Optimizing Operations: Conveyor Roller Belt Drive Insights
Conveyor roller belt drive systems are at the core of modern industrial operations, serving as the backbone for material handling across various sectors. These systems utilize a combination of rollers and a belt to efficiently move goods and materials from one point to another within facilities. This introductory section will guide you through the basics of what a conveyor roller belt drive is, and why it’s indispensable in today’s fast-paced production environments. Furthermore, we will provide a brief overview of what to expect in the subsequent sections of this blog post, which delve into the functionality, applications, and advancements of conveyor roller belt drive technologies. This discussion is essential for understanding how these systems optimize operational workflows and enhance productivity.
What are Conveyor Roller Belt Drives
Definition and Functionality
A conveyor roller belt drive is a mechanized system designed to transport materials within an array of industrial settings. This system consists of rollers mounted in series, driven by a belt that is typically powered by electric motors. The rollers support and guide the belt that carries materials from one location to another, efficiently minimizing human labor and the time needed for transportation.
The use of conveyor roller belt drives spans various industries due to their adaptability and efficiency. For example, in the manufacturing sector, these systems facilitate the assembly line process by moving parts between workstations seamlessly. In the warehousing and logistics field, conveyor roller belt drives expedite the sorting and shipping processes, increasing throughput. The mining industry relies on these robust systems to transport extracted materials over long distances, even in harsh environments. Additionally, the food processing industry uses these conveyors to handle products safely and hygienically from one stage of production to the next.
Importance in Material Handling
The advantages of using conveyor roller belt drives in material handling are significant and varied. Primarily, these systems enhance efficiency; they allow for continuous operation and can move a vast array of goods at consistent speeds. This continuous flow reduces downtime and increases productivity across operations. Moreover, conveyor roller belt drives are highly reliable; designed for long-term use, they require minimal maintenance and can operate under substantial load conditions without failure.
These benefits are evident in several practical applications. In e-commerce fulfillment centers, conveyor roller belt drives speed up the processing of orders by swiftly moving products through picking and packing zones. In automotive manufacturing, these conveyors transport components to assembly lines, ensuring a steady supply of parts without interruptions. In airport baggage handling systems, reliability and efficiency are crucial, and conveyor roller belt drives provide the robustness needed to handle large volumes of luggage reliably. Lastly, in the pharmaceutical industry, these systems guarantee the gentle handling required to transport sensitive products, thereby maintaining integrity and compliance with safety standards.
Conveyor Roller Belt Drive Systems on the Market
Used Conveyor Roller Belt Drives
Purchasing used conveyor roller belt drives can be an economically advantageous decision, especially for companies looking to expand operations or replace worn-out systems without the hefty investment associated with new equipment. One of the main benefits of buying used is the significant cost savings, as used drives often come at a fraction of the price of new ones. Additionally, this option can lead to shorter lead times compared to waiting for new equipment to be manufactured and delivered.
However, there are also cons to consider. The primary drawback is the potential for increased maintenance costs and shorter service life, as the equipment may have already undergone considerable wear and tear. There’s also the risk of inheriting problems from previous usage that might not be apparent at the time of purchase.
When looking to purchase used conveyor roller belt drives, it’s crucial to inspect the equipment thoroughly. Look for signs of excessive wear, such as worn-out belts or damaged rollers, which could indicate looming repair needs. Ensure that the drive is compatible with your existing systems to avoid integration issues. Check maintenance records to understand the history of the equipment and confirm it has been properly serviced. Lastly, consider the seller’s reputation to ensure reliability and support after purchase.
New Conveyor Roller Belt Drives for Sale
Investing in new conveyor roller belt drives offers several advantages that can justify the initial higher cost. First, new equipment typically comes with the latest technology, which can improve efficiency and compatibility with modern control systems. This can lead to better integration with digital tracking and management systems, enhancing overall productivity. New drives also offer longer lifespans and lower maintenance costs due to their unused condition and latest designs.
Moreover, new conveyor roller belt drives often come with manufacturer warranties and support services, providing peace of mind and protection against early failures. Investing in new equipment can also reflect positively on a company’s commitment to reliability and safety, which can be important for maintaining corporate image and compliance with industry standards.
When purchasing new conveyor roller belt drives, it’s important to identify reputable manufacturers and suppliers. Companies like Hytrol, Dorner, and Siemens are known for their high-quality conveyor solutions and comprehensive customer support. They offer a range of conveyor roller belt drives that can be tailored to specific industry needs, ensuring that you get the most out of your investment. Additionally, dealing with established suppliers often ensures access to ongoing service and parts availability, crucial for minimizing downtime and maintaining high operational standards.
Categories and Specifications About Conveyor Roller Belt Drive
Conveyor Roller Belt Drive Dimensions
When selecting a conveyor roller belt drive, understanding the dimensions and specifications that best fit your application is crucial. Common dimensions for conveyor roller belt drives include the belt width, which typically ranges from 6 inches up to 60 inches or more, and the length of the conveyor, which can vary greatly depending on the installation site and the needs of the material handling system.
To determine the right size for your application, consider the size and weight of the materials being transported. The belt width should be wide enough to handle the largest items without overcrowding, while the conveyor length should match the layout of your facility, allowing for efficient transport from start to end points. Load capacity is also critical; ensure the system can handle the maximum expected load plus a margin for safety. Additionally, the speed of the conveyor should align with your operational requirements to maintain a balanced and efficient workflow.
Conveyor Belt Roller Types
There are several types of conveyor belt rollers, each designed to meet specific operational needs and environments. Here are four common types:
- Gravity Rollers: These are non-powered and work by allowing the conveyor belt to glide over them, driven by gravity or manual force. They are suitable for lightweight applications and are cost-effective, but not ideal for heavy or uneven loads.
- Motorized Rollers: Equipped with internal motors, these rollers drive the conveyor belt directly and provide greater control over speed and handling. They are excellent for applications requiring precise movement and speed, such as in automated warehouses.
- Impact Rollers: Positioned at conveyor loading zones, impact rollers help absorb the shock and impact of loading materials onto the conveyor, which protects the belt and other components from damage. They are crucial in heavy-duty applications like mining and quarrying.
- Tapered Rollers: Ideal for curves and corners in a conveyor system, tapered rollers help maintain the alignment and tension of the conveyor belt. They prevent the belt from slippage and ensure smooth operation in curved sections.
Each type of roller offers specific advantages. Gravity rollers are economical and simple to install, making them ideal for lightweight and low-speed applications. Motorized rollers provide enhanced control and efficiency for automated systems. Impact rollers extend the lifespan of the conveyor system in rough operational environments, and tapered rollers are essential for maintaining conveyor integrity in complex layouts. When selecting the type of roller for your conveyor roller belt drive, consider these characteristics to match the rollers to your application’s specific demands.
Manufacturers and Design Choices About Conveyor Roller Belt Drive
Conveyor Roller Manufacturer Spotlight
In the world of conveyor roller belt drives, several manufacturers stand out due to their innovation, quality, and reliability. Companies like Hytrol, Interroll, and Dematic are considered leaders in the conveyor technology sector.
Hytrol is renowned for its comprehensive range of conveyor solutions that cater to various industries from distribution to manufacturing. Their conveyor roller belt drive systems are particularly praised for their durability and ease of integration into existing setups. Hytrol’s commitment to research and development ensures that they remain at the forefront of conveyor technology, continually improving speed, efficiency, and system intelligence.
Interroll offers unique modular conveyor solutions that are highly flexible and scalable, making them ideal for businesses that anticipate future growth or changes in production demands. Their products are known for high energy efficiency and low maintenance costs, which help businesses reduce their operational expenses over time.
Dematic specializes in automated material handling systems, integrating advanced software with their conveyor roller belt drives to optimize warehouse and distribution center operations. Dematic’s systems are tailored to boost productivity and accuracy in high-volume environments, making them indispensable in the logistics and e-commerce sectors.
Custom Roller Belt Conveyors
Customization is a key aspect when it comes to conveyor roller belt drives, as different applications require specific features to enhance functionality and efficiency. Many manufacturers offer tailor-made solutions that can precisely fit the unique needs of their customers.
Custom roller belt conveyors can be designed to handle particular materials, such as those that are abrasive, fragile, or require a non-standard temperature environment during transport. For instance, food processing industries often need conveyors with easy-to-clean surfaces and materials that comply with food safety standards.
Another customization option is the integration of various sensor technologies. These can monitor the condition of the conveyor system in real-time, predicting maintenance needs before a breakdown occurs, thus reducing downtime.
Additionally, the size and shape of the conveyor can be customized to fit specific spatial configurations. This includes adjustable lengths and widths, as well as curved or inclined sections to navigate complex routes within a facility.
By leveraging these customization options, businesses can ensure that their conveyor roller belt drive systems are not only effective and efficient but also perfectly aligned with their operational needs and constraints.
Technical Aspects of Conveyor Roller Belt Drives
Roller Belt Conveyor Mechanics
Understanding the mechanics of a conveyor roller belt drive involves examining its core components, which include the belt drive roller and the conveyor drive roller. These elements are pivotal in the functioning of the conveyor system.
The belt drive roller is responsible for the transmission of power from the motor to the conveyor belt. It’s typically coated with a high-friction material to ensure that it effectively grips the conveyor belt, reducing slippage and enhancing the overall drive performance. The drive roller must be robust and precisely engineered to handle the load and continuous operation without excessive wear.
The conveyor drive roller, on the other hand, supports the belt and guides it along its path. It is designed to work under varying load conditions and operational speeds. The rollers are spaced strategically along the conveyor frame to support the belt and the materials being transported. This spacing is crucial for preventing sagging of the belt, which can lead to uneven load distribution and increased wear on the belt and rollers.
These rollers are made from materials such as steel, stainless steel, or plastic, depending on the application requirements, such as weight, chemical exposure, and required speed of the conveyor. Precision in design and manufacturing of these components ensures efficiency, durability, and a reduced need for maintenance.
Automation and Technology
In the realm of conveyor roller belt drives, automation and technology play crucial roles in enhancing system efficiency and adaptability. Motorized belt conveyors represent a significant advancement in this field, incorporating motors directly within the roller assembly to provide controlled, consistent motion that is easily integrated into digital management systems.
Recent trends in automation include the integration of Internet of Things (IoT) sensors and artificial intelligence (AI). These technologies offer real-time tracking of conveyor performance and maintenance needs. IoT sensors can monitor various parameters such as speed, temperature, and load capacity, providing data that can be used to optimize conveyor operation and predict potential breakdowns before they occur.
AI plays a role in dynamically adjusting conveyor operations based on incoming data streams. For example, AI can automatically adjust the speed of the conveyor roller belt drive based on the current load and upcoming production schedules to maximize throughput and reduce energy consumption.
Another trend is the use of robotic systems integrated with conveyor roller belt drives to automate loading and unloading processes. These systems are particularly useful in high-volume shipping environments or where precision and repetitive tasks are required.
These technological advancements not only increase the productivity and efficiency of conveyor roller belt drives but also enhance their reliability and extend their operational life, making them more cost-effective and adaptable to future industrial needs.
FAQs About Conveyor Roller Belt Drive
A belt-driven roller conveyor is a type of conveyor system that uses belts to drive rollers, which in turn move goods and materials along the conveyor path. This system consists of a series of rollers that are attached to a belt, which is typically powered by an electric motor. The belt loops around the rollers, causing them to rotate and push the materials along the conveyor. Belt-driven roller conveyors are highly efficient for transporting products over long distances within a facility, especially where smooth, continuous movement is essential. They are commonly used in warehouses, distribution centers, and manufacturing plants for tasks such as assembly lines, sorting operations, and packaging processes. Their versatility allows them to handle a wide range of items from small boxes to large pallets, making them a fundamental part of modern material handling and logistics.
While both “conveyor belt” and “belt drive” involve belts, they serve different functions. A conveyor belt is part of a conveyor system used primarily for moving materials and goods from one location to another. It typically runs over a series of metal or plastic rollers and is driven by motors or manual effort. The main purpose of a conveyor belt is to transport objects along a fixed path within industrial or commercial settings. On the other hand, a belt drive is a mechanism that transmits power between machinery components, typically using belts and pulleys to link rotating shafts. It can be found in various applications, including in machinery, vehicles, and other equipment where transferring rotational force is necessary. Therefore, while a conveyor belt might be part of a system that includes a belt drive for movement, it is not itself a belt drive.
A belt conveyor roller is an essential component of a belt conveyor system. It supports the conveyor belt and provides a smooth surface over which the belt can travel. The rollers are cylindrical and are usually made from materials like steel, plastic, or rubber, depending on the application’s requirements. They are spaced strategically along the length of the conveyor to support the weight and movement of the materials being transported. The design and material of the rollers play a crucial role in the system’s efficiency, as they must minimize friction and wear to maintain a consistent flow of goods. In addition to supporting the belt, these rollers can help guide the belt and maintain its alignment, preventing slippage and reducing the potential for operational disruptions.
The drive mechanism of a belt conveyor refers to the components that provide the motive power to move the conveyor belt. This typically includes a motor, drive belt, and pulleys, along with gearboxes and drive drums or rollers. The motor generates power, which is transmitted through the drive belt and pulleys to the drive drum or roller. This drum then turns, causing the conveyor belt to move along the rollers that support it. The effectiveness of the drive mechanism is critical to the overall performance of the conveyor system, as it must provide reliable and consistent power to handle varying loads and operational demands. The choice of motor and gearbox often depends on the specific requirements of the application, including speed, torque, and the type of materials being transported. Proper maintenance and alignment of these components are vital to ensure efficient and long-lasting operation of the belt conveyor system.
Last Updated on April 17, 2024 by Jordan Smith
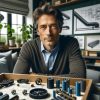
Jordan Smith, a seasoned professional with over 20 years of experience in the conveyor system industry. Jordan’s expertise lies in providing comprehensive solutions for conveyor rollers, belts, and accessories, catering to a wide range of industrial needs. From initial design and configuration to installation and meticulous troubleshooting, Jordan is adept at handling all aspects of conveyor system management. Whether you’re looking to upgrade your production line with efficient conveyor belts, require custom conveyor rollers for specific operations, or need expert advice on selecting the right conveyor accessories for your facility, Jordan is your reliable consultant. For any inquiries or assistance with conveyor system optimization, Jordan is available to share his wealth of knowledge and experience. Feel free to reach out at any time for professional guidance on all matters related to conveyor rollers, belts, and accessories.