Customizing Conveyor Roller Covers for Specific Needs
Conveyor systems are integral to the operations of various industries, including manufacturing, packaging, and distribution. These systems streamline processes, enhance efficiency, and reduce labor costs by automating the movement of goods across facilities. Central to the functionality of these systems are conveyor roller covers, which play a crucial role in improving the performance and extending the lifespan of conveyor rollers. These covers not only protect the rollers from wear and environmental damage but also reduce noise levels and increase traction, which helps prevent slippage and misalignment of goods. By enhancing grip and reducing operational noise, conveyor roller covers improve workplace safety and overall system effectiveness, making them essential components in the maintenance and enhancement of conveyor systems.
Importance of Conveyor Roller Covers
Conveyor roller covers are essential components in the management and operation of conveyor systems. These covers provide numerous benefits that enhance the efficiency, safety, and longevity of conveyor rollers. Here we will discuss six general benefits of using conveyor roller covers, specifically focusing on their roles in noise reduction, increasing grip, and providing protection against wear and tear.
Noise Reduction
One of the primary benefits of conveyor roller covers is their ability to significantly reduce operational noise. The materials used in roller covers, such as urethane or rubber, naturally absorb vibrations and dampen the sound produced when rollers operate. This reduction in noise can be crucial in environments where constant noise is a concern for the comfort and safety of workers, and can also comply with local noise regulation standards.
Increased Grip
Conveyor roller covers improve the grip between the rollers and the materials being conveyed. This is particularly important in applications where materials need to be moved at inclined angles or at high speeds. Covers made from materials with high friction coefficients, such as textured rubber, prevent slippage and misalignment of items on the conveyor, ensuring a smooth, continuous flow and reducing the risk of disruptions or accidents.
Protection Against Wear and Tear
The protective layer provided by conveyor roller covers shields the rollers from abrasions, scratches, and impact damages. Regular contact with materials can cause significant wear and tear on bare rollers, which can lead to costly maintenance or the need for premature replacement. By adding a cover, the lifespan of the rollers is extended, and the overall maintenance costs are reduced.
Chemical Resistance
Many conveyor roller covers are designed to resist chemicals that could otherwise corrode or degrade the surface of the rollers. For industries dealing with harsh chemicals, such as chemical processing or painting sectors, using chemically resistant covers can prevent operational hazards and equipment deterioration, preserving the integrity of the conveyor system.
Temperature Resistance
Conveyor systems that operate in extreme temperatures benefit greatly from roller covers that can withstand such conditions. Whether the environment involves high heat or sub-zero conditions, the right type of cover, such as silicone for heat resistance or PVC for cold resistance, can protect the rollers from thermal damage and keep the conveyor system running efficiently.
Aesthetic and Branding Opportunities
Aside from functional benefits, conveyor roller covers also offer aesthetic advantages. They can be customized in various colors and patterns that can be used to identify different lines or phases of operations within a facility, enhancing visual management. Additionally, branding opportunities exist as companies can use colors and logos on the covers to reinforce brand identity.
Conveyor roller covers are not just accessories but critical components that enhance the performance, safety, and durability of conveyor systems. Implementing quality conveyor roller covers brings operational benefits such as noise reduction, increased grip, and extensive protection against wear and tear, making them invaluable in many industrial applications. Incorporating these covers into a conveyor system setup ensures a higher return on investment through improved efficiency and reduced maintenance costs.
Types of Conveyor Roller Covers
Conveyor systems are integral to numerous industries, and the efficiency and longevity of these systems often hinge on the use of specialized conveyor roller covers. Each type of cover is designed to meet specific operational needs, from heavy-duty applications to customizable DIY solutions. Here, we explore various types of conveyor roller covers, including DIY options, heavy-duty covers, vinyl guard covers, and polyurethane sleeves, detailing their benefits and applications.
DIY Conveyor Roller Covers
DIY conveyor roller covers provide a flexible and cost-effective solution for businesses and individuals looking to tailor their conveyor systems to specific needs. These covers can be made from a variety of materials, including recycled plastics, rubber, or even fabric sleeves, depending on the application requirements. Users can customize the thickness, texture, and material type to match the exact needs of their conveyors, whether it’s for improved grip, increased durability, or chemical resistance. DIY covers are particularly popular in small-scale operations or in scenarios where standard sizes and features do not suffice.
Heavy Duty Conveyor Roller Covers
Designed to withstand extreme environments and handle heavy loads, heavy duty conveyor roller covers are essential for industries such as mining, quarrying, and other bulk material handling applications. These covers are typically made from highly durable materials like reinforced rubber or thick polyurethane to resist wear, tear, and abrasions. Additionally, they are often designed to withstand environmental challenges such as exposure to oils, greases, and various chemicals, ensuring that they maintain functionality and integrity even under tough conditions.
Vinyl Guard Conveyor Roller Covers
Vinyl guard conveyor roller covers are known for their durability and ease of installation. These covers are made from thick, durable vinyl that provides excellent protection against abrasions, moisture, and chemical exposures. The smooth surface of vinyl covers ensures that materials glide easily over the roller, reducing drag and thereby enhancing the efficiency of the conveyor system. Vinyl guard covers are commonly used in food processing, pharmaceuticals, and other industries where cleanliness and contamination prevention are critical.
Polyurethane Roller Sleeves
Polyurethane roller sleeves are favored for their exceptional durability and grip. Polyurethane is a versatile polymer that can be cast in varying hardness levels, which allows these covers to be perfectly tuned for specific applications—from soft, tacky versions that are ideal for delicate item handling to hard, durable versions for rough and abrasive materials. The advantages of polyurethane include its resistance to oils, solvents, and wear, making these sleeves a popular choice for a wide range of industrial applications. Their ability to absorb noise and reduce vibration is also a significant benefit, contributing to a quieter and smoother operation.
Each type of conveyor roller cover serves distinct purposes and offers unique advantages. From the customizable aspects of DIY covers to the rugged durability of heavy-duty and polyurethane options, and the clean, efficient functionality of vinyl guards, these covers collectively enhance the performance, safety, and operational lifespan of conveyor systems. Selecting the right type of conveyor roller covers is crucial in achieving optimal results and maintaining high standards of productivity and safety in any material handling setup.
Features and Benefits of Conveyor Roller Covers
Conveyor roller covers play a pivotal role in optimizing the performance of conveyor systems. They not only protect the rollers themselves but also enhance the process of material handling through various features. Below, we delve into the specifics of different coatings and the use of grip tape, each enhancing roller performance in unique ways.
Conveyor Roller Covers and Coatings
The choice of coating for conveyor roller covers significantly impacts their performance, especially concerning the type of material handled and the environment in which the rollers operate. Various coatings offer unique properties such as increased durability, resistance to environmental factors, and reduced friction, which are crucial in maintaining the efficiency of the conveyor system. Here are some common types of coatings:
- Rubber Coatings: Provide excellent grip and high impact resistance, making them suitable for handling bulky items. Rubber coatings are also effective in reducing noise levels within facilities.
- Silicone Coatings: Best known for their high-temperature resistance, silicone covers are ideal in environments where heat is a factor, such as in baking or curing operations. They also provide good release properties, minimizing stick-slip issues.
- Teflon (PTFE) Coatings: Offer exceptional chemical resistance and a slick surface, reducing friction and preventing materials from sticking to the roller. This type of coating is ideal for industries involving corrosive substances or where cleanliness is a priority.
- PVC Coatings: Versatile and economical, PVC covers resist chemicals, abrasion, and weathering, suitable for outdoor or harsh environments.
- Polyurethane Coatings: Known for their durability and wear resistance, these coatings provide a balance between grip and smoothness, allowing for efficient material transfer without damaging the items being conveyed.
Each type of coating ensures that the conveyor rollers perform optimally, tailored to specific environmental conditions and handling requirements. The right choice of material can reduce maintenance needs and prolong the lifespan of both the rollers and the conveyor belt.
Conveyor Roller Grip Tape
Another critical feature in the realm of conveyor roller covers is the application of grip tape. Grip tape is an adhesive product applied directly to the rollers to enhance traction, which prevents slippage and aids in the smooth conveyance of materials across the belt. Key benefits and considerations include:
- Enhanced Traction: Grip tape increases the coefficient of friction between the roller surface and the conveyed materials, ensuring stable and consistent movement, especially in incline or decline configurations.
- Versatility: Available in various textures and materials, grip tape can be selected based on the specific needs of the application, whether it needs to resist heat, abrasion, or exposure to chemicals.
- Ease of Application: Unlike permanent coatings, grip tape can be easily applied and replaced as needed, making it a convenient option for temporary or changing conditions on the conveyor line.
- Cost-Effectiveness: Using grip tape is a cost-efficient way to modify roller surfaces without the need for extensive downtime or replacement of rollers, ideal for testing different traction levels or as a short-term solution.
The features and benefits of conveyor roller covers, including various coatings and the use of grip tape, are designed to enhance the functionality and efficiency of conveyor systems. These enhancements help in managing the wear and tear on the equipment, improving material handling processes, and ensuring that operations run smoothly and efficiently. By selecting the appropriate roller covers and coatings, businesses can achieve better control over their conveyor operations and extend the lifespan of their equipment.
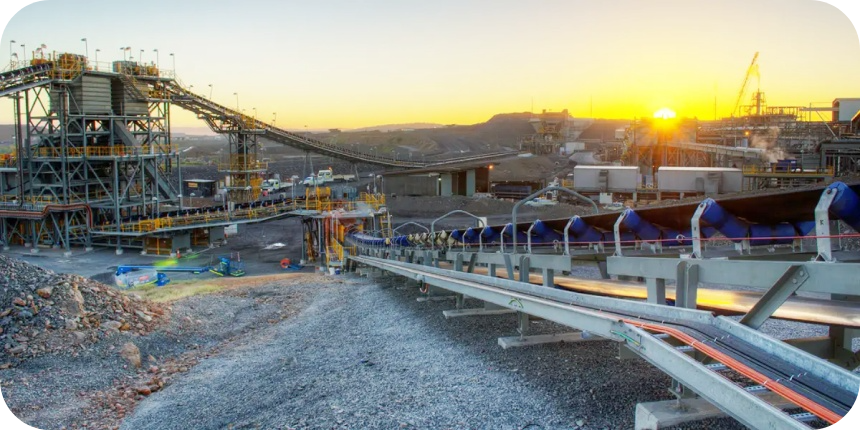
Choosing the Right Conveyor Roller Covers
Selecting the right conveyor roller covers is crucial for optimizing the performance and longevity of your conveyor system. The appropriate covers not only protect the rollers but also enhance the system’s efficiency by improving traction, reducing noise, and minimizing wear and tear. This selection process involves understanding the different types of rollers, their specific applications, and how covers can best complement these components.
Conveyor Roller Types
Conveyor rollers come in various types, each designed for different applications and subjected to different kinds of stresses and environments. Choosing the correct type of roller cover depends on understanding these variables:
- Gravity Rollers: Typically used in manual or gravity conveyors, these rollers move products manually or by natural gravity. They are best suited with lightweight rubber or polyurethane covers which enhance grip without requiring high friction levels.
- Live Powered Rollers: Used in powered conveyor systems where the roller is motorized to move the belt. Durable covers such as thick polyurethane or reinforced rubber are ideal here to handle the increased wear and tear.
- Grooved Rollers: Often used with round belts, grooved rollers require covers that fit into the grooves and do not flatten the belt’s round profile. Custom-shaped polyurethane covers are commonly used.
- Tapered Rollers: Ideal for curves, tapered rollers help maintain the alignment and orientation of products. Flexible and resilient covers like rubber or silicone are needed to maintain performance without compromising the roller geometry.
Understanding these roller types and their mechanisms is critical in selecting the right covers that provide the best performance, protection, and durability.
Conveyor Roller Parts
Compatibility with various roller parts is another essential factor when choosing conveyor roller covers. Effective maintenance and replacement depend on how well the covers integrate with the roller components. Consider the following parts:
- Tube: The cylindrical body of the roller where the cover is applied. The material of the tube (steel, aluminum, plastic) affects the choice of cover material regarding adhesion, durability, and environmental resistance.
- Shaft: Extends through the tube to mount the roller in the system. Covers should not interfere with the shaft’s fit or function, particularly at the end caps where the shaft often protrudes.
- Bearings: Facilitate smooth roller operation. Roller covers need to be selected based on their ability not to impede access to bearings for maintenance. Also, the cover material should withstand the grease or lubricants used with bearings.
- End Caps: Protect the ends of the roller and help mount the roller in the frame. Covers should be precisely sized to avoid overlapping or bunching at the ends, which can cause jamming and increased wear.
Each part of the roller must be considered to ensure that the cover enhances the roller’s function without compromising the system’s integrity. Proper assessment of these parts will aid in selecting covers that are easy to maintain, replace, and that align with the system’s operational demands.
Choosing the right conveyor roller covers involves a detailed understanding of the types of rollers used, their specific applications, and the compatibility of the covers with various roller parts. By carefully selecting covers based on these criteria, you can significantly enhance your conveyor system’s performance, reduce maintenance costs, and extend the service life of the rollers. This proactive approach in selecting roller covers not only improves efficiency but also ensures smoother operations and better material handling.
Application and Installation of Conveyor Roller Covers
The application and installation of conveyor roller covers are crucial steps to enhance the functionality and efficiency of your conveyor system. Whether you’re looking to reduce noise, minimize wear on products, or extend the life of your rollers, proper installation is key. Here, we provide a detailed step-by-step guide on applying and installing different types of roller covers, along with eight tips for DIY enthusiasts interested in creating custom roller covers for unique conveyor setups.
Step-by-Step Guide for Applying and Installing Conveyor Roller Covers
- Measure and Cut: Measure the length of your conveyor rollers to determine the required length of your roller covers. Cut the covers to size with a slight overlap to ensure full coverage without stretching the material excessively.
- Choose the Right Type: Select the appropriate material for your conveyor roller covers based on your conveyor’s application. Options include polyurethane for durability and grip, rubber for impact resistance, or PVC for chemical resistance.
- Clean the Rollers: Before applying the covers, ensure the rollers are clean and free of debris. Any particles on the rollers can cause unevenness or slippage once the covers are applied.
- Apply Adhesive (If Required): Some roller covers require an adhesive for installation. Apply a thin, even layer of the recommended adhesive to the roller, avoiding any clumps or bubbles.
- Install the Covers: Carefully slide the roller covers onto the rollers. For tight-fitting covers, it may be helpful to use a lubricant (such as soapy water) that does not interfere with the adhesive or material.
- Secure the Covers: Ensure the covers are securely in place. Some covers may require additional fasteners or heat shrink to tightly bind them to the rollers.
- Trim Excess Material: If there’s any excess material after installation, trim it carefully to avoid any operational interference.
- Test the Conveyor: Run your conveyor system for a short period to ensure the roller covers are correctly installed and functioning as expected.
Tips for DIY Custom Conveyor Roller Covers
- Understand Your Needs: Assess the specific requirements of your conveyor setup, including material handling, environmental conditions, and operational speeds, to design effective custom covers.
- Material Selection: Choose materials that not only fit the application but also can be easily worked with using tools you have available. Consider flexibility, durability, and resistance properties.
- Use Templates: For complex shapes or sizes, create templates out of cardboard or paper first. This ensures your custom covers will have the correct dimensions before cutting into your chosen material.
- Experiment with Textures: Depending on your conveyor’s function, different textures on the roller covers can improve grip, reduce noise, or influence the movement of conveyed materials.
- Consider Color Coding: Using different colors for various sections of your conveyor can help with quick identification of zones, especially for troubleshooting or during maintenance.
- Test for Compatibility: Ensure that the materials you choose for the roller covers are compatible with the items being conveyed, especially if chemical reactions could occur.
- Plan for Adjustments: Your first attempt at custom roller covers might not be perfect. Plan for adjustments and be willing to rework your designs based on performance.
- Safety First: When creating and installing custom conveyor roller covers, prioritize safety. Wear protective gear, and ensure that all modifications do not compromise the structural integrity or safety of the conveyor system.
By following these detailed steps and tips, you can successfully apply and install conveyor roller covers, enhancing your conveyor system’s performance and durability. Customizing your own covers allows for a tailored approach to meet the unique demands of your setup, ensuring optimal efficiency and longevity.
Find the right conveyor roller for your specific requirements.
Maintenance and Care of Conveyor Roller Covers
Maintaining your conveyor roller covers is crucial for ensuring peak performance and longevity. These components play a vital role in the smooth operation of conveyor systems, reducing noise levels, and protecting both the rollers and the materials being transported. Below, we offer comprehensive guidelines for regular maintenance and troubleshooting common issues associated with conveyor roller covers.
Regular Maintenance Guidelines
- Inspection Schedule: Establish a regular inspection schedule for your conveyor roller covers. This should include checking for wear and tear, cracks, and any signs of aging. Early detection of potential issues can prevent more significant problems down the line.
- Cleaning Procedures: Conveyor roller covers should be kept clean to ensure optimal performance. The cleaning frequency will depend on the environment in which they operate. In dusty or dirty environments, more frequent cleaning is necessary. Use mild soap and water for cleaning and avoid harsh chemicals that could damage the material of the covers.
- Lubrication: While the roller covers themselves do not require lubrication, the bearings and mechanisms they protect might. Ensure these components are appropriately lubricated according to the manufacturer’s recommendations to prevent overheating and wear.
- Alignment Checks: Misalignment can lead to uneven wear on conveyor roller covers. Regularly check the alignment of your conveyor system and make adjustments as needed to prevent this issue.
- Replacement Plans: Even with diligent maintenance, conveyor roller covers will eventually wear out and need replacement. Having a replacement plan in place ensures that you can quickly swap out old or damaged covers, minimizing downtime.
Troubleshooting Common Issues
- Excessive Wear: If you notice that your conveyor roller covers are wearing out more quickly than expected, check for misalignment or an improper installation. It could also be a sign that the material being transported is too abrasive for the type of cover you’re using.
- Cracking or Splitting: Exposure to extreme temperatures or chemicals can cause conveyor roller covers to crack or split. Ensure the materials used are suitable for your operational environment. If environmental conditions are not the cause, consider consulting with the manufacturer for a more resilient material option.
- Slippage: Slippage between the conveyor belt and roller covers can indicate a tension issue. Ensure that your conveyor system is correctly tensioned. Additionally, check for the accumulation of dust or debris under the covers, as this can also lead to slippage.
- Noise Increase: An increase in noise could indicate that the conveyor roller covers are hardening or that there is an issue with the rollers themselves. Check both the covers and rollers for signs of wear or damage.
Regular maintenance and timely troubleshooting of conveyor roller covers are essential steps in maintaining the efficiency and longevity of your conveyor system. By adhering to these guidelines, you can prevent most common issues and ensure that your conveyor system operates smoothly and reliably.
Last Updated on July 26, 2024 by Jordan Smith
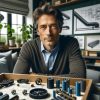
Jordan Smith, a seasoned professional with over 20 years of experience in the conveyor system industry. Jordan’s expertise lies in providing comprehensive solutions for conveyor rollers, belts, and accessories, catering to a wide range of industrial needs. From initial design and configuration to installation and meticulous troubleshooting, Jordan is adept at handling all aspects of conveyor system management. Whether you’re looking to upgrade your production line with efficient conveyor belts, require custom conveyor rollers for specific operations, or need expert advice on selecting the right conveyor accessories for your facility, Jordan is your reliable consultant. For any inquiries or assistance with conveyor system optimization, Jordan is available to share his wealth of knowledge and experience. Feel free to reach out at any time for professional guidance on all matters related to conveyor rollers, belts, and accessories.