Selecting Conveyor Pulley Specification
Understanding conveyor pulley specification is crucial for designing and selecting the right pulley for your conveyor system. The conveyor pulley specification includes details such as dimensions, material, load capacity, and surface finish. These specifications ensure the pulley can handle the operational demands, provide adequate grip, and maintain belt alignment. Properly specified pulleys enhance the efficiency and longevity of the conveyor system, reducing maintenance costs and preventing operational disruptions. By adhering to precise conveyor pulley specifications, you can optimize performance and reliability in various industrial applications.
What Are Conveyor Pulley Specifications
Conveyor pulleys are essential components of conveyor systems, providing the driving force and maintaining belt tension. Their specifications can vary based on the application, environment, and type of conveyor system. Here are some key aspects and specifications to consider for conveyor pulleys:
Pulley Diameter
- Standard Diameters: Common diameters range from 100 mm to 800 mm or more, depending on the belt width and application requirements.
- Selection Criteria: Pulley diameter should be chosen based on the belt’s tensile strength and the load it needs to carry. Larger diameters are preferred for higher loads and to reduce belt flexing.
Pulley Face Width
- Width Range: Typically, the face width should be about 150 mm to 300 mm wider than the belt width.
- Importance: Adequate face width ensures proper tracking and prevents belt edge damage.
Pulley Material
- Common Materials: Mild steel, stainless steel, aluminum, and occasionally plastic for lightweight applications.
- Selection Criteria: Material choice depends on environmental conditions such as exposure to moisture, chemicals, or abrasive materials.
- Types of Lagging: Rubber lagging, ceramic lagging, and diamond lagging are common types.
- Purpose: Lagging improves grip, reduces belt slippage, and protects the pulley surface. Rubber lagging is suitable for general purposes, while ceramic lagging is used in high-wear environments.
Pulley Shaft
- Shaft Diameter: Determined by the load, pulley size, and bearing size. Typical shaft diameters range from 20 mm to 150 mm or more.
- Shaft Material: Generally made from high-strength steel to withstand bending and torsional stresses.
Pulley Bearings
- Types: Roller bearings and ball bearings are commonly used.
- Selection Criteria: Bearings should be chosen based on load capacity, rotational speed, and environmental conditions.
Pulley Configuration
- Drive Pulley: Typically larger and with higher torque requirements.
- Tail Pulley: Generally a tensioning or redirecting pulley with a simpler design.
- Snub Pulley: Used to increase the angle of wrap on the drive pulley for better traction.
- Bend Pulley: Used to change the direction of the belt in the conveyor system.
Pulley Construction
- Crowned or Flat: Crowning helps in belt tracking, ensuring the belt remains centered on the pulley.
- Welded or Bolted: Welded construction offers more strength and rigidity, while bolted construction allows for easier maintenance and component replacement.
Pulley Balance
- Static and Dynamic Balancing: Ensures smooth operation at high speeds, reducing vibrations and prolonging the lifespan of both the pulley and the conveyor belt.
Load Capacity
- Load Rating: Must match or exceed the maximum load expected in the conveyor system to prevent failure.
- Safety Factor: A higher safety factor (typically 1.5 to 3 times the maximum load) is used to account for unexpected load variations and ensure reliable operation.
Additional Considerations
Environmental Conditions
- Corrosion Resistance: Stainless steel or coated pulleys for corrosive environments.
- Temperature Resistance: Materials and bearings that can withstand extreme temperatures if the conveyor operates in such conditions.
Maintenance and Accessibility
- Ease of Maintenance: Pulleys should be designed for easy access and maintenance to reduce downtime.
- Replacement Parts: Availability of replacement parts can be crucial for reducing operational interruptions.
Customization Options
- Custom Designs: For unique applications, pulleys can be customized in terms of size, material, and configuration.
- Special Features: Features such as integrated sensors for monitoring pulley and belt conditions.
The specifications of a conveyor pulley play a crucial role in the efficiency, reliability, and longevity of a conveyor system. Proper selection based on the operational requirements, environmental conditions, and maintenance needs ensures optimal performance. Customization options further allow for tailored solutions to meet specific application demands.
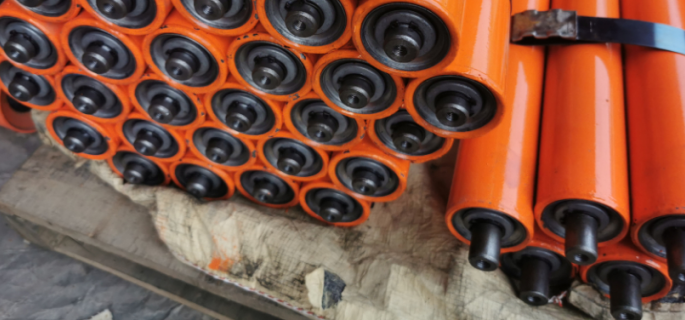
Conveyor Pulley Specification PDF
Conveyor Pulley Specification PDF: Detailed Discussion on Benefits and Key Elements
A comprehensive Conveyor Pulley Specification PDF is an invaluable resource for engineers, procurement specialists, and maintenance teams involved in the design, selection, and maintenance of conveyor systems. This document serves as a detailed guide that outlines the essential specifications and criteria for selecting the right conveyor pulleys for various applications. In this section, we will explore the benefits of having a Conveyor Pulley Specification PDF and the key elements it should contain.
Benefits of a Conveyor Pulley Specification PDF
- Standardized Information: A well-structured Conveyor Pulley Specification PDF ensures that all relevant information is standardized, making it easier for stakeholders to understand and use. This standardization helps in maintaining consistency across different projects and teams.
- Easy Accessibility: Having the specifications in a PDF format allows for easy distribution and accessibility. Stakeholders can quickly share the document via email or cloud storage, ensuring that everyone involved has access to the latest and most accurate information.
- Comprehensive Reference: A detailed specification PDF serves as a comprehensive reference that covers all aspects of conveyor pulley design and selection. This helps in making informed decisions, reducing the risk of errors and mismatches during the procurement and installation processes.
- Improved Communication: Clear and detailed specifications improve communication between different departments, such as engineering, procurement, and maintenance. This ensures that everyone is on the same page and working towards the same goals.
- Enhanced Efficiency: With all the necessary information readily available in a single document, the time required to select and specify conveyor pulleys is significantly reduced. This enhances the overall efficiency of the project and reduces delays.
Key Elements in a Conveyor Pulley Specification PDF
A comprehensive Conveyor Pulley Specification PDF should include the following key elements:
- Pulley Dimensions: Detailed information on the dimensions of the pulley, including diameter, width, and shaft size. These dimensions are critical for ensuring compatibility with the conveyor system and achieving optimal performance.
- Material Specifications: Information on the materials used in the construction of the pulley, such as steel grade, lagging type, and any coatings. Material specifications are essential for determining the durability and suitability of the pulley for specific applications.
- Load Capacity: The maximum load capacity of the pulley, including static and dynamic loads. This information is crucial for ensuring that the pulley can handle the expected loads without failure.
- Lagging Type: Details on the type of lagging used on the pulley, such as rubber, ceramic, or diamond. The type of lagging affects the traction and wear resistance of the pulley, which are important factors in its performance and longevity.
- Bearings and Seals: Specifications for the bearings and seals used in the pulley, including type, size, and material. High-quality bearings and seals are essential for smooth operation and long service life.
- Mounting and Installation: Instructions and guidelines for mounting and installing the pulley, including any special requirements or considerations. Proper installation is critical for ensuring the pulley operates efficiently and safely.
- Maintenance Guidelines: Recommendations for maintaining the pulley, including lubrication schedules, inspection procedures, and replacement intervals. Regular maintenance is key to extending the life of the pulley and preventing unexpected failures.
- Performance Criteria: Information on the performance criteria for the pulley, such as maximum operating speed, temperature range, and environmental conditions. These criteria help in selecting a pulley that meets the specific needs of the application.
- Compliance and Standards: Details on any relevant standards and certifications that the pulley meets, such as ISO, CEMA, or AS/NZS. Compliance with these standards ensures that the pulley meets industry benchmarks for quality and performance.
A Conveyor Pulley Specification PDF is an essential tool for ensuring the successful design, selection, and maintenance of conveyor pulleys. By providing standardized, comprehensive, and easily accessible information, this document enhances efficiency, improves communication, and reduces the risk of errors. Including key elements such as pulley dimensions, material specifications, load capacity, lagging type, bearings and seals, mounting and installation guidelines, maintenance recommendations, performance criteria, and compliance standards ensures that the PDF serves as a valuable reference for all stakeholders involved in conveyor system projects.
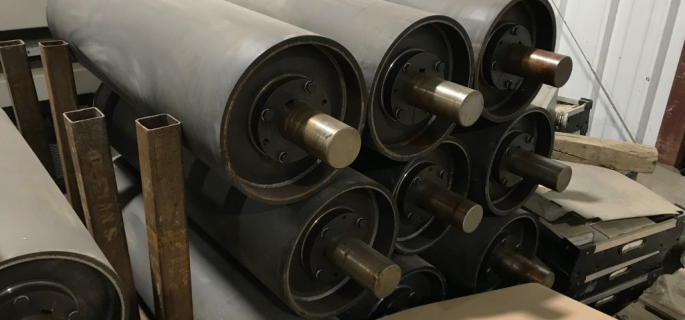
Heavy Duty Conveyor Pulley Specification
Insights into Requirements and Standards
Heavy duty conveyor pulleys are designed to handle demanding applications where high loads, continuous operation, and harsh environments are common. These pulleys require specific design features and materials to ensure they can withstand the rigors of heavy-duty use. In this section, we will provide insights into the specific requirements and standards for heavy duty conveyor pulleys, including materials, construction, and performance criteria.
Materials Used in Heavy Duty Conveyor Pulleys
- High-Grade Steel: Heavy duty conveyor pulleys are typically constructed from high-grade steel, such as carbon steel or alloy steel. These materials provide the necessary strength and durability to withstand high loads and resist wear and fatigue.
- Stainless Steel: For applications that require corrosion resistance, stainless steel is often used. Stainless steel pulleys are ideal for environments where exposure to moisture, chemicals, or extreme temperatures is common.
- Composite Materials: In some cases, composite materials are used to reduce weight while maintaining strength and durability. These materials can offer advantages in specific applications where reduced weight is beneficial.
Construction Features
- Reinforced Shell: The shell of a heavy duty conveyor pulley is reinforced to handle high loads and resist deformation. This typically involves using thicker steel and additional support structures.
- Heavy-Duty Shafts: The shafts of heavy duty pulleys are designed to handle significant stress and torque. They are often made from hardened steel and may include features such as keyways or splines to enhance their strength and stability.
- Robust End Discs: End discs are critical for maintaining the structural integrity of the pulley. Heavy duty pulleys use robust end discs that are securely welded or bolted to the shell and shaft.
- Lagging: Heavy duty pulleys often feature lagging made from durable materials such as rubber or ceramic. Lagging improves traction, reduces belt slippage, and protects the pulley from wear.
Performance Criteria
- Load Capacity: Heavy duty pulleys must be capable of handling high static and dynamic loads. Specifications should include the maximum load capacity, taking into account factors such as material weight, belt tension, and operational conditions.
- Speed and Torque: The operating speed and torque of the pulley must be specified to ensure it can handle the demands of the application. This includes maximum rotational speed and the torque required to drive the conveyor belt.
- Environmental Conditions: Heavy duty pulleys must be designed to operate in harsh environments, including extreme temperatures, high humidity, and exposure to chemicals or abrasive materials. Specifications should include the permissible operating conditions and any necessary protective measures.
Standards and Compliance
- ISO Standards: International Organization for Standardization (ISO) standards provide guidelines for the design, materials, and performance of conveyor pulleys. Compliance with ISO standards ensures that pulleys meet globally recognized benchmarks for quality and reliability.
- CEMA Standards: The Conveyor Equipment Manufacturers Association (CEMA) sets standards for conveyor components, including pulleys. CEMA standards cover dimensions, materials, and performance criteria, ensuring compatibility and performance in conveyor systems.
- AS/NZS Standards: Australian/New Zealand Standards (AS/NZS) provide specific guidelines for conveyor pulleys used in the region. Compliance with these standards ensures that pulleys meet local requirements for safety and performance.
Maintenance and Inspection
- Regular Inspections: Heavy duty pulleys require regular inspections to identify signs of wear, damage, or misalignment. Inspections should include checking the condition of the shell, lagging, bearings, and seals.
- Lubrication: Proper lubrication of bearings and seals is essential for maintaining the performance and longevity of heavy duty pulleys. Lubrication schedules should be followed according to manufacturer recommendations.
- Replacement Intervals: Based on the operational conditions and usage, heavy duty pulleys should be replaced at regular intervals to prevent unexpected failures and ensure continuous operation.
Heavy duty conveyor pulleys are essential components in demanding applications, requiring specific design features, materials, and performance criteria to ensure reliability and durability. Key elements of heavy duty conveyor pulley specification include high-grade materials, reinforced construction, robust end discs, lagging, load capacity, speed and torque, environmental conditions, and compliance with standards such as ISO, CEMA, and AS/NZS. Regular maintenance and inspections are crucial for maintaining the performance and extending the life of heavy duty pulleys. By adhering to these specifications and standards, businesses can ensure the efficient and reliable operation of their conveyor systems in heavy-duty environments.
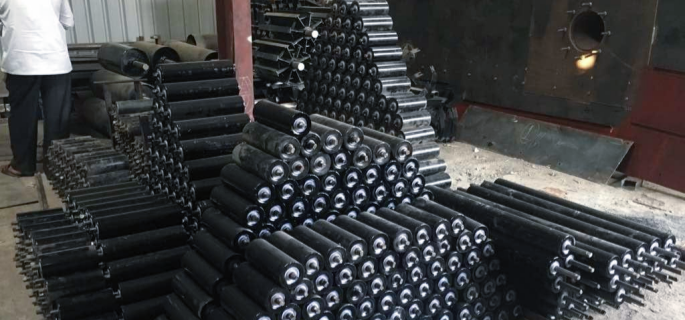
Metric Conveyor Pulley Specification
Metric Conveyor Pulley Specification: Dimensions, Tolerances, and International Standards
Metric conveyor pulley specifications are essential for ensuring that pulleys meet the precise requirements of conveyor systems designed using the metric system. These specifications cover dimensions, tolerances, and compliance with international standards, providing a clear framework for the design, selection, and manufacturing of conveyor pulleys. This section provides an explanation of metric specifications for conveyor pulleys, focusing on dimensions, tolerances, and relevant standards.
Dimensions and Tolerances
- Diameter and Width: The diameter and width of a conveyor pulley are critical dimensions that determine its compatibility with the conveyor system. Metric specifications provide these dimensions in millimeters (mm), ensuring precision and consistency. For example, a standard conveyor pulley might have a diameter of 500 mm and a width of 1200 mm.
- Shaft Size: The size of the shaft, including its diameter and length, is specified in metric units. Shaft dimensions must be precise to ensure proper fit and function within the pulley and the conveyor system. Common shaft diameters might range from 50 mm to 200 mm, depending on the application.
- Bearing and Seal Specifications: Bearings and seals used in metric conveyor pulleys are specified in metric units, including inner and outer diameters, widths, and tolerances. These components are critical for the smooth operation and longevity of the pulley.
- Tolerances: Metric conveyor pulley specifications include tolerances for critical dimensions to ensure that the pulleys meet the required precision and performance standards. Tolerances might be specified as ±0.1 mm for diameters and ±0.2 mm for widths, depending on the application and industry standards.
International Standards
- ISO Standards: The International Organization for Standardization (ISO) provides globally recognized standards for conveyor pulleys. ISO standards cover various aspects of pulley design, materials, and performance, ensuring consistency and quality across different manufacturers and regions. Compliance with ISO standards, such as ISO 3684 for belt conveyors, ensures that pulleys meet stringent quality and performance criteria.
- DIN Standards: The German Institute for Standardization (DIN) provides specific standards for conveyor pulleys and components used in metric-based systems. DIN standards, such as DIN 22101 for belt conveyors, specify dimensions, materials, and performance criteria, ensuring compatibility and reliability.
- EN Standards: The European Norm (EN) standards provide guidelines for conveyor pulleys used in the European Union and other regions that follow metric specifications. EN standards, such as EN 1554 for steel cord conveyor belts, cover various aspects of conveyor pulley design and performance.
Key Elements in Metric Conveyor Pulley Specification
- Material Specifications: Metric specifications include detailed information on the materials used in the construction of the pulley, such as steel grade, lagging type, and any protective coatings. These specifications ensure that the pulley can withstand the operational conditions and provide long-term reliability.
- Load Capacity: The maximum load capacity of the pulley, specified in metric units (kilograms or tonnes), ensures that the pulley can handle the expected loads without failure. Load capacity specifications consider both static and dynamic loads.
- Lagging Type: Information on the type of lagging used, such as rubber or ceramic, and its thickness, specified in millimeters, is included in the metric specifications. Lagging improves traction and wear resistance, enhancing the performance and lifespan of the pulley.
- Performance Criteria: Metric specifications include performance criteria such as maximum operating speed (meters per second), temperature range (degrees Celsius), and environmental conditions. These criteria ensure that the pulley can perform reliably under the specified conditions.
- Compliance and Certification: Details on compliance with relevant international standards and certifications, such as ISO, DIN, and EN, are included in the metric specifications. Compliance ensures that the pulley meets industry benchmarks for quality and performance.
Benefits of Metric Conveyor Pulley Specifications
- Precision and Consistency: Metric specifications ensure precision and consistency in the design and manufacturing of conveyor pulleys. This precision is crucial for achieving optimal performance and reliability in conveyor systems.
- Global Compatibility: Metric specifications facilitate global compatibility, making it easier to source and integrate pulleys from different manufacturers and regions. This compatibility is essential for multinational operations and projects.
- Quality Assurance: Adhering to international standards and specifications provides assurance of quality and performance. This reduces the risk of failures and ensures that the pulleys meet the stringent requirements of various applications.
- Ease of Communication: Using a standardized metric system simplifies communication between engineers, manufacturers, and suppliers, ensuring that everyone is on the same page and reducing the risk of misunderstandings.
Metric conveyor pulley specifications provide a clear and precise framework for the design, selection, and manufacturing of conveyor pulleys. By specifying dimensions, tolerances, materials, load capacity, lagging type, performance criteria, and compliance with international standards such as ISO, DIN, and EN, these specifications ensure that pulleys meet the exact requirements of metric-based conveyor systems. The benefits of using metric specifications include precision, consistency, global compatibility, quality assurance, and ease of communication. By adhering to these specifications, businesses can ensure the reliable and efficient operation of their conveyor systems.
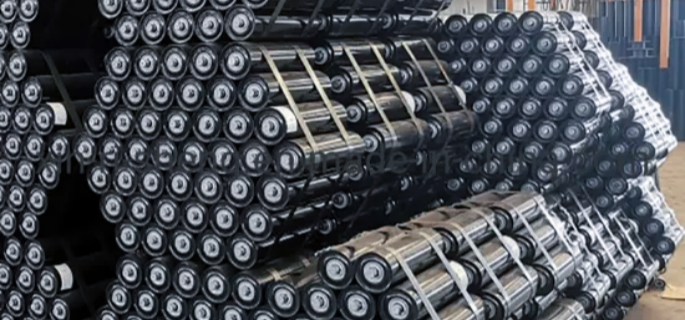
Conveyor Pulley Specification Chart
A conveyor pulley specification chart is a vital tool used in the design and selection process of conveyor pulleys. This chart outlines the essential specifications and parameters that must be considered to ensure the pulley fits and functions correctly within a conveyor system. Here’s an in-depth look at the elements typically included in a conveyor pulley specification chart and how to use it effectively.
Elements of a Conveyor Pulley Specification Chart
- Pulley Diameter: This is the diameter of the pulley drum, which directly affects the belt speed and tension. Larger diameters are generally used for higher loads and longer belt life.
- Face Width: This is the width of the pulley drum, which should be slightly wider than the belt to ensure proper belt tracking and reduce edge wear.
- Shaft Diameter: The diameter of the shaft on which the pulley is mounted. It must be robust enough to support the pulley and the load it carries.
- Lagging Type: Information about the type of lagging material used on the pulley surface, such as rubber, ceramic, or polyurethane, to enhance grip and reduce slippage.
- Hub Type: The type of hub used in the pulley, which affects how the pulley is mounted and its compatibility with the shaft and bearings.
- Bearing Type: The type of bearings used, which influence the pulley’s load capacity and rotational efficiency.
- Load Capacity: The maximum load the pulley can handle, ensuring it can support the weight of the conveyed materials without failing.
- Material: The material from which the pulley is made, such as steel, stainless steel, or aluminum, affecting its durability and suitability for different environments.
- RPM (Revolutions Per Minute): The rotational speed of the pulley, which influences the conveyor belt speed and overall system performance.
How to Use a Conveyor Pulley Specification Chart
- Identify System Requirements: Determine the operational requirements of your conveyor system, such as load capacity, belt speed, and environmental conditions.
- Match Specifications: Use the chart to find pulleys that match these requirements. Ensure the pulley diameter, face width, and shaft diameter are appropriate for your system.
- Check Compatibility: Verify that the chosen pulley is compatible with your existing conveyor components, including the belt, bearings, and motor.
- Consult with Manufacturers: If you need custom specifications, consult with pulley manufacturers to tailor the pulley to your specific needs. The specification chart provides a basis for these discussions.
A conveyor pulley specification chart is an essential resource for selecting the right pulley for your conveyor system. By understanding and using the chart effectively, you can ensure optimal performance, reliability, and longevity of your conveyor system.
Conveyor Pulley Specification Chart PDF
Advantages of a Conveyor Pulley Specification Chart PDF
Having a downloadable PDF version of a conveyor pulley specification chart offers numerous advantages for engineers, maintenance teams, and purchasing departments. Here’s why having this resource in PDF format can be beneficial.
Easy Reference and Sharing
- Portable and Accessible: A PDF can be easily accessed on various devices, including laptops, tablets, and smartphones, allowing for quick reference whether in the office or on-site.
- Easy to Share: PDFs can be shared effortlessly via email, cloud storage, or internal networks. This facilitates better communication and collaboration among team members and departments.
Comprehensive and Detailed Information
- Inclusion of All Necessary Details: A PDF specification chart can include all relevant details in one document, making it easy to ensure no critical information is overlooked during the selection process.
- Visual Aids: PDF documents can incorporate diagrams, images, and tables to illustrate specifications more clearly, aiding in better understanding and decision-making.
Enhanced Decision-Making
- Comparison Tool: A specification chart PDF allows for easy comparison of different pulleys side-by-side, helping to identify the best fit for your application.
- Documentation: Keeping a PDF record of specifications helps maintain a consistent reference, ensuring that all selected pulleys meet the required standards and specifications.
How to Utilize a Conveyor Pulley Specification Chart PDF
- Download and Save: Ensure that the PDF is downloaded from a reliable source and saved in a centralized location where all relevant team members can access it.
- Regular Updates: Keep the PDF updated with the latest specifications and standards to ensure that all references are current and accurate.
- Training and Education: Use the PDF as a training tool for new employees or team members unfamiliar with conveyor pulley specifications, enhancing their knowledge and proficiency.
- Project Planning: Incorporate the specification chart into project planning documents to ensure that all components are selected according to the required specifications from the outset.
A conveyor pulley specification chart PDF is an invaluable resource that enhances accessibility, communication, and decision-making. By utilizing this tool, businesses can ensure they select the right pulleys for their conveyor systems, leading to improved efficiency and reliability.
Key Elements in Conveyor Pulley Specification
Understanding the key elements in a conveyor pulley specification is essential for selecting the right pulley for your conveyor system. These elements ensure that the pulley can handle the operational demands, provide adequate grip, maintain belt alignment, and contribute to the overall efficiency and reliability of the conveyor system. Here, we provide a detailed explanation of the crucial components that should be included in any conveyor pulley specification.
Face Width
Definition and Importance
The face width of the pulley refers to the width of the pulley drum. It should be slightly wider than the conveyor belt to ensure proper tracking and to reduce edge wear. The typical rule of thumb is to make the face width 25-33% wider than the belt width.
Factors Affecting Face Width
The face width must accommodate the belt width plus any additional width required for belt misalignment and edge clearance. This ensures the belt remains centered on the pulley during operation, reducing wear and extending the life of both the belt and the pulley.
Shaft Diameter
Role of Shaft Diameter
The shaft diameter is another critical element in conveyor pulley specification. It must be robust enough to support the pulley and the load it carries without bending or failing. The shaft diameter affects the strength and durability of the pulley.
Calculating Shaft Diameter
The shaft diameter is determined based on the load it needs to support and the material properties of the shaft. It must be sized to prevent excessive deflection and to withstand the forces applied during operation.
Material
Common Materials Used
The material of the pulley affects its strength, durability, and suitability for specific environments. Common materials include:
- Steel: Used for its strength and durability, suitable for most industrial applications.
- Stainless Steel: Provides corrosion resistance, ideal for food processing and pharmaceutical industries.
- Aluminum: Lightweight and resistant to corrosion, used in applications where weight is a concern.
Choosing the Right Material
The choice of material depends on factors such as the type of load, environmental conditions, and specific industry requirements. For example, stainless steel is preferred in environments where corrosion resistance is critical, while steel is used for heavy-duty applications due to its high strength.
Lagging Type
Purpose of Lagging
Lagging is a material applied to the surface of the pulley to increase friction between the pulley and the conveyor belt. This prevents slippage and enhances the grip, ensuring smooth operation.
Types of Lagging
- Rubber Lagging: The most common type, providing good grip and shock absorption. It can be smooth or patterned, such as diamond or herringbone.
- Ceramic Lagging: Offers superior wear resistance and increased friction, ideal for high-tension applications and harsh environments.
- Polyurethane Lagging: Resistant to oils, chemicals, and abrasion, suitable for environments where exposure to harsh chemicals is common.
Hub Type
Definition and Importance
The hub type affects how the pulley is mounted on the shaft and its compatibility with the conveyor system. Common hub types include:
- Welded Hubs: Permanently fixed to the pulley, offering high strength.
- Taper-Lock Hubs: Allow for easy installation and removal, providing flexibility.
Bearing Type
Role of Bearings
Bearings support the shaft and allow the pulley to rotate smoothly. The type of bearings used affects the load capacity and efficiency of the pulley.
Common Bearing Types
- Ball Bearings: Used for light to medium loads, providing low friction and smooth operation.
- Roller Bearings: Suitable for heavier loads, offering higher load capacity and durability.
Load Capacity
Importance of Load Capacity
Load capacity indicates the maximum load the pulley can handle. It is crucial to ensure the pulley can support the weight of the conveyed materials without failing.
Factors Affecting Load Capacity
Load capacity is influenced by the material, shaft diameter, and bearing type. Ensuring the pulley can handle the anticipated load prevents operational failures and extends the system’s lifespan.
RPM (Revolutions Per Minute)
Role of RPM
The RPM of the pulley affects the belt speed and overall performance of the conveyor system. Ensuring the pulley operates at the correct RPM is essential for maintaining the desired belt speed and efficiency.
Tolerance and Finish
Importance of Tolerance and Finish
Manufacturing tolerances and surface finish affect the pulley’s performance and longevity. Tight tolerances ensure the pulley fits correctly with other components, while a smooth finish reduces wear on the belt.
Understanding and specifying the key elements in conveyor pulley specification is essential for designing and selecting the right pulley for your conveyor system. Each element, from diameter and face width to material and lagging type, plays a critical role in ensuring the pulley meets operational demands and contributes to the overall efficiency and reliability of the system. By carefully considering these specifications, businesses can optimize their conveyor systems for performance and longevity.
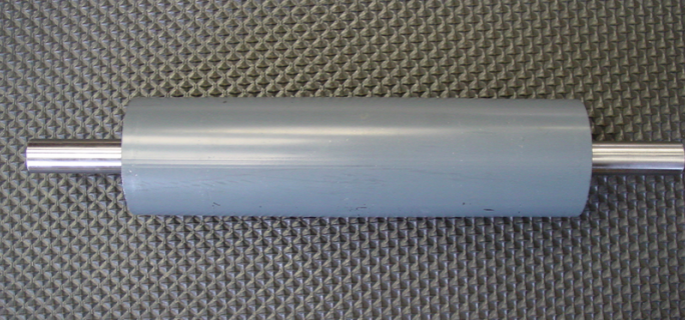
How to Select Conveyor Pulley Specifications
Selecting the right conveyor pulley specification involves a systematic evaluation of several key factors to ensure that the pulley meets the operational requirements, enhances efficiency, and ensures durability. Here’s a step-by-step guide to help you select the appropriate conveyor pulley specification:
Step 1: Understand the Application Requirements
Load Capacity:
- Determine the maximum load the conveyor system will handle.
- Consider both static and dynamic loads.
Belt Width and Type:
- Identify the width of the conveyor belt.
- Determine the type of belt (e.g., fabric, steel-cord, modular plastic).
Conveyor Speed:
- Ascertain the operating speed of the conveyor system.
Environmental Conditions:
- Assess the operating environment (e.g., temperature, humidity, exposure to chemicals or abrasives).
Step 2: Determine Pulley Diameter and Face Width
Pulley Diameter:
- Use the conveyor belt manufacturer’s recommendations for minimum pulley diameters.
- Consider larger diameters for reducing belt flexing and extending belt life.
Face Width:
- Ensure the face width is wider than the belt width (typically by 150 mm to 300 mm) to prevent belt edge damage and ensure proper tracking.
Step 3: Select Pulley Material
Mild Steel:
- Suitable for general applications with moderate load and environmental conditions.
Stainless Steel:
- Ideal for corrosive environments or food-grade applications.
Aluminum:
- Used for lightweight applications where weight reduction is crucial.
Plastic:
- Suitable for lightweight, low-load applications, and corrosive environments.
Step 4: Choose Appropriate Lagging
Rubber Lagging:
- General-purpose lagging that provides good traction and wear resistance.
Ceramic Lagging:
- High-durability lagging for abrasive environments, offering excellent grip and wear resistance.
Diamond Lagging:
- Provides enhanced grip and is suitable for applications requiring high traction.
Step 5: Determine Shaft Diameter and Material
Shaft Diameter:
- Based on the load, pulley size, and bearing size.
- Ensure the shaft diameter can handle the expected load without excessive deflection.
Shaft Material:
- Typically high-strength steel to withstand bending and torsional stresses.
Step 6: Select Bearings
Roller Bearings:
- Suitable for higher load capacities.
Ball Bearings:
- Ideal for higher speed applications with lower load requirements.
Step 7: Decide on Pulley Configuration
Drive Pulley:
- Primary pulley responsible for driving the belt.
Tail Pulley:
- Used at the end of the conveyor to tension and redirect the belt.
Snub Pulley:
- Increases the angle of wrap on the drive pulley for better traction.
Bend Pulley:
- Changes the direction of the belt in the conveyor system.
Step 8: Evaluate Construction Options
Crowned or Flat:
- Crowning helps in belt tracking, ensuring the belt remains centered on the pulley.
Welded or Bolted:
- Welded construction for strength and rigidity.
- Bolted construction for easier maintenance and component replacement.
Step 9: Ensure Proper Balance
Static and Dynamic Balancing:
- Necessary for smooth operation at high speeds, reducing vibrations and prolonging pulley and belt life.
Step 10: Check Load Capacity and Safety Factor
Load Rating:
- Ensure the pulley’s load rating matches or exceeds the maximum expected load.
Safety Factor:
- A safety factor of 1.5 to 3 times the maximum load is recommended to account for unexpected load variations.
Step 11: Consider Environmental Resistance
Corrosion Resistance:
- Select materials and coatings that can withstand the operating environment.
Temperature Resistance:
- Choose materials and bearings that can operate efficiently within the expected temperature range.
Step 12: Plan for Maintenance and Accessibility
Ease of Maintenance:
- Design for easy access to reduce downtime during maintenance.
Replacement Parts:
- Ensure availability of replacement parts to maintain operational continuity.
Step 13: Evaluate Customization Needs
Custom Sizes and Designs:
- For unique applications, consider custom pulley designs to meet specific requirements.
Special Features:
- Integrate sensors or other monitoring devices to track pulley and belt conditions.
Selecting the right conveyor pulley specification is crucial for the efficient and reliable operation of a conveyor system. By systematically evaluating application requirements, pulley dimensions, materials, lagging, bearings, and other key factors, you can ensure that the selected pulley meets the operational demands and extends the lifespan of the conveyor system. Customization options further allow for tailored solutions to address specific needs and challenges.
FAQs about Conveyor Pulley Specification
Conveyor belts use various types of pulleys to ensure smooth operation and efficient material handling. The primary types include:
Head Pulley: Located at the discharge point, the head pulley drives the belt and moves materials along the conveyor. It’s typically lagged to increase friction and prevent slippage.
Tail Pulley: Positioned at the opposite end of the conveyor from the head pulley, the tail pulley redirects the belt back towards the head pulley. It helps maintain proper belt tension and alignment.
Drive Pulley: Often synonymous with the head pulley, the drive pulley is powered by a motor to move the conveyor belt. It’s essential for the belt’s motion and overall system efficiency.
Snub Pulley: Used to increase the belt wrap around the drive pulley, enhancing friction and preventing belt slippage. It’s positioned close to the drive pulley to provide additional belt contact.
Take-Up Pulley: Adjusts the tension of the conveyor belt to compensate for belt stretch and wear. It’s usually part of the take-up mechanism, ensuring the belt remains taut.
Bend Pulley: Redirects the belt in a different direction, used in more complex conveyor systems with multiple angles. It helps change the belt’s path without affecting its tension.
Each type of pulley plays a crucial role in the overall performance and efficiency of conveyor belt systems, ensuring smooth and reliable operation.
Determining the correct pulley size for a conveyor system involves several key factors:
Belt Width: The width of the conveyor belt dictates the minimum face width of the pulley. Typically, the face width of the pulley should be approximately 25-33% wider than the belt width to ensure proper tracking and reduce edge wear.
Load Capacity: The size of the pulley must be adequate to handle the maximum load that the conveyor belt will carry. This involves considering the weight of the materials transported and the belt itself.
Belt Speed: The speed at which the conveyor belt will operate influences the diameter of the pulley. Higher speeds generally require larger diameters to reduce the stress on the belt and prevent excessive wear.
Material and Construction: The type of material and construction of the pulley (such as steel or composite materials) can also affect the size. Heavy-duty applications might require larger and more robust pulleys.
Application Requirements: Specific application needs, such as the need for increased friction, might dictate the use of lagged pulleys. This lagging material can also influence the required size.
Safety Factors: Incorporating a safety factor to account for unexpected loads or environmental conditions can also influence the size of the pulley. Ensuring that the pulley can handle more than the anticipated load prevents failure and extends the life of the conveyor system.
By considering these factors, you can determine the appropriate pulley size to ensure efficient and reliable operation of your conveyor system.
Last Updated on June 25, 2024 by Jordan Smith
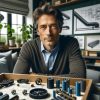
Jordan Smith, a seasoned professional with over 20 years of experience in the conveyor system industry. Jordan’s expertise lies in providing comprehensive solutions for conveyor rollers, belts, and accessories, catering to a wide range of industrial needs. From initial design and configuration to installation and meticulous troubleshooting, Jordan is adept at handling all aspects of conveyor system management. Whether you’re looking to upgrade your production line with efficient conveyor belts, require custom conveyor rollers for specific operations, or need expert advice on selecting the right conveyor accessories for your facility, Jordan is your reliable consultant. For any inquiries or assistance with conveyor system optimization, Jordan is available to share his wealth of knowledge and experience. Feel free to reach out at any time for professional guidance on all matters related to conveyor rollers, belts, and accessories.