Conveyor Roller Bearing Housing: Features And Applications
In the realm of material handling and transportation, the efficiency and longevity of conveyor systems are paramount. Central to this efficiency lies the conveyor roller bearing housing, a critical component that plays a pivotal role in the smooth operation of conveyor rollers. These housings are not just mere enclosures; they serve as the foundational support for bearings, ensuring that they remain in optimal working condition. By effectively shielding bearings from harmful contaminants and facilitating the retention of lubricant, these housings significantly reduce the risk of premature wear and tear. This protective mechanism not only enhances the durability of the conveyor system but also ensures consistent performance, minimizing downtime and maintenance requirements. The importance of bearing housing for conveyor roller in maintaining the integrity and reliability of conveyor systems cannot be overstated, making it an indispensable element in the design and operation of efficient material handling solutions.
Types of Conveyor Roller Bearing Housings
The diversity in the design and application of conveyor systems necessitates a variety of bearing housing for conveyor roller types to accommodate different operational needs and environments. These housings are categorized into several series, each designed with specific features and applications in mind. Below is an overview of some of the prominent series in conveyor roller bearing housings:
Among these, the belt conveyor roller bearing housing stands out for its specific application in belt conveyor systems. This type of housing is engineered to withstand the dynamic forces and load variations typical of belt conveyors, ensuring smooth roller operation and extended system life. The belt bearing housing for conveyor roller is particularly crucial in industries where conveyor systems are subjected to heavy loads and continuous operation, such as mining, agriculture, and bulk material handling.
Each conveyor roller bearing housing type is designed with precision to ensure it meets the specific requirements of its intended application. From supporting the weight of conveyed materials to resisting environmental challenges like dust, moisture, and varying temperatures, these housings play a vital role in the conveyor’s overall performance and durability. By selecting the appropriate bearing housing for conveyor roller, businesses can significantly enhance the efficiency, reliability, and lifespan of their conveyor systems, leading to improved operational productivity and reduced maintenance costs.

Materials and Construction of Conveyor Roller Bearing Housing
The integrity and performance of a conveyor roller bearing housing hinge significantly on the materials used in its construction and the engineering precision behind its design. Typically, materials like steel (SPHC) and carbon steel are preferred for their durability, strength, and ability to withstand the rigorous demands of conveyor operations. These materials ensure that the bearing housing for conveyor roller can support the load and stress exerted by the conveyor system without succumbing to deformation or failure.
Materials of Conveyor Roller Bearing Housing
The material used for conveyor roller bearing housings significantly affects their performance, durability, and suitability for specific applications. Different materials offer various benefits and are chosen based on factors like load capacity, environmental conditions, and maintenance requirements. Here’s a detailed overview of the common materials used for conveyor roller bearing housings:
1. Cast Iron
- Properties: Cast iron is known for its excellent strength and wear resistance. It can handle high loads and offers good damping properties, which help reduce vibration and noise.
- Applications: Commonly used in heavy-duty industrial applications such as mining, aggregate processing, and bulk material handling.
- Advantages: Durable, cost-effective, and has a long service life.
- Disadvantages: Can be heavy and prone to corrosion if not properly maintained.
2. Stainless Steel
- Properties: Stainless steel is highly resistant to corrosion and can withstand harsh environmental conditions, including exposure to moisture, chemicals, and extreme temperatures.
- Applications: Ideal for food processing, pharmaceuticals, and chemical industries where hygiene and resistance to corrosion are critical.
- Advantages: Corrosion-resistant, hygienic, and has a good aesthetic appearance.
- Disadvantages: More expensive than cast iron and may be less strong in very high-load applications.
3. Carbon Steel
- Properties: Carbon steel is strong and durable, suitable for heavy-load applications. It can be coated or treated to improve its resistance to corrosion and wear.
- Applications: Used in a variety of industrial applications, including manufacturing, mining, and construction.
- Advantages: Strong, cost-effective, and versatile.
- Disadvantages: Can corrode if not properly coated or maintained.
4. Polymer/Plastic
- Properties: Polymers or plastics like nylon, polyethylene, and polypropylene are lightweight and resistant to corrosion and chemicals. They offer low friction and can be used in wet environments.
- Applications: Suitable for applications in food processing, pharmaceuticals, and lightweight material handling where reduced weight and corrosion resistance are important.
- Advantages: Lightweight, corrosion-resistant, and quiet in operation.
- Disadvantages: Limited load-carrying capacity and may wear out faster than metal in high-stress applications.
5. Aluminum
- Properties: Aluminum is lightweight, corrosion-resistant, and easy to machine. It is not as strong as steel but offers sufficient strength for many medium-duty applications.
- Applications: Used in conveyor systems where weight reduction is crucial, such as in the aerospace and automotive industries.
- Advantages: Lightweight, corrosion-resistant, and easy to work with.
- Disadvantages: Lower strength compared to steel and can be more expensive.
6. Composite Materials
- Properties: Composite materials, which combine two or more constituent materials with different properties, can offer high strength, durability, and resistance to corrosion and wear.
- Applications: Used in specialized applications where specific performance characteristics are required.
- Advantages: Customizable properties, high strength-to-weight ratio, and excellent resistance to environmental factors.
- Disadvantages: Can be expensive and complex to manufacture.
7. Brass/Bronze
- Properties: Brass and bronze offer good corrosion resistance, low friction, and excellent wear characteristics. They are softer than steel but provide good performance in specific environments.
- Applications: Often used in marine applications, and situations where lubrication is limited, and for parts that require low friction.
- Advantages: Corrosion-resistant, low friction, and good wear properties.
- Disadvantages: Not suitable for very high-load applications and can be more expensive than common steels.
Selecting the appropriate material for conveyor roller bearing housing depends on the specific requirements of the application, including load capacity, environmental conditions, and maintenance considerations. Cast iron and carbon steel are commonly used for their strength and durability, while stainless steel, polymers, and composites are chosen for their resistance to corrosion and suitability for specific environments. Aluminum and brass/bronze offer unique advantages for lightweight and low-friction applications, respectively. By understanding the properties and advantages of each material, you can choose the best option for your conveyor system needs.
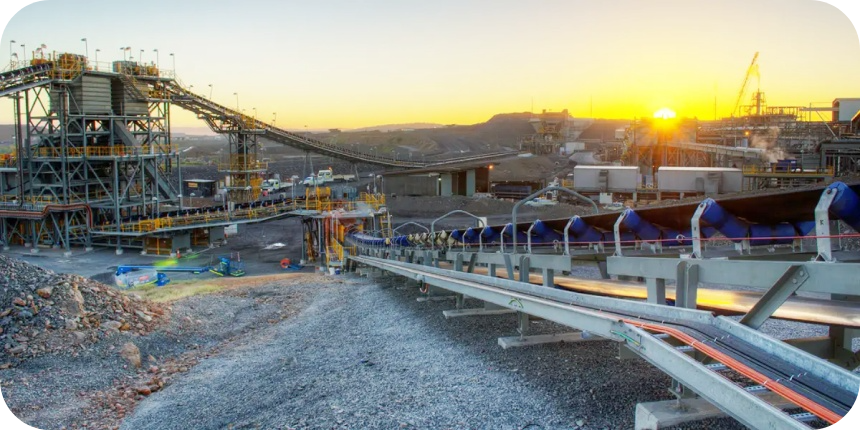
Construction of Conveyor Roller Bearing Housing
The construction features of a conveyor roller bearing housing are meticulously designed to enhance its functionality and longevity. Here are 10 notable construction features:
- Robust Design: The overall structure is engineered for resilience, capable of enduring the continuous stress and load of conveyor operations.
- Steel Pressings: High-quality steel pressings reinforce the housing’s strength, providing a sturdy framework that maintains its integrity under pressure.
- Hardened Balls: Incorporated within the housing, these hardened balls are essential for smooth roller movement, reducing friction and wear.
- Finish Options: Options for stainless steel or zinc-plated finishes offer additional protection against corrosion, extending the housing’s service life in harsh environments.
- Precision Engineering: Each housing is precisely engineered to ensure a perfect fit with the bearings and the conveyor system, minimizing the risk of operational disruptions.
- Sealing Mechanisms: Advanced sealing mechanisms protect the bearings from contaminants like dust and water, crucial for maintaining optimal performance.
- Lubrication Paths: Designed with lubrication in mind, these housings facilitate easy maintenance, ensuring bearings remain well-lubricated for smooth operation.
- Customizable Dimensions: The housings can be customized to various dimensions, accommodating a wide range of bearing sizes and conveyor specifications.
- Thermal Treatment: Certain models undergo thermal treatment to enhance their hardness and resistance to wear and tear.
- Mounting Flexibility: The design allows for versatile mounting options, ensuring compatibility with different conveyor setups and ease of installation.
The meticulous attention to the materials and construction of the conveyor roller bearing housing is what sets apart high-quality conveyor systems. These features not only ensure the durability and reliability of the housing itself but also contribute to the overall efficiency and longevity of the conveyor system. By investing in well-designed and robustly constructed bearing housings, businesses can achieve smoother operations, reduced maintenance requirements, and longer service life for their conveyor systems.

Applications and Compatibility of Conveyor Roller Bearing Housing
The bearing housing for conveyor roller is a versatile component that finds applications across a broad spectrum of industries, each with its unique demands and operational challenges. Its primary function is to provide a secure and stable enclosure for bearings, facilitating smooth and efficient conveyor operations. This section delves into the specific applications of conveyor roller bearing housing in the mining industry, transportation systems, and its compatibility with various types of bearings.
Mining and Quarrying
Applications:
- Handling bulk materials such as ores, coal, and aggregates.
- Operating in harsh environments with heavy loads and abrasive materials.
Compatibility:
- Material: Cast iron or carbon steel housings are preferred due to their high strength and durability.
- Design: Sealed housings to protect bearings from dust, debris, and moisture.
- Maintenance: Regular lubrication and inspection to prevent wear and corrosion.
Food Processing
Applications:
- Conveying food products in clean, hygienic environments.
- Handling ingredients, packaging, and finished products.
Compatibility:
- Material: Stainless steel or polymer housings are ideal for their corrosion resistance and ease of cleaning.
- Design: Hygienic design with minimal crevices to prevent contamination.
- Maintenance: Regular cleaning and sterilization to meet food safety standards.
Pharmaceutical and Chemical Industries
Applications:
- Conveying raw materials, intermediate products, and finished goods.
- Operating in environments with exposure to chemicals and strict cleanliness requirements.
Compatibility:
- Material: Stainless steel or corrosion-resistant polymers to withstand chemical exposure.
- Design: Sealed and easy-to-clean housings to prevent contamination.
- Maintenance: Frequent inspections and cleaning to ensure compliance with industry regulations.
Automotive Manufacturing
Applications:
- Assembly lines and material handling within manufacturing plants.
- Conveying automotive components and finished vehicles.
Compatibility:
- Material: Cast iron or carbon steel for high strength and load-bearing capacity.
- Design: Precision-engineered housings to ensure smooth and reliable operation.
- Maintenance: Regular lubrication and alignment checks to prevent downtime.
Aerospace Industry
Applications:
- Manufacturing and assembling aircraft components.
- Testing and quality control of aerospace parts.
Compatibility:
- Material: Aluminum or stainless steel for lightweight and corrosion resistance.
- Design: High-precision housings to meet stringent aerospace standards.
- Maintenance: Detailed inspection and maintenance schedules to ensure reliability.
Logistics and Warehousing
Applications:
- Handling and sorting packages and goods in distribution centers.
- Conveyor systems for automated material handling.
Compatibility:
- Material: Carbon steel or polymer housings for balanced strength and weight.
- Design: Modular and easy-to-maintain housings for flexibility and efficiency.
- Maintenance: Regular checks and maintenance to ensure continuous operation.
Construction and Heavy Machinery
Applications:
- Conveying building materials and components on construction sites.
- Handling heavy loads and operating in rugged conditions.
Compatibility:
- Material: Cast iron or carbon steel for maximum strength and durability.
- Design: Robust housings to withstand impact and heavy use.
- Maintenance: Frequent inspections and lubrication to maintain performance.
Recycling and Waste Management
Applications:
- Sorting and processing recyclable materials.
- Handling waste and debris in recycling plants.
Compatibility:
- Material: Carbon steel or stainless steel for strength and corrosion resistance.
- Design: Sealed housings to protect bearings from debris and contaminants.
- Maintenance: Regular cleaning and maintenance to prevent clogging and wear.
The compatibility of conveyor roller bearing housings with specific applications depends on several factors, including material, design, and maintenance requirements. Choosing the right bearing housing involves considering the operating environment, load capacity, and the specific needs of the industry. By selecting appropriate materials and designs, you can ensure the efficient and reliable operation of conveyor systems across various applications.
Compatibility with Bearings
One of the critical aspects of conveyor roller bearing housing is its compatibility with a wide range of bearing sizes and types. These housings are designed to accommodate bearings from 6203 to 6312, covering a broad spectrum of sizes to suit various operational requirements. The compatibility extends to various shaft and bore diameters, ensuring that the housing can be integrated seamlessly into different conveyor systems. This versatility is crucial for ensuring that the conveyor system can be tailored to specific operational needs, whether it involves light-duty applications or heavy-duty industrial use.
Deep Groove Ball Bearings and Others
The conveyor roller bearing housing is particularly well-suited for deep groove ball bearings, known for their versatility and ability to support both radial and axial loads. The design of the housing ensures that these bearings are adequately protected and lubricated, maximizing their performance and lifespan. Additionally, the housing is compatible with other types of bearings, providing flexibility in the design and optimization of conveyor systems.
The bearing housing for conveyor roller plays a pivotal role in the efficient and reliable operation of conveyor systems across various industries. Its robust design, compatibility with a wide range of bearings, and suitability for different shaft and bore diameters make it an indispensable component in the design of conveyor systems. Whether in the demanding environment of the mining industry or the dynamic world of transportation and logistics, the conveyor roller bearing housing ensures that conveyor systems operate at their best, contributing to the overall productivity and efficiency of operations.

Manufacturing Process of Conveyor Roller Bearing Housings
The manufacturing process of conveyor roller bearing housings is a sophisticated sequence of operations that involves precision engineering and meticulous quality control. This process is crucial in ensuring that the housings meet the stringent requirements of various industrial applications, providing the necessary support and protection for bearings in conveyor systems.
Production Process Overview
The production of bearing housing for conveyor roller begins with the selection of high-quality materials, such as steel (SPHC) and carbon steel, known for their durability and strength. These materials are then subjected to a series of manufacturing steps, including cutting, forming, and machining, to shape the housing according to precise specifications. Advanced techniques such as steel pressing are employed to enhance the structural integrity of the housing, ensuring it can withstand the operational stresses it will encounter.
Technological Advancements
The manufacturing process has significantly benefited from technological advancements in recent years. Computer Numerical Control (CNC) machining has introduced a new level of precision in the shaping and drilling of housings, allowing for tighter tolerances and more consistent quality. Additionally, automation in various stages of production has increased efficiency, reducing lead times and minimizing human error.
Quality Control Measures
Quality control is an integral part of the manufacturing process for conveyor roller bearing housings. Rigorous inspections are conducted at various stages of production to ensure that each housing meets the required standards. This includes dimensional checks, material analysis, and testing for structural integrity. Advanced testing methods, such as 3D scanning and ultrasonic testing, are used to detect any defects or inconsistencies that could compromise the performance of the housing.
Finishing and Treatment
After passing quality control, the housings undergo finishing processes, such as powder coating or galvanization, to enhance their corrosion resistance and durability. Some housings may also receive thermal treatment to improve their hardness and wear resistance, further extending their service life in demanding industrial environments.
Final Assembly and Inspection
The final step in the manufacturing process involves the assembly of additional components, such as seals and lubrication systems, into the housing. A final inspection is conducted to ensure that the complete bearing housing for conveyor roller is ready for deployment in conveyor systems, meeting all the specifications and quality standards required for its intended application.
The manufacturing process of conveyor roller bearing housings is a complex but well-orchestrated sequence of operations that emphasizes precision, quality, and durability. Technological advancements and stringent quality control measures play a crucial role in ensuring that these housings meet the high standards required for efficient and reliable operation in conveyor systems across various industries.
Comparison: Sliding Bearing vs Roller Bearing in Conveyor Roller Bearing Housing
When it comes to bearing housing for conveyor roller, the choice between sliding bearings and roller bearings is crucial, as it significantly impacts the efficiency, durability, and maintenance requirements of the conveyor system. This section provides a detailed comparison of these two types of bearings, highlighting their differences, advantages, and disadvantages.
In the context of conveyor roller bearing housing, roller bearings are often preferred due to their ability to handle higher speeds and loads with greater efficiency and less maintenance. However, sliding bearings might still be chosen for specific applications where their unique advantages, such as tolerance for misalignment and shock loads, outweigh the benefits of roller bearings.
The choice between sliding and roller bearings in bearing housing for conveyor roller depends on the specific requirements of the conveyor system, including load, speed, maintenance capabilities, and environmental conditions. Understanding the characteristics of each bearing type is essential for making an informed decision that ensures the optimal performance and longevity of the conveyor system.
How Roller Bearings Work in Conveyor Roller Bearing Housing
Roller bearings play a pivotal role in the functionality of conveyor roller bearing housing, ensuring smooth and efficient operation of conveyor systems. Understanding the working principle of roller bearings and their contribution to load movement efficiency and precision is crucial for optimizing conveyor performance.
Working Principle
Roller bearings consist of cylindrical rollers positioned between two races, one stationary and the other attached to the rotating assembly. Unlike ball bearings, roller bearings utilize a line contact rather than a point contact, allowing for a larger surface area to carry the load. This design significantly reduces friction and wear, as the rolling elements distribute the load evenly across a broader area, facilitating smoother rotation and higher load-bearing capacity.
Efficiency in Load Movement
The efficiency of roller bearings in conveyor roller bearing housing is primarily attributed to their ability to minimize friction. This reduced friction not only enhances the speed and smoothness of the conveyor rollers but also contributes to lower energy consumption and heat generation. As a result, conveyor systems equipped with roller bearings can operate more efficiently, with less downtime and maintenance required.
Precision in Load Movement
Roller bearings are renowned for their precision in handling loads. The design of roller bearings allows for precise control over the movement of the conveyor rollers, ensuring that goods are transported smoothly and accurately along the conveyor path. This precision is particularly important in applications where exact positioning and alignment of goods are critical, such as in automated assembly lines or sorting systems.
Incorporating roller bearings into conveyor roller bearing housing provides a robust solution for enhancing the performance of conveyor systems. Their ability to support heavy loads with high efficiency and precision makes them an ideal choice for a wide range of industrial applications. By leveraging the advantages of roller bearings, businesses can achieve improved operational efficiency, reduced maintenance costs, and increased longevity of their conveyor systems.

Choosing the Right Conveyor Roller Bearing Housing
Selecting the appropriate bearing housing for conveyor roller is a critical decision that can significantly impact the efficiency, reliability, and longevity of a conveyor system. Here are 10 key factors to consider when choosing the right bearing housing for conveyor roller, followed by 10 tips on effectively using roller bearings in conveyor systems.
Factors to Consider
- Load Capacity: Assess the maximum load the conveyor system will carry to ensure the bearing housing can withstand the operational stress.
- Environmental Conditions: Consider the working environment, including temperature, humidity, and exposure to corrosive substances, to select a housing material and design that can endure these conditions.
- Compatibility with Conveyor Design: Ensure the bearing housing is compatible with the conveyor system’s design, including roller size, shaft diameter, and mounting requirements.
- Material: Choose a housing material (e.g., steel, stainless steel, or plastic) that offers the best balance of strength, durability, and resistance to environmental factors.
- Speed Requirements: Consider the operational speed of the conveyor system; higher speeds may require housings designed to minimize friction and heat buildup.
- Maintenance Needs: Evaluate the ease of maintenance and accessibility of the bearing housing, considering features like lubrication fittings and sealing options.
- Lifespan and Durability: Look for housings made with high-quality materials and robust construction to ensure a long service life under the expected operating conditions.
- Cost: Balance the upfront cost with the expected lifespan and maintenance requirements to find a cost-effective solution.
- Supplier Reputation: Choose a reputable supplier known for quality products and reliable service to ensure you get a well-engineered conveyor roller bearing housing.
- Customization Options: Consider whether custom-designed housings are necessary to meet specific requirements or challenges of your conveyor system.
Tips for Effective Use
- Regular Inspection: Conduct regular inspections of the bearing housing for signs of wear, damage, or contamination.
- Proper Lubrication: Follow the manufacturer’s recommendations for lubrication to reduce friction and prevent premature wear.
- Correct Installation: Ensure that the bearing housing is installed correctly, with proper alignment and tension, to avoid operational issues.
- Cleanliness: Maintain cleanliness around the conveyor system to prevent dirt and debris from entering the bearing housing.
- Temperature Monitoring: Monitor the operating temperature of the bearing housing, as excessive heat can indicate issues like overloading or insufficient lubrication.
- Load Distribution: Ensure that loads are evenly distributed across the conveyor to prevent uneven wear on the bearings and housing.
- Use Seals: Utilize appropriate sealing solutions to protect the bearings from contaminants and retain lubricant.
- Avoid Overloading: Never exceed the specified load capacity of the conveyor roller bearing housing to prevent damage and failure.
- Training: Train maintenance personnel on the proper care and maintenance of bearing housings to ensure they are kept in optimal condition.
- Replacement Planning: Have a plan for timely replacement of bearing housings to prevent unexpected downtime and maintain system efficiency.
By carefully considering these factors and following these tips, you can ensure that you choose the right conveyor roller bearing housing for your system and use it effectively to maintain optimal performance and reliability.
Maintaining the Conveyor Roller Bearing Housing
Maintaining the conveyor roller bearing housing is essential for ensuring the longevity and efficient operation of conveyor systems. Proper maintenance helps prevent downtime, reduces the risk of equipment failure, and ensures smooth operation. Here’s a detailed guide on how to maintain conveyor roller bearing housing:
Regular Inspection
- Visual Check: Regularly inspect the bearing housing for signs of wear, damage, or misalignment. Look for any cracks, dents, or unusual wear patterns.
- Listen for Noise: Unusual noises during operation can indicate problems with the bearings, such as grinding or squealing, which could signify insufficient lubrication or worn-out bearings.
Lubrication
- Correct Lubricant: Use the appropriate lubricant specified by the manufacturer. Lubricants can be either grease or oil, depending on the application and operating conditions.
- Lubrication Schedule: Follow a regular lubrication schedule. Over-lubrication and under-lubrication can both cause issues. Typically, bearings should be lubricated every few weeks to months, depending on usage and environment.
- Cleanliness: Ensure the bearing and housing area is clean before applying new lubricant to prevent contamination.
Alignment
- Check Alignment: Ensure the bearing housing is correctly aligned with the conveyor roller. Misalignment can cause uneven wear and increase friction, leading to premature bearing failure.
- Adjust if Necessary: If misalignment is detected, adjust the bearing housing and conveyor roller to ensure they are correctly aligned.
Cleaning
- Remove Debris: Regularly clean the bearing housing to remove dirt, dust, and debris. This helps prevent contamination that can lead to bearing wear and failure.
- Use Appropriate Cleaning Agents: Use suitable cleaning agents that do not damage the bearing or housing material. Avoid using harsh chemicals that can corrode the housing.
Sealing
- Inspect Seals: Check the seals of the bearing housing for damage or wear. Seals prevent contaminants from entering the bearing housing and keep lubricants inside.
- Replace if Needed: Replace damaged or worn seals promptly to maintain the integrity of the bearing housing.
Temperature Monitoring
- Monitor Operating Temperature: Bearings should operate within a specified temperature range. Excessive heat can indicate problems such as overloading, inadequate lubrication, or bearing wear.
- Investigate High Temperatures: If high temperatures are detected, investigate and address the underlying cause to prevent bearing failure.
Bearing Replacement
- Scheduled Replacement: Bearings have a finite lifespan and should be replaced according to the manufacturer’s recommended schedule or if significant wear is detected.
- Proper Installation: Ensure new bearings are installed correctly, with the proper tools and techniques to avoid damage.
Vibration Analysis
- Regular Checks: Perform regular vibration analysis to detect early signs of bearing issues. Excessive vibration can indicate misalignment, imbalance, or bearing defects.
- Address Issues Promptly: If abnormal vibrations are detected, investigate and address the root cause to prevent further damage.
Environmental Control
- Protect from Contaminants: If the conveyor operates in a harsh environment, such as a dusty or wet area, use protective covers or enclosures for the bearing housing.
- Control Humidity and Temperature: Ensure the operating environment is within the recommended conditions to prevent corrosion and excessive wear.
Documentation and Record Keeping
- Maintain Records: Keep detailed records of all maintenance activities, including inspections, lubrication schedules, replacements, and any issues detected.
- Review Trends: Regularly review maintenance records to identify trends or recurring issues that may indicate underlying problems.
Proper maintenance of conveyor roller bearing housing involves regular inspection, appropriate lubrication, correct alignment, thorough cleaning, effective sealing, temperature monitoring, scheduled bearing replacement, vibration analysis, environmental control, and diligent record keeping. By following these steps, you can ensure the efficient and reliable operation of your conveyor systems, extend the lifespan of the bearings, and reduce downtime and maintenance costs.
Our conveyor rollers are designed for peak performance.
FAQs about Conveyor Roller Bearing Housing
A bearing housing, often referred to as a bearing block or pillow block, is a pedestal used to provide support for a rotating shaft with the help of compatible bearings and various accessories. Housing materials include cast iron, stainless steel, or plastic, depending on the application’s requirements. In the context of conveyor systems, the bearing housing plays a crucial role in ensuring the smooth operation of the conveyor rollers. It not only supports the bearings that allow the roller to rotate with minimal friction but also protects the bearings from environmental contaminants and helps retain lubrication, extending the life of the bearings and, by extension, the conveyor system itself. The design and material of the bearing housing can significantly impact the efficiency and durability of the conveyor system, making it a critical component in conveyor design and maintenance.
Bearings in a conveyor system are mechanical components that reduce friction between the moving parts of the conveyor, facilitating smooth and efficient operation. They are typically found in the rollers and pulleys of the conveyor, where they support the rotational movement of these parts. There are various types of bearings used in conveyor systems, including ball bearings, roller bearings, and spherical roller bearings, each selected based on the specific requirements of the system, such as load capacity, speed, and environmental conditions. The choice of bearing impacts the conveyor’s performance, maintenance needs, and longevity. Properly selected and maintained bearings can significantly enhance the efficiency of a conveyor system and reduce downtime due to wear and tear or failure.
The rollers on a conveyor, also known as conveyor rollers, are the cylindrical components that facilitate the movement of materials along the conveyor belt or track. They are mounted on the conveyor frame and can be powered (driven) or unpowered (gravity rollers). The primary function of these rollers is to support the conveyor belt and the material being transported. The design and material of the rollers can vary depending on the application, with options including steel, plastic, and rubber-coated rollers. The choice of roller type is influenced by factors such as the weight of the materials being conveyed, the environment in which the conveyor operates (e.g., wet, dry, corrosive), and the desired speed of material transport. Conveyor rollers are essential for the efficient operation of the conveyor system, as they directly affect the system’s speed, noise level, and wear on the belt.
The spacing for conveyor rollers, also known as roller pitch, is the distance between the centers of adjacent rollers on the conveyor. This spacing is a critical design consideration, as it affects the conveyor’s ability to smoothly and efficiently transport materials. The optimal roller spacing is determined by the size and weight of the items being conveyed; smaller and lighter items require closer spacing to prevent them from sagging or getting stuck between rollers. Conversely, larger and heavier items can be supported with wider spacing. The goal is to ensure that at least three rollers are in contact with the item being conveyed at any given time for stability and support. Incorrect roller spacing can lead to increased wear on the conveyor belt, damage to the items being conveyed, and potential jamming of the conveyor system, highlighting the importance of careful planning and design in setting the roller spacing.
Last Updated on July 4, 2024 by Jordan Smith
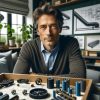
Jordan Smith, a seasoned professional with over 20 years of experience in the conveyor system industry. Jordan’s expertise lies in providing comprehensive solutions for conveyor rollers, belts, and accessories, catering to a wide range of industrial needs. From initial design and configuration to installation and meticulous troubleshooting, Jordan is adept at handling all aspects of conveyor system management. Whether you’re looking to upgrade your production line with efficient conveyor belts, require custom conveyor rollers for specific operations, or need expert advice on selecting the right conveyor accessories for your facility, Jordan is your reliable consultant. For any inquiries or assistance with conveyor system optimization, Jordan is available to share his wealth of knowledge and experience. Feel free to reach out at any time for professional guidance on all matters related to conveyor rollers, belts, and accessories.