Top Conveyor Roller Bearings Manufacturers
In the heart of modern industrial operations lies the unsung hero: conveyor roller bearings. These pivotal components, crafted meticulously by conveyor roller bearings manufacturers, ensure the seamless movement of goods across numerous sectors. From the bustling floors of manufacturing plants to the intricate systems of distribution centers, the role of these bearings is irreplaceable. Taking inspiration from the ‘Innovating Bearing Manufacturing – WD Bearings Group’ section, it’s evident that the landscape of conveyor roller bearings manufacturing is one of continuous evolution. Manufacturers like WD Bearings Group are at the forefront, pushing the boundaries of technology and materials science to produce bearings that meet the ever-growing demands of efficiency, durability, and precision. Their commitment to innovation not only enhances the performance of conveyor systems but also drives the industries forward, underscoring the critical role conveyor roller bearings manufacturers play in the global economy.
What is Conveyor Roller Bearings Manufacturers
What Are Conveyor Roller Bearings?
Conveyor roller bearings are precision-engineered components designed to facilitate the smooth and efficient movement of conveyor belts. These bearings are pivotal in reducing friction between the roller and the shaft, thereby ensuring the conveyor system operates smoothly and with minimal resistance. The significance of these components cannot be overstated, as they directly impact the productivity and operational efficiency of various material handling systems. Conveyor roller bearings manufacturers play a crucial role in developing bearings that cater to specific industrial needs, offering solutions that range from standard sizes to custom-engineered components.
- Standard Precision Ball Bearings: Commonly used for light to medium load applications, offering smooth motion.
- Sealed Bearings: Designed with seals to prevent the ingress of contaminants, extending the bearing’s life.
- Stainless Steel Bearings: Ideal for applications where corrosion resistance is necessary.
- High-Temperature Bearings: Specifically engineered to perform under high-temperature conditions without losing efficiency.
- Impact-Resistant Bearings: Built to withstand heavy impacts, suitable for heavy-duty material handling applications.
Types of Conveyor Roller Bearings
Conveyor roller bearings come in various types, each designed to meet different operational demands and applications. Conveyor roller bearings manufacturers have developed a range of bearings to suit the varied needs of industries, ensuring there’s a bearing solution for virtually any scenario. These types include:
- Deep Groove Ball Bearings: Known for their versatility and ability to support both radial and axial loads. Ideal for high-speed applications.
- Tapered Roller Bearings: Best suited for applications where there are high radial and axial loads, offering durability and resistance to overturning moments.
- Radial Ball Bearings: Typically used where high-speed and low-power loss is required.
- Hex Bore Bearings: Designed for special applications where a hexagonal bore is needed for mounting.
- Cylindrical Roller Bearings: Offer high radial load capacity and are suitable for high-speed applications.
Applications in Industries
The applications of conveyor roller bearings span across various industries, underscoring their versatility and critical role in material handling and equipment operations. Manufacturers like WD Bearings specialize in producing bearings that cater to specific industrial applications, ensuring that there is a bearing solution for every need. Examples of applications in industries include:
- Material Handling Systems: Such as conveyor belts in manufacturing plants and warehouses, where they facilitate the smooth movement of goods.
- Sorting Equipment: Used in postal and courier services for efficient package sorting.
- Forklifts: Bearings in forklift wheels and mechanisms enhance mobility and load-bearing capacity.
- Lifting Equipment: Cranes and hoists rely on specialized bearings for safe and efficient lifting operations.
- Agricultural Machinery: Bearings are crucial in the operation of equipment used in farming and food production, ensuring reliability and efficiency.
Conveyor roller bearings manufacturers are integral to the continuous innovation and improvement of bearing technology, addressing the evolving needs of industries and contributing significantly to the operational efficiency of various systems. Their expertise in engineering and manufacturing high-quality bearings ensures that businesses can rely on these components for their critical operations.
The Importance of Quality and Durability in Conveyor Roller Bearings Manufacturers
The operational integrity of conveyor systems crucially depends on the quality and durability of conveyor roller bearings, underscoring the pivotal role of conveyor roller bearings manufacturers in ensuring these components withstand the rigors of continuous use. Quality and durability are not merely attributes but are foundational to the performance and reliability of conveyor systems across various industries.
Materials and Manufacturing Processes
The choice of material is paramount in the production of high-quality conveyor roller bearings. Conveyor roller bearings manufacturers prioritize materials that offer superior strength, durability, and resistance to wear and environmental conditions. Examples of high-quality materials used include:
- 99.98% VIM-VAR Steel: This ultra-pure steel is known for its exceptional cleanliness and uniformity, ensuring high strength and toughness.
- Stainless Steel: Offers excellent corrosion resistance, making it suitable for food processing and marine applications.
- Ceramic Materials: Used for balls and races in bearings, ceramics reduce friction, wear, and heat generation.
- High-Carbon Chrome Steel: Commonly used for its durability and resistance to deformation under heavy loads.
- Nylon and Polyurethane: For seals and cages, providing excellent wear resistance and reducing noise.
These materials, combined with advanced manufacturing processes such as precision grinding and automated assembly, enable conveyor roller bearings manufacturers to produce bearings that meet exacting standards.
Product Verification and Testing
Ensuring the quality and durability of conveyor roller bearings extends beyond material selection and manufacturing processes. Conveyor roller bearings manufacturers engage in rigorous product verification and testing protocols to guarantee performance under real-world conditions.
- MESYS Analysis: Advanced software tools like MESYS are used for bearing simulation and analysis, allowing manufacturers to predict performance and optimize designs.
- Field Testing: Bearings are tested in actual working conditions to assess their performance, longevity, and resistance to environmental factors.
- Certifications: Manufacturers seek certifications such as ISO 9001 for quality management systems, ensuring consistent product quality and reliability.
Longevity and Fracture Resistance
Durability and resistance against fractures are critical considerations for conveyor roller bearings, impacting their longevity and the overall uptime of conveyor systems. Manufacturers focus on:
- Heat Treatment Processes: Such as case hardening and through-hardening to enhance surface durability and core toughness.
- Surface Finishing Techniques: Like black oxide coating to increase corrosion resistance and fatigue strength.
- Optimized Design Features: Including reinforced raceways and high-grade lubrication systems to reduce stress concentrations and wear.
- Material Science Innovations: Employing nanostructured materials and coatings to improve hardness and reduce the risk of fractures.
- Stress Analysis: Using finite element analysis (FEA) to identify and strengthen potential weak points in the bearing design.
Conveyor roller bearings manufacturers invest in these areas to ensure that their products are not only capable of performing under the expected load conditions but also surpassing industry standards for durability and reliability. This commitment to quality and durability is what makes the choice of conveyor roller bearings manufacturers a critical decision for businesses looking to maximize the efficiency and lifespan of their conveyor systems.
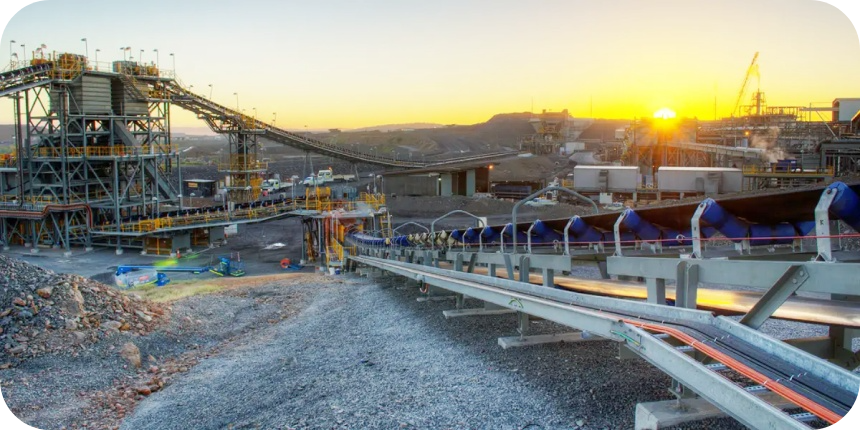
Conveyor Roller Bearings Manufacturers: A Global and Local Overview
The landscape of conveyor roller bearings manufacturers is diverse, encompassing a range of companies from global giants to local specialists. These manufacturers are critical to the functionality and efficiency of conveyor systems worldwide, providing solutions that cater to a broad spectrum of industrial needs.
Conveyor Roller Bearings Manufacturers in the USA
The United States hosts some of the industry’s most renowned conveyor roller bearings manufacturers, known for their innovation, quality, and reliability. Key players include:
- TIMKEN MANUFACTURER: Renowned for its wide range of high-quality roller bearings suitable for numerous applications, including heavy industrial conveyor systems.
- ROYERSFORD FOUNDRY & MACHINE CO., INC.: Specializes in producing rugged and durable bearings designed to withstand harsh conditions.
- Rexnord: Offers a comprehensive line of roller bearings, including engineered and spherical roller bearings for varied conveyor applications.
- Martin Sprocket & Gear, Inc.: Known for their manufacturing excellence, providing a variety of conveyor components and accessories.
- Precision Pulley & Idler (PPI): Delivers a range of conveyor bearings and rollers, emphasizing performance and durability.
These manufacturers stand out for their commitment to quality, extensive product ranges, and their ability to meet the demands of complex industrial environments.
Global Conveyor Roller Bearings Manufacturers
The global stage of conveyor roller bearings manufacturers features companies that are leaders in innovation and technology. Among the notable names are:
- THK UK MANUFACTURER (Japan): Offers precision bearings with a focus on high efficiency and reliability for various applications.
- SKF (Sweden): A leading global provider known for its high-quality bearings, offering solutions that enhance energy efficiency and reduce maintenance needs.
- NSK (Japan): Delivers bearings that are critical to conveyor systems, known for their durability and precision engineering.
- FAG (Germany): Part of the Schaeffler Group, renowned for its comprehensive range of roller bearings suitable for a wide array of industrial applications.
- NTN (Japan): Provides a wide range of bearings, including those specifically designed for conveyor systems, focusing on performance and reliability.
These global manufacturers contribute significantly to the advancement of conveyor roller bearings technology, offering products that meet the highest standards of quality and efficiency.
Local Options for Conveyor Roller Bearings
For businesses seeking more localized solutions, finding “conveyor roller bearings manufacturers near me” can provide several benefits, including reduced lead times, personalized service, and support for local economies. To find local manufacturers:
- Industry Directories and Associations: Utilize online directories and industry associations specific to your region to identify local manufacturers.
- Trade Shows and Expos: Attend industry trade shows and expos to connect directly with manufacturers and learn about their product offerings.
- Search Engines: Use search engines with specific geographical keywords to find manufacturers in your area.
- Local Business Listings: Check local business listings and online marketplaces that cater to industrial supplies and services.
Choosing a local manufacturer can also facilitate easier communication, customization, and quick response to any operational issues. Whether opting for a global leader or a local specialist, the selection of conveyor roller bearings manufacturers should be guided by the specific needs of your conveyor system, ensuring optimal performance and longevity.
Selection and Replacement of Conveyor Roller Bearings: Insights from Manufacturers
The process of selecting and replacing conveyor roller bearings is crucial for maintaining the efficiency and longevity of conveyor systems. Conveyor roller bearings manufacturers provide valuable insights into making informed decisions that ensure optimal performance and durability of these essential components.
Assessing the Right Type of Bearing
Selecting the right type of bearing for specific conveyor equipment involves understanding the operational demands and environmental conditions of the system. Conveyor roller bearings manufacturers recommend considering the following factors:
- Load Capacity: Determine whether the bearing needs to support heavy, medium, or light loads. For heavy loads, tapered roller bearings might be the best choice, while deep groove ball bearings are suitable for lighter loads.
- Speed Requirements: High-speed applications may require bearings designed for minimal friction and heat generation, such as precision ball bearings.
- Operating Environment: Bearings in harsh environments may need enhanced protection against contaminants. Sealed or shielded bearings, made from stainless steel or with protective coatings, are ideal in such cases.
- Alignment and Mounting Needs: Consider bearings that accommodate misalignment if the application is prone to shaft or mounting inaccuracies. Self-aligning ball bearings can be a good option.
- Maintenance and Accessibility: Choose bearings that match the maintenance capabilities and accessibility of the system. Split roller bearings, for example, offer ease of replacement without disassembling surrounding components.
Conveyor Roller Bearing Replacement
Replacing conveyor roller bearings at the right time and in the correct manner is essential to avoid prolonged downtimes and ensure the reliability of the conveyor system. Following the guidelines from the ‘Conveyor Equipment Components and Bearings’ section from WD Bearings, consider these tips:
- Regular Inspection: Schedule regular inspections to assess wear and performance. Indications for replacement include abnormal noises, decreased performance, or visible wear and damage.
- Proper Lubrication: Ensure bearings are properly lubricated according to the manufacturer’s recommendations. Inadequate lubrication can lead to premature failure.
- Use of Correct Tools and Techniques: Utilize the right tools and follow the manufacturer’s instructions for bearing removal and installation. This prevents damage to the new bearings and surrounding components.
- Alignment and Calibration: After replacement, ensure the conveyor system is correctly aligned and calibrated to prevent undue stress on the new bearings.
- Documentation and Monitoring: Keep records of bearing replacements and monitor the performance of new bearings closely. This helps in predicting future maintenance needs and identifying any issues early on.
Conveyor roller bearings manufacturers emphasize the importance of using high-quality bearings and following best practices for replacement to maximize the life and efficiency of conveyor systems. Proper selection and timely replacement of conveyor roller bearings are key to maintaining optimal operations and preventing costly downtimes.
Comparing Conveyor Roller Bearings Manufacturers and Products
In the vast market of conveyor systems, the selection of the right conveyor roller bearings and their manufacturers is a pivotal decision that impacts the efficiency, durability, and overall performance of the system. Comparing manufacturers and their products, especially for heavy-duty applications, involves assessing various factors and features that contribute to the longevity and reliability of the bearings.
Comparing Heavy Duty Options
For operations requiring heavy-duty conveyor roller bearings, certain manufacturers have specialized in producing components that are robust, durable, and capable of withstanding extreme conditions. Examples of manufacturers known for their heavy-duty conveyor roller bearings include:
- TIMKEN: Recognized globally for their innovative bearing designs and reliability in heavy-duty applications.
- SKF: Offers a wide range of high-load-capacity bearings, known for their durability and performance.
- NSK: Specializes in bearings that provide high radial load capacity, ideal for heavy-duty conveyor systems.
- FAG (Schaeffler): Known for their rigorous testing and quality assurance, ensuring their bearings can handle heavy loads and high speeds.
- NTN: Their bearings are designed for heavy industrial applications, providing excellent load capacity and longevity.
These manufacturers stand out not just for their product quality but also for their commitment to innovation and their ability to meet the specific needs of heavy-duty applications.
Identifying the Best Manufacturers
Determining the best conveyor roller bearings manufacturers requires considering several criteria, as outlined in the ‘Why Choose WD’ section. Key factors include:
- Quality Assurance: Top manufacturers adhere to strict quality control standards, ensuring their products meet or exceed industry benchmarks.
- Innovative Design: The best manufacturers invest in research and development to offer bearings that provide superior performance and efficiency.
- Customization Capabilities: The ability to provide custom solutions tailored to specific operational needs is a hallmark of leading manufacturers.
- Comprehensive Support: Offering technical support, from selection through to maintenance advice, signifies a manufacturer’s commitment to customer satisfaction.
- Global Presence with Local Support: Manufacturers that combine a global reach with localized service and support ensure that clients have access to the best products and expertise, regardless of location.
Essential Features in Conveyor Bearings
When comparing conveyor roller bearings, several key features must be considered to ensure the selection of the most suitable component for the application:
- Hex Bore: Bearings with a hexagonal bore are designed for specific mounting requirements, offering easy installation and secure fit.
- Radial Capacity: The ability of a bearing to support radial loads is critical, especially in applications where the conveyor will carry heavy materials.
- Load Rating: The maximum load a bearing can handle while still providing optimal performance is a vital consideration, ensuring the longevity and reliability of the system.
- Sealing and Lubrication: Features that protect the bearing from contaminants and ensure proper lubrication are essential for maintaining performance and extending the bearing’s life.
- Material and Coating: The choice of materials and surface coatings can significantly impact the bearing’s resistance to wear, corrosion, and environmental conditions.
Comparing conveyor roller bearings manufacturers and their products involves a thorough assessment of these and other features, ensuring that the selected bearings meet the operational demands of the conveyor system while offering the best value and performance.
Ready to enhance your conveyor systems with our roller bearings? Submit your inquiry, and we’ll provide you with the best solutions.
Catalogs and Resources from Conveyor Roller Bearings Manufacturers
In the quest for the right conveyor roller bearings, access to detailed catalogs and resources is invaluable. These materials not only provide a comprehensive look at product offerings but also offer insights into the specifications, applications, and innovations that set each manufacturer apart. Conveyor roller bearings manufacturers understand the importance of this information to customers, ensuring that catalogs and resources are readily available and informative.
Accessing Manufacturer Catalogs
For professionals and businesses seeking detailed product information, manufacturer catalogs are a crucial resource. They offer an in-depth look at the range of conveyor roller bearings available, along with technical specifications, installation guides, and application examples. Notable resources include:
- Mathews Conveyor Bearings Catalog: This catalog provides a wide array of conveyor bearings, showcasing the variety and versatility of their product line, suitable for different industry needs.
- Nice Bearing Catalog: Known for precision and quality, the Nice bearing catalog offers detailed product specifications and engineering data, assisting in the selection of the right bearing for specific applications.
These catalogs are designed to facilitate the decision-making process, providing all necessary information to select the most appropriate bearings for any conveyor system requirement.
Understanding the Frantz Bearings Offerings
Frantz bearings stand out in the conveyor roller bearings market for several reasons. Known for their durability and performance, Frantz’s offerings include a range of conveyor bearings designed to meet the rigorous demands of various industries. What sets Frantz apart is their commitment to quality and innovation, with bearings that offer:
- Superior Load Capacity: Designed to handle heavy loads without compromising performance.
- Exceptional Durability: Manufactured to withstand harsh environments and continuous operation.
- Innovative Design: Incorporating features that reduce maintenance needs and extend the lifespan of the bearings.
Frantz bearings are a testament to the manufacturer’s dedication to providing solutions that enhance the efficiency and reliability of conveyor systems. Their offerings are a reflection of the advanced engineering and manufacturing capabilities that have made them a preferred choice among conveyor roller bearings manufacturers.
Catalogs and resources from conveyor roller bearings manufacturers are essential tools for engineers, designers, and maintenance professionals. They not only aid in the selection process but also provide a wealth of knowledge on the latest advancements and best practices in the industry. By leveraging these resources, businesses can ensure they are making informed decisions that will benefit their operations in the long term.
FAQs About Conveyor Roller Bearings Manufacturers
Roller bearings are manufactured by a diverse array of companies worldwide, ranging from industry giants to specialized local manufacturers. Notable names include TIMKEN, SKF, NSK, FAG (part of the Schaeffler Group), and NTN, each renowned for their engineering excellence, quality assurance, and innovation in bearing technology. These manufacturers have established themselves as leaders in the field by consistently delivering products that meet the highest standards of performance and reliability. They invest heavily in research and development to introduce bearings that address the evolving needs of various industries, including automotive, aerospace, and industrial machinery. Local manufacturers also play a crucial role, offering customized solutions and specialized products tailored to specific market demands. The choice of manufacturer often depends on the application’s specific requirements, such as load capacity, speed, and environmental conditions, with each manufacturer bringing its unique strengths to the table.
Conveyors utilize a variety of bearings to ensure smooth operation and efficiency across different applications. The most common types include deep groove ball bearings, which are known for their versatility and ability to handle both radial and axial loads, making them suitable for a wide range of conveyor systems. Tapered roller bearings are preferred for applications experiencing high radial and axial loads, offering durability and resistance to overturning moments. Spherical roller bearings are used in heavy-duty applications for their ability to accommodate misalignment while handling high radial loads. Cylindrical roller bearings are chosen for their high radial load capacity and suitability for high-speed applications. Additionally, needle roller bearings find use in areas where space is limited, providing high load capacity in a compact design. Each type offers unique advantages, with the selection based on factors like load, speed, and the operational environment of the conveyor system.
What are the three types of roller bearings
The three primary types of roller bearings are cylindrical, tapered, and spherical roller bearings, each designed to serve distinct applications and load-handling capabilities. Cylindrical roller bearings feature rollers that are slightly longer than their diameter, ideal for high-speed applications because of their ability to handle high radial loads with minimal friction. Tapered roller bearings, recognizable by their cone-shaped rollers and raceways, are designed to handle both radial and axial loads, making them suitable for applications requiring precision and durability under heavy load conditions. Spherical roller bearings, equipped with an outer ring that has a spherical shape, allow for angular misalignment and are particularly useful in applications prone to shaft misalignment or bending. These bearings are known for their robustness and are commonly used in heavy industrial environments, where load conditions can be severe and varied.
The most common type of roller bearing is the tapered roller bearing, renowned for its versatility and capacity to accommodate both radial and axial loads efficiently. Its unique design, featuring tapered rollers arranged between tapered inner and outer ring raceways, allows it to handle a combination of forces. This capability makes it indispensable in many applications, from automotive wheel bearings to heavy machinery and industrial conveyors. The tapered roller bearing’s ability to support substantial loads and withstand harsh conditions while providing precise control and reduced friction has cemented its status as a go-to solution in a broad array of mechanical systems. Its prevalence across various industries underscores its reliability and effectiveness in meeting the demands of diverse operational requirements.
Last Updated on July 26, 2024 by Jordan Smith
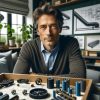
Jordan Smith, a seasoned professional with over 20 years of experience in the conveyor system industry. Jordan’s expertise lies in providing comprehensive solutions for conveyor rollers, belts, and accessories, catering to a wide range of industrial needs. From initial design and configuration to installation and meticulous troubleshooting, Jordan is adept at handling all aspects of conveyor system management. Whether you’re looking to upgrade your production line with efficient conveyor belts, require custom conveyor rollers for specific operations, or need expert advice on selecting the right conveyor accessories for your facility, Jordan is your reliable consultant. For any inquiries or assistance with conveyor system optimization, Jordan is available to share his wealth of knowledge and experience. Feel free to reach out at any time for professional guidance on all matters related to conveyor rollers, belts, and accessories.