pulley shaft materials is crucial for ensuring the quality and performance of conveyor systems. Here, we provide an overview of some of the leading manufacturers in the industry, highlighting their product offerings and industry reputation.
Leading Conveyor Pulley Shaft Material Manufacturers
- SKF
- Product Offerings: SKF offers a wide range of high-quality bearings and shaft materials designed for industrial applications. Their products are known for their durability and reliability.
- Industry Reputation: SKF is a globally recognized brand with a reputation for innovation and excellence in the manufacturing of industrial components.
- Timken
- Product Offerings: Timken provides a variety of alloy and carbon steel shaft materials, known for their strength and wear resistance. They also offer customized solutions to meet specific application requirements.
- Industry Reputation: Timken is known for its high standards of quality and engineering expertise, making it a trusted name in the industry.
- Rexnord
- Product Offerings: Rexnord offers a comprehensive range of conveyor components, including high-strength pulley shaft materials. Their products are designed to withstand the toughest industrial conditions.
- Industry Reputation: Rexnord is recognized for its commitment to quality and customer satisfaction, with a strong presence in the global market.
- NSK
- Product Offerings: NSK provides advanced shaft materials and bearings that offer excellent performance in heavy duty applications. Their products are engineered for high reliability and long service life.
- Industry Reputation: NSK is known for its innovative solutions and high-quality products, making it a leader in the industrial components sector.
- NTN
- Product Offerings: NTN offers a range of shaft materials suitable for heavy duty conveyor applications. Their products are known for their high strength and resistance to wear and corrosion.
- Industry Reputation: NTN is a respected manufacturer with a reputation for delivering high-performance products and excellent customer service.
Factors to Consider When Choosing a Manufacturer
- Product Quality
- Ensure the manufacturer uses high-quality materials and adheres to stringent quality control standards to produce reliable and durable products.
- Customization Options
- Look for manufacturers that offer customization options to meet specific application requirements and provide tailored solutions.
- Industry Experience
- Choose manufacturers with extensive experience in the industry, as they are more likely to understand the unique challenges and requirements of different applications.
- Technical Support
- Consider manufacturers that provide comprehensive technical support, including engineering assistance and after-sales service, to ensure optimal performance of the conveyor system.
- Reputation and Reliability
- Select manufacturers with a strong reputation for reliability and customer satisfaction, as this indicates their commitment to delivering high-quality products and services.
Selecting the right manufacturer for conveyor pulley shaft material is essential for ensuring the quality and performance of your conveyor system. By considering factors such as product quality, customization options, industry experience, and technical support, businesses can choose manufacturers that offer the best value and reliability.
Conveyor Pulley Shaft Material: Conveyor Pulley Shaft Assembly Process
Detailed Explanation of the Pulley Shaft Assembly Process
The assembly process of a conveyor pulley shaft is critical for ensuring the secure and efficient operation of the conveyor system. A well-executed assembly process minimizes the risk of component failure and enhances the overall performance of the system. Here, we provide a detailed explanation of the steps involved in the pulley shaft assembly process and best practices for ensuring a successful assembly.
Steps Involved in Pulley Shaft Assembly
- Preparation
- Material Inspection: Inspect all materials and components for defects or damage before beginning the assembly process. Ensure that all parts meet the required specifications.
- Workspace Setup: Set up a clean and organized workspace with all necessary tools and equipment readily available.
- Aligning the Shaft and Pulley
- Shaft Alignment: Align the shaft with the pulley, ensuring that the shaft is centered and properly positioned within the pulley bore.
- Pulley Alignment: Align the pulley with the conveyor system, making sure it is properly positioned to maintain belt alignment and tension.
- Installing the Bearings
- Bearing Selection: Choose the appropriate bearings based on the load capacity and operational requirements of the conveyor system.
- Bearing Installation: Install the bearings onto the shaft, ensuring they are securely fitted and properly lubricated to minimize friction and wear.
- Securing the Pulley
- Mounting Hubs: Use the appropriate mounting hubs to secure the pulley to the shaft. Ensure that the hubs are tightened to the recommended torque specifications to prevent loosening during operation.
- Locking Mechanisms: Use locking mechanisms, such as set screws or locking collars, to secure the pulley and prevent axial movement along the shaft.
- Testing and Adjustment
- Initial Testing: Conduct an initial test run of the conveyor system to check for proper alignment, tension, and smooth operation.
- Adjustments: Make any necessary adjustments to the pulley alignment, tension, or bearing placement to ensure optimal performance.
- Final Inspection
- Performance Check: Perform a final inspection to verify that the pulley shaft assembly is functioning correctly and meets all operational requirements.
- Documentation: Document the assembly process, including any adjustments made, to provide a record for future maintenance and troubleshooting.
Best Practices for Pulley Shaft Assembly
- Follow Manufacturer Guidelines
- Adhere to the manufacturer’s guidelines and recommendations for assembly procedures and torque specifications to ensure proper installation.
- Use Quality Tools and Equipment
- Utilize high-quality tools and equipment to prevent damage to components and ensure precise assembly.
- Ensure Proper Lubrication
- Apply the appropriate lubrication to bearings and other moving parts to reduce friction and prevent premature wear.
- Regular Maintenance
- Implement a regular maintenance schedule to inspect and service the pulley shaft assembly, ensuring continued reliable operation.
- Training and Safety
- Ensure that all personnel involved in the assembly process are adequately trained and follow safety protocols to prevent accidents and injuries.
The pulley shaft assembly process is a critical aspect of ensuring the efficient and reliable operation of a conveyor system. By following the detailed steps and best practices outlined above, businesses can achieve a secure and effective assembly, minimizing the risk of component failure and optimizing the performance of their conveyor systems.
FAQs about Conveyor Pulley Shaft Material
Shaft pulleys are typically made from high-strength materials to withstand the mechanical stresses they encounter during operation. Common materials used for shaft pulleys include:
Steel: The most common material for shaft pulleys, steel offers excellent strength, durability, and resistance to wear and tear. It is suitable for both high-load and high-speed applications, making it a versatile choice for various industries.
Stainless Steel: Used in environments where corrosion resistance is critical, such as in food processing, chemical, and marine applications. Stainless steel shaft pulleys provide durability while resisting rust and corrosion.
Aluminum: Lightweight and corrosion-resistant, aluminum shaft pulleys are often used in applications where weight reduction is important, such as in automotive and aerospace industries. They are not as strong as steel but offer sufficient strength for lighter loads.
Cast Iron: Known for its good wear resistance and ability to dampen vibrations, cast iron is used in heavy-duty applications where noise reduction is beneficial. However, it is more brittle compared to steel.
Choosing the right material for a shaft pulley depends on factors such as load capacity, environmental conditions, and specific application requirements.
Conveyor pulleys are constructed from materials designed to endure the stresses and environmental conditions of material handling systems. The primary materials used include:
Steel: Steel is the most commonly used material for conveyor pulleys due to its high strength, durability, and ability to withstand heavy loads. Carbon steel and alloy steel are typical choices, providing excellent performance in various industrial applications.
Stainless Steel: Stainless steel conveyor pulleys are used in industries where corrosion resistance is crucial, such as food processing, pharmaceuticals, and chemical manufacturing. The material prevents rust and contamination, ensuring hygienic operation.
Aluminum: Aluminum conveyor pulleys are used in applications where weight reduction is important. While not as strong as steel, aluminum offers sufficient strength for lighter loads and is resistant to corrosion, making it suitable for specific industries like packaging and light manufacturing.
Rubber or Ceramic Lagging: Often, conveyor pulleys are coated with lagging made from rubber or ceramic materials. Lagging enhances grip, reduces belt slippage, and protects the pulley surface from wear.
Idler pulleys are essential components in conveyor systems and belt-driven machinery, guiding and supporting the belt while maintaining proper tension. The materials used for idler pulleys include:
Steel: Steel idler pulleys are durable and capable of handling high loads and harsh environments. They are commonly used in heavy-duty applications such as mining, quarrying, and industrial manufacturing.
Plastic: Plastic idler pulleys, often made from materials like nylon or polypropylene, are lightweight and resistant to corrosion. They are used in applications where weight reduction and noise reduction are important, such as in automotive and office machinery.
Aluminum: Aluminum idler pulleys offer a balance between strength and weight. They are resistant to corrosion and suitable for applications where moderate strength and lightweight are required, such as in packaging and light manufacturing.
Composite Materials: Composites, combining materials like fiberglass and resins, are used for idler pulleys to provide high strength-to-weight ratios and excellent resistance to wear and environmental factors.
Pulleys are constructed from various materials depending on their application, load requirements, and environmental conditions. Common materials include:
Steel: Steel is the most widely used material for pulleys due to its high strength, durability, and ability to handle heavy loads. Carbon steel and alloy steel are typical choices, providing excellent performance in a wide range of industrial applications.
Stainless Steel: Used in environments where corrosion resistance is crucial, such as food processing, pharmaceuticals, and chemical manufacturing. Stainless steel pulleys offer durability and hygienic operation, preventing rust and contamination.
Aluminum: Aluminum pulleys are lightweight and resistant to corrosion, making them suitable for applications where weight reduction is important, such as in automotive and aerospace industries. They are not as strong as steel but offer sufficient strength for lighter loads.
Cast Iron: Known for its good wear resistance and ability to dampen vibrations, cast iron is used in heavy-duty applications where noise reduction is beneficial. However, it is more brittle compared to steel and aluminum.
Plastic and Composites: Plastic pulleys, made from materials like nylon or polypropylene, and composite pulleys, which combine materials like fiberglass and resins, are used in applications requiring lightweight and corrosion-resistant properties. They are common in automotive, office machinery, and other light-duty applications.
Last Updated on May 30, 2024 by Jordan Smith
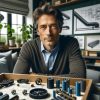
Jordan Smith, a seasoned professional with over 20 years of experience in the conveyor system industry. Jordan’s expertise lies in providing comprehensive solutions for conveyor rollers, belts, and accessories, catering to a wide range of industrial needs. From initial design and configuration to installation and meticulous troubleshooting, Jordan is adept at handling all aspects of conveyor system management. Whether you’re looking to upgrade your production line with efficient conveyor belts, require custom conveyor rollers for specific operations, or need expert advice on selecting the right conveyor accessories for your facility, Jordan is your reliable consultant. For any inquiries or assistance with conveyor system optimization, Jordan is available to share his wealth of knowledge and experience. Feel free to reach out at any time for professional guidance on all matters related to conveyor rollers, belts, and accessories.