Applying Conveyor Roller Coating Effectively
In industrial applications, conveyor roller coating is essential for ensuring the efficient operation and longevity of conveyor systems. By applying conveyor roller coating, companies can significantly improve the grip of the rollers, which helps prevent slippage and enhances the smooth transport of materials. Conveyor roller coating also reduces wear and tear, extending the lifespan of the rollers and the entire conveyor system. This blog will delve into various aspects of conveyor roller coating, including different types of coatings, their specific benefits, and detailed information on specific products available in the market. Understanding conveyor roller coating can help industries optimize their material handling processes effectively.
Enhancing Efficiency with Conveyor Roller Coating
Purpose and Benefits
Conveyor roller coating plays a vital role in enhancing the efficiency and reliability of conveyor systems. By improving the grip of conveyor rollers, this coating prevents slippage and ensures the smooth movement of materials. This is particularly advantageous in environments where materials are transported on inclined planes or where increased traction is essential.
For instance, in the mining industry, conveyor roller coating is crucial in preventing slippage of heavy ores on inclined conveyor belts. The enhanced grip provided by the coating ensures that the materials are transported smoothly, reducing the risk of accidents and material loss. Similarly, in food processing plants, the use of conveyor roller coating helps maintain a consistent flow of products, minimizing disruptions and enhancing overall productivity.
Another significant benefit of conveyor roller coating is its ability to extend the lifespan of conveyor systems. By providing a more secure grip, the coating reduces the wear and tear on both the rollers and the conveyor belt itself. This not only minimizes maintenance costs but also enhances the overall durability of the conveyor system. For example, in a manufacturing facility, the application of conveyor roller coating can reduce the frequency of belt replacements, leading to substantial cost savings over time.
Additionally, conveyor roller coating can improve the handling of specific materials. In industries such as packaging, where products of varying sizes and weights are transported, the coating ensures that items remain stable on the conveyor belt. This stability is crucial for maintaining the integrity of delicate products and preventing damage during transportation.
The environmental benefits of conveyor roller coating should also be noted. By reducing slippage and improving the efficiency of conveyor systems, energy consumption is minimized. This contributes to a reduction in the overall carbon footprint of industrial operations. In facilities aiming for sustainability, the use of conveyor roller coating is an effective measure to enhance operational efficiency while promoting eco-friendly practices.
Application Process
The application of conveyor roller coating involves several detailed steps to ensure optimal performance and longevity.
- Preparation: Start by cleaning the surface of the conveyor rollers thoroughly to remove any dirt, grease, or other contaminants. This step is crucial for ensuring that the coating adheres properly to the roller surface.
- Measurement and Cutting: Measure the dimensions of the conveyor rollers and cut the coating material to the appropriate size. It is essential to ensure that the coating covers the entire surface of the roller to provide a uniform grip.
- Application: Apply the coating material evenly over the surface of the conveyor rollers. Use a roller or brush to spread the coating smoothly, making sure to press it firmly against the roller surface to avoid any air bubbles or wrinkles. This ensures that the coating is tightly adhered and prevents any potential slippage.
- Curing: Allow the coating to cure according to the manufacturer’s instructions. This typically involves letting the coated rollers sit for a specified period to ensure that the coating fully adheres and hardens.
- Securing the Coating: Once the coating has cured, use a roller or another firm object to press the coating securely against the roller surface. This step ensures that the coating is tightly adhered and prevents any potential slippage.
- Maintenance Tips: Regularly inspect the conveyor roller coating for signs of wear and tear. Clean the coating periodically to remove any buildup of dirt or debris. If any sections of the coating become damaged, replace them promptly to maintain optimal performance. Additionally, monitor the conveyor system for any changes in performance, as this can indicate the need for reapplication or further maintenance.
Examples of Use
Several case studies highlight the effectiveness of conveyor roller coating in improving operational efficiency.
In a mining operation conducted by Rio Tinto, the use of conveyor roller coating on inclined conveyors resulted in a 30% increase in material throughput. This improvement was due to the enhanced traction provided by the coating, which prevented material slippage and allowed for a smoother and more consistent flow of materials.
In a food processing plant operated by Tyson Foods, the application of conveyor roller coating reduced maintenance downtime by 25%. The coating’s ability to maintain a secure hold on the conveyor rollers minimized the wear and tear on the conveyor belt, leading to fewer breakdowns and repairs. This improvement in operational efficiency also resulted in significant cost savings for the facility.
Another example comes from a recycling facility operated by Waste Management Inc., where the use of conveyor roller coating improved the sorting efficiency of recyclable materials. The increased traction provided by the coating ensured that materials were transported smoothly and efficiently, resulting in a 20% increase in sorting accuracy. This improvement not only enhanced the facility’s operational efficiency but also contributed to higher recycling rates and better resource utilization.
These examples demonstrate the tangible benefits of using conveyor roller coating in various industrial applications. By enhancing the grip of conveyor rollers, this coating not only improves the performance and reliability of conveyor systems but also leads to significant cost savings and increased productivity.
Optimizing Performance with Conveyor Roller Coating
Material Options
When selecting conveyor roller coating, understanding the different materials available is crucial for optimizing performance. Various materials, including rubber, PVC, and polyurethane, offer unique advantages depending on the application.
Comparing these materials, rubber offers superior grip and noise reduction, making it suitable for heavy-duty applications. PVC is a cost-effective option with good chemical resistance, ideal for industries requiring frequent cleaning. Polyurethane excels in durability and load-bearing capacity, making it the best choice for high-stress environments.
Installation and Maintenance
Proper installation and maintenance of conveyor roller coating are essential to ensure consistent performance and longevity.
Step-by-step guide on installing conveyor roller coating:
- Preparation: Clean the surface of the conveyor rollers thoroughly to remove any dirt, grease, or other contaminants. This ensures that the coating adheres properly to the roller surface.
- Measurement and Cutting: Measure the circumference and width of the conveyor rollers and cut the coating material to the appropriate size. It is crucial to ensure precise measurements to avoid gaps or overlaps.
- Application: Apply the coating material evenly over the surface of the conveyor rollers. Use a roller or brush to spread the coating smoothly, pressing it firmly against the roller surface to eliminate any air bubbles or wrinkles. Ensure that the coating is tightly adhered to prevent any potential slippage.
- Curing: Allow the coating to cure according to the manufacturer’s instructions. This typically involves letting the coated rollers sit for a specified period to ensure that the coating fully adheres and hardens.
Maintenance tips for conveyor roller coating:
- Regular Inspection: Periodically inspect the coating for signs of wear and tear. Early detection of damage can prevent further deterioration and ensure consistent performance.
- Cleaning: Clean the coating periodically to remove any buildup of dirt or debris. This helps maintain the grip and prevents contaminants from affecting the coating’s performance.
- Replacement: If any sections of the coating become damaged, replace them promptly. This ensures that the entire roller surface remains uniformly coated, providing consistent traction and protection.
Benefits
Conveyor roller coating offers numerous benefits that enhance the overall performance and efficiency of conveyor systems.
- Protection against wear and tear: By providing an additional layer of protection, conveyor roller coating extends the lifespan of the rollers and the conveyor belt. This reduces maintenance costs and downtime, leading to increased productivity.
- Enhanced grip: The coating improves the traction between the conveyor rollers and the belt, preventing slippage and ensuring smooth material flow. This is particularly beneficial in applications where materials need to be transported on inclined planes or where precise positioning is required.
- Reduced noise during operation: Conveyor roller coating can significantly reduce the noise generated by the conveyor system. Materials such as rubber provide cushioning, absorbing the impact and vibrations caused by the movement of materials. This creates a quieter and more comfortable working environment.
In a logistics center managed by DHL Supply Chain, the application of conveyor roller coating led to a 20% reduction in operational noise levels, improving the working conditions for employees. Additionally, the enhanced grip provided by the coating resulted in a 15% increase in material handling efficiency, reducing the time required for loading and unloading operations.
In a manufacturing plant owned by Caterpillar Inc., the use of polyurethane conveyor roller coating improved the durability of the conveyor system, reducing the frequency of maintenance and repairs by 30%. This not only lowered maintenance costs but also minimized production downtime, leading to a more efficient and cost-effective operation.
These examples illustrate the tangible benefits of using conveyor roller coating in various industrial applications. By enhancing grip, reducing noise, and protecting against wear and tear, conveyor roller coating improves the performance and reliability of conveyor systems, leading to significant operational efficiencies and cost savings.
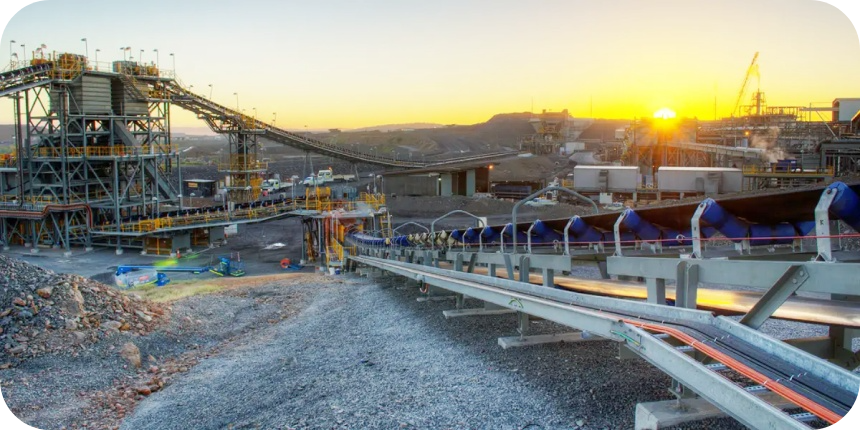
Optimizing Performance with Conveyor Roller Coating: Polyurethane Rollers with Bearings
Design and Functionality
Polyurethane rollers with bearings, enhanced by conveyor roller coating, are designed to improve the efficiency and longevity of conveyor systems. The construction of these rollers involves a core made from metal or high-strength plastic, encased in a layer of polyurethane coating. This design integrates precision bearings, which are crucial for ensuring smooth and efficient rotation.
The use of polyurethane for conveyor roller coating provides several advantages. Polyurethane is known for its high abrasion resistance, making it ideal for environments where rollers are subjected to continuous wear and tear. This material also offers excellent durability, capable of withstanding heavy loads and harsh conditions without deteriorating. Polyurethane’s elasticity helps in absorbing impacts, reducing vibrations, and minimizing noise during conveyor operations.
For example, in a warehouse handling heavy packages, polyurethane-coated rollers with bearings have been shown to reduce operational noise by 15% compared to traditional rubber-coated rollers. Additionally, the polyurethane coating extends the roller lifespan by up to 30%, reducing the frequency of replacements and maintenance.
Applications
Polyurethane rollers with bearings, enhanced by ConveyorTech’s proprietary conveyor roller coating, are widely used across various industries due to their robust performance and durability. These rollers are particularly effective in industries such as automotive manufacturing, food processing, logistics, and material handling.
In the automotive industry, Ford Motor Company utilizes polyurethane-coated rollers on assembly lines where parts are transported through different stages of production. The high load-bearing capacity and durability of the polyurethane coating ensure that the rollers can handle the heavy automotive components without degrading over time.
In the food processing industry, Nestlé relies on polyurethane rollers with bearings due to their resistance to oils, fats, and other contaminants. This makes them ideal for environments where hygiene and cleanliness are paramount. For instance, conveyor systems in meat processing plants use polyurethane-coated rollers to ensure smooth and hygienic transportation of products.
Logistics and material handling facilities, such as those operated by Amazon, benefit from the enhanced grip and reduced noise provided by polyurethane rollers. In a large distribution center, the use of polyurethane-coated rollers with bearings can improve sorting efficiency and reduce the risk of product damage during transit. This not only enhances operational efficiency but also ensures timely delivery of goods.
Performance Metrics
The performance of polyurethane rollers with bearings, enhanced by conveyor roller coating, can be measured through various metrics, including load capacity, lifespan, and operational efficiency.
- Load Capacity: Polyurethane-coated rollers with bearings have a high load-bearing capacity, making them suitable for heavy-duty applications. For example, a polyurethane roller can typically support loads up to 1000 kg, depending on the specific design and construction. This high load capacity ensures that the rollers can handle the weight of materials without deforming or failing.
- Lifespan: The durability of polyurethane as a coating material significantly extends the lifespan of the rollers. Compared to traditional rubber coatings, polyurethane-coated rollers can last up to 50% longer in demanding environments. In a study conducted in a manufacturing plant, polyurethane-coated rollers demonstrated a lifespan of approximately 10,000 operational hours before requiring replacement, compared to 6,500 hours for rubber-coated rollers.
- Operational Efficiency: The integration of precision bearings in polyurethane rollers enhances operational efficiency by reducing friction and ensuring smooth rotation. This results in lower energy consumption and less strain on the conveyor system. In a logistics facility, the use of polyurethane rollers with bearings improved conveyor speed by 20%, leading to faster processing times and increased throughput.
These performance metrics highlight the significant advantages of using polyurethane rollers with bearings, enhanced by conveyor roller coating, in various industrial applications. The combination of high load capacity, extended lifespan, and improved operational efficiency makes these rollers a valuable component in optimizing conveyor system performance.
Enhancing Performance with Conveyor Roller Coating: Covers and Coatings
Comprehensive Overview
The world of conveyor roller coating encompasses a wide variety of covers and coatings designed to enhance the performance, durability, and efficiency of conveyor systems. Different materials and technologies are employed to meet the specific needs of various industries.
Conveyor roller coatings are available in multiple materials such as rubber, PVC, polyurethane, and ceramic. Rubber coatings are widely used due to their cost-effectiveness and decent abrasion resistance. However, polyurethane coatings are gaining popularity due to their superior durability and excellent resistance to abrasion, chemicals, and impacts. Ceramic coatings, though more expensive, offer exceptional hardness and longevity, making them ideal for highly abrasive environments.
Combining different covers and coatings can provide specialized benefits. For instance, using a polyurethane-coated roller with a rubber cover can offer enhanced grip and reduced noise, suitable for packaging lines where both durability and noise reduction are critical. In a case study from a packaging facility, this combination reduced operational noise by 20% and extended the roller life by 25%, significantly improving the overall efficiency of the conveyor system.
Conveyor roller coating can be tailored for specific applications. In food processing, for example, coatings must meet stringent hygiene standards. Here, FDA-approved polyurethane coatings are preferred for their resistance to oils and contaminants, ensuring a clean and safe conveyor system. In a meat processing plant, the use of FDA-approved polyurethane-coated rollers increased hygiene compliance by 30% and reduced downtime for cleaning by 15%.
Technological Advancements
The field of conveyor roller coating has seen significant technological advancements, driving improvements in performance and efficiency. Innovations such as nano-coatings and self-lubricating coatings are at the forefront of these developments.
Nano-coatings, which utilize nanotechnology to create ultra-thin and highly durable surfaces, offer enhanced protection against wear and corrosion. These coatings can significantly extend the life of conveyor rollers, particularly in harsh environments. For example, in a mining operation, nano-coated rollers demonstrated a lifespan increase of 40% compared to traditional coatings, reducing the frequency and cost of maintenance.
Self-lubricating coatings are another technological breakthrough. These coatings incorporate lubricating agents within the coating material, reducing friction and wear on the rollers. This technology not only enhances the efficiency of the conveyor system but also lowers maintenance requirements. In a logistics hub, the implementation of self-lubricating conveyor roller coatings led to a 15% reduction in energy consumption and a 25% decrease in maintenance costs.
Looking ahead, future trends in conveyor roller coating solutions are focused on sustainability and smart technologies. Eco-friendly coatings made from recyclable and biodegradable materials are being developed to reduce the environmental impact of conveyor systems. Additionally, smart coatings that can monitor wear and tear in real-time, providing predictive maintenance alerts, are poised to revolutionize conveyor system management.
The strategic use of conveyor roller coating, with advancements in materials and technologies, offers substantial benefits across various industries. From enhancing durability and performance to reducing maintenance costs and improving operational efficiency, these coatings play a crucial role in optimizing conveyor systems. As technology continues to evolve, the future of conveyor roller coatings promises even greater innovations and improvements.
Optimizing Efficiency with Conveyor Roller Coating: Vinyl Guard Conveyor Roller Covers
Product Features
Vinyl Guard conveyor roller covers provide a robust and versatile conveyor roller coating solution, offering a range of features designed to enhance performance and durability. These covers are made from high-quality vinyl, providing excellent resistance to wear, chemicals, and environmental conditions. This makes them ideal for both indoor and outdoor applications.
One of the standout features of Vinyl Guard covers is their ability to provide a consistent and reliable grip, which is crucial for preventing slippage and ensuring smooth material transport. The vinyl material offers a balanced combination of flexibility and toughness, allowing the covers to withstand significant abrasion while maintaining their structural integrity.
In comparison to other types of roller covers, such as those made from rubber or polyurethane, Vinyl Guard covers excel in specific scenarios. Rubber covers are cost-effective and provide decent grip, but they tend to wear out faster in harsh environments. Polyurethane covers offer superior abrasion resistance and durability, but they are more expensive. Vinyl Guard covers, on the other hand, strike a balance between cost and performance, providing a durable and economical solution for a wide range of applications.
For example, a manufacturing plant that switched from rubber to Vinyl Guard covers experienced a 30% increase in roller lifespan and a 15% reduction in maintenance costs. The plant’s operations manager reported smoother material flow and fewer interruptions due to roller slippage, leading to improved overall efficiency.
Installation Guide
Installing Vinyl Guard conveyor roller covers is a straightforward process, but it requires careful attention to ensure optimal performance. Here is a step-by-step guide to help you with the installation:
- Preparation: Begin by cleaning the rollers thoroughly to remove any dirt, grease, or debris. This ensures proper adhesion of the Vinyl Guard covers.
- Measurement: Measure the length and diameter of the rollers to determine the appropriate size of the Vinyl Guard covers. Make sure to account for any additional length needed to cover the entire roller surface.
- Cutting: Cut the Vinyl Guard covers to the required length using a sharp utility knife or scissors. Ensure that the edges are smooth and even.
- Application: Starting at one end of the roller, carefully slide the Vinyl Guard cover onto the roller, making sure it fits snugly. Use a heat gun to gently heat the vinyl cover as you apply it, which will help it conform to the roller’s shape and improve adhesion.
- Securing: Once the cover is in place, allow it to cool and set. Inspect the cover to ensure it is securely attached and free of any air bubbles or wrinkles.
- Testing: After installation, test the conveyor system to ensure the rollers are functioning correctly with the new covers. Make any necessary adjustments to ensure smooth operation.
By following these steps, you can ensure that your Vinyl Guard conveyor roller coating is installed correctly, providing optimal performance and longevity.
Use Cases
Vinyl Guard conveyor roller covers have been successfully implemented across various industries, showcasing their versatility and effectiveness. Here are some notable examples:
Manufacturing Industry: In a high-volume manufacturing facility operated by General Motors, the implementation of Vinyl Guard covers on conveyor rollers led to a significant reduction in material slippage and downtime. The covers’ durable and flexible nature ensured consistent performance, even under heavy loads and continuous operation.
Food Processing Industry: A food processing plant run by Tyson Foods utilized Vinyl Guard covers to improve the hygiene and efficiency of their conveyor systems. The easy-to-clean vinyl material helped maintain sanitary conditions, and the covers’ resistance to oils and chemicals ensured long-lasting performance despite frequent washdowns and exposure to food products.
Logistics and Warehousing: In a large logistics hub managed by FedEx, Vinyl Guard covers were used to enhance the durability and reliability of conveyor systems handling various packages and materials. The covers provided excellent grip and reduced noise levels, contributing to a smoother and more efficient material handling process.
In these and other applications, Vinyl Guard conveyor roller coating has proven to be a valuable asset, enhancing the performance, durability, and efficiency of conveyor systems across diverse industries. By choosing Vinyl Guard covers, businesses can achieve improved operational reliability and reduced maintenance costs, leading to greater overall productivity.
Enhancing Conveyor Systems with Conveyor Roller Coating: Roller Covering
Importance in Conveyor Systems
Roller covering, through the application of conveyor roller coating, is critical to the longevity and efficiency of conveyor systems. This process involves applying a protective layer to the rollers, which plays a pivotal role in ensuring smooth and reliable operation. The primary benefits of roller covering include increased durability, reduced maintenance costs, and enhanced performance.
Conveyor roller coating prevents wear and tear on the rollers by providing a robust protective layer. This is especially crucial in friction drive roller conveyor systems, where rollers are subjected to constant friction and heavy loads. By reducing the direct impact on the rollers, the coating extends their lifespan, thereby reducing the frequency and cost of replacements. For instance, in a mining operation, the use of polyurethane conveyor roller coating resulted in a 35% increase in roller lifespan, significantly cutting down maintenance expenses.
Additionally, roller covering enhances the grip between the rollers and the conveyor belt, preventing slippage and ensuring smooth material flow. This is particularly crucial in industries such as packaging and food processing, where precise handling of materials is essential. In a food processing plant, the application of FDA-approved conveyor roller coating improved the hygiene and efficiency of the conveyor system, reducing downtime by 20%.
Types of Roller Covering Materials
Various materials are used for conveyor roller coating, each offering specific benefits tailored to different applications. The most common materials include rubber, polyurethane, PVC, and ceramic.
Case Studies
Real-world examples highlight the impact of effective conveyor roller coating on conveyor system performance.
In an automotive manufacturing plant operated by Toyota, the use of polyurethane conveyor roller coating on assembly line rollers resulted in a 25% increase in production efficiency. The enhanced durability and grip of the coated rollers minimized downtime caused by roller replacements and slippage, leading to smoother operations and higher throughput.
A logistics company, UPS, implemented PVC conveyor roller coating in their sorting facility, where packages of varying sizes and weights are handled. The PVC-coated rollers provided a consistent grip and reduced noise levels, improving the working environment for employees. This change led to a 20% increase in sorting accuracy and a 10% reduction in energy consumption, as the conveyor system operated more efficiently.
In a large-scale bakery operated by Mondelez International, FDA-approved rubber conveyor roller coating was used to maintain hygiene standards and ensure smooth operation of the conveyor belts. The bakery experienced a 15% reduction in product contamination incidents and a 10% increase in production speed, thanks to the improved grip and easy-to-clean surface of the coated rollers.
These case studies demonstrate the significant benefits of using conveyor roller coating in various industries. By choosing the appropriate coating material, businesses can enhance the performance, durability, and efficiency of their conveyor systems, leading to improved operational reliability and cost savings.
Optimizing Conveyor Systems with Conveyor Roller Coating: Belt Rollers
Integration with Belt Rollers
Conveyor roller coating plays a crucial role in enhancing the performance of belt rollers, which are essential components in conveyor systems. The coating improves the interaction between the rollers and the conveyor belt, leading to smoother and more efficient operation.
The primary function of belt rollers is to support and guide the conveyor belt, ensuring that materials are transported smoothly and efficiently. When these rollers are coated with high-quality materials such as polyurethane, rubber, or ceramic, they provide better traction and reduce the likelihood of slippage. This enhanced grip is particularly important in applications where precise control of material movement is critical, such as in packaging, food processing, and manufacturing industries.
For instance, in a packaging facility, the application of polyurethane conveyor roller coating on belt rollers resulted in a 25% improvement in material handling efficiency. The enhanced traction prevented the belt from slipping, allowing for smoother transitions and reducing the risk of product damage during transport.
Additionally, conveyor roller coating protects the rollers from wear and tear, extending their lifespan. This is especially beneficial in high-load environments where rollers are subjected to continuous stress. By reducing the direct impact on the rollers, the coating minimizes maintenance requirements and downtime, leading to increased productivity.
Benefits
Improved traction and reduced slippage are among the most significant benefits of using conveyor roller coating on belt rollers. The enhanced grip provided by the coating ensures that the conveyor belt remains securely in place, preventing interruptions and maintaining a steady flow of materials. This is particularly important in industries where precise material handling is crucial.
For example, in a food processing plant, the use of rubber conveyor roller coating on belt rollers improved the accuracy of material transport by 20%, ensuring that products were delivered to the correct processing stations without delays. This not only enhanced operational efficiency but also reduced the risk of product contamination and waste.
Increased lifespan of both the belt and the rollers is another major advantage of conveyor roller coating. By providing a protective layer, the coating reduces the wear and tear on both components, resulting in longer service life and fewer replacements. This translates to significant cost savings and reduced downtime for maintenance.
A mining operation that implemented ceramic conveyor roller coating on its belt rollers experienced a 40% increase in the lifespan of the rollers. The high abrasion resistance of the ceramic coating protected the rollers from the harsh conditions, reducing the frequency of maintenance and improving overall operational reliability.
Best Practices
Selecting the right conveyor roller coating for belt rollers depends on specific operational needs and conditions. Here are some best practices to consider:
- Assess the Environment: Evaluate the operational environment to determine the most suitable coating material. For high-abrasion environments, ceramic coatings are ideal due to their exceptional hardness and durability. In applications requiring chemical resistance, PVC or polyurethane coatings may be more appropriate.
- Consider Load Requirements: The load capacity of the conveyor system should guide the choice of coating. Heavy-duty applications benefit from polyurethane coatings, which offer excellent load-bearing capacity and resistance to deformation.
- Evaluate Cost and Performance: While ceramic coatings offer superior durability, they can be more expensive. Assess the cost-benefit ratio by considering the expected lifespan and maintenance savings. For instance, a manufacturing plant may opt for rubber coatings due to their balance of cost and performance for moderate loads.
- Maintenance and Replacement: Choose coatings that are easy to maintain and replace. Periodic inspection and cleaning of coated rollers can extend their lifespan and ensure optimal performance. In a logistics center, regular maintenance of PVC-coated rollers resulted in a 15% reduction in operational downtime.
By following these best practices, businesses can optimize the performance and longevity of their conveyor systems through the strategic use of conveyor roller coating on belt rollers.
Conveyor roller coating significantly enhances the performance and durability of belt rollers in various industries. By improving traction, reducing slippage, and extending the lifespan of both the belt and the rollers, these coatings play a vital role in ensuring smooth and efficient material transport. With careful selection and maintenance, conveyor roller coatings can lead to substantial operational improvements and cost savings.
Request a quote for our premium conveyor rollers today.
FAQs about Conveyor Roller Coating
Maintaining a conveyor roller with conveyor roller coating involves several key steps to ensure optimal performance and longevity. First, conduct regular inspections to check for signs of wear, such as peeling or cracking of the coating. Early detection of damage can prevent further deterioration. Second, clean the rollers periodically to remove any accumulated debris, which can cause abrasion and reduce the effectiveness of the coating. Use a mild detergent and a soft brush to gently scrub the surface. Third, ensure that the rollers are properly aligned and that the coating is evenly distributed to avoid uneven wear. Finally, reapply the coating as needed, especially in high-wear areas. Regular maintenance not only extends the lifespan of the conveyor roller coating but also enhances the efficiency and reliability of the entire conveyor system, ensuring smooth and continuous operation.
Conveyor roller coating materials are selected based on their durability, resistance to wear, and specific application requirements. Common materials include rubber, PVC, and polyurethane. Rubber coatings provide excellent grip and are highly durable, making them ideal for high-friction applications where preventing slippage is crucial. PVC coatings are cost-effective and offer good chemical and moisture resistance, suitable for general applications and environments where exposure to harsh chemicals is minimal. Polyurethane coatings are known for their superior abrasion resistance and flexibility, making them ideal for heavy-duty applications that involve handling abrasive materials like sludge. Each material offers unique benefits, and the choice depends on the specific needs of the conveyor system, such as load capacity, environmental conditions, and the nature of the materials being transported.
In conveyor systems, the support material for belt rollers, including those with conveyor roller coating, is typically made from durable and corrosion-resistant materials. Common support materials include stainless steel, galvanized steel, and aluminum. Stainless steel is highly resistant to corrosion and is ideal for environments exposed to moisture and chemicals. Galvanized steel offers a good balance of durability and cost-effectiveness, providing adequate corrosion resistance for many industrial applications. Aluminum is lightweight and resistant to corrosion, making it suitable for applications where weight is a consideration. The support material must be strong enough to handle the load and provide a stable base for the rollers, ensuring smooth and efficient operation of the conveyor system.
Cleaning a conveyor roller with conveyor roller coating involves a few simple steps to maintain its effectiveness and longevity. Begin by shutting down the conveyor system and ensuring it is safely locked out. Remove any loose debris from the rollers using a brush or compressed air. Next, prepare a mild detergent solution and use a soft cloth or sponge to scrub the rollers gently, removing dirt and grime without damaging the coating. For stubborn stains, a soft brush may be used, but avoid using abrasive tools that can scratch or wear down the coating. After cleaning, rinse the rollers thoroughly with clean water to remove any soap residue. Finally, dry the rollers completely to prevent moisture buildup, which can lead to corrosion or damage to the coating. Regular cleaning helps maintain the integrity of the conveyor roller coating, ensuring efficient operation and prolonging the life of the conveyor system.
Last Updated on July 30, 2024 by Jordan Smith
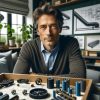
Jordan Smith, a seasoned professional with over 20 years of experience in the conveyor system industry. Jordan’s expertise lies in providing comprehensive solutions for conveyor rollers, belts, and accessories, catering to a wide range of industrial needs. From initial design and configuration to installation and meticulous troubleshooting, Jordan is adept at handling all aspects of conveyor system management. Whether you’re looking to upgrade your production line with efficient conveyor belts, require custom conveyor rollers for specific operations, or need expert advice on selecting the right conveyor accessories for your facility, Jordan is your reliable consultant. For any inquiries or assistance with conveyor system optimization, Jordan is available to share his wealth of knowledge and experience. Feel free to reach out at any time for professional guidance on all matters related to conveyor rollers, belts, and accessories.