Calculating Conveyor Pulley Weight
Understanding conveyor pulley weight in kg is crucial for the efficient operation of conveyor systems. Conveyor pulley weight impacts the overall performance, energy consumption, and lifespan of the conveyor. Accurate measurement of this weight in kilograms (kg) is essential for designing and maintaining effective conveyor systems. The weight of a conveyor pulley can vary significantly based on its size, material, and design specifications. Properly calculating and managing conveyor pulley weight ensures optimal tension, reduces wear and tear, and prevents system malfunctions. By comprehending the importance of conveyor pulley weight, operators can make informed decisions that enhance system reliability and efficiency.
Conveyor Pulley Weight:Classification
Conveyor pulleys are essential components of conveyor systems, used to drive the belt, change its direction, or provide tension. They come in various designs to suit different applications, and they are generally classified into two main types: Drum Conveyor Pulleys and Wing Conveyor Pulleys.
Drum Conveyor Pulleys
Drum pulleys are the most common type of conveyor pulley. They are cylindrical in shape and come in various diameters and lengths depending on the application. Drum pulleys are typically used in situations where the conveyor belt needs to be driven or tensioned.
Types of Drum Conveyor Pulleys:
- Drive Pulley: This pulley is connected to the motor and is responsible for driving the conveyor belt.
- Return/Tail Pulley: Located at the opposite end of the conveyor, this pulley guides the belt back to the drive pulley.
- Snub Pulley: Positioned close to the drive pulley, it increases the belt’s wrap angle around the drive pulley, enhancing the frictional grip.
- Bend Pulley: Used to change the direction of the conveyor belt.
Features:
- Smooth Surface: Provides a consistent grip on the conveyor belt.
- Lagging Options: Rubber or ceramic lagging can be added to increase friction and reduce wear.
Wing Conveyor Pulleys
Wing pulleys are designed for use in environments where there is a high possibility of material buildup on the pulley surface, such as in mining or bulk material handling applications. The unique design allows debris to be expelled, reducing the risk of conveyor belt slippage or damage.
Types of Wing Conveyor Pulleys:
- Standard Wing Pulley: Features a series of flat bars that are attached to the hub in a wing-like pattern, creating gaps for material to be expelled.
- Heavy-Duty Wing Pulley: Similar to the standard wing pulley but built with more robust materials for higher-stress applications.
Features:
- Self-Cleaning: The gaps between the wings allow for material to be ejected as the pulley rotates.
- Less Material Buildup: Reduces the risk of belt damage and extends the life of the conveyor system.
Key Differences
- Design: Drum pulleys have a smooth surface, while wing pulleys have a winged structure.
- Application: Drum pulleys are used where consistent contact with the belt is needed, while wing pulleys are preferred in dirty or abrasive environments to prevent material buildup.
Each type of pulley serves specific purposes within a conveyor system, ensuring efficient and reliable operation under various conditions.
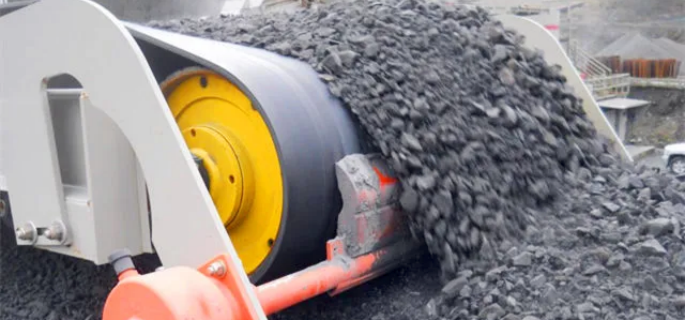
How to Calculate Conveyor Pulley Weight
Calculating the conveyor pulley weight involves the volume of the different components multiplying each by the material density. Finally, the weights of all components are summed up to get the total pulley weight. Here’s a step-by-step guide on how to perform this calculation:
Determine the Pulley Components
- Shell: The cylindrical outer body of the pulley.
- End Discs: The circular plates at both ends of the pulley shell.
- Shaft: The central axis that runs through the pulley and connects to the drive system.
Calculate the Volume of Each Component
Shell Volume:
- The shell is essentially a hollow cylinder.
- Formula for the volume of a hollow cylinder (shell):
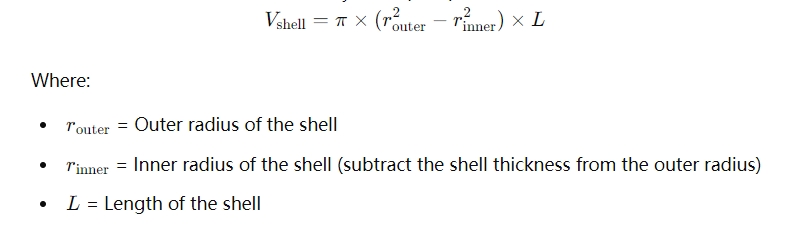
- End Disc Volume:
- The end disc is a solid cylinder (or two, one for each end).
- Formula for the volume of each end disc:
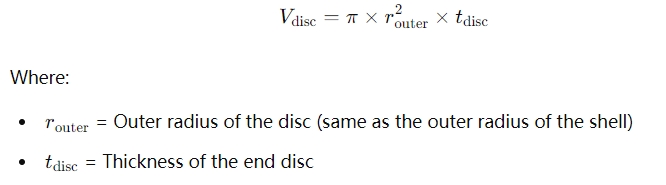
- Shaft Volume:
- The shaft is a solid cylinder.
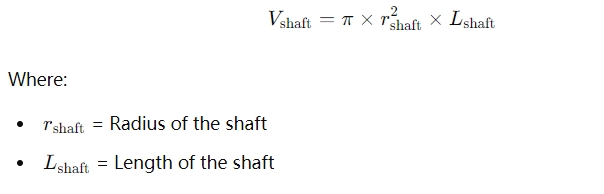
Determine the Material Density
- Identify the material of each component (e.g., steel, aluminum).
- Use standard density values (e.g., density of steel ≈ 7850 kg/m³).
Calculate the Weight of Each Component
- Multiply the volume of each component by the material’s density to get the weight.
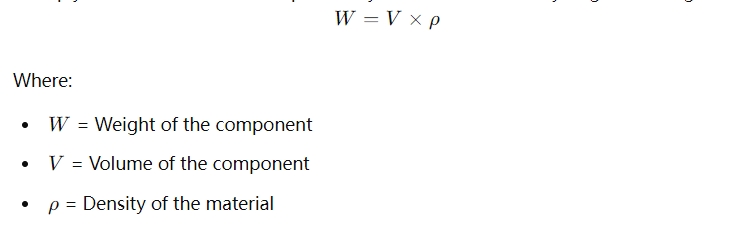
Sum the Weights
- Add the weights of the shell, both end discs, and the shaft to get the total pulley weight.

How to Determine the Proper Conveyor Pulley Weight
Determining the proper weight of a conveyor pulley involves considering several factors related to the conveyor system’s requirements, including the type of material being transported, the conveyor belt’s tension, the pulley size, and the system’s operating conditions. The goal is to ensure the pulley is strong and durable enough to withstand the forces it will encounter during operation without being unnecessarily heavy, which could increase costs and strain on the system. Here’s a step-by-step approach:
Identify Conveyor System Requirements
- Material Type: What material will be transported? Consider its weight, abrasiveness, and whether it’s corrosive.
- Belt Tension: The tension applied to the conveyor belt affects the load on the pulley. Higher tension generally requires a stronger, and potentially heavier, pulley.
- Belt Speed: Faster speeds may necessitate a more robust pulley design to handle dynamic loads.
- Operating Environment: Consider factors like temperature, moisture, dust, and the potential for material buildup, which might influence the choice of pulley design and material.
Select Pulley Type and Material
- Pulley Type: Choose between drum pulleys (typically heavier and stronger) or wing pulleys (lighter, self-cleaning, but potentially less robust).
- Material: Steel is common due to its strength and durability, but aluminum or composite materials may be chosen for lighter applications.
Calculate the Required Strength
- Calculate Belt Tension: Use the following formula to calculate belt tension: [ T = P ÷v ] Where:
- ( T ) = Belt tension (N)
- ( P ) = Power transmitted by the belt (W)
- ( v ) = Belt speed (m/s)
- Safety Factor: Apply a safety factor to account for unexpected loads or operational conditions. A typical safety factor ranges from 1.5 to 2.0.
Determine Pulley Dimensions
- Pulley Diameter: The diameter is usually determined based on the belt speed and tension. Larger diameters can handle higher tension but add weight.
- Face Width: The pulley width should be slightly wider than the belt width to ensure proper belt tracking.
- Shaft Size: Calculate the shaft size to ensure it can handle the torque and bending forces. The shaft’s diameter is critical for determining the pulley’s strength and weight.
Estimate Pulley Weight
- Shell Thickness: Calculate the shell thickness needed to handle the tension and stress without excessive deflection.
- End Disc Design: Design the end discs to handle the stress concentrations where the pulley connects to the shaft.
- Material Density: Use the material’s density to calculate the weight of the pulley components as outlined in the previous steps.
Perform Finite Element Analysis (Optional)
- Simulation: Conduct a finite element analysis (FEA) to simulate the pulley under load conditions. This analysis helps ensure that the pulley design is optimized for strength without unnecessary weight.
- Optimization: Adjust the design based on FEA results to achieve the best balance between weight and durability.
Consult Design Standards
- Industry Standards: Refer to industry standards such as CEMA (Conveyor Equipment Manufacturers Association) guidelines, which provide recommendations for pulley design based on various operational parameters.
Prototype and Testing
- Prototype: If possible, create a prototype pulley and test it under simulated operational conditions.
- Testing: Test the pulley to ensure it meets the strength and durability requirements without being excessively heavy.
Adjust for Specific Application
- Tailor to Application: Depending on the specific conveyor system (e.g., mining, bulk handling, food processing), adjust the design to meet particular needs, like corrosion resistance or ease of maintenance.
The proper conveyor pulley weight is a balance between the strength needed to handle the operational loads and the desire to minimize weight for cost, ease of installation, and reduced strain on the conveyor system. By considering the factors above and possibly using design optimization tools like FEA, you can determine the appropriate pulley weight for your specific application.
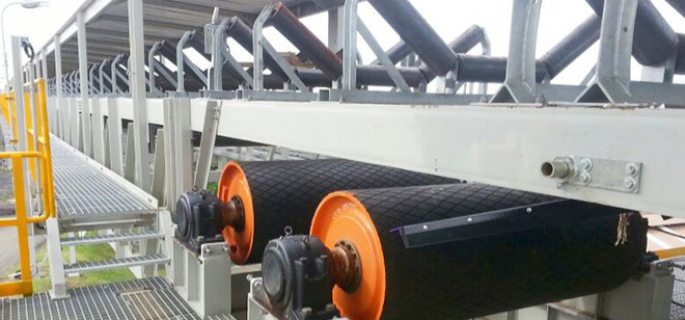
The Importance of Properly Calculating Conveyor Pulley Weight
Properly calculating the weight of a conveyor pulley is crucial for several reasons, all of which contribute to the overall efficiency, safety, and longevity of the conveyor system. Here are some key points highlighting the importance:
1. Ensuring Structural Integrity
- Avoiding Overload: If a pulley is not adequately designed and its weight is miscalculated, the pulley may not withstand the loads and stresses imposed by the conveyor belt tension, leading to potential structural failure. Proper calculation ensures that the pulley can handle the required forces without bending, cracking, or collapsing.
- Maintaining Balance: A pulley with an incorrect weight can lead to imbalances in the conveyor system, causing excessive vibrations, misalignment, or uneven wear on the belt and other components. This imbalance can reduce the system’s operational efficiency and increase maintenance costs.
2. Optimizing Conveyor System Performance
- Efficient Power Consumption: An overly heavy pulley requires more energy to rotate, leading to higher power consumption and operating costs. By accurately calculating the pulley weight, you can minimize unnecessary energy usage, leading to more cost-effective and environmentally friendly operations.
- Maximizing Belt Life: The proper pulley weight helps ensure that the conveyor belt runs smoothly and evenly across the pulley, reducing the risk of excessive wear or damage. This, in turn, extends the life of the conveyor belt and reduces the frequency and cost of replacements.
3. Enhancing Safety
- Preventing Accidents: Overloaded or improperly balanced pulleys can lead to catastrophic failures, which may cause accidents or injuries to personnel. Proper weight calculation reduces the risk of pulley or belt failure, thereby enhancing the overall safety of the conveyor system.
- Compliance with Safety Standards: Ensuring that the pulley weight is accurately calculated helps in meeting industry safety standards and regulations, which are designed to protect both workers and equipment.
4. Reducing Maintenance Costs
- Minimizing Wear and Tear: A pulley with the correct weight distribution reduces unnecessary stress on the conveyor belt and other system components, leading to less frequent maintenance and lower repair costs.
- Extending Component Life: By avoiding excessive weight, the entire conveyor system—especially critical components like bearings, shafts, and the belt—will have a longer service life, reducing the need for replacements and downtime.
5. Facilitating Installation and Upgrades
- Ease of Installation: Correctly calculated pulley weight ensures that the pulley can be installed without requiring overly complex or expensive lifting equipment. This makes the installation process more straightforward and cost-effective.
- Adaptability for Upgrades: When upgrading or modifying the conveyor system, knowing the accurate weight of existing pulleys is essential for ensuring compatibility with new components or changes in system design.
6. Cost Efficiency
- Material Cost Optimization: Overestimating the weight can lead to the use of more material than necessary, increasing costs. Conversely, underestimating the weight could lead to a need for more frequent repairs or replacements. Accurate weight calculations allow for cost-effective use of materials.
- Energy Savings: Properly weighted pulleys help in maintaining optimal power usage, reducing operational costs over time.
7. Ensuring System Longevity
- Balanced Load Distribution: Correctly weighted pulleys help in evenly distributing the load across the conveyor system, reducing stress on all components and ensuring the longevity of the entire system.
- Preventing Fatigue Failure: Over time, improper pulley weight can lead to fatigue failure in both the pulley and other associated components, shortening the lifespan of the conveyor system.
8. Meeting Design Specifications
- Alignment with Design Goals: Proper weight calculation ensures that the pulley meets the intended design specifications and performance criteria, leading to a system that operates as intended under various conditions.
- Consistency with Engineering Standards: Adhering to engineering standards and best practices in weight calculation helps in achieving a conveyor system that is reliable, efficient, and safe.
Properly calculating the weight of a conveyor pulley is a critical step in designing, installing, and maintaining an efficient and reliable conveyor system. It impacts the system’s performance, safety, cost-effectiveness, and longevity, making it an essential aspect of conveyor system engineering. Neglecting this calculation can lead to significant operational problems, safety hazards, and increased costs, highlighting the need for precise and accurate engineering practices.
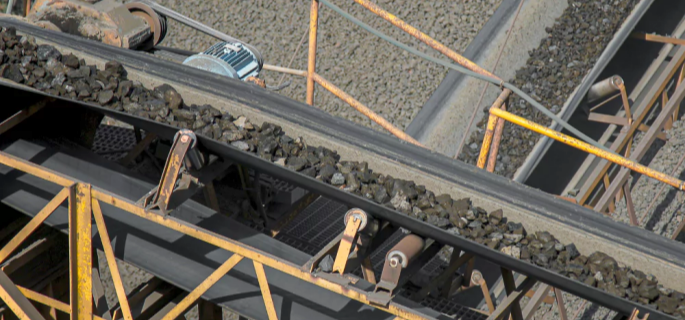
Utilizing a Conveyor Pulley Weight Calculator
Description of How a Conveyor Pulley Weight Calculator Works
A conveyor pulley weight calculator is an essential tool for engineers and technicians involved in the design and maintenance of conveyor systems. The primary function of this calculator is to estimate the weight of a conveyor pulley based on specific input parameters. These parameters typically include the pulley’s diameter, width, material, and other relevant dimensions.
When using a conveyor pulley weight calculator, users start by entering the basic dimensions of the pulley. This includes the diameter and face width, which are crucial in determining the overall size and weight of the pulley. The material of the pulley is another critical factor, as different materials have varying densities. For instance, a pulley made from steel will have a different weight than one made from aluminum or plastic, even if their dimensions are identical.
The calculator also considers the construction type of the pulley. Pulleys can be solid, winged, or drum types, each having a different structure and weight distribution. By inputting the construction type, the calculator can provide a more accurate weight estimate.
Advanced conveyor pulley weight calculators may also include additional parameters such as the shaft diameter, hub size, and whether the pulley is crowned or flat. These factors further refine the accuracy of the weight calculation. Once all the necessary information is entered, the calculator processes the data and outputs the estimated weight of the pulley.
Benefits of Using a Calculator for Determining Pulley Weight
Using a conveyor pulley weight calculator offers several significant benefits:
- Accuracy: Manually calculating the weight of a conveyor pulley can be prone to errors, especially when dealing with complex dimensions and varying materials. A calculator ensures precise calculations by using standardized formulas and up-to-date material density data.
- Time-Saving: Calculating the weight of a pulley manually can be time-consuming, particularly for larger systems with multiple pulleys. A calculator streamlines this process, providing quick and reliable results, which allows engineers to focus on other critical tasks.
- Design Optimization: Accurate weight calculations are essential for the design and optimization of conveyor systems. Knowing the exact weight of each pulley helps in selecting appropriate motor power, supporting structures, and other system components, ensuring efficiency and longevity of the conveyor system.
- Cost Efficiency: By accurately determining the weight of conveyor pulleys, companies can avoid over-engineering or under-engineering their systems. This balance reduces unnecessary material costs and potential downtime due to component failure, leading to overall cost savings.
- Ease of Use: Most conveyor pulley weight calculators are user-friendly and require minimal training to use effectively. They often come with intuitive interfaces and detailed instructions, making them accessible to both seasoned engineers and new technicians.
Conveyor Pulley Weight Chart
A conveyor pulley weight chart is a comprehensive reference tool that provides detailed information about the weights of various pulley types and sizes. These charts are typically created by pulley manufacturers and are used by engineers and designers to select the appropriate pulley for their conveyor systems.
The chart includes a range of pulley sizes, from small to large diameters and widths, and lists the corresponding weights for each size. It also categorizes pulleys based on their construction types, such as drum pulleys, wing pulleys, and solid pulleys. Each category may have its own specific weight range due to differences in design and material usage.
How to Read and Interpret the Chart for Different Pulley Types and Sizes
Reading and interpreting a conveyor pulley weight chart involves several steps:
- Identify the Pulley Type: Start by identifying the type of pulley you need for your conveyor system. This could be a drum pulley, wing pulley, or another type. Each type has unique characteristics and applications, which are reflected in their weight specifications.
- Determine the Pulley Dimensions: Once you have identified the pulley type, determine the required dimensions for your application. This includes the pulley diameter and face width. These dimensions are usually specified in inches or millimeters.
- Locate the Dimensions on the Chart: Find the corresponding dimensions on the weight chart. Most charts are organized in a tabular format, with dimensions listed along the rows and columns. Locate the row and column that match your pulley’s diameter and face width.
- Check the Weight Information: After locating the correct dimensions, check the weight information provided in the chart. This will give you the estimated weight of the pulley based on its size and type. Some charts may also include additional details such as material type and construction specifics.
- Consider Additional Factors: If the chart includes information on material and construction, take these factors into account as well. The weight can vary significantly based on whether the pulley is made from steel, aluminum, or another material. Additionally, construction details such as whether the pulley is solid or has a winged design can affect the weight.
- Cross-Reference with Design Requirements: Finally, cross-reference the weight information with your conveyor system’s design requirements. Ensure that the pulley weight fits within the system’s load capacity and that it aligns with other components’ specifications.
Understanding how to read and interpret a conveyor pulley weight chart is crucial for designing efficient and reliable conveyor systems. It allows engineers to make informed decisions, ensuring that the selected pulleys meet the operational demands and constraints of their specific applications.
Conveyor Pulley Weight: Conveyor Pulley Catalogue
Overview of a Typical Conveyor Pulley Catalogue
A conveyor pulley catalogue is a comprehensive document that provides detailed information about the various pulleys offered by a manufacturer. It serves as a valuable resource for engineers, designers, and procurement specialists who need to select the appropriate pulleys for their conveyor systems.
A typical conveyor pulley catalogue includes several key sections:
- Introduction: This section provides an overview of the catalogue and the manufacturer’s offerings. It may include a company profile, a summary of their expertise, and an outline of the product range.
- Product Listings: The main body of the catalogue consists of detailed listings for each type of pulley. Each listing includes specifications such as diameter, face width, shaft size, and construction type. The listings may be organized by pulley type, with separate sections for drum pulleys, wing pulleys, and other types.
- Technical Specifications: In addition to basic dimensions, the catalogue includes technical specifications such as material type, weight, and load capacity. These details are crucial for ensuring that the selected pulleys meet the operational requirements of the conveyor system.
- Weight Information: A dedicated section of the catalogue is often devoted to conveyor pulley weight information. This section includes weight charts, tables, and calculators to help users determine the weight of each pulley based on its dimensions and material.
- Installation and Maintenance Guidelines: To ensure proper installation and long-term performance, the catalogue includes guidelines and best practices for installing and maintaining conveyor pulleys. This section may cover topics such as alignment, tensioning, lubrication, and inspection procedures.
- Accessories and Spare Parts: Many catalogues also include information about available accessories and spare parts. This can include items such as bearings, shafts, seals, and mounting hardware, which are essential for the installation and maintenance of conveyor pulleys.
Key Features to Look for in the Catalogue Related to Pulley Weight
When exploring a conveyor pulley catalogue, there are several key features to look for related to pulley weight:
- Comprehensive Weight Charts: A good catalogue should include comprehensive weight charts that provide detailed weight information for various pulley sizes and types. These charts should be easy to read and interpret, with clear labels and units of measurement.
- Material Information: Since the weight of a pulley can vary significantly based on the material used, the catalogue should include detailed information about the materials available. This includes the density of each material and how it affects the overall weight of the pulley.
- Customization Options: Some conveyor systems may require custom pulleys with specific dimensions and weights. Look for catalogues that offer customization options and provide information on how to request custom pulleys. This may include contact information for sales representatives or technical support teams.
- Weight Calculators: In addition to weight charts, some catalogues include online or downloadable weight calculators. These tools allow users to input specific dimensions and material types to get an instant weight estimate. This feature is especially useful for quickly assessing the weight of custom or non-standard pulleys.
- Detailed Product Descriptions: Each pulley listing should include a detailed description that highlights its key features and benefits. This includes information on construction type, load capacity, and any special features that may affect the weight, such as reinforced hubs or special coatings.
- Installation and Maintenance Tips: Proper installation and maintenance are crucial for ensuring that the pulleys perform as expected and maintain their weight specifications over time. Look for catalogues that include detailed tips and guidelines for installing and maintaining pulleys.
- Case Studies and Examples: Some catalogues include case studies or examples of how their pulleys have been used in real-world applications. These examples can provide valuable insights into the performance and weight characteristics of the pulleys in different settings.
By paying attention to these key features, users can make informed decisions when selecting pulleys and ensure that they choose products that meet their specific weight and performance requirements.
Understanding and utilizing tools like the conveyor pulley weight calculator, weight charts, and detailed catalogues are essential for designing and maintaining efficient conveyor systems. These resources provide accurate weight information, streamline the selection process, and ensure that the pulleys meet the operational demands of various applications. Whether designing a new system or maintaining an existing one, these tools are invaluable for achieving optimal performance and cost efficiency.
Conveyor Pulley Weight: Analyzing Conveyor Pulley Dimensions
Importance of Dimensions in Relation to Pulley Weight
In the realm of conveyor systems, the dimensions of conveyor pulleys are critical parameters that influence their overall weight and performance. Conveyor pulley weight is a pivotal factor that affects the efficiency, safety, and operational costs of conveyor systems. The dimensions of a conveyor pulley, including its diameter, face width, and shaft size, play a significant role in determining its weight.
The diameter of a pulley is one of the primary dimensions that impact its weight. Larger diameters generally result in heavier pulleys due to the increased amount of material required for construction. Additionally, the face width, which is the length of the pulley surface in contact with the conveyor belt, also contributes to the weight. A wider face requires more material, thus increasing the overall pulley weight.
Shaft size, which pertains to the diameter and length of the pulley’s shaft, further adds to the weight. The shaft must be robust enough to handle the forces exerted by the conveyor belt and the materials being transported, necessitating a certain thickness and length that correspondingly increase the weight.
The importance of these dimensions extends beyond mere weight considerations. They also affect the pulley’s ability to withstand operational stresses, its alignment with the conveyor belt, and the smoothness of belt movement. A pulley that is too heavy might require stronger support structures and more powerful motors, leading to higher installation and maintenance costs. Conversely, a pulley that is too light might not offer sufficient structural integrity, potentially leading to premature wear or failure.
Common Dimensions and Their Impact on Overall Pulley Weight
Conveyor pulleys come in a variety of standard dimensions, each suited for specific applications. Common pulley diameters range from as small as 4 inches to over 60 inches, depending on the size of the conveyor system and the load it is designed to carry. Similarly, face widths can vary from a few inches to several feet.
For instance, a pulley with a diameter of 12 inches and a face width of 36 inches will weigh significantly less than a pulley with a diameter of 48 inches and a face width of 60 inches. The materials used for construction, such as steel or aluminum, also influence the weight. Steel pulleys are generally heavier but offer greater strength and durability compared to aluminum pulleys, which are lighter but may not be suitable for heavy-duty applications.
The interplay between these dimensions means that each must be carefully considered during the design phase. Engineers must balance the need for strength and durability with the practical limitations imposed by weight. This balance ensures that the pulley can perform effectively without imposing unnecessary strain on the conveyor system.
Understanding the relationship between conveyor pulley dimensions and their weight is crucial for designing efficient and reliable conveyor systems. By optimizing these dimensions, engineers can create pulleys that meet the specific needs of their application while minimizing costs and maximizing performance.
Heavy Duty Conveyor Pulley Weight Considerations
Characteristics of Heavy-Duty Conveyor Pulleys
Heavy-duty conveyor pulleys are designed to handle the most demanding industrial applications, where the loads are substantial, and the operational conditions are harsh. These pulleys are characterized by their robust construction, typically using high-strength materials such as reinforced steel, to withstand the intense forces and stresses they encounter.
The design of heavy-duty pulleys often includes thicker shells, larger diameters, and wider faces compared to standard pulleys. These features contribute to a significant increase in conveyor pulley weight. The thicker shells provide additional structural integrity, allowing the pulley to endure the wear and tear associated with continuous operation under heavy loads. Larger diameters help distribute the load more evenly, reducing the risk of belt slippage and enhancing the overall efficiency of the conveyor system.
Additionally, heavy-duty pulleys often incorporate advanced features such as reinforced end discs, heavy-duty bearings, and enhanced shaft designs. These features ensure that the pulley can operate reliably over extended periods, even in challenging environments such as mining, construction, and bulk material handling.
How Weight Influences the Performance of Heavy-Duty Pulleys
The weight of a heavy-duty conveyor pulley is a crucial factor that influences its performance in several ways. Firstly, the weight affects the pulley’s rotational inertia. Heavier pulleys have greater inertia, which can be advantageous in maintaining a steady rotational speed under load. This stability is essential for ensuring smooth and consistent operation, especially in applications where sudden changes in load can occur.
However, the increased conveyor pulley weight also means that the supporting structure must be capable of handling the additional load. This requirement can lead to higher costs for the support framework and drive systems. Moreover, heavier pulleys necessitate more powerful motors to achieve the desired rotational speed, further increasing the overall operational costs.
Another important consideration is the impact of weight on installation and maintenance. Heavy-duty pulleys can be challenging to install and may require specialized equipment and procedures. Maintenance activities such as replacing bearings or refurbishing the pulley surface also become more complex and time-consuming due to the increased weight.
Despite these challenges, the benefits of heavy-duty pulleys often outweigh the drawbacks. Their enhanced durability and reliability make them indispensable in industries where downtime can result in significant financial losses. By carefully considering the weight and its implications, engineers can design pulley systems that deliver optimal performance while minimizing operational costs.

Conveyor Pulley Weight: Methods for Conveyor Pulley Diameter Calculation
Steps Involved in Calculating the Diameter of a Conveyor Pulley
Calculating the diameter of a conveyor pulley involves several steps that take into account various factors such as the belt size, the load to be carried, and the operational conditions. The following steps outline a typical approach to pulley diameter calculation:
- Determine the Belt Size: The width and thickness of the conveyor belt are critical factors in determining the pulley diameter. The belt size must be chosen based on the maximum load it will carry and the speed at which it will operate.
- Calculate the Belt Tension: The tension in the conveyor belt is influenced by the load, the incline of the conveyor, and the friction between the belt and the pulleys. Accurate calculation of belt tension is essential for selecting an appropriate pulley diameter.
- Consider the Load: The type and weight of the material being transported affect the required pulley diameter. Heavier loads generally require larger diameters to ensure that the belt can handle the stress without slipping or experiencing excessive wear.
- Factor in the Speed: The operational speed of the conveyor system impacts the pulley diameter. Higher speeds necessitate larger diameters to reduce the rotational speed of the pulley and minimize the risk of belt slippage.
- Account for Environmental Conditions: Conditions such as temperature, humidity, and exposure to corrosive substances can affect the performance of the conveyor pulley. These factors should be considered when calculating the diameter to ensure long-term reliability.
- Use Engineering Formulas: Engineering formulas and industry standards provide guidelines for calculating the pulley diameter based on the above factors. These formulas often incorporate safety factors to account for unforeseen operational challenges.
Relationship Between Pulley Diameter and Weight
The diameter of a conveyor pulley has a direct relationship with its weight. Larger diameters typically result in heavier pulleys due to the increased volume of material required for their construction. This relationship is especially pronounced in heavy-duty applications, where the pulleys are designed to handle substantial loads and must therefore be constructed from robust materials.
The conveyor pulley weight increases as the diameter increases, which in turn affects the overall design and operation of the conveyor system. For example, a larger, heavier pulley requires more substantial support structures and more powerful motors to achieve the desired performance. This increase in weight can also impact the energy efficiency of the system, as more energy is required to rotate the heavier pulley.
In addition to the material volume, the choice of material itself plays a crucial role in determining the weight. Steel, being denser and stronger, results in heavier pulleys compared to materials like aluminum or composite materials. However, steel’s strength and durability often make it the preferred choice for heavy-duty applications despite the added weight.
Understanding the methods for calculating conveyor pulley diameter and the relationship between diameter and weight is essential for designing efficient and reliable conveyor systems. By carefully considering these factors, engineers can create pulleys that meet the specific demands of their application, ensuring optimal performance and longevity.
FAQs about Conveyor Pulley Weight
The weight of a conveyor belt can vary significantly based on the material, width, thickness, and length of the belt. For instance, a general-purpose rubber conveyor belt typically weighs between 10 to 20 kilograms per meter. Heavier-duty belts, designed for industrial applications, can weigh considerably more. The weight is an important factor to consider as it affects the overall load capacity and energy consumption of the conveyor system. Therefore, it’s essential to check the manufacturer’s specifications for accurate weight details when selecting a conveyor belt for your application.
PVC conveyor belts are generally lighter than rubber belts. On average, a PVC conveyor belt weighs between 5 to 10 kilograms per meter, depending on its thickness and width. The weight can be calculated more precisely by referring to the manufacturer’s data sheet, which usually provides detailed information about the belt’s weight per square meter. This information is crucial for determining the load that the conveyor system will handle and for calculating the power requirements of the drive system.
The counter weight on a conveyor system is used to maintain tension on the conveyor belt, ensuring smooth and efficient operation. It is typically located on the tail end of the conveyor and helps to keep the belt tight and prevent it from sagging or slipping off the rollers. The counter weight is adjusted based on the length and weight of the conveyor belt, as well as the load it carries. Proper tension is essential for minimizing wear and tear on the belt and other components, and for preventing downtime due to belt misalignment or slippage.
To measure the weight on a conveyor belt, a load cell system is commonly used. These systems include belt weighers or belt scales that are installed directly on the conveyor belt. The load cells measure the force exerted by the material on the belt, and this data is used to calculate the weight of the material being transported. Accurate weight measurement is essential for process control, inventory management, and ensuring compliance with industry regulations. Modern systems often integrate with digital controllers and software for real-time monitoring and data analysis, enhancing operational efficiency and accuracy.
To calculate the weight of a pulley, you need to consider the material it is made from, its dimensions (diameter, thickness, and width), and its design (solid or with spokes). The basic formula involves calculating the volume of the pulley and multiplying it by the density of the material. For a solid cylindrical pulley, the formula is:
Weight=Volume×Material Density
The volume of the pulley can be calculated using the formula for the volume of a cylinder:
Volume=π×(Radius)2×Width
Then multiply this volume by the material density (e.g., steel has a density of approximately 7850 kg/m³).
The weight of a conveyor system can be calculated by summing the weights of all its components, including the conveyor belt, rollers, pulleys, frame, and any other mechanical parts. For a basic estimation, you can add up the weight per meter of the conveyor belt (which is often provided by the manufacturer) multiplied by the total length, along with the weight of the pulleys and support structure. The formula would look like this:
Conveyor Weight=(Belt Weight per Meter×Belt Length)+Total Pulley Weight+Frame Weight+ Additional Components Weight
Pulleys do not reduce the actual weight of a load but rather reduce the force required to lift it. The reduction depends on the configuration of the pulley system. For a simple pulley, the force required is equal to the weight of the load. However, for a system with multiple pulleys (e.g., a block and tackle), the force required is reduced by the number of ropes supporting the load. The mechanical advantage (MA) is given by:
Mechanical Advantage (MA)=Number of Ropes Supporting the Load
The weight reduction felt by the operator (or system) is:
Effective Force=Load Weight ÷ MA
Yes, the weight of the pulley matters, especially in industrial applications like mining. A heavier pulley adds to the overall load on the system, which can affect the tension in the conveyor belt and the power required to drive the system. In some cases, a heavier pulley may be necessary for durability and inertia, but it increases the overall energy consumption and structural load.
If you use a two-pulley system (like a simple block and tackle), it can theoretically reduce the force required to lift a load by half. This is because the load is distributed over two ropes, effectively doubling the mechanical advantage:
Mechanical Advantage=2
Effective Force=Load Weight ÷ 2
However, this assumes an ideal system with no friction or other losses.
No, a conveyor belt is not a pulley. A conveyor belt is a continuous loop of material used to transport objects, often driven by pulleys. The pulleys in a conveyor system are the rotating components that move the belt along, often consisting of a drive pulley and an idler pulley. The belt itself is the medium that carries the load.
In heavy industries like mining, conveyors are critical components for moving bulk materials efficiently, and understanding the role of pulleys within these systems is essential for their effective operation.
Last Updated on August 13, 2024 by Jordan Smith
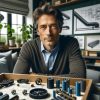
Jordan Smith, a seasoned professional with over 20 years of experience in the conveyor system industry. Jordan’s expertise lies in providing comprehensive solutions for conveyor rollers, belts, and accessories, catering to a wide range of industrial needs. From initial design and configuration to installation and meticulous troubleshooting, Jordan is adept at handling all aspects of conveyor system management. Whether you’re looking to upgrade your production line with efficient conveyor belts, require custom conveyor rollers for specific operations, or need expert advice on selecting the right conveyor accessories for your facility, Jordan is your reliable consultant. For any inquiries or assistance with conveyor system optimization, Jordan is available to share his wealth of knowledge and experience. Feel free to reach out at any time for professional guidance on all matters related to conveyor rollers, belts, and accessories.