Types of Materials for Conveyor Roller Bearings
A conveyor roller bearing is a crucial component that ensures smooth rotation of conveyor rollers. Positioned on the axle, it supports and guides rotational movement, facilitating the transportation of goods and materials along the conveyor system. By minimizing friction, these bearings help carry heavy loads efficiently, ensuring consistent movement even in challenging environments. Their role in improving efficiency makes them indispensable in material handling systems, directly impacting productivity. Whether for general or precision use, conveyor roller bearings are designed to withstand varying speeds and loads, adapting to different requirements. Their ability to streamline operations underscores their importance in diverse industries reliant on conveyor systems.
What Is Conveyor Roller Bearing
Conveyor roller bearings are specialized components designed to handle the complexities of conveyor systems across various industries. These bearings are tailored to meet specific operational demands, ranging from general-purpose use to applications requiring high precision and durability in harsh environments. Each type of bearing roller conveyor is engineered to provide optimal performance under different conditions, ensuring that conveyor systems operate smoothly and efficiently.
General Purpose Conveyor Roller Bearings
General purpose conveyor roller bearings are the most commonly used bearings due to their versatility and reliability. They are engineered to meet the demands of standard industrial applications, offering consistent performance and moderate load handling. Their design ensures they can accommodate a variety of conveyor roller systems, providing efficient and trouble-free rotation even under consistent daily use. By balancing affordability with functionality, these bearings remain the go-to choice for businesses seeking dependable performance across a broad spectrum of operational scenarios.
Key Features:
- Material Variability: Available in both steel and stainless steel to suit different environments.
- Load Capacity: Adequately supports moderate load weights typical of most industrial applications.
- Speed Compatibility: Performs well under standard conveyor speeds.
- Durability: Designed to withstand regular use without excessive maintenance.
- Cost-Effectiveness: Offers a balance between performance and affordability.
- Ease of Replacement: Standardized sizes make these bearings easy to replace.
- Availability: Widely available due to their common application.
- Versatility: Compatible with a wide range of conveyor systems.
Heavy-Duty Precision Conveyor Roller Bearings
Heavy-duty precision conveyor roller bearings are meticulously crafted to support substantial loads and maintain stability at higher speeds. They are indispensable in heavy manufacturing environments where machinery and products require a durable solution capable of enduring extreme conditions. Designed for industries like mining, automotive, and steel production, these bearings deliver precise, smooth operation without compromising on strength. Their robust construction, coupled with high-precision engineering, ensures reliable performance, reduced downtime, and minimized maintenance needs, which are essential in high-stress, high-impact environments.
Key Features:
- Enhanced Load Capacity: Engineered to support heavier loads, crucial in heavy manufacturing processes.
- High-Speed Tolerance: Maintains stability and performance at higher operational speeds.
- Robust Construction: Built with stronger materials to ensure longevity and resistance to wear.
- Precision Engineering: Offers tighter tolerances for improved performance.
- Optimal Lubrication: Features advanced lubrication capabilities to reduce friction and wear.
- Temperature Resistance: Capable of operating in higher temperature ranges.
- Shock Resistance: Designed to withstand shocks and impacts during operations.
- Reduced Vibration: Minimizes vibrations, which is critical for maintaining precision in operations.
Close-Tolerance Conveyor Roller Bearings
Close-tolerance conveyor roller bearings excel in high-speed and high-precision applications, providing exceptional rotational accuracy. They are designed for conveyor systems that demand minimal friction and superior alignment, ensuring accurate material transport even at high speeds. This precision reduces product damage and enhances sorting accuracy. Commonly utilized in industries like electronics, pharmaceuticals, and food processing, these bearings facilitate energy-efficient, noise-reduced, and vibration-free operation. They also integrate seamlessly into automated and synchronized systems, providing superior performance in technologically advanced environments.
Key Features:
- Precision Alignment: Ensures precise alignment of conveyor rollers.
- High Rotational Speeds: Supports higher than average rotational speeds with ease.
- Low Friction Coefficient: Minimizes friction to allow smoother operation.
- Enhanced Durability: Made with high-quality materials that offer extended service life.
- Reduced Maintenance Needs: Low maintenance requirements due to superior build quality.
- Improved Efficiency: Enhances overall system efficiency by reducing energy loss.
- Noise Reduction: Operates quieter compared to standard bearings.
- Seamless Integration: Easily integrates with existing conveyor systems designed for high accuracy.
Sealed Conveyor Roller Bearings
Sealed conveyor roller bearings are crafted to thrive in the harshest operating conditions, where contaminants like dust, moisture, and chemicals are prevalent. They feature advanced sealing technology to shield internal components, ensuring continued performance in wet, dusty, and high-temperature environments. Their resilience makes them ideal for industries like agriculture, food processing, and chemical manufacturing. These bearings reduce the risk of internal damage, prolonging lifespan and ensuring maintenance remains minimal. With sealed conveyor roller bearings, systems are protected against wear and tear, providing dependable, efficient operation while mitigating costly downtime.
Key Features:
- Seal Protection: Equipped with robust seals to prevent contaminants from entering the bearing.
- Corrosion Resistance: Materials used are resistant to corrosion caused by moisture and chemicals.
- Longer Lifespan: The seals extend the operational lifespan by protecting internal components.
- Low Maintenance: Seals reduce the need for frequent cleaning and maintenance.
- Enhanced Reliability: Provides consistent performance despite environmental challenges.
- Moisture Barrier: Effective against various forms of moisture, including steam and water spray.
- Dust Resistance: Keeps out particulate matter, maintaining clean internal mechanisms.
- Application Specific Design: Tailored for use in industries such as mining and agriculture, where exposure to harsh elements is common.
Through these distinct types, conveyor roller bearings cater to a broad range of industrial needs, ensuring that each system achieves optimal functionality with specifically designed components that meet the demands of different operational conditions.
Conveyor Roller Bearing Sizes
Choosing the right size for a conveyor roller bearing is crucial for the optimal performance and longevity of the conveyor system. The size of the bearing affects not only the fit and alignment within the conveyor roller but also influences load capacity, speed, and efficiency. Here, we will discuss the two primary dimensions to consider when selecting a bearing for roller conveyor: the axle size and the bearing’s outer diameter (OD). Each dimension serves a specific functional purpose and suits various industrial needs.
Axle Size Options
Axle size is a fundamental aspect to consider as it directly impacts the bearing’s fit and the overall stability of the conveyor system. The axle serves as the pivot point around which the roller rotates, so choosing the correct axle size is essential for smooth operation.
1/4 Inch Axle:
- Use Case: Best suited for light-duty applications, such as small package conveyance.
- Features: Provides minimal friction and is ideal for conveyors with limited space.
- Benefits: Enhances system speed without sacrificing stability.
5/16 Inch Axle:
- Use Case: Commonly used in distribution centers for medium-load items.
- Features: Offers a good balance between durability and flexibility.
- Benefits: Allows for a higher load capacity while maintaining moderate speed.
3/8 Inch Axle:
- Use Case: Ideal for heavier industrial applications requiring robust support.
- Features: Stronger axle size that supports greater loads effectively.
- Benefits: Provides enhanced durability and resistance against bending under stress.
7/16 Inch and Larger:
- Use Case: Used in heavy-duty industrial settings like mining and bulk material handling.
- Features: Offers maximum strength and can handle high impact loads.
- Benefits: Ensures longevity and reliability under extreme conditions.
Bearing Outer Diameter Sizes
The outer diameter of a conveyor roller bearing is critical as it determines how well the bearing fits within the roller housing and interacts with the load being transported. Proper OD sizing is vital for maintaining alignment and reducing wear on the roller system.
Sub-Inch Diameters:
- Use Case: Perfect for precision applications and small conveyors.
- Features: Compact and designed for light loads and high speeds.
- Benefits: Minimizes space usage and reduces weight on the conveyor.
1 to 1.5 Inches:
- Use Case: Suitable for general conveyor systems found in retail and packaging.
- Features: Balances between size and load capacity, offering versatility.
- Benefits: Provides good speed and reliability with moderate load handling.
1.5 to 2 Inches:
- Use Case: Common in manufacturing and processing industries where durability is crucial.
- Features: Larger bearings designed to handle increased loads.
- Benefits: Offers improved stability and extended lifespan under regular industrial use.
Over 2.5 Inches:
- Use Case: Ideal for extreme-duty applications requiring maximum load support.
- Features: Heavy-duty bearings capable of supporting the largest loads.
- Benefits: Ensures optimal performance and minimal downtime in critical operations.
By understanding these key dimensions—axle size and outer diameter—engineers and maintenance professionals can make informed decisions that enhance the efficiency and reliability of their conveyor systems.
Conveyor Roller Bearing Replacement
Proper replacement of conveyor roller bearings ensures the continued smooth operation of conveyor systems. With time and constant use, even the best bearings require maintenance or replacement to sustain their performance. This guide will provide clear signs indicating when it’s time for replacement and outline a detailed step-by-step process to ensure effective conveyor roller bearing replacement.
Signs It’s Time to Replace Bearings
Recognizing when a bearing conveyor roller requires replacement is crucial to prevent unexpected downtime and further damage to the conveyor system. Here are eight key signs that signal it’s time to replace:
- Excessive Noise: Bearings that make unusual grinding, clicking, or squeaking noises often indicate internal wear or misalignment.
- Decreased Efficiency: Reduced conveyor speed or increased energy consumption suggests that bearings aren’t rotating freely.
- Visible Wear: Cracks, rust, or deformation on bearing housings signal that replacements are due.
- Overheating: Bearings that generate excessive heat point to lubrication issues or internal damage.
- Frequent Vibrations: Bearings that vibrate or create tremors during operation show signs of misalignment or internal degradation.
- Roller Imbalance: Uneven roller movement may indicate a bearing imbalance or uneven load distribution.
- Excessive Lubrication Loss: Bearing seals that leak lubrication demonstrate wear, leading to increased friction.
- Load Handling Issues: Bearings struggling to support their designated load capacity can signal internal wear or damage.
Step-by-Step Replacement Guide
After identifying the need for conveyor roller bearing replacement, following these steps will ensure safe and efficient installation:
Identify Bearing Type and Size:
- Review system specifications or consult manufacturer documents to choose the correct replacement bearing.
- Ensure the replacement bearing matches the load requirements and environment.
Gather Tools and Safety Gear:
- Secure the necessary tools like wrenches, bearing pullers, and protective gloves.
Disconnect Power:
- Ensure the conveyor system is powered down and locked out to avoid accidents during maintenance.
Access the Bearing:
- Carefully remove any roller guards or protective coverings to access the bearing assembly.
Safely Remove Worn Bearings:
- Use appropriate tools to pull out the old bearing, avoiding damage to the roller or axle.
- Inspect other components for wear and clean the surrounding area.
Inspect the Axle and Roller:
- Check for wear or damage to the axle or roller shaft.
- Repair or replace if necessary before installing the new bearing.
Install New Bearings:
- Gently slide or press-fit the new bearing into the roller, ensuring proper alignment.
- Follow manufacturer instructions for securing the bearing.
Lubricate if Necessary:
- Apply the recommended lubricant or grease for smooth rotation and protection.
Test the Conveyor System:
- Reconnect power and perform a test run to ensure the new bearing is installed correctly.
- Listen for unusual sounds or vibrations and monitor for optimal performance.
By adhering to these guidelines, replacing a conveyor roller bearing can significantly improve the efficiency and lifespan of the entire system. Proper maintenance and timely replacements are key to reducing downtime and ensuring consistent material handling operations.
Conveyor Roller Bearing Types
Differentiating conveyor roller bearings based on material and bore type is essential for achieving optimal performance in various operational environments. Below, we delve into the specifics of each type, providing a detailed introduction followed by key features that define their suitability and performance in conveyor systems.
Material Types
Stainless Steel:
Stainless steel bearings are renowned for their corrosion resistance and durability, making them a preferred choice for applications in harsh or sterile environments. These bearings are essential in industries where resistance to rust and a clean operation are mandatory.
- Corrosion Resistance: Exceptionally resistant to oxidization and corrosion, stainless steel bearings are ideal for use in environments exposed to water, steam, and other corrosive elements.
- High-Temperature Tolerance: Maintains structural integrity and performance even under high thermal conditions, which is crucial in processes involving heat.
- Non-Magnetic Properties: Suitable for operations where magnetic interference must be avoided, such as in electronic manufacturing or in proximity to sensitive instrumentation.
- Hygienic Qualities: The non-porous surface prevents contamination accumulation, crucial in food processing, pharmaceuticals, and medical industries.
- Durability: Despite frequent exposure to challenging conditions, stainless steel bearings exhibit excellent longevity and reliability.
- Load Capacity: Engineered to handle moderate to heavy loads, making them versatile across various mechanical applications.
Carbon Steel:
Carbon steel bearings are popular due to their strength and cost-effectiveness. They are widely used in general engineering applications where extreme conditions are not a primary concern.
- Cost Efficiency: Provides a more economical solution without significantly compromising quality or performance.
- High Strength: Offers superior strength and hardness, which is beneficial in supporting heavy loads.
- Ease of Fabrication: Carbon steel is more malleable, allowing for easier machining and customization to specific requirements.
- Wide Availability: These bearings are commonly available, making them a quick and accessible option for replacements and repairs.
- Surface Modification: Can be treated with coatings or platings such as galvanization to enhance rust resistance.
- Versatile Use: Fits a broad spectrum of industrial applications, from agriculture to automotive conveyors.
Bore Types
Hex Bore:
Hex bore bearings are designed for high-torque applications where a secure axle grip is critical. The hexagonal inner profile provides a unique locking feature that prevents the bearing from rotating around the axle.
- Torque Transmission: Ideal for systems that require high torque output without slippage, ensuring efficient power transfer.
- Axle Engagement: Provides a tight fit that significantly reduces movement between the bearing and axle, promoting stability and precision.
- Reduced Wear: The firm engagement minimizes internal wear from misalignment, enhancing the bearing’s lifespan.
- Maintenance Advantages: Easier to service and replace due to the distinctive shape that allows for quick disengagement.
- Vibration Dampening: Helps in reducing operational noise and vibrations, a crucial factor in maintaining system integrity.
- Customization: Available in a variety of sizes to meet different mechanical and load requirements.
Round Bore:
Round bore bearings are the most common type used in various industries due to their ease of installation and ability to facilitate smooth, consistent rotational movement.
- Uniform Rotation: Ensures seamless and stable operation, which is essential for applications requiring continuous motion.
- Simplified Installation: The straightforward cylindrical design allows for easy installation and replacement.
- Friction Reduction: Promotes lower friction between the bearing and axle, leading to higher efficiency and reduced energy consumption.
- Lubrication Efficiency: Supports effective lubrication management, critical for prolonged bearing life and reduced maintenance.
- Versatility: Compatible with a wide range of axle sizes, enhancing their suitability for diverse industrial applications.
- Cost-Effectiveness: Typically less expensive than specialized bore types, providing a cost-effective solution without sacrificing quality.
These introductions and detailed points ensure a comprehensive understanding of the key features and applications of stainless steel and carbon steel bearings, as well as hex bore and round bore types, aiding in informed decision-making for conveyor system design and maintenance.
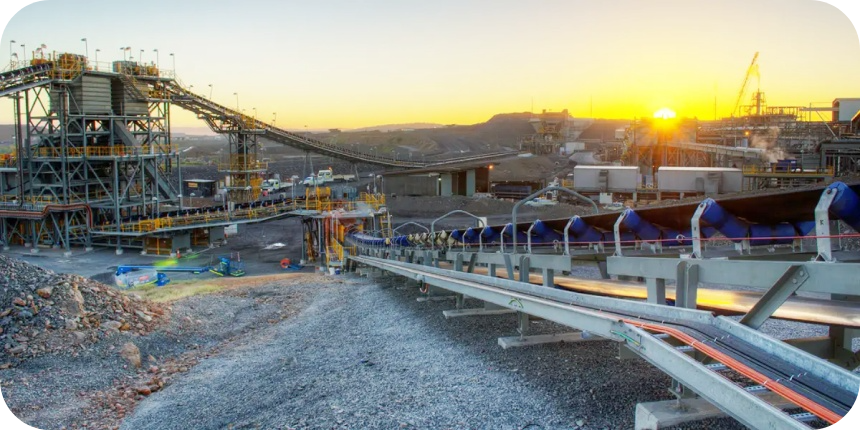
Conveyor Roller Bearing Housing
The housing for a conveyor roller bearing plays a critical role in the operational efficiency and longevity of the bearing itself. Understanding the purpose and different types of housings can significantly impact the performance and maintenance of conveyor systems.
Purpose of Bearing Housings
Bearing housings serve as the structural support for roller conveyor bearings, providing a stable and secure environment that is critical for optimal bearing performance. These housings are designed to protect the bearings from external elements and help maintain the integrity of the entire conveyor system.
Key Functions:
- Protection: Bearing housings shield the bearings from dust, debris, and other environmental contaminants that could impair their function.
- Support: They provide a rigid support structure that helps maintain alignment of the bearing, reducing stress and uneven wear.
- Lubrication Containment: Housings often include a space for lubricants, which helps maintain adequate lubrication for the bearings, reducing friction and wear.
- Ease of Maintenance: Designed for accessibility, bearing housings facilitate straightforward inspection, maintenance, and replacement of the bearings.
- Enhanced Durability: By protecting the bearings, the housings extend the lifespan of the conveyor system components.
- Noise Reduction: Properly designed housings can reduce noise generated by the bearing operation, contributing to a more pleasant work environment.
Types of Housings
Different types of conveyor roller bearing housings are tailored to various applications, each designed to meet specific operational demands and installation settings within conveyor systems.
Pillow Block Housings:
- Structure: Pillow block housings are typically mounted on a surface parallel to the shaft, making them a staple in conveyor systems. These housings support the shaft in a horizontal configuration.
- Application: These housings are perfect for scenarios requiring both radial and axial load support, commonly found in bulk material handling and manufacturing conveyor systems.
- Features:
- Versatility: They can accommodate a wide range of shaft sizes, from small to large diameters, making them suitable for diverse applications.
- Material Variety: Available in cast iron, stainless steel, or thermoplastic materials to match environmental conditions.
- Accessibility: Designed for easy access to the bearing for maintenance and replacement without the need to disassemble the conveyor setup.
Flanged Housings:
- Structure: Flanged housings include a flange on one side, facilitating easy mounting to vertical surfaces or the side of conveyors.
- Application: Best suited for heavy load applications and perfect where precise shaft alignment is crucial, such as in vertical conveyor systems or where the conveyor changes direction.
- Features:
- Stability: Offers exceptional mounting stability, crucial for applications involving high-speed conveyors.
- Fixed Bearing Configuration: Commonly used to prevent shaft movement axially, enhancing system reliability.
- Diverse Mounting Options: Available in two, three, or four-bolt flange options to provide additional support and strength.
Custom Configurations:
- Customization: Tailored to meet specific industrial requirements, these housings are designed based on the unique demands of the machinery they support.
- Application: Essential in specialized applications where standard bearings do not suffice, such as in high-temperature or corrosive environments.
- Features:
- Integrated Technology: May include sensors for condition monitoring or automated lubrication systems to enhance maintenance protocols.
- Enhanced Sealing: Offers advanced sealing solutions to protect against contaminants and prolong bearing life.
- Special Materials: Constructed from materials that withstand unusual stress, temperatures, or chemical exposure.
Take-Up Housings:
- Structure: Take-up housings allow for adjustment along the conveyor frame, essential for maintaining belt tension and alignment.
- Application: Useful in applications where belt length varies or needs adjustment due to stretching and wear, such as in mining conveyors.
- Features:
- Adjustability: Features a sliding or pivoting mechanism that facilitates easy adjustment of belt tension.
- Robust Design: Often constructed to endure heavy loads and high impacts.
- Compatibility: Compatible with various types of conveyor belts and environmental conditions.
Split Housings:
- Structure: Split housings are designed in two pieces that come together around the bearing, making them easier to install and maintain without moving other components.
- Application: Ideal for situations where conveyor roller bearings are difficult to access or replace, such as in tightly integrated systems or elevated tracks.
- Features:
- Ease of Maintenance: Allows for quick replacement of bearings without the need for significant disassembly of the conveyor shaft.
- Enhanced Protection: Provides excellent protection from dust and other particulates through improved sealing capabilities.
- Flexibility in Installation: Can be installed in a variety of orientations, providing flexibility in complex conveyor layouts.
These types of housings offer a range of options to enhance the performance and reliability of conveyor systems, catering to the specific needs and challenges of different industrial environments.
Conveyor Roller Bearing Price Factors
When selecting a conveyor roller bearing, understanding the price factors that influence your investment is essential. The cost of these components is driven by various specifications and manufacturing considerations. Here are nine critical factors that determine the price of conveyor roller bearings.
- Material Composition: The type of material used significantly affects cost. For instance, bearings made from specialty stainless steel are more expensive due to their superior corrosion resistance and durability compared to those made from carbon steel or aluminum.
- Size and Scale: Larger bearings require more material and thus are more expensive. The scale of the bearing directly impacts the amount of raw material needed, which in turn affects the cost.
- Load Capacity: Bearings designed to handle higher loads are constructed with thicker materials and robust designs to withstand the additional stress, increasing their cost.
- Precision Engineering: High-precision bearings that require tight tolerances are more expensive due to the advanced manufacturing processes needed to achieve such precision.
- Special Coatings: Coatings such as Teflon for chemical resistance or galvanized for rust prevention add to the manufacturing costs due to additional processing and materials.
- Sealing Technology: Bearings equipped with high-quality seals, such as triple-lip seals or magnetic seals, offer better protection against contaminants and longer life but at a higher price point.
- Customization: Custom features like integrated sensors for condition monitoring or unique size adjustments tailored to specific machinery requirements lead to higher prices due to the additional design and manufacturing effort.
- Brand Value: Established brands with a proven track record of reliability and quality often price their bearings higher than lesser-known manufacturers due to brand reputation and the assurance of product dependability.
- Market Dynamics: Factors like fluctuations in raw material costs, changes in trade policies, or logistic challenges can influence the final cost of bearings. For example, a sudden increase in steel prices due to tariffs would directly affect the price of steel bearings.
These factors collectively determine the pricing of conveyor roller bearings, with each contributing to the final cost based on the specific requirements and conditions of use.
Additional Conveyor Roller Components
Exploring specialized components like coated, PVC, and custom conveyor rollers can significantly enhance conveyor system performance tailored to specific industry needs. Here’s a deeper look into these innovative conveyor roller options, emphasizing the unique benefits each type offers.
Coated Conveyor Rollers
Coated conveyor rollers are designed with various protective coatings that enhance their functionality and durability. The benefits include:
- Enhanced Grip: Coatings like polyurethane provide a non-slip surface that helps maintain the movement of materials without slippage, crucial for steep or high-speed conveyors.
- Reduced Noise: A rubber or foam coating can significantly dampen operational noise, creating a quieter work environment which is essential in noise-sensitive areas.
- Minimized Product Damage: Soft coatings prevent scuffing and damage to delicate items during transport, preserving product quality.
- Increased Durability: Protective coatings can shield the roller from environmental factors like moisture and chemicals, prolonging its lifespan.
- Reduced Vibration: Some coatings can absorb vibrations, which helps protect sensitive goods from damage and reduces wear on the conveyor system itself.
- Corrosion Resistance: Coatings such as zinc or nickel plating prevent rust and corrosion, ideal for use in harsh environments.
- Improved Traction: Coatings can increase the traction between the roller and conveyor belt, which improves the transfer of power and efficiency.
- Ease of Cleaning: Many coatings have smooth surfaces that are easier to clean and maintain, which is particularly beneficial in industries where hygiene is a priority.
PVC Conveyor Rollers
PVC conveyor rollers are a lightweight and cost-effective alternative to metal rollers, offering several distinct advantages:
- Lightweight: PVC rollers are significantly lighter than metal, reducing the load on the conveyor motor and energy usage.
- Cost-Effective: Less expensive than metal rollers, PVC provides an economical solution for budget-sensitive operations.
- Corrosion Resistant: Unlike metal rollers, PVC is naturally resistant to corrosion and chemical degradation.
- Reduced Noise Levels: PVC inherently absorbs sound better than harder materials, contributing to a quieter operation.
- Low Maintenance: These rollers do not rust or corrode, thus requiring less maintenance over their lifespan.
- Non-Marking: PVC does not mark materials it contacts, important for transporting delicate or light-colored goods.
- Chemical Resistance: PVC is resistant to many acids, alkalis, and solvents, making it suitable for chemical processing environments.
- Flexibility in Design: PVC rollers can be easily fabricated to fit specific dimensions and are available in various colors for coding and safety purposes.
Custom Conveyor Rollers
Custom conveyor rollers are specifically designed to meet unique operational requirements, providing tailored solutions that can significantly improve material handling:
- Specific Load Handling: Designed to handle specific weight requirements without deforming or failing.
- Unique Material Compatibility: Custom materials can be used to deal with abrasive, corrosive, or sticky products.
- Dimensional Adaptability: Can be made to any size or shape required by the conveyor system, perfect for non-standard applications.
- Integrated Technology: Rollers can be outfitted with sensors or other technology to monitor load and performance in real-time.
- Enhanced Efficiency: Custom designs can optimize system efficiency, tailored to the specific products or materials being transported.
- Improved Durability: Materials and designs can be selected to enhance durability based on the operational environment.
- Special Coatings or Treatments: Can include specialized coatings or treatments that are not available in standard rollers.
- Aesthetic Requirements: Can be designed to fit aesthetic needs or to blend with existing machinery and equipment aesthetics.
Each type of specialized conveyor roller bearing plays a crucial role in adapting the conveyor system to meet the precise needs of different industries, ensuring both efficiency and longevity.
Need help selecting the perfect conveyor roller? Contact us now!
FAQs about Conveyor Roller Bearing
The most commonly used bearing in conveyor systems is the conveyor roller bearing. These are specifically designed to support the rotation of conveyor rollers while also guiding and reducing friction during movement. Different types include ball bearings, tapered roller bearings, and cylindrical roller bearings, each offering specific benefits. Ball bearings are suitable for lighter loads with high speeds, while tapered and cylindrical roller bearings are designed to handle heavier loads and axial forces efficiently. Choosing the right type depends on the load capacity, speed requirements, and environmental conditions. The selection of a particular bearing ensures that the conveyor system operates smoothly and efficiently.
Yes, conveyor rollers do have bearings. The conveyor roller bearing is an integral component that allows the rollers to rotate smoothly on their axles. Bearings reduce the friction between the roller and the axle, ensuring seamless movement and efficient material transport. Depending on the application, rollers can use different types of bearings like ball bearings, precision bearings, or sealed bearings, which can withstand harsh environmental conditions. The choice of bearing type impacts not just the performance of the conveyor but also its durability, noise level, and energy efficiency.
Three common types of roller bearings used in conveyor systems include:
Cylindrical Roller Bearings: Known for their high load capacity, these bearings consist of cylindrical rollers between inner and outer raceways. They are ideal for applications that need to support high radial loads.
Tapered Roller Bearings: These bearings feature tapered rollers that can accommodate both radial and axial loads, making them suitable for applications where axial thrust is a factor.
Needle Roller Bearings: These bearings use thin cylindrical rollers and are perfect for applications requiring a compact design and high load capacity.
Each type has distinct characteristics and is chosen based on the specific load and application requirements of the conveyor system.
A roller bearing is a specific type of bearing that uses cylindrical, tapered, or needle rollers as rolling elements to reduce friction between moving parts. In contrast, the term “bearing” is a broader category encompassing all devices that facilitate movement between two parts by reducing friction. Bearings include both roller bearings and ball bearings, with ball bearings using balls as rolling elements. Roller bearings are generally better suited for handling higher radial loads due to their larger contact area, while ball bearings excel in applications requiring high-speed operation and lower friction. The choice between roller bearings and other bearing types depends on the specific application’s load capacity, speed, and environmental conditions.
Last Updated on July 18, 2024 by Jordan Smith
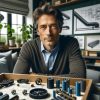
Jordan Smith, a seasoned professional with over 20 years of experience in the conveyor system industry. Jordan’s expertise lies in providing comprehensive solutions for conveyor rollers, belts, and accessories, catering to a wide range of industrial needs. From initial design and configuration to installation and meticulous troubleshooting, Jordan is adept at handling all aspects of conveyor system management. Whether you’re looking to upgrade your production line with efficient conveyor belts, require custom conveyor rollers for specific operations, or need expert advice on selecting the right conveyor accessories for your facility, Jordan is your reliable consultant. For any inquiries or assistance with conveyor system optimization, Jordan is available to share his wealth of knowledge and experience. Feel free to reach out at any time for professional guidance on all matters related to conveyor rollers, belts, and accessories.