Ultimate Guide to Conveyor Roller Ends Selection
Conveyor systems are integral to numerous industries, enabling efficient transport and handling of materials across extensive facilities. Central to these systems are the conveyor roller ends, which play a pivotal role in maintaining the stability and functionality of the conveyor belts. These components cap the ends of conveyor rollers, providing a smooth surface that interacts with other parts of the conveyor system, such as the frame and the belt itself.The importance of conveyor roller ends cannot be overstated. They are crucial for the smooth operation of conveyor systems; they minimize friction and wear at the points where rollers meet the conveyor belt, thus extending the life of the system and reducing maintenance needs. Without effective conveyor roller ends, the rollers could destabilize, leading to belt misalignment, increased friction, and potential operational failures. Therefore, ensuring that your conveyor system is equipped with high-quality conveyor roller ends is essential for uninterrupted and efficient operations. This component not only supports operational integrity but also enhances safety and productivity through its pivotal role in the conveyor system.
What are Conveyor Roller Ends
Conveyor roller ends are critical components of conveyor systems, specifically designed to secure the ends of conveyor rollers to ensure smooth and consistent movement of the conveyor belt. These ends fit snugly into the roller tube, helping to reduce rotational friction and facilitate easy movement. The primary function of conveyor roller ends is to provide stability and support to the rollers, allowing them to rotate uniformly without excessive play or movement that could affect the conveyor’s efficiency.
Types of Conveyor Roller Ends
Conveyor roller ends come in various designs, each tailored to meet different operational demands and environmental conditions. Understanding the differences among these types can help in selecting the right type for your application, enhancing the system’s overall effectiveness and durability. Here are the most common types:
Round Conveyor Roller Ends
Round conveyor roller ends are the most widely used type due to their simplicity and effectiveness. They feature a circular design that fits into the ends of cylindrical rollers. This shape allows for easy rotation and is generally used in less demanding environments where the load and operational speeds are moderate.
Flatted Conveyor Roller Ends
Flatted conveyor roller ends include a flat side along the otherwise round end cap, which can be used to lock the roller into a fixed orientation relative to the conveyor frame. This design is particularly useful in applications where the roller alignment is critical to the maintenance of the belt path and reduces the risk of misalignment issues.
Threaded Conveyor Roller Ends
Threaded conveyor roller ends feature screw-like threads that help securely fasten the rollers into the conveyor frame, offering enhanced stability. These are ideal for heavy-duty applications where rollers need to withstand higher loads or more vigorous operational conditions. The threaded design ensures that the roller ends do not loosen over time, maintaining the system’s integrity and prolonging its lifespan.
Each type of conveyor roller end serves its specific purpose and selecting the right one depends largely on the operational conditions and the physical demands of the application. By understanding these types and their functions, businesses can make informed decisions that optimize the performance and reliability of their conveyor systems. Selecting the appropriate conveyor roller ends is a critical step in designing or upgrading a conveyor system, ensuring it operates smoothly and efficiently with minimal maintenance requirements.
Key Features and Specifications of Conveyor Roller Ends
Conveyor roller ends are essential for the optimal performance of conveyor systems, serving to cap the ends of the rollers which facilitate smooth and effective operation. The design and material of the conveyor roller ends play a significant role in the system’s functionality and longevity. Below we detail the key features and specifications of conveyor roller ends, illustrated through informative tables that compare different types, materials, and compatibility features.
Material Types
The choice of material for conveyor roller ends affects their durability, weight, and suitability for different environments. Common materials used include:
- Steel: Highly durable and perfect for heavy-duty applications.
- Aluminum: Lighter than steel, resistant to corrosion, suitable for medium-load applications.
- Plastic: Best for lighter applications, less durable than metal options but corrosion-resistant and cost-effective.
Diameter and Load Capacity
The diameter of conveyor roller ends and their load capacities are critical specs that determine what weight the rollers can handle and affect the overall system performance.
Compatibility with Roller Materials and Sizes
Conveyor roller ends must be compatible with the materials and sizes of the rollers they are to be fitted on. Compatibility affects the roller’s operational efficiency and risk of failure.
Choosing the right conveyor roller ends involves understanding the complete dynamics of the conveyor system, including the materials, environmental conditions, and load requirements. By ensuring compatibility and selecting the appropriate specifications, the longevity and efficiency of the conveyor system can be significantly enhanced. These tables serve as a guide to help in making an informed choice when purchasing conveyor roller ends, tailored to specific operational needs and conditions.
Types of Conveyor Roller Ends
Conveyor roller ends are crucial for the efficient operation of conveyor systems, serving as the main contact points between the rollers and the frame of the conveyor, which supports the belt. These ends come in various types and specifications, tailored to meet different operational needs and environmental conditions. Below, we explore the different types of conveyor roller ends available, including new models, replacement strategies, considerations for purchasing used items, and features of heavy-duty options.
Conveyor Roller Ends for Sale: New Models and Their Specifications
New conveyor roller ends are continually developed to improve efficiency and compatibility with evolving industrial machinery. These new models often feature enhanced materials and designs, such as increased load capacity, better corrosion resistance, and reduced friction properties.
Conveyor Roller Ends Replacement: When and Why Replacements are Needed
Replacements of conveyor roller ends are typically required when they exhibit wear and tear that could compromise the conveyor’s functionality. Common signs necessitating replacements include visible damage, such as cracks or significant wear, unusual noise during operation, or increased friction and resistance that impede the conveyor’s efficiency.
Used Conveyor Roller Ends: Considerations for Purchasing Used Roller Ends
Purchasing used conveyor roller ends can be a cost-effective option, especially for short-term use or less critical applications. However, several considerations should be taken into account to ensure they are suitable for your needs.
Heavy-Duty Conveyor Roller Ends: Features and Ideal Applications
Heavy-duty conveyor roller ends are designed to withstand high loads and harsh environments, making them ideal for industries such as mining, heavy manufacturing, and agriculture.
These heavy-duty ends are essential for operations that require robust performance and minimal downtime. Their enhanced features ensure that they meet the operational demands of various industries, providing reliability and efficiency where it matters most. Selecting the right type of conveyor roller ends, whether new, used, or heavy-duty, depends on the specific requirements and environmental conditions of your conveyor system. This strategic choice is crucial for optimizing the performance and longevity of your conveyor operations.
Purchasing Guide for Conveyor Roller Ends
When it comes to maintaining an efficient conveyor system, selecting the right conveyor roller ends is crucial. These components are vital for the proper functioning of conveyor rollers, affecting everything from system stability to maintenance frequency and longevity. Below is a comprehensive guide detailing the factors to consider when purchasing conveyor roller ends and where to find them.
Factors to Consider When Buying Conveyor Roller Ends
The performance and durability of conveyor roller ends depend significantly on their construction and compatibility with the conveyor system. Here are key considerations to keep in mind:
Durability and Material
The material of the conveyor roller ends determines their durability and resistance to environmental challenges such as corrosion, abrasion, and physical impacts.
- Steel: Best for high-strength requirements; prone to corrosion unless treated.
- Aluminum: Lighter than steel, naturally corrosion-resistant, suitable for moderate loads.
- Plastic: Least expensive, corrosion-resistant, not suited for high-load applications.
Selecting a material that matches the operational demands and environmental conditions of your application is essential for optimizing longevity and reducing maintenance costs.
Load Capacity and Suitability for Application
Load capacity is a critical spec to consider, as it must meet or exceed the demands of the materials the conveyor will transport. Ensure the conveyor roller ends can support the weight and stress of typical loads in your application to prevent premature wear and failure.
- High-load Applications: Opt for steel or reinforced materials.
- Moderate-load Applications: Aluminum may be sufficient.
- Light-load Applications: Plastic ends can be cost-effective and adequate.
Compatibility with Existing Systems
Conveyor roller ends must be compatible with the existing roller tubes and conveyor framework to ensure smooth installation and operation.
- Size Compatibility: The ends should fit snugly into the existing roller tubes.
- Material Compatibility: Choose materials that are compatible with the environment (e.g., non-reactive metals in corrosive environments).
Where to Find Conveyor Roller Ends
Once you’ve determined the specifications required for your conveyor system, the next step is purchasing the right product. Here are some reliable sources:
McMaster-Carr’s Offerings
McMaster-Carr is renowned for its comprehensive inventory of industrial parts, including conveyor roller ends. They offer a wide variety of types and sizes, suitable for many different applications and readily available for quick shipping.
- Advantages:
- Extensive selection
- Detailed product specifications and CAD models
- Quick delivery
Other Reputable Suppliers
Besides McMaster-Carr, several other suppliers and manufacturers specialize in conveyor components and can provide high-quality conveyor roller ends.
- Global Industrial:
- Offers a range of industrial equipment, including conveyor system components.
- Competitive pricing and good customer support.
- Grainger:
- Wide selection, including heavy-duty options.
- Reliable delivery and service.
- Direct Industry:
- Connects buyers with manufacturers globally.
- Good for customized orders.
- Local Suppliers:
- Can offer faster delivery and personalized service.
- Potential cost savings on shipping.
Purchasing conveyor roller ends from reputable suppliers ensures you receive high-quality components that meet industry standards and are compatible with your specific system requirements. Whether upgrading your current system or building a new one, selecting the right conveyor roller ends is crucial for operational efficiency and system longevity. This guide aims to assist you in making an informed purchasing decision, taking into consideration all necessary specifications and supplier options.
Installation and Maintenance of Conveyor Roller Ends
Proper installation and regular maintenance of conveyor roller ends are crucial for extending the life and enhancing the performance of conveyor systems. This section provides basic guidelines on how to install conveyor roller ends and offers practical tips for their maintenance.
Basic Guidance on Installing Conveyor Roller Ends
Installing conveyor roller ends correctly is essential to ensure that the conveyor system operates smoothly and efficiently. Here are the steps to follow for installation:
Preparation:
- Inspect the Conveyor: Before installation, check the conveyor frame and rollers for any signs of damage or wear. Ensure that the rollers are clean and free of debris.
- Gather Tools and Materials: Typically, you will need a rubber mallet, wrenches, and lubricants. Make sure you have the correct size of conveyor roller ends.
Alignment:
- Position the Roller: Align the roller tube properly within the conveyor frame to ensure that the conveyor roller ends will fit snugly.
- Check Alignment: Use a level to verify that the roller is perfectly horizontal. An improperly aligned roller can cause the belt to traverse off-center, leading to increased wear and tear.
Installation:
- Insert the Roller Ends: Carefully place the conveyor roller ends into the ends of the roller tube. If they are tight-fitting, use a rubber mallet to gently tap them into place.
- Secure the Ends: Depending on the type of roller end (e.g., threaded), use the appropriate tools to secure the ends. For threaded ends, screw them in until they are firm, but do not over-tighten as this may strip the threads.
Final Checks:
- Rotate the Roller: Once installed, rotate the roller by hand to ensure it moves freely. This check will help confirm that the roller ends are not overly tight and that there is no misalignment.
- Reinspect Alignment: Verify once more that the roller is level and aligned correctly within the conveyor frame.
Tips for Maintaining Conveyor Roller Ends to Ensure Longevity and Performance
Regular maintenance of conveyor roller ends is necessary to prevent breakdowns and extend the lifespan of conveyor systems. Here are five maintenance tips:
Regular Inspection:
- Periodically check conveyor roller ends for signs of wear or damage such as cracks, rust, or accumulation of debris. Early detection of issues can prevent costly repairs and downtime.
Lubrication:
- Apply appropriate lubricants to the conveyor roller ends to reduce friction and wear. Ensure the use of lubricants compatible with the material of the roller ends and the operating conditions of the conveyor.
Cleaning:
- Keep the roller ends clean from dust, grime, and chemical residues, which can corrode or clog the moving parts. Use a mild solvent or degreaser to clean the roller ends thoroughly.
Tightening and Adjustments:
- Regularly check and tighten any loose components in the conveyor roller ends. Adjustments may be necessary to align the rollers correctly with the conveyor belt to prevent uneven wear.
Replacement:
- Replace conveyor roller ends that are beyond repair to maintain the efficiency of the conveyor system. Use this opportunity to upgrade to more durable models if frequent replacements are needed.
By following these installation and maintenance guidelines, you can ensure that your conveyor roller ends are well-maintained, leading to improved functionality and reduced operational costs. Proper care and regular checks are the keys to extending the life of these essential components.
Cost Considerations for Conveyor Roller Ends
When planning to purchase conveyor roller ends, understanding the cost implications and identifying ways to save money without compromising on quality is crucial. This section provides an overview of the pricing range for conveyor roller ends and offers practical cost-saving tips.
Overview of the Pricing Range for Conveyor Roller Ends
The cost of conveyor roller ends can vary widely based on factors such as material, size, type, and manufacturer. Here’s a general pricing breakdown:
- Plastic Roller Ends: These are the most economical option, typically ranging from $5 to $20 per piece. Suitable for light-duty applications where high durability is not critical.
- Aluminum Roller Ends: Mid-range price, generally between $15 to $40 per piece. They offer a good balance of weight and strength for medium-load applications.
- Steel Roller Ends: These are the most expensive, usually costing between $25 and $100 per piece, depending on the size and specific design. Ideal for heavy-duty applications due to their high durability and load capacity.
Cost-Saving Tips When Purchasing Conveyor Roller Ends
To maximize your investment in conveyor roller ends, consider the following cost-saving strategies:
Bulk Purchases:
- Economies of Scale: Buying conveyor roller ends in bulk often results in lower per-unit costs. Suppliers may offer discounts for large orders, which is particularly advantageous for large projects or ongoing needs.
- Example: Purchasing 100+ units might reduce the cost by 10-20% compared to buying in smaller quantities.
Select the Appropriate Material:
- Material Suitability: Choose the material that best fits the operational demands and environmental conditions. Opting for a more expensive material that is over-specified for the job can unnecessarily increase costs.
- Example: Using aluminum roller ends instead of steel in environments that do not involve extreme conditions or high loads can save 25-50% per unit.
Compare Suppliers:
- Shop Around: Evaluate prices from multiple suppliers to find the best deal. Include both local and international suppliers in your comparison.
- Example: Prices can vary by as much as 50% between suppliers, especially when including international options.
Consider Refurbished or Used Parts:
- Cost-Effective Alternatives: Used or refurbished conveyor roller ends can provide significant savings, especially for temporary installations or non-critical applications.
- Example: Refurbished roller ends might cost 50-70% of the price of new ones.
Right-Sizing the Components:
- Avoid Over-Specifying: Ensure that the specifications (like load capacity and size) of the conveyor roller ends precisely match your needs. Over-specifying can lead to unnecessary cost increases.
- Example: Choosing roller ends with a correct load capacity for your application could save 10-30% compared to opting for the highest available capacity.
Lifetime Cost Considerations:
- Evaluate Total Cost of Ownership: Consider factors such as durability, maintenance requirements, and operational efficiency. A cheaper initial option that requires frequent replacements or more maintenance may be more expensive in the long run.
- Example: Steel roller ends, while more expensive upfront, might offer lower lifetime costs through reduced maintenance and longer life span compared to plastic ends.
By taking these cost considerations into account when purchasing conveyor roller ends, you can significantly reduce expenses while ensuring you acquire components that meet your operational requirements efficiently. Strategic purchasing decisions not only cut immediate costs but also contribute to the sustainability and profitability of your operations in the long term.
FAQs About Conveyor Roller Ends
The rollers on a conveyor, commonly known as conveyor rollers, are the moving parts attached to a conveyor system. They are designed to support and move the conveyor belt or the items being transported efficiently along the path of the conveyor system. These rollers are cylindrical tubes that rotate around a central axis and are typically made from materials such as metal (steel or aluminum), plastic, or a combination of both.
Conveyor rollers are critical for the smooth operation of the conveyor system. They reduce the friction between the belt and the surface it moves on, which helps in moving the belt with less effort and energy. This not only improves the efficiency of the conveyor but also extends its lifespan by minimizing wear and tear. Rollers are spaced at regular intervals along the conveyor frame to provide consistent support and stability to the belt or items being moved.
A roller conveyor typically consists of the following key components:
Conveyor Rollers: The cylindrical tubes that directly support and move the conveyor belt or items. These can vary in material and size depending on the application.
Frame: The structure that supports the rollers. It is usually made from materials like steel, aluminum, or heavy-duty plastics.
Bearing and Shafts: Bearings help reduce the friction at the roller ends, allowing them to rotate smoothly. Shafts connect the rollers to the frame.
Drive Unit: In powered roller conveyors, a drive unit is used to provide the rotational force needed to move the rollers. This can be a motor that drives the rollers via belts, chains, or gears.
Support Legs: These support the frame at a suitable height, typically with adjustments available to cater to different belt heights and terrains.
A conveyor roller works by providing a rolling surface for the conveyor belt or directly for goods/materials, reducing the amount of friction that the belt would typically encounter when dragged across a standard surface. In powered roller conveyors, each roller is connected to a motor (either directly or via a chain or belt system) that rotates the rollers, which in turn moves the belt or items placed on the rollers.
In gravity roller conveyors, the conveyor is slightly inclined or manually adjusted to utilize gravity, allowing goods to travel down the rollers without the need for motor power. The rollers are closely spaced to ensure that items travel smoothly without significant drops or snagging.
The efficiency of conveyor rollers can be impacted by several factors including roller diameter, material, spacing between rollers, and the type of bearings used. Properly designed conveyor rollers not only facilitate efficient transport but also reduce the workload on the conveyor motor and other mechanical components, thereby increasing the system’s overall efficiency and durability.
While roller conveyors are advantageous in many applications, they also come with several limitations:
Limited Types of Materials: Roller conveyors are typically not suitable for transporting material that is sticky or wet as it can adhere to the rollers and cause jams and slippage.
Load Limitations: They are not ideal for very heavy loads that might require stronger conveyor systems such as belt conveyors. The weight limits are determined by the rollers’ material strength and design.
Inclines and Declines: Handling inclines and declines can be challenging with roller conveyors as there is a risk of goods slipping back down or rolling uncontrollably.
Directional Limitation: Conveyors generally move materials in a single direction. Reversing the direction often requires additional equipment and expense.
Maintenance: Rollers require regular maintenance to ensure they are not seized and are free of materials that may cause blockage or reduce efficiency.
Last Updated on April 23, 2024 by Jordan Smith
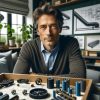
Jordan Smith, a seasoned professional with over 20 years of experience in the conveyor system industry. Jordan’s expertise lies in providing comprehensive solutions for conveyor rollers, belts, and accessories, catering to a wide range of industrial needs. From initial design and configuration to installation and meticulous troubleshooting, Jordan is adept at handling all aspects of conveyor system management. Whether you’re looking to upgrade your production line with efficient conveyor belts, require custom conveyor rollers for specific operations, or need expert advice on selecting the right conveyor accessories for your facility, Jordan is your reliable consultant. For any inquiries or assistance with conveyor system optimization, Jordan is available to share his wealth of knowledge and experience. Feel free to reach out at any time for professional guidance on all matters related to conveyor rollers, belts, and accessories.