Conveyor rollers are integral components of material handling systems, providing efficient movement of goods in various industrial settings. roller conveyors are designed to support and move bulky items, such as boxes and totes, with minimal effort. Conveyor rollers are particularly useful in warehousing, package handling, manufacturing, and distribution tasks. The versatility of conveyor rollers is evident in their application in both powered and unpowered (gravity-flow) roller conveyors. In a roller conveyor system, rollers can be used singly or together to form a continuous surface, accommodating various sizes and types of packages for efficient transport. Conveyor rollers are crucial for the smooth, efficient transport of goods in diverse settings, offering adaptability and ease of use in material handling systems.
GRAM Conveyor’s popular products about Conveyor Roller:
2.5″ Dia – Heavy Duty Rollers Conveyor
High quality dustproof waterproof carrier plastic nylon conveyor rollers
133 mm – 202 mm Conveyor Impact Roller
Double Sealed Bearing Ceramic Conveyor Rollers
Carrying Garland Idlers-Optimal
Anticorrosion Polymer Roller (Housings And Tube) for Medum-Heavy Duty
Silent Roller Conveyor | Quiet, Efficient and Waterproof
Guide Rollers – Precision Pulley / Idler
Steel Conveyor Roller I as Support Rollers for Roller Stand or Conveyor Rollers
GRAM Conveyor Offers The Following Types of Conveyor Rollers
At GRAM Conveyor, we take immense pride in offering a diverse range of high-quality conveyor rollers meticulously designed to meet your unique material handling needs. Whether you’re operating in a fast-paced warehouse, a manufacturing plant, or a specialized production facility, our extensive selection ensures that you find the perfect solution to streamline your workflow and enhance productivity. We understand the critical role that conveyor rollers play in efficient material transport, which is why we focus on delivering products that embody excellence in durability, performance, and reliability.
How to Choose The Right Conveyor Roller?
Selecting the appropriate conveyor roller is crucial to optimizing your material handling system.
1.Identify Your Material Handling Needs
Type of Material: Understand the nature of the material being transported (e.g., fragile, abrasive, corrosive).
Weight of the Load: Determine the average and maximum weight of the materials.
Size and Shape of the Load: Consider the dimensions and shape to ensure proper roller spacing.
2.Consider Roller Type and Material
Gravity Rollers: Best for lightweight or non-powered applications.
Powered Rollers: Ideal for continuous movement in powered conveyor systems.
Tapered Rollers: Suitable for curved conveyor paths.
Sprocket-Driven Rollers: Designed for heavy-duty applications with reliable chain-driven power.
Grooved Rollers: Work well with belt-driven systems for better tracking.
Stainless Steel Rollers: Perfect for corrosive environments or industries requiring high hygiene.
3.Check the Roller Diameter and Length
Roller Diameter: Choose a diameter that supports the load without deflection.
Roller Length: Ensure it is suitable for the width of your conveyor frame and load.
4.Select the Appropriate Roller Bearings
Ball Bearings: Offer high-speed operation and low friction.
Precision Bearings: Ensure smooth and quiet movement.
Sealed Bearings: Protect against dust and moisture in harsh environments.
5.Choose the Shaft Type and Mounting Style
Plain Shaft: Works well with set screws or retaining pins.
Hex Shaft: Provides anti-rotation features.
Spring-Loaded Shaft: Allows quick and easy installation and removal.
6.Evaluate Roller Load Capacity
Ensure the selected rollers can handle the maximum load per unit.
7.Consider Environmental Factors
Temperature: Choose materials that can withstand extreme temperatures.
Corrosive Elements: Opt for stainless steel or coated rollers in corrosive environments.
8.Assess Roller Speed and Performance Requirements
Ensure the rollers can operate at the required conveyor speed.
Verify the rollers can handle the required duty cycle (continuous or intermittent operation).
9.Think About Maintenance and Durability
Choose low-maintenance rollers to reduce downtime.
Select rollers with robust construction for long-term reliability.
When in doubt, consult a conveyor roller expert at GRAM Conveyor for personalized guidance and recommendations.By following these steps, you can confidently choose the right conveyor roller that will enhance your system’s efficiency and productivity.
The Featrues of Conveyor Roller
The Types of Conveyor Roller
Conveyor rollers are critical components of conveyor systems, used to transport materials across various distances in numerous industries. They come in different types designed to meet specific needs based on load requirements, environmental conditions, and operational speeds. Here’s a detailed description of the main types of conveyor rollers:
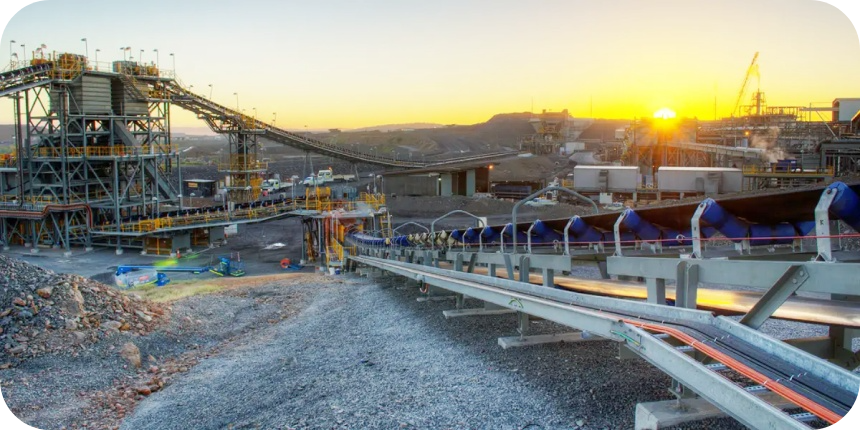
1. Gravity Rollers
- Design: Simple and non-powered.
- Material: Typically made of metal, plastic, or a combination.
- Function: Rely on gravity or manual force to move items.
- Application: Suitable for lightweight packages and when low cost and low maintenance are priorities.
2. Live (Powered) Rollers
- Design: Powered by electric motors.
- Material: Usually metal for added strength.
- Function: Can control the movement speed of items.
- Application: Ideal for handling heavy loads and essential in automated handling systems.
3. Grooved Rollers
- Design: Feature grooves that are designed to match with belts or o-rings.
- Material: Metal or plastic, depending on load requirements.
- Function: Provide drive belts with added traction, helping to propel materials.
- Application: Used in belt-driven conveyors, typically for moving items in sorting or assembly operations.
4. Sprocket Rollers
- Design: Equipped with sprockets that engage with a chain.
- Material: Predominantly metal to withstand the stress of engagement.
- Function: Ensures synchronized movement, vital for precise control of the conveyor system.
- Application: Frequently used in chain-driven conveyor systems.
5. Tapered Rollers
- Design: Taper towards one end.
- Material: Metal or reinforced plastic.
- Function: Allow the conveyor to curve around bends without the material slipping or getting misaligned.
- Application: Essential in systems that require curves or turns.
6. Impact Rollers
- Design: Built robust to absorb shocks.
- Material: Rubber-coated or with thick layers of rubber.
- Function: Absorb the impact of heavy or sharp objects.
- Application: Used in loading zones or where materials are dropped onto the conveyors from a height.
7. Return Rollers
- Design: Positioned on the underside of conveyor belts to support the return section.
- Material: Can be plain metal or rubber-coated.
- Function: Support the belt’s weight and prevent sagging.
- Application: Vital for maintaining the structural integrity and efficiency of belt conveyors.
8. Plastic Rollers
- Design: Lightweight and corrosion-resistant.
- Material: Various types of durable plastics.
- Function: Resist corrosion and wear, with reduced noise and friction.
- Application: Suitable for environments with moisture, chemicals, or where a quiet operation is needed.
9. Stainless Steel Rollers
- Design: Made of stainless steel for enhanced durability.
- Material: High-grade stainless steel.
- Function: Withstand harsh conditions including corrosive environments and washdown processes.
- Application: Ideal for the food processing industry, pharmaceuticals, and other areas where sanitation is a priority.
10. High-Temperature Rollers
- Design: Constructed to endure high temperatures.
- Material: Special alloys or heat-resistant materials.
- Function: Perform reliably in environments where temperature can degrade conventional materials.
- Application: Used in ovens, foundries, and other high-heat areas.
Application of Conveyor Roller
Conveyor rollers are versatile components used in various industries to move materials efficiently. They play a crucial role in optimizing the workflow of material handling systems. Here is a detailed description of the applications of conveyor rollers across different sectors:
7. Automotive Industry
- Assembly Lines: Convey vehicle parts and sub-assemblies through various stages of production.
- Paint Shops: Transport car bodies to painting and drying stations.
- Quality Inspection: Move finished vehicles through inspection lines.
8. Construction and Building Materials
- Cement and Concrete Plants: Transport cement, gravel, and sand for mixing.
- Brick and Tile Manufacturing: Move raw and finished materials between kilns, sorting, and packaging stations.
- Gypsum and Drywall Production: Convey raw gypsum and finished drywall panels.
9. Recycling and Waste Management
- Material Recovery Facilities (MRFs): Sort and separate recyclable materials from waste streams.
- E-Waste Recycling: Move electronic waste through disassembly and processing lines.
- Composting Plants: Convey organic waste for processing and packaging of compost.
10. Pharmaceutical and Chemical Industries
- Pharmaceutical Manufacturing: Convey medicinal products between processing, packaging, and quality control stations.
- Chemical Processing: Move raw materials and chemicals through different stages of production.
- Sterile Environments: Stainless steel and plastic rollers ensure safe transportation in sterile environments.
11. Retail Sector
- Sorting and Distribution: Move products in sorting centers and distribution warehouses.
- Retail Stores: Automated conveyors in large retail stores to transport products from storage to display areas.
12. Furniture Manufacturing
- Wood Processing: Convey logs and wooden planks between sawing, sanding, and assembling stages.
- Upholstery Lines: Move furniture frames through upholstering stations.
- Finished Product Transport: Transport completed furniture for inspection and packaging.
Each of these applications leverages specific types of conveyor rollers suited to the unique requirements of the industry. By providing efficient movement of materials, conveyor rollers help improve productivity, reduce labor costs, and ensure safety across a wide range of material handling environments.
Conveyor Roller Bearing
Conveyor roller bearings are essential components in the smooth operation of a roller conveyor. These bearings are specifically designed to be pressed into the ends of conveyor rollers, enabling them to rotate effortlessly on their axles during the conveying process. In any roller conveyor system, the efficiency and effectiveness largely depend on the condition of these bearings. They play a pivotal role in ensuring that the conveyor rolls move smoothly, which is crucial for the seamless transportation of goods. A conveyor roll equipped with high-quality bearings can significantly reduce conveyor noise, enhance performance, and extend the overall lifespan of the conveyor system.
When these bearings become worn or damaged, they can cause the rollers to seize up, leading to potential downtime or malfunction of the conveyor. Therefore, it’s vital to replace worn or damaged conveyor roller bearings promptly to maintain the efficiency of the system. Choosing the right conveyor roller bearing involves considering the specific tube diameter and gauge, shaft size, and the environment in which the conveyor will operate. There are various types of bearings available, each designed to meet different operational needs and environmental conditions. For instance, some bearings are shielded to keep out dirt and debris, ensuring a longer life in more demanding settings.
Conveyor Roller Shaft
The conveyor roller shaft is a crucial component in the mechanics of a roller conveyor for sale. The shaft, serving as the central axis for the conveyor roll’s rotation, is crucial for the roller conveyor system’s functionality, fitting tightly inside the roll to ensure efficient support and stability. The conveyor roll’s smooth functioning depends on its shaft’s strength and durability, typically made from sturdy materials like steel or stainless steel to endure constant stress and wear during operation. Besides supporting the conveyor roll, the shaft is crucial for attaching roller bearings, enabling smooth, low-friction rotation of the roll, with the right shaft and bearings being vital for the conveyor system’s efficient and quiet operation.
Conveyor Roller Tube
The conveyor roller tube form the main body of each roller in a roller conveyor system, providing the structure around which the entire system operates. The durability and efficiency of a rolling conveyor largely depend on the quality and design of these roller tubes. Conveyor roller tubes, typically made of steel, stainless steel, aluminum, rubber, or polyurethane, are chosen for their durability and ability to handle constant use and load weight, often with coatings or treatments to enhance longevity, reduce noise, or increase friction. The design of the conveyor roller tube is also important. It must be precisely engineered to fit seamlessly with other conveyor parts, such as bearings, shafts, and frames. This ensures smooth operation and reduces the risk of breakdowns or malfunctions.
Conveyor Roller Material
Conveyor roller material is a critical factor in determining the efficiency, durability, and application of a roller conveyor for sale.The material chosen for the rollers in roller conveyor system significantly impacts its performance in various industrial and commercial environments. When selecting a roller conveyor, understanding the properties of different materials is essential to ensure optimal functionality. Conveyor rollers are commonly made from steel, stainless steel, aluminum, rubber, or polyurethane; steel is preferred for its strength in heavy-duty applications, stainless steel for corrosion resistance in harsh environments, aluminum for lighter applications like packaging, and rubber or polyurethane for softer contact surfaces, suitable for delicate items or noise reduction.
Material choice for conveyor rollers, based on load capacity, environmental conditions, and conveyed material nature, ensures smooth, efficient operation with minimal maintenance. In summary, the material of conveyor rollers is a key consideration in the design and functionality of roller conveyors. It determines the conveyor’s suitability for different applications and its overall performance and longevity. Whether for industrial manufacturing, packaging, or distribution, selecting the appropriate roller material is crucial for the success of any roller conveyor system.
Pipe Conveyor Rollers
Pipe conveyor rollers are a specialized component in the material handling industry, designed specifically for use in pipe conveyor systems. When looking for a roller conveyor for sale, it’s important to consider the unique features of pipe conveyor rollers if your system involves the use of a pipe conveyor. These rollers play a crucial role in the functionality of roller conveyor system, particularly in systems where the conveyor belt forms into a pipe shape to enclose the material being transported. In a typical conveyor roll, rollers are the primary elements that facilitate the movement of the conveyor belt and the materials placed on it.
However, in a pipe conveyor system, the rollers have a unique function. They support the belt as it transitions from a flat shape at the loading and discharge points to a pipe shape along the conveying route. This transformation is essential for containing the material, preventing spillage, and reducing environmental pollution. Pipe conveyor rollers are designed to accommodate the curved transportation of materials, allowing for more flexible and efficient layout designs in confined spaces. They are also capable of supporting inclined transportation, leveraging the increased friction between the material and the inside of the belt in the pipe shape, which can lead to shorter conveyor lengths. Additionally, pipe conveyor rollers often come with preassembled brackets for easy and fast assembly onto the pipe frame. These brackets are typically designed with high corrosion resistance finishing, such as strong zinc plating and resin sealing, enhancing their durability and longevity in various industrial environments.
Pipe conveyor rollers are an integral part of pipe conveyor systems, offering unique advantages in material handling by enabling enclosed, curved, and inclined transportation. Their specialized design and features make them a key consideration when looking into roller conveyors for sale for specific industrial applications.
Maintenance of Conveyor Roller
Maintaining conveyor rollers is crucial for the efficient operation of conveyor systems, minimizing downtime, and prolonging the lifespan of the rollers and other associated components. Here’s a comprehensive guide on the maintenance of conveyor rollers:
1. Regular Inspection
- Visual Examination:
- Check for visible signs of damage such as cracks, dents, or deformation.
- Inspect for misalignment, which can cause belt tracking issues and uneven wear.
- Sound Test:
- Listen for unusual noises such as squeaking or grinding, which can indicate a lack of lubrication or internal damage.
2. Cleaning
- Surface Cleaning:
- Remove debris, dust, or other contaminants from the surface of rollers.
- Use appropriate cleaning agents based on the roller material (e.g., steel, rubber, or plastic).
- End Cap Cleaning:
- Ensure that the end caps are clean and free of obstructions that could lead to misalignment.
3. Lubrication
- Greasing Schedule:
- Follow a regular lubrication schedule as recommended by the manufacturer.
- Use grease or oil that is suitable for the roller bearing type.
- Automated Lubrication Systems:
- Install automatic lubrication systems for continuous lubrication of critical rollers.
4. Alignment Check
- Belt Alignment:
- Ensure that the belt runs straight and doesn’t drift to one side.
- Roller Alignment:
- Adjust rollers that are not square to the conveyor frame, which can cause tracking issues.
5. Bearing Maintenance
- Bearing Inspection:
- Regularly check the condition of bearings.
- Look for signs of excessive wear, corrosion, or damage.
- Bearing Replacement:
- Replace worn-out or damaged bearings promptly to prevent roller failure.
6. Roller Replacement Criteria
- Surface Wear:
- Replace rollers with excessive surface wear that affects conveyor performance.
- Diameter Reduction:
- If the roller diameter is significantly reduced due to abrasion, consider replacement.
- Structural Damage:
- Replace any roller showing cracks, bends, or other structural issues.
7. Impact Roller Maintenance
- Rubber Rings Inspection:
- Inspect rubber rings or impact surfaces for cracks or wear.
- Replace missing or heavily worn rings promptly.
8. Sprocket and Chain Maintenance
- Sprocket Teeth:
- Check for worn or damaged sprocket teeth in chain-driven rollers.
- Chain Lubrication and Tension:
- Ensure chains are well-lubricated and properly tensioned.
9. Tapered Roller Maintenance
- Taper Wear Check:
- Ensure the taper section isn’t worn unevenly, which could lead to belt misalignment in curved conveyors.
- Bearing Check:
- Check that bearings in tapered rollers rotate smoothly.
10. Environmental Adaptations
- Corrosive Environments:
- Use stainless steel or specially coated rollers in corrosive environments.
- Regularly wash down the rollers with fresh water if exposed to chemicals or salt.
- High-Temperature Areas:
- Monitor rollers in high-temperature areas for signs of heat degradation.
- Use heat-resistant lubricants.
11. Documentation
- Maintenance Log:
- Keep detailed maintenance records, including inspection dates, performed tasks, and component replacements.
- Manufacturer Recommendations:
- Follow the specific maintenance guidelines provided by the roller manufacturer.
12. Preventive Maintenance Schedule Example
- Daily:
- Perform a quick visual inspection for damage, misalignment, and unusual noises.
- Weekly:
- Clean roller surfaces.
- Check belt alignment and roller alignment.
- Monthly:
- Inspect bearings for wear or corrosion.
- Lubricate bearings if required.
- Quarterly:
- Inspect impact rollers for damage.
- Verify that all rollers are rotating smoothly.
- Annually:
- Replace damaged or heavily worn rollers.
- Conduct a thorough inspection of the entire conveyor system.
Custom Conveyor Rollers
Custom conveyor rollers are a specialized solution in the material handling industry, tailored to meet specific operational needs and challenges. These rollers are an integral part of rolling conveyor, designed to enhance efficiency and functionality in various industrial applications. When integrated into roller conveyor system, custom conveyor rollers can significantly improve the system’s performance, addressing unique requirements that standard rollers may not fulfill. In a typical roller conveyor, rollers are the primary components that facilitate the movement of the conveyor belt and the materials being transported.
Custom conveyor rollers take this a step further by offering design options and material choices tailored to specific needs. These may include variations in tubing materials like plastic, steel, or stainless steel, and bearings such as UHMW, Nylon, or steel ball bearings. Additionally, shafting options like steel, stainless steel, and stub shafts can be customized.
Design options for custom conveyor rollers are diverse, including features like cotter pin holes in the shaft, threaded ends on the shaft, grooves for drive belts, sprocket drive ends, and crowned rollers. These tailored features ensure that the conveyor rollers meet the exact requirements of different conveyor systems, whether it’s for handling delicate materials, operating in corrosive environments, or fitting into unique spatial configurations.
We offer Specialty roller solutions like tapered conveyor rollers, covered conveyor rollers, coated conveyor rollers, non-metallic conveyor rollers, gravity conveyor rollers, belt-driven conveyor rollers, and custom-sized conveyor rollers are available. Composite roller materials are also used to create custom rollers that resist rust, are lighter than steel, and can be formulated to increase grip, reduce noise, and minimize parcel damage. This customization extends to the material formulation phase, where polymers are blended to meet the unique requirements of a specific product or system. Custom conveyor rollers are a vital component in enhancing the efficiency and effectiveness of a rolling conveyor.
Gram fabricates rollers to your specification, applying our experience in materials and design to provide an economical roller with an extended useful life.We offer a range of design and material options to fit the specific needs of a roller conveyor system, ensuring that each roller conveyor operates optimally in its intended environment.
CONTACT US
Let us help you find a better solution!
FAQs about Gram Conveyor Roller
What is a roller conveyor?
A roller conveyor is a type of material handling system extensively used in heavy industries, such as mining and construction, to transport bulk materials and heavy loads efficiently. In these sectors, roller conveyors are designed to handle rugged and demanding conditions, where they transport large, heavy, and often abrasive materials like ore, coal, and gravel. The conveyor system consists of a series of rollers mounted on a frame, which supports and guides the material as it moves along the conveyor path. These rollers are typically made of durable materials like steel or heavy-duty plastic to withstand the harsh conditions. Roller conveyors can be powered or unpowered; powered versions use motors to drive the rollers, providing controlled and continuous movement of materials, while unpowered versions rely on gravity or manual effort. In heavy industries, powered roller conveyors are preferred for their ability to handle large volumes and facilitate automation, enhancing efficiency and reducing manual labor. Their robust design and ability to handle high loads make them integral to the material handling processes in mining, construction, and similar heavy-duty applications.
what are the hazards of roller conveyors?
Roller conveyors, while efficient for material handling, pose several hazards that need to be managed to ensure safety. One significant risk is pinch points, where rollers and moving parts can trap or pinch fingers, clothing, or other body parts, leading to serious injuries. Entanglement is another concern, as loose clothing, hair, or accessories can get caught in the moving rollers. This can result in severe injuries or equipment damage. Falls and trips around the conveyor system are also common, particularly if the area is cluttered or the conveyor is not properly installed. Mechanical failures, such as bearing malfunctions or belt misalignment, can cause sudden stops or erratic movements, posing risks to operators. Crushing injuries can occur if hands or limbs come into contact with the rollers, emphasizing the need for proper safety guards. Overloading the conveyor can lead to mechanical stress and potential breakdowns. Additionally, electrical hazards from powered conveyors and noise hazards from the system’s operation can pose health risks. Proper safety measures, including training, regular maintenance, and the use of safety guards, are essential to mitigate these hazards and protect workers.
What are the three types of conveyor?
The three main types of conveyors are:
Belt Conveyors: Use a continuous belt to transport materials.
Roller Conveyors: Use a series of rollers to move items.
Chain Conveyors: Use chains to transport materials along a track.
Where are roller conveyors used?
How heavy is a conveyor roller?
The weight of a conveyor roller can vary widely depending on its size and material. Roller weights can range from a few kilograms for smaller, lightweight rollers to over 100 kilograms for larger, heavy-duty rollers.
What is a roller bed conveyor?
A roller bed conveyor is a type of conveyor system designed for heavy-duty applications, commonly used in industries like mining and heavy manufacturing. It features a series of rollers mounted on a frame, creating a smooth surface for materials to be transported. In heavy industries, roller bed conveyors are essential for handling bulky and heavy items, such as ore, minerals, and large equipment parts. The robust design allows these conveyors to support significant loads and withstand harsh operating conditions. Their modularity and durability make them ideal for continuous material handling in demanding environments, ensuring efficient and reliable transport of materials throughout the production or processing line.
What is motorized roller conveyor?
A motorized roller conveyor is a sophisticated material handling system designed to efficiently transport heavy and bulk materials in demanding industrial environments, such as mining and construction. Unlike traditional roller conveyors that rely on gravity or manual effort, motorized roller conveyors use integrated electric motors to drive the rollers, providing a controlled and continuous movement of materials. This system is particularly advantageous in heavy industries where large volumes of materials, such as ore, coal, or construction debris, need to be moved across extensive distances and challenging conditions. The motorized rollers can be equipped with advanced features such as variable speed controls, which allow for precise adjustments to the movement speed, enhancing operational flexibility and efficiency. The robust design of motorized roller conveyors is built to withstand the harsh conditions typical of heavy industrial applications, including exposure to dust, moisture, and abrasive materials. This durability ensures reliable performance and reduces maintenance needs. Additionally, the automation provided by motorized rollers minimizes manual handling, improving safety and operational efficiency in demanding environments.
what is a live roller conveyor?
A live roller conveyor is a type of roller conveyor where the rollers are powered and actively move items along the conveyor line. Unlike gravity conveyors, which rely on the slope of the conveyor to move items, live roller conveyors use motors to drive the rollers.
what is the purpose of a conveyor?
The primary purpose of a conveyor is to transport materials or products from one point to another efficiently and continuously. Conveyors are used to improve productivity, reduce manual handling, and streamline operations in various industries.
What are the different types of conveyor rollers?
Different types of conveyor rollers include:
Gravity Rollers: Use gravity to move items.
Powered Rollers: Driven by motors to move items.
PVC Rollers: Made from PVC for lightweight applications.
Steel Rollers: Made from steel for heavy-duty applications.
Polyurethane Rollers: Provide quiet and non-marring movement.
What is a flexible roller conveyor used for?
A flexible roller conveyor is essential in heavy industries like mining and construction due to its adaptability and durability. In mining, these conveyors efficiently transport bulk materials such as ores and minerals across varying terrain and layouts, streamlining the movement from extraction sites to processing or stockpiling areas. Their modular design allows for quick reconfiguration to meet different operational needs, enhancing versatility on dynamic work sites. In construction, they handle materials like gravel and sand, reducing manual labor and improving efficiency. Constructed from robust materials like steel, flexible roller conveyors are built to withstand the harsh conditions of heavy industries, making them a reliable and effective solution for material handling. Their capacity to manage large loads and operate continuously helps boost productivity and safety on demanding job sites.
What does a conveyor person do?
A conveyor person typically operates, maintains, and monitors conveyor systems to ensure they function correctly. Their responsibilities may include setting up the conveyor, troubleshooting issues, performing regular maintenance, and ensuring safety standards are met.
What is the most common type of conveyor?
The most common type of conveyor is the belt conveyor. It is widely used due to its versatility, ease of use, and ability to handle various types of materials and product sizes.
what are the rollers on a conveyor called?
The rollers on a conveyor are commonly referred to as conveyor rollers.
what are the parts of a conveyor?
The main parts of a conveyor system typically include:
Conveyor Belt: The moving surface that carries the materials.
Rollers: Cylindrical components that support and move the belt.
Pulley: The rotating component that drives the belt.
Idlers: Support rollers that maintain belt tension and alignment.
Drive Motor: Powers the pulley to move the belt.
Frame: The structure that supports the conveyor system.
Take-Up Assembly: Adjusts belt tension.
Hoppers and Chutes: Direct materials onto and off the conveyor.
what is the difference between an idler and a roller?
Idler: An idler is a type of roller that does not drive the belt but supports it and helps maintain its alignment and tension. Idlers are typically used to support the belt along its length.
Roller: A roller is a general term that can include both powered and non-powered types. Powered rollers drive the belt or materials, while non-powered rollers, like idlers, merely support the belt or material.
What are conveyor belt wheels called?
Conveyor belt wheels are often called pulleys. They include drive pulleys (which power the belt) and tail pulleys (which support the belt at the end of the conveyor).
What is a snub roller on a conveyor?
A snub roller is a type of roller used to increase the contact area between the conveyor belt and the drive pulley, which improves belt traction and helps to correct belt alignment.
What is the difference between a belt conveyor and a roller conveyor?
Belt Conveyor: Uses a continuous belt to move materials. The belt is driven by pulleys and is suitable for moving items of various shapes and sizes over different distances.
Roller Conveyor: Uses a series of rollers to move materials. Rollers can be powered (live) or non-powered (gravity), and this type is often used for moving packages or pallets along a horizontal path.
which of the following are types of rollers found on conveyors?
Gravity Rollers
Powered Rollers
PVC Rollers
Steel Rollers
Polyurethane Rollers
what are the three types of rollers?
The three main types of rollers are:
Gravity Rollers: Use gravity to move items down an inclined conveyor.
Powered Rollers: Driven by motors to move items along a conveyor.
Conveyor Rollers: A general term that can include both gravity and powered rollers.
what is the purpose of rollers in conveyor?
Rollers in a conveyor system support and facilitate the movement of materials. They reduce friction between the conveyor belt and the supporting frame, enabling smoother and more efficient transport of items along the conveyor.
what type of conveyor is a roller?
A roller conveyor is a common industrial conveying system, particularly suited for heavy industries such as mining, metallurgy, and construction. It consists primarily of a series of horizontally arranged rollers, which rotate to move materials along the conveyor path. This type of conveyor is typically used for transporting heavy items like ores, coal, and construction materials due to its robust structure, which can withstand substantial loads. Roller conveyors can be divided into powered and non-powered types. Powered roller conveyors use motors to drive the rollers, while non-powered roller conveyors rely on gravity or manual pushing. The design of roller conveyors is flexible, allowing for customization to meet specific needs and adapt to various working environments and operational conditions. They are crucial in heavy industries for enhancing production efficiency and safety.
what is a belt roller?
A belt roller refers to a roller that is part of a conveyor system and supports the conveyor belt. Belt rollers can be idlers that help maintain belt tension and alignment or powered rollers that drive the belt.
what size are roller conveyors?
Roller conveyors come in various sizes depending on the application and requirements. Typical widths range from 400 mm (15.75 inches) to 1200 mm (47.24 inches), and lengths can vary from a few meters to several meters. Custom sizes are also available based on specific needs.
How do l know what size roller to use?
To determine the appropriate roller size, consider the following factors:
Load Capacity: Ensure the roller can handle the weight of the items being transported.
Roller Diameter: Larger diameters are generally used for heavier loads or longer spans.
Roller Material: Choose material based on the type of load and environment (e.g., steel for heavy-duty applications, plastic for lighter loads).
Spacing: Roller spacing should be close enough to support the load without causing sagging or instability.
How long is a standard roller?
The length of a standard roller can vary, but common lengths are 300 mm (11.81 inches), 600 mm (23.62 inches), and 1200 mm (47.24 inches). Custom lengths are available based on specific conveyor design needs.
How to choose a roller conveyor?
To choose a roller conveyor, consider the following:
Load Capacity: Ensure the conveyor can handle the weight and size of the items.
Roller Type: Decide between gravity or powered rollers based on the application.
Conveyor Length and Width: Match the conveyor size to your space and material dimensions.
Roller Spacing: Determine the spacing based on the size and weight of the items being transported.
Material and Environment: Choose rollers and components suitable for the operating environment and material being handled.
what is the spacing for roller conveyor rollers?
Roller spacing typically ranges from 150 mm (5.91 inches) to 500 mm (19.69 inches) depending on the load and type of roller used. For heavier loads, the spacing is usually closer to ensure adequate support.
what is the size of a standard conveyor?
Standard conveyor sizes can vary, but typical widths range from 300 mm (11.81 inches) to 1200 mm (47.24 inches) and lengths from 1 meter (3.28 feet) to several meters. Custom sizes are also available based on specific needs.
what is the diameter of a conveyor belt roller?
The diameter of a conveyor belt roller typically ranges from 19 mm (0.75 inches) to 100 mm (3.94 inches), depending on the load capacity and conveyor design.
what size rollers to use where?
In heavy industries such as mining, metallurgy, and construction, the size of rollers used in conveyor systems is crucial for efficient and reliable operation. For these applications, larger diameter rollers, typically 3 inches or more, are preferred. These rollers are designed to handle substantial loads, such as ores, coal, and heavy construction materials, and provide the necessary robustness and durability required in harsh working environments. Larger rollers offer greater stability and reduce the risk of material slippage, especially in high-speed conveying systems. Additionally, selecting rollers made from durable materials like stainless steel or those with protective coatings is essential to withstand abrasive conditions and ensure long-term performance. Thus, for heavy industrial use, opting for large, robust rollers is key to maintaining efficient and safe material handling operations.
which roller is used to track a conveyor belt?
The snub roller or tracking roller is used to help track a conveyor belt. It increases the contact area between the belt and the drive pulley, improving traction and alignment. Additionally, idler rollers positioned along the conveyor can assist with belt tracking.
How to roll up a conveyor belt?
To roll up a conveyor belt:
Turn off the conveyor system and ensure it is disconnected from the power source.
Release the tension from the belt by adjusting the take-up assembly or other tensioning mechanisms.
Remove the belt from the conveyor by loosening any fasteners or removing it from pulleys.
Carefully roll the belt starting from one end, keeping it as even and tight as possible to avoid kinks or creases.
Secure the rolled belt with ties or straps to keep it in place during storage or transportation.
How do you track a belt on a roller?
To track a belt on a roller:
Adjust the idler rollers to ensure the belt is centered and aligned properly.
Check the tension of the belt and adjust as necessary using the take-up assembly.
Inspect and adjust the snub rollers to ensure they are correctly positioned to guide the belt.
Regularly monitor and adjust as the belt moves to ensure consistent tracking.
what do you use to track a conveyor belt that is running on one side?
To correct a conveyor belt running to one side, you can use:
Tracking rollers or training idlers placed on the side of the conveyor to guide the belt back to the center.
Adjustable idler rollers that can be tilted or moved to help center the belt.
Conveyor belt alignment devices that apply tension to guide the belt into the correct position.
How roller chain can be used as conveyor belts?
In heavy industries such as mining, roller chains are used as conveyor belts to efficiently transport bulk materials across rugged and demanding environments. Roller chain conveyors consist of a series of interconnected chain links with rollers that move along a track, providing a durable and reliable means of material handling. These conveyors can handle substantial loads, including ores, rocks, and aggregates, and are designed to withstand harsh conditions like dust, moisture, and extreme temperatures. The robust construction of roller chains ensures longevity and reduces maintenance needs in challenging environments. Additionally, roller chain conveyors offer flexibility in design, allowing for various configurations and lengths to fit specific operational requirements. Their ability to operate continuously under heavy loads makes them a preferred choice in mining and other heavy industries where efficiency and durability are paramount.
What is the idler roller?
An idler roller is a non-powered roller that supports and guides the conveyor belt. It helps maintain proper belt tension, alignment, and supports the belt as it moves. Idlers are essential for preventing belt sagging and ensuring smooth operation.
How to adjust conveyor tracking?
To adjust conveyor tracking:
Check the alignment of the conveyor belt and rollers.
Adjust the idler rollers to ensure the belt is centered and aligned correctly.
Adjust the take-up assembly to ensure proper tension and reduce misalignment.
Inspect and adjust snub rollers as needed to guide the belt back to the center.
Monitor the conveyor during operation and make incremental adjustments as needed.
How do track rollers work?
Track rollers work by guiding and supporting the movement of a conveyor belt or other components along a track or rail system. They typically have a cylindrical design and are mounted to ensure smooth and precise movement. Track rollers can help with belt alignment, reduce friction, and ensure stable operation of the conveyor system.